Классификация и маркировка твердых сплавов
Содержание
Содержание. 2
Введение. 3
1 Методы обработки резанием лезвийными инструментами. 4
2 Твердые сплавы.. 8
2.1 Классификация и маркировка твердых сплавов. 8
2.2 Свойства сплавов. 8
3 Отделочная обработка зубьев зубчатых колес. 11
4 Накатывание рифлений и клейм.. 15
Упрочняющая обработка поверхностей деталей. 15
5 Технологическая оснастка плазменно-механической обработки. 17
Заключение. 23
Литература. 24
Методы обработки резанием лезвийными инструментами 211
Обработка резанием — это процесс получения детали требуемой геометрической формы, точности размеров, взаиморасположения и шероховатости поверхностей за счет механического срезания с поверхностей заготовки режущим инструментом материала технологического припуска в виде стружки (рис. 1.1).
Основным режущим элементом любого инструмента является режущий клин (рис. 1.1, а ). Его твердость и прочность должны существенно превосходить твердость и прочность обрабатываемого материала, обеспечивая его режущие свойства. К инструменту прикладывается усилие резания, равное силе сопротивления материала резанию, и сообщается перемещение относительно заготовки со скоростью ν . Под действием приложенного усилия режущий клин врезается в заготовку и, разрушая обрабатываемый материал, срезает с поверхности заготовки стружку. Стружка образуется в результате интенсивной упругопластической деформации сжатия материала, приводящей к его разрушению у режущей кромки, и сдвигу в зоне действия максимальных касательных напряжений под углом φ. Величина φ зависит от параметров резания и свойств обрабатываемого материала. Она составляет ~30° к направлению движения резца[3] .
|
|
Внешний вид стружки характеризует процессы деформирования и разрушения материала, происходящие при резании. Различают четыре возможных типа образующихся стружек: сливная, суставчатая, элементная и стружка надлома (рис. 1.1, б ).
В процессе резания режущий клин, испытывая интенсивное трение, контактирует с материалом стружки и обработанной поверхностью в контактных зонах. Для снижения сил трения и нагрева инструмента применяют принудительное охлаждение зоны резания смазочно-охлаждающими средами (СОС), подавая их в зону резания специальными устройствами [1].
Рис. 1.1. Условная схема процесса резания:
а – 1 – обрабатываемый материал; 2 – стружка; 3 – подача смазочно-охлаждающих средств; 4 – режущий клин; 5 – режущая кромка; φ – угол сдвига, характеризующий положение условной плоскости сдвига (П) относительно плоскости резания; γ – главный передний угол режущего клина; Р z – сила резания; Р y – сила нормального давления инструмента на материал; Сγ u , Сγ l – длины пластичного и упругого контактов; Сγ , С a – длина зон контактного взаимодействия по передней и задней поверхностям инструмента; LOM – область главного упругопластичного деформирования при стружкообразовании; FKPT – область вторичной контактной упруго–пластичнеской деформации металла; h – глубина резания; Н – толщина зоны пластического деформирования (наклепа) металла.
|
|
Детали и инструменты закрепляются в специальных органах станка или приспособлениях. Станок, приспособление, инструмент и деталь образуют силовую систему (СПИД), передающую усилие и движение резания от привода станка режущему инструменту и детали.
Реальные схемы различных способов обработки резанием, используемый инструмент, а также виды движения инструмента и заготовки в процессе обработки приведены на рис. 1.2. В зависимости от используемого типа инструмента способы механической обработки подразделяются на лезвийную и абразивную.
Отличительной особенностью лезвийной обработки является наличие у обрабатываемого инструмента острой режущей кромки определенной геометрической формы, а для абразивной обработки – наличие различным образом ориентированных режущих зерен абразивного инструмента, каждое из которых представляет собой микроклин.
|
|
Рис. 1.2. Схемы способов обработки резанием:
а – точение; б – сверление; в – фрезерование; г – строгание; д – протягивание; е – шлифование; ж – хонингование; з – суперфиниширование; Dr – главное движение резания; Ds – движение подачи; Ro – обрабатываемая поверхность; R – поверхность резания; Rоп – обработанная поверхность; 1 – токарный резец; 2 – сверло; 3 – фреза; 4 – строгальный резец; 5 – протяжка; 6 – абразивный круг; 7 – хон; 8 – бруски; 9 – головка.
Рис. 1.3. Конструкция и элементы лезвийных режущих инструментов:
а – токарного резца; б – фрезы; в – сверла; 1 – главная режущая кромка; 2 – главная задняя поверхность; 3 – вершина лезвия; 4 – вспомогательная задняя поверхность лезвия; 5 – вспомогательная режущая кромка; 6 – передняя поверхность; 7 – крепежная часть инструмента.
Рассмотрим конструкцию лезвийных инструментов, используемых при резании (рис. 1.3). Инструмент состоит из рабочей части, включающей режущие лезвия, образующие их поверхности, режущие кромки и крепежной части, предназначенной для установки и закрепления в рабочих органах станка.
|
|
Основными способами лезвийной обработки являются точение, сверление, фрезерование, строгание и протягивание. К абразивной обработке относятсяпроцессы шлифования, хонингования и суперфиниша. В основу классификации способов механической обработки заложен вид используемого инструмента и кинематика движений. Так, в качестве инструмента при точении используются токарные резцы, при сверлении – сверла, при фрезеровании – фрезы, при строгании – строгальные резцы, при протягивании – протяжки, при шлифовании – шлифовальные круги, при хонинговании – хоны, а при суперфинише – абразивные бруски. Любой способ обработки включает два движения (рис. 1.2.): главное – движене резания Dr – и вспомогательное – движение подачи Ds . Главное движение обеспечивает съем металла, а вспомогательное – подачу в зону обработки следующего необработанного участка заготовки. Эти движения осуществляются за счет перемещения заготовки или инструмента. Поэтому при оценках движение инструмента во всех процессах резания удобно рассматривать при неподвижной заготовке как суммарное (рис. 1.4).
Рис. 1.4. Схемы определения максимальной скорости режущей кромки инструмента υе , формы поверхности резания R и глубины резания h при обработке: а – точением; б – сверлением; в – фрезерованием; г – строганием; д – протягиванием; е – хонингованием; ж – суперфинишированием.
Тогда полная скорость перемещения (ve )произвольной точки М режущей кромки складывается из скорости главного движения (v ) и скорости подачи (vs ):
ve = v + vs (1)
Поверхность резания R представляет собой поверхность, которую описывает режущая кромка или зерно при осуществлении суммарного движения, включающего главное движение и движение подачи. При точении, сверлении, фрезеровании, шлифовании поверхности резания — пространственные линейчатые, при строгании и протягивании — плоские, совпадающие с поверхностями главного движения; при хонинговании и суперфинишировании они совпадают с поверхностями главного движения.
Поверхности Ro и Ro п называются, соответственно, обрабатываемой поверхностью заготовки и обработанной поверхностью детали (см. рис. 1.2).
В процессах точения, сверления, фрезерования и шлифования главное движение и движение подачи выполняются одновременно, а в процессах строгания, хонингования движение подачи выполняется после главного движения.
К поступательным видам обработки относятся строгальные, долбежные и протяжные виды обработки.
Строгание и долбление - обработка резанием, осуществляемая однолезвийным инструментом с возвратно-поступательным главным движением резания. Строгание и долбление обычно применяются при обработке несложных профильных поверхностей с прямолинейными образующими, а также для обработки вертикальных и горизонтальных плоскостей в единичном и массовом производствах. Для этого процесса характерно действие на инструмент ударных нагрузок, небольшие скорости резания (1…1,5 м/c) и низкая производительность обработки вследствие инерционности движущихся частей станков и наличия холостого хода стола или инструмента.
Протягивание - обработка многолезвийным инструментом с поступательным главным движением резания, распространяемая на всю обрабатываемую поверхность без движения подачи. Срезание припуска осущетсвляется за счет превышения (подъема) последующего зуба над предыдущим. Производительность этого процесса, несмотря на низкие скорости резания (до 0,2…0,3м/с), в 5…10 раз выше фрезерования и в 10…15 раз - зенкерования и развертывания. Применяется в массовом и серийном производствах при получении отверстий, обработке плоских и цилиндрических наружных поверхностей с точностью до 7…9 квалитетов и шероховатостью Rz=6,3…0,8 мкм. К особенностям протягивания относится прерывистый характер работы лезвий инструмента, ударные нагрузки на зуб, срезание припуска большим количеством зубьев.
Внутреннее протягивание - протягивание внутренней замкнутой поверхности и ее элемента. Наружное протягивание - протягивание наружной или незамкнутой внутренней поверхности [2].
Осевая обработка - лезвийная обработка с вращательным главным движением резания при постоянном радиусе его траектории и движением подачи только вдоль оси главного движения резания. Основные виды осевой обработки — это сверление, зенкерование и развертывание.
Зенкерование и развертывание - осевая обработка соответственно зенкером и разверткой. Зенкерование применяется для обработки предварительно просверленных, прошитых или отлитых отверстий с целью повышения их точности (11…9-й квалитеты) и снижения шероховатости до Ra=2 мкм. Развертывание предназначено для окончательной (чистовой) обработки предварительно просверленных или расточенных резцом или зенкером цилиндрических и конических отверстий с точностью до 7-го квалитета и шероховатостью до Ra=0,6 мкм. Процессы зенкерования и разверывания протекают в более благоприятных условиях, чем сверление, так как у зенкера и развертки нет поперечной режущей кромки; глубина резания сравнительно небольшая и скорость резания вдоль режущих кромок постоянна. Вместе с тем наблюдаются большие силы трения на ленточках и неудовлетворительные условия размещения и отвода стружки.
Зенкование и цекование - осевая обработка соответственно зенковкой и цековкой.
Сверление - осевая обработка сверлом. Сверление применяется для получения отверстий в сплошном материале, а также для рассверливания на больший диаметр уже имеющихся отверстий и получения центровочных отверстий. Сверлением обеспечивается 11…12-й квалитеты точности и шероховатость обработанной поверхности Rz=80…20 мкм. Процесс резания при сверлении во многом аналогичен точению, но имеет ряд особенностей, обусловленных: 1) переменностью переднего угла, принимающего малые и даже отрицательные значения у поперечной кромки, что приводит к повышению деформации срезаемого слоя, силы и температуры резания; 2) изменением скорости резания по длине режущей кромки, сказывающимся на изменении деформации в смежных элементах; 3) ухудшением отвода стружки и затруднением проникновения СОЖ в зону резания; 4) отсутствием задних углов на вспомогательных режущих кромках, что повышает силы трения.
Сверлами обычно обрабатываются отверстия в сплошном материале, когда требуется получить отверстия невысокой точности. Более точные отверстия после сверления обрабатываются зенкерами и развертками. В этом случае точность отверстий обеспечивается лучшим центрированием инструмента (благодаря наличию большего числа режущих лезвий), повышенной жесткостью инструмента и более легкими условиями работы каждого лезвия.
Твердые сплавы 240
Классификация и маркировка твердых сплавов
Твердые сплавы представляют собой сплавы на основе карбидов тугоплавких металлов (WC, TiC, TaC) и металлической связки (кобальт или никель). Твердые сплавы обычно содержат 70-97 % тугоплавких карбидов. Они обладают высокой твердостью (86-92 HRA), красностойкостью (800-1000 °С) и износостойкостью при меньшей прочности по сравнению с быстрорежущей сталью (у < 2500 МПа).
Твердые сплавы условно делят на 4 группы:
1) однокарбидные вольфрамовые, состоящие из карбида вольфрама и кобальта (WC - Co);
2) двухкарбидные титановольфрамовые, состоящие из карбида вольфрама (основа), карбида титана и кобальта (WC - TiC - Co);
3) титанотанталовольфрамовые сплавы, в состав входят карбиды вольфрама (основа), титана, тантала и кобальт (WC - TiC - TaC - Co);
4) безвольфрамовые твёрдые сплавы, состоящие из карбида или карбонитрида титана, связки Ni или сплава Ni - Mo: TiC - Ni - Mo (сплавы ТН); TiC - TiN - Ni - Mo (сплавы КНТ).
Вольфрамовые сплавы обозначаются буквами ВК и цифрой, указывающей процентное содержание кобальта, например, сплав ВК6 содержит 6 % кобальта, остальное (94 %) - карбид вольфрама. К этой группе относятся сплавы ВК3, ВК4, ВК6, ВК8, BKIO, BKI5, ВК20, ВК25. Чем больше кобальта в твердом сплаве, тем выше прочность, но ниже твердость и износостойкость. Теплостойкость их - до 800 °С. Для сплава ВК8, например, предел прочности при изгибе уu = 1717 МПа, твёрдость 87,5 НRА, а для сплава ВК25: уu = 2452 МПа, 83 HRA. Буква М в марке сплава обозначает, что сплав мелкозернистый (ВК6 М), буква К - крупнозернистый (ВК20 - К), буква В указывает, что изделия спекались в атмосфере водорода (ВК6-В).
Сплавы с крупным зерном отличаются повышенной ударной вязкостью. Чем меньше зерно карбидной фазы, тем выше износостойкость твёрдого сплава. Титановольфрамовые твердые сплавы обозначаются буквами ТК и цифрами, стоящими после каждой цифры, которые указывают конкретное содержание карбида титана и кобальта. Так, Т15К6 содержит 15 % карбида титана, 6 % кобальта, остальное - карбид вольфрама. Теплостойкость сплавов группы ТК - до 900-1000 °С. Титанотанталовольфрамовые сплавы обозначаются буквами ТТК и цифрами: ТТ7К12 - карбидов титана и тантала - 7 %, кобальта 12 %, остальное - карбид вольфрама. Теплостойкость сплавов группы ТТК- до 1000 °С.
Безвольфрамовые твердые сплавы отличаются высокой окалиностойкостью, отсутствием дефицитного вольфрама, вдвое меньшей плотностью по сравнению со сплавами группы ВК, однако уступают им по прочности, ударной вязкости и теплопроводности. Химический состав безвольфрамовых твёрдых сплавов:- карбидотитановые - 70-80 % TiC, 20-40% Ni-Mo (сплавы TH-20, TH-30, TH-40);- карбидонитридотитановые - 25-45% TiC, 25-45 % TiN, 30-35 % Ni-Mo(KHT16 и др.)При обработке сталей используются сплавы группы ТК, а чугунов - группы ВК. Сплавы группы ТТК более универсальные, применяются как при обработке сталей, так и чугунов. Безвольфрамовые твердые сплавы рационально использовать при получистовой и чистовой обработке углеродистых сталей и цветных металлов.
Свойства сплавов
Физические свойства
Плотность. Плотность сплавов зависит от химического состава сплавов (с увеличением содержания Со и титана уменьшается). Плотность снижается при наличии в конкретном сплаве остаточной пористости, свободного графита.
Теплопроводность. Твердые сплавы работают в условиях трения. В результате образуется тепло, которое при хорошей теплопроводности отводится от места контакта с обрабатываемым материалом.
Большое влияние теплопроводность оказывает на обработку резанием материалов, дающих сливную стружку, т.е. такую, которая в процессе резания трется о твердый сплав. Если твердый сплав имеет низкую теплопроводность, то выделяющееся тепло сосредоточивается на режущей кромке резца и стружке. В этом случае стружка размягчается и мало изнашивает сплав, но режущая кромка разогревается и интенсивнее изнашивается. Поэтому теплопроводность должна быть оптимальной, обеспечивая наилучшие режущие свойства сплава.
В пределах одной группы сплавов теплопроводность зависит от количества карбидной фазы и пористости. С уменьшением карбидной фазы и пористости теплопроводность возрастает.
Вольфрамокобальтовые сплавы более теплопроводны, чем титановольфрамкобальтовые.
Коэффициент линейного расширения. Он характеризует удлинение тела при нагреве. Коэффициент линейного расширения твердых сплавов зависит от химического состава сплава. С увеличением содержания кобальта коэффициент линейного расширения увеличивается.
Коэффициент линейного расширения титановольфрамовых сплавов примерно в 2 раза ниже, чем для малоуглеродистой стали. Это различие отражается на качестве инструмента с напаянными пластинами. Из-за дополнительных напряжений, возникающих в результате различия в коэффициентах линейного расширения, пластины могут отслаиваться от державки или иметь трещины.
Термические свойства твердых сплавов играют большую роль при изготовлении и эксплуатации инструмента. Твердые сплавы чувствительны к условиям нагрева и охлаждения, а они всегда имеют место при пайке пластин твердого сплава к инструменту, при шлифовании и заточке изделий. Во избежание образования трещин в изделиях из твердых сплавов. Следует применять медленное нагревание и охлаждение при пайке, оптимальные режимы при шлифовании и обильное охлаждение.
Красностойкость - свойство твердого сплава сохранять твердость, износостойкость и другие качества, необходимые для резания. Красностойкость важна для резания стали, т.к. сливная стружка трется о твердосплавную пластину и разогревает ее. Она проявляется в интервале температур 900- 100С. Красностойкость титановольфрамовых сплавов выше, чем вольфрамокобальтовых, благодаря присутствию карбида титана.
Магнитные свойства. Из магнитных свойств сплавов практически важной является величина коэрцитивной силы. Зависит главным образом от содержания кобальта и дисперсности кобальтовой фазы. Чем выше дисперсность кобальтовой фазы, тем выше значение коэрцитивной силы. Чем выше содержание кобальта, тем ниже коэрцитивная сила. (т.к. увеличивается толщина прослоек).
Значения коэрцитивной силы указывают на размер зерен карбидной фазы, т.к. размер участков кобальтовой фазы (при одном и том же содержании кобальта) зависит от величины зерен карбидной составляющей.
Механические свойства
Твердость - свойство твердого тела сопротивляться проникновению в него другого тела. Твердость - одно из главных свойств твердых сплавов, т.к. от нее зависит износостойкость. Главное влияние на нее оказывает количество карбидной фазы и величина зерна этой фазы. С увеличение количества карбидной фазы или уменьшением величины зерна твердость возрастает.
Для ТК-сплавов при постоянном размере зерен фазы WC и при увеличении размера зерен титановой фазы твердость сплава практически не меняется.
Титановольфрамовые сплавы отличаются более высокой твердостью, чем вольфрамовые, т.к. карбид титана тверже, чем карбид вольфрама.
С увеличением плотности (снижении пористости) твердость возрастает.
Наличие в избытке углерода в виде графита снижает твердость сплава, а недостаток углерода, вызывающий появление з-фазы, существенно повышает твердость, но снижает прочность.
Содержание углерода в пределах двухфазной области системы WC-Co не приводит к изменению фазового состава сплава, но отражается на составе кобальтовой фазы в связи с изменением растворимости вольфрама в кобальте (с уменьшением содержания углерода, увеличивается содержание растворенного вольфрама). Состав кобальтовой фазы в значительной степени определяет ее свойства и тем самым свойства сплава в целом.
Предел прочности при изгибе. Прочность - свойство твердого тела сопротивляться воздействию внешних сил.
Обычно прочность характеризуется величиной разрушающих нагрузок при сжатии, изгибе, растяжении и т.д.
Прочность твердых сплавов - одно из основных свойств.
Предел прочности находится в обратной зависимости от твердости и увеличивается с увеличением содержания кобальта, проходя через максимум 15-20%. Зависит и от величины зерна карбидной фазы. Максимум зависит от содержания кобальта.
Титановольфрамовые сплавы менее прочные, т.к. карбид титана менее прочный. Зависимость прочности и др. свойств от зернистости у ТК-сплавов более сложная. Наименьшую прочность имеют сплавы с крупной титановой фазой и мелкой фазой WC. При постоянной зернистости титановой фазы с увеличением размера зерен WC-фазы прочность растет, а твердость падает.
Прочность зависит от пористости, наличия графита, степени обезуглероживания, от интенсивности размола.
Предел прочности зависит и от содержания углерода в сплаве. Зависимость отражается кривой, максимум которой проходит при содержании в сплаве углерода 6.12 в пересчете на карбид вольфрама. Причем падение прочности происходит более резко при дефиците углерода, чем в случае его избытка. В общем можно сказать, что предел прочности сохраняет практически постоянное значение в интервале содержания в сплаве от 0.5% Соб. до 0.1%з-фазы [3].
Предел прочности при сжатии. Прочность твердых сплавов при сжатии имеет весьма большое значение и характеризует в некоторой степени пластические свойства.
Кривые зависимости усж от содержания кобальта проходят через максимум, но максимум лежит при значительно меньшем содержании кобальта (4-6%).
С увеличением среднего размера зерна карбидных зерен усж монотонно уменьшается, но для всех размеров наблюдается максимум в интервале 6-8%. Наиболее высокий уровень усж наблюдается у мелкозернистых сплавов при содержании кобальта 4 или 8.6%Со.
Ударная вязкость растет непрерывно с увеличением содержания кобальта и ростом зерна. Является функцией прочности, так и пластичности. Поэтому зависимость более сложная.
Пластичность достигается не только увеличением размера зерна, но и применением высокотемпературных процессов восстановления вольфрама и карбидизации.
Дата добавления: 2021-07-19; просмотров: 70; Мы поможем в написании вашей работы! |
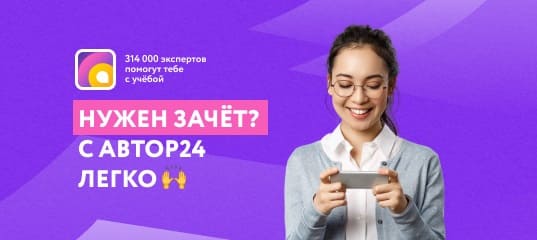
Мы поможем в написании ваших работ!