ПОРЯДОК ПРОВЕДЕНИЯ ПРОВЕРОК ОБОРУДОВАНИЯ НА ТЕХНОЛОГИЧЕСКУЮ ТОЧНОСТЬ
Проверка оснастки на технологическую точность
https://burforum.ru/obrabotka-stali/metodika-proverki-oborudovaniya-na-tehnologicheskuyu-tochnost.html
Регламент контроля
Плановый контроль технологической точности металлообрабатывающей техники проводится по графику, который составляется согласно специальному документу – ведомости станочного оборудования. В неё заносятся сведения о периодичности технологических операций, влияющих на точность изготовления продукции. Этот документ содержит также сведения о режимах работы станков.
Проверка может носить не только плановый характер, но и выполняться при аварийных отказах оборудования. В этом случае контрольные мероприятия проводятся в соответствии с регламентами, разработанными для устранения форс-мажорных обстоятельств.
Любые проверки – как плановые, так и аварийные – проводятся при условии временного вывода машин из эксплуатации. По этой причине разработка графика контрольных мероприятий является весьма важной для планирования как производственной деятельности, так и модернизации оборудования. Остаётся добавить, что ответственным за это направление работы предприятия отвечает, как правило, главный технолог завода.
Порядок проведения проверки оборудования
Технический осмотр приспособлений производится комиссионно. Результаты технического осмотра записываются в журнале записи результатов технического осмотра оснастки.
|
|
Проверку на технологическую точность крупногабаритной оснастки в случае ее сложного демонтажа, допускается производить путем выборочных проверок деталей, изготовленных на этом приспособлении.
Техническому осмотру подлежит вся эксплуатируемая технологическая оснастка, определенная ведомостью. Технический осмотр проводится два раза в месяц, путем внешнего осмотра и замера контролируемых размеров изготавливаемой на приспособлении детали, отдельных параметров технологической оснастки, влияющих на точность изготовления детали.
ТЕХНИЧЕСКАЯ ИНФОРМАЦИЯ.
Технологическая оснастка, точность которой при проверке оказалась ниже допустимой, подлежит ремонту и последующей проверке.
Также одним из важных измерений при проверке токарного станка на точность является определение точности шага ходового винта. Величина отклонения в соответствии с ГОСТ определяется с помощью следующей методики:
ОБЩИЕ ПОЛОЖЕНИЯ
1. ОБЩИЕ ПОЛОЖЕНИЯ
1.1. Проверка оборудования на технологическую точность является одним из основных элементов контроля технологической дисциплины (КТД), проводимый в соответствии с ОСТ 24.001.22-82 (новый - РД 24.022.09-87).
|
|
1.2. Технологическая точность оборудования (ТТО) — способность оборудования в оснащенном состоянии (станок-приспособление-инструмент-деталь) обеспечивать в течение определенного периода времени заданную точность изготовления изделия по размерам, форме и чистоте поверхностей, установленную конструкторской документацией и техническими требованиями.
1.3. Целью проверки оборудования на технологическую точность является предупреждение возможного снижения заданной технологической точности и преждевременного выхода из строя оборудования, технологической оснастки, инструмента, исключение производственного брака, предупреждение производственного травматизма, повышение организации производства и охрана окружающей среды.
1.4. Проверке на технологическую точность подлежит металлорежущее оборудование, специальное и уникальное оборудование, занятое на выполнении окончательных отделочных операций, а также литейное, кузнечно-прессовое оборудование, неточность которого может повлечь за собой брак деталей, выявляемый на окончательных операциях.
1.5. Проверка оборудования на технологическую точность должна проводиться:
1.5.1. периодически в установленные сроки;
|
|
1.5.2. при вводе оборудования в эксплуатацию;
1.5.3. при внедрении новых технологических процессов;
1.5.4. во всех случаях изготовления деталей с отступлениями от технических требований, чертежа и технологической документации, а также по требованию отдела технического контроля (ОТК) и Государственной приемки.
1.6. Следует отличать проверку оборудования на технологическую точность от проверки оборудования по нормам точности, проводимой при приемке после ремонта или монтажа и предусматривающей: для отечественных металлорежущих станков проверку в соответствии с паспортными данными на оборудование и государственными стандартами; для импортного оборудования — в соответствии с техническими характеристиками, гарантируемыми фирмой-изготовителем.
1.7. Проверка оборудования на технологическую точность включает в себя выбор норм технологической точности, исходя из чертежей и технических требований на обработку закрепленных деталей, и схватывают только те отклонения форм и относительного положения линий и поверхностей оборудования, а также траектории движения его рабочих органов, которые непосредственно влияют на точность выполнения закрепленных за оборудованием технологических операций.
|
|
1.8. Нормы технологической точности оборудования следует устанавливать, исходя из допуска наиболее точной операции, выполняемой на проверяемом оборудовании.
1.9. Перед проверкой оборудования на технологическую точность следует убедиться в соответствии технологическому процессу заготовки, инструмента, приспособления, оборудования и в их исправности.
1.10. Методы выполнения проверок и применяемые приборы, контрольно-измерительные приспособления, измерительные инструменты определяются исходя из особенностей технологического процесса, конструктивных особенностей детали, приспособления, оборудования.
1.11. Объем параметров, выбираемый при проверке оборудования на технологическую точность, должен быть минимальным, но достаточным для получения необходимой достоверности результатов и принятия решения об уровне точности оборудования.
1.12. Периодичность проверок технологического оборудования определяется службами главных специалистов по видам производств, исходя из применяемых режимов обработки, требующейся точности, степени износа оборудования.
1.13. В целях сокращения простоев оборудования следует совмещать сроки проверок оборудования на технологическую точность со сроками ремонта или профилактического осмотра оборудования.
1.14. С оборудования, не прошедшего в установленный срок проверки на технологическую точность или показавшего при проверке снижение установленных норм технологической точности, ОТК предприятия приемку продукции не производит.
1.15. При несоответствии оборудования нормам технологической точности необходимо проверить элементы системы станок-приспособление-инструмент-деталь раздельно.
1.16. В случае невозможности определения значений технологической точности системы разрешается, по согласованию со службами главных специалистов и ОТК, раздельная проверка оборудования, приспособления, инструмента на геометрическую точность, при этом оборудование проверяется по паспорту или Государственному стандарту с внесением значений определяемых параметров в инструкционную карту.
1.17. При проверке оборудования на технологическую точность следует учитывать: нормы технологической точности не являются нижним пределом точности оборудования, при котором обеспечивается получение с него годной продукции. Эти нормы должны предусматривать определенный запас точности, позволяющий производить обработку закрепленных за оборудованием деталей в пределах допусков, определяемых чертежами и техническими требованиями на их изготовление и гарантирующий отсутствие брака обрабатываемых деталей в период между плановыми ремонтами.
ПОРЯДОК ПРОВЕДЕНИЯ ПРОВЕРОК ОБОРУДОВАНИЯ НА ТЕХНОЛОГИЧЕСКУЮ ТОЧНОСТЬ
2.1. Проверка технологической точности оборудования проводится силами и средствами предприятия.
2.2. Процесс планирования и проведения проверок ТТО должен включать в себя следующие работы:
составление и утверждение ведомости оборудования, подлежащего периодической проверке;
установление периодов и сроков проверки оборудования на технологическую точность;
составление и утверждение графиков проверки оборудования;
разработка и оформление инструкционных карт проверки оборудования;
оформление актов проверки оборудования.
2.3. Организация проверки оборудования на технологическую точность возлагается на механика цеха.
2.4. Проверку оборудования на технологическую точность проводит комиссия.
2.5. В состав комиссии должны входить специалисты службы технического контроля, технологической службы цеха, начальник участка (старший мастер участка), механик цеха. При необходимости в состав комиссии включаются работники отделов главного технолога, главного метролога, промышленной электроники, инструментального отдела и др.
2.6. В обязанности комиссии входит:
Дата добавления: 2022-01-22; просмотров: 546; Мы поможем в написании вашей работы! |
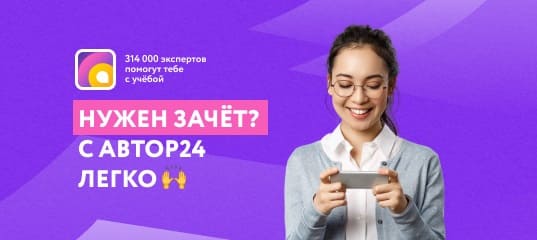
Мы поможем в написании ваших работ!