Конструктивное оформление фланцев
Министерство образования и науки Российской Федерации
Федеральное государственное бюджетное образовательное
учреждение высшего профессионального образования
«Кузбасский государственный технический университет
имени Т. Ф. Горбачева»
Кафедра прикладной механики
ИЗУЧЕНИЕ КОНСТРУКЦИЙ ЭЛЕМЕНТОВ
ПОДШИПНИКОВЫХ УЗЛОВ РЕДУКТОРОВ
Методические указания к лабораторному занятию
по курсу «Прикладная механика»
для студентов направления 220700.62
«Автоматизация технологических процессов и производств»
Составители О. В. Любимов
Л. М. Полетаева
Утверждены на заседании кафедры
Протокол № 10 от 30.04.2013
Рекомендованы к печати
учебно-методической комиссией
направления 220700.62
Протокол № 79 от 17.05.2013
Электронная копия находится
в библиотеке КузГТУ
Кемерово 2013
Цель занятия. Основные положения
Цель лабораторного занятия – изучить конструктивное оформление подшипниковых узлов редукторов и выработать практические навыки по их конструированию.
Работа рассчитана на 2 часа.
В процессе создания машин и механизмов, содержащих вращающиеся или качающиеся части, возникает необходимость в поддерживающих эти части опорах, обеспечивающих легкость их вращения и восприятие действующих на них сил.
Основными видами опор в машинах общего назначения являются в настоящее время подшипники качения, занявшие такое положение благодаря своим многочисленным положительным свойствам.
|
|
Задача проектирования опор качения заключается не только в правильном выборе типоразмера подшипника и доказательстве достаточности его ресурсных показателей, но также требует конструктивного оформления комплекса необходимых элементов, входящих в подшипниковый узел, который призван выполнять ряд функций:
• обеспечение фиксации колец подшипника как в радиальном, так и при необходимости в осевом направлении;
• обеспечение легкого вращения вала и компенсация возможного теплового расширения;
• своевременное поступление в необходимом количестве смазочных материалов к подшипнику;
• надежное уплотнение подшипника, препятствующее как проникновению частиц пыли извне в рабочую зону подшипника, так и вытеканию из нее смазки;
• возможность монтажа и демонтажа подшипника и узла в целом.
На конструкцию подшипниковых узлов редукторов накладываются также ограничения, связанные с габаритными размерами корпусных деталей, в которых сблокированы звенья, валы (оси) и опоры одной или нескольких механических передач.
Подшипниковый узел включает в себя:
|
|
а) собственно подшипник;
б) подшипниковые крышки и стаканы, а также болты (винты) для их крепления и шайбы для стопорения;
в) уплотнительные устройства;
г) мазеудерживающие и маслоотражательные кольца;
д) устройства для крепления колец подшипников;
е) комплекты прокладок для регулирования подшипников.
Подшипниковые крышки
Крышки подшипников изготовляют из чугуна СЧ 15-32 и СЧ 15-36. В малогабаритных редукторах при небольших осевых нагрузках наряду с чугуном можно применять низкоуглеродистые стали, стеклопластики и другие синтетические материалы, а при ограничении массы редуктора – легкие сплавы [1].
Различают крышки привертные и закладные, а также глухие и проходные с отверстием для выходного конца вала.
Привертные крышки
На рис. 1, 2 показаны основные конструкции привертных крышек: на рис. 1 – глухих, на рис. 2 – с отверстием для выходного конца вала (проходных).
Крышки данной разновидности имеют следующие конструктивные элементы: фланец диаметром и толщиной
, которым они накладываются на торец корпуса и крепятся болтами (винтами), проходящими через отверстия в нем, и цилиндрическую часть с пояском
. Крышки подшипников ведомых валов выполняются, как правило, без занижения за пояском (рис. 1, а; 2, а), крышки подшипников ведущих валов – с занижением (рис. 1, б; 2, б).
|
|
Определяющим при конструировании крышки является наружный диаметр подшипника качения (он же диаметр подшипникового гнезда). В табл. 1 приведены рекомендации по выбору толщины стенки
, диаметра
и числа
болтов крепления крышки к корпусу в зависимости от
; в табл. 2 даны зависимости для определения размеров прочих конструктивных элементов крышки.
Таблица 1
![]() | 50...62 | 63...95 | 100...145 | 150...220 |
![]() | 5 | 6 | 7 | 8 |
![]() | 6 | 8 | 10 | 12 |
![]() | 4 | 4 | 6 | 6 |
Примечание. Конструктивные размеры болтов, крепящих крышку к корпусу, см. прил. А. |
Для обеспечения правильности сопряжения крышки с корпусом, а также для возможности выхода инструмента при обработке пояска в месте перехода ступени диаметром
в ступень диаметром
предусматривается канавка (проточка) (см. рис. 1, выносной элемент I), размеры которой приведены в табл. 3.
Основные размеры привертных проходных крышек определяют аналогично соответствующим размерам глухих (см. табл. 1, 2, 3), за исключением размеров отверстий под манжетное уплотнение ,
и для выходного конца вала
. Зависимости для определения этих размеров приведены на рис. 2 (см. подрисуночный текст).
|
|
Конструктивное оформление фланцев
Чаще фланцы крышек выполняют круглой формы (рис. 3, а, б); обычно форма крышки должна соответствовать форме платика корпусной детали, к которой крышка привертывается.
При определенных соотношениях межосевого расстояния и размеров подшипников качения (например, при сравнительно небольшом и при принятых подшипниках средней серии) фланцы двух крышек могут перекрывать друг друга. В этом случае у обеих крышек фланцы срезают, оставляя между срезами зазор (рис. 3, а).
С целью снижения расхода металла при изготовлении как самой крышки, так и корпусной детали, фланцы привертных крышек иногда изготовляют некруглой формы. На рис. 3, в фланец крышки очерчен дугами радиусов и
. Еще большее снижение расхода металла можно получить, если крышку выполнить квадратной (рис. 3, г). Фланец крышки с шестью отверстиями под крепежные болты можно конструировать по рис. 3, д.
![]() |
Рис. 1
Таблица 2 | I | |||||||
![]() | ![]() | |||||||
![]() | ![]() | |||||||
![]() | ![]() | |||||||
![]() | ![]() | Таблица 3 В миллиметрах | ||||||
![]() | ![]() | ![]() | ![]() | ![]() | ![]() | ![]() | ||
Примечание. Полученные значения округлить до целых чисел. | Св. 10 до 50 | 3 | ![]() | 1,0 | 0,5 | |||
Св. 50 до 100 | 5 | | 1,6 | 0,5 | ||||
Св. 100 | 8 | 2,0 | 1,0 |
Диаметр отверстия для выходного конца вала:
мм при
мм;
мм при
мм.
Размеры отверстия под манжету:
;
мм,
где ,
– соответственно наружный диаметр и ширина
манжеты (см. рис. 6 и табл. 8)
Рис. 2
а | |
![]() | ![]() |
![]() | ![]() |
Рис. 3
Закладные крышки
На рис. 4 показаны основные конструкции закладных крышек: на рис. 4, а, б – глухих, на рис. 4, в, г – с отверстием для выходного конца вала (проходных).
Закладные крышки широко применяют в редукторах, имеющих плоскость разъема корпуса по осям валов. Эти крышки не требуют крепления к корпусу резьбовыми деталями; они удерживаются кольцевым выступом, для которого в корпусе протачивают кольцевую канавку.
Крышки подшипников ведомых валов выполняют, как правило, без занижения за выступом (рис. 4, а, в), крышки подшипников ведущих валов – с занижением (рис. 4, б, г).
Толщину стенки принимают в зависимости от наружного диаметра подшипника (равного диаметру расточки в корпусе); действительны рекомендации из табл. 1. Зависимости для определения размеров других элементов врезных крышек приведены в табл. 4.
Основные размеры закладных проходных крышек определяют аналогично соответствующим размерам глухих, за исключением размеров отверстий под манжетное уплотнение ,
и для выходного конца вала
, которые определяют по аналогии с этими же размерами для привертных проходных крышек.
Стаканы
Стаканы применяют для создания самостоятельного сборочного комплекта вала с фиксирующими опорами. Они широко используются в конических передачах, где требуются точная установка и регулирование относительного положения зубчатых колес [1].
Конструкция стакана определяется схемой расположения подшипников. На рис. 5 показаны варианты конструкций, наиболее часто встречающиеся на практике.
Стаканы обычно выполняют литыми из чугуна СЧ 15.
В зависимости от диаметра отверстия под подшипник (наружного диаметра подшипника) принимают толщину стенки
(табл. 5), а также диаметр
и число болтов
для крепления стакана к корпусу (табл. 6). В табл. 7 приведены зависимости для определения остальных конструктивных элементов стаканов.
![]() |
![]() |
Рис. 4
I | Таблица 4 | |
![]() | ![]() | |
![]() | ![]() | |
![]() | ![]() | |
![]() | ![]() | |
Примечание. Полученные значения округлить до целых чисел. |
а
б
Рис. 5
Таблица 5
В миллиметрах
![]() | 52 | 52...80 | 80...120 | 120...170 |
![]() | 4...5 | 6...8 | 8...10 | 10...12,5 |
Таблица 6
![]() | 40...62 | 63...95 | 100...145 | 150...220 |
![]() | 6 | 8 | 10 | 12 |
![]() | 4 | 4 | 6 | 6 |
Примечание. Конструктивные размеры болтов, крепящих стакан к корпусу, см. прил. А. |
Таблица 7
![]() | ![]() | Примечание. Полученные значения округлить до целых чисел. |
![]() | ![]() | |
![]() | ![]() | |
![]() | ![]() |
Высота упорного заплечика должна образовывать достаточную опорную поверхность для торцов подшипниковых колец, поэтому ее согласуют с размером фаски наружного кольца подшипника и возможностью его демонтажа винтовым съемником.
Обычно высоту заплечика принимают равной половине толщины кольца подшипника.
Уплотнительные устройства
Уплотнительными называют устройства, которые препятствуют вытеканию смазки из подшипникового узла. Одновременно уплотнения защищают подшипниковый узел от проникновения из окружающей среды посторонних веществ, в том числе и твердых абразивных частиц (например, пыли, грязи) [2].
По принципу действия такие устройства разделяются на:
а) контактные, применяемые при низких и средних скоростях; уплотнение достигается непосредственным соприкосновением уплотняющего элемента с шейкой вала;
б) щелевые и лабиринтные, применяемые при любых скоростях; уплотнение достигается сопротивлением протеканию жидкости через узкие щели;
в) центробежные, применяемые при средних и высоких скоростях; уплотнение достигается отбрасыванием протекающей смазки центробежными силами;
г) комбинированные, в которых объединяются два или три предыдущих устройства.
Наиболее распространены контактные уплотнения. К ним относятся манжеты, войлочные или фетровые кольца (сальники).
При смазке жидким маслом наиболее распространено манжетное уплотнение, которое применяют при окружной скорости шлифованной и полированной поверхности вала до 10 м/с. Манжетные уплотнения делят на кассетные и бескассетные, последние подразделяют на каркасные и бескаркасные.
Типовое бескаркасное (армированное) манжетное уплотнение, представленное на рис. 6, а, состоит из корпуса 1 из бензомаслостойкой резины, металлического кольца 2 уголкового сечения (армирующего элемента), служащего для придания манжете жесткости, и браслетной пружины 3, служащей для поджатия уплотняющей кромки к шейке вала. Она стягивает уплотняющую часть манжеты, вследствие чего образуется рабочая кромка шириной мм (рис. 6, б). В табл. 8 приведены сведения из ГОСТ 8752-79, позволяющие осуществить выбор манжеты из стандартного ряда.
Манжету обычно устанавливают открытой стороной внутрь корпуса. К рабочей кромке манжеты в этом случае обеспечен хороший доступ смазочного масла.
При запрессовывании в подшипник пластичного смазочного материала давление внутри его рабочей зоны может быть достаточно высоким. В этом случае, чтобы не повредить манжету, ее устанавливают рабочей кромкой наружу – при повышенном давлении смазка отогнет кромку манжеты и ее избыток вытечет наружу.
![]() |
![]() |
Рис. 6
Таблица 8
В миллиметрах
![]() | ![]() | ![]() | ![]() | ![]() | ![]() |
14...18 | 30 | 7 | 48...50 | 70 | 10 |
18 | 35 | 52 | 75 | ||
20...24 | 40 | 10 | 55...58 | 80 | 12 |
25 | 42 | 60 | 85 | ||
26 | 45 | 65 | 90 | ||
28 | 47 | 70 | 95 | ||
30...32 | 52 | 75 | 100 | ||
35...38 | 55 | 80 | 105 | ||
40 | 60 | 85 | 110 | ||
42 | 62 | 90 | 120 | ||
45 | 65 | 95 | 125 |
Пример условного обозначения манжеты типа I для вала мм с наружным диаметром
мм: «Манжета I-50´70 ГОСТ 8752-79»
Дата добавления: 2021-04-05; просмотров: 50; Мы поможем в написании вашей работы! |
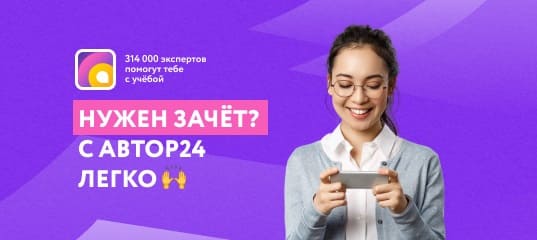
Мы поможем в написании ваших работ!