АНАЛИЗ И УСЛОВИЯ РАБОТЫ КОЛЕСНЫХ ПАР.
ВВЕДЕНИЕ
Как известно, движение подвижного составa в кривых и в прямолинейных участках железнодорожного пути происходит с сильным трением бандажей колёсных пар в точке контакта с боковыми гранями наружных рельсов. Это трение сопровождает интенсивный износ гребней и рельсов, что создаёт угрозу безопасности движения , увеличивает сопротивление движению и энергозатраты , вследствие чего растет эксплуатационный расход.
Проблемa износa гребней колёс и бокового износa рельсов в последние годы является одной из нaиболее острых на железных дорогах России и других стран мирa. Анализ дaнных показал, что частыми причинами отбраковки колесных пар тягового подвижного состава являются износ и подрез гребня, a также возникновение остроконечного накатa.
Интенсивность износа поверхностей в зоне контакта колесо-рельс обусловлено характером взаимодействия пути и тягового подвижного состава (ТПС) и зависит от состояния экипажа ТПС и параметров рельсовой колеи.
На основании логического анализа многочисленных исследователей, а также аналитических и экспериментальных данных получается, что проблема износа гребней бандажей колёсных пар – комплексная.
В качестве решения данной проблемы на железных дорогах разработан совокупность мер состоящих из применения различных технических устройств и средств, призванный исключить вредные факторы, влияющие на износ гребней колёсных пар локомотива и боковых граней наружных рельсов. При обточке колёсных пар, если они не вызваны полным износом гребня оставлять прокат 1,5-2,0 мм, так как максимальный износ гребня возникает с бандажами, имеющими нулевой прокат. Износ гребня в несколько раз снижается при нарастанию проката от 1,5 мм и более. Учитывая это можно сказать что при появлении накатанного слоя на гребне бандажа и по кругу катания бандажа, повышается износоустойчивость гребня и бандажа при обточках их на станках без выкатки.
|
|
Воизбежании одностороннего износа гребня и с целью преодоления ресурса работы бандажей перед каждым ТО-4 производить замер диаметров левого и правого бандажей. По опыту ряда железных дорог обязать техников по замеру колёсных пар выдавать токарю справку со значениями диаметров правого и левого бандажей, величину проката, толщены гребней и задание на величену толщены гребня и диаметра после обточки.
Периодически проводить инструктаж токарей, мастеров занимающихся обточкой колёсных пар, о том что из-за не качественной обточки поверхности гребня, вызванной большой подачей, со снятием с бандажа стружки толщиной 3-4 мм на любом типе станка при последнем проходе, износ гребня достигает в 1-ю поездку после обточки достигает 1-1,5 мм. Это вызвано ухудшением частоты поверхности гребня, наличием волнообразности и надрывами гребня. Во избежании этого последствия последний чистовой проход должен осуществляться подачей резца или фрезы величиной 0,5-1,0 мм. Выполнение обточки до заданной величины гребня, а затем выполнение чистовой обточки, которая вызывает дополнительную величину потери толщины гребня не допустима. . Производить в дорожнохимической лаборатории периодический контроль смазок, применяемых для лубрекации, на основании их ТУ, так как эффективность использования лубрикации зависит от физико-химических и антифрикционных свойств смазки.
|
|
Для получения необходимой чистоты поверхности бандажа и гребня а так же снижения износа в первые поездки после обточки необходимо осуществлять дополнительный проход фрезы на станках КЖ-20 с 0-й подачей или последний проход с глубиной подачи менее 1-го мм. На станках А-41 последний проход резца выполнять с минимальной подачей. Периодически, не реже одного раза в квартал проверять настройку специального приспособления станка КЖ-20. «Линейка», для контроля диаметра колеса.
|
|
При образовании одностороннего подреза гребня на одной или двух колёсных пар локомотива, когда устранение подреза осуществляется за счёт замены колёсных пар, подвергать буксовые поводки на соответствие жёсткостным характеристикам и принемать меры к замене бракованных буксовых поводков. Предъявлять рекламации локомотиворемонтным заводам, за не качественный ремонт и изготовление буксовых поводков.
На дорогах с интенсивным подрезом гребней, особенно при применении кратной тяги, обращать особое внимание на содержание шаровых связей и противоткосных устройств, межтележочных сочленяющих устройств, опор кузова люлечного подвешивания электровозов, так как нарушение норм их содержания приводит к ухудшению условий вписывания в кривые участки пути.
Проверять на ТО-2 тепловозов состояние системы пескоподачи, обращая внимание на правильное положение наконечников песочных труб. Регулировать расход песка под каждую к/п в соответствии с требованиями инструкции.
|
|
Подкатывать на ТР-3 КМБ с разницей диаметров бандажей на первый КП, не более 0,5 мм, в тележке не более 3 мм, на одной секции не более 5 мм, а на одном электровозе не более 8 мм. Разность характеристик КМБ подкатываемых под тепловозы, не должна превышать 3%.
Обеспечить закупку сертифицированных смазочных материалов в тех объемах, которые необходим для безусловного выполнения установленной технологии работы передвижных рельсосмазователей и бортовых гребнесмазывателей.
Назначить в каждом ТЧ ответственного работника за обучение локомотивной бригады, ремонтного персонала и мастеров, особенностям конструкции, правилами проверки работы и назначения лубрикаторов, методом установки форсунок для обеспечения подачи смазки точно под гребень, прочистки их в случае засорения и периодического контроля за включением лубрикаторов локомотивными бригадами.
Установить в ТЧ технически обоснованные нормы времени для приемки локомотива локомотивными бригадами с учетом проверки действия лубрикаторов контроля положения форсунок и при необходимости прочистки и закрепления форсунок для обеспечения подачи смазки точно под гребень. Обязать локомотивные бригады делать запись о приемке и сдаче лубрикаторов в ТУ-152.
Локомотивная бригада обслуживающая передвижной рельсосмазыватель, перед выездом должна добиться регулировки форсунок для подачи смазки или лыжи для ее нанесения таким образом чтобы смазка наносилась в место контакта гребня с боковой поверхностью рельса. Правильность нанесения смазки и в необходимых количествах, должно контролироваться локомотивными бригадами в момент остановок на перегонах во время поездом. Со стороны руководителей депо и отделения дороги необходим постоянный систематический контроль за работой передвижных рельсосмазывателей с внесением корректировок в технологию смазывания рельсов.
Учитывать, что на затяжных спусках после длительного следования, в режиме пневматического торможения смазка на рельсах сгорает и потребовать от локомотивной бригады применять реостатное и рекупировочное торможение с целью уменьшения времени применения пневматического торможения.
Хорошим методом сокращения отрицательных последствий взаимодействия гребней колёсных пар с рельсом является подача в зону их контакта (гребней и боковой грани рельса) смазочного материала (лубрикация – смазывание).
В настоящий период времени на железных дорогах Российской Федерации повсеместно используются различные типы рельсосмазывателей и гребнесмазыватей.
Приведу некоторые сведения о применяемых типах и конструкциях лубрикаторов.
Рельсосмазывающая установка РС-2 ВНИИЖТ. Монтируется в кузове и раме тележки подвижного состава и предназначена для нанесения консистентных смазок на внутреннюю боковую поверхность рельсов.
Передвижной вагон рельсосмазыватель. Предназначен для бесконтактного нанесения консистентной смазки на боковую грань головки рельса.
Рельсосмазывательная машина РСМ-1. Представляет собой дизельный подвижной состав для нанесения смазки на внутренние грани головок рельсов.
Гребнесмазыватель АГС-10, АГС-8. Он предназначен для дозированного нанесения консистентной или жидкой смазки на гребни бандажей колёсных пар локомотива.
Гребнесмазыватели польстерного типа. Главное отличие этого гребнесмазывателя от других конструкций гребнесмазывателей в том, что он исключает появление на гребне абразивного покрытия, так как польстер при смазывании стирает с гребня пыль, песок и другие абразивообразующие материалы.
Стационарные лубрикаторы – рельсосмазыватель РС-5. Используется для «прикрытия» горловин станций в кривых участках пути, в местах подхода к стрелочным переводам и на самих стрелочных переводах. Его крепят при помощи специальной арматуры на подошве рельса. Смазка подается на контактную поверхность рабочей грани гребня колеса и далее разносится по рельсу колёсами подвижного состава.
На локомотиворемонтных предприятиях железнодорожного транспорта проводят развеску локомотивов, с целью исключить повышенное воздействие отдельных колёсных пар на путь и склонности к боксованию других. В обоих случаях - как путь, так и колёсные пары подвержены интенсивному износу.
Не маловажное значение имеет и выбор профиля бандажа колесных пар. Сейчас в ряде локомотивных депо широкое применение получил профиль ДМетИ ЛР с толщиной гребня 30 мм и высотой 28 мм. Это обусловлено тем, что при достижении толщины гребня 29-30 мм значительно снижается интенсивность его износа.
Нельзя забывать и о том, что на взаимодействие пути и ТПС оказывает немалое влияние чистота и точность обточек колесных пар на станках, а также качество ремонта механической части локомотивов.
Одним из основных методов применяемых с 1994 года мероприятий по сохранности колес локомотивов и вагонов является термическое упрочнение гребней колесных пар. Термическая поверхностная закалка гребней колесных пар повышает контактно-усталостную прочность металла и, как следствие, увеличивает ресурс и надежность колесных пар тягового подвижного состава. Результаты проведенных специалистами ВНИИЖТа лабораторных исследований доказывают, что закалка гребней колес на твердость свыше 600 НV может стать эффективным способом борьбы с боковым износом, причем не только гребней колес, но и рельсов.
В настоящее время метод термического упрочнения применяется при использовании различных источников нагрева (плазменный, лазерный и др.). Основным параметром, влияющим на процесс закалки, является тепловой поток, создаваемый на поверхности изделия, его распределение в пространстве и времени. Именно этот параметр определяет условия нагрева металла и, соответственно, параметры закалённого слоя (глубина, ширина, макро- и микроструктура, распределение твёрдости по глубине слоя и др.). А источник нагрева определяет только возможности устройства реализации теплового потока на поверхности изделия.
Для локомотивного хозяйства установки комплексной программы (см. рис.1), применение технических средств лубрикации, создание поверхностных участков плазменного упрочнения гребней колесных пар позволит не только сократить потребление электроэнергии и дизельного топлива на тягу поездов, но и уменьшить износ гребней и за счет этого сократить число обточек колесных пар, снизить объемы их ремонта.
В представленном дипломном проекте приведен сравнительный анализ различных видов упрочнения, выполнен анализ эффективности использования магнитоплазменного метода упрочнения (МПУ) гребней колесных пар тепловозов в локомотивном депо, спроектирована стойловая часть для проведения упрочнения с последующей дефектоскопией колесных пар, разработано приспособление для вывешивания и вращения колесной пары при обработке, приведен расчет привода для вращения колесных пар при упрочнении. Выполнен расчет экономической эффективности внедрения данного приспособления, предложен ряд мероприятий по созданию безопасных условий труда при проведении магнитоплазменного упрочнения, выполнен проверочный расчет на прочность винта подъемного устройства.
АНАЛИЗ И УСЛОВИЯ РАБОТЫ КОЛЕСНЫХ ПАР.
1.1. Условия работы колесных пар.
Движение подвижного состава в кривых и в прямолинейных участках пути сопровождается повышенным трением гребней бандажей колёсных пар в точке контакта с боковыми гранями наружных рельсов. Это трение вызывает износ гребней и рельсов, что создаёт угрозу безопасности движения, увеличивает сопротивление движению и энергозатраты , вследствие чего повышены эксплуатационные расходы.
Проблема износа гребней колёс и бокового износа рельсов в последние годы является одной из наиболее острых на железных дорогах России и других стран мира. Анализ статистических данных показал, что основными причинами отбраковки колесных пар подвижного состава являются износ и подрез гребня, а также возникновение остроконечного наката.
Интенсивный износ поверхностей в зоне контакта колесо-рельс обусловлено характером взаимодействия пути и тягового подвижного состава (ТПС) и зависит от состояния экипажа ТПС и параметров рельсовой колеи.
1.2. Основные неисправности и причины износа колесных пар.
Техническое содержание и основные требования, предъявляемые к колесным парам в эксплуатации:
1.2.1 Колесные пары для определения их технического состояния и пригодности к эксплуатации подвергаются осмотру с регистрацией в книге формы ТУ-28:
- под ТПС — при всех видах технических обслуживании и текущих ремонтов ТР-1, ТР-2, каждой проверке ТПС в эксплуатации;
- при первой подкатке под ТПС новой колесной пары (после формирования) и после производства полного освидетельствования, если после них прошло не более 2 лет. При этом проверка даты формирования и освидетельствования производится по клеймам на торце (бурте) оси;
- после крушений, аварий, схода с рельсов, если отсутствуют повреждения элементов колесной пары, требующие их замены.
1.2.2. Осмотр колесных пар под ТПС должны производить:
- машинист — при каждой приемке и сдаче ТПС (локомотивов в доступных местах, доступных местах по доступной осмотру стороне); - в эксплуатации при стоянках локомотивов на станциях и в пунктах оборота; при техническом обслуживании ТО-2 ТПС (в случае производства последнего локомотивными бригадами);
- мастер — при техническом обслуживании ТО-3 ТПС;
- мастер или бригадир (где смены слесарей возглавляет бригадир) — при техническом обслуживании ТО-2 ТПС (в случае производства ТО-2 ремонтными бригадами пункта технического обслуживания);
- мастер и приемщик локомотивов — при техническом обслуживании ТО-4, ТО-5, текущих ремонтах ТР-1 и ТР-2 ТПС, при первой подкатке новых колесных пар.
1.2.3. При осмотре колесных пар проверять:
- на бандажах и ободьях цельнокатаных колес — отсутствие трещин, ползунов (выбоин), плен, раздавленностей, вмятин, отколов, раковин, выщербин, ослабления бандажей на ободе центра (остукиванием молотком), сдвига бандажа (по контрольным меткам на бандаже и ободе центра), предельного проката (предельной высоты гребня) или износа, вертикального подреза гребня, ослабления бандажного кольца, опасной формы гребня и остроконечного наката, являющегося признаком возможности опасной формы гребня.
Предельный прокат (предельная высота гребня) и наличие опасной формы гребня проверяются шаблоном УТ-1 при технических обслуживаниях ТО-2 (при их выполнении в крытых помещениях), ТО-3, ТО-4, ТО-5, текущих ремонтах ТР-1, ТР-2 и ежемесячных обмерах колесных пар. Допускается при проведении технического обслуживания ТО-2 контролировать опасную форму гребня шаблоном ДО-1. После выявления колес с опасной формой гребня с помощью этого шаблона необходимо шаблоном УТ-1 измерить величину этого параметра и по результатам этого измерения принимать решение о допуске их к эксплуатации или о назначении ремонта;
- на колесных центрах, цельнокатаных колесах и ступицах дискового тормоза — отсутствие трещин в спицах, дисках, ступицах, ободьях, признаков ослабления или сдвига ступиц на оси;
- на открытых частях осей — отсутствие поперечных, косых и продольных трещин, плен, протертых мест, электроожога и других дефектов;
- отсутствие нагрева букс;
- состояние зубчатой передачи тяговых редукторов ТПС (при текущих ремонтах, когда это предусмотрено по циклу);
- отсутствие нагрева моторно-осевых подшипников, опорных подшипников тяговых редукторов при постановке ТПС на смотровую канаву.
1.2.4. В соответствии с ПТЭ номинальное расстояние между внутренними гранями колес у ненагруженной колесной пары должно быть 1440 мм. У локомотивов и вагонов, обращающихся в поездах со скоростью:
- до 120 км/ч отклонения допускаются в сторону увеличения и уменьшения не более 3 мм;
- от 120 км/ч до 140 км/ч отклонения допускаются в сторону увеличения не более 3 мм и в сторону уменьшения не более 1 мм.
1.2.5. В соответствии с ПТЭ запрещается выпускать из ТО-2, ТО-3, текущих ремонтов и допускать к следованию в поездах подвижной состав с трещиной в любой части оси колесной пары, ободе, диске, спице, ступице и бандаже, а также при следующих износах и повреждениях колесных пар, нарушающих нормальное взаимодействие пути и подвижного состава.
1.2.5.1. При скоростях движения до 120 км/ч:
- при прокате по кругу катания у локомотивов, а также у моторвагонного подвижного состава дальнего следования — более 7 мм, у моторвагонного подвижного состава в поездах местного и пригородного сообщения — более 8 мм;
- при высоте гребня бандажа, измеряемого шаблоном УТ-1, более 37 мм или менее 27 мм для колес локомотивов с профилем по рисунку 15; более 35 мм или менее 27 мм для колес локомотивов с профилями ДМеТИ и МВПС дальнего сообщения; более 36 мм или менее 27 мм для МВПС местного и пригородного сообщения; более 39 мм или менее 27 мм для колес локомотивов с профилем Зинюка-Никитского;
- при толщине гребня более 33 мм или менее 25 мм, измеряемой на расстоянии 20 мм от вершины гребня — для колес локомотивов;
- при толщине гребня более 34 мм или менее 25 мм, измеряемой шаблоном УТ-1 в сечении гребня, расположенном на расстоянии 13 мм от поверхности круга катания колеса.
1.2.5.2. При скоростях движения от 120 км/ч до 140 км/ч:
- при прокате по кругу катания у локомотивов, моторвагонного подвижного состава более 5 мм;
- при высоте гребня бандажа, измеряемого шаблоном УТ-1, более 35 мм или менее 27 мм для колес локомотивов с профилем по рисунку 15; более 33 мм или менее 27 мм для колес локомотивов с профилями ДМеТИ и МВПС; более 37 мм или менее 27 мм для колес локомотивов с профилем Зинюка-Никитского;
- при толщине гребня более 33 мм или менее 25 мм, измеряемой на расстоянии 20 мм от вершины гребня — для колес локомотивов с чертежной высотой гребня 30 мм и на расстоянии 18 мм от вершины гребня колес с чертежной высотой гребня 28 мм;
- при толщине гребня более 34 мм или менее 25 мм, измеряемой шаблоном УТ-1 в сечении гребня, расположенном на расстоянии 13 мм от поверхности круга катания колеса.
1.2.5.3. При вертикальном подрезе гребня высотой более 18мм. Контроль вертикального подреза гребня бандажа и опасной формы гребня производится специальным шаблоном (рис. 2) и шаблоном ДО-1. Измерение опасной формы гребня у ТПС производится универсальным измерительным шаблоном УТ-1.
Рис. 2. Шаблон для контроля вертикального подреза гребня бандажа
а) Гребень бракуется
б) Гребень не бракуется
1.2.5.4. При ползуне (выбоине) на поверхности катания у локомотивов, моторвагонного подвижного состава более 1,0 мм.
При обнаружении в пути следования у прицепного вагона МВПС ползуна (выбоины) глубиной более 1,0 мм, но не более 2,0 мм, разрешается довести его без отцепки от поезда со скоростью не выше 100 км/ч до ближайшего локомотивного депо.
При наличии ползуна на колесных парах локомотивов и МВПС допускается их следование без отцепки от поезда до ближайшей станции со скоростью указанной в таблице 1, где колесные пары с ползунами должны быть заменены.
Таблица 1
Колесная пара | Глубина ползуна, мм | Допускаемая скорость следования, км/ч |
локомотива и моторного вагона МВПС | 1—2 | 15 |
2 — 4 | 10 | |
более 4 | Передвижение локомотива (вагона) без качения колесных пар с ползунами по рельсам* | |
прицепного вагона МВПС | 2 — 6 | 15 |
6—12 | 10 | |
более 12 | Передвижение вагона без качения колесных пар с ползунами по рельсам* | |
* При этом колесные пары должны быть вывешены или транспортированы другим способом, обеспечивающим указанное передвижение. Локомотив должен быть отцеплен от поезда, тормозные цилиндры и тяговый электродвигатель (группа двигателей) поврежденной колесной пары (колесных пар) отключены. Транспортироваться до места смены колесной пары локомотив должен в одиночном следовании. Для вывода с перегона локомотивов с двухосными тележками следует использовать специальные транспортные тележки. Вывешивать колесные пары на локомотивах с такими тележками для вывода локомотива с перегона — запрещается. |
В таблице 2 приведена длина ползуна в зависимости от его глубины и диаметра колеса.
Таблица 2
Диаметр колес по кругу катания, мм | Длина ползуна при его глубине, мм | ||||||||||||
0,5 | 1 | 2 | 3 | 4 | 5 | 6 | 7 | 8 | 9 | 10 | 11 | 12 | |
1250 | 50 | 71 | 100 | 122 | 141 | 158 | 173 | 186 | 199 | 211 | 223 | 233 | 244 |
1220 | 49 | 70 | 99 | 121 | 139 | 156 | 171 | 184 | 197 | 209 | 220 | 231 | 241 |
1050 | 46 | 65 | 92 | 112 | 129 | 145 | 158 | 171 | 183 | 194 | 204 | 214 | 223 |
950 | 44 | 62 | 87 | 107 | 123 | 137 | 151 | 162 | 174 | 184 | 194 | 203 | 212 |
1.2.6. Запрещается выдавать в поезда ТПС с колесными парами, имеющими хотя бы один из следующих дефектов или отступлений:
- выщербину, раковину или вмятину на поверхности катания глубиной более 3,0 мм и длиной: у локомотива и моторного вагона более 10,0 мм, а у прицепного вагона более 25,0 мм;
- выщербину или вмятину на вершине гребня длиной более 4,0 мм;
- разницу прокатов у левой и правой стороны колесной пары более 2 мм;
- ослабление бандажа на колесном центре, зубчатого колеса на оси или ступице колесного центра, пальцев тягового привода в отверстиях приливов колесного центра, цельнокатаного колеса или колесного центра на оси;
- опасную форму гребня (параметр крутизны — менее 6,0 мм для профилей с чертежной высотой гребня 30 мм и более; и менее 5,5 мм — для профилей с чертежной высотой гребня 28,0), измеряемую универсальным шаблоном УТ-1;
- остроконечный накат гребня в зоне поверхности на расстоянии 2 мм от вершины гребня и до 13 мм от круга катания;
- толщину гребня более 23 мм и менее 21 мм у 2-й и 5-й колесных пар электровозов ЧС2, ЧС2т, ЧС4, ЧС4т (до № 263) при измерении на расстоянии 16,25 мм от вершины гребня и более 24 мм и менее 19,5 мм при измерении шаблоном УТ-1;
- острые поперечные риски и задиры на шейках и предподступичных частях осей;
- протертое место на средней части оси локомотива глубиной более 4,0 мм, а на оси моторвагонного подвижного состава — более 2,5 мм;
- местное или общее увеличение ширины бандажа или обода цельнокатаного колеса более 6,0 мм;
- ослабление бандажного кольца более, чем в 3-х местах: по его окружности суммарной длиной ослабленного места более 30 % общей длины окружности кольца — для локомотивов и более 20 % для МВПС, а также ближе 100 мм от замка кольца;
- толщину бандажей колесных пар менее (мм):
- тепловозов с нагрузкой на ось 23 т и выше— 40;
- тепловозов с нагрузкой на ось менее 23 т — 36;
- моторных вагонов моторвагонного подвижного состава — 35;
- толщиной ободьев цельнокатаных колес менее (мм):
- тепловозов ТГМ (ТГМ-3, ТГМ-4, ТГМ-6) — 30;
- прицепных вагонов моторвагонного подвижного состава — 25;
- трещины в ободе, диске, ступице и бандаже колеса ТПС;
- кольцевые выработки на поверхности катания у основания гребня глубиной более 1,0 мм, на конусности 1:3,5 более 2,0 мм и шириной более 15,0 мм.
При наличии кольцевых выработок на других участках поверхности катания бандажа нормы браковки — как для кольцевых выработок, расположенных у гребня.
1.2.7. Обнаруженные дефекты при осмотре колесных пар под ТПС должны записываться в журнал технического состояния локомотива ТУ № 152 и в книгу записи ремонта.
1.2.8. У колесных пар на каждом техническом обслуживании ТО-3 и плановом ремонте, но не реже одного раза в течение календарного месяца производить измерения проката (высоты гребня), толщины бандажей (ободьев цельнокатаных колес), толщины гребней, параметра крутизны (опасной формы) гребня и диаметра бандажей (колес). В случае, если конструкция ходовых частей ТПС не позволяет производить непосредственное измерение диаметра бандажей без их демонтажа, допускается вместо обмера производить оценку диаметров расчетным способом, исходя из толщины бандажа и диаметра колесного центра. В случае обточки бандажей без выкатки и перенодкатки колесных пар измерения обточенных и замененных колесных пар проводятся как до, так и после обточки (переподкатки). Результаты замеров следует заносить в книгу в соответствии с формой, утвержденной МПС России. Замеры должны выполняться работником, назначенным начальником депо, после сдачи им экзаменов комиссии депо на знание настоящей Инструкции.
Периодичность контрольных обмеров колесных пар начальниками депо, их заместителями и приемщиками локомотивов устанавливается начальником службы локомотивного хозяйства в зависимости от положения с износом гребней бандажей в различных депо дороги.
1.3. Обоснование необходимости упрочнения гребней колесных пар.
С середины 80-х годов на отечественных железных дорогах обострилась проблема износа колес и рельсов, не потерявшая своей актуальности и в настоящее время.
Среди причин, вызвавших падение износостойкости колес и рельсов, называли следующие: завершение перешивки колеи на ширину 1520 мм; насыщение железнодорожного пути рельсами утвержденного в 1979 г. профиля, предусматривающего наличие двухточечного контакта профиля катания колеса с головкой рельса; снижение в эксплуатации количества вагонов, работающих на подшипниках скольжения, и уменьшение в связи с этим естественной смазки рельсов; активное внедрение интенсивных технологий, связанных с увеличением статической нагрузки на ось грузового вагона, увеличением массы и длины поездов, распространением кратной тяги, вождением сдвоенных поездов, и многие другие.
Однако подобные изменения в параметрах железнодорожной продукции и условиях движения были присущи железнодорожному транспорту на протяжении практически всей истории его развития и ни в отдельности, ни в совокупности не способны объяснить обвальное падение износостойкости колес и рельсов. До сих пор не развиты физические представления, которые объяснили бы, почему после замены в кривых сырых рельсов объемнозакаленными, имеющими на 25 % большую твердость, износ рельсов в несколько раз превысил нормативный и почему колеса пассажирских вагонов, для которых не использовались интенсивные технологии типа увеличения нагрузки на ось либо кратной тяги, стали служить в среднем в 6 раз меньше из-за внеплановых обточек (данные отделения вагонного хозяйства ВНИИЖТа). Вопрос о причинах повышенного износа колес и рельсов остается открытым.
Рис.3. Схема контакта колесо-рельс:
Р – вертикальная нагрузка; Р(х) – распределение давлений в зоне контакта колесо-рельс; 2 w – ширина контакта колесо-рельс; w – глубина зоны пластической деформации.
Колесные пары являются основными элементами ходовой части и наиболее ответственными узлами подвижного состава железных дорог. Железнодорожные колеса реализуют функции:
· обеспечения перемещения экипажа относительно рельсов, что связано с восприятием конструкцией колеса значительных статических и переменных нагрузок;
· обеспечения качения колеса с продольным и поперечным проскальзыванием относительно поверхности рельса в условиях контактных давлений, превосходящих предел текучести колесной стали;
· выполнения поверхностью катания роли «тормозного барабана», воспринимающего нагрев и охлаждение с высокой скоростью, а также высокие напряжения сдвига и сжатия при значительном разогреве металла бандажа колес.
Взаимодействие колеса и рельса вызывает комплекс явлений на их поверхности, приводящий в конечном счете к ее разрушению. Качение колеса по рельсу с проскальзыванием вызывает в основном два процесса: объемную пластическую деформацию (смятие), протекающую в условиях статических, мало- и многоцикловых нагрузок, нормальных и касательных по отношению к пятну контакта, в широком интервале температур, и истирание, обусловленное скольжением в системе колесо - рельс.
Объемная пластическая деформация (смятие) неравномерна по глубине от поверхности катания, достигает наибольших величин непосредственно у поверхности и сокращается по мере удаления от нее. Величина и характер деформации зависят от термомеханических свойств колесных и рельсовых сталей, циклической упрочняемости либо разупрочняемости этих сталей, соотношения нагрузок и циклических пределов текучести материалов, а также от температуры.
Под истиранием понимается комплекс физико-механических и физико-химических процессов, включающих:
· перемещение материала, вызванное смещающей нагрузкой, включая микросрез;
· образование и отделение межповерхностных точек сцепления — схватывание;
· усталость и образование трещин на поверхности, обусловленные трибологическими переменными нагрузками, приводящими к отделению материала;
· химические реакции, в частности окисления;
· пластинчатый сдвиг участков поверхности, обусловленный образованием трещин под поверхностью из-за пластической деформации.
Всем перечисленным процессам разрушения поверхности катания при истирании предшествует пластическая деформация. Подавление пластической деформации в условиях эксплуатации за счет регулирования состава и параметров микроструктуры колесных и рельсовых сталей является основой повышения их износостойкости.
Условия качения колеса по рельсу, определяющие условия пластического деформирования и вследствие этого и износа, существенным образом зависят от свойств материалов колеса и рельса. При этом в отличие от прочностных свойств, являющихся характеристиками материала, износ является характеристикой трибологической системы колесо-рельс и потому определяется взаимодействием ее элементов.
В системе колесо-рельс осуществляется упругопластический контакт на уровне взаимодействия как в макромасштабе, так и на уровне шероховатости поверхностей катания, для которого существенны физико-химическое состояние поверхностей (наличие на поверхности контакта влаги, масла, грязи, снега и т. д.), механические свойства менее жесткого из взаимодействующих тел и шероховатости более жесткого тела. Важнейшей механической характеристикой колесных, бандажных и рельсовых сталей, определяющей их износостойкость, является твердость. Твердость представляет собой комплексное свойство материала, отражающее его способность оказывать сопротивление механическому проникновению в него другого материала.
При движении колеса по рельсу микронеровности на его поверхности внедряются в поверхность рельса и передают ей крутящий момент локомотива либо момент, возникающий при перекатывании ведомых колес. В зависимости от соотношения твердостей колесной и рельсовой стали могут реализовываться два основных варианта:
а) твердость колесной стали существенно выше рельсовой. Происходит внедрение микронеровностей поверхности колеса в относительно мягкую опорную поверхность и макровнедрение конусообразной поверхности колеса в рельс по эллиптической поверхности контакта;
б) твердость рельсовой стали равна или более твердости колесной. В этом случае проникновение идет в сторону колеса и сопротивление проскальзыванию происходит только за счет взаимодействия микронеровностей на плоских поверхностях колеса и рельса.
Такое макровнедрение весьма существенно при передаче крутящего момента для обеспечения сцепления колеса с рельсом.
Рис.4. Макровнедрение и проскальзывание в трибосистеме колесо-рельс:
а – твердость колеса выше твердости рельса; б – твердость рельса выше твердости колеса.
Для вариантов типа «б» условия сцепления существенно хуже, чем для типа «а». При этом если в условиях примерного равенства твердостей может происходить передача крутящего момента и осуществляться какое-то сцепление, то в случае более мягкого колеса должно происходить смятие микронеровностей на его поверхности и развиваться значительное скольжение в системе колесо-рельс.
Таким образом, увеличение твердости рельса до уровня, превышающего твердость колеса, должно приводить к ухудшению сцепления и облегчению проскальзывания.
С внедрением объемнозакаленных рельсов, существенно более твердых, чем железнодорожные колеса (колеса по ГОСТ 10791 при меньшем содержании углерода имеют твердость в среднем меньшую на 30 % твердости рельсов по ГОСТ 18267), сцепление колеса и рельса резко упало.
Из трибологии известно, что скорость истирания существенным образом зависит от того, какие из его механизмов, перечисленных выше, задействованы в конкретных условиях эксплуатации. В зависимости от скорости истирания различают нормальный, интенсивный и катастрофический износ. Главным параметром, по которому различаются эти виды износа, является величина проскальзывания при качении колеса по рельсу, без которого истирание не реализуется. В условиях эксплуатации величина проскальзывания варьируется от нуля до 100 %. Лабораторные эксперименты обычно проводятся при фиксированной величине проскальзывания.
Получено, что для нормального износа при проскальзывании до 2 % минимальный износ наблюдается для соотношения твердостей в системе колесо – рельс 1,2 : 1, т. е. при 20 %-ном превышении твердости колеса над твердостью рельса. При этом при широком варьировании твердостей элементов системы суммарный износ меняется слабо. Для существующего в настоящее время соотношения твердостей 300 НВ колесо – 350 НВ рельс износ колес в 5 раз превышает износ рельсов.
Для повышенного износа при проскальзывании 10 % получено: при существующей твердости рельсов на уровне 350 НВ с увеличением твердости колес от 280 до 350 ... 370 НВ износ колесных роликов уменьшается более чем в 6 раз, а износ рельсовых - практически не меняется.
Для катастрофического износа, соответствующего юзу или боксованию, имеющиеся экспериментальные данные показывают, что с увеличением твердости колеса склонность к проскальзыванию уменьшается.
При существующем положении, когда с применением объемнозакаленных рельсов в сочетании с мягкими колесами сцепление колес с рельсами является чисто условным и проскальзывания в системе колесо-рельс в продольном и поперечном направлениях не ограничены, переход от одной стадии износа к другой происходит неконтролируемо. Предсказать результаты износа в такой ситуации практически невозможно, износостойкость колес и рельсов в этих условиях может изменяться без видимых причин не только в десятки, но и сотни раз, что в настоящее время и наблюдается на сети дорог.
Соотношение твердости колесной и рельсовой стали, поэтому представляется одной из важных эксплуатационных характеристик. Довольно продолжительное время оптимальным с точки зрения износа считалось превышение твердости колес и бандажей над рельсами на 20 %.
Рис.5. Зависимость нагрузки заедания от твердости колесного и рельсового роликов при испытании в условиях чистого скольжения на воздухе.
В настоящее время объемнозакаленные в масло рельсы твердостью 341...388 НВ (ГОСТ 18267) работают в контакте с цельнокатаными колесами (ГОСТ 10791) и бандажами (ГОСТ 398), имеющими при меньшем содержании углерода твердость в среднем меньшую на 30 % (60...80 НВ) при средней твердости обода 260...280 НВ. В эксплуатации эта разница доходит до 40 % (240...388 НВ). С точки зрения изложенных выше представлений такое соотношение губительно как для колес, так и для рельсов.
Повышение износостойкости колес – сложный многофакторный процесс, требующий для своего решения комплексного подхода. В то же время первым и естественным шагом к решению данной проблемы является ликвидация сложившегося соотношения твердостей. Возможны два пути.
Первый путь связан с возвратом к сырым (не термообработанным) рельсам. Это привело бы к существенному сдвигу в соотношении твердости колеса и рельса и позволило бы реализовать оправданное отечественной и зарубежной практикой превышение твердости колеса над твердостью рельса, восстановить сцепление колеса с рельсом.
Второй путь – ликвидация различий по твердости в сторону объемнозакаленных рельсов. Проведенные в последние годы эксперименты по развитию технологий упрочнения гребней колес и лубрикации боковых поверхностей гребней колес и головок рельсов показали плодотворность данного направления в части повышения износостойкости колесных пар.
Более рациональным представляется организация производства железнодорожных колес как цельнокатаных, так и бандажных термоупрочненных на значительную глубину от поверхности катания до твердости, не уступающей объемнозакаленным рельсам и поддержание этой твердости в процессе эксплуатации.
1.4. Виды упрочнения.
Существуют несколько способов закалки гребней колес, которые классифицируются по способу нагрева и охлаждения.
Можно выделить шесть основных способов нагрева:
· объемный нагрев в печах;
· индукционный нагрев токами высокой частоты;
· нагрев низкотемпературной плазмой (3000 °С), получаемой с помощью химических реакций;
· нагрев высокотемпературной плазмой (15000°С), получаемой с помощью электротока;
· электроконтактный нагрев;
· нагрев лазерным лучом.
Нагрев под закалку всеми способами, кроме первого, может осуществляться как путем непрерывно-последовательного перемещения вдоль окружности колеса локально нагретого участка, так и путем одновременного нагрева сразу всего гребня.
Охлаждение может быть также непрерывно-последовательным и одновременным.
Возможны два способа охлаждения:
· свободным отводом тепла во внутренний объем металла;
· принудительным охлаждением какой-либо охлаждающей средой.
Рассмотрим преимущества и недостатки каждого из способов охлаждения в отдельности.
Принудительный отвод тепла с помощью охлаждающей среды. Данный способ, позволяющий закаливать гребни на глубину 4...5 мм, и хорошо применим для упрочнения вагонных колес при изготовлении на заводах и после обточек в вагонных депо. Недостатком является сложность применения способа для закалки колес под локомотивом.
Закалка отводом тепла во внутренние слои метала. Такая закалка в последнее время получила широкое распространение из-за своей простоты и возможности использования сравнительно дешевого маломощного оборудования и достаточно высокой производительности. Основной недостаток этого способа состоит в том, что он не позволяет получить на стандартной колесно- бандажной стали закаленный слой толщиной более 2,5 мм. Толщина слоя лимитируется теплотехническими свойствами стали. При увеличении толщины до 2 мм твердость на поверхности снижается от 700...800 до 350...450 НV. Оптимальный режим прогрева достигается при плотности потока мощности через поверхность 15...20 Вт/мм2. Такую плотность позволяют создать три способа: электроконтактный; плазменный; нагрев лазерным лучом. Расчеты и опыт использования этих способов показывают, что для промышленной закалки гребней колес достаточно, чтобы мощность установки была 15...30 кВт. Распределение твердости по сечению гребня и максимальная твердость при закалке отводом тепла во внутренний объем не зависят от способа нагрева и определяются только толщиной прогретого слоя.
В настоящее время в вагонных и локомотивных депо работают установки плазменной закалки гребней колесных пар, в основу которых положено несколько различных технических решений, отличающихся лишь режимом закалки, параметрами закаленного слоя, температурой плазмы, мощностью, рабочим газом и др. Разрабатываются электроконтактные, лазерные и другие способы обработки гребней, которые часто не только не приводят к желаемому результату, но и опасны. Настала острая необходимость в теоретическом обосновании, классификации методов поверхностного упрочнения, разработке способов их оценки и сравнения эффективности. Эту работу провели специалисты ВНИИЖТ.
1.5. Результаты исследований.
В работе были исследованы триботехнические характеристики гребней колес подвижного состава, обработанных по различным технологиям до и после эксплуатации:
плазменно-дуговое упрочнение с магнитным управлением дугой (магнитоплазменное упрочнение, далее МПУ);
плазменно-дуговое упрочнение двумя дорожками (ПДД);
плазменно-пламенное упрочнение (ППУ);
закалка ТВЧ (опытная партия колес);
лазерная закалка (опытная партия колес);
электродуговое упрочнение (ЭДУ);
специальная антифрикционная механическая обработка (САМО - натирание гребня бронзовым стержнем в специальной среде, опытная партия колес).
Параметры упрочненного слоя после различных обработок представлены в таблице 3.
Таблица 3.
Вид упрочнения
| Параметры упрочненного слоя на гребнях колес | ||
Твердость, HV | Глубина слоя, мм | Ширина слоя, мм | |
САМО | 320 | - | 30 |
МПУ | 860 | 0,7 | 40 |
МПУ после эксплуатации | 650 | 0,5 | 40 |
ППУ | 600 | 1,2 | 60 |
ПДД на дорожке | 600 | 0,8 | 45 |
ПДД между дорожками | 370.. .400 | 0,5 | |
ТВЧ | 570 | 3 | 30 |
Лазер | 800 | 0,8 | 30 |
ЭДУ | 1050 | 0,4 | 40 |
После обточки | 350.. .400 | 0,02.. .0,05 | |
После фрезеровки | 340... 620 | 0,02.. .0,2 |
После всех обработок, за исключением САМО, гребни имели у поверхности структуру мартенсита, который плавно переходил в троостит при всех видах плазменного упрочнения (рис.5.), а также при закалке ТВЧ и резко обрывался, переходя сразу в сорбит на образцах с лазерным упрочнением и ЭДУ. Между дорожками при ПДД получалась мартенситно-ферритная структура неполной закалки. После САМО структура и твердость гребней практически не отличались от гребней после обточки.
Рис.6. Распределение микро твёрдости по толщине упрочненного слоя гребня.
На обычных колесах после изготовления также имеется тонкий упрочненный слой. На бандажах, обточенных резцом, твердость на глубине 0,02 мм повышена на 50...100 HV0,1 (до 350...370 HV0,1). После фрезеровки на станке КЖ-20 толщина упрочненного слоя достигает 0,1 мм, а твердость в отдельных точках на глубине 0,02 мм — 620 HV0,1 (нижний индекс – нагрузка на индентор, кгс). Однако это упрочнение неравномерное, упрочненные участки чередуются с не упрочненными.
В процессе эксплуатации рабочие поверхности колес сильно упрочняются. Характер упрочнения поверхностей катания и гребней разительно отличается. На поверхности катания (исключая ползуны и белые пятна) металл наклепан до твердости 400...450 HV0,1. Твердость медленно снижается, выходя на равномерный уровень на глубине 5...8 мм.
Микро твёрдость, измеренная на наклонной поверхности гребней вагонных колес, составляет 650...850 HV0,1 и быстро снижается до 450 HV0,1 на глубине 0,01 мм. На глубине 0,3...0,4 мм твердость уже не отличается от исходной. На поверхности гребней локомотивных колес твердость еще выше благодаря тонким белым слоям (рис. 7), возникающим, по-видимому, при трении о тормозную колодку. Их твердость у поверхности достигает 1200 HV0,1.
Рис.7. Микроструктура поверхностного слоя гребней колес (х300) после эксплуатации на Свердловской дороге: a — вагонного; б — локомотивного.
Для экономии металла и увеличения ресурса колес был опробован метод закалки колес МПУ без предварительной обточки. За период между обточками гребень может быть повторно закален 2...3 раза, что значительно увеличило срок службы колеса. В процессе нагрева при закалке наклепанного в эксплуатации слоя происходит быстрая рекристаллизация деформированной структуры, что приводит к измельчению зерна, увеличению пластичности с одновременным снижением твердости, остаточных напряжений и глубины закаленного слоя (см. таблицу 3).
Рис.8. Зависимость средней толщины гребней колес пассажирского поезда «Россия» от пробега (начальная толщина всех гребней условна приведена к средней 32,3 мм):
1 – лазерная закалка; 2 – плазменная закалка; 3 и 4 –сравнительные.
Определение износостойкости гребней. При выборе метода оценки влияния различных обработок на стойкость гребней колес подвижного состава к изнашиванию остановились на схеме чистого скольжения ролика из рельсовой стали по рабочей поверхности гребней. Такая схема имеет отличие от эксплуатационной, она позволяет испытывать натурные поверхности гребней, в том числе бывших в эксплуатации. Кроме того, увеличение проскальзывания до 100 % ужесточает режим испытания, что позволяет получать данные с гарантированным запасом по износостойкости. Испытания проводились на машине СМТ-1. В темплете шириной 10 мм, вырезанном из гребня колеса, сверлилось отверстие, с помощью которого он закреплялся на верхнем неподвижном валу машины так, чтобы рабочая поверхность располагалась перпендикулярно направлению приложения нагрузки. На нижнем валу крепился ролик диаметром 40 мм из рельсовой стали, который прижимался к гребню с усилием 600 Н и вращался со скоростью 100 оборотов в минуту. Такой метод обеспечивал «заедание» в первом периоде испытания, которое после увеличения площади и снижения контактного давления переходило в нормальный износ. В ходе испытания постоянно замерялись длина лунки износа на гребневом образце, диаметр рельсового контроля, коэффициент трения. Момент прекращения заедания легко определялся по изменению угла наклона кривой, характеризующей длину лунки износа от числа оборотов рельсового ролика, а также по внешнему виду поверхности трения. Метод позволяет определить критические давления и величину износа гребней, при которых прекращается заедание (величину прибавочного износа), а также число оборотов, необходимое для полного изнашивания упрочненного слоя.
Кривые зависимости длины лунки и уменьшения диаметра рельсового ролика от числа оборотов последнего представлены на рис. 9 и 10.
Рис.9. Зависимость длины лунки износа на гребневых образцах от числа оборотов после различных обработок:
1 – фрезеровка на КЖ-20; 2 – обточка резцом; 3 – САМО; 4 – с ПДД (между дорожками); 5 – стандартная обработка после эксплуатации; 6 – ПДД (в центре дорожки); 7 – ППУ; 8 – ТВЧ; 9 – лазерное упрочнение; 10 – ЭДУ; 11 – МПУ.
Рис.10. Зависимость износа рельсового ролика от числа оборотов при испытании в паре:
1 – с ЭДУ; 2 – с ПДД (между дорожками); 3 – с САМО; 4 – с фрезеровкой на КЖ-20; 5 – с обточкой резцом; 6 – с ППУ; 7 – с ТВЧ; 8 – с лазерным упрочнением; 9 – с ПДД (в центре дорожки); 10 – с МПУ; 11 – со стандартно обработанным после эксплуатации.
Самый большой износ наблюдался на неупрочненных гребнях. После фрезеровки на станке КЖ-20, несмотря на больший наклеп поверхности, износ был выше, чем после обточки. Причина этого, в сильной неравномерности наклепа при фрезеровке. После САМО износ не изменился. На гребнях после всех упрочняющих обработок заедание не наблюдалось и износ был низким. Самый низкий износ имели образцы после ЭДУ и МПУ (см. рис. 9, кривые 10 и 11). Интересно, что стандартные гребни колес после эксплуатации, несмотря на значительно более тонкий упрочненный слой, имели почти такую же износостойкость, как упрочненные (см. рис. 9, кривая 3), причем коэффициент трения держался на уровне 0,45 вместо 0,58…0,68, как на других образцах. Причина этого в том, что в результате выглаживания грубого рельефа в поверхностном слое на глубине до 1 мм оказываются заделанными загрязнения, оказывающие смазывающее действие. Еще более низкий коэффициент трения — 0,4 — после короткого всплеска в начале испытания устанавливался на образцах после МПУ. Наиболее высокие коэффициенты трения были на образцах с неоднородным упрочнением — ЭДУ и ПДД.
Важной характеристикой является износ контртела, в данном случае рельсового ролика. Категорически недопустимый износ, в несколько раз превышающий износ при заедании стандартных гребней, наблюдался на роликах, испытанных в паре с гребнями после ПДД и в особенности ЭДУ (см. рис. 10, кривые 1 и 2). Износ роликов, испытанных в паре со всеми остальными упрочненными гребнями, в особенности с МПУ (кривые 6… 10), был значительно ниже, чем со стандартными, к которым можно отнести и САМО (кривые 3…5). Износ роликов после испытания с гребнями, бывшими в эксплуатации, был нулевым (кривая 11).
После сравнение различных методов упрочнения показало, что САМО, по существу, не является упрочняющей обработкой. Гребни, упрочненные ТВЧ, лазером, плазмой, имеют близкие характеристики. Плазменная закалка двумя дорожками и электродуговая закалка вызывают высокий износ контртела. Наилучшие результаты показали магнитоплазменное (МПУ) и плазменно-пламенное (ППУ) упрочнения.
Подробнее рассмотрим различные технологии упрочнения, а именно: магнитоплазменную (МПУ), плазменно-дуговую (ПДД), плазменно-пламенную (ППУ), электродуговую (ЭДУ), лазерную, ТВЧ.
Технология ПДД не позволяет получать ширину закаленной зоны, которая бы покрывала всю поверхность гребня. По этой причине возникает необходимость в закалке второй дорожки на поверхности гребня с просветом между дорожками. В этом просвете наблюдается разупрочненная зона. К тому же, при закалке второй дорожки в не которых случаев разупрочняется и предыдущая закаленная дорожка, что не обеспечивает необходимый износостойкости гребня.
Кроме того, глубина закаленного слоя быстро уменьшается от центра к краю дорожки до нуля. Вместе с тем, плазменный генератор, используемый в этой технологии, создает высокий уровень шума, что приводит к необходимости создания звуковой изоляции поста плазменной обработки. А это, в ряде случаев, практически невозможно, например, при работе под локомотивом. Также, в этой технологии в качестве плазмообразующего газа используется азот особой чистоты, который в ряде регионов отсутствует.
Лазерная технология требует громоздкого и дорогостоящего оборудования, а при его эксплуатации – высококвалифицированного персонала, что в условиях депо практически неосуществимо. Глубина закаленного слоя незначительна (0,8 мм) из-за высокого уровня тепловых потоков, создаваемых лазерным лучом на поверхности обработки.
Рис.11. Распределение твердости по сечению закаленного слоя при лазерной закалке с потоком мощности 15…20 Вт/мм2 и скоростей закалки, мм/мин:
1 – 630; 2 – 500; 3 – 380
Технология ППУ также использует азот особой чистоты, но в гораздо большем объеме – 10 нм3/ч. Время упрочнения при этой технологии в 5 – 6 раз больше, чем, например, при МПУ, что приводит к значительным энергозатратам (приблизительно 100 кВт-ч/колесо). Низкая скорость закалки как следствие относительно низких тепловых потоков, реализуемых на поверхности гребня, может приводить к росту зерна закаленного слоя и, соответственно, к снижению его прочностных характеристик.
Высокотемпературная газовая струя, истекающая из щелевой насадки, и два работающих плазменных генератора так же, как и в предыдущем способе, создают высокий уровень шума, что требует звуковой изоляции и затрудняет использование метода ППУ под локомотивом. Глубина слоя закалки по этой технологии также невелика – 1,2 мм.
Технология ЭДУ тоже имеет ряд существенных недостатков. В связи с тем, что тепловое воздействие на металл осуществляется электрической дугой прямого действия, то на его поверхности реализуются значительные тепловые потоки (около 108 Вт/м2), приводящие к уменьшению толщины закаленного слоя и высокой твердости его в приповерхностных слоях. Так, толщина закаленного слоя равна 0,7 мм, т.е. ниже, чем при упрочнении лазером, а твердость – 860 НV.
Высокую твердость обуславливает образование «жестких» мартенситных структур в приповерхностных слоях и, как следствие, повышенные значения напряжений, которые могут приводить к образованию микротрещин. Анодное пятно, в котором происходит основное выделение тепла в процессе закалки при ЭДУ, движется не равномерно по поверхности гребня, а дискретно – с некоторым шагом. При этом происходит подплавление металла в месте «привязки» анодного пятна, что приводит к неоднородности закаленного слоя по ширине и, соответственно, к дополнительной концентрации напряжений.
Кроме того, перечисленные способы упрочнения не позволяют оперативно (в считанные доли секунды) изменять величину теплового потока в материал непосредственно в процессе упрочнения для предотвращения подплавления поверхности, например, в случае внезапного нарушения равномерности вращения колеса, либо при попадании в зону обработки локальных неоднородностей металла (микропор или раковин).
В настоящее время широкое применение для упрочнения гребней колес (в т.ч. и в локомотивном депо) получила технология МПУ с использованием плазменного генератора с вынесенной электрической дугой, управляемой магнитными полями. Эта технология позволяет получать упрочненный слой на всей поверхности гребня за один проход. Глубина закаленного слоя здесь в 3 раза больше, чем при ЭДУ и в 2 раза больше, чем при ППУ, что обеспечивает больший ресурс упрочненного слоя при эксплуатации закаленных бандажей.
В связи с тем, что анодные пятна при сканировании плазменного шнура располагают на поверхности вращающегося анода, то закаленный слой формируется однородным по всей ширине обработки (в отличие от ЭДУ). Расход плазмообразующего газа (азота) составляет 0,35 нм3/ч, что в 20 раз меньше, чем при ПДД и в 30 раз меньше, чем при использовании азота в ППУ. Кроме того, в отличие от вышеназванных технологий используется азот не ОСИ, а технический азот — чистоты 99,5 %.
Шум при истечении плазменной струи из сопла катодного узла ниже, чем в ЭДУ, ППУ, ПДД, что позволяет применять эту технологию без звукоизолирующих систем, как под локомотивом, так и с выкаткой колесных пар. Время обработки одного колеса по этой технологии составляет 6 мин, что в 12 раз меньше, чем при ППУ.
В процессе закалки оператор может с помощью системы магнитных полей точно сориентировать на гребень зону закалки, а также во время самого процесса активно и оперативно изменять интенсивность теплового потока в поверхность гребня (приближая или удаляя плазменный шнур к его поверхности), тем самым избегать подплавления, например, в случае неоднородности металла.
Итак, плазменная технология, использующая плазмотрон с вынесенной электрической дугой, управляемой магнитными полями, имеет вышеперечисленные технологические преимущества перед другими способами закалки и позволяет получать более качественные упрочненные слои на гребнях локомотивных и вагонных колес. По сравнению с другими технологиями предлагаемая позволяет создавать более низкую твердость поверхностного закаленного слоя на всю ширину гребня, что имеет ключевое значение при эксплуатации упрочненных колес.
1.6. Анализ влияния магнитоплазменного упрочнения на интенсивность износа гребней колёсных пар электровозов в локомотивном депо.
Мною был проведен анализ влияния магнитоплазменного упрочнения на интенсивность износа гребней колёсных пар тепловозов в локомотивном депо.
В депо введена в эксплуатацию установка по магнитоплазменному упрочнению гребней бандажей колесных пар локомотивов УМПУ-2. Организация поставщик ВНИИЖТ. Наиболее интенсивно установка использовалась в период с 2006 по 2008 год.
Для анализа было взято 4 электровоза со стандартными колесными парами и 4 электровоза после проведения магнитоплазменного упрочнения гребней колёсных пар.
Замеры колесных пар были взяты из книг ремонта локомотивов формы ТУ-28, пробеги электровозов взяты из книги учета пробегов локомотивов формы ТУ-27.
Интенсивность износа была определена по методике разработанной ВНИИЖТ и утвержденной ЦТ.
Были получены следующие данные:
1.4.1. Локомотивы с упрочненными колёсными парами.
Таблица 4.
Дата замера | № лок | 1 КП | 2 КП | 3 КП | 4 КП | 5 КП | 6 КП |
05.02.09 | 6949 | 31,5 | 31 | 31,5 | 30 | 30 | 30,5 |
30,5 | 30,5 | 31 | 30,5 | 31,5 | 31 | ||
16.04.19 | 6949 | 30,5 | 30,5 | 30 | 29,5 | 28,5 | 30 |
29 | 29 | 30,5 | 30 | 31 | 30 | ||
Износ | 1 | 0,5 | 1,5 | 0,5 | 1,5 | 0,5 | |
1,5 | 1,5 | 0,5 | 0,5 | 0,5 | 1 |
Износ гребней тепловоза – 0,84375 мм
Пробег тепловоза – 28800 км
Таблица 5.
Дата замера | № лок | 1 КП | 2 КП | 3 КП | 4 КП | 5 КП | 6 КП |
21.02.19 | 6546 | 28 | 29 | 31 | 29,5 | 28,8 | 29,5 |
28,5 | 28,7 | 28,7 | 28,5 | 29,5 | 30,5 | ||
07.04.19 | 6546 | 27 | 28,5 | 31 | 28,5 | 28 | 29 |
27 | 27 | 28 | 28 | 29 | 30 | ||
Износ | 1 | 0,5 | 0 | 1 | 0,8 | 0,5 | |
1,5 | 1,7 | 0,7 | 0,5 | 0,5 | 0,5 |
Износ гребней тепловоза – 0,7313 мм
Пробег тепловоза – 21730 км
Таблица 6.
Дата замера | № лок | 1 КП | 2 КП | 3 КП | 4 КП | 5 КП | 6 КП |
05.03.19 | 3288 | 31,5 | 29,7 | 30 | 27 | 27 | 30 |
30,5 | 30 | 30 | 31 | 30,5 | 28 | ||
20.04.19 | 3288 | 30,5 | 28 | 30 | 27 | 27 | 28,5 |
29 | 30 | 30 | 30 | 30 | 28 | ||
Износ | 1 | 1,7 | 0 | 0 | 0 | 1,5 | |
1,5 | 0,5 | 0,5 | 0,5 | 0,5 | 0,5 |
Износ гребня тепловоза – 0,638 мм
Пробег тепловоза –26860 км
Таблица 7.
Дата замера | № лок | 1 КП | 2 КП | 3 КП | 4 КП | 5 КП | 6 КП |
18.01.19 | 7042 | 27 | 30,5 | 29 | 30 | 31,5 | 29 |
30 | 30,5 | 28 | 30 | 30 | 27 | ||
18.03.19 | 7042 | 27 | 30 | 29 | 30,5 | 31 | 28,5 |
29,5 | 30 | 28,5 | 31 | 28,5 | 26,5 | ||
Износ | 0 | 0,5 | 0 | 0,5 | 0,5 | 0,5 | |
0,5 | 1,5 | 0,5 | 1 | 1,5 | 0,5 |
Износ гребней электровоза – 0,46 мм
Пробег электровоза – 25222 км
Износ гребня упрочнённых колёсных пар.
, мм
мм
км
мм.
1.4.2. Локомотивы с не упрочнёнными колёсными парами.
Таблица 8.
Дата замера | № лок | 1 КП | 2 КП | 3 КП | 4 КП | 5 КП | 6 КП |
16.03.19 | 7394 | 32 | 33 | 32,5 | 32 | 32,5 | 32 |
32,5 | 33 | 32,5 | 32 | 32,5 | 32 | ||
29.05.19 | 7394 | 31,5 | 31 | 32 | 31 | 31,5 | 31 |
29,5 | 31 | 30,5 | 30 | 31 | 31 | ||
Износ | 0,5 | 2 | 0,5 | 1 | 1 | 1 | |
3 | 2 | 2 | 1 | 1,5 | 1 |
Износ гребня тепловоза – 1,1875 мм
Пробег тепловоза – 25582 км
Таблица 9.
Дата замера | № лок | 1 КП | 2 КП | 3 КП | 4 КП | 5 КП | 6 КП |
27.03.19 | 6546 | 30 | 30 | 29 | 32 | 32,5 | 32 |
28 | 29 | 31 | 32 | 32,5 | 32 | ||
15.05.19 | 6546 | 30 | 29 | 28,5 | 31 | 31,5 | 31 |
27 | 27,5 | 30 | 30 | 31 | 31 | ||
Износ | 0 | 1 | 0,5 | 1 | 1 | 1 | |
1 | 1,5 | 1 | 1 | 1,5 | 1 |
Износ гребня тепловоза – 1,062 мм
Пробег тепловоза – 24841 км
Таблица 10.
Дата замера | № лок | 1 КП | 2 КП | 3 КП | 4 КП | 5 КП | 6 КП |
21.04.19 | 3213 | 28,5 | 29 | 28,5 | 31 | 28 | 29 |
30,5 | 30,5 | 30,5 | 30,5 | 31,5 | 31 | ||
16.06.19 | 3213 | 27,5 | 28 | 28 | 30,5 | 26 | 28 |
30 | 30 | 30 | 30 | 31 | 31 | ||
Износ | 1 | 1 | 0,5 | 0,5 | 2 | 1 | |
0,5 | 0,5 | 0,5 | 0,5 | 0,5 | 0 |
Износ гребня тепловоза – 0,78 мм
Пробег тепловоза – 20851 км
Таблица 11.
Дата замера | № лок | 1 КП | 2 КП | 3 КП | 4 КП | 5 КП | 6 КП |
10.02.19 | 7441 | 32 | 33 | 28 | 28,5 | 29,5 | 32 |
32,5 | 33 | 28,5 | 26 | 29 | 31 | ||
04.04.19 | 7441 | 31,5 | 31 | 28 | 28 | 27 | 32 |
29 | 31 | 28 | 25 | 28 | 31 | ||
Износ | 0,5 | 2 | 0 | 0,5 | 2,5 | 0 | |
2,5 | 2 | 0,5 | 1 | 1 | 0 |
Износ гребней тепловоза – 0,9813 мм
Пробег тепловоза – 25220 км
Износ гребня не упрочнённых колёсных пар с профилем ГОСТ 11018 – 87
мм.
мм.
км.
мм.
Износ упрочнённых составляет 0,26, не упрочнённых – 0,416.
Для восстановления гребня изношенного по толщине на 1 мм необходимо снять 3 мм металла по толщине бандажа при обточке К.П.
Согласно этому ресурс бандажа в зависимости от износа гребня по толщине рассчитаем по формуле:
км.; где
мм. – разница между начальным и конечным размером толщины бандажа в эксплуатации;
δ – Интенсивность износа гребня колёсных пар за исследуемый период, мм на 10000 км.
Тогда имеем
Средний ресурс бандажа с не упрочненными гребнями, по толщине в зависимости от износа гребня с профилем ГОСТ 11018-87
км.
Средний ресурс бандажа с упрочненными гребнями, по толщине в зависимости от износа гребня с профилем ГОСТ 11018-87
км.
Проведённые расчёты показывают, что средний ресурс бандажа, в зависимости от износа гребня по толщине, колёсных пар с упрочнением больше ресурса бандажа с колёсных пар без упрочнения.
Интенсивность износа гребней бандажей колёсных пар на 10000 км. пробега в соотношении со среднемесячным объёмом работы за 2019 год в локомотивном депо распределилась следующим образом
Таблица 12.
МЕСЯЦ | Интенсивность износа упрочненного гребня | Интенсивность износа не упрочненного гребня | Объем работы ткм.брутто х 106 |
Январь | 0,20 | 0,24 | 2830,2 |
Февраль | 0,19 | 0,23 | 2670,8 |
Март | 0,22 | 0,29 | 3166,8 |
Апрель | 0,29 | 0,31 | 3219,3 |
Май | 0,27 | 0,33 | 3068,3 |
Июнь | 0,26 | 0,34 | 3106,8 |
Июль | 0,25 | 0,36 | 3317 |
Август | 0,26 | 0,31 | 3576,5 |
Сентябрь | 0,29 | 0,34 | 3294,9 |
Октябрь | 0,21 | 0,38 | 3363,4 |
Ноябрь | 0,22 | 0,31 | 3435,2 |
Декабрь | 0,20 | 0,30 | 3673 |
Динамика изменения интенсивности износа гребней колёсных пар локомотивов ЧМЭ3 показана на диаграмме (рис.12)
На рис.13 показан сравнительный износ двух колесных пар первой тележки тепловоза ЧМЭ3, 1 колесная пара стандартная (рис.13, кривая 1), 2 упрочнена на первом ТР-1 после ТР-3 при пробеге 21634 км (рис.13, кривая 2), износ гребней распределился следующим образом:
Таблица 13.
Пробег, тыс. км | 0 | 21,634 | 49,133 | 77,933 | 104,357 | 122,157 |
Износ не упрочненного гребня, мм | 0 | 3,0 | 4,125 | 5,25 | 6,5 | - |
Износ упрочненного гребня, мм | 0 | 3,0 | 3,75 | 4,25 | 5,0 | 6,0 |
Вывод: Упрочнённые колёсные пары по сравнению с не упрочнёнными имеют меньший износ гребней.
Поэтому одной из основных мер по сокращению обточек колёсных пар и увеличению ресурса бандажа в депо применяется упрочнение гребней бандажей колёсных пар.
1.5. Мероприятия для повышения эффективности упрочнения.
Эффективность применения плазменного упрочнения гребней можно существенно повысить, выполнив следующие условия:
· оборудовать отдельное стойло приспособлением для вывешивания и вращения колесных пар локомотивов для проведения магнитоплазменного упрочнения с целью более эффективного использования производительности установки УМПУ-2;
· усилить контроль над своевременностью постановки локомотивов на проведение плазменного упрочнения и определить порядок учета упрочненных колесных пар;
· подвергать упрочнению новые колесные пары после проведения электровозу крупных ремонтов как ТР-3, СР, КР (при пробеге 500 -1000 км после обкатки), а также после обточки колесных пар до полного профиля (толщина гребня 33 мм);
· после проведения упрочнения гребня, при износе упрочненного слоя (2 – 3 мм) во время эксплуатации (2-3 раза), проводить повторное упрочнение без обточки колесной пары.
Эти мероприятия существенно повысят пробег колесной пары между обточками и увеличат ресурс бандажа. Ожидаемый износ после проведения предложенных мероприятий представлен на рис. 14.
Дата добавления: 2021-04-24; просмотров: 1545; Мы поможем в написании вашей работы! |
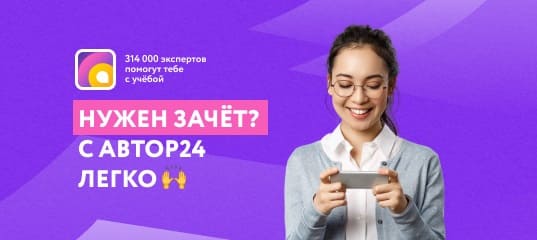
Мы поможем в написании ваших работ!