Классификация видов термообработки деталей из литейных алюминиевых сплавов
Урок № 17-18
Свойства, маркировка, применение меди, алюминия, титана, магния, и их сплавов.
Алюминий и сплавы на основе алюминия
Алюминий — металл серебристо-белого цвета, трехвалентен, находится в II группе периодической системы элементов, порядковый номер 13. Его атомный радиус 1,43А; имеет гранецентрированную кристаллическую решетку с параметром от 4,041 до 4,047А, изменяющимся в зависимости от чистоты алюминия. Плотность алюминия в зависимости от температуры имеет следующие значения:
Температура, 0С ........ 20 100 400
Плотность, кг/м3 ......... 2703 2690 2620
В зависимости от чистоты температура плавления алюминия колеблется от 667 до 660° С. Чистый алюминий обладает высокой пластичностью (δ≈40%), небольшой прочностью (σв≈80 МН/м2(МПа), высокой электропроводностью, относительно высокой теплопроводностью, теплоемкостью и коррозионной стойкостью на воздухе. В зависимости от содержания примесей чистый алюминий по ГОСТ 11069—64 подразделяется на особо чистый А999 (99,999% Аl) и высокой чистоты А99, А995, А97, А95 и технически чистый А85, А8, А7, А6, А5 и т. д. Примеси значительно снижают электропроводность, теплопроводность и пластические свойства алюминия.
Низкий предел прочности чистого алюминия сильно ограничивает область его применения. В качестве конструкционных материалов промышленность широко применяет сплавы алюминия с другими металлами и неметаллами, сочетающие в себе лучшие свойства чистого алюминия и повышенные прочностные характеристики добавок. За последние годы в технике нашли применение многокомпонентные легированные сплавы на основе алюминия, которые по своим прочностным и другим свойствам конкурируют с традиционными сплавами на основе железа и других металлов.
|
|
Все сплавы на основе алюминия подразделяются на два класса — деформируемые и литейные.
Деформируемые алюминиевые сплавы. В зависимости от химического состава деформируемые сплавы можно разделить на следующие семь групп: сплавы на основе системы А1—Мn (АМц); сплавы на основе системы А1—Mg—Si (АД31, ДДЗЗ, АД35, АВ); сплавы на основе системы А1—Сu—Mg (Д1, Д16, В65, ВД17, Д18, Д19); сплавы на основе системы А1—Mg—Мn (АМН, АМг2, АМгЗ, АМг5, АМг6); сплавы на основе системы А1—Mg—Zn—Сu (В93, В94, В95, В96); сплавы на основе системы А1—Сu—Mg—Ni—Fe (AK2, АК4, АК4-1); сплавы на основе системы А1—Si—Mg—Сu (АК6—АК8).
Алюминиевые деформируемые сплавы разделяются на сплавы, упрочняемые и неупрочняемые термической обработкой.
Деформируемые алюминиевые сплавы, подвергаемые механической и термической обработке, имеют специальные буквенные обозначения, указывающие характер этой обработки; М (мягкий) — отожженный; Н — нагартованный, Т — термически обработанный (после закалки и естественного старения), Т1 —, после закалки и искусственного старения ТН — нагартованный после закалки и естественного старения, ТНВ — нагартованный после закалки и естественного старения с повышенным качеством выкатки, О — отожженные листы с повышенной выкаткой, А — плакированные листы, Б — без плакировки (листы), УП — утолщенная плакировка, Р — сплав для заклепок. По новому ГОСТу принята единая цифровая маркировка.
|
|
Обработкой давлением в холодном или горячем состоянии из этих сплавов изготавливают трубы, уголки, тавры, плиты, листы и т. д.
Высокопластичные термически неупрочняемые сплавы разделяют на «мягкие» (АД, АДО, АД1, АМц, АМг, АМг2) и «твердые» (АМгЗ, АМгб, АМг6). Содержание магния в этих сплавах
колеблется от 2 до 7%, а марганца 1,0—1,6%. По структуре эти сплавы представляют однородный твердый раствор марганца, магния, меди и других элементов в алюминии. Упрочнение указанных сплавов достигается деформацией в холодном состоянии (наклеп, нагартовка).
В строительстве и мостостроении термически неупрочняемые алюминиевые сплавы применяют для несущих сварных конструкций (фермы, арки, балки и т. д.), малонагруженных и ненагруженных элементов конструкций здания (кровельные настилы, стеновые панели, дверные и оконные переплеты, арматурные детали).
|
|
В строительстве применяют сплавы АМг6М (5,8—6,8% Mg, 0,5— 0,8% Мп, 0,02—0,1 % Ti), АМг5 (4,7—5,7% Mg, 0,2—0,6% Мп), АМгЗМ (3,2—3,8% Mg, 0,3—0,6% Мп, 0,5—0,8% Si), АМг5ВМ (4,8—5,5% Mg, 0,3—0,6% Мп, 0,02% V). Все эти сплавы обладают высокой коррозийной стойкостью.
Сплав марки АМг6 в состоянии поставки (АМг6М) обладает следующими механическими свойствами: σв = 320 МН/м2 (МПа); НВ 800 МН/м2 (МПа), δ =20%. Прочность этого сплава по сравнению со сталью марки СтЗ в 1,9 раза больше; по сравнению с легированной сталью марки 15ХСНД — в 1,38, а марки 10ХСНД — в 1,17 раза.
Сплав высокой прочности АМг4ВМ (σв = 280 МН/м2 (МПа), 5 =15%) применяют для сварных ответственных конструкций.
Деформируемые сплавы, упрочняемые термической обработкой. Сплавы этой подгруппы приобретают высокие механические свойства и хорошую сопротивляемость коррозии только в результате термической обработки. Эти сплавы делят на авиали (АВ, АД31, АДЗЗ), дуралюмин (Д1,Д16, АК6, АК8), сплавы высокой прочности (В96, В95) и специальные сплавы, работающие при повышенных температурах — жаропрочные (АК4, АК4-1, ВД17). Термическая обработка заключается в закалке и последующем старении. Изменение структуры можно проследить по диаграмме состояния системы А1—Сu (рис. 55). Выбор температуры закалки определяется левой частью этой диаграммы. При обычной температуре содержание Си составляет 0,5%; с возрастанием температуры растворимость меди в алюминии увеличивается при эвтектической температуре (5489С).
|
|
Из диаграммы видно, что алюминий с медью образует ограниченные твердые растворы различной концентрации (в зависимости от температуры) и химическое соединение СuА12. Сплавы А1—Сu, содержащие до 0,5% Сu, после медленного охлаждения имеют однофазную структуру α-раствора меди в алюминии; при содержании 0,5— 5,7% Сu — двухфазный α-раствор +СuА12. Если этот двухфазный сплав нагреть до температуры выше линии предельной растворимости меди в алюминии, то химическое соединение СuА12 растворится в алюминии и сплав станет однофазным. Это обстоятельство используется при закалке А1—Сu сплавов. При быстром охлаждении примерно с температуры 550° С СuА12 не успевает выделиться из α -твердого раствора и последний зафиксируется в неустойчивом метастабильном состоянии. Этот пересыщенный твердый раствор сохраняется, как правило, около 30 мин {инкубационный период) и в дальнейшем распадаетсz с выделением соединения CuAI2. Происходит процесс старения. После старения прочность и твердость увеличиваются. Во время инкубационного периода можно осуществлять пластическую деформацию. По окончании этого периода производить ковку, гибку, отбортовку невозможно.
Естественное старение протекает при комнатной температуре и заканчивается через 4—7 суток. При искусственном старении этот процесс протекает при температуре 150—180° С с выдержкой 2—3 ч.
Выделившиеся дисперсные частицы (Θ-фаза) не отличаются по химсоставу от СuА12 и вызывают упрочнение сплава; так, например, если алюминиевомедный сплав после отжига имеет предел прочности разрыву σв=200 МН/м2 (МПа), и свежезакаленный сплав 250 МН/м2 (МПа), то после старения прочность повышается до 400 МН/м2 (МПа).
Если сплав после естественного старения подвергнуть кратковременному нагреву при 150—250° С, то он вновь приобретает свойства свежезакаленного сплава (явление
возврата). Это широко используют на практике при выполнении различных технологических операций, связанных с пластической деформацией.
С течением времени сплав, обработанный на «возврат», вновь подвергается естественному старению.
К сплавам низкой прочности σв < 300 МН/м2 (МПа) относятся марки AMrl, АМг2, АМгЗ, АМг4,АМг5. Они обладают хорошей коррозийной стойкостью. Средней прочностью σв = 300 до 450 МН/м2 (МПа) обладают ковочные сплавы АК4, АК6, АК8, а также дуралюмин Д1, Д16, Д19 и др. Их применяют после закалки и искусственного или естественного старения. Холодная пластическая деформация со степенью обжатия 5—10% повышает прочностные свойства дуралюмина. Сплавы высокой прочности (σв>450 МН/м2) типа В93, В95 применяют после закалки и искусственного старения.
Литейные алюминиевые сплавы находят в промышленности широкое применение. ГОСТ 2685—63 предусматривает более 35 марок литейных алюминиевых сплавов, которые можно разделить на шесть основных групп (по химическому составу):
На основе системы А1—Si (силумины): АЛ2, АЛЗ, АЛ4, АЛ5, АЛ6, АЛ9, АЛ4М, ВАЛ5 и др.; А1—Mg: АЛ8, АЛ13, АЛ22, АЛ23, АЛ23-1,
АЛ27, АЛ27-1, АЛ28, АЛ29 и др.; А1—Сu: АЛ7; АЛ19; А1—Zn: АЛИ,j АЛ24; поршневые: АЛ10В, АЛ25, АЛ26, АЛЗО; жаропрочные: АЛ1, АЛ20, АЛ21, ВАЛ1, АЦР-1 и др.
Химический состав некоторых из этих сплавов представлен в табл. 3.
Таблица 3
Химический состав некоторых литейных алюминиевых сплавов (ГОСТ 2685—63)
Химический состав. % А1—основа | ||||||
Марка сплава | Mg | Si | Мn | Сu | Ti | Прочие элементы |
АЛ2 АЛ4 АЛ9 | 0,17—0,3 0,2—0,4 | 10,0—13,0 8,0—10,5 6,0—8,0 | 0,2—0,5 | |||
АЛ7 АЛ9 | — | — | 0,6—1,0 | 4,0—5,0 4,5—5,8 | 0,15—0,35 | |
АЛ27 АЛ13 АЛ22 АЛ23 АЛ 28 АЛЗ АЛ6 АЛ10В АЛ15В АЛ1 АЛИ АЛ18 АЛ20 АЛ24 АЛ26 АЛЗО | 9,5—11,5 4,5-5,5 10,5—13,0 6,0—7,0 4,8—6,3 0.35—0,6 0,2—0,5 1,25—1,75 0,1—0,3 0,7—1,2 1,5—2,0 0,4—0,7 0,8-1,3 | 0,8—1,3 0,8—1,2 4,5-5,5 4,5—6,0 4,5—6,5 3,0—5,0 6,0—8,0 1,5-2,5 1,5—2,0 20,0—22,0 11,0-13,0 | 0,1—0,4 0,4—1,0 0,6—0,9 0,2—0,6 0,3—0,8 0,15—0,3 0,2-0,5 0,4—0,8 | 1,5-3,0 2,0—3,0 6,0-8,0 3,5-5,0 3,75—4,0 7,5-9,0 3,5-4,5 1,5 2,5 0,8 1,5 | 0,05—0,15 0,05—0,15 0,05—0,15 0,05—0,15 0,05—0,1 0,1—0,2 | 0,05-0,1 Sb 0,05—0,20 Zr 0,03—0,07 Be 0,05—0,20 Zr 0,02—0,1 Be 1,75—2,25 Ni 7,0—12,0 Zn 1,0—1,8 Fe 1,2-1,7 Fe 3,5—4,5 Zn 0,1—0,4 Cr 1,0—2,0 Ni 0,8 Ni 0,8—1,3 Ni |
В зависимости от условий работы детали и химического состава сплава выбирают тот или иной вид термической обработки. Классификация этих видов в зависимости от назначения детали приведена втабл. 4.
Сплавы на основе системы Al—Si (силумины) (рис. 56) обладают хорошими литейными и достаточно высокими механическими свойствами: высокой жидкотекучестью (от 350 до 420 мм при 700° С), небольшой литейной усадкой, малой склонностью к образованию горячих трещин, хорошим отпечатком по полости формы, достаточно высокой
Таблица 4
Классификация видов термообработки деталей из литейных алюминиевых сплавов
Вид термической обработки и его обозначение | Назначение |
Искусственное старение без закалки Т1 | Улучшение обрабатываемости резанием для повышения чистоты поверхности. Повышение механической прочности (до 20%) деталей из сплавов АЛЗ, АЛ5 и др. |
Отжиг Т2 | Снятие литейных и термических напряжений, а также наклепа. Повышение пластичности сплава |
Закалка Т4 | Повышение прочностных характеристик и коррозийной стойкости деталей, работающих при температурах до 100°С |
Закалка+неполное искусственное старение Т5 | Получение высокого предела прочности при сохранении хорошей пластичности |
Закалка+полное искусственное старение Т6 | Получение максимальной прочности при некотором снижении пластичности |
Ззкалка+стабилизирующий отпуск Т7 | Получение достаточно высокой прочности и высоких стабильных свойств по структуре и объемным изменениям |
Закалка +смягчающий отпуск Т8 | Получение повышенной пластичности и стабильных размеров при некотором снижении прочностных характеристик |
прочностью и удовлетворительной пластичностью (от 2,5 до 8%). Механические свойства и режимы термической обработки некоторых сплавов этой группы приведены в табл. 5
Таблица 5
Дата добавления: 2022-01-22; просмотров: 29; Мы поможем в написании вашей работы! |
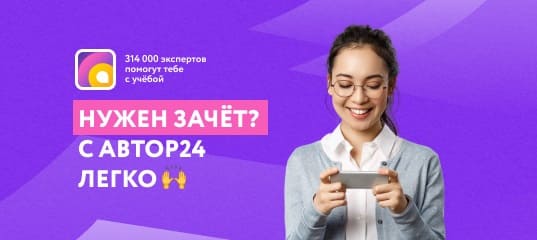
Мы поможем в написании ваших работ!