ОБСЛУЖИВАНИЕ АВТОСЦЕПНОГО УСТРОЙСТВА
ВНЕШНИЕ ПРИЗНАКИ ОБНАРУЖЕНИЯ НЕИСПРАВНОСТЕЙ БУКС С РОЛИКОВЫМИ ПОДШИПНИКАМИ
Опыт показывает, что каждая неисправность роликовой буксы сопровождается наличием определенных внешних признаков на ходовых частях вагона.
На разрушение упорного бурта или сепаратора заднего подшипника указывают грение буксы и перемещение ее вдоль шейки оси колесной пары, слышится резкий стук рычажной передачи;на центре колеса, на полу вагона и на рычажной передаче видны следы буксовой смазки, а в тележках пассажирских вагонов, кроме того, частые вертикальные колебания буксового рессорного подвешивания вызывают сильную тряску рамы тележки. Перемещение буксы вдоль шейки оси колесной пары может указывать также на разрушение торцового крепления подшипников.
О полностью разрушенном сепараторе и выпадении роликов из его гнезд свидетельствуют вибрация тележки, подпрыгивание буксы, сопровождаемое характерным пощелкиванием, которое можно легко услышать при скорости движения поезда 5—8 км/ч, а в пассажирских и рефрижераторных вагонах возникает еще излом буксовой пружины. На разрушение сепаратора указывает и наличие в смазке, выделяемой через лабиринтное уплотнение и в местах соединения - крепительной или смотровой крышек буксы, бронзового порошка, который легко обнаружить при растирании смазки на ладони.
Если колесная пара при отжатых тормозных колодках идет юзом, то это является признаком разрушения подшипника и заклинивания роликов. Обстукиванием нижней части смотровой или крепительной крышки можно обнаружить расстройство торцового крепления буксы. Слышимые при этом дребезжащие звуки или двойные удары свидетельствуют об изломе стопорной планки или обрыве крепящих болтов. Сдвиг буксы в наружную сторону (определяется по увеличенному более 1,5 мм зазору между корпусом буксы и лабиринтным кольцом) свидетельствует о сворачивании осевой гайки с шейки оси. Если гайка отвернулась до упора в смотровую крышку, то на крышке видны трещины, протертости, пробоины, следы цветов побежалости в виде кольца, а при движе-
|
|
нии поезда может быть слышен скрежет от трения осевой гайки о крышку.
Любая из перечисленных неисправностей чаще всего сопровождается грением буксы. Поэтому при осмотре роликовой буксы обя-, зательно следует контролировать температуру ее нагрева путем ощупывания корпуса буксы рукой. Нагрев считается нормальным, если температура корпуса не превышает 70 °С (плотно прижатая к буксе рука легко выдерживает такую температуру) и во всех буксах одинакова.
Причиной грения может быть также излишнее количество смазки в буксе или ее недостаток. В первом случае смазка вытекает из лабиринта, а во втором при встрече поезда сходу слышно своеобразное шуршание, вызываемое сухой перекаткой роликов по беговым дорожкам наружных и внутренних колец подшипников. К увеличенному нагреву корпуса буксы в задней части приводит и отсутствие зазора между лабиринтами буксы и кольца.
|
|
При шелушении краски на корпусе буксы, отсутствии в зимний период на одной из букс вагона инея, снега или льда, наличии неравномерного проката, ползунов, наваров и других дефектов колёс, вызывающих увеличенные динамические нагрузки, осмотр букс с роликовыми подшипниками необходимо произвести особенно внимательно.
В случае обнаружения чрезмерно нагретой роликовой буксы или с неисправностями, которые при дальнейшем следовании могут привести к грению, вагон должен быть отцеплен и подан в ремонт для смены колесной пары. Исключением является грение буксы по причине излишнего количества смазки в ней. В этом случае грение не является опасным и обычно после пробега вагона 500—600 км прекращается. Грение из-за обильного количества смазки в роликовой буксе возможно лишь после полной или промежуточной ревизии ее, на что могут указывать свежие трафареты о недавних (день-два назад) плановом ремонте вагона, технической ревизии или подкатке новой колесной пары. Однако в этих случаях к установлению причины грения следует подходить осторожно, так как увеличенный нагрев может быть также и следствием неисправности роликовой буксы.
|
|
При остановке поезда по причине грения роликовой буксы вагона в пути следования необходимо тщательно осмотреть ее и, если букса не имеет следов сползания с шейки оси, а колесная пара свободно вращается, следовать дальше- до ближайшей станции со скоростью не свыше 15 км/ч с остановками через каждые 5—6 км для осмотра состояния буксы. Тормоз вагона следует выключить. Если будет замечено сползание буксы с шейки оси, то дальнейшее следование поезда возможно только при сопровождении осмотрщиком вагонов, который обязан непрерывно следить за греющейся буксой, находясь на подножке или идя по обочине рядом с аварийным вагоном. Скорость поезда в этом случае не должна превышать 5—7 км/ч. Заметив увеличение сползания буксы или возникновение заклинивания колесной пары, осмотрщик вагонов обязан принять меры к немедленной остановке поезда, а машинист локомотива — доложить поездному диспетчеру о невозможности дальнейшего следования.
|
|
ОБСЛУЖИВАНИЕ КОЛЕСНЫХ ПАР
В зимнее время на колесных парах вагонов возникают различные дефекты в значительно большей степени, чем летом. Поэтому их осмотр в этот период необходимо производить с особой тщательностью.
Неисправности колесных пар обнаруживают при встрече поезда сходу и после его остановки.
Во время осмотра поезда на ходу легко выявляются такие дефекты, как ползуны (выбоины), навары, неравномерный прокат. Наличие на поверхности катания ползунов и наваров вызывает через равные промежутки времени характерные удары колеса о рельсы. Стук повторяется при каждом обороте колесной пары и слышен чаще, чем от ударов колес на стыках. Если имеется неравномерный прокат, то во время движения наблюдаются биение такой колесной .пары и, как следствие, увеличенные и более частые колебания рессорных комплектов. Кроме того, этот вид неисправности сопровождается ударами деталей рычажной передачи о другие детали тележки и раму вагона и вибрацией рамы тележки.
Замеченные при встрече на ходу колесные пары с дефектами после остановки поезда должны быть внимательно осмотрены; размеры дефектов необходимо измерить и сравнить с допускаемыми.
О наличии на колесной паре ползунов, наваров и неравномерного проката могут свидетельствовать частично или полностью отвернутые гайки шпинтонов. На неравномерный прокат, кроме того, указывает местное уширение обода колеса. Толщина обода в месте уширения всегда меньше, чем в остальной части, и если обод колеса тонкий (до 30—35 мм), то разница хорошо видна. Эти признаки особенно важны при осмотре поездов в парке отправления и подготовке вагонов к перевозкам.
Осматривая колесные пары после остановки поезда, осмотрщик вагонов обязан убедиться в отсутствии любых размеров трещин в ступице, диске, гребне, ободе колеса, поперечных в оси и раковин. Размеры проката, выщербины, кольцевых выработок на поверхности катания колеса, поверхностного откола наружной грани обода колеса, толщины обода, гребня, продольной трещины на средней части оси и т. д. не должны превышать нормы допуска.
Признаками наличия трещин являются вздутие над ними краски, концентрация инея и скопление пыли или ржавчины в виде валика. Для окончательного выявления трещины место предполагаемого ее расположения следует проверить магнитным щупом, предварительно осторожно удалив иней или вздувшуюся краску. Обнаруженная с его помощью металлическая пыль служит доказательством наличия трещины. В дополнение к проверке магнитным щупом и особенно в случаях, если не обнаружена металлическая пыль, обследуемое место необходимо зачистить металлической щеткой и тщательно осмотреть с помощью лупы.
Производя осмотр колесных пар, осмотрщик вагонов должен также контролировать наличие признаков ослабления и сдвига ступицы колеса на подступичной части оси. Об ослаблении ступицы свидетельствует выступившая ржавчина или масло в месте соединения оси со ступицей, разрыв краски по всему периметру этого соединения. При сдвиге ступицы с внутренней стороны появляется узкая полоска, имеющая цвет, резко отличающийся от цвета средней части оси (если сдвиг наружу), или происходит вспучивание краски вокруг ступицы (если сдвиг внутрь) колесной пары.
Вагоны с колесными парами, имеющими неисправности, выходящие за пределы допуска, от поезда отцепляют.
ОБСЛУЖИВАНИЕ ТЕЛЕЖЕК
В тележках пассажирских вагонов трещины образуются в кронштей нах подвесок тормозных башмаков, сварочных швах над-рессорной балки и рамы тележки, шпинтонах, люлечных подвесках и кронштейнах гидравлических гасителей колебаний. На наличие трещины в этих местах указывает скопление пыли или ржавчины в виде валика, а зимой — концентрация инея. При обнаружении таких признаков место с предполагаемой трещиной должно быть тщательно обследовано с помощью магнитного щупа, металлической щетки, лупы и наборного щупа.
Кроме образования трещин, в тележках возможны износы отдельных деталей до размеров, больших установленных нормой.
Во всех этих случаях осмотрщики вагонов обязаны дать заяв-; ку на отцепку вагона от поезда для подачи в текущий ремонт.
ОБСЛУЖИВАНИЕ АВТОСЦЕПНОГО УСТРОЙСТВА
Автосцепное устройство, как и другие ответственные узлы вагона, в зимние месяцы требует более тщательного наблюдения, так как эксплуатационные условия работы его в этот период усложняются. Работая в режимах постоянно действующих значительных ударно-тяговых сил, узлы и детали автосцепного устройства при низких температурах гораздо чаще выходят из строя, чем при обычных условиях. В зимнее время вследствие попадания внутрь корпуса автосцепки снега и образования льда появляются также дополнительные причины возникновения одной из основных неисправностей автосцепки — саморасцепа. Поэтому выявлению, и.устранению неисправностей автосцепного устройства осмотрщикам вагонов следует уделять повышенное внимание.
Осмотр автосцепного устройства необходимо начинать при встрече прибывающего поезда сходу. При этом легко обнаружить вагоны, имеющие разную высоту осей сцепления автосцепок, с увеличенным расстоянием от упора автосцепки до ударной розетки, с натянутой цепочкой расценочного привода. После остановки поезда осмотр автосцепного устройства следует выполнять в такой последовательности: проверить корпус автосцепки, расцепной привод, центрирующий прибор, положение валика подъемника, а также наличие и исправность сигнального отростка и направляющего зуба замка; замерить расстояние между упором автосцепки и ударной розеткой, которое должно быть от 60 до 100 мм, между хвостовиком автосцепки и потолком ударной розетки, допускаемое не менее 25 и не более 40 мм.
В последнее время строятся вагоны, оборудованные поглощающим пружинно-фрикционным аппаратом типа Ш-2-B повышенной энергоемкости. Отличительной особенностью таких вагонов является ударная розетка, выступающая грань которой выполнена не сферической, а прямолинейной. Допускаемое расстояние между упором автосцепки и ударной розеткой при этом установлено в пределах 120—150 мм. Поглощающие аппараты Ш-2-В можно заменять серийными. Однако установка нового поглощающего аппарата на вагоны с ударной розеткой обычного исполнения не допускается.
Специальным ломиком следует проверить действие предохранителя от саморасцепа сцепленных автосцепок, а в пунктах формирования и оборота пассажирских составов дополнительно проверить износ элементов контура зацепления. Ломик (рис. 1) заостренным концом шириной 20 мм вводят сверху в пространство между ударной стенкой зева одной автосцепки и торцовой поверхностью замка другой. Поворачивая выступающий конец ломика, нажимают заостренным концом на замок. Если он уходит внутрь головы автосцепки на 7—20 мм и при этом слышен четкий металлический звук от удара предохранителя в противовес замкодержателя, значит предохранительное устройство исправно.
Износ элементов контура зацепления в растянутом пассажирском поезде проверяют ломиком-калибром (рис. 2). При этом зазоры а и б (рис. 3) проверяют утолщенной крестообразной частью ломика, имеющей контрольные, размеры (22±0,1) мм для проверки зазора а и )(25±0,1) мм для проверки зазора б. В обоих случаях в соответствующие зазоры ломик проходить не должен.
Если при проверке ломиками будет обнаружена неисправность предохранителя от саморасцепа или износ элементов контура зацепления, то автосцепки необходимо разъединить и проверить шаблонами 873 и 940р.
Для удобства работы при проверке автосцепки многие осмотрщики вагонов делают насечки на ломиках со стороны заостренного конца на расстоянии 60, 100 и 140 мм. Контроль размеров между упором автосцепки и ударной розеткой с помощью таких насечек ускоряет осмотр вагонов.
Неисправности и нарушения в работе автосцепных устройств могут привести к таким явлениям, как саморасцепы, обрывы поездов, потеря эффективности поглощающих аппаратов при действии продольных сил и др.
Причинами саморасцепов автосцепок являются следующие наиболее часто встречаемые неисправности:
- изгиб или излом полочки для верхнего плеча предохранителя от саморасцепа;
- износ, изгиб или излом предохранителя от саморасцепа и противовеса или лапы замкодержателя;
- спадание замкодержателя с шипа и при этом заклинивание замка;
- излом шипа замка для навешивания предохранителя от саморасцепа;
- излом перемычки прорези в замке для нижнего плеча предохранителя от саморасцепа;
- западание подъемника в овальный вырез замка, вследствие чего теряется подвижность замка;
- тонкомерность замка;
- изгиб сигнального отростка замка, в результате чего отросток не имеет свободного прохода через отверстие в дне кармана корпуса автосцепки;
- износ тяговых и ударных поверхностей' большого и малого зубьев;
- уширение зева;
- удары направляющей плоскостью большого зуба одной автосцепки в противовес валика подъемника второй автосцепки при износах по контуру зацепления.
Однако саморасцепы возможны не только из-за неисправности деталей автосцепок, но и вследствие других причин. Так, попадание под замок посторонних предметов, а в зимний период также скопление снега или льда может вызвать,саморасцеп ввиду того, что в процессе сцепления замок не сможет полностью возвратиться в свое нижнее положение и предохранитель от саморасцепа оказывается выключенным.
Повышение допускаемой разницы высот между продольными осями автосцепок (в грузовых поездах эта разница допускается не более 100 мм, а в пассажирских, курсирующих со скоростью до 120 км/ч, — не более 70 мм и со скоростью свыше 120 км/ч — не более 50 мм) может послужить причиной саморасцепа при дви женин поезда на участках пути, имеющих большую просадку или пучины.
В пассажирских вагонах, имеющих повышенную вертикальную динамику, автосцепки должны быть оборудованы специальными ограничителями, препятствующими взаимным вертикальным перемещениям двух сцепленных автосцепок в пути следования поезда.
Обнаруженные при осмотре под головками маятниковых подвесок и на центрирующей балочке под хвостовиком автосцепки различные посторонние предметы необходимо снять, так как наличие их недопустимо не только с точки зрения возможной утери этих предметов в пути следования, но и, что особенно важно, при-
водит к нарушению параллельности продольных осей автосцепок, преждевременному износу и повреждению, отдельных деталей автосцепного устройства. К нарушению соосности автосцепок приводит также провисание автосцепки из-за износа деталей центрирующего прибора.
Кроме названных причин, к саморасцепу может привести выпадание или заедание валика подъемника при его повороте, погнутость державки или расцепного рычага, обрыв крепящих болтов или излом державки и кронштейна рычага, короткая или длинная цепь расцепного привода. Так, короткая цепь при выдвижении автосцепки за счет сжатия поглощающего аппарата, а также при значительных боковых отклонениях корпуса автосцепки на кривых участках пути поворачивает валик подъемника, и происходит выключение предохранителя от саморасцепа. Длинная цепь также может создать условия для саморасцепа автосцепок, поскольку при невнимательном осмотре поезд может быть отправлен с рычагом, установленным в расцепное .положение. В этом случае происходит либо неполное сцепление, либо выключается предохранитель от саморасцепа, как и при короткой цепи.
Наличие трещин в корпусе автосцепки, тяговом хомуте, клине тягового хомута и упорной плите нередко приводит к их излому или обрыву поезда. Характерными признаками наличия трещин в узлах автосцепного устройства являются следы коррозии, образование инея в зимнее время, а в летнее — пылевого валика. Трещины в корпусе автосцепки обычно встречаются в местах перехода головы к хвостовику, в углах ударной поверхности зева ив хвостовике около овального отверстия для клина.
На излом тягового хомута, клина тягового хомута, упорной, плиты, пружины, стяжного болта или корпуса поглощающего аппарата указывает увеличенное или уменьшенное расстояние от упора корпуса автосцепки до ударной розетки. При изломе клина, кроме того, болты, поддерживающие его, имеют изгиб, причем болт, расположенный ближе к передней.балке рамы вагона, изогнут в большей степени, чем другой. На заплечике клина в этом случае появляется блестящий намин, а на тяговом хомуте— крупнозернистая металлическая пыль. При поднятии клина ломиком с резким опусканием слышен звук двойного удара. Изломанная упорная плита имеет вид как бы согнутой, если состав; растянут, если сжат, то видны вмятины в виде полумесяца в местах ее примыкания к нажимному конусу поглощающего аппарата,, а нажимной- конус имеет овальные края.
Во всех случаях, когда обнаружены в деталях и узлах автосцепного устройства недопустимые износы, трещины, изломы и: другие неисправности, такие узлы и детали подлежат немедленной замене. В зависимости от сложности работ по уходу за автосцепкой они могут быть выполнены с отцепкой вагона от поезда или без отцепки.
СПОСОБЫ ВЫЯВЛЕНИЯ И УСТРАНЕНИЯ НЕИСПРАВНОСТЕЙ ТОРМОЗОВ
Автоматические тормоза являются одной из ответственных частей подвижного состава и требуют тщательного ухода. Внимание осмотрщиков к ним особенно зимой должно быть повышено, так как морозы, снегопады и метели ухудшают условия работы автотормозов и их обслуживание затрудняется. В зимний период может происходить замерзание воздухопровода, воздухораспределителей и других тормозных приборов вагона; увеличение утечек воздуха из тормозной магистрали и случаев неисправности воздухораспределителей, обрыва деталей рычажной передачи.
Причиной замерзания тормозных приборов и закупорки воздухопровода является попадание влаги в тормозную магистраль. Попадание снега в головки соединительных рукавов также приводит к образованию ледяных пробок.
Замерзание скопившегося в магистрали конденсата обычно происходит при наличии утечки воздуха, а также в местах изгибов и вмятин на трубах. Одним из признаков закупорки воздухопровода является появление инея или черноты в местах изгиба магистральных труб и в резьбовых соединениях. Если при обстукивании магистрального воздухопровода легкими ударами молотка слышен глухой звук, это указывает на наличие в данном месте ледяной пробки.
Для предупреждения случаев образования пробок и замерзания тормозных приборов осмотрщики обязаны следить за тем, чтобы сжатый воздух, используемый для зарядки тормозной магистрали вагонов, не был влажным. Кроме того, перед соединением рукава тормозной магистрали обязательно следует продуть сжатым воздухом, головки рукавов очистить от загрязнений, льда и снега, а также заменить негодные уплотнительные кольца. Нельзя наносить смазку на кольца. В случае обнаружения в воздухопроводе ледяной пробки это место тщательно обстукивают молотком, а затем производят продувку магистрали сжатым воздухом. Если пробка не устраняется, то разрешается отогреть магистраль паяльной лампой с соблюдением правил пожарной безопасности и снова продуть ее.
Закупорка магистрального воздухопровода может произойти и при постановке на вагон нового концевого крана, если из него вследствие невнимательного отношения исполнителя не будет предварительно удалена хотя бы одна из деревянных пробок, которыми закрывают отверстия крана в целях предотвращения попадания внутрь его песка, грязи, посторонних предметов и т. п. Поэтому запрещается хранить на стеллажах концевые краны без предварительного удаления из них деревянных пробок.
При замерзании соединительные рукава, концевые краны, выпускные клапаны, воздухораспределители и другие приборы тормозного оборудования заменяют исправными. Если в тормозном цилиндре из-за замерзания в нем влаги поршень потерял подвижность, такой цилиндр надо вскрыть, вынуть поршень, очистить рабочую поверхность цилиндра, протереть ее сухой салфеткой и смазать. Негодную манжету следует сменить. После сборки цилиндр должен быть испытан на плотность. Снижение давления при утечке воздуха из тормозного цилиндра с начального давления 0,39 МПа (3,9 кгс/см2) допускается не более 0,01 МПа (0,1 кгс/см2) за 2 минуты.
Утечки воздуха из тормозной магистрали поезда снижают управляемость тормозами в пути следования, так как приводят к замедлению зарядки и отпуска их, преждевременному отпуску, самоторможению. Кроме того, из-за утечек воздуха увеличивается расход топлива или электроэнергии. Причиной возникновения утечек являются неплотности в соединениях воздухопровода и приборов автотормоза. Утечки выявляют при полностью заряженной тормозной сети по наличию ряда признаков: слышен шум выходящего сжатого воздуха, наличие черных мест на белом фоне изморози, скопление инея в местах утечки.
Большое значение для устойчивой работы любого соединения имеет чистая, без повреждений, резьба. Если резьба на трубах неполномерная или с поврежденными витками, то необходимой прочности соединения без замены труб или муфт с такой резьбой добиться невозможно, и в пути следования плотность будет нарушена. Кроме того, осматривая автотормозное оборудование, необходимо следить за креплением к раме вагона воздухопровода и его ответвлений, резервуаров, и тормозных приборов, так как нарушение креплений влечет за собой расстройство соединений. С наступлением морозов прокладки во фланцах тормозных приборов сжимаются и начинают пропускать воздух. Поэтому фланцы при необходимости должны быть укреплены. Крепить болты следует по диагонали равномерным нажатием.
На наличие утечки в соединительном рукаве указывают тонкий' слой его обледенения, небольшие остроконечные ледяные шипы или пузыри. Рукава с такими признаками заменяют.
Слабее крепление головки на трубке соединительного рукава или трубки на штуцере можно обнаружить по следам сдвига или поворачиванием резиновой трубки в местах соединений ее при легком вращении рукава. Такая проверка обычно производится перед соединением рукавов. Для укрепления головки или штуцера необходимо подтянуть хомутик. Если после этого дефект не исчез, то рукав следует заменить.
Величину утечек воздуха в тормозной магистрали поезда характеризует ее плотность. Для проверки плотности тормозной сети в пассажирском поезде после зарядки магистрали состава до давления 0,50—0,52 МПа (5,0—5,2" кгс/см2) необходимо перекрыть комбинированный кран и по истечении 20 с после этого замерить давление в тормозной магистрали. Снижение давления при этом: не должно происходить быстрее чем 0,02 МПа (0,2 кгс/см2) за. 1 мин или 0,05 МПа (0,5 кгс/см2) за 2,5 минуты.
В грузовых поездах проверка плотности осуществляется следующим порядком: после полной зарядки тормозной сети до давления 0,53—0,55 МПа (5,3-—5,5 кгс/см2) и автоматическом отключении компрессоров, при достижении предельного давления в главных резервуарах необходимо после снижения давления от максимального на 0,04—0,05 МПа (0,4—0,5 кгс/см2) замерить время дальнейшего падения давления в главных резервуарах еще на 0,05 МПа (0,5 кгс/см2) и сравнить его с допускаемым, которое определяют по таблицам в зависимости от длины поезда и типа локомотива. Ручка крана машиниста при проверке плотности тормозной сети должна находиться в поездном положении.
Неисправные воздухораспределители и авторежимы выявляют в процессе опробования тормозов. Однако наличие коррозии или грязи на трущейся поверхности колодок указывает, что воздухораспределитель или авторежим не действует. Обгорание смазки на боковых поверхностях тормозной колодки, а также появление на
ней цветов побежалости свидетельствует о затяжном отпуске воздухораспределителя.
В случае обнаружения при опробовании автотормозов воздухораспределителей, не чувствительных к торможению и отпуску, а также с наличием замедленного отпуска необходимо закрепить фланцы, осмотреть и очистить пылеулавливающую сетку, фильтр, после чего проверить действие тормоза вторично. Если эти меры положительного результата не дали, воздухораспределитель необходимо заменить. Производя смену воздухораспределителя, осмотрщик должен убедиться в чистоте прокладки привалочного фланца и в отсутствии прорывов, порезов, забоин и других неисправностей, которые могут вызвать пропуск воздуха. Оборотный запас воздухораспределителей, предназначенный для замены неисправных на вагонах, следует хранить на закрытых стеллажах.
При осмотре автотормозного оборудования необходимо обращать внимание также на состояние рычажной передачи вагонов. Следует иметь в виду, что наиболее опасными неисправностями рычажных передач грузовых вагонов являются те, которые могут привести к падению триангелей и тормозных колодок на путь. Основными причинами падения триангелей являются утеря валиков подвесок тормозных башмаков, обрыв подвесок, отсутствие или нарушение дополнительного коепления со стороны головок валиков, соединяющих вертикальные рычаги с триангелем и распорной тягой, ненадежность предохранительных устройств триангелей. Утеря валиков подвесок тормозных башмаков происходит из-за закрепления их нетиповыми шплинтами без постановки шайб. Обрывы и изломы подвесок тормозных башмаков происходят в основном в углах и в местах перехода к вертикальным ветвям.
Излом подвески башмака в нижней ее части, закрытой колодкой, можно обнаружить, отжимая одну из половин подвески от башмака или нанося по ней легкие удары. Свободное перемещение при этом одной половины подвески относительно другой ее части указывает на наличие излома. Узел дополнительного крепления каждого из нижних валиков вертикальных рычагов (рис. 4) представляет собой две планки 4, приваренные к вертикальному рычагу, через отверстия которых над головкой валика проходит шплинт 5 размером 8Х60 мм. Отсутствие или постановка нетипового шплинта, а также излом хотя бы одной планки не допускаются.
С целью исключения случаев выпадания валика подвески тормозного башмака из-за среза или отсутствия основного шплинта узел крепления подвески при плановых видах ремонта вагонов подвергается модернизации. На валик со стороны его головки между торцом кронштейна боковой рамы и внутренним буртом резиновой втулки подвески башмака устанавливают предохранительную скобу (рис. 5). После монтажа узла подвески в отверстие скобы заводят фиксатор, свободный конец которого загибают на скобу. Фиксатор изготавливают из проволоки диаметром 6 мм, но он может быть заменен шплинтом размером 6Х120 мм.
Осмотрщики по тормозам, контролируя состояние тормозного оборудования вагонов, обязаны следить за наличием и исправностью всех предохранительных устройств от падения: для тяг и горизонтальных рычагов — скоб, для триангелей —угольников в тележках КВЗ, для траверс пассажирских и рефрижераторных вагонов — скоб, изготавливаемых из полосовой стали.
Падение тормозных колодок возможно из-за неправильного их крепления. Увеличенный зазор между нижним концом колодки и башмаком является признаком того, что клин тормозной колодки закреплен лишь в одной верхней перемычке башмака. Причиной падения колодки может быть также и излом перемычек тормозного башмака для крепления клина.
Нарушения в содержании и эксплуатации автотормозного оборудования часто являются причиной заклинивания колесных пар вагонов в пути следования.
При заклинивании на поверхности катания колесных пар образуются ползуны или навары. Во время движения поезда на рельсы в этом случае действуют значительные ударные нагрузки, которые нередко, особенно зимой, приводят к повреждению и излому рельсов.
Основными причинами заклинивания колесных пар, вагонов являются:
- неисправности автотормозных приборов — воздухораспределителей, их рабочих резервуаров, тормозных цилиндров, грузовых авторежимов, авторегуляторов рычажной передачи и др.;
- засорение фильтров, пылеулавливающих сеток, - образование ледяных пробок в воздухопроводе;
- неисправности тормозной рычажной передачи — несоответствие плеч рычагов, неправильная регулировка и заедание рычажной передачи;
- нарушение правил технического обслуживания и ремонта автотормозного оборудования на вагонах, несоблюдение правил испытания и опробования, автотормозов в поездах и управления автотормозами при.ведении поезда. К этому относятся неправильное применение режимов торможения, отправление вагонов с заторможенным автоматическим или ручным тормозами, наличие чрезмерных утечек воздуха в тормозной сети поезда, выход штока поршня тормозного цилиндра больше или меньше допускаемых норм, постановка композиционных колодок на вагон при рычажной передаче, собранной для чугунных колодок, перезарядка автотормозов и др.
У вагонов, оборудованных чугунными тормозными колодками, воздухораспределитель следует включать на груженый режим при загрузке вагона не менее 6 т на ось, на средний режим — от 3 до 6 т на ось и на порожний — менее 3 т на ось. Если вагон оборудован композиционными колодками, то включать воздухораспределитель на груженый режим запрещено. В этом случае при загрузке до 6 т на ось его включают на порожний режим, а при.загрузке свыше 6 т на ось — на средний.
Для правильного выбора режима торможения, на который следует включить воздухораспределитель, многие осмотрщики по тормозам пользуются зависимостью между прогибом рессорных комплектов и степенью загрузки вагона.
При опробовании автотормозов необходимо, тщательно проверять, все ли тормоза в поезде отпустили. Воздухораспределители, не отпустившие или дающие замедленный отпуск, следует заменить исправными. Для выявления не чувствительных к отпуску воздухораспределителей во время проверки действия автотормозов от станционной воздушной сети отпуск следует производить постановкой ручки крана машиниста во второе (поездное) положение. Перед опробованием автотормозов в составе от стационарной компрессорной установки при температуре —40 °С и ниже разрешается после полной зарядки тормозной сети произвести несколько раз полное торможение и отпуск.
При опробовании тормозов и отправлении поезда нельзя отпускать тормоза вручную выпускным клапаном, так как в пути следования воздухораспределитель при последующих торможениях не отпустит, что неизбежно приведет к заклиниванию колесных пар.
Чтобы избежать заклинивания колесных пар, осмотрщикам нужно, помимо проверки отпуска тормозов во время опробования проверять их состояние при отправлении поезда на ходу. Если будут замечены заторможенные вагоны или идущие юзом, а также с ползунами на колесах, то необходимо принять меры к немедленной остановке поезда и устранить неисправность.
Если в пути следования поезда выявлена неудовлетворительная или недостаточно эффективная работа тормозов, то на станции расположения ПТО, а при необходимости на ближайшей промежуточной станции должна быть произведена контрольная проверка тормозов. Очередность и объем проверки определяются причинами, вызвавшими необходимость такой проверки.
При контрольной проверке прежде всего следует, определить зарядное давление и утечку воздуха из тормозной магистрали поезда. На всех вагонах необходимо проверить правильность включения режимов воздухораспределителей в соответствии с загрузкой вагона, профилем пути, числом вагонов в пассажирском поезде и т.д.
Кроме того, проверяют действие авторегуляторов, рычажных передач, грузовых режимов, соответствие типа колодок положению затяжек горизонтальных рычагов, правильность регулировки рычажной передачи, состояние ручных тормозов, выхода штоков тормозных цилиндров. При контрольной проверке допускается увеличение размера выхода штока тормозного цилиндра, по сравнению со значениями, установленными для вагонов при отправлении с ПТО, на пассажирских вагонах на 10 мм, кроме пассажирских вагонов с чугунными колодками без авторегулятора рычажной передачи, в которых максимальный выход штока может достигать 180 мм.
Затем производят полное опробование тормозов и подсчет фактического тормозного нажатия на 100 т веса поезда. При этом воздухораспределители пассажирские на равнинном режиме, отпускающие в течение 5 мин, в расчет приниматься не должны.
В вагонах, имевших заклинивание колесных пар или подозрение на неисправность авторежима, а также при пониженной эффективности автотормозов поезда необходимо проверить по манометру давление в тормозных цилиндрах при снижении давления в магистрали до 0,52 МПа (5,2 кгс/см2). Давление в тормозных цилиндрах на груженом режиме торможения не должно превышать 0,43 МПа (4,3 кгс/см2).
Проверяют также работу крана машиниста, стабильность поддержания давления в тормозной магистрали в поездном положении и положении, перекрыши после ступени торможения, пределы давления в главных резервуарах, включение и действие автоматического тормоза локомотива. После этого следует проверить проходимость воздуха через блокировочное устройство № 367, которая считается нормальной, если при нахождении ручки крана машиниста в I положении и открытии концевого крана магистрали со стороны проверяемого блокированного устройства падение давления с 0,6 до 0,5 МПа (с 6 до 5 кгс/см2) в главных резервуарах объемом 1000 л при начальном зарядном давлении не менее 0,8 МПа (8 кгс/см2) происходит за время не более 12 с. При большем объеме главных резервуаров это время должно быть пропорционально увеличено.
Правильность управления автотормозами проверяют торможением и отпуском в соответствии с данными скоростемерной ленты, зафиксированными в момент ненормальной работы тормозов.
Затем необходимо произвести торможение и отпуск автотормозов I положением ручки крана машиниста с выдержкой ее в этом положении в пассажирском поезде — до зарядки уравнительного резервуара установленным давлением на 0,03—0,05 МПа (0,3—0,5 кгс/см2) сверх предтормозного зарядного с последующим переводом ручки в поездное положение. При этом время отпуска тормозов у вагонов с заклиниванием колесных пар в пассажирском поезде должно быть не более 25 с при длине до 80 осей и не более 40 с, если длина поезда более 80 осей.
Воздухораспределители вагонов, имевших заклинивание колесных пар, в которых при проверке в поезде не выявлены неисправности, проверяют на стенде в контрольном пункте автотормозов. При снятии воздухораспределителей обязательно нужно проверить чистоту сетки на магистральном воздухопроводе и фильтра.
В пассажирских поездах на электропневматических тормозах следует проверить их действие. Результаты контрольной проверки должны быть оформлены актом.
ОСОБЕННОСТИ ОСМОТРА РАМ, КУЗОВОВ, КРЫШ ВАГОНОВ. МЕРЫ ПО СОХРАННОСТИ ВАГОНОВ
Основными неисправностями рам вагонов является образование в них различных трещин и надрывов, особенно в условиях низких температур, когда увеличивается хрупкость металла. Чаще всего трещины встречаются в местах соединения удар- ной розетки с концевой балкой, на хребтовой балке в местах расположения передних и задних упоров автосцепного устройства и между ними, в сварных швах, соединяющих шкворневую и хребтовую балки. Признаком наличия трещин является скопление в местах их образования зимой инея, а летом — валиков пыли, ржавчины и т. п.
Причинами повреждения рам вагонов является воздействие на них всевозможных толчков и ударов в процессе эксплуатации, а также соударения, возникающие при маневровых работах.
На наличие неисправностей в рамах вагонов могут указывать дефекты в кузовах, так как нагрузки, действующие, на эти части вагона, имеют одинаковый характер.
Вагоны, имеющие изломы или трещины балок рамы, размеры которых выходят за пределы допустимых, должны быть отремонтированы после отцепки от поезда.
Коррозионный износ крыш чаще наблюдается из-за несоблюдения правил и технологии их окраски при плановых видах ремонта. Анализ показал, что у вагонов, построенных в зимние месяцы и проходящих плановые виды ремонта тоже зимой, повреждения крыш коррозией встречаются в 1,5—2 раза чаще, чем у построенных в другое время года. Объясняется это сложностью окраски и сушки крыш в зимних условиях.
Дата добавления: 2018-02-18; просмотров: 2249; Мы поможем в написании вашей работы! |
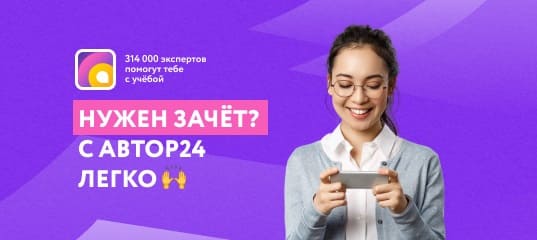
Мы поможем в написании ваших работ!