Стенд для диагностирования сцепления
Экономичность и экологичность автомобильного транспорта
Стенды для диагностирования ДВС
3.1.1 Стенд для диагностирования дизельного ДВС по часовому расходу топлива. На первой стадии проектирования стенда для диагностирования дизельных двигателей были проведены исследования работы дизельного двигателя в исправном состоянии и при наличии неисправностей. В результате было установлено, что статическая характеристика дизельного двигателя, представляющая собой зависимость часового расхода топлива от крутящего момента на его валу, для заданного скоростного режима работы двигателя претерпевает изменения в неисправном дизельном двигателе по сравнению с исправным [12]. Примерный вид полученной зависимости представлен на рисунке 3.1 (кривая 1 соответствует исправному дизельному двигателю, 2 – неисправному). При наличии неисправностей в дизельном двигателе каждому из возможных значений момента на его валу соответствует более высокий часовой расход топлива.
|
|
|

Рисунок 3.1 – Статическая характеристика дизельного двигателя
Изложенное выше дало основание предложить новый метод диагностирования дизельных двигателей на стенде, заключающийся в том, что диагностируемый дизельный двигатель устанавливают на стенд, содержащий электрический тормоз, карданный вал, соединяющий вал двигателя с валом тормоза, снабженный контрольно-диагностической аппаратурой и измерительными приборами с пультом управления, задают скоростной и нагрузочный режимы работы диагностируемого двигателя, измеряют часовой расход топлива и, сравнивая полученное значение расхода топлива с нормативным значением, соответствующим исправному двигателю, принимают решение о техническом состоянии двигателя.
|
|
Для реализации предложенного метода диагностирования дизельного двигателя был разработан стенд, общая схема которого изображена на рисунке 3.2.
|
|

Рисунок 3.2 – Схема диагностического стенда
Стенд включает в себя следующие агрегаты, узлы и отдельные элементы: дизельный двигатель 1, соединенный карданным валом с электрическим тормозом 2, систему 3 управления питанием, систему 4 нагружения, измерительную систему 5 расхода топлива, датчик 6 момента, установленный на карданном валу. Система 4 нагружения включает в себя автотрансформатор 7 с движком 8, трансформатор 9, выпрямитель 10 и сглаживающий конденсатор 11. Выход этой системы подключен к обмотке 12 возбуждения тормоза. Датчик 6 момента имеет металлические диски 13 и 14 с прорезями, установленные по концам вала. Вблизи прорезей каждого из дисков установлены импульсные преобразователи 15 и 16. При вращении вала на электрических выводах преобразователей 15 и 16 формируются импульсы, которые подаются соответственно на дифференцирующие резисторы 17 и 18, снабженные диодами 19 и 20 на своих выходах. Сигналы с выходов дифференцирующих цепей поступают на базы 21 и 22 транзисторов 23 и 24 триггера 25. Сформированные триггером 25 сигналы посредством согласующего усилителя 26 и фильтра 27 низких частот поступают на прибор 28, которым измеряется момент на валу двигателя. Расход топлива определяется весовым методом.
|
|
Диагностирование дизеля на стенде происходит следующим образом. Запускается дизельный двигатель, его вал свободно вращается. С помощью движка 8 автотрансформатора 7, включенного в сеть переменного тока, устанавливается на выходе системы нагружения 4 напряжение, соответствующее 20 % от номинального момента двигателя. Установка этого момента на валу двигателя производится по прибору 28. Расход топлива измеряется за две минуты работы дизельного двигателя. Далее измерения расхода топлива продолжаются с увеличивающимся моментом нагружения каждый раз на 20 % и до номинального.
|
|
По полученным данным строится зависимость часового расхода топлива от момента на валу двигателя в установившемся режиме. Эта зависимость и есть статическая характеристика дизеля по расходу топлива (см. рисунок 3.1). Если полученное значение расхода топлива на заданных скоростном и нагрузочном режимах превышает нормативное значение, то диагностируемый двигатель неисправен. Диагностирование проводится при наибольшей подаче топлива, при этом рычаг управления подачей топлива перемещается до упора. В этом случае дизельный двигатель нагружается в соответствии с внешней регуляторной характеристикой, которая изображена на рисунке 3.3 и обозначена цифрой 1. Кроме указанной характеристики, на этом же рисунке приведены внешняя скоростная характеристика (цифра 2), номинальный момент дизельного двигателя Мд.н., его номинальная частота вращения ώд.н., частота вращения вала двигателя, соответствующая его холостому ходу, ώд.х.х.. При полной подаче топлива и холостом ходе дизельный двигатель развивает наибольшую частоту вращения вала.
|
|
|
|
|
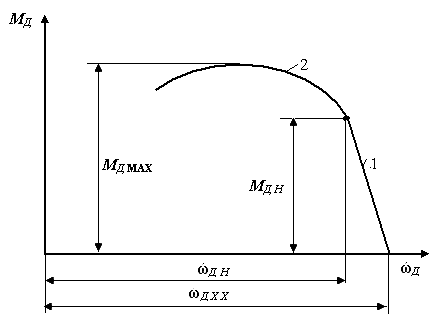
|
|
|
Рисунок 3.3 – Внешние регуляторная (1) и скоростная (2) характеристики ДВС
|
|
С увеличением момента сопротивления на валу дизельного двигателя центробежный регулятор частоты вращения увеличивает подачу топлива в цилиндры путем перемещения рейки топливного насоса.
Момент, развиваемый двигателем, возрастает. Возникает новое статическое равновесие момента, развиваемого двигателем, и момента сопротивления, приведенного к валу двигателя, но при более низкой частоте вращения вала двигателя. На рисунке 3.4 изображена функциональная схема системы автоматического регулирования частоты вращения вала двигателя, регулируемым параметром в которой является частота вращения вала двигателя.
|
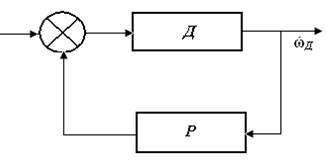
Рисунок 3.4 – Функциональная схема системы автоматического регулирования частоты вращения вала ДВС
Частота вращения измеряется чувствительным элементом регулятора, установленным в цепи обратной связи. При ее снижении возникает сигнал обратной связи, поступающий на сумматор (рычаг управления рейкой насоса), где он сравнивается с заданным значением, которое формируется водителем в зависимости от положения педали управления подачей топлива. На выходе сумматора формируется сигнал рассогласования (управления), с его помощью перемешается рейка топливного насоса в сторону увеличения подачи топлива. В результате этого крутящий момент дизеля увеличивается в соответствии с регуляторной характеристикой (см. рисунок 3.3, кривая 1) при одновременном некотором снижении частоты вращения вала. Дизельный двигатель начинает работать на новом скоростном и нагрузочном режимах.
3.1.2 Стенд для диагностирования дизельного двигателя с переменным синусоидальным нагружением. Согласно практике, находящиеся в эксплуатации дизельные ДВС очень часто имеют недостаточную по сравнению с паспортной топливную экономичность. Объясняется это многими причинами, в том числе несовершенством стендов для диагностирования дизелей, которые воспроизводят только постоянные по уровню нагрузки, вследствие чего получаемые результаты не соответствуют реальным условиям эксплуатации автомобилей, когда на коленчатом валу дизеля действуют переменные по величине крутящие моменты.
Чтобы устранить такое противоречие, создан стенд, работающий не при постоянной нагрузке на дизель, а при нагрузке, величина которой представляет собой сумму среднего значения крутящего момента и его переменной составляющей, изменяющейся по синусоидальному закону. Эта сумма нагрузок ближе к реальным нагрузкам, которые воздействуют на дизель в процессе его эксплуатации. Для проверки этой идеи проводились специальные исследования, суть которых сводилась к следующему [12].
Дизель устанавливали на стенд, оборудованный электромагнитным тормозом с двумя обмотками возбуждения и муфтой, соединенной с карданным валом, второй конец которого соединен с валом диагностируемого дизеля специальными нагрузочным и измерительным устройствами. Дизель пускают и нагружают постоянным моментом и его переменным синусоидальным составляющим, определяя амплитуду и частоту. Потом перемещают педаль управления подачей топлива в режим полной подачи, т. е. переводят дизель на работу по внешней регуляторной характеристике. На этом режиме измеряют часовой расход топлива и сравнивают полученное значение с нормативным для получения сведений о техническом состоянии дизеля.
На основе этих исследований разработан стенд (рисунок 3.5), содержащий дизель, коленчатый вал которого соединен с упругим валом 21. Второй конец последнего, в свою очередь, соединен с валом электромагнитного тормоза 45, имеющего две (43 и 44) обмотки возбуждения.
Специальное нагрузочное устройство выполнено в виде двух цепей. В первую цепь входят последовательно соединенные автотрансформатор 28 с регулятором 29, трансформатор 36, выпрямитель 37, выполненный на четырех диодах, конденсатор 42, выводы которого соединены с первой 43 обмоткой возбуждения тормоза 45, во вторую цепь – магнитный усилитель 48 с двумя (50 и 51) обмотками управления постоянного тока, рабочая обмотка 47, источник 49 переменного тока, выпрямитель 46, регулируемый источник 52 постоянного тока и регулируемый по частоте и амплитуде генератор 53 синусоидальных колебаний.
Стенд снабжен специальным измерительным устройством – датчиком крутящего момента, который состоит из двух дисков 4 и 38 с выступами и прорезями, установленных по концам упругого вала 21, и двух импульсных преобразователей 5 и 39 в виде катушек индуктивности с магнитными сердечниками и в котором обеспечена возможность прохождения выступов и прорезей каждого из дисков вблизи соответствующего преобразователя.
Рисунок 3.5 – Схема стенда
К выходам импульсных преобразователей подсоединены дифференцирующие цепи 11 и 19, которые выполнены на конденсаторах 9 и 18 и резисторах 12 и 20 с отсекающими диодами 10 и 17. Эти цепи имеют триггер 13 (два биполярных транзистора 8, 16 и четыре резистора 6, 7, 14, 15), согласующий усилитель (транзистор 23 и резистор 24), первый интегрирующий элемент 26 с заданной постоянной времени Т, равной произведению сопротивления резистора 25 на емкость конденсатора 27, выбором величины которой обеспечивается получение на выходе первого интегрирующего элемента суммы постоянной составляющей крутящего момента и его синусоидальной составляющей, второй интегрирующий элемент 31 с заданной постоянной времени Т, т. е. в 10 раз больше постоянной времени 1 первого интегрирующего элемента, вход которого соединен с выходом первого интегрирующего элемента, а выход – с измерительным прибором 40, выполненным на резисторе 30 и конденсаторе 32, дифференцирующий элемент 34, вход которого соединен с выходом первого интегрирующего элемента, а выход – с цифровым запоминающим осциллографом 41 (конденсатор 33 и резистор 35). Стенд также снабжен датчиком 2 частоты вращения и измерителем 3 часового расхода топлива.
Алгоритм диагностирования дизеля на рассматриваемом стенде следующий.
После пуска диагностируемого дизеля включают в сеть автотрансформатор 28 и, поворачивая регулятор 29 автотрансформатора, увеличивают напряжение постоянного тока, прикладываемое к первой обмотке 43 возбуждения тормоза. Напряжение увеличивают до тех пор, пока на коленчатом валу дизеля установится крутящий момент, равный 0,95 его номинального значения. Далее включают в сеть источник 52 постоянного тока и генератор 53 синусоидальных колебаний и, вращая регуляторы источника 52 и генератора 53, задают такой переменный синусоидальный нагрузочный режим, которому соответствует амплитуда колебаний крутящего момента, равная 5 % номинального, а частота – 1 Гц. При этом непрерывно измеряют переменный момент на коленчатом валу диагностируемого двигателя, а также его постоянную и переменную составляющие. Измерения этих параметров выполняют прибором 40 и цифровым запоминающим осциллографом 41, работающими следующим образом.
При включении датчика момента первый транзистор 8 триггера 13 закрыт, вследствие чего второй его транзистор 16 из-за наличия положительной обратной связи открыт. Поэтому на коллекторе первого транзистора положительное напряжение, равное напряжению питания, а на коллекторе второго оно равно нулю.
При вращении упругого вала с первым диском 4 на выходе первого импульсного преобразователя 5 формируется импульс, который дифференцируется первой дифференцирующей цепью 11 и выпрямляется диодом 10. В итоге образуется положительный импульс, который подаётся на базу первого транзистора триггера. Этот транзистор открывается, второй закрывается, а на его коллекторе появляется положительное напряжение, равное напряжению питания.
Известно, что при нагружении упругих валов они закручиваются пропорционально приложенному моменту. Поэтому второй диск 38 с выступами и прорезями закручивается относительно первого диска 4, и на выходе второго импульсного преобразователя 39 образуется второй импульс, имеющий фазовое смещение относительно первого импульса, сформированного преобразователем 5.
Параллельно с выхода первого интегрирующего элемента напряжение подается и на дифференцирующий элемент 34, на выходе которого появляется напряжение, изменяющееся по синусоидальному закону и отражающее переменную составляющую момента на валу диагностируемого двигателя. Амплитуда и частота этой составляющей измеряются подключенным к выходу дифференцирующего элемента 34 запоминающим цифровым осциллографом 41.
Далее обычным весовым методом измеряют часовой расход топлива и сравнивают его с нормативным, т.е. соответствующим исправному двигателю. И если он превышает нормативный, то это означает, что диагностируемый двигатель имеет неисправности.
Результаты испытаний на стенде приведены на рисунке 3.6. Они показывают, что такие информационные параметры диагностируемого двигателя, как изменение во времени расхода GT топлива и частоты вращения коленчатого вала дизеля, подчиняются тому же синусоидальному закону, что и момент Мт на валу двигателя. На основании этого можно сделать вывод: дизель в процессе диагностирования работал при синусоидальной нагрузке и часовой расход топлива определялся более точно, чем при постоянном нагружении.
|
|
|
|
|
|
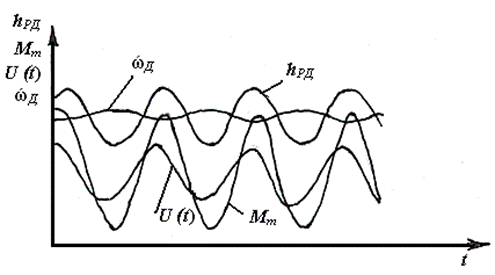
Рисунок 3.6 – Осциллограмма синусоидальных колебаний напряжения U вx(t), момента Мт, перемещения рейки изменения подачи топлива h рд и частоты вращения ώд вала диагностируемого двигателя
3.1.3 Стенд для диагностирования ДВС с переменным случайным нагружением. Стенд предназначен для повышения качества испытания двигателей внутреннего сгорания путем воспроизведения различных эксплуатационных режимов и обеспечения оперативного управления процессом испытания. Достигается это путем создания необходимого момента сопротивления, имитирующего постоянную составляющую нагрузки, а также воспроизведения и добавления к ней случайной составляющей нагрузки.
На рисунке 3.7 показана общая схема такого стенда. Стенд содержит ДВС 1, соединенный с нагрузочным устройством 2,состоящим из электротормоза 3, жидкостного реостата 4, снабженного электродами 5.
Вал 6 электродов 5 соединен с одной стороны с первым программным устройством 7, а с другой – с исполнительным элементом 8 нагрузки, выполненным в виде электродвигателя 9, обмотка 10 управления которого подключена к схеме управления, состоящей из последовательно соединенных источника 11 и формирователя 12 случайных сигналов, системы 13 для их воспроизведения и преобразователя 14, выполненного в виде дифференцирующей цепи, входом подключенного к выходу формирователя 12 случайных сигналов, а выходом соединенного с обмоткой 10 управления электродвигателя 9. Источник 11 случайных сигналов содержит трансформатор 15, выпрямитель 16 и сглаживающий фильтр 17. Формирователь 12 случайных сигналов выполнен в виде последовательно соединенных элемента 18 выделения случайной составляющей и формирователя 19, состоящего из усилителей 20 и 21.
Рисунок 3.7 – Стенд с переменным случайным нагружением
Система 13 для воспроизведения случайных процессов, характеризующихся корреляционной функцией экспоненциально-косинусного типа с различными коэффициентами корреляционной функции, соответствующими реальным эксплуатационным значениям, состоит из блока 22 конденсаторов различной емкости и переключателя 23, причем общим выводом переключатель 23 соединен с базой транзистора второго усилителя 21 формирователя 19, а другим выводом – с первыми выводами каждого конденсатора блока 22, вторые выводы которых соединены с нулевой шиной формирователя 12, а ось переключателя 23 соединена посредством привода 24 и редуктора 25 с валом электродвигателя 26, обмотка 27 управления которого подключена ко второму программному устройству 28.
Стенд работает следующим образом. При испытании двигателя 1 внутреннего сгорания путем изменения сопротивления жидкостного реостата 4 программным устройством 7 задается необходимый изменяющийся по заданному закону момент сопротивления на валу двигателя 1, имитируя тем самым постоянную составляющую уровня нагрузки.
Воспроизведение на стенде случайной составляющей момента сопротивления, соответствующей различным эксплуатационным режимам работы двигателя внутреннего сгорания, производится программным устройством 28, определяющим необходимый режим вращения вала электродвигателя 26, который посредством редуктора 25 и привода 24 поворачивает ось переключателя 23, тем самым подключая на базу транзистора второго усилителя 21 формирователя 19 конденсаторы различной емкости блока 22, изменяя передаточную функцию формирователя 19. Вследствие этого для каждого определенного значения емкости конденсаторов на входе второго транзистора формирователя 19 на его выходе из одной и той же случайной составляющей, выделенной элементом 18, формируются случайные процессы, характеризующиеся корреляционной функцией экспоненциально-косинусного типа с различными коэффициентами корреляционной функции, соответствующими разным эксплуатационным режимам двигателя внутреннего сгорания. При этом количеству конденсаторов различной емкости, установленных в блоке 22 и поочередно подключаемых на вход второго транзистора формирователя 19, соответствует количество воспроизводимых на стенде режимов испытаний двигателей.
3.1.4 Стенд для диагностирования дизельного двигателя по частотной характеристике. Исследования показали, что в процессе эксплуатации дизельных двигателей их амплитудно-частотная характеристика претерпевает изменения из-за появления неисправностей. Эта характеристика определяется как зависимость отношения амплитуды перемещения рейки топливного насоса дизельного двигателя к амплитуде момента на его валу от частоты колебаний этих информационных параметров при постоянной амплитуде колебаний момента на валу двигателя. Это дало основание разработать и предложить новый метод диагностирования дизельных двигателей на стенде, заключающийся в том, что диагностируемый дизельный двигатель устанавливают на стенд, содержащий электрический тормоз, карданный вал, соединяющий валы дизельного двигателя и электрического тормоза, снабженный контрольно-диагностической аппаратурой и измерительными приборами с пультом управления; нагружают дизельный двигатель крутящим моментом, включающим постоянную составляющую, равную половине номинального крутящего момента диагностируемого двигателя, и синусоидальную составляющую, амплитуда которой меньше уровня постоянной составляющей момента; задают частоту синусоидальных колебаний момента и измеряют амплитуду синусоидальной составляющей перемещения рейки топливного насоса; затем, не изменяя амплитуду синусоидальной составляющей момента на валу двигателя, измеряют амплитуду синусоидальной составляющей перемещения рейки для нескольких фиксированных частот колебаний момента; строят амплитудно-частотную характеристику дизельного двигателя, определяя ее ординаты для этих фиксированных значений частоты колебаний момента и рейки топливного насоса, и, сравнивая полученные значения ординат с нормативами, принимают решение о техническом состоянии данного диагностируемого дизельного двигателя.
Для реализации предложенного метода диагностирования дизельных двигателей разработан стенд, общая схема которого приведена на рисунке 3.8. Он включает в себя следующие основные элементы: дизельный двигатель 1, вал которого соединен упругим валом с валом тормоза 2, имеющим обмотки возбуждения 3 и 4, датчик 5 момента, установленный на упругом валу, преобразователь 6 перемещения рейки топливного насоса, автотрансформатор 7, трансформатор 8, выпрямитель 9, сглаживающий конденсатор 10, записывающий осциллограф 11 с каналами 12, 13, генератор синусоидальных сигналов 14, подключенный к обмотке возбуждения 4 тормоза посредством магнитного усилителя 15. Канал 12 осциллографа 11 подключен к выходу датчика 5 момента, канал 13 осциллографа 11 - к выходу преобразователя 6, обмотка возбуждения 3 электротормоза – к обкладкам конденсатора 10.
|
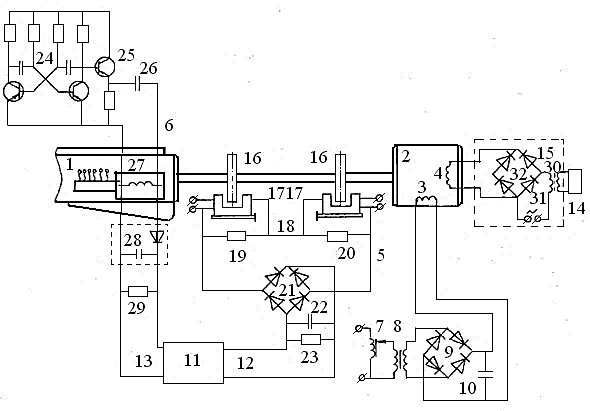
Рисунок 3.8 – Схема стенда
Датчик 5 момента включает в себя два тонких металлических диска 16 с радиальными выступами и прорезями, закрепленных по концам упругого вала, импульсные щелевые преобразователи 17, установленные вблизи упругого вала по его концам с обеспечением возможности свободного вхождения выступов металлических дисков в щели импульсных преобразователей, сумматор 18, выполненный на резисторах 19, 20, выпрямитель 21, конденсатор 22, резистор 23.
Преобразователь перемещения рейки 6 топливного насоса состоит из мультивибратора 24, выполненного на двух транзисторах, согласующего усилителя 25, конденсатора 26, катушки индуктивности 27, выполненной с возможностью вхождения в нее рейки топливного насоса дизельного двигателя, детектора 28 амплитудно-модулированных сигналов, выходного резистора 29.
Магнитный усилитель 15 имеет обмотку 30 управления, обмотку переменного тока 31, выпрямитель 32.
После запуска и прогрева дизельного двигателя стенда устанавливается заданный скоростной режим, а на обмотку 3 возбуждения тормоза посредством автотрансформатора 7, трансформатора 8, выпрямителя 9 и конденсатора 10 подается напряжение постоянного тока, изображенное на рисунке 3.9, а. Уровень этого напряжения соответствует формированию на валу двигателя момента, равного половине его номинального. На обмотку 4 возбуждения подается напряжение синусоидальной формы от генератора 14, при этом амплитуда синусоидального напряжения, подаваемого на эту обмотку, меньше, чем уровень напряжения постоянного тока, подаваемого на обмотку возбуждения 3, а частота этого синусоидального напряжения равна, например, 0,5 рад/с (на рисунке 3.9, б изображено это напряжение). Вследствие этого на валу дизельного двигателя появляется момент, который имеет как постоянную, так и переменную составляющую (рисунок 3.9, в).
Металлические диски 16 своими выступами и прорезями проходят в щели преобразователей 17, в результате чего на электрических выводах этих преобразователей формируются прямоугольные импульсы одинаковой высоты и длительности, которые суммируются сумматором 18, выпрямляются, сглаживаются, при этом на резисторе 23 формируется сигнал, пропорциональный моменту на валу дизельного двигателя. На рисунке 3.18, в буквой А0 обозначена амплитуда переменной синусоидальной составляющей момента на валу диагностируемого двигателя при угловой частоте этого синусоидального колебания момента w0.
Аналитическая запись момента, воспроизводимого на валу двигателя, описывается уравнением
, (3.1)
где – постоянная составляющая момента на валу двигателя;
,
– амплитуда и угловая частота синусоидальной составляющей момента на валу дизельного двигателя.
Под действием момента, воспроизведенного на валу диагностируемого двигателя, рейка топливного насоса претерпевает перемещение по закону (рисунок 3.18, г)
, (3.2)
где постоянная составляющая колебания рейки;
амплитуда синусоидальных колебаний рейки;
фаза отставания колебания рейки относительно колебаний момента на валу дизельного двигателя.
Рисунок 3.9 - Сигналы, регистрируемые на стенде
С помощью осциллографа 11 записываются колебание момента на валу двигателя и колебание рейки топливного насоса.
Затем оператором устанавливается новое колебание момента на валу двигателя, имеющее такую же амплитуду и такую же постоянную составляющую М0, но другую угловую частоту
, равную, например, 1,0 рад/с. Это колебание устанавливается на стенде вращением движка регулятора частоты выходного сигнала генератора синусоидальных сигналов. Аналитическое выражение этого момента на валу двигателя
. (3.3)
В результате изменения частоты колебаний момента на валу двигателя постоянная составляющая колебания рейки остается такой же, как и в первом случае, но изменяются как амплитуда, так и фаза синусоидальной составляющей перемещения рейки. Выражение для перемещения рейки примет вид:
, (3.4)
где В2 и – амплитуда и фаза синусоидальной составляющей колебания рейки соответственно.
С помощью осциллографа опять записываются колебания момента и рейки топливного насоса.
Устанавливая одну и ту же амплитуду колебаний момента на валу двигателя, но увеличивая всякий раз частоту этих колебаний момента, получают и регистрируют колебания рейки с разными амплитудами и фазами. Опыт повторяется 10 раз. По полученным данным строится амплитудно-частотная характеристика = r = f(w) дизельного двигателя на заданном скороcтном режиме его работы, которая является текущей амплитудно-частотной характеристикой дизельного двигателя. Для ее построения по оси ординат откладывается модуль вектора r, по оси абсцисс – угловая частота колебаний момента и рейки. Эта характеристика приведена на рисунке 3.10 (кривая 2), частота
называется резонансной.
|
|

|
|

![]() |
Рисунок 3.10 – Амплитудно-частотные характеристики дизельного двигателя
Условия работоспособности дизельного двигателя определяют, оценивая полученную текущую характеристику по точкам. Для этого находят значения отклонений текущей амплитудно-частотной характеристики двигателя от номинальной, обозначенной на рисунке 3.10 цифрой 1:
, (3.5)
где – значение текущей амплитудно-частотной характеристики дизельного двигателя в некоторой точке;
– значение номинальной амплитудно-частотной характеристики для такой же частоты колебаний момента и рейки, что и для текущей амплитудно-частотной характеристики;
– допустимое отклонение характеристики в данной рассматриваемой точке.
Если выражение (3.5) справедливо для всех рассматриваемых точек характеристики, то принимается решение, что дизельный двигатель исправен.
Динамические свойства дизельного двигателя с регулятором описываются дифференциальным уравнением третьего порядка. В первом приближении принимаем следующее выражение для построения амплитудно-частотной характеристики дизельного двигателя с регулятором:
. (3.6)
Две кривые амплитудно-частотных характеристик дизельного двигателя представлены на рисунке 3.10 (кривая 2 – для дизельного двигателя при наличии в нем неисправности).
3.1.5 Стенд для диагностирования дизельных двигателей по статистической характеристике. Существующие стенды для диагностирования дизельных двигателей наиболее эффективны в том случае, если на них обеспечивается воспроизведение реальных эксплуатационных режимов работы машин, которые являются случайными по своей природе и описываются статистическими характеристиками.
В условиях эксплуатации машин на их валах действуют моменты, непрерывно изменяющиеся по случайному закону. Для описания этих моментов применим статистические характеристики. Это могут быть среднее значение момента, его среднеквадратическое отклонение, дисперсия, корреляционная функция, спектральная плотность.
Если принять, что момент на валу двигателя распределен по случайному закону, то плотность вероятности момента находят по формуле, в которую входят такие статистические характеристики, как среднее значение момента и среднеквадратическое отклонение момента
:
. (3.7)
Среднее значение момента на валу двигателя определится на конечном интервале :
. (3.8)
При увеличении длины интервала получают формулу для определения среднего по времени момента на бесконечном интервале:
. (3.9)
Дисперсия момента на валу двигателя, представляющая собой меру разброса значений момента вокруг среднего значения, – это среднее значение квадрата отклонения момента от его среднего значения:
. (3.10)
Дисперсия случайного момента имеет размерность ньютон в квадрате-квадратный метр. Для характеристики рассеивания более удобно использовать величину, размерность которой совпадает с размерностью момента. Для этого из дисперсии извлекают квадратный корень. Полученная величина называется среднеквадратическим отклонением момента :
. (3.11)
На рисунке 3.11, а приведена осциллограмма момента на валу дизельного двигателя. Этот момент может быть охарактеризован средним значением момента (рисунок 3.11, б) и среднеквадратическим отклонением момента (рисунок 3.11, в).
Таким образом, в любой момент времени в первом приближении нагрузочный режим ДВС может быть охарактеризован средним моментом на его валу и среднеквадратическим отклонением момента. Поэтому при диагностировании двигателя (коробок передач) необходимо воспроизведение на стенде случайного нагружения с заданным нагрузочным режимом, т.е. с определенными значениями среднего момента на его валу и среднеквадратического отклонения.
|
|
|
|
|
|
|
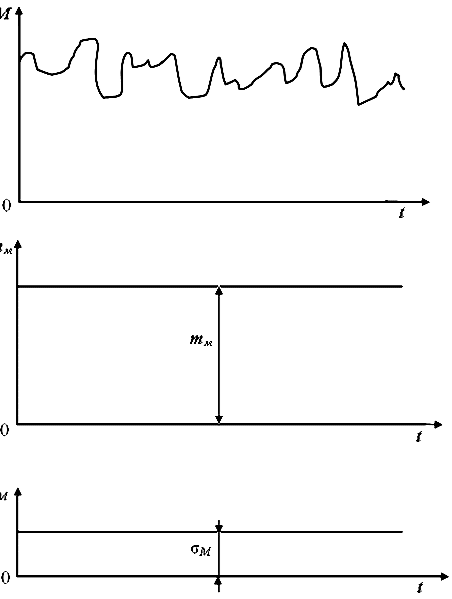
|
|
|
|
|
|
|
Рисунок 3.11 – Осциллограммы момента на валу двигателя и его статистических характеристик
Более точно нагрузочные режимы ДВС могут быть охарактеризованы корреляционной функцией, которая отражает связь между значениями момента на валу двигателя в различные моменты времени.
Для повышения точности диагностирования дизельных двигателей (механических коробок передач) на стендах должно быть обеспечено воспроизведение момента на валах этих агрегатов с различными корреляционными функциями и средними значениями. При воспроизведении момента на стенде в процессе диагностирования из-за влияния внешних факторов, например температуры окружающей среды, температуры агрегатов, нагрева масла, статистические характеристики изменяются. Поэтому эти заданные статистические характеристики воспроизводимого момента на валу двигателя необходимо поддерживать автоматически, т. е. на стендах для диагностирования агрегатов следует устанавливать системы автоматического регулирования.
Рассматриваемая система, применяемая, например, для поддержания в процессе эксплуатации среднего значения момента, его среднеквадратического отклонения, имеет следующие элементы измерения, сравнения и преобразования информации: датчик момента, элемент сравнения, блоки, определяющие уровень момента, его среднее значение, его среднеквадратическое отклонение. Кроме того, такая система должна иметь исполнительные регулирующие элементы: микроэлектродвигатели с источниками питания, электромагниты, соленоиды и др.
К системе автоматического регулирования статистических характеристик воспроизводимого на валу двигателя момента при проектировании предъявляется много требований. Наиболее важные из них – требование к надежности, простоте конструкции, малой стоимости, достаточной точности поддержания заданных статистических характеристик момента. Кроме того, спроектированная система должна быть устойчивой, иметь малую величину перерегулирования, в ней должны отсутствовать колебательные процессы.
Отличием проектируемых систем автоматического регулирования статистических характеристик от подобных систем, применяемых в других областях техники, является наличие в них элементов преобразования сигналов (информации). Так, для того чтобы поддерживать среднее значение воспроизводимого момента на валу двигателя, необходимо получить это среднее значение, т. е. иметь электрический сигнал, пропорциональный этому среднему значению момента. Очевидно, что такими элементами могут быть блоки интегрирования или фильтрации электрических сигналов. Для получения же сигнала о величине среднеквадратического отклонения следует ввести в систему автоматики и специально разработать более сложные, чем в первом случае, преобразователи сигналов. Проектирование устройства воспроизведения случайных нагрузок на валах диагностического стенда произведем применительно к стенду (рисунок 3.12).
Такой стенд содержит дизельный двигатель 1, кинематически соединенный с коробкой передач 2, маховик 3, электрический тормоз 4 с обмотками 5 и 6 возбуждения. На валу двигателя установлены металлические диски 7 и 8 с прорезями. Они предназначены для измерения момента на валу двигателя. Система воспроизведения случайных нагрузок имеет автотрансформатор 9, трансформатор 10, выпрямитель 11, конденсатор 12, дифференцирующую цепь 13, первый и второй усилители 14 и 15 с общим эмиттером.
Рисунок 3.12 – Стенд с воспроизведением случайных нагрузок
На входе второго усилителя 15 установлен блок 16 конденсаторов переменной емкости, который может быть выполнен в виде комбинации отдельных конденсаторов с устройством переключения и конденсатора с непрерывным изменением емкости. Поэтому в зависимости от величины емкости блока конденсаторов изменяются напряжение на выходе первого усилителя и его спектральная плотность.
Второй усилитель 15 осуществляет в соответствии со своим коэффициентом усиления, под которым понимается отношение напряжения на его выходе к напряжению на входе, увеличение сигнала. Так как его выходное сопротивление высоко, то непосредственная подача его выходного сигнала в обмотку тормоза, которая отличается малым сопротивлением, невозможна. Для согласования указанных сопротивлений между обмоткой тормоза и выходом второго усилителя установлен эмиттерный повторитель с высоким входным и малым выходным сопротивлениями. При этом резистор в этом усилителе включен в эмиттерную цепь.
Таким образом, обмотка 6 тормоза подключена на обкладки конденсатора 12, на котором формируется почти постоянный уровень напряжения. Обмотка 5 возбуждения получает питание от усиленного и преобразованного напряжения случайного характера.
Переменная составляющая момента на валу тормоза формируется следующим образом. Автотрансформатор 9 включается в сеть переменного тока с частотой 50 Гц и напряжением 220 В. На выходе автотрансформатора появляется напряжение, величина которого пропорциональна перемещению движка автотрансформатора. Это напряжение подается на первичную обмотку трансформатора 10. На выходе трансформатора, т. е. на его вторичной обмотке, формируется напряжение, амплитуда которого уменьшается в соответствии с его коэффициентом трансформации, например, в 10 раз. Соответственно коэффициенту трансформации изменяется в 10 раз нагрузочная способность вторичной обмотки трансформатора по отношению к его первичной обмотке.
Напряжение с вторичной обмотки трансформатора подается на выпрямитель 11, на выходе которого создается выпрямленное пульсирующее напряжение. Затем полученное напряжение с целью сглаживания пульсаций подается на конденсатор 12, который вместе с диодами, обладающими прямым сопротивлением, образует фильтр низких частот. Амплитудно-частотная характеристика этого фильтра определяется модулем частотной функции апериодического звена первого порядка. С увеличением частоты подаваемого на его вход сигнала переменной амплитуды амплитуда на его выходе падает. Поэтому на обкладках конденсатора 12 формируется напряжение с постоянной и переменной составляющими, что изображено на рисунке 3.13, а.
При этом, если полученная постоянная составляющая равна, например, 12 В, то переменная составляющая имеет незначительную величину, равную 10–30 мВ. Переменная составляющая на обкладках конденсатора всегда присутствует, т. к. автотрансформатор 9 подключен к сети переменного тока, в которой происходят изменения уровня переменного напряжения, занимающие инфранизкочастотную область, если определить их частотный диапазон.
Объясняется это тем, что к сети непрерывно подключаются и от нее отключаются потребители электрической энергии. Это происходит в случайные моменты времени, и поэтому колебания уровня полученного напряжения являются случайной величиной. Число потребителей исчисляется десятками и сотнями тысяч, например, в качестве потребителей наиболее распространены электрические двигатели переменного трехфазного тока. В результате напряжение на обкладках конденсатора непрерывно случайно изменяется от 10 до 30 мВ.
| |||
| |||
|
|
|
|
|
|
|
|
|
|
|
|
|
|
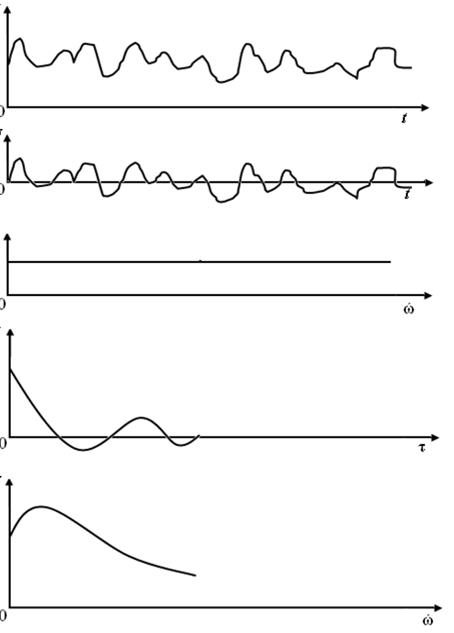
|
|
|
|
|
|
Рисунок 3.13 – Осциллограммы сигналов и статистические характеристики воспроизводимого момента на валу двигателя
График изменения выделенной на резисторе посредством конденсатора 13 случайной составляющей этого напряжения представлен на рисунке 3.13, б.
Основные положения, по которым проектировался данный стенд, следующие. Сначала определяется передаточная функция каждого входящего в динамическую систему стенда элемента. Так, например, электрический тормоз с точки зрения его динамических свойств определяется передаточной функцией , маховик – передаточной функцией
, датчик момента –
. На основании этого строится структурная схема данного стенда вместе с его системой управления, посредством которой обеспечивается воспроизведение момента на валах двигателя и коробки передач с заданной корреляционной функцией
.
Корреляционная функция является статистической характеристикой момента, который необходимо воспроизвести на стенде. Она определяется характером эксплуатационного режима работы двигателя, при котором необходимо произвести диагностирование данного двигателя. С помощью корреляционной функции учитывается связь между двумя значениями воспроизводимого момента и
в моменты времени
и
. Эта взаимосвязь оценивается средним значением произведения
и
, при этом эти значения разделены промежутком времени, равным
. Поэтому формула для исчисления корреляционной функции момента имеет вид:
, (3.12)
где – аргумент корреляционной функции,
.
Имея структурную схему стенда для диагностирования двигателей внутреннего сгорания, которая представляет собой совокупность прямоугольников с записанными на них передаточными функциями двигателя внутреннего сгорания, коробки передач, электрического тормоза, системы воспроизведения переменных случайных нагрузок, связанных между собой прямыми линиями со стрелками на одном из концов этих линий, выбирают параметры системы управления воспроизведением случайных нагрузок. Затем определяются качественные показатели систем автоматического поддержания заданных уровней статистических характеристик воспроизводимого случайного момента на валу двигателя внутреннего сгорания. Спектральная плотность выделенной на входе усилителя 14 случайной составляющей изображена на рисунке 3.13, в.
Момент на валу двигателя стенда, изменяющийся случайным образом, воспроизводится с корреляционной функцией, изображенной на рисунке 3.13, г. Соответствующая спектральная плотность воспроизведенного момента на валу двигателя на стенде изображена на рисунке 3.13, д.
3.1.6 Диагностирование дизельного двигателя на стенде по переходной характеристике его частоты вращения. Функциональный расчет стенда и измерителя частоты вращения состоит в выборе параметров электрического тормоза, принимаемого в качестве нагружающего устройства, параметров упругого вала и параметров измерительных устройств [12].
Экспериментальные исследования работы дизельных двигателей в исправном и неисправном состояниях показали, что при наличии неисправностей такая динамическая характеристика двигателя, как переходная характеристика по его частоте вращения, претерпевает изменения у неисправного дизельного двигателя по сравнению с исправным. На основании установленного был предложен метод диагностирования дизельных двигателей на стенде по переходной характеристике частоты вращения его вала, представляющей собой изменение во времени частоты вращения вала при ступенчатом изменении момента на валу двигателя.
Ступенчатое воспроизведение момента на валу дизельного двигателя затруднительно, поэтому был разработан метод определения переходной характеристики дизельного двигателя, заключающийся в определении переходной характеристики последовательного соединения двигателя и электрического тормоза при известной заранее переходной характеристике электрического тормоза.
Для реализации этого метода спроектирован стенд для диагностирования дизельного двигателя, общая схема которого приведена на рисунке 3.14, а. Стенд содержит дизельный двигатель 1, электрический тормоз 2 с обмотками 3 и 4 возбуждения. Для измерения частоты вращения вала двигателя имеется датчик частоты вращения 5, для измерения момента на его валу – датчик 6, для измерения перемещения рейки топливного насоса двигателя – датчик 7.
|
|
|
|
|
|
|
|
|
|
|
|
|

Рисунок 3.14 – Схема стенда и его характеристики
Для воспроизведения момента на валу двигателя используется следующее оборудование: автотрансформатор 8, трансформатор 9, выпрямитель 10, конденсатор 11, обкладки которого параллельно подключены к обмоткам 3 возбуждения и к регистрирующему прибору 12. Для регистрации переходной характеристики двигателя выбрано записывающее устройство 13 с тремя входами 14, 15, 16. Входом 14 данное устройство подключено к датчику 6 момента, входом 15 – к датчику 5 частоты вращения, входом 16 – к датчику перемещения рейки. Выходом 17 записывающее устройство 13 подключено к обмотке 4 возбуждения тормоза и параллельно к регулируемому источнику постоянного тока.
На выходе источника 18 постоянного тока с регулятором установлен коммутатор 19 и дополнительный измерительный прибор 20, с помощью которого измеряется уровень подаваемого в обмотку 4 напряжения.
После запуска двигателя внутреннего сгорания на обмотку 3 возбуждения тормоза подается напряжение постоянного тока, уровень которого соответствует 50 % номинального момента диагностируемого двигателя. Это достигается применением измерительного прибора 12. Например, если номинальный момент диагностируемого двигателя составляет 600 Н×м, то необходимо, передвигая движок автотрансформатора, установить по прибору 12 такое напряжение на обмотке 3 тормоза, чтобы момент на валу дизельного двигателя составил 300 Н×м. Выполнить эту операцию на данном стенде можно, если предварительно снять или иметь снятую заранее статическую характеристику тормоза, представляющую собой зависимость момента, воспроизводимого на валу тормоза, от напряжения, подаваемого в обмотку возбуждения в установившемся режиме его работы. При этом для построения статической характеристики он нагружается моментом, составляющим 0,2; 0,4; 0,6; 0,8; 1,0 от номинального момента. Тормозной момент на валу тормоза регистрируется одновременно с величиной напряжения, соответствующего этим моментам. Статистическая характеристика тормоза характеризуется коэффициентом усиления, под которым понимается величина приращения момента на валу тормоза при изменении напряжения на его обмотке возбуждения на 1 В.
На данном стенде для воспроизведения нагрузок выбран порошковый тормоз, коэффициент усиления которого равен 40 Н×м/В. Для заданного значения момента, воспроизводимого на валу тормоза, равного 300 Н×м, определяется величина напряжения, которое нужно подать в обмотку 3 возбуждения. Эта величина напряжения вычисляется по формуле
, (3.13)
где – момент на валу тормоза стенда, который необходимо воспроизвести для нагружения диагностируемого дизельного двигателя;
– коэффициент воспроизведения электрического тормоза.
Далее при отключенном положении коммутатора 19 на выходе регулируемого источника постоянного тока устанавливается напряжение, равное 15 % от напряжения, соответствующего номинальной нагрузке на двигатель. Включается коммутатор, на обмотку 4 возбуждения тормоза и одновременно на вход 17 регистрирующего записывающего устройства 13 ступенчатым образом подается напряжение.
В ДВС возникают переходные процессы, изменяются частота вращения вала двигателя, момент на его валу, а также приходит в движение рейка топливного насоса. На рисунке 3.15, а–д приведены осциллограммы сигналов, записанных с помощью устройства 13. Они поступают на это устройство с обмотки возбуждения, выходов датчика частоты вращения, датчика момента.
![]() |
|
|
|
|
|
|
|
|
|
|
|
|
|
|
|
|
|
|
|

Рисунок 3.15 – Осциллограммы сигналов в электрических цепях преобразователя частоты вращения
Ступенчатое напряжение, подаваемое в обмотку 4 тормоза, приведено на рисунке 3.15, б. Момент на валу тормоза изменяется по экспоненциальной кривой (см. рисунок 3.15, в), частота вращения двигателя - в соответствии с кривыми 1 и 2 рисунка 3.15, г, причем частота вращения вала двигателя изменяется в соответствии с кривой 1, если двигатель не имеет неисправности, и в соответствии с кривой 2, если неисправности в двигателе имеются.
При наличии неисправностей увеличивается постоянная времени двигателя, что видно из анализа кривых рисунка 3.15, г. Эти сигналы подаются на соответствующие входы регистрирующего устройства, в качестве которого принимается светолучевой осциллограф типа К 12-22.
Разработанный преобразователь (рисунок 3.16) частоты вращения содержит датчик 1 частоты вращения вала, формирователь 2 импульсов, фильтр 3 нижних частот, измерительный прибор 4, диск 5 с прорезями и выступами, установленный на валу, катушка индуктивности 6 с магнитным сердечником, жестко закрепленная вблизи прорезей и выступов диска. Формирователь 2 импульсов изготовлен в виде последовательно соединенных триггера 7 с одним входом, выполненного на двух 8 и 9 биполярных транзисторах с коллекторно-базовыми связями, и эмиттерного повторителя 10. Устройство имеет дифференцирующую цепь 11, входом подключенную к катушке индуктивности 6, последовательно соединенные вторую дифференцирующую цепь 12 и выпрямитель 13, при этом выпрямитель 13 соединен с фильтром 3 нижних частот, база 14 первого биполярного транзистора 8 триггера 7 подключена к дифференцирующей цепи 11, а выход эмиттерного повторителя 10 – ко входу второй дифференцирующей цепи 12. Первая дифференцирующая цепь 11 содержит резисторы 15,16, конденсатор 17. Триггер 7 имеет резисторы 18, 19, 20, 21. Вторая дифференцирующая цепь 12 содержит резисторы 22, 23, конденсатор 24.
При вращении вала с металлическим диском 5 с прорезями и выступами на выходах катушки 6 индуктивности формируются разнополярные импульсы, которые дифференцируются с помощью первой дифференцирующей цепи 11. На рисунке 3.17, а представлена осциллограмма остроконечных импульсов, пригодных для запуска триггера 7. В исходном положении триггера считается, что первый транзистор 8 закрыт, а второй 0 открыт. При поступлении на базу 14 транзистора 8 положительного остроконечного импульса А в момент времени (см. рисунок 3.17, а) транзистор 8 открывается, а транзистор 9 закрывается (рисунок 3.17, б, в). При последующем поступлении в момент времени
отрицательного остроконечного импульса Б (см. рисунок 3.17, а) на базу 14 транзистора 8 этот транзистор закрывается, а транзистор 9 открывается. В результате этого на выходе триггера 7 формируется прямоугольный импульс Д (см. рисунок 3.15, в).
Рисунок 3.16 – Схема преобразователя частоты вращения
При поступлении от первой дифференцирующей цепи 11 остроконечных импульсов В и Г (см. рисунок 3.15, а) на базу 14 транзистора 8 происходит формирование прямоугольного импульса Е (см. рисунок 3.15, в). Далее импульсы образуются с помощью триггера 7 аналогично описанному выше. При изменении частоты вращения вала формируются прямоугольные импульсы, которые отличаются своей длительностью, но имеют одинаковую высоту, а следовательно, и различную площадь, но нет возможности их интегрирования. Для получения одинаковой площади они дифференцируются второй дифференцирующей цепью, при этом формируется разнополярная последовательность экспоненциальных импульсов. С помощью операции выпрямления они преобразуются в последовательность экспоненциальных импульсов положительной полярности, после чего сглаживаются фильтром 3 и измеряются прибором 4.
Стенд для диагностирования сцепления
Стенд (рисунок 3.17) или транспортное средство содержит первый датчик 1 частоты вращения, установленный вблизи зубьев маховика 2 двигателя 3, первый преобразователь 4 сигналов, соединенный с выходом первого датчика 1 частоты вращения, второй датчик 5 частоты вращения, установленный вблизи зубьев зубчатого колеса 6 с постоянным зацеплением коробки передач 7, второй преобразователь 8 сигналов, соединенный с входом второго датчика 5 частоты вращения, при этом каждый из датчиков частоты вращения выполнен в виде катушек 9 индуктивности с магнитным сердечником 10, каждый из преобразователей 4, 8 сигналов выполнен в виде логического элемента И-НЕ 11, два входа которого соединены параллельно с выходом соответствующего датчика частоты вращения, первого резистора 12, соединенного с выходом логического элемента И-НЕ 11, дифференцирующей цепи 13, выполненной на втором 14 и третьем 15 резисторах и первом конденсаторе 16 и соединенной посредством первого импульсного диода 17с первым резистором 12, интегрирующей цепи 18, выполненной на четвертом резисторе 19, втором конденсаторе 20 и соединенной с выходом дифференцирующей цепи 13 вторым импульсным диодом 21; делитель 22 напряжения, вьполненный на двух последовательно соединенных резисторах 23, 24 с коэффициентом деления по напряжению, равным отношению числа зубьев маховика 2 к числу зубьев зубчатого колеса 6 с постоянным зацеплением коробки передач 7, вход которого соединен с выходом первого преобразователя 4 сигналов, первый фильтр 25, соединенный с выходом делителя 22 напряжения, второй фильтр 26, соединенный с выходом второго преобразователя 8 сигналов, первый вычитающий операционный усилитель 27 с инвертирующим и неинвертирующим входами, первый повторитель 28 напряжения, вход которого соединен с выходом первого вычитающего операционного усилителя 27, при этом неинвертирующий вход первого вычитающего операционного усилителя 27 соединен с выходом первого фильтра 25, инвертирующий вход – с выходом второго фильтра 26, третий преобразователь 29 сигналов, входом соединенный с выходом делителя 22 напряжения параллельно первому фильтру 25, четвертый преобразователь 30 сигналов, входом соединенный с выходом второго преобразователя 8 сигналов параллельно второму фильтру 26, второй вычитающий операционный усилитель 31с инвертирующим и неинвертирующим входами, второй повторитель 32 напряжения, вход которого соединен с выходом второго вычитающего операционного усилителя 31, при этом неинвертирующий вход второго вычитающего операционного усилителя 31 соединен с выходом четвертого преобразователя 30 сигналов, а инвертирующий вход второго вычитающего операционного усилителя 31 – с выходом третьего преобразователя 29 сигналов; первый измерительный прибор 33, соединенный с выходом первого повторителя 28, второй измерительный прибор 34, соединенный с выходом второго повторителя 32 напряжения, при этом шкала каждого измерительного прибора 33, 34 содержит отметки предельных значений измеряемых величин.
Рисунок 3.17 – Стенд для диагностирования сцепления
Третий преобразователь сигналов 29 содержит последовательно соединенные дифференцирующую цепь 35, состоящую из конденсатора 36 и резистора 37, диода 38, интегрирующей цепи 39, состоящей из резистора 40 и конденсатора 41. Четвертый преобразователь сигналов 30 содержит последовательно соединенные дифференцирующую цепь 42, состоящую из резистора 43, конденсатора 44, резистора 45, диод 46, интегрирующую цепь 47, состоящую из резистора 48 и конденсатора 49. Каждый из вычитающих операционных усилителей 27, 31 содержит четыре резистора 50, 51, 52, 53 и операционный усилитель 54. Каждый из повторителей напряжения 28, 32 выполнен на операционном усилителе 55, каждый из фильтров 25, 26 – на резисторе 56 и конденсаторе 57.
В процессе эксплуатации транспортное средство находится под воздействием случайных нагрузок, поэтому частота вращения маховика и частота вращения зубчатого колеса изменяются случайным образом, что изображено на рисунке 3.18. Поэтому эти частоты вращения могут быть описаны статистическими характеристиками, т. е. своими средними значениями частоты вращения и среднеквадратическими отклонениями частоты вращения. При отсутствии неисправностей как средние значения (рисунок 3.19) частот вращения маховика 2 и зубчатого колеса 6, так и среднеквадратические отклонения (рисунок 3.20) частот вращения маховика 2 и зубчатого колеса 6 совпадают.
|
|
|
|
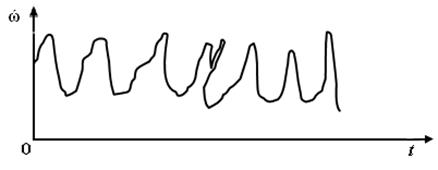
Рисунок 3.18 – График частоты вращения вала
|
|
|

Рисунок 3.19 – Среднее значение частоты вращения
|
|
|

Рисунок 3.20 – Среднеквадратическое отклонение частоты вращения
При наличии неисправностей в сцеплении среднее значение частоты вращения зубчатого колеса 6 снижается относительно среднего значения частоты вращения маховика 2, а среднеквадратическое отклонение частоты вращения зубчатого колеса 6, наоборот, увеличивается относительно среднеквадратического отклонения частоты вращения маховика 2. Происходит это из-за многих причин, вызывающих неисправности, например, из-за отсутствия или малой величины свободного хода педали, замасливания и износа дисков, усадки нажимных пружин и др. В результате происходит проскальзывание дисков, что вызывает изменение статистических характеристик частоты вращения зубчатого колеса относительно таких же статистических характеристик частоты вращения маховика.
Случайно изменяющиеся в процессе эксплуатации транспортного средства частоты вращения маховика и зубчатого колеса измеряются датчиком 1 частоты вращения маховика и датчиком 5 частоты вращения зубчатого колеса, преобразуются преобразователями 4 и 8, на выходе которых появляются напряжения, случайным образом изменяющиеся в соответствии с изменением частот вращения маховика и зубчатого колеса.
При работе транспортного средства и включении устройства на выходе датчика 1 частоты вращения маховика 2 и на выходе датчика 5 частоты вращения зубчатого колеса 6 с постоянным зацеплением коробки передач 7 появляется напряжение, которое подается одновременно на два входа каждого из логических элементов И-НЕ 11. При этом на первом резисторе 12 возникает разнополярная последовательность прямоугольных импульсов напряжения. Эти импульсы после прохождения диода 17 дифференцируются цепью 13, на выходе которой появляются разнополярные экспоненциальные импульсы одинаковой площади. После прохождения диода 21 экспоненциальные импульсы положительной полярности интегрируются цепью 18, а на конденсаторе 20 формируется напряжение, уровень которого пропорционален частоте вращения маховика 2 и зубчатого колеса 6 соответственно. При этом при отсутствии неисправностей в сцеплении величина напряжения на выходе первого преобразователя 4 сигналов в любой момент времени больше величины напряжения на выходе второго преобразователя 8 сигналов во столько раз, во сколько число зубьев маховика больше числа зубьев зубчатого колеса. Для выравнивания этих напряжений выход первого преобразователя 4 сигналов соединен с делителем напряжения с коэффициентом деления, равным отношению числа зубьев маховика к числу зубьев зубчатого колеса.
С выхода делителя 22 напряжение поступает на первый фильтр 25, на выходе которого появляется напряжение, пропорциональное среднему значению частоты вращения маховика. С выхода второго преобразователя 8 сигналов напряжение подается на второй фильтр 26, на выходе которого появляется напряжение, пропорциональное среднему значению частоты вращения зубчатого колеса, с выхода первого фильтра 25 напряжение поступает на неинвертирующий вход первого вычитающего операционного усилителя 27, на инвертирующий вход которого поступает напряжение с выхода второго 26 фильтра.
При отсутствии неисправностей на выходе усилителя 27 напряжение равно нулю, т. к. напряжения, подаваемые на входы усилителя 27, равны между собой, показания измерительного прибора 33 равны нулю. При наличии неисправностей любой величины напряжение с выхода второго фильтра 26 снижается из-за появления буксования. На выходе усилителя 27 появляется напряжение, пропорциональное разности напряжений, подаваемых на входы усилителя 27. Это напряжение подается посредством повторителя 28 на измерительный прибор 33, при этом показания прибора 33 свидетельствуют о неисправностях по разности средних значений частот вращения маховика и зубчатого колеса.
Одновременно напряжение с выхода делителя 22 подается на третий преобразователь 29, в котором дифференцирующей цепью 35 выделяется случайная переменная составляющая подаваемого напряжения, выпрямляется диодом 38, интегрируется цепью 39. На выходе цепи 39 появляется напряжение, пропорциональное среднеквадратическому отклонению частоты вращения маховика. С выхода второго преобразователя 8 сигналов напряжение подается на четвертый преобразователь 30 сигналов, в котором дифференцирующей цепью 42 выделяется случайная составляющая подаваемого напряжения, выпрямляется диодом 46, интегрируется цепью 47. На выходе цепи 47 появляется напряжение, пропорциональное среднеквадратическому отклонению частоты вращения зубчатого колеса 6.
С выхода четвертого преобразователя 39 сигналов напряжение, пропорциональное среднеквадратическому отклонению частоты вращения зубчатого колеса 6, поступает на неинвертирующий вход второго вычитающего операционного усилителя 31, на инвертирующий вход которого поступает напряжение с выхода третьего преобразователя 29 сигналов, пропорциональное среднеквадратическому отклонению частоты вращения маховика.
При отсутствии неисправностей на выходе усилителя 31 напряжение равно нулю, т. к. напряжения, подаваемые на входы усилителя 31, равны между собой, показания измерительного прибора 34 равны нулю. При наличии неисправностей любой величины напряжение на выходе четвертого преобразователя 39 сигналов увеличивается из-за появления буксования или других причин, на выходе усилителя 31 появляется напряжение, пропорциональное разности напряжений, подаваемых на входы усилителя 31. Это напряжение подается посредством повторителя 32 на измерительный прибор 34, при этом показания прибора 34 свидетельствуют о неисправностях по разности среднеквадратических отклонений частот вращения зубчатого колеса и маховика.
При наличии даже малых показаний хотя бы одного из измерительных приборов 33 или 34 принимается решение о наличии неисправностей в сцеплении эксплуатируемого транспортного средства.
Дата добавления: 2021-04-15; просмотров: 126; Мы поможем в написании вашей работы! |
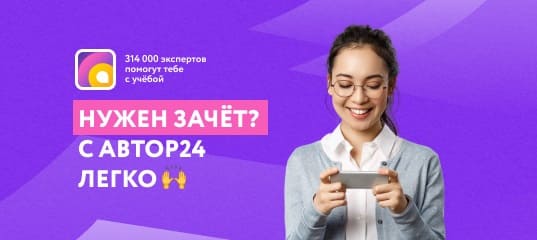
Мы поможем в написании ваших работ!