Общая схема производства сульфатной целлюлозы
Волокнистые полуфабрикаты с использованием щелочной обработки растительного сырья получали еще в древнем Китае.
Первые патенты на получение целлюлозы натронным способом были получены в 1853-54 гг., а первый завод, производящий натронную целлюлозу, был построен в США в 1860 г.
В 1879 г. немецкий инженер Даль предложил добавлять перед сжиганием упаренных щелоков, в процессе их регенерации, сульфат натрия. При сжигании сульфат восстанавливался до сульфида натрия, который становился вторым после NaOH компонентом варочного раствора. Способ получения целлюлозы с варочным раствором, содержащим NaOH и Na2S, был назван сульфатным, а получаемая целлюлоза – сульфатной целлюлозой.
Доля сульфатной целлюлозы в мировом производстве волокнистых полуфабрикатов долгое время оставалась низкой (25 % в 1925 г.) в основном из-за темного цвета целлюлозы. Но впоследствии потребность в сульфатной целлюлозе возросла, что было связанно с ростом производства тароупаковочных видов бумаги и картона, электроизоляционных и других видов бумаги, которые не могли производиться из сульфитной целлюлозы. Сейчас сульфатным способом производится более 97 % всей целлюлозы в мире.
Общая технологическая схема производства сульфатной целлюлозы представлена на рис.1. [6]
Древесина после подготовки, т. е. после получения технологической щепы необходимых размеров, поступает на варку. Варка сульфатной целлюлозы осуществляется непрерывным или периодическим методами. В котел загружают щепу и заливают варочный раствор - белый щелок, который содержит необходимую для варки активную щелочь.
|
|
Обычно, кроме белого щелока, в котел подают также некоторое количество черного (отработанного) щелока. Содержимое котла нагревают, прокачивая щелок через подогреватель, обогреваемый паром. В процессе подъема температуры проводят терпентинную (скипидарную) сдувку, с которой из котла уходят пары скипидара, воздух, оставшийся в котле, некоторое количество органических летучих продуктов и водяных паров. Сдувки направляют на установку для утилизации тепла и получения скипидара. На конечной температуре (150 - 170 °С) устраивают стоянку - выдерживают котел определенное время (от 0,5 до 3 ч), необходимое для получения данного вида целлюлозы.
Регенерация извести |
Древесина
Подготовка древесины |
Шлам
CaCO3
Дурнопахнущие Щепа Скипидар Известняк CaO
Газы
|
|
Каустизация |
Варка |
NaOH + Na2S
Промывка, сортирование, очистка |
Сжигание |
Упаренный щелок (С= 60-80 %) |
Na2SO4 |
Черный щелок (С=12-17 %) |

Выпарка |
Целлюлоза на использование |
Рис. 1 - Структурная технологическая схема производства сульфатной целлюлозы
После завершения варки целлюлозная масса вместе со щелоком поступает в выдувной резервуар и направляется на сортирование (для отделения от целлюлозной массы отходов) и промывку (для отделения черного щелока от сваренной целлюлозы). Затем промытая целлюлоза может использоваться в небеленом виде или после отбелки для производства бумаги и картона.
Черный щелок после промывки целлюлозы имеет концентрацию сухих веществ от 12 до 17 % и направляется на регенерацию химикатов, которая состоит из операций выпарки, сжигания и каустизации щелоков. Перед выпаркой черный щелок проходит подготовку, которая заключается в отделении сырого сульфатного мыла и мелкого волокна. Затем черный щелок выпаривается на многокорпусной вакуум-выпарной станции до концентрации сухого вещества 60 - 80 %. Упаренный щелок поступает на сжигание в содорегенерационный котлоагрегат (СРК). Перед сжиганием к щелоку для возмещения потерь щелочи и серы в производственном цикле добавляют свежий сульфат натрия. В процессе сжигания щелока его органические вещества полностью сгорают, а минеральные вещества образуют жидкий плав. В результате химических реакций, происходящих при высокой температуре (1000-1200°С), сульфат натрия восстанавливается углеродом до сульфида натрия, а большинство других соединений натрия под действием CO2 карбонизируется до Na2CO3. Поэтому плав содержит главным образом Na2CO3 и Na2S. Выделившееся при сжигании тепло используется для получения пара и электроэнергии. После сжигания щелоков плав растворяют в слабом белом щелоке, а раствор, называемый зеленым щелоком, подвергают каустизации (реакции с Ca(OH)2) для перевода карбоната в гидроксид натрия.
|
|
(1)
|
|
Полученный в результате каустизации белый щелок, содержащий NaOH и Na2S (не принимает участия в реакции каустизации), вновь используют для варки. Отделенный от белого щелока осадок CaCO3 подвергают обжигу в известерегенерационных печах при температуре 1100-1200 °С. При этом происходит следующая реакция:
(2)
Оксид кальция (негашенную известь) снова используют для каустизации. [2]
Технологическая часть
Целлюлозная масса после варки представляет собой суспензию волокон в отработанном щелоке, в которой содержится 4 - 6 м3 (сульфатная варка) и 6 - 8 м3 (сульфитная варка) щелока на 1 т воздушносухой целлюлозы. Основная масса щелока (около 75%) составляет свободный (наружный) щелок, окружающий отдельные щепочки, пучки волокон и волокна, 15 - 20 % щелока заключено во внутренних каналах и полостях клеток, около 5 % щелока содержится в межфибриллярных пространствах клеточных стенок. Назначение промывки заключается в возможно более полном отделении отработанного щелока от целлюлозных волокон при минимальном разбавлении его промывной водой. Поскольку методы механического разделения щелока и волокна (прессование, центрифугирование) дают возможность удалить только свободный щелок и его часть, заключенную в волокнах, т. е. не обеспечивают полноты разделения, то главным образом применяют промывку водой.
При промывке водой свободный щелок из массы удаляется вытеснением без существенного разбавления. Щелок, заключенный внутри волокон, можно удалить только за счет диффузии веществ, растворенных в щелоке, из волокон в промывную воду. Этот процесс неизбежно связан со значительным разбавлением щелока промывной жидкостью, омывающей волокна снаружи. Полностью завершить процесс диффузии практически не удается даже при длительной последующей домывке целлюлозы свежей горячей водой и поэтому при отборе щелоков и промывке целлюлозы неизбежны потери растворенных, веществ. Следовательно, в виде используемого щелока невозможно отобрать все 100 % растворенных веществ, находящихся в щелоке после варки. В зависимости от преобладания процесса вытеснения или диффузии (разбавления) в практике применяют промывку методами вытеснения или разбавления.
Промывку целлюлозы осуществляют периодически и непрерывным методами. Для промывки используют несколько типов аппаратов: диффузоры периодического и непрерывного действия, различные барабанные фильтры, прессы, а также сочетание этих аппаратов. Промывка сульфатной целлюлозы и других полуфабрикатов, получаемых щелочными методами варки, по сравнению с промывкой сульфитных полуфабрикатов протекает значительно труднее и осложняется обильным пенообразованием из-за наличия в черном щелоке поверхностно-активных веществ (ПАВ). В качестве ПАВ выступают натриевые соли смоляных и жирных кислот (сульфатное мыло), продукты растворения экстрактивных веществ при щелочной варке. Поэтому для промывки сульфатной целлюлозы требуется применение более сложных схем и оборудования. Промывка целлюлозы в настоящее время осуществляется высокопроизводительным непрерывным методом на барабанных фильтрах и в диффузорах непрерывного действия.
Промывка в диффузорах периодического действия, являвшаяся основным методом промывки до середины 50-х годов, теперь встречается редко. Промывка на барабанных фильтрах. Барабанный фильтр состоит из ванны и вращающегося в ней барабана, цилиндрическая поверхность которого выполнена из перфорированных стальных листов и обтянута снаружи мелкой (фильтрующей) сеткой. Принцип работы всех фильтров одинаков и заключается в отделении щелоков и промывной жидкости от слоя целлюлозной массы, формируемой на поверхности барабана, путем фильтрации жидкости через слой массы и сетку внутрь барабана при его вращении. В зависимости от метода интенсификации процесса фильтрации жидкости созданием определенной разности давлений над слоем целлюлозы и под фильтрующей сеткой барабана различают вакуум-фильтры и фильтры давления. [7]
Дата добавления: 2021-07-19; просмотров: 285; Мы поможем в написании вашей работы! |
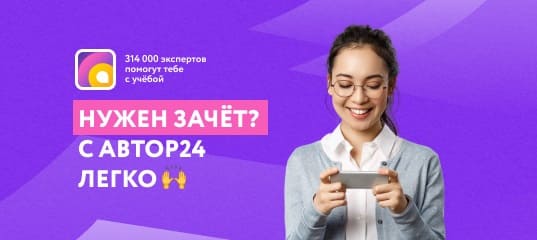
Мы поможем в написании ваших работ!