Подбор шпонок и их проверочный расчет
Ведущий вал
Из предыдущих расчётов:
Принимаем напряжение смятия ..
1.9.1 По табл. К42[3] выбираем размеры соединений:
принимаем ; (48)
принимаем ; (49)
. (50)
1.9.2 Расчётное напряжения смятия:
(51)
Ведомый вал
Из предыдущих расчётов:
По табл. К42[3] выбираем размеры соединений:
.
;
;
;
.
Рисунок 6 – Шпоночное соединение
Прочность шпоночных соединений обеспечена
1.10 Проверочный расчет ведомого вала
Из предыдущих расчетов:
Назначаем материал вала сталь 45;
термообработка - улучшение до 248 НВ;
по табл. 3.2[1]
Обработка поверхностей: цапфы - шлифование; посадочная поверхность - чистовая обработка.
Из эскизной компоновки:
Размеры шпоночного паза:
1.10.1 Определяем осевой момент в зацеплении:
(52)
1.10.2 Определяем консольную сила:
. (53)
1.10.3 Выполняем эскиз ведомого вала и его расчетную схему. Строим вертикальную схему нагружения ведомого вала, определяем вертикальные реакции в подшипниках ведомого вала:
; (54)
; (55)
;
;
Проверка:
(56)
- реакции найдены верно.
1.10.4 Строим эпюру изгибающих моментов в вертикальной плоскости
;
;
;
.
1.10.5 Строим схему нагружения в горизонтальной плоскости. Определяем горизонтальные реакции в подшипниках вала:
; (57)
; (58)
;
Проверка:
; (59)
|
|
- реакции найдены верно.
1.10.6 Строим эпюру изгибающих моментов в горизонтальной плоскости :
;
.
1.10.7 Строим суммарную эпюру изгибающих моментов:
; (60)
;
;
;
;
.
1.10.8 Строим эпюру крутящих моментов:
Дальнейший расчет ведем по более нагруженному сечению А.
1.10.9 Определяю геометрические характеристики сечения А:
1.10.10 Определяем максимальные напряжения:
; (61)
. (62)
Полагаем, что нормальные напряжения изменяются по симметричному циклу, а касательные по от нулевому.
1.10.11 Амплитудные напряжения:
..
1.10.12 Выписываем из таблиц 2.1, 2.2, 2.4, 2.5[2] коэффициенты влияния на предел выносливости:
1.10.13 Коэффициенты снижения предела выносливости:
; (63)
. (64)
1.10.14 Пределы выносливости в данном сечении:
; (65)
.. (66)
1.10.15 Запас усталостной прочности по нормальным и касательным напряжениям:
; (67)
. (68)
1.10.16 Определение расчетного запаса усталостной прочности:
(69)
Усталостная прочность обеспечена.
Рисунок 7 – Эпюры изгибающих моментов
Выбор и проверочный расчет подшипников ведомого вала
Расчет заключается в определении расчетной динамической грузоподъемности и сравнении ее с грузоподъемностью подшипника, взятой из таблицы К27[1].
|
|
Из предыдущих расчетов:
1.11.1 Суммарные реакции опор:
; (70)
. (71)
1.11.2 Выписываем из таблицы К27[3] характеристики подшипника :
; P =90 мм..
1.11.3 В соответствии с условиями работы принимаем расчетные коэффициенты:
- коэффициент вращения, принимаем
- коэффициент безопасности, принимаем
- коэффициент, учитывающий влияние температуры, принимаем
1.11.4 Определяем коэффициенты радиальной Х и осевой Y нагрузок:
Определяем соотношение тогда
Определяем соотношение
т. к.
1.11.5 Определяем эквивалентную динамическую радиальную нагрузку:
Дальнейший расчёт ведём по более нагруженной опоре.
1.11.6 Расчетная динамическая грузоподъемность:
(72)
Где
выбранный подшипник удовлетворяет заданному режиму работы.
1.12 Выбор посадок
Единая система допусков и посадок регламентирована стандартами и в основном соответствует требованиям Международной организации по стандартизации – ИСО
Посадки назначаем в соответствии с указаниями, данными в 4, табл. 10.13.
Внутренние кольца шарикоподшипников устанавливаются с посадкой с натягом, наружные – с посадкой с зазором. Основной деталью системы в обоих случаях являются кольца подшипника. Шейки валов под подшипники выполняем с отклонением k 6. Отклонение отверстий в корпусе под наружные кольца по Н7.
|
|
Зубчатое колесо насаживается на вал по посадке с натягом ( по ГОСТ 25347-82) обесечивает необходимый натяг в соединении.
Посадка шкива ременной передачи на вал редуктора для удобства демонтажа выполняется по посадке с зазором, обеспечивающей надежность центрирования – , с допольнительным креплением шпонкой.
1.13 Смазка редуктора
Из предыдущих расчетов известно:
1.13.1 Смазывание зубчатого зацепления производится окунанием зубчатого колеса в масло, заливаемое внутрь корпуса до погружения колеса на всю длину зуба. По табл. 10.8[3] устанавливаем вязкость масла. При контактном напряжении и окружной скорости вязкость масла должна быть приблизительно равна По табл. 10.29. принимаем масло индустриальное И-Г-А-68 (ГОСТ 20799-75).
1.13.2 Определяем количество масла.
На 1 кВт мощности необходимо литра масла
Камеры подшипников заполняем пластичным смазочным материалом пресс-солидол (С) (ГОСТ 21150-75).
Сборка редуктора
Перед сборкой внутреннюю полость корпуса редуктора тщательно очищают и покрывают маслостойкой краской.
|
|
Сборку производят в соответствии со сборочным чертежом, начиная с узлов валов:
На ведущий бал (6) насаживают мазеудерживающее кольцо (16) и шариковые радиальные однорядные подшипники (26), предварительно нагретые в масле до 80-100°С;
В ведомый бал (5) закладывают шпонку (30) и напрессовывают зубчатое коническое колесо (7) до упора в бурт вала; затем надевают распорное кольцо (32) мазеудерживающие кольца (15) и устанавливают шариковые радиальные однорядные подшипники (27), нагретые в масле.
Собранные балы укладывают в основание корпуса редуктора (3) и надевают крышку корпуса (4), покрывая предварительно поверхности стыка крышки и корпуса спиртовым лаком. Затягивают болты (20) и (21), крепящие крышку к корпусу.
После этого в подшипниковые камеры закладывают пластичную смазку, ставят крышки подшипников (9) и (11).
Для нормальной работы подшипников следует следить за тем, чтобы, с одной стороны, вращение подвижных элементов подшипников проходило легко и свободно и, с другой стороны, чтобы в подшипниках не было излишне больших зазоров. Создание в подшипниках зазоров оптимальной величины, производится с помощью регулировки подшипников, для чего применяют наборы тонких металлических прокладок, устанавливаемых под фланцы крышек подшипников. Необходимая толщина набора прокладок может быть составлена из тонких металлических колец
Перед постановкой сквозных крышек (8) и (10) с манжетами в проточки зокладывают войлочные уплотнения, пропитанные горячим маслом. Проверяют проворачиванием валов отсутствие заклинивания подшипников и закрепляют крышки болтами (19).
Далее на конец ведомого вала (5) и ведущего бала (6) в шпоночные канавки закладывают шпонки (28) и (29) соответственно, устанавливают звездочку и закрепляют ее торцовым креплением; винт торцового крепления стопорят специальной планкой.
Затем ввертывают пробку (17) маслоспускного отверстия с прокладкой (14) и жезловый маслоуказатель (1) с прокладкой.
Заливают в корпус масло и закрывают смотровое отверстие крышкой (2) с прокладкой (12) из технического картона; закрепляют крышку болтами (19).
Собранный редуктор обкатывают и подвергают испытанию на стенде по программе, устанавливаемой техническими условиями.
![]() |
Дата добавления: 2021-03-18; просмотров: 188; Мы поможем в написании вашей работы! |
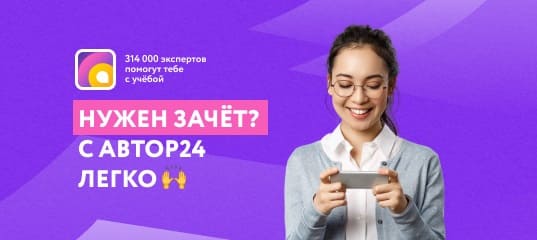
Мы поможем в написании ваших работ!