Электроконтактное напекание металлических порошков
Способ электроконтактного напекания порошков сочетает в себе ряд процессов, протекающих одновременно: прессование и спекание металлического порошка, припекание его к поверхности детали под действием давления и температуры.
Сущность способа состоит в том, что в место контакта двух токопроводящих поверхностей подается металлический порошок, который под давлением инструмента спрессовывается и под воздействием тепла, выделяемого электрическим током, и давления спекается и припекается к поверхности детали. Принципиальная схема процесса приведена на рисунке 3.2.
Рисунок 3.2. – Принципиальная схема способа электроконтактного напекания металлических порошков на поверхность деталей: 1 – цилиндр пневматический; 2 – ролик медный;3 – порошок; 4 – деталь; 5 – трансформатор;
6 – слой спеченного порошка.
Напряжение от понижающего трансформатора 5 подается на деталь, вращающуюся в центрах или патроне станка, и на прижимной ролик. В зазор между роликом и деталью подается, например, металлический порошок ПЖЗМ 2 (С 0,1%; Mn 0,32; Si 0,18; P 0,02; S 0,015%) размером частиц 0,16-0,071 мм, который прокатывается между медным роликом 2, охлаждаемым водой, и поверхностью детали с усилием 0,75-1,2 кН на сантиметр ролика. Процесс протекает при напряжении 0,8-1,2 В и токе 2500-4000 А (ширина ролика 15-30 мм) и 3500-5000 А (3-8 мм) на 1 см ширины ролика. Скорость напекания до 90 м/ч, шаг при напекании по винтовой линии от 0 до 0,35 ширины слоя.
|
|
Физико-химическая суть процесса заключается в том, что спекаемый и напекаемый на поверхность слой порошка нагревается за счет прохождения тока не до температуры плавления (Т), а до температуры (0,7-0,8) Т. Спекание частиц порошка в слой и припекание слоя к основе происходят за счет диффузионных процессов и сплавления частиц порошка в отдельных контактирующих точках их поверхности.
Эта особенность процесса приводит к тому, что покрытия получаются пористыми. Заполнение маслом поры способствуют образованию устойчивой масляной пленки и уменьшению пускового момента.
Припекание можно производить на торцевые поверхности (торцы клапанов, стержни мерительного инструмента), на плоские и цилиндрические поверхности (например, шейки коленчатого вала и др.). Во всех случаях давление на порошок и подвод тока осуществляются через охлаждаемый электрод (ролик, брус, стержень).
Толщина слоя, нанесенного за один проход, зависит от диаметра детали и ролика и колеблется в пределах 0,2-1,0 мм. Возможно напекание в несколько проходов. Ширина слоя зависит от ширины ролика, но не более 35 мм за один проход.
Этот способ позволяет восстановить такие сложные детали, как коленчатые валы двигателей, и обеспечить повышение их износостойкости в 1,5-2 раза за счет создания пористого маслоемкого слоя на шейках. Недостатками способа является ограниченная толщина напекаемого слоя, сложность механизации и дозирования подачи металлического порошка.
|
|
Электроконтактная приварка ленты
Сущность процесса восстановления электроконтактной приварки ленты заключается в приварке стальной ленты к восстанавливаемой поверхности детали мощными импульсами сварочного тока. В сварной точке, полученной от действия импульса тока, происходит расплавление металла ленты и детали. Металл ленты в этом случае расплавляется не по всей её длине, а лишь в тонком поверхностном слое в месте контакта детали и ленты. Слой приваривают по всей изношенной поверхности регулируемыми импульсами тока, перекрывающимися точками, которые располагаются по винтовой линии. Перекрытие точек, как вдоль рядков, так и между рядками достигается вращением детали со скоростью, пропорциональной частоте импульсов, и продольным перемещением сварочных роликов. С целью уменьшения нагрева детали и обеспечения закалки приваренного слоя в зону сварки подают охлаждающую жидкость.
|
|
Технология восстановления деталей контактной наваркой стальной ленты включает в себя подготовку деталей и лент, наварку ленты, обработку деталей после наварки.
Подготовка валов и осей к восстановлению заключается в правке центровых фасок и снятии с шейки слоя до диаметра меньше номинального на 0,3…0,5 мм, с изношенными внутренними поверхностями – в шлифовании их до диаметра больше номинального на 0,3…0,5 мм.
Заготовки нарезают из лент толщиной 0,3…1,0 мм. Ширина их должна равняться ширине восстанавливаемого участка, а длина – его периметру. Зазор в месте стыка концов ленты не должен превышать 0,5…0,8 мм, нахлест концов не допускается. Заготовки из стальной ленты изготавливают на установке 02.11-157 "Ремдеталь".
Регулируемые импульсы сварочного тока могут быть получены путём использования прерывателей, применяемых в контактных сварочных машинах, а также конденсаторных источников питания.
Схема приварки металлической ленты к поверхности вала представлена на рисунке 3.3.
Рисунок 3.3 – Схема электроконтактной приварки ленты
1-ролик; 2-навариваемая лента; 3-деталь; 4-наваренный слой; 5-трансформатор; 6-регулятор цикла сварки; n-частота вращения; р-сила прижатия ролика.
|
|
Механические свойства покрытий (твёрдость, износостойкость и прочность сцепления) зависят от качества стальной ленты. Ленту следует подбирать с учётом получения необходимой твёрдости восстанавливаемой поверхности детали. Высокую твердость обеспечивают ленты из хромистых и марганцевых сталей.
Таблица 3.8. – Режимы наварки металлической ленты к деталям типа "вал"
Диаметр детали, мм | Частота вращения шпинделя, мин ־¹ | Подача каретки, мм/об | Сила тока, кА | Время, с | |
сварки | паузы | ||||
15 20 30 40 50 60 70 80 100 130 | 8…10 6…8 5…7 5…6 4…5 3…5 3…4 3…3,5 2…3 1,5…2 | 3…3,5 3…3,5 3…3,6 3,5…4 3,5…4 3,5…4 3,5…4 3,5…4 3,5…4 3,5…4 | 4…5 4,5…5 5…5,5 5,5…6 5,8…6,2 6…6,5 6,5…7 6,4…7,2 7,2…7,5 7,5…8,5 | 0,06 0,06 0,06 0,06 0,06 0,06 0,06 0,08 0,08 0,08 | 0,12 0,12 0,12 0,12 0,12 0,12 0,12 0,1 0,1 0,1 |
Контактная наварка имеет ряд преимуществ по сравнению с другими способами восстановления деталей:
- благодаря малому нагреву детали уменьшаются внутренние напряжения и деформации;
- наносятся покрытия заданной толщины;
- потери металла и выгорание легирующих элементов почти отсутствуют;
- процесс экологически чистый;
- в процессе наварки происходит закалка поверхностных слоев;
- высокая прочность сцепления покрытий (100…250 МПа).
Дата добавления: 2021-05-18; просмотров: 215; Мы поможем в написании вашей работы! |
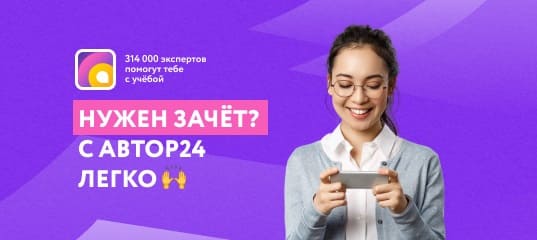
Мы поможем в написании ваших работ!