Вимоги до готової продукції (за ДСТУ Б В.2.7-75-98)
Вимоги до сировини
Граніт – кисла вивержена інтрузивна гірська порода. Мінерали, що входять до складу граніту наведені в Таблиці 1. Граніти мають густину 2600…2700кг/м³, водопоглинання не більше 0,5%, міцність при стиску 200…250 МПа, міцність при розтягу у 50 разів менший міцності при стиску, колір визначається червоно-сірою гамою відтінків.
Таблиця 1 – Мінеральний скла гранітів
Назва мінералу | Кількість, % |
Польові шпати (в більшості ортоклаз) | до 70% |
Кварц (кристалічний кремнезем) | більше 20% |
Слюди (мусковіт та біотит) | біля 5% |
2. Особливості технологічного процесу отримання заповнювача (технологічна схема + опис технології)
Технологічна схема типового щебеневого заводу з переробки абразивних однорідних вивержених порід (Рисунок 1).
Гірську масу рівномірно подають на I стадію дроблення в щокову дробарку. Потім матеріал крупністю йде в конусні дробарки середнього дроблення II стадії. Продукт II стадії дроблення направляють в корпус дрібного дроблення, і він надходить в проміжні бункери, звідки з віброживильників розподіляється в конусні дробарки дрібного дроблення III стадії. Продукт III стадії дроблення системою конвеєрів транспортують в розподільні бункери, з яких віброживильників він прямує на вісім секцій грохотів I стадії грохочення. На 1 стадії грохочення отримують фракції 40…20 мм. Щебінь крупніше 40 мм повертається на додроблювання в коротко конусні дробарки III стадії дроблення. Щебінь 40…20 мм направляють на склад готової продукції. Щебінь фракції 20…0 мм самопливом надходить на грохоти II стадії грохочення, де розсіюється на щебінь фракції 20…10 мм і фракції 10…5 мм. Потім відбувається промивання та класифікація піску із відсівів подрібнення; зневоднення піску і складування готової продукції.
|
|
Вихідна гірська порода
І стадія подрібнення
(щокова дробарка)
![]() |
Проміжний бункер
Грохочення ІІІ стадія подрібнення
(конусна дробарка)
Грохочення фр. 0…20мм,
Промивання фр. 0…5мм.
![]() |
Класифікація та
Зневоднення фр.
0…0,16 мм.
Фр. 0,16…5 мм
Зневоднення
Пісок збагачений
З відсівів 0,16…5 мм.
Рисунок 1 – технологічна схема типового щебеневого заводу з переробки абразивних однорідних вивержених порід.
Для процесів отримання гранітного щебеню використовують щокові та конусні дробарки.
|
|
В щокових дробарках (Рисунок 2) матеріал подрібнюється за допомогою роздавлювання у сполученні з розколюванням між нерухомою та рухомою щоками і залежно від характеру руху елемента, що пересувається, дробарки розділяють на дробарки з простим або складним хитанням щоки.
Рисунок 2 - Щокова дробарка:
1 – нерухома щока; 2 – рухома щока; 3 – ексцентриковий вал; 4 – клини; 5 – запобіжний пристрій; 6 – замикальна плита; 7- розпірна плита.
На практиці щокові дробарки використовують для крупного та середнього подрібнення.
В конусній дробарці (Рисунок 3) матеріал подрібнюється роздавлюванням при зближенні поверхонь внутрішнього рухомого і нерухомого зовнішнього конусів.
Конусні дробарки використовують для крупного, середнього та дрібного подрібнення. Робочий процес в конусних дробарках складається з роздавлювання матеріалу, який міститься у кільцевому просторі між зовнішнім нерухомим та внутрішнім рухомим конусами.
Рисунок 3 - Схеми конусних дробарок з підвішеним (а) і з консольним (б) валом:
1 – нерухомий зовнішній конус; 2 – рухомий конус; 3 – хитний вал; 4 – стакан; 5, 6 – конічні шестерні; 7 – лоток.
|
|
Число стадій подрібнення залежить від заданого ступеня подрібнення каміння :
і = а1/ а2,
де а1 – найбільша крупність каменя, що надходить;
а2 – найбільша крупність продукту подрібнення.
Для щокової та конусної дробарок звичайний ступінь подрібнення дорівнює 3…5. Загальний ступінь подрібнення визначається за рівнянням:
і = і1 і2 і3 іn,
де і – ступінь подрібнення на кожній із n-стадій.
Для регулювання крупності, а також і кількості матеріалу, що надходить на подрібнення, застосовують грохочення.
Розрізняють наступні види грохочення: попереднє, контрольне та заключне (товарне). Попереднє грохочення використовують для видалення дрібних класів з матеріалу, що подається на подрібнення. Контрольне грохочення проводиться для видалення окремих класів із продуктів подрібнення, що направляють на доробку – повторне подрібнення в замкнутому циклі. При використанні замкнутого циклу подрібнення, крім збільшення виходу необхідних фракцій, поліпшується форма зерен щебеню. Товарне або заключне грохочення проводять з метою отримання товарних фракцій щебеню для відправки споживачеві.
Вимоги до готової продукції (за ДСТУ Б В.2.7-75-98)
|
|
Зерновий склад
КРЗ випускають у вигляді таких основних фракцій: понад 5 до 10 мм вкл.; понад 10 до 20 мм вкл., понад. 20 до 40 мм вкл., понад 40 до 80 (70 мм вкл.).
За погодженням виготовлювача зі споживачем допускається випускати КРЗ у вигляді сумішей наведених вище фракцій або будь-якого іншого зернового складу, у тому числі нефракціоновані, за умови дотримання наведених у договорі на поставку продукції обов'язкових вимог даного стандарту .
4.2.3 Повні залишки на контрольних ситах при розсіві КРЗ фракцій понад 5 до 10 мм вкл.; понад 10 до 20 мм вкл., понад. 20 до 40 мм вкл., понад 40 до 80 (70) мм вкл. повинні відповідати зазначеним у таблиці 1, де d і D- найменші та найбільші номінальні розміри зерен.
Таблиця 1
Діаметр отворів контрольних сит, мм | d | 0,5(d+D) | D | 1,25D |
Повні залишки на ситах, у відсотках за масою | Понад 90 до 100 вкл. | Понад 30 до 80 вкл. | До 10 вкл. | До 0,5 вкл. |
Форма зерен і вміст подрібнених зерен у КРЗ, які одержані дробленням гравію.
Форму зерен КРЗ характеризують вмістом зерен пластинчастої (лещадної) та голчастої форми.
До зерен пластинчастої (лещадної) та голчастої форми відносять такі зерна, товщина або ширина яких менше довжини у три і більше разів.
КРЗ в залежності від вмісту зерен пластинчастої (лещадної) та голчастої форми поділяють на чотири групи, які повинні відповідати зазначеним у таблиці 2.
(За ДСТУ Б В.2.7 -74)
Таблиця 2
В відсотках за масою
Група КРЗ за формою зерен | Вміст зерен пластинчастої (лещадної) та голчастої форми |
Окатана | До 10 вкл. |
Кубопоібна | Більше 10 до 15 вкл. |
Покращена | Більше 15 до 25 вкл. |
Звичайна | Більше 25 до 35 вкл. |
КРЗ не повинні містити більше 35% за масою зерен пластинчастої (лещадної) та голчастої форми.
За погодженням виробника зі споживачем допускається випуск КРЗ , що містять до 65 % вкл. зерен пластинчастої (лещадної) та голчастої форми.
Міцність
Міцність КРЗ з щільного природного каменю характеризують маркою, яка визначається за його подрібнюваністю при стисканні (роздавлюванні) у циліндрі, яка повинна відповідати вимогам, зазначеним у таблиці 3.
Таблиця 3
Марка КРЗ за дробильністю | Щебінь із вивержених порід |
із інтрузивних | |
1400 | До 12 вкл. |
1200 | Понад 12 до 16 вкл. |
1000 | Понад 16 до 20 вкл. |
800 | Понад 20 до 25 вкл. |
600 | Понад 25 до 34 |
КРЗ, призначені для будівництва автомобільних доріг, додатково характеризують маркою за стиранням, яка повинна відповідати вимогам, зазначеним у таблиці 4.
(За ДСТУ Б В.2.7 -74)
Таблиця 4
Група КРЗ за міцністю на стиранність | Марка КРЗ за стиранністю | Стиранність (втата за масою) в відсотках |
Щебеню | ||
Високоміцна | И-I | До 25 вкл. |
Міцна | И-II | Більше 25 до 35 вкл. |
Середньої міцності | И-III | Більше 35 до 45 вкл. |
Слабка | И-IV | Більше 45 до 60 вкл. |
Дуже слабка | И-V | Більше 60 |
Вміст зерен слабких порід
Вміст зерен слабких порід у КРЗ залежно від виду гірської породи і марки за дробильністю не повинно бути більше зазначеного в таблиці 5.
До слабких відносять зерна з границею міцності вихідної гірської породи при стисненні в насиченому водою стані менше 20 МПа (200 кгс/см2).
Таблиця 5
Марка КРЗ за дробильністю | Вміст зерен слабких порід, у відсотках за масою |
Щебінь із природного каменю (вивержених, метаморфічних і осадових порід) марок: | |
1400; 1200; 1000 | 5 |
800; 600; 400 | 10 |
300 | 15 |
Морозостійкість
Морозостійкість КРЗ характеризують числом циклів поперемінного заморожування і відтавання, при якому його втрати у відсотках за масою не перевищують встановлених значень.
Допускається оцінювати морозостійкість КРЗ за результатами випробування насиченням в розчині сірчанокислого натрію і висушуванням. При розбіжності марок морозостійкість оцінюють за результатами випробування заморожуванням і розморожуванням.
КРЗ за морозостійкістю підрозділяють па марки згідно з таблицею 6 за винятком марки F10.
(За ДСТУ Б В.2.7 -74)
Таблиця 6
Група КРЗ за морозостійкістю | Марки за морозостійкістю | Число циклів поперемінного заморожування і відтавання, при яких втрати в масі не перевищують встановлених значень |
Низька | F10 | До 14 вкл. |
Середня | F15 | Від 15 до 24 вкл. |
F25 | Від 25 до 34 вкл. | |
F35 | Від 35 до 49 вкл. | |
F50 | Від 50 до 99 вкл. | |
Висока | F100 | Від 100 до 149 вкл. |
F150 | Від 150 до 199 вкл. | |
F200 | Від 200 до 299 вкл. | |
Дуже висока | F300 | Від 300 до 399 вкл. |
F400 | Від 400 і більше |
Показники морозостійкості КРЗ при випробуванні заморожуванням і розморожуванням або насиченням у розчині сірчанокислого натрію і висушуванні повинні відповідати зазначеним у таблиці 7.
Таблиця 7
Вид випробування | Марка КРЗ за морозостійкістю | ||||||||
F15 | F25 | F35 | F50 | F100 | F150 | F200 | F300 | F400 | |
Заморожування-відтавання: | |||||||||
число циклів | 15 | 25 | 35 | 50 | 100 | 150 | 200 | 300 | 400 |
втрата маси після випробування у відсотках, не більше | 10 | 10 | 5 | 5 | 5 | 5 | 5 | 5 | 5 |
Насичення у розчинні сірчанокислого натрію – висушування: | |||||||||
число циклів | 3 | 5 | 8 | 10 | 10 | 15 | 15 | 15 | 15 |
втрата маси після випробування у відсотках, не більше | 10 | 10 | 10 | 10 | 5 | 5 | 3 | 2 | 1 |
Дата добавления: 2018-02-18; просмотров: 960; Мы поможем в написании вашей работы! |
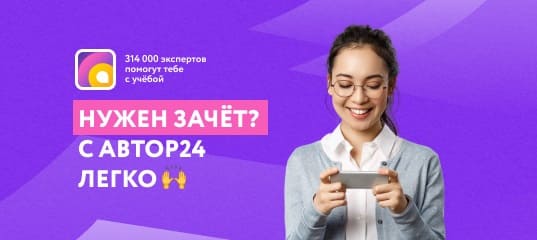
Мы поможем в написании ваших работ!