Технические требования к муфтам и тормозам
Технические требования к капитальному ремонту машины
Технические требования к деталям резьбовых соединений :
- прямолинейность оси стержня болта, винта, шпильки;
- перпендикулярность опорных поверхностей гайки и головки болта к оси их резьбы;
- наличие резьбы полного и неискаженного профиля;
- отсутствие сорванных витков, забоин, вмятин и трещин на резьбе, наличие фаски на концах резьбовых деталей;
- отсутствие смятия граней гаек, головок болтов и винтов, а также отверстий и шлицев для ключей и отверток;
- высота выступающего из гайки конца болта или шпильки не должна превышать трех витков;
- в групповом резьбовом соединении все гайки, болты или винты должны иметь одинаковый размер под ключ.
Технические требования к шпоночным соединениям :
- правильность формы и размеров шпонки, пазов вала и ступицы по всей их длине;
- отсутствие заусенцев и забоин на рабочих поверхностях шпонки и пазов;
- параллельность оси шпонки к осям вала и отверстия ступицы;
- симметричность боковых поверхностей пазов вала и ступицы относительно их диаметральной плоскости;
- тщательная пригонка рабочих поверхностей шпонки и пазов;
- наличие зазоров по высоте для призматических и сегментных шпонок и по ширине для клиновых шпонок.
Технические требования к валам и осям :
- отсутствие износа цапф и подступичных частей, забоин и задиров на них ;
|
|
- наличие заданных размеров и правильной геометрической формы цапф и подступичных частей;
- перпендикулярность опорных уступов и буртиков оси вала;
- прямолинейность оси вала и отсутствие его скрученности;
- отсутствие трещин и изломов;
- отсутствие износа и смятия рабочих поверхностей шлицев, шпоночных пазов, резьбы.
Технические требования к отремонтированным шпинделям
1.Отклонение от цилиндричности шеек под подшипники не должно превышать 10 % допуска на диаметр шейки для шпинделей станков точности А и С, 25 % допуска – при точности станков П и В и 50 % допуска – при точности Н.
2. При проверке правильности геометрической формы конусных поверхностей шпинделя с помощью конусного калибра длина неокрашенных мест не должна превышать 5 мм по окружности; вдоль образующей – 20 % ее длины; четыре продольные риски, нанесенные на калибр через 90°, должны равномерно растираться, нестертые места не должны быть более 3 мм.
3. При проверке размера конусного отверстия торец шпинделя должен находиться в пределах двух рисок на конусном калибре.
4. При протачивании и перешлифовке основных поверхностей шпинделя допускается уменьшение их диаметров в пределах 5 %, а уменьшение диаметра резьбы – до следующего меньшего стандартного размера.
|
|
5. Увеличение размеров шпоночных пазов недопустимо.
6. Вращение шпинделя от руки должно происходить без люфта и заедания.
7. После сборки шпиндельного узла проверяется параллельность или перпендикулярность оси шпинделя к поверхности стола или направляющих.
Технические требования к сборке узлов с подшипниками качения
1. Кольца и тела качения подшипника должны быть чистыми, без заметных дефектов. При вращении от руки подшипник должен вращаться свободно, без значительного шума. Новый подшипник с неповрежденной упаковкой и незагустевшим смазочным материалом можно не промывать. Загрязненные подшипники промывают в бензине с добавлением 6…8 % минерального масла или в масле (индустриальное 12 или 20) в ванне с электроподогревом при температуре 60…90 °С в течение 15…20 мин. Сильно загрязненные подшипники промывают дважды. После промывки подшипник просушивают на бумаге или с помощью сжатого воздуха. Пятна коррозии на подшипнике удаляют мягкой шкуркой и пастой ГОИ с последующей промывкой.
2. Осевой и радиальный зазоры в подшипнике должны быть в допустимых пределах. Величины начальных (установочных) зазоров для подшипников качения различных типов приводятся в справочной литературе и стандартах.
|
|
3. Выбор посадки подшипника на вал и в отверстие корпуса зависит от типа машины, требований к точности вращения, характера нагрузки, типа, размера и условия монтажа подшипника. Необходимая посадка подшипника обеспечивается за счет допусков на диаметры вала и отверстия корпуса. На сборочных чертежах и чертежах деталей рядом с номинальным размером дается условное обозначение поля допуска только поверхности, сопряженной с подшипником.
При установке подшипника качения на коническую закрепительную втулку поле допуска ее поверхности под подшипник h 8 или h 9; в случае необходимости частого демонтажа и монтажа подшипников поле допуска вала e 8 или e 9.
4. Посадочные места для подшипника в корпусе и на валу должны быть точно и чисто обработаны.
Перед сборкой подшипникового узла посадочные места промывают керосином, просушивают и смазывают. Механические повреждения, забоины, вмятины, следы коррозии устраняют. Диаметры шеек валов контролируют с помощью предельных скоб и микрометров, а диаметры отверстий корпусов – предельными пробками, индикаторными нутромерами или штихмассами.
|
|
5. Во избежание перекоса радиус закругления галтели на валу (при отсутствии кольцевой проточки или выточки) должен быть меньше, чем радиус фаски у подшипника. Величину радиуса галтели проверяют с помощью радиусомера или шаблона.
6. Упорный заплечик вала или отверстия в корпусе должен быть перпендикулярен к посадочным поверхностям. Перпендикулярность заплечиков вала и корпуса оси посадочного места проверяют угольником или индикатором.
7. Для обеспечения правильной установки подшипника на вал и в корпус следует применять специальные приспособления. При напрессовке подшипника на вал или запрессовке в корпус используют монтажные трубы из мягкого металла, винтовые и гидравлические прессы. Усилие запрессовки прикладывается к тому кольцу подшипника, которое устанавливается с натягом, а при запрессовке одновременно на вал и в корпус – к обоим кольцам. Для облегчения монтажа вал может охлаждаться, а корпус нагреваться, подшипник, соответственно, либо нагреваться, либо охлаждаться.
8. Отсутствие перекоса подшипника при установке его вместе с валом в корпус проверяют свободным проворотом вала вручную.
9. Во избежание защемления тел качения подшипники, устанавливаемые с предварительным натягом, должны иметь плавный ход и незначительный шум при провороте от руки, а в подшипниках без предварительного натяга, кроме того, должен ощущаться небольшой осевой люфт.
10. Недопустимо попадание в подшипниковый узел грязи или абразива, т.к. это приводит к ускоренному изнашиванию подшипника.
11. После сборки проверяют по периметру прилегание подшипника к заплечику вала и корпуса; вхождение щупа 0,03 мм и более не допускается.
12. При правильной сборке подшипник должен работать плавно и бесшумно, а также не нагреваться выше 70 °С.
Технические требования к подшипникам скольжения
1. Предельные отклонения отверстий во втулках и вкладышах – по Н7, Н8, Н9, а цапфы вала – по f, е и d в 7, 8 и 9-м квалитетах в зависимости от назначения подшипников. Шероховатость поверхности Ra в пределах от 1 мкм (для 7-го квалитета) до 3 мкм (для 9-го квалитета).
2. Отверстия всех опор вала должны быть соосны.
3. Отверстие в подшипнике должно иметь правильную цилиндрическую форму.
4. Торцы подшипника должны быть перпендикулярны оси отверстия.
5. Вкладыши разъемных подшипников должны быть пригнаны к гнездам корпуса до полного отсутствия люфта. В отдельных местах допускается закусывание щупа 0,04 мм на длине не более 20 мм. Бурт вкладыша должен плотно прилегать к торцу корпуса; вхождение щупа 0,05 мм недопустимо. Прилегание вкладыша к торцу проверяется «на краску»: число несущих пятен 6…8.
6. Вкладыши должны быть надежно закреплены в корпусе от проворота и осевого смещения.
7. При отсутствии данных о посадке цапфы и вкладыша величина зазора между ними может быть принята по таблицам в справочной литературе.
8. Слой баббита залитого в подшипники должен быть ровным и чистым, без раковин и отслоений.
9. Растачивание и развертывание отверстия вкладыша должны производиться после его установки и закрепления в корпусе подшипника.
10. Регулировочные прокладки в разъемном подшипнике не должны выступать за габариты подшипника, а их толщина не должна превышать 2 мм.
11.Канавки для жидкого смазочного материала должны быть расположены в середине ненагруженной зоны вкладыша, а для пластичного смазочного материала – настолько ближе к зоне давления, насколько медленнее вращается и тяжелее нагружен вал. Канавка должна выполняться длиной 0,8 от длины подшипника и не доходить до торца подшипника на 0,1 его длины. Форма канавки: для горизонтальных подшипников – прямолинейная или изогнутая; для вертикальных подшипников – кольцевая у верхнего конца вкладыша или спиральная с направлением спирали противоположно направлению вращения; для подпятников – кольцевая. В подшипнике, вращающемся на неподвижной цапфе, канавка выполняется на цапфе.
Технические требования к муфтам и тормозам
1. Полумуфты и тормозные шкивы должны надежно крепиться на валах; крепежные детали не должны выступать из корпуса.
2. Величины осевого, радиального и углового смещений соединяемых валов при монтаже муфт не должны превышать предельных значений для муфты конкретного типа.
3. Нагрев фрикционных муфт и тормозов не должен превышать допустимых – 65…100 °С в зависимости от конструкции.
4. Регулировка сцепных муфт должна обеспечивать полное вхождение в зацепление кулачков и зубьев и сжатие дисков при включении муфты и наоборот.
5. Регулировка фрикционных муфт должна обеспечивать запас сцепления (отношение передаваемого муфтой допускаемого крутящего момента к максимальному рабочему моменту) в пределах 1,3…1,5. Для тормозов коэффициент запаса сцепления равен 2.
6. Быстроходные муфты и шкивы должны быть отбалансированы.
7. Необходим строгий контроль за уровнем и периодичностью смены масла в муфтах, работающих со смазкой (зубчатых и др.).
Дата добавления: 2021-04-15; просмотров: 67; Мы поможем в написании вашей работы! |
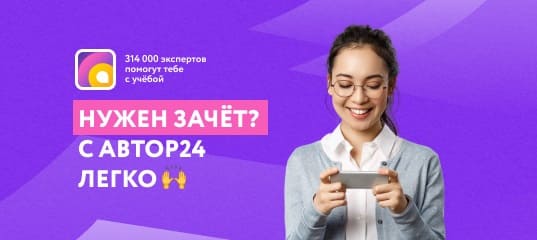
Мы поможем в написании ваших работ!