Особенности штамповки на прессах
Содержание
Введение
1. Разработка чертежа поковки
2. Расчет и оптимизация технологических параметров при штамповке на ГКШП
. Определение экономических показателей использования металла
. Конструкторский расчет штампа для формоизменяющих операций
. Определение усилие обрезки и выбор обрезного пресса
. Конструирование штампа для завершающих операций
. Планировка участка штамповки
. Выбор температурного интервала штамповки и подбор нагревательных устройств
. Выбор режимов термообработки поковки
. Охрана труда и техника безопасности
Технологическая карта штамповки
Литература
Введение
Свободная ковка и объемная штамповка являются одними из видов обработки металлов давлением. Горячая штамповка является важнейшей областью металлообработки. Современная технология горячей штамповки - сложный комплекс различных по своему характеру операций.
Основной задачей ковки и объемной штамповки является придание заготовке требуемой формы путем пластической деформации. При правильной разработке технологического процесса обработке давлением и обеспечении необходимого термомеханического режима можно создать в обрабатываемом металле структуру и механические свойства, которые в большей мере удовлетворяют требованиям, предъявляемым к изготовляемой из него детали.
Производство поковок характеризуется повышенными механическими свойствами изготовленных деталей и точностью заготовок, позволяющими использовать их в наиболее ответственных узлах машин (коленчатые и распределительные валы, шатуны, шестерни и т. д.)
|
|
Дальнейшее совершенствование процессов горячей объемной штамповки, повышение точности размеров и улучшение качества поверхности, получаемых при обработке давлением, приводят к тому, что во многих случаях этот способ обработки полностью заменяет традиционную обработку резанием. Поэтому курс “Горячей штамповки” является одним из профилирующих при подготовки специалистов по обработке металлов давлением.
Наряду с высокой пластичностью при обработке давлением стремятся получить возможно меньшее сопротивление деформированию. Повышение температуры значительно уменьшает эту характеристику деформируемого металла, поэтому его перед кузнечной обработкой нагревают.
При всем многообразии применяемых методов процесс горячей объемной штамповки имеет следующую последовательность:
1. разделка исходного металла на заготовки;
2. нагрев заготовок;
. формообразование поковок;
. обрезка облоя и пробивка перемычек;
. термическая обработка поковок;
|
|
. очистка и отделка поковок.
1. Разработка чертежа поковки
Деталь - полумуфта зубчатая.
Штамповочное оборудование - КГШП.
Нагрев заготовок - индукционный.
1. Исходные данные по детали:
1.1. Материал - сталь 45:
- 0,42-0,50% C;
- 0,17-0,37% Si;
- 0,50-0,80% Mn;
- 0,04max % S;
- 0,035max % P;
- 0,25 % Cr;
- 0,3 % Ni;
- 0,3% Cu.
1.2. Масса детали - 1 , 4 кг
2. Исходные данные для расчета:
2.1 Масса поковки (расчетная) определяется:
,
где - масса детали, кг;
- расчетный коэффициент, устанавливаемый в соответствии с табл.3 ([2], стр.8, табл.3)
Класс точности выбираем из таблицы 2 ([2], стр. 5).
Класс точности - Т3.
Группа стали - М2 ([2], стр.5, табл.1)
Средняя массовая доля углерода в стали 45 - 0,46%
2.4 Степень сложности - С2
Размеры описывающей поковку фигуры (цилиндр), мм:
диаметр ( )
высота ( )
Объем описывающей фигуры:
Масса описывающей фигуры (расчетная) - 6,21 кг.
Степень сложности определяется путем вычисления отношения массы поковки к массе геометрической фигуры
, в которую вписывается форма поковки. Получаем
, что соответствует степени сложности С2.
Конфигурация поверхности разъема штампа П (плоская) ([2], стр.5, табл.1)
Исходный индекс - 10 ([2], стр.9, табл.4)
|
|
3. Припуски и кузнечные напуски:
3.1 Основные припуски на размеры ([1], стр.12,табл.3)
1,5 - диаметр 65мм и чистота поверхности 10;
1,6 - диаметр 117мм и чистота поверхности 10;
1,5 - диаметр 46мм и чистота поверхности 10;
1,2 - толщина 80мм и чистота поверхности 20;
1,5 - толщина 64мм и чистота поверхности 10;
1,2 - толщина 64мм и чистота поверхности 20;
1,4 - толщина 14,1мм и чистота поверхности 10;
Дополнительные припуски, учитывающие:
смещение по поверхности разъема штампа - 0,3 мм ([1], стр.14, табл.4)
отклонение от плоскостности - 0,3 мм ([1], стр.14, табл.5)
Штамповочный уклон:
на внутренней поверхности - не более 7º, принимается 7º;
на наружной поверхности - не более 5º, принимаем 5º.
4. Размеры поковки и их допускаемые отклонения:
4.1Размеры поковки, мм:
диаметр , принимаем 68,5 мм
диаметр , принимаем 121 мм
диаметр , принимаем 42,5мм
толщина , принимаем 83мм
толщина , принимаем 67,5 мм
толщина , принимаем 83мм
4.2 Радиус закругления наружных углов - 3,0 мм ([2], стр.13, табл.7)
Допускаемые отклонения размеров ([1], стр.17, табл.8)
диаметр
диаметр
диаметр
толщина
толщина
толщина
Неуказанные предельные отклонения размеров равны допуска
соответствующего размера поковки
Неуказанные допуски радиусов закругления - ([1], стр.26, табл.17)
|
|
Допускаемая величина остаточного облоя - 1,2 мм ([1])
Допускаемое смещение по поверхности разъема штампа - 0,5 мм ([1], стр.20, табл.9)
Допускаемое отклонение от плоскостности и прямолинейности - 0,5 мм ([1])
Допускаемое отклонение от концентричности пробитого отверстия относительно внешнего контура поковки - 0,5 мм ([1], стр.23, табл.13)
Допустимая величина высоты заусенца - 3 мм ([1]).
При прошивке поковок с отверстием возможно получение наметок. Возможность выполнения наметок определяется по следующим зависимостям: металл штамп пресс обрезной
,
где - максимальный диаметр поковки, мм
, принимаем 122,5 мм
Т.к. полученный диаметр (31,5мм) меньше диаметра отверстия поковки (42,5мм), то выполняется напуск металла, т.е. отверстие поковки полностью закрываем, а наметку - не выполняем.
Разработка горячей поковки
Расчет чертежа горячей поковки осуществляется по чертежу холодной поковки и вычерчивается в том же масштабе. Номинальные размеры на чертежах поковок отличаются между собой на величину тепловой усадки, которая соответствует величине линейной усадки равной 1,2-1,3%. Размеры округляем в сторону увеличения до 0,5 - 1мм.
Получаем:
диаметр 121мм → , принимаем 122,5 мм
диаметр 83 мм → , принимаем 84мм
диаметр 68,9 мм → , принимаем 69,5мм
диаметр 53 мм → , принимаем 54мм
диаметр 42,5 мм → , принимаем 43мм
толщина 17,5 мм → , принимаем 18мм
толщина 67,5 мм → , принимаем 68,5мм
2. Расчет и оптимизация технологических параметров при штамповке на КГШП
Особенности штамповки на прессах
Современные кузнечные цеха имеют большое количество кривошипных горячештамповочных прессов. Это связано с рядом преимуществ по сравнению со штамповкой на молотах. К ним относятся:
Ø более высокая точность поковок;
Ø меньшие припуски и напуски, что снижает расход металла и последующую механическую обработку;
Ø высокая производительность - в 1,5-3 раза выше, на молотах;
Ø возможность механизации и автоматизации рабочего цикла штамповки за счет жесткого графика движения ползуна и отсутствия ударных нагрузок;
Ø наличие выталкивателей.
Дата добавления: 2021-04-24; просмотров: 312; Мы поможем в написании вашей работы! |
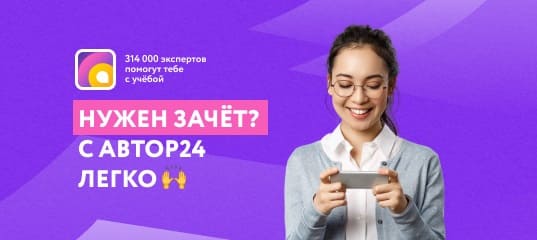
Мы поможем в написании ваших работ!