Расчет степени и скорости деформации при стружкообразовании.
В работах АрмарегоИ.Дж.А. ,Боброва В.Ф., Зорева Н.Н. скорость деформации определялась по выражению
,
где Г - степень пластической деформации,
- время, в течение которого происходит деформация.
Для модели стружкообразования с одной плоскостью сдвига величина Гсоответствует величине истинного сдвига, определяемого по формуле
где ф — угол наклона условной плоскости сдвига,
у- передний угол.
Другой интерпретацией формулы является выражение вида:
где - коэффициент усадки стружки.
Применительно к модели стружкообразования с развитой веерообразной зоной пластической деформации А.А. Брикс использовал зависимость между углом наклона касательной кнаружной границе стружки v, углом сдвига ф и деформациейсдвига Г в виде:
Аналогичная зависимость позднее была использована Н.Н. Зоревым, М.И. Клушиным , Де Шифром и другими исследователями. Как показали Н.Н. Зорев, М.И. Клушин , К. Окушима и К. Хитоми, для конечной границы зоны
пластической деформации и
, поэтому конечнаядеформация равна
Э. Томсен и Ш. Кобаяшивозражают против формулы и считают, что конечная деформация при стружкообразовании должна быть равна
где фо - угол наклона начальной границы пластически деформированной зоны.
Анализируя процесс пластической деформации для модели стружкообразования с параллельными границами В.И. Садчиков , B.C. Кушнер , П.Б. Оксли пришли к выводу, что конечная деформация не зависит от размеров зоны пластической деформации и совпадает с истинным сдвигом, определяемым моделью стружкообразования с единственной плоскостью сдвига.
|
|
Другой подход к определению степени пластической деформации в зоне резания продемонстрировали В.К. Старков. Он показал, что если зона пластической деформации представляет собой семейство параллельных плоскостей сдвига, то относительная деформация сдвига может быть определена исходя из перемещения дислокаций в срезаемом слое
где - скорость перемещения дислокаций, t„- время деформирования,
а - толщина срезаемого слоя.
В этом случае степень деформации при стружкообразования является функцией толщины среза, что не учитывалось предыдущими формулами.
Другой распространенной формулой, используемой для расчета скорости деформации является
где v – скорость резания, δ – толщина зоны пластической деформации.
Используя те или иные допущение о размерах зоны пластической деформации можно получить расчетные значения скорости деформации.
Ориентировочно толщину зоны пластической деформации рассчитывают по зависимости:
,
где к – коэффициент, определяемый экспериментально; а – толщина среза; φ – угол сдвига.
|
|
11. Определение длины контакта режущего инструмента с обрабатываемым материалом.
В общем случае начальная граница зоны стружкообразования не может быть представлена прямой линией. При резании в активных средах с относительно большим передним углом (γ > 20°),когда трение на передней поверхности снижено, границы зоны стружкообразования приближаются к прямым линиям. При переходе от недеформированной или малодеформированной области к стружке градиент деформации мал и зона стружкообразования настолько узка, что ее можно условно принять за узкую полосу, в которой сосредотачивается вся деформация сдвига. В этом случае допустимо представить процесс стружкообразования, как последовательные сдвиги слоев малой толщины вдоль определенной плоскости — плоскости сдвига. Линия сдвига и плоскость сдвига являются условными, но подобная абстракция с целью получения расчетной (упрощенной) схемы допустима. По упрощенной схеме с помощью измеренных составляющих силы резания Рх, Рy и Рz, а также усадки ξ определяются углы сдвига Ф и трения ƞ), относительный сдвиг ε, напряжение сдвига ԎФ и другие характеристики напряженно-деформированного состояния процесса стружкообразования при образовании сливной стружки. С помощью упрощенной схемы на сновании закономерности, установленной Н. Г. Абуладзе, что контакт стружки с передней поверхностью инструмента кончается в точке пересечения передней поверхности и линии, проведенной от сопряжения стружки и обрабатываемого материала под углом 45° к передней поверхности (для удобства изложения рассматривается сечение корня стружки), выведена формула длины контакта в случае образования сливной стружки ɩ = a [ ξ ( 1 - t g γ ) + secγ],где γ — передний угол режущего инструмента; а — толщина среза; ξ — коэффициент усадки стружки по толщине. Упрощенная схема стружкообразования не учитывает плавного сопряжения стружки и обрабатываемой поверхности, ввиду чего рассчитанная по формуле длина контакта ɩ' меньше действительной длины контакта ɩ. Установлено , что при образовании сливной стружки с достаточным приближением соблюдается равенство l\ll= ξ0,1 Учитывая формулы, получим формулу для расчета длины контакта с учетом плавного сопряжения стружки и обрабатываемой поверхности
|
|
ɩ = a ξ0.1 [ ξ ( 1 - t g γ ) + secγ], Рассчитанная по формуле длина контакта отличается от длины контакта, определенной экспериментальным путем, на 5—8%. Помимо формулы для аналитического определения длины контакта имеются формулы, полученные Н. Н. Зоревым М. И. Клушиным и другими исследователями.
|
|
12. расчетный метод определения размеров контактного пластически деформированного слоя стружки
Пластический контакт стружки с резцом определяется зависимостью:
, (9.1)
Расчетный метод определения толщины контактного слоя предполагает совместное решение двух выражений полученных для давления, действующего на переднюю поверхность при деформировании контактного слоя стружки толщиной ак и длиной (рис. 9.1), и давления, которое может передавать материал стружки, заключенный между поверхностью сдвига и поверхностью инструмента.
Совместное решение этих соотношений дает возможность получить величину ак для различных условий обработки материалов резанием.
Рассмотрим несущую способность приконтактного слоя стружки, деформируемого под действием сжатия и сдвига. Для упрощения решения допускаем, что деформация является плоской, а деформируемый материал является идеально-пластичным.
Под действием сжатия в условиях плоской деформации направление составляющей вдоль оси Х скорости любой материальной точки прирезцового слоя по отношению к системе координат будет либо совпадать с направлением перемещения поверхности резца (основной массы стружки), либо отличаться на 180°. Силы трения на этих участках имеют противоположное направление. Точка D 1 в которой перемещение приконтактного слоя по отношению к поверхности резца (основной массе стружки) равна нулю является нейтральной (рис.9.1).
Рис. 9.1 Схема расчета толщины приконтактного слоя стружки
Задачу решаем полагая, что трение на передней поверхности инструмента подчиняется закону t ху = ±m t к где m - коэффициент, характеризующий трение стружки о резец, t к - предел прочности на срез контактного слоя стружки.
Из дифференциальных уравнений равновесия при плоскодеформированном состоянии для постоянных величин m и t к вдоль передней поверхности инструмента имеет место соотношение t х = С1 + С2у, т.е. касательные напряжения по толщине контактного слоя изменяются по линейному закону.
Анализ шлифов стружки, свидетельствует, что деформация сдвига имеет затухающий характер по мере удаления от передней поверхности резца вглубь стружки. Поэтому по границе с основной массой стружки принимаем t ху = 0 (рис. 9.1).
Определяя постоянные С1 и С2 из граничных условий и решая систему дифференциальных уравнений равновесия совместно с условием пластичности получим:
(9.2)
Здесь знак «-» и индекс 3 относится к участку внешнему, а знак «+» и индекс 4 - к участку внутреннему.
Постоянную С3определим из условия равенства нулю напряжений s х в точке выхода стружки из контакта с резцом. Из уравнения (9.2) при s х = 0, у = 0, х = найдем:
. (9.3)
Постоянную С4 найдем из условия неразрывности напряжений s х в точке х = х0
, (9.4)
где х0 – абсцисса нейтральной точки.
Абсциссу нейтральной точки определим, приравнивая скорости перемещения стружки по передней поверхности резца к скорости точек приконтактного слоя перемещающихся вдоль оси Х под действием сжатия.
. (9.5)
Из условия равенства потока материала прирезцового слоя стружки, проходящего через сечение количеству выдавливаемого материала на длине при его сжатии постоянная интегрирования равна:
. (9.6)
Подставляя выражение для с учетом (9.6) в равенство (9.5) и решая относительно х0 получим
. (9.7)
Поскольку u х равна скорости стружки , а скорость перемещения обрабатываемого материала по оси Y u у = cosg, то выражение для х0 принимает вид:
(9.8)
Нагрузка, действующая по нормали к передней поверхности резца, отнесенная к единичной ширине среза составляет
(9.9)
Усилие, которое передается через плоскость сдвига АВ единичной ширины по нормали к передней поверхности, определим, используя формулу
(9.10)
Приравнивая значения Р N . и , решая относительно величины a к, получим:
, (9.11)
где ;
.
Из полученных данных следует, что наибольшее влияние на относительные размеры прирезцового слоя стружки оказывают угол сдвига коэффициент трения стружки о резец, степень размягчения приконтактного слоя стружки и передний угол.
Уменьшению толщины приконтактного слоя стружки способствует увеличение угла сдвига f, степень размягчения контактного слоя стружки и уменьшение трения стружки о резец и переднего угла. зависимости имеют чисто теоретическое значение, так как при изменении каждого из параметров предполагается постоянное значение других. В действительности изменение одного из них влечет за собой изменение других. Например, увеличение переднего угла непременно приводит к увеличению угла сдвига, действие которого противоположно действию переднего угла.
Если размеры прирезцового слоя стружки представить в долях от ее толщины, то зависимость относительной величины от некоторых параметров процесса резания принимает иной вид (рис. 9.3) Например, передний угол g и угол сдвига f оказывают влияние на отношение
в меньшей степени, чем на
. Это свидетельствует о более тесной связи размера приконтактного слоя с толщиной стружки, чем с толщиной среза.
Истинное значение предела текучести на сдвиг в каждой точке приконтактного слоя является величиной переменной, ввиду крутых градиентов температуры и постоянно меняющейся картины скоростей деформаций.
Точное описание изменения механических характеристик приконтактного слоя представляет сложную задачу. Упрощенное решение может быть получено из следующих соображений. Согласно положению теории пластичности совместное пластическое деформирование компонентов системы, обладающей различными механическими свойствами, возможно лишь в том случае, если в каждом элементарном объеме напряжения сдвига достигнут значения предела текучести на сдвиг. Следовательно, совместную пластическую деформацию элементов приконтактного слоя можно представить как деформацию полосы, предел прочности на сдвиг которой, изменяется в соответствии с изменением касательных напряжений по сечению стружки.
Учитывая, что в зоне пластического контакта стружки с резцом напряжения сдвига равны m × t s, получим для среднего значения предела прочности на сдвиг приконтактного слоя стружки следующее соотношение:
. (9.12)
С учетом полученной зависимости между t s и t к формула (9.11) примет вид:
.
13. Теоретическое описание распределения напряжений на передней поверхности инструмента
Уравнения (2.59), описывающие изменение величин s и t дают слишком грубую аппроксимацию закона распределения напряжений по длине контакта стружка – резец. Более точное решение можно получить, если учесть взаимодействие контактного слоя с основной массой стружки интенсивностью напряжений и принять, что в конце контактной поверхности трение стружки о резец подчиняется закону Кулона t к = m sу. Здесь m - коэффициент трения стружки о резец,
– сопротивление материала стружки на сдвиг.
Распределение нормальных напряжений определяем только на контактной поверхности с резцом (Y = 0). В этом случае напряжения sу не зависят от координаты у. Это дает возможность свести задачу к одномерной и использовать условие пластичности в виде . Выделим в контактном слое, находящемся в деформированном состоянии, элемент длиной dx, шириной b и толщиной ак (рис. 2.28) и составим для него уравнение равновесия - s x akb - t k bdx - t c bdx + (s x + d s x) akb = 0, из которого следует
. Влиянием момента сил, действующих на контактный слой, пренебрегаем ввиду малости отношения
.
С учетом функции для tк и t c, а также условия пластичности d s y = d s x уравнение равновесия преобразуется к виду
. (2.71)
Интегрируя это уравнение, найдем .
Постоянную С определим из условия отсутствия напряжений sу в точке выхода стружки из контакта с резцом. Из условия sу = 0 при следует
и касательные и нормальные напряжения в конце площадки контакта стружки с резцом будут изменяться по следующему закону
(2.72)
Рис. 2.28 Схема расчета контактных напряжений
Поскольку разность касательных напряжений, действующих со стороны основной массы стружки и инструмента, не может превосходить прочность материала стружки на срез, то на некотором расстояний от режущей кромки может возникать зона, интенсивность касательных напряжений в которой постоянна и равна пределу прочности материала на срез. Границу этой зоны (х = х1) определим из равенства , решая которое получим
. (2.73)
Из граничного условия sу = s0 при х = х0 следует , где s0 - нормальное напряжение в точке х = х0. Подставляя значение sу0 из уравнения (2.74) и выполняя преобразования получим для участка 0 £ х £ x0.
. (2.75)
Эпюра нормальных напряжений в общем случае состоит из параболической кривой у режущей кромки (х £ x0) и экспоненциальной кривой в зоне входа стружки из контакта с резцом , сопрягаемых между собой прямой линией в средней части контактной зоны (x0 £ х £ x1). Эпюра касательных напряжений включает горизонтальный участок (0 ≤ х ≤ х1) и экспоненциальный при
. Очевидно, что в случае x0³ x1, промежуточный прямолинейный участок эпюры нормальных напряжений исчезает. Учитывая, что
из уравнения (2.73) определяем, что такое произойдет при
Некоторые расхождения между величиной расчетных и экспериментальных нормальных напряжений наблюдаются в основном у режущей кромки. Причем для меди экспериментальные значения нормальных напряжений у режущей кромки отличаются не только от расчетных значений, но имеют значительные расхождения между собой. Величина контактных нагрузок полученные методом разрезного резца у режущей кромки в 3 раза меньше, чем нагрузки замеренные методом различной твердости. Поэтому в области режущей кромки теоретический метод определения напряжений, разработанный на основе положений теории пластичности, является предпочтительным.
В то же время, в работе [237] отмечается, что при малых толщинах среза метод разрезного резца дает завышенные значения напряжений, особенно касательных. Полученное решение позволяет установить связь между величиной участка контакта, с постоянным касательным напряжением и параметрами процесса резания. Из формулы (2.73) следует, что протяженность этого участка увеличивается с ростом коэффициента трения стружки о переднюю поверхность резца и уменьшается с увеличением толщины контактного слоя. Применение смазочно-охлаждающих жидкостей уменьшает коэффициент трения и, следовательно, способствует уменьшению протяженности участка с постоянным касательным напряжением.
Проанализируем соответствие полученного теоретического распределения напряжений деформированному состоянию стружки, которое однозначно характеризуется направлением и интенсивностью искривления текстуры стружки. В свою очередь по текстуре можно судить о величине и знаке касательных напряжений, действующих в прирезцовом слое.
В общем случае изменение текстуры, по мере перемещения стружки по передней поверхности инструмента характеризуется схемой /58, 93/, изображенной на рис.2. 31.
На внутренней границе контактного слоя направление текстуры незначительно отличается от текстуры основной массы стружки, Непосредственно у поверхности контакта текстура стружки сильно искривлена и вытянута вдоль передней поверхности, что свидетельствует о значительных касательных напряжениях. Таким образом, в зоне выхода стружки из контакта с резцом изменение касательных напряжений по толщине стружки имеет затухающий характер, уменьшаясь от некоторой величины на контакте до нуля в точке сопряжения с прямолинейной текстурой основной массы стружки.
Рис. 2.31 Линии текстуры и эпюры касательных
напряжений
Вблизи режущей кромки линии текстуры имеют более сложную форму Соответственно касательные напряжения изменяются от минимальных значений в точках в точке А у режущей кромки, причем на участках GD, G1D1, G2D2 линии скольжения поворачиваются по часовой стрелке, а на участках DA, D1A1, D2A2 – в противоположном направлении, что свидетельствует о смене знака касательных напряжений в точках D, D1, D2.
В центральной части контакта напряженно-деформированное состояние прирезцового слоя имеет промежуточное значение между рассмотренными напряженно-деформированными состояниями у режущей кромки и в конце контакта стружки с резцом.
Аналогично проанализируем закономерность изменения касательных напряжении по длине контакта резец–стружка. У режущей кромки линии текстуры примыкают к передней поверхности, поворачиваясь против часовой стрелки, а в зоне выхода стружки из контакта - по часовой стрелке. Отсюда заключаем, что по длине контакта имеет место смена знака касательных напряжений.
15. Определение глубины деформации подрезцового слоя
Применение методов теории пластичности позволяет не только разработать методику прогнозирования глубины пластически деформированного подрезцового слоя, но и оценить степень пластической деформации этого слоя. Для решения этой задачи воспользуемся схемой взаимодействия режущего инструмента с обрабатываемым материалом, представленной на рис. 2.32.
Степень пластической деформации поверхностного слоя оценим исходя из равенства работы, совершаемой внешними силами на участках LQ и PQ и работы пластической деформации подрезцового слоя на тех же участках.
Работа, совершаемая внешними силами на участках LQ и PQ, равна
, (2.84)
где и
– контактные нормальные напряжения, действующие на поверхностях LQ и PQ;
e – угол наклона участков LQ и PQ к линии среза;
Работа пластической деформации подрезцового слоя на участке LQP определяется выражением
, (2.86)
где t - предел прочности обрабатываемого материала на срез.
Г - степень деформации подрезцового слоя,
V - объем металла, заключенный между линиями скольжения и поверхностями LQ и PQ.
Подставляя значения и
в (2.84), значение V в (2.86) и приравнивая уравнения (2.84) и (2.86), получим следующее выражение для определения степени пластической деформации подрезцового слоя
. (2.88)
Расчеты по формуле (2.88) показывают, что обработка материалов изношенным резцом, с большими подачами и повышенным трением по задней поверхности резца сопровождается не только большей глубиной деформированного слоя, но и более высокой степенью пластической деформации.
Повышение скорости резанья уменьшает степень пластической деформации поверхностного слоя. Влияние скорости резания проявляется через изменение размеров переходной пластически деформированной зоны стружкообразования.
Знание степени пластической деформации, а также зависимости упрочнения материала от степени пластической деформации позволяет определить характеристики наклепанного слоя обработанной детали. Степень наклепа поверхностного слоя определяется по формуле:
(2.89)
где – НМпов твердость поверхностного наклепанного слоя детали,
НМ ucx – твердость исходной структуры материала.
Упрочнение материала в процессе резания протекает в более сложных условиях, чем при обычных способах деформирования: сжатия, растяжения и кручения. Пластической деформации срезаемого слоя одновременно присущи элементы устойчивого и неустойчивого течения материала.
Если по аналогии с процессом стружкообразования долю устойчивого течения в подрезцовом слое оценить коэффициентом А, то этим же коэффициентом можно учесть вклад в упрочнение от устойчивого течения.
При испытаниях на растяжение между напряжением течения, параметрами кривых упрочнения и временным сопротивлением на разрыв имеется следующая взаимосвязь [85]:
при устойчивом течении деформируемого материала (до образования шейки)
, (2.90)
при неустойчивом течении деформируемого материала (после образования шейки)
, (2.91)
где s s – напряжения течения деформируемого материала,
sзв - напряжение течения в момент появления шейки,
sв – временное сопротивление на разрыв,
Г – мера деформации,
n – показатель упрочнения.
Поскольку между величинами s s, sзв, sв, и твердостью обрабатываемого материала имеется прямопропорциональная зависимость, то соотношения (2.90) и (2.91) справедливы для описания изменения твердости в процессе пластической деформации. С учетом отмеченного, уравнение (2.89) преобразуется к виду
(2.92)
Сопоставление расчетных и экспериментальных значений степени наклепа обрабатываемых материалов показывает что формула (2.92) дает несколько завышенные результаты по сравнению с фактическими значениями степени наклепа. Более высокие расчетные значения объясняются тем, что формула (2.92) не учитывает явления разупрочнения поверхностного слоя под действием высоких температур и нарушения его сплошности.
Качественное изменение степени наклепа обработанной поверхности с изменением различных параметров процесса резания по формуле (2.92) полностью совпадает с экспериментальными данными.
Таким образом, применение методов теории пластичности и разрушения к обработке материалов резанием позволяет математически описать поведение деформируемого материала не только в срезаемом, но и в подрезцовом слое.
16. Расчетный метод построения эпюры напряжений на задней поверхности режущего инструмента
Анализ моделирования пластической деформации подрезцового слоя показывает, что один и тот результат по определению глубины деформации можно получить при различных схемах линий скольжения. Однако каждому полю линий скольжения соответствует определенное напряженно-деформированное состояние. Поэтому использование метода линий скольжения не позволяет получить однозначного решения и следовательно, является малопригодным для определения напряженного состояния подрезцового слоя.
Решение задачи о распределении напряжений в подрезцовом слое выполним методом совместного решения уравнений равновесия и условия пластичности. Деформацию поверхностного слоя детали под резцом рассматриваем по аналогии с деформацией под действием индентора протяженностью . Здесь принято: hз – износ резца по задней поверхности, а – толщина среза, f - угол наклона пластически деформируемой зоны стружкообразования.
Касательное напряжение по задней поверхности резца характеризуем величиной t = m t s, где m - коэффициент трения резца о поверхность обрабатываемой детали, t s – предел прочности обрабатываемого материала на срез. Касательное напряжение по линии среза перед резцом принимаем t = t s. Усредненное касательное напряжение по линии среза и по задней поверхности составляет:
(2.93)
Материал, расположенный вне зоны пластической деформации и поверхность резца рассматриваем как абсолютно жесткие, деформирующие пластическую зону под линией среза со скоростями uх и uу (рис. 2.40). Точку, в которой скорость перемещения деформируемого материала под действием сжатия и скорость сдвига равны, определим как нейтральную. Поскольку uх = u, uу = u × tgf, где u - скорость резания, то абсцисса нейтральной точки равна:
, (2.94)
где Н – глубина зоны пластической деформации под линией среза.
Используя дифференциальные уравнения равновесия и условие пластичности, а также допущения изапишем для нагрузки, действующей по нормали к поверхности среза единичной ширины
. (2.95)
Рис. 2.40 Схема расчета контактных напряжений по задней поверхности резца
Эта нагрузка эквивалентна усилию внедрения индентора единичной ширины и протяженностью . (2.96)
За величину максимальных касательных напряжений принято их усредненное значение перед условной плоскостью сдвига .
Приравнивая величины Р N и и решая относительно Н получим:
, (2.97)
где ,
.
В частности при m1® 0 Н ® 0, т.е. уменьшение коэффициента трения обрабатываемого материала о заднюю поверхность резца уменьшает глубину наклепанного слоя детали. При максимальном трении m1= 1 глубина наклепа максимальная и определяется выражением:
. (2.98)
Расчетные значения глубины наклепа, полученные методом совместного решения уравнений равновесия и пластичности имеют практически такое же совпадение с экстремальными, как и при моделировании пластического вихря под резцом.
Следовательно, в конце площадки контакта имеют место следующие напряжения
. (2.104)
По мере удаления от конца площадки контакта напряжения возрастают по экспоненциальной зависимости. Так как разность касательных напряжений, действующих на пластически деформированный слой со стороны инструмента и обрабатываемой детали не может превосходить величины t s, то из условия получим:
. (2.105)
Итак, начиная с Х = Х1 имеет место условие
(2.106)
Величину С определим из условия: при Х = Х1
. (2.107)
Таким образом, в области контакта с максимальным касательным напряжением (Х £ Х1)
(2.108)
С учетом смены знака касательных напряжений по границе с недеформированным материалом условие равновесия на участке 0 £ Х £ Х0 будет
(2.109)
или
,
где Х0 – координата нейтральной точки определяемой по уравнению (2.94)
Из граничного условия sу = sу0 при Х = Х0 следует , где sу0 – нормальное напряжение, действующее по линии среза и определяемое по уравнению (2.108) при Х = Х0.
Соответственно на участке 0 £ Х £ Х0 будут действовать следующие напряжения:
(2.110)
Закономерность изменения напряжений аналогична закономерности изменения напряжений на передней поверхности резца и включает параболическую, линейную и экспоненциальную зависимости.
Характерной особенностью эпюр напряжений, является то, что касательные и нормальные напряжения отличаются между собой только в области, примыкающей к режущей кромке. Это связано с тем, что при низких скоростях резания коэффициента трения незначительно отличается от единицы. Поэтому на участке выхода резца из контакта с обрабатываемым материалом касательные напряжения могут меньше или больше нормальных напряжений. Вблизи режущей кромки нормальные напряжения, как правило, больше чем касательные.
Разработанная методика определения напряжений по линии среза обрабатываемого материала может быть использована для прочностного расчета режущей части инструмента.
17. Расчет сил резания методом линий скольжения
Определение усилия резания по этому методу включает построение сетки линий скольжения, получение уравнения изменения гидростатического давления и проверку выполнения условия для скоростей деформации вдоль линий скольжения.
Для упрощения решения пренебрегаем влиянием наплыва металла перед резцом в начальный момент врезания.
Применительно к процессу врезания расчет усилия проводим исходя из нагрузки, которую может передавать пластически деформированный материал, заключенный между его начальной границей и передней поверхностью режущего инструмента. Упрочнение и несплошность материала в момент врезания не учитываем.
Если допустить равномерное упрочнение материала при переходе в стружку, то на условной плоскости сдвига приращение предела прочности на сдвиг будет характеризоваться коэффициентом . В дальнейшем для упрощения решения считаем это упрочнение скачкообразным.
Составление уравнений изменения гидростатического давления и определение поля напряжений начинаем с анализа граничных условий на поверхности АЕ (А1А) (рис. 3.1). По нормали к этой поверхности sУА = 0 и, следовательно, напряжение sХА является главным сжимающим напряжением.
Рис. 3.1. К расчету сил методом линий скольжения
Пользуясь соотношением Генки для линий скольжения в виде РА – Р D = ± (1 + А)tА jАВ, получим для гидростатического давления в точке D:
для процесса врезания инструмента:
, (3.1)
для установившегося процесса стружкообразования:
. (3.2)
Нормальное напряжение, действующее в момент врезания по передней поверхности режущего инструмента, определим, используя известные из теории пластичности соотношения [45, 97] или круг Mopa, построенный для точки D (рис. 3.2.):
Рис. 3.2. Круг Мора для точки D (врезание)
Учитывая, что удельное давление на передней поверхности инструмента равно по величине и противоположно по направлению нормальному напряжению, а также значение касательного напряжения , запишем выражения для расчета тангенциальной Р Z и нормальной Р N составляющих усилия врезания инструмента в обрабатываемый материал:
(3.4)
Составляющие силы резания для установившегося процесса стружкообразования определим из рассмотрения сил, действующих на условную плоскость сдвига. Тангенциальная Р Z и нормальная Р N составляющее усилия резания передаваемые на этом участке равны:
(3.5)
Уравнения (3.5) учитывают упрочнение обрабатываемого материала только перед условной плоскостью сдвига. Влияние упрочнения материала после пересечения условной плоскости сдвига учтем усредненным коэффициентом :
(3.6)
Отметим, что формулы (3.4) и (3.6) получены из условия плоской деформации.
Применительно к обработке малопластичных материалов, когда отделение элементов срезаемого слоя от основной массы изделия является следствием распространения хрупкой трещины перед резцом и сопровождается образованием стружки надлома, величину составляющих силы резания для установившегося процесса стружкообразования целесообразно определять исходя из сил, передаваемых частицами стружки на переднюю поверхность инструмента (рис. 3.2).
Используя модель сыпучего тела, заключенного между передней поверхностью инструмента и поверхностью разрыва, и считая, что свободная поверхность ориентирована по направлению действия равнодействующей сил, запишем для нормального давления оказываемого на переднюю поверхность:
Рп = f t s (1 + p - 2b), (3.7)
где f – коэффициент, характеризующий взаимодействие между частицами стружки при их взаимном перемещении;
b - угол трения частиц стружки о переднюю поверхность.
Длина контакта элементов стружки с передней поверхностью режущего инструмента согласно схеме их взаимодействия составит (рис. 3.2):
. (3.8)
С учетом полученных выражений (3.7) и (3.8) и условий трения между частицами стружки вблизи передней поверхности выражения для определения касательной Р Z и нормальной Р N запишем в виде:
(3.9)
Расчетные значения касательной и нормальной составляющих силы резания имеют заниженные значения по сравнению с экспериментальными, причем большие расхождения наблюдаются для нормальной составляющей силы резания.
Формулы (3.6 и 3.9) для расчета составляющих силы резания могут быть использованы при приближенной их оценке применительно к обработке мягких материалов. Применительно к обработке высокотвердых материалов формулы (3.8) дают удовлетворительное совпадение для тангенциальной составляющей силы резания и большое расхождение для нормальной составляющей. В этом случае учет сил, действующих по задней поверхности, является обязательным.
Доля сил, действующих по задней поверхности режущего инструмента, в общем сопротивлении материалов резанию зависит в основном от величины площадки износа, толщины среза, величины радиуса закругления режущей кромки, а также контактной деформации и интенсивности трения между обрабатываемой поверхностью и режущим инструментом.
Поскольку метод линий скольжения является не единственным, позволяющим определить усилия, действующие по передней и задней поверхностям режущего инструмента, то по аналогии с методом линий скольжения предварительно рассмотрены экстремальные методы оценки усилий, действующих на режущий инструмент без учета сил по задней поверхности.
18. Метод верхней оценки
Согласно методу верхней оценки нагрузка, вычисленная для соответствующего кинематического состояния деформируемого металла, всегда больше, чем фактическая нагрузка. Рассматривая различные кинематические состояния можно определить различные нагрузки. Но все они будут больше фактических. Наименьшая из них будет наиболее близкой к фактической нагрузке.
Теорема о верхней оценке для условий плоской деформации математически может быть записана в виде:
(8.1)
Для упрощенного поля линий скольжения, состоящего из спрямленных линий, вдоль которых имеет место разрыв скоростей и между которыми материал движется как жесткое тело (Г=0), первый интеграл правой части равен 0; второй и третий интеграл заменим суммой, поскольку скорость разрыва постоянна вдоль спрямленной линии скольжения.
С учетом принятого можем записать:
, (8.2)
Рисунок 8.1 – Схема напряженного состояния в зоне резания и годограф скоростей
По теореме синусов:
(8.3)
Откуда
(8.4)
Откуда
Подставляя полученные значения скоростей в формулу 8.2 получим:
(8.5)
Сокращая в выражении 8.5 скорость υ и преобразуя его, получим формулу для вычисления составляющей силы резания Рz для плоской задачи:
(8.6)
Составляющая силы резания Рz для объемной задачи рассчитывается по формуле:
19. Метод нижней оценки
Теорема нижней оценки несущей способности жестко пластического материала доказывает, что нагрузка соответствует статистически возможному состоянию меньше, чем предельная нагрузка.
Рассматривая различные возможности статистического состояния, можно подсчитать различные нагрузки, меньшие предельной. Наибольшая из них будет ближе всего к предельной нагрузке.
Для испытания данного метода представим напряженное состояние в области, примыкающей к зоне резания, как сумму напряженных состояний двух полос.
Рис. 7.1 Схема напряженно деформированного состояния
на поверхности резца
Рис. 7.2 Круг Мора для смоделированного напряженного состояния на задней поверхности резца
Используя схему напряженно деформированного состояния на рисунке 7.1 и 7.2 заменим для тангенциальной и нормальной составляющей силы резания следующие выражения:
(7.1)
где h - угол между направлением полосы I и нормальным напряжением s n .
Тангенциальная составляющая силы резания, рассчитанная по методу нижней оценки, является меньшей величиной не только в сравнении с экспериментальными данными, но и в сравнении со значениями, полученными по методу линий скольжения и верхней оценки.
Поскольку, применительно к процессу резания, метод нижней оценки уступает по точности методу линий скольжения и методу верхней оценки, то в дальнейшем предпочтение будет отдаваться первым двум методам.
Дата добавления: 2021-03-18; просмотров: 95; Мы поможем в написании вашей работы! |
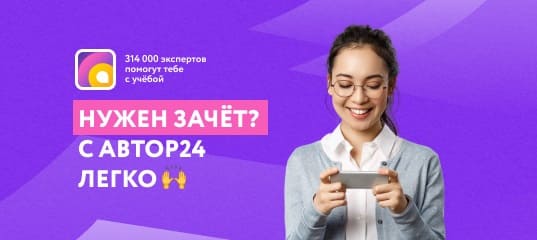
Мы поможем в написании ваших работ!