Основные неисправности при пуске ДВС
Большинство неисправностей при пуске возникает от несоблюдения правил и инструкций по эксплуатации. Любые неполадки в двигателе, даже самые незначительные, должны быть устранены немедленно или при первой возможности.
Выясним некоторые наиболее характерные неисправности при пуске двигателя, их причины и способы устранения.
1. Двигатель не пускается сжатым воздухом или пускается с трудом
При переводе рукоятки управления в положение «Пуск» коленчатый вал не поворачивается. Причинами этого могут быть:
а) не открыт клапан на пусковом баллоне;
б) мало давление пускового воздуха;
в) неправильно установлен воздухораспределитель;
г) заедает шток пускового клапана или заедают золотники воздухораспределителя.
В этих случаях для точного установления причин неисправности следует произвести тщательный осмотр и проверку. Установить, открыт ли клапан на пусковом баллоне, проверить по пусковому манометру давление; если оно достаточно, проверить исправность воздухораспределителя, пускового клапана и уплотнения.
2. Двигатель работает на сжатом воздухе, но не работает или не развивает нужной мощности при переводе на топливо
При переводе рукоятки поста управления в положение «Работа» двигатель перестает работать или не развивает нужную мощность.
Причинами здесь могут быть:
а) топливо не соответствующего качества;
б) в топливную систему попал воздух, который не удален перед пуском;
|
|
в) нет доступа топлива к двигателю (не заправлен бак, закрыт кран бака, засорен фильтр или топливопровод);
г) топливные насосы не подают топлива в рабочие цилиндры или подают в недостаточном количестве;
д) неправильно установлен (меньше нормального) угол опережения подачи топлива;
е) засорен воздухоочиститель, в результате чего в цилиндр попадает мало воздуха;
ж) слабая компрессия вследствие износа или закоксования поршневых колец или неплотного прилегания клапанов к седлам;
з) форсунки плохо распыливают топливо вследствие неправильной затяжки пружин, разработки сопловых отверстий, износа иглы и направляющей.
При низкой температуре машинного отделения текучесть топлива с повышенной вязкостью сильно понижается. Обводненное топливо может также служить причиной затруднений при пуске. Качество топлива следует проверить, пользуясь спускным краном.
Следует проверить, имеется ли в наличии топливо в баке, открыт ли кран, не засорился ли топливный фильтр или топливопровод, и при обнаружении неполадок устранить их.
Одной из частых причин неудачного пуска является скопление воздуха в топливной системе, что можно проверить по воздушному крану в трубопроводе. При вытекании из крана воздуха или топлива с воздушными пузырьками необходима повторная прокачка всех топливных насосов и удаление воздуха из магистрали.
|
|
При неисправности отдельных топливных насосов топливо подается не во все цилиндры. Прежде всего следует проверить плунжеры и приводы топливных насосов на отсутствие заеданий. Далее проверить плунжерные пары на плотность и при необходимости заменить. Следует проверить и в случае необходимости установить угол опережения подачи топлива в соответствии с заводской инструкцией. Если засорен воздухоочиститель, следует его промыть.
Пропуск клапанов обнаруживается по шипению воздуха при сжатии. При обнаружении дефекта, указанного в пункте «ж», следует залить в цилиндры небольшое количество масла (не более 20—30% объема пространства сжатия); в ближайшем длительном бездействии двигателя нужно проверить состояние поршневых колец и клапанов и, при необходимости, заменить часть колец и притереть клапаны.
При обнаружении вышеуказанных дефектов у форсунки устранить эти дефекты, опрессовать форсунку и установить нормальное давление распыливания. Отрегулировать затяжку пружины форсунки на нормальное давление, проверить ее на своем насосе.
|
|
3. Двигатель не развивает нужного числа оборотов
Это может произойти вследствие неправильной установки привода от регулятора к топливным насосам или ослабления, поломки пружины регулятора. Поэтому следует проверить и при необходимости изменить установку привода; если нужно, заменить пружины.
4. Масляный циркуляционный насос не подает масло или давление его недостаточно
Прежде всего следует проверить исправность манометра. Если масляный насос действительно не подает масло или создаваемое им давление недостаточно, то причинами этого могут быть:
а) недостаточное количество масла в картере или баке;
б) неплотность всасывающего трубопровода, вследствие чего подсасывается воздух;
в) засорение сетки приемной трубы масляного насоса;
г) разработка торцовых и радиальных зазоров у рабочих шестерен масляного насоса.
Необходимо проверить уровень масла и, в случае необходимости, добавить его. Следует опрессовать приемный трубопровод и устранить все неплотности. Нужно осмотреть сетку и приемный клапан; при необходимости очистить сетку.
При первой возможности следует опрессовать систему смазки и устранить причины утечки масла (через заглушки коленчатого вала, большие зазоры в мотылевых и коренных подшипниках, соединения шарнирных и телескопических труб охлаждения поршней и пр.). Рекомендуется также снять крышку масляного насоса и проверить торцовые и радиальные зазоры между шестернями и корпусом насоса. В случае необходимости уменьшения торцовых (аксиальных) зазоров у шестерен — заменить прокладку под крышкой более тонкой. При значительном износе шестерен их надлежит заменить новыми.
|
|
Рg180 = - 8.12 • 104.8 = - 81,73 кг / см2 = 11,73мм
EF = - 11,73 = - 11,43
Рис. 1 – Индикаторная диаграмма
Таблица 2 - Таблица динамических показателей (порядок вспышек по цилиндрам
1 – 6 – 2 – 4 – 3 -5).
Φ | Р ПМа | ![]() | Т1 | Т6 | Т2 | Т4 | Т3 | T5 | ΣТ |
0 | 11 | 0 | 0 | -6,35 | -5,28 | 0 | 5,66 | -0,732 | -6,702 |
15 | 7 | 0,322 | 2,254 | -7,50 | -5,41 | -1,42 | 3,77 | 1,030 | -7,276 |
30 | 1 | 0,609 | 0,609 | -7,61 | -5,50 | -2,93 | 2,54 | 2,000 | -10,891 |
45 | -2 | 0,834 | -1,668 | -5,63 | -5,15 | -4,20 | 1,27 | 4,51 | -10,698 |
60 | -0,75 | 0,977 | -0,732 | 0 | -6,35 | -5,28 | 0 | 5,66 | -6,702 |
75 | 1 | 1,030 | 1,030 | 2,254 | -7,50 | -5,41 | -1,42 | 3,77 | -7,276 |
90 | 2 | 1,000 | 2,000 | 0,609 | -7,61 | -5,50 | -2,93 | 2,54 | -10,891 |
105 | 5 | 0,902 | 4,51 | -1,668 | -5,63 | -5,15 | -4,20 | 1,27 | -10,698 |
120 | 7,5 | 0,755 | 5,66 | -0,732 | 0 | -6,35 | -5,28 | 0 | -6,702 |
135 | 6,5 | 0,580 | 3,77 | 1,030 | 2,254 | -7,50 | -5,41 | -1,42 | -7,276 |
150 | 6,5 | 0,391 | 2,54 | 2,000 | 0,609 | -7,61 | -5,50 | -2,39 | -10,891 |
165 | 6,5 | 0,196 | 1,27 | 4,51 | -1,668 | -5,63 | -5,15 | -4,20 | -10,698 |
180 | 6,5 | 0 | 0 | 5,66 | -0,732 | 0 | -6,35 | -5,28 | -6,702 |
195 | -7,25 | -0,196 | -1,42 | 3,77 | 1,030 | 2,254 | -7,50 | -5,41 | -7,276 |
210 | -7,5 | -0,391 | -2,93 | 2,54 | 2,000 | 0,609 | -7,61 | -5,50 | -10,891 |
225 | -7,25 | -0,580 | -4,20 | 1,27 | 4,51 | -1,668 | -5,63 | -5,15 | -10,698 |
240 | -7 | -0,755 | -5,28 | 0 | 5,66 | -0,732 | 0 | -6,35 | -6,702 |
255 | -6 | -0,902 | -5,41 | -1,42 | 3,77 | 1,030 | 2,254 | -7,50 | -7,276 |
270 | -5,5 | -1000 | -5,50 | -2,93 | 2,54 | 2,000 | 0,609 | -7,61 | -10,891 |
285 | -5 | -1,030 | -5,15 | -4,20 | 1,27 | 4,51 | -1,668 | -5,63 | -10,698 |
300 | -6,5 | -0,977 | -6,35 | -5,28 | 0 | 5,66 | -0,732 | 0 | -6,702 |
315 | -9 | -0,834 | -7,50 | -5,41 | -1,42 | 3,77 | 1,030 | 2,254 | -7,276 |
330 | -12,5 | -0,609 | -7,61 | -5,50 | -2,93 | 2,54 | 2,000 | 0,609 | -10,891 |
345 | -17,5 | -0,322 | -5,63 | -5,15 | -4,20 | 1,27 | 4,51 | -1,668 | -10,698 |
Рис 2.Динамические показатели
Конструктивный расчет.
Расчет коленчатого вала
Расчет и конструирование коленчатых валов необходимо производить с особой тщательностью, так как вал представляет собой более нагруженную ответственную и дорогостоящую часть двигателя. Современная тенденция к повышению мощности дизелей приводит к соответственному увеличению напряженности элементов коленчатого вала, поэтому при проектировании необходимо принимать меры к понижению концентрации напряжений а так же к повышению усталостной прочности. Коленчатый вал нагружен силами от давления газов, а так же силами инерции поступательно движущихся и вращающихся частей, вызывающих появление значительных скручивающих и изгибающих напряжений.
Сложная конфигурация напряжений в галтелях, выходах сверлений, местах грубой обработки и т.д. Расчеты коленчатых валов показывают, что наиболее напряженны галтели сопряжения щек с шейками. Запасы прочности в этих местах имеют обычно минимальное значение. Не следует думать что указанные напряжения могут быть уменьшены только за счет увеличения радиуса галтелей.
На величину коэфициэнта концентрация напряжений в галтелях существенное влияние оказывают другие конструктивные параметры вала, например величина перекрытия шеек, диаметр и смещение облегчающего отверстия, бочкообразность отверстий и крутильные колебания, возникающие в судовом валопроводе, которые вызывают дополнительные напряжения кручения.
В виду значительной сложности расчета коленчатого вала ниже приведен только его проверочный расчет по формулам Морского Регистра СССР и проверка шеек на удельную прочность.
Для составления предварительного эскиза коленчатого вала следует воспользоваться конструктивными соотношениями, выработанными практикой судового дизеле строения часть которых дана в табл.17.
Диаметры шеек стального коленчатого вала в любом случае должны удовлетворять размерам, которые определяются формулой Морского Регистра СССР.
d ≥ 0,115K3 +(φts)2
d=0,115*0,693 2 + (5,6*16,9*140)=
d=0,0793 +
d=0,0793
t=8, 5+pi=8,5+8,4=16,9кг/см2
D – Диаметр цилиндра, см.
S – ход поршня, см.
L – расстояние между серединами рамовых шеек, см.
Ф – коэффициент принимается из табл. 18.
Pz – максимальное давление сгорания, кгс/см.
t – амплитуда удельных тангециальных сил цилиндра, t= 8,5+pi.
Конструктивные соотношения элементов коленчатого вала.
Показатель. | Тихоходные. | Быстроходные. |
Расстояние между осями цилиндров двигателя Lц | (1,6 – 1,8)D 1,7*70=105,4 | (1,13 – 1,4)D |
Диаметр шейки кривошипа dк | (0,6 – 0,75)D 0,62*70=38,44 | (0,57 – 0,85)D |
Диаметр рамовой шейки dр | (0,6 – 0,8)D 0,62*70=38,44 | (0,6 – 1,0)D |
Диаметр сверления в шейке d0 | (0,4 – 0,5)d 0,4*70=24,8 | (0,45 – 0,6)d |
Длина шейки кривошипа Lк | (0,5 – 1,1)d 1,1*70=70 | (0,50 – 1,0)dk |
Длина рамовой шейки Lp | (0,40 – 1,0)d 1*70=70 | (0,35 – 1,0)dp |
Толщина щеки кривошипа h | (0,3 – 0,35)D 0,3*70=18,6 | (0,16 – 0,30)D |
Ширина щеки кривошипа b | (0,9 – 1,1)D | (0,9 – 1,5)D |
Радиус галтели r | (0,055 – 0,07)d | (0,055 – 0,07)d |
Примечание D – Диаметр цилиндра таблица 17
K= =
=0,69
Где; предел прочности материала при растяжении, кгс/см2. Значение
принимать в соответствии с маркой стали , из которой предполагают изготовить коленчатый вал. Эти данные имеються в справочниках. При использовании материала с
80
следует принимать
= 80 кгс/см2 толщина кривошипа вала.
h= 0,033K1D
Ψ1=2,32
Ψ2=1,00
K1=0,82
B=1,6*30,89=49,42
С= =
=12,2
h= 0,33*0,82*70 =
h= 1,67772 =11,42см
Где; D – диаметр цилиндра.
Pz – максимальное давление цилиндра кгс/см2
b – ширина щеки см.
С – расстояние от середины рамового подшипника до средней плоскости щеки см.
K1 – коэффициент учитывающий влияние материала вала K=1 – 0,82
Ψ1 – коэффициент принимаемый из табл.19.
r – радиус галтели.
Значение коэффициента
Типы двигателей | Число цилиндров | |||||||
1 | 2 | 3 | 4 | 5 | 6 | 7 | 8 | |
Двухтактные | 4,80 | 4,80 | 5,14 | 5,47 | 5,81 | 6,14 | 6,48 | 6,82 |
Четырехтактные | 4,80 | 4,80 | 5,08 | 5,37 | 5,67 | 5,59 | 6,24 | 6,53 |
Таблица 18
Значение коэффициента Ψ1
r/h | Σ/h | ||||||
0 | 0,2 | 0,4 | 0,6 | 0,6 | 1,0 | 1,2 | |
0,10 | 3,50 | 3,50 | 3,34 | 3,18 | 2,88 | 2,57 | 2,18 |
0,15 | 2,90 | 2,90 | 2,82 | 2,65 | 2,40 | 2,07 | 1,83 |
0,20 | 2,50 | 2,50 | 2,41 | 2,32 | 2,06 | 1,79 | 1,61 |
0,25 | 2,30 | 2,30 | 2,20 | 2,10 | 1,90 | 1,70 | 1,40 |
Примечание; значение |
Таблица 19
Значение коэффициента Ψ2
b/d | 1,2 | 1,3 | 1,5 | 1,8 | 2,0 | 2,2 |
Ψ2 | 0,92 | 0,95 | 1,00 | 1,08 | 1,15 | 1,27 |
b/d – отношение ширины щеки к диаметру вала.
Величина нагрузки на шейку коленчатого вала определяет условие работы подшипников и их срок службы. Очень важно что бы при работе подшипников не происходило выдавливание масляного слоя, разрушение антифрикационного слоя подшипника и ускорение износа шеек коленчатого вала.
Поэтому диаметры шеек вала, полученные по формуле Регистра СССР, должны быть проверены на максимально допускаемое давление определяемое по формулам :
- Для кривошипных шеек
K max= =
Pz=pz кг
Pz=69* 208210,26 кг
K max= =87,36 кг/см2
- для рамовых шеек:
K max= =
54, 60 кг/см2
Где m 1,25 – коэффициент, учитывающий влияние наиболее нагруженного соединения кривошипа: K max
80 – 120 кгс/см2 для тихоходных двигателей : K max
120 – 180 кгс/см2 для быстроходных двигателей. Приведенные пределы значений K max справедливы для подшипников, залитых баббитом б83, с толщиной заливки (0,03 – 0,04)d. В том случае, если предполагается применить тонкостенные вкладыши, залитые свинцовистой бронзой с толщиной заливки (0,04 – 0,06мм), значение K max может быть принято K max
350кгс/см2.
Если принятые размеры шеек удовлетворяют обоим условиям (требованиям регистра и удельное давление) , то в дальнейшем коленчатый вал проверяют по формулам сопротивлениям материалов, рассматривая его как многоопорную балку, нагруженную силами, величина и направление которых изменяются в функции от угла поворота вала. Для упрощения рассчитывается лишь один, наиболее нагруженный кривошип коленчатого вала. Рассматриваемый как абсолютно жесткая балка, лежащая на двух опорах. Расчетные напряжения изгиба при этом получаются несколько выше фактических, что делает расчет более надежным.
Проверку производят в двух опасных положениях: при нахождении расчетного кривошипа на верху и при его повороте на угол фк. При котором касательная сила достигает максимального значения. При проведении проверочного расчета учитывают действие моментов от суммарных касательных сил соседних цилиндров на расчетный кривошип (с носа и кормы).
Методика расчета вала в двух опасных положениях проводится в руководствах по курсовому проектированию.
Заключение.
В расчетную часть входить поверочный расчет малооборотного двигателя внутреннего сгорания 6kz70/120.
Дизельная энергетическая установка в настоящее время является наиболее широко распространенным типом судовых энергетических установок (ДЭУ)
ДЭУ отличается разнообразием технических и конструктивных схем.
Преимущественное применение ДЭУ на судах объясняется главным образом тем, что они обладают наиболее высокой тепловой экономичностью по сравнению с СЭУ других типов. При этом дизельные СЭУ отличаются сравнительно несложным составом вспомогательного оборудования и простотой обслуживания. Устойчивое сохранение эффективного КПД при сравнительно широком диапазоне изменения нагрузок является положительной особенностью ДЭУ.
Дизельные СЭУ делят на установки с малооборотным ДВС (МОД), Дизель – редукторными среднеоборотными ДВС (СОД) , Дизель – электрические установки и установки с высокооборотными ДВС (ВОД).
Большинство судов оборудованы дизельными установками с МОД.
Современные МОД имеют значительные размеры и массу, в связи с чем требуется их размещать в центрально части МО в соответствии с расположением линий валопровода. МОД могут работать на тяжелых остаточных сортах топлив.
Современные судовые СОД имеют массогабаритные показатели лучше, чем у МОД связанно с большими значениями среднего эффективного давления СОД.
К ВОД относят двигатели, достигающие частоту вращения более 750 об/мин.
Высокооборотные двигатели имеют в сравнении с МОД и СОД лучшие массовые стоимые показатели, однако большой удельный расход топлива и масла, меньший ресурс работы и повышенный уровень шума.
Дата добавления: 2021-04-15; просмотров: 223; Мы поможем в написании вашей работы! |
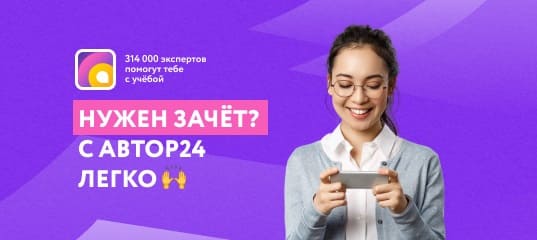
Мы поможем в написании ваших работ!