Тема 3.5. Обработка фасонных поверхностей.
Фасонные поверхности встречаются в конструкции деталей различного назначения и относительно широкой номенклатуры. В отличие от классических форм поверхностей — цилиндрических, конических, плоских — границы, определяющие фасонные поверхности, выражены менее четко. К фасонным относят поверхности, отличающиеся от упомянутых классических. К этому классу поверхностей относятся также резьбовые, зубчатые, шлицевые поверхности, рассматриваемые в отдельных разделах.
Классификация фасонных поверхностей предусматривает следующие три класса:
I — поверхности тел вращения с криволинейной образующей;
II — поверхности сложной формы с прямолинейной образующей;
III — пространственные фасонные поверхности.
Каждый класс включает две группы поверхностей: наружные и внутренние.
Технические требования, предъявляемые к фасонным поверхностям, включают те же показатели, что и для других поверхностей: точность, шероховатость, физико-механические и, в ряде случаев, оптические и другие свойства.
Детали, имеющие фасонные поверхности, наиболее широко представлены в изделиях авиационной техники, судостроении, инструментальном производстве, медицинской технике и инструментах, энергетическом оборудовании и др.
Общий арсенал методов обработки фасонных поверхностей различного класса включает обработку фасонным инструментом, обработку по разметке (в том числе с применением слесарно-механической обработки), обработку по копирам и шаблонам, обработку на копировальных станках, на станках с программным управлением, электрическую, электроэрозионную размерную обработку, безразмерную обработку мягкими инструментами .и в среде свободного абразива и других твердых тел. Ниже рассматриваются методы обработки фасонных поверхностей упомянутых классов.
|
|
Поверхности деталей (как наружные, так и внутренние) относят к фасонным, если они образованы криволинейной образующей, комбинацией прямолинейных образующих, расположенных под различными углами к оси детали, или комбинацией криволинейных и прямолинейных образующих.
На токарных станках фасонные поверхности получают:
· ручным или автоматическим поперечным и продольным движением подачи резца относительно заготовки с подгонкой профиля обрабатываемой поверхности по шаблону;
· фасонными резцами, профиль которых соответствует профилю обработанной детали;
· с помощью приспособлений и копирных устройств, позволяющих обработать поверхность заданного профиля;
· комбинированием перечисленных выше методов.
Фасонные поверхности на длинных деталях, заданный профиль которых получается с помощью шаблона, копира и приспособлений, обрабатывают проходными резцами из быстрорежущей стали или твердого сплава.
|
|
При обработке галтелей и канавок радиусом R < 20 мм на стальных и чугунных деталях применяют резцы, режущая часть которых выполнена по профилю обрабатываемой галтели или канавки.
Для обработки галтелей и канавок радиусом R >20 мм режущую часть резцов выполняют с радиусом скругления, равным (1,5... 2)R. При этом используют как продольное, так и поперечное перемещение суппорта.
Для повышения производительности обработки фасонных поверхностей сложного профиля применяют фасонные резцы (рис. 4.39). Ширина фасонных резцов не превышает 60 мм и зависит от жесткости системы станок—приспособление — инструмент— обрабатываемая деталь (СИД) и радиального усилия резания.
Обработка проходными резцами
При небольшой партии заготовок и соответствующей подготовке рабочего фасонную поверхность можно обрабатывать проходным резцом при его одновременном продольном и поперечном движении, осуществляемом вручную.
При выборе резца форма его вершины и расположение режущих кромок должны позволить обработать фасонную поверхность с заданными углами наклона и радиусами.
|
|
Для приобретения навыка одновременного продольного и поперечного перемещения резца по заданной траектории следует предварительно (перед обработкой фасонной детали) выполнить несколько упражнений, что позволит освоиться с особенностями управления станком при фасонной обработке. Для этого в патроне или в центрах устанавливают готовую деталь с фасонной поверхностью сложного профиля. Перемещая суппорт координированным вращением его рукояток, следят за тем, чтобы вершина резца перемещалась в непосредственной близости (с одинаковым зазором до 1 мм) от поверхности детали.
Убедившись в надежности управления станком, переходят к обработке детали с фасонной поверхностью. На рис. 4.40, а показана последовательность обработки описанным способом фасонной поверхности заготовки рукоятки. Заготовку закрепляют в трех-кулачковом патроне, используя для этого поверхность А (рис. 4.40, б), и обрабатывают проходным резцом хвостовую часть рукоятки, состоящую из поверхностей В, С, D, и Е. Установив рукоятку в патроне по поверхности G (рис. 4.40, в), обрабатывают фасонную часть рукоятки. С помощью шкалы на станине станка производят разметку (вдоль оси заготовки) наибольшего и наименьшего диаметров фасонной поверхности рукоятки, а затем проходным резцом снимают черновой припуск в несколько проходов (см. заштрихованные участки на рис. 4.40, в).
|
|
Окончательный съем припуска (рис. 4.40, г) выполняют в несколько проходов. Вначале аккуратно снимают гребешки плавным перемещением резца вдоль оси обрабатываемой детали и возвратно-поступательным перемещением поперечных салазок суппорта. Затем к невращающейся заготовке прикладывают шаблон с профилем готовой детали, измеряют наибольший и наименьший диаметры фасонной поверхности и определяют места, с которых необходимо снять припуск. Для облегчения условий труда и повышения его производительности опытные рабочие используют автоматическую продольную подачу, перемещая вручную только поперечный суппорт.
Для повышения производительности и точности обработки фасонных поверхностей проходным резцом применяют копир (рис. 4.41). Фасонную поверхность рукоятки 2 обрабатывают резцом 7, поперечное перемещение которого осуществляется по копиру 5 пальцем 4 в соответствии с его профилем. Вместе с пальцем 4 в поперечном направлении перемещается тяга 3 и связанный с ней суппорт с резцовой головкой. При этом винт поперечного движения подачи выводится из зацепления с гайкой поперечного суппорта, а движение продольной подачи может осуществляться автоматически.
Обработка на токарном станке фасонных поверхностей по копиру по существу не отличается от обработки конических поверхностей с помощью конусной линейки. Необходимо лишь заменить конусную линейку линейкой с криволинейным очертанием (рис. 177), называемой копиром.
Если разъединить нижнюю суппорта с винтом поперечной подачи и затем сообщить каретке продольное перемещение, то резец получит от копира наряду с продольным также и поперечное перемещение. При этом резец, образующая которой будет соответствовать профилю копира. Такой способ работы называется работой по копиру.
На рис. 177 показано обтачивание фасонной рукоятки 1 при помощи копира 3. Ролик 4, закрепленный в тяге 2, совершает вместе с суппортом продольное движение. При этом он перемещается в криволинейном пазу, образованном двумя пластинами копира, и перемещает в поперечном направлении резец 5. Резец следует за движением ролика и таким образом воспроизводит на детали поверхность, профиль которой соответствует профилю копира.
Иногда фасонные поверхности деталей обтачивают при помощи одностороннего копира. В этом случае прижим ролика к копиру происходит под действием пружины или груза, подвешиваемого на тросе за станиной и перемещаемого вместе с кареткой.
Дата добавления: 2018-02-18; просмотров: 4068; Мы поможем в написании вашей работы! |
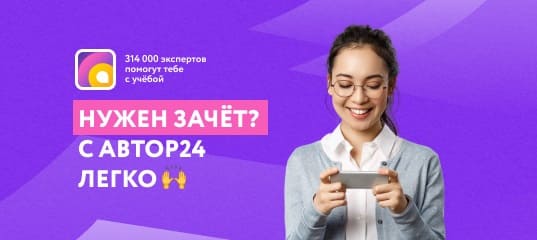
Мы поможем в написании ваших работ!