Механические свойства и режимы термообработки (ТО) некоторых силуминов
сплав | Способ литья | Режим ТО | σв кгс/мм2 | δ, % | НВ кгс/мм2 | Сплав | Способ литья | Режим ТО | σв кгс/мм2 | δ, % | НВ кгс/мм2 |
не менее | не менее | ||||||||||
3,0, В, К | — | 16 | 2 | 50 | ВАЛ5 | зм | Т5 | 30 | 2 | 100 | |
д | — | 17 | 1 | 50 | АЛ4М | км | Т5 | 30 | 3 | 90 | |
АЛ9 | 3,0,В,К,Д | Т2 | 14 | 2 | 45 | зм | Т5 | 30 | 2 | 90 | |
к | Т4 | 19 | 4 | 50 | АЛ5 | 3,0,В, к | Т1 | 16 | 0,5 | 65 | |
3,0,В | Т4 | 19 | 4 | 50 | з,о,в | Т5 | 20 | 0,5 | 70 | ||
к | Т5 | 21 | 2 | 60 | з.о.в | Т6 | 23 | 0,5 | 70 | ||
з.о.в | Т5 | 20 | 2 | 60 | з.о.в, к | Т7 | 18 | 1 | |||
зм.ом.вм | Т6 | 23 | 1 | 70 |
| ||||||
зм.ом.вм | Т7 | 20 | 2 | 60 |
| ||||||
зм.ом.вм | Т8 | 16 | 3 | 55 |
|
Примечания: 1) 3 — литье в землю; О — оболочковое литье; К — литье в кокиль; Д — литье под давлением; В — литье по выплавляемым моделям; М —модифицированное состояние.
2) 1 кгс/мм2 ≈ 10 МН/ма (МПа).
Сплавы на основе системы Al—Mg обладают высокими свойствами (σ и δ), хорошо обрабатываются резанием и имеют высокую коррозийную стойкость. Высокая удельная прочность σв/γ (т. е. с учетом плотности) сплавов на основе Al—Mg позволяет широко применять их в качестве конструкционных материалов, работающих в условиях повышенных статических и удар-
|
|
нагрузок в различных климатических условиях. Режимы термообработки (ТО) и механические свойства некоторых сплавов этой группы представлены в табл. 6.
Таблица 6 Механические свойства сплавов на основе системы Al — Mg
Сплав | Способ литья* | Режим ТО | σв кгс/мм2 | δ, % | НВ кгс/мм2 | Сплав | Способ литья* | σв кгс/мм2 | δ, % | НВ кгс/мм2 |
не менее | не менее | |||||||||
АЛ8 | 3,0,В,К | Т4 | 29 | 9 | 60 | АЛ13 | 3,0,В, К | 15 | 1 | 55 |
АЛ27 | З,О,К, Д | Т4 | 32 | 12 | 75 | Д | 17 | 0,5 | 55 | |
АЛ27-1 | 3,0,К, Д | Т4 | 35 | 15 | 75 | АЛ29 | Д | 21 | 3 | 60 |
АЛ23-1 | 3,0,К | Т4 | 25 | 10 | 60 |
* См. примечания к табл. 5.
Промышленные сплавы на основе системы А1 — С u характеризуются высокими физико-механическими свойствами, повышенной жаропрочностью и хорошей обрабатываемостью резанием. Литейные свойства и герметичность (т. е. непроницаемость для газов и жидкостей, часто в условиях повышенных давлений) этих сплавов несколько хуже, чем у силуминов (это обусловлено широким температурным интервалом кристаллизации); коррозийная стойкость невысокая.
|
|
Классическими представителями сплавов на основе системы Al — Zn являются сплавы АЛ11 и АЛ24. Согласно диаграмме состояния этих сплавов цинк имеет высокую растворимость в алюминии, образуя твердый раствор α, крайне неустойчивый при повышенных температурах. Обладая низкими технологическими и физико-механическими свойствами, двойные сплавы Al—Zn в настоящее время не применяются: используются сплавы системы А1—Zn—Si (сплав АЛ 11) и Аl—Zn—Mg (АЛ24), склонные к естественному старению и обладающие высокими механическими свойствами. Общий недостаток цинко-алюминиевых сплавов — их сравнительно высокая плотность (до 3 г/см3).
Сплавы на основе Al—Zn обладают хорошей обрабатываемостью резанием и удовлетворительной герметичностью, а также хорошо свариваются. Используют эти сплавы для изготовления сложных по конструкции средненагруженных деталей, работающих при температурах до 150°С.
Строительные алюминиевые сплавы
В строительной индустрии с каждым годом увеличивается применение строительных алюминиевых сплавов в качестве основного конструкционного материала в несущих конструкциях зданий и сооружений, а не только в ограждающих элементах, оконных и дверных переплетах.
|
|
Основными достоинствами деформируемых и литейных сплавов являются: значительная удельная прочность, высокая технологичность (в холодном и в горячем состоянии), сохранение высоких прочностных свойств при отрицательных температурах, повышенная жаростойкость, значительная стойкость против коррозии.
Из сплавов марок Д1, Д6, Д16 изготовляют клепаные несущие конструкции сооружений и зданий (арки, фермы, балки и др.), а также различные элементы конструкций, совмещающих функции ограждающих и несущих конструкций (кровельные панели, каркасы стеновых панелей, подвижные потолки и др.). Для силовых элементов конструкций рекомендуется применять дюралюминий Д6 и Д16, а для элементов конструкций средней прочности сплав Д1. Сварку можно применять только в тех конструкциях, в которых сварные швы мало нагружены. Ответственные конструкции не рекомендуется сваривать, так как в околошовной зоне в результате нагрева прочность значительно понижается. Это не относится к сплавам АВ, АД31, АДЗЗ.
|
|
Магний и его сплавы
Магний — металл II группы периодической системы серебристо-белого цвета, порядковый номер 12, кристаллическая решетка Г12. Температура плавления 651° С, кипения 1007° С, плотность 1740 кг/м3, σв = 180 МН/м2, δ=5%, НВ 300 МН/м2, мягкий, относительно легко воспламеняется и горит ослепительным пламенем, выделяя значительное количество тепла. Среди конструкционных материалов он самый мягкий и легкий.
Магний выпускают двух марок Мг1 и Мг2. В машиностроении в чистом виде магний не применяют, но сплавы на его основе широко используют в различных отраслях промышленности как в литом, так и в деформируемом состояниях. Основные легирующие элементы магниевых сплавов: Al, Zn, Mn, Zr, C1.
К вредным примесям относят К, Na, Ni, Fe, Сг и газ Н2, снижающие коррозийные и механические свойства сплавов. Легирующие элементы образуют с магнием твердые растворы и соединения типа Mg2Al3, MgAl, MgZn2, Mg4Al3Zn3 и др. Алюминий (до 10%) и цинк (до 50%) повышают механические свойства магниевых сплавов. Марганец в количестве от 1 до 2,5 % улучшает прочностные свойства, а при малом содержании (0,15—0,5%) только антикоррозийные свойства. Термическая обработка (включая старение) повышает прочностные свойства сплавов на 25—35%.
Небольшие добавки к этим сплавам циркония, бериллия и некоторых других редкоземельных металлов (например, церия) способствует получению мелкозернистой структуры, улучшают механические свойства и пластичность, понижают окисляемость при нагреве.
Магниевые сплавы так же, как и алюминиевые, разделяются на деформируемые и литейные. В настоящее время возрос ассортимент деформируемых сплавов, применяемых в промышленности главным образом в виде фасонных штамповок, профилей, труб и пр. Обработку давлением магниевых сплавов ведут преимущественно в горячем состоянии при температурах 225—400° С. Здесь находят применение следующие марки: МА1, МА2, МАЗ, МА8, МА9, ВМ17, ВМ65-1 (ГОСТ 14957—69).
Сплавы МА1 и МА8 содержат от 1,0 до 2,5% Мn; в состав МА8 входит также церий до 0,35%. Эти сплавы обладают следующими механическими свойствами: σв ≈250 МН/м2, НВ 500 МН/м2, δ = 18 %, плотность 1760 кг/м3. Сплавы хорошо обрабатываются резанием, отличаются высокой пластичностью в горячем состоянии, обладают удовлетворительной коррозийной стойкостью, хорошо свариваются, относительно экономичны.
Сплавы МА2, МАЗ, МА5 легированы алюминием (3,5—9,2% А1 с добавкой десятых долей процента цинка и марганца), обладают следующими механическими свойствами: σв=250—320 МН/м2, НВ 550—600МН/м2, δ = 10—14%. Сплав ВМ65-1 (4,0—5,0% Zn, 0,3—0,5% Се) имеет повышенную прочность, хорошую пластичность (σв = 340 МН/м2, δ=9%, НВ 550—750 МН/м2) и плотность ~1700 кг/м3. Для повышения прочностных свойств (до 400 МН/м2) его подвергают термической обработке по режиму: нагрев под закалку в течение 16 ч до температуры 410—425° С, отпуск при 175° С также в течение 16 ч.
Сплавы МА9 и ВМ19 относят к жаропрочным, т. е. выдерживающим нагрузку при 350—400° С. Сплав МА9 имеет состав: 0,4—0,8% А1, 1,0—1,8% Мn, 0,1—0,3% Се, а сплав ВМ19 — 2% Мn и 3% Се.
Литейные магниевые сплавы широко применяют для изготовления фасонного литья, хотя по сравнению с алюминиевыми сплавами обладают значительно худшими литейными свойствами. Они имеют маркировку, подобную алюминиевым сплавам, и могут быть разделены на пять основных групп:
на основе системы Mg—Si (МЛ1); Mg—Мп (МЛ2); Mg—Al—Zn (МЛЗ, МЛ4, МЛ5, МЛ6, МЛ7-1); сплавы, содержащие цирконий и редкоземельные металлы (МЛ9, МЛ10, МЛН, МЛ12, ВМЛЗ); сплавы, содержащие торий и другие элементы (МЛ 14, ВМЛ1, ВМЛЗ).
Сплавы группы I (МЛ1) содержат 1,0—1,5% Si, обладают сравнительно низкими механическими свойствами (σв= 110 МН/м2, НВ 44 МН/м2 и δ= 3%), малой удельной плотностью; их применяют главным образом для отливки деталей, от которых требуется герметичность при повышенных давлениях.
Сплавы группы II (МЛ2) содержат 1—2% Мn. Примерные механические свойства: σв= 100 МН/м2, НВ 350 МН/м2, δ = 4%. Сплавы обладают повышенной коррозийной стойкостью, красноломкостью и пониженными технологическими свойствами.
Сплавы первых двух групп термической обработкой не упрочняют.
Сплавы группы III (МЛЗ) в отличие от первых двух обладают лучшими механическими свойствами как в литом состоянии, так и после термической обработки. Типичные представители этой группы сплавы МЛЗ, МЛ4 и МЛ5. Упрочняющими фазами при термообработке являются соединения типа: Mgl7All2 и Mg3Al2Zn3. Из сплава МЛЗ (2,5—3,5% А1, 0,5—1,5% Zn и 0,15—0,5% Мn) отливают детали повышенной герметичности (корпуса насосов, части арматуры и др.). Механические свойства сплава МЛЗ: σв = 160 МН/м2, НВ 400 МН/м2; δ =6%.
Сплав группы IV (МЛ4) (5—7% А1, 2—3% Zn, 0,15—0,5% Мn) после гомогенизации с закалкой на воздухе и последующем старении имеет повышенные механические свойства: σв = 230 МН/м2, НВ 600 МН/м2 и δ = 2—5%.
Сплавы группы IV применяют для отливки деталей, работающих при повышенной температуре (250—260° С).
Сплав группы V (МЛ5) обладает аналогичными механическими свойствами. Из этого сплава отливают высоконагруженные детали двигателей и приборов, корпуса пневматических и ручных инструментов и т. д.
Сплавы V группы относят к жаропрочным. Литые детали могут работать при температурах 350—400° С. Сплавы этой группы подвергают закалке от температуры 410° С с последующим искусственным старением при 180° С в течение 12 ч. Такая термическая обработка повышает σв до 260 МН/м2, НВ до 800 МН/м2 и δ до 9%.
Следует отметить, что литейные магниевые сплавы по удельной прочности превосходят высокопрочные алюминиевые сплавы и некоторые конструкционные стали.
Медь и ее сплавы
Медь относится к тяжелым цветным металлам, ее плотность 8,94 кг/м3, температура плавления 1083° С, кипения 2360° С, кристаллическая решетка — гранецентрированный куб. Механические свойства чистой меди после отжига: σв = 220—240 МН/м2, НВ 45 МН/м2, δ= 50%, ψ = 75%. В чистом виде медь применяют для электротехнических целей (провода, шины, кабель). Согласно ГОСТ 854—66 имеется 10 марок технической меди (М00, М0, Ml, M1P, М2, М2Р, МЗ, МЗР, М4).
Основные примеси меди Bi, As, Pb, Sb, Fe, Ni, S, 02; суммарное количество их в марке М00 допускается 0,01%, а в марке М4 — 1%. Более 50% чистой меди потребляет электротехническая промышленность и энергетика. Сплавы меди сцинком — латуни и сплавы меди с другими элементами — бронзы широко применяют в технике в качестве конструкционных материалов.
Применяют латуни с содержанием цинка до 45%; максимальной прочностью обладают латуни, содержащие 42—45% Zn, а наибольшей
пластичностью — латуни с 30—32% Zn. Сплавы, содержащие до 10% цинка, называют томпаками, а от 10 до 20% Zn — полутомпаками. В технике применяют деформируемые и литейные, латуни.
С увеличением содержания цинка (рис. 57) прочность и пластичность латуни сначала повышаются, а затем уменьшаются. При содержании до 39% Zn латунь состоит из одной α-фазы. С увеличением содержания цинка до 46% возникает вторая фаза β, представляющая твердый раствор CuZn. Эта фаза является твердой и хрупкой структурной составляющей. Широкое применение получили α-латуни, содержащие до 39% Zn и обладающие высокой прочностью. Эти латуни можно обрабатывать давлением в холодном состоянии. Пластичность нагартованного сплава восстанавливают рекристаллизационным отжигом при температуре 600—700°С с последующим охлаждением на воздухе. Широко применяют также латуни, содержащие от 39 до 45% Zn и имеющие структуру α + β твердые растворы. К латуням относят также томпак, содержащий 90% и более меди (остальное цинк), и много других не только двухкомпонентных, но и более сложных сплавов, содержащих кроме цинка и меди Al, Pb, Мn, Sn и другие элементы. Эти добавки повышают прочность, а также придают латуням специальные свойства. Алюминий и никель, присутствующие в сплаве одновременно, после термической обработки повышают прочность и твердость латуней; олово, никель и марганец увеличивают прочность и коррозийную стойкость латуней, свинец улучшает антифрикционные свойства и обрабатываемость латуней резанием,
но одновременно, при повышенных температурах, сообщает однофазным латуням хрупкость.
Применяют следующий принцип маркировки латуней: буква Л означает латунь, следующие буквы означают легирующие элементы, цифры показывают содержание меди и легирующих элементов. Согласно ГОСТ 15527—70 существует семь марок обыкновенных α-латуней (Л99, Л90, Л85, Л80, Л70, Л68, Л62). Специальные латуни, например ЛА 59—32, содержат 59% Си, 2—3% №, 2% А1, остальное Zn. Согласно этому же ГОСТу существует 18 марок специальных латуней.
Бронзы. Сплавы меди с оловом, алюминием, кремнием, марганцем, свинцом, бериллием называют бронзами. Раньше к бронзам относили сплавы только двойной системы медь — олово. С течением времени разработаны новые сплавы на медной основе, в которых олово частично или полностью заменено другими элементами. Однако название сплавов осталось прежним, так как они по многим физико-механическим свойствам и цвету не отличаются от медно-оловянистых сплавов. В зависимости от введенного элемента бронзы называют оловянистыми, алюминиевыми, кремнистыми, марганцовистыми и т. д.
На рис. 58 представлена левая часть диаграммы состояния системы Сu—Sn, охватывающая бронзы, применяемые в промышленности. Практический интерес представляют сплавы, содержащие до 14% Sn. Они обладают высокими механическими и антифрикционными свойствами. Сплавы, содержащие до 14% Sn, при медленном охлаждении однофазны, состоят из однородного твердого раствора олова в меди (α-фаза). При содержании более 14% Sn(до22%) бронза становится двухфазной (а + β-фаза). Оловянистые бронзы разделяют на две группы: обрабатываемые давлением (до 6% Sn) и литейные (до 15% Sn). Бронзы, подвергаемые обработке давлением, идут на приготовление прутков, лент, полос, проволоки, трубок и т. д. Литейные оловянистые бронзы применяют для получения различных фасонных литых деталей. Дефицитность и высокая стоимость олова — основной недостаток оловянистых бронз.
Безоловянистые, или специальные, бронзы в ряде случаев имеют более высокие механические и физические свойства.
Бронзы маркируют следующим образом: буквы Бр означают бронзу, следующие буквы означают легирующий элемент (О — олово, Ц — цинк, Ф — фосфор, Б — бериллий, Н — никель, А—-алюминий, Ж — железо, К — кремний, Мц — марганец, С — свинец), цифры показывают содержание элементов в сплаве. Так, бронза марки БрОФ-10-1 имеет следующий химический состав: 10% Sn, 1,02% Р, остальное медь.
Алюминиевые бронзы, содержащие от 4 до 11,5% А1, обладают высокими механическими свойствами и высокой коррозийной устойчивостью, значительно превосходящей устойчивость оловянистой бронзы и латуни.
Алюминиевые бронзы БрА5 и БрА6 обладают хорошими пластическими свойствами; из них изготовляют прутки, проволоку, ленты и листы. Они также имеют хорошие литейные свойства. Буква «Л» в конце марки показывает, что бронза литейная.
Алюминиевые бронзы упрочняют термической обработкой, состоящей из закалки с температуры 850—900° С и последующего отпуска при температуре 400—600° С.
Алюминиевожелезомарганцевые бронзы (БрАЖМц 10-3-1,5 и БрАМц 9-2Л) применяют в качестве литейных и деформируемых сплавов.
Алюминиевые бронзы с добавкой железа и никеля (БрАЖН 10-4-4, БрАЖН 10-4-4Л и БрАЖН 11-6-6) являются сложными сплавами на медной основе, которые пригодны для обработки давлением (ковки и штамповки) и для фасонного литья.
Коемнистые бронзы, содержащие 0,6—0,8% Sn и небольшое количество Ni и Мn, удачно сочетают механические, антифрикционные антикоррозийные свойства. Они успешно поддаются обработке давлением в горячем состоянии и литью (БрКМц 3-1, БрКН 1-3).
Свинцовистые бронзы (БрСЗО, БрСН 60-2,5) содержат 27-63% Рb. Они обладают весьма высокими антифрикционными свойствами и применяются для изготовления деталей, работающих в условиях трения и скольжения, а также для заливки стальных вкладышей высоконагруженных подшипников.
Бериллиевые бронзы (1,6—2,2 Be) отличаются высокой прочностью и коррозийной устойчивостью, хорошими пластическими и антифрикционными свойствами. Одновременно они обладают высокой электро- и теплопроводностью. Растворимость бериллия в меди при 860° С составляет 2,8%, а с понижением температуры до комнатной уменьшается до 0,2%. Это позволяет проводить термическую обработку, состоящую из закалки с 800° С и искусственного старения в течение 9 ч при температуре 250—350° С. Такая обработка повышает прочность и твердость. Бериллиевая бронза хорошо поддается горячей обработке давлением, сварке, резанию. Ее применяют для изготовления мембран, пружин, электроконтактов, часовых механизмов и других пружинящих деталей.
Титан и его сплавы
Титан — самый «молодой» из крупных конструкционных металлов, хотя был открыт в 1795 г. Содержание его в земной коре 0,6%. Титан — переходный металл IV группы, порядковый номер 22, плотность 4510 кг/м3. Температура плавления 1800° С, кипения 3400° С; твердость НВ 850 МН/м2 и σв = 320 МН/м2.
Титан существует в двух модификациях: до 882° С в виде α-титана с гексагональной плотно упакованной кристаллической решеткой и при температуре выше 882° С β-титан с кубической объемно-центрированной решеткой.
Чистый титан пластичен, мягок; технический — хрупкий и твердый. Механические свойства титана резко изменяются в зависимости от содержания примесей (N2, H2, 02, С). В промышленности применяют титан двух марок ВТ1-1 и ВТ 1-2 (табл. 7).
Таблица 7
Состав и механические свойства технического титана (ГОСТ 9855—61)
Примеси, % | Механические свойства | |||
Марка титана | σв МН/м2 | δ, % | нв, МН/м2 | |
ВТ1-1 ВТ1-2 | 0,1 %С; 0,15%О2; 0,04o/0N2; 0,3o/0H2 0,15%Si; 0,015%Н2 | 450—600 550—750 | 25-30 20—25 | 500 450 |
Азот и кислород резко снижают пластичность титана; водород вызывает повышенную чувствительность к надрезу. Такое явление называют водородной хрупкостью. При содержании в титане более 0,15% С ухудшается его ковкость и свариваемость и затрудняется обработка резанием. Образующиеся на поверхности титана оксидные пленки (TiO2, ТiO3 и др.) обладают высокой коррозийной стойкостью в пресной и морской воде, в атмосфере и различных кислотах.
При нагреве до температуры 400° С титан почти не изменяет свои механические свойства, при дальнейшем нагреве эти свойства постепенно ухудшаются, но особенно после 540° С (из-за энергичного поглощения кислорода титан становится хрупким). С увеличением степени холодной деформации прочностные свойства титана улучшаются, а пластичность снижается. Вследствие недостаточной прочности чистый титан имеет ограниченное применение. Сплавы титана представляют значительный интерес.
Сплавы на титановой основе применяют широко. Известно 30 марок титана. Наиболее важные легирующие элементы Al, Cr, Fe, Mn, Mo, Sn, V. Сплавы титана разделяются на пять групп: 1) свариваемые конструкционные; 2) высокопрочные; 3) жаропрочные; 4) для фасонного литья; 5) сплавы со специальными свойствами.
Титановые сплавы подразделяются на три структурные группы: с α-, (α + β)- и β-структурой.
Сплавы с α-структурой имеют при комнатной температуре однофазную структуру α-твердого раствора, термически обрабатываются, малопластичны.
Двухфазные сплавы с (α + β-структурой имеют при комнатной температуре структуру α- и β-твердых растворов, термически обрабатываются, пластичны, обладают высокими механическими свойствами.
Сплавы с β-структурой сохраняют структуру β-твердого раствора, не подвергаются термической обработке, пластичны, малопрочны и не находят сколько-нибудь широкого применения в технике.
Титановые сплавы обладают высокой удельной прочностью, характеризуемой отношением предела прочности к плотностиσ в/γ =20—28. В настоящее время имеется несколько марок высокопрочных титановых сплавов: ВТ6, ВТ14, ВТЗ-1, ВТ15 и ВТ16.
Обычно промышленные титановые сплавы содержат несколько легирующих элементов, но обязательным компонентом является алюминий, повышающий жаропрочность и улучшающий свариваемость.
Таблица 8
Химический состав и механические свойства титановых сплавов (ГОСТ 5632—68)
Состав, % | σв | ||||
Марка | А1 | другие элементы | МН/м2 | кгс/мм2 | δ, % |
ВТЗ ВТЗ-1 ВТ4 ВТ5 ВТ6 ВТ8 | 4—6,2 4—6,2 4-5 4-5,5 5-6,5 5,8—6,8 | 2Сг 1,5-2,5Сг 1-2,8Мо 1—2Мn 3,5-4,5V 2,8—3,8Мо | 932—1128 932—1177 785-883 785—972 833—980 1030—1155 | 93—112 93-117 78—88 79—97 83—98 103—116 | 10-16 10-16 15-22 12—15 8—13 9—15 |
Примечание: Высокой прочностью обладают однофазные α-сплавы ТЗ, Т4, Т6, Т9, Т10. Все сплавы, кроме ВТ4 и ВТ5, имеют двухфазную структуру.
Для повышения прочностных свойств целесообразно некоторые марки титановых сплавов термически обрабатывать; нагревать до 700— 950° С, закаливать в воде и искусственно старить при 480—550° С. Сочетание высоких прочностных свойств при малой плотности, высокой коррозийной стойкости и жаропрочности позволили применять титан и его сплавы в качестве конструкционного материала в реактивной технике, в космических кораблях, самолетостроении.
Данные о составе и свойствах сплавов титана приведены в табл. 8.
Дата добавления: 2022-01-22; просмотров: 57; Мы поможем в написании вашей работы! |
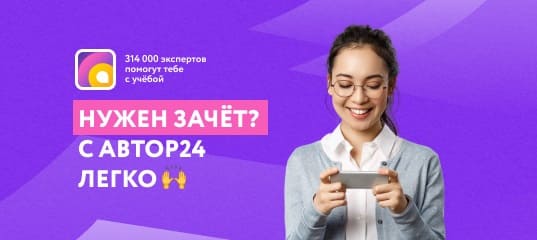
Мы поможем в написании ваших работ!