Расчет переходно пластически деформированной зоны при стружкообразовании.
Математические модели описания формообразования материала при стружкообразования
Изучению особенностей пластического формоизменения материала при обработке его резанием посвящено большое количество работ.
Не останавливаясь на физической стороне процесса резания, отметим, что аналитическое исследование напряженно-деформированного состояния срезаемого слоя, прямо или косвенно сводится к использованию элементов теории пластичности. Основу теории пластичности составляет теория напряжений, теория деформаций и уравнения связи между напряжениями и деформациями. Теория напряжений описывает статическое состояние процесса. Напряженное состояние в любой точке описывается тензором напряжений [63, 67, 97]:
(1.1)
где sх, sу, s z – нормальные напряжения;
tху, t xz, t zy – касательные напряжения.
Теория деформации описывает кинематическое состояние процесса. Деформационное состояние описывается тензором скоростей деформаций:
, (1.3)
где Sх, Sу, Sz – нормальные компоненты скорости деформаций;
Sху, Syz, Szx – компоненты скорости деформаций сдвига.
Критерием перехода в пластическое состояние являются условия текучести Треска-Сен-Венана или Мизеса [63, 67, 153]. Согласно первому условию,
s1 - s3 = 2t S, (1.5)
Большее соответствие опытным данным дает условие Мизеса /10, 15/, согласно которому пластическое течение наступает при достижении интенсивностью касательных напряжений предела текучести материала на сдвиг
|
|
, (1.6)
В теории резания известно использование условия пластичности Треска-Сен-Венана [16, 100] и условия пластичности Мизеса [169, 230].
Стремясь упростить математические выкладки, использовали упрощенные методы
Метод линий скольжения. Этот метод применим в основном к плоским задачам.
Решение сводится к построению сетки линий скольжения и использованию их свойств Напряжения и скорости находятся последовательно. Применение метода линий скольжения позволило получить целый ряд важных решений в области механики процесса резания материалов.
Существенным недостатком этого метода является то. что решение задач проводится методом проб и ошибок.
Расчетные методы они основаны на экстремальных принципах теории пластичности. Мощность, вычисленная на основе статически допускаемого поля напряжений, является нижней оценкой, а мощность, вычисленная на основе кинематически возможного поля скоростей, является верхней оценкой.
В методе нижней оценки поле напряжений удовлетворяет уравнениям равновесия, условию пластичности, граничным условиям для напряжений. Метод верхней оценки требует, чтобы поле скоростей удовлетворяло условию несжимаемости среды и граничным условиям для скоростей и перемещении Ш. Кобаяши и Е Г Томсеном В.А. Остафьев С-Г Мелихов Г А Дель.
|
|
Применение этого метода позволило решить задачи о распределении напряжений в зоне стружкообразовамия, положении границ пластически деформированной зоны и остаточных напряжений обработанной поверхности.
2. Расчетные схемы стружкообразования
Основной механизм процесса резания обычно изучают на модели с одной режущей кромкой, расположенной перпендикулярно вектору скорости относительного перемещения инструмента и заготовки.
Рис. 1.1 Схема стружкообразования по И.А. Тиме:
1 – срезаемый слой; 2 – плоскость сдвига; 3 – стружка;
4 – резец
В соответствии с этой моделью предполагается, что переход срезаемого слоя в стружку происходит в результате сдвиговых деформаций по единственной плоскости, проходящей от режущей кромки к свободной поверхности срезаемого слоя. По обе стороны от этой плоскости деформация отсутствует.
Наиболее простая схема, учитывающая конечные размеры зоны деформации, впервые предложена А.А. Бриксом [24] (рис. 1.2).
|
|
Рис. 1.2 Схема стружкообразования по А.А. Бриксу
А.А. Брикс высказал предположение, что пластические сдвиги в срезаемом слое происходят по семейству плоскостей, расположенных веерообразно и расходящихся от режущей кромки (из точки 0). В точке В наружная поверхность стружки претерпевает излом. Наличие такого излома приводит к разрыву напряжений и скоростей перемещения частиц материала в этой точке.
Н.Н. Зорев в своих работах [58, 59] рассмотрел упрощенную схему стружкообразования с веерообразной переходной пластически деформированной зоной отличающуюся от схемы А.А. Брикса наличием плавного споряжения в точке В (рис. 1.3).
Рис. 1.3 Упрощенная схема стружкообразования по Н.Н. Зореву
Применение такой схемы стружкообразования приводит к неопределенности задачи в области режущей кромки.
В.Б. Палмер и П.Б. Оксли [10] исключили эту неопределенность, поместив центр веера линий скольжения на некотором расстоянии от режущей кромки (рис. 1.4). Кроме того, авторы использовали криволинейный контур зоны пластической деформации вблизи свободной поверхности для соблюдения условия выхода линий скольжения.
Рис. 1.4 Схема стружкообразования по В. Палмеру и П. Оксли
|
|
Э. Ли и Б. Шафер предложили гипотезу, в которой предполагается, что стружка напряжена до предела тякучести в треугольной зоне, прилегающей к плоскости сдвига АВ (рис. 1.5), но деформация остается при этом простым сдвигом вдоль АВ. Трение стружки по передней поверхности режущего инструмента определяется углом h.
Рис. 1.5 Схема стружкообразования по Э. Ли и Б. Шаферу
Анализируя поле линий скольжения, соответствующее принятой схеме стружкообразования Э.Ли и Б. Шаффера, в работе [82] справедливо отмечено, что в области, примыкающей к свободной поверхности стружки, оно мало достоверно и может быть использовано лишь в той мере, в какой это делается в настоящее время при решении задач с применением метода верхних оценок [45, 188, 189].
Схему стружкообразования Э.Х. Ли и Б.В. Шаффера усовершенствовали М.К. Шоу, Н.Г. Кук, И. Финни [244]. Ими было сделано предположение, что плоскость сдвига не является плоскостью максимальных касательных напряжений и линия скольжения не совпадает с плоскостью сдвига (рис. 1.6).
Некоторые исследователи стремясь учесть размеры зоны пластической деформации ограничивали ее параллельными линиями. В.И. Садчиков [166] и В.С. Кушнер [91] показывают, что схемы стружкообразования с зоной пластической деформации ограниченной параллельными линиями удовлетворяют условиям сплошности и непрерывности деформируемой среды.
Типичные схемы стружкообразования, пластическая деформация в которых происходит в зоне с параллельными границами, приведены на рис. 1.10.
Рис. 1.10 Схема стружкообразования с параллельными границами срезаемого слоя со стружкой: а) без учета сопряжения;
б) с учетом плавного сопряжения
Анализируя напряженное и деформированное состояние при резании металлов, В.И. Садчиков [165] допускает, что передняя граница зоны стружкообразования совпадает с плоскостью сдвига (рис. 1.11).
Рис. 1.11 Схема стружкообразования по В.И. Садчикову
И. Шакрабарти [218] рассмотрел схему стружкообразования, в которой зона пластической деформации расположена перед плоскостью сдвига (рис. 1.12)
Рис. 1.12 Поле линий скольжения по И. Шакрабарти
Несмотря на то, что схема не отражает действительного состояния обрабатываемого материала в зоне деформаций и носит искусственный характер, подобный подход позволил автору аналитически оценить размеры зоны стружкообразования.
Рис. 1.14 Схемы стружкообразования с учетом пластической деформации
В работах [16, 89] приводятся схемы зоны пластической деформации, иллюстрирующие результаты, полученные Г.Л. Куфаревым методом делительной сетки (рис. 1.15, а) и Г.Д. Делем по изменению микротвердости (рис. 1.15, б).
Рис. 1.15 Зоны деформации по Г.Л. Куфареву (а)
и Г.Д. Делю (б)
Наиболее близкой к экспериментальным очертаниям зоны пластической деформации, представленных на рис. 1.15, является схема, предложенная Н.Н. Зоревым [58] на основании анализа статически возможного поля напряжений и свойств линий скольжения
3. Аналитические соотношения для определения положения и размеров зоны стружкообразования
Анализ схем стружкообразования свидетельствует о большой значимости зоны пластической деформации, поскольку ее положение и размеры определяют закономерности формоизменения срезаемого слоя. Этим объясняется тот факт, что уже с самых ранних работ в области механики процесса резания делаются попытки установить математические соотношения, позволяющие определить положение и размеры зоны стружкообразования в зависимости от основных параметров процесса резания.
схематизации зоны стружкообразования одной плоскостью сдвига или областью с параллельными границами ее положение характеризуется углом наклона условной плоскости сдвига f (рис. 1.20, а). В схемах стружкообразования с веерообразной переходной пластической зоной ее положение определяют углом наклона конечной границы. f1. (рис. 1.20, б).
Рис. 1.20 – Параметры пластической зоны:
а – с параллельными границами; б - веерообразная
Размеры зоны пластической деформации в моделях стружкообразования с единственной плоскостью сдвига характеризуется ее длиной, в моделях с параллельными границами – длиной и расстоянием между начальной и конечной границами этой зоны d и в моделях с веерообразной пластической зоной – длиной и углом между границами d f (рис. 1.20, б).
Одно из самых ранних соотношений для угла сдвига было дано С.А. Зворыкиным [55]. Анализируя схему сил для модели стружкообразования с единственной плоскостью сдвига и используя гипотезу о минимуме усилий резания К.А. Зворыкин получил следующее выражение для угла сдвига
, (1.7)
где h - угол внутреннего трения;
b - угол трения стружки о переднюю поверхность резца;
g - передний угол.
Несколько позднее А.А. Брикс /24/ вывел соотношение для модели с веерообразной зоной пластической деформации, определяющее положение ее конечной границы
, (1.8)
где g1 – угол наклона касательной, проведенной к наружной границе зоны стружкообразования в точке ее пересечения с наружной поверхностью стружки.
В дальнейшем Х. Эрнст и М.Е. Мерчант [222], применяя принцип минимума работы резания к модели с одной плоскостью сдвига, получили формулу:
, (1.9)
Г.В. Стэблер [243], анализируя процесс резания и основываясь на эмпирическом законе о направлении потока стружки предложил зависимость между углами:
(1.10)
Х. Хукс [225] применил другие методы аналитических исследований и получил следующее решение:
, (1.11)
где В – коэффициент, характеризующий влияние нормальных напряжений на сопротивление пластическому сдвигу;
m - коэффициент трения стружки о резец.
Приведенные выше формулы получены из рассмотрения только сил, действующих на стружку. Возникающие при этом напряжения не рассматривались. Э.Х Ли и Б.В. Шаффер [10, 189] предположили, что напряжения, передающие силы резания от плоскости сдвига на переднюю поверхность достигают предела текучести, но вызывают деформацию лишь по одной плоскости сдвига. Из геометрии поля линий скольжения (рис. 1.5) получено уравнение вида
, (1.12)
Э. Х. Ли и Б.В. Шаффер считают решение Х. Эрнста и М.Е. Мерчанта правильным в диапазоне b - g £ 0 и отклонили его в диапазоне b - g > 0, так как материал стружки здесь не может передавать требуемые усилия. Согласно теории Э.Х. Ли и Б.В. Шаффера к перенапряжению материала стружки приводят также соотношения для угла сдвига полученные Г.В. Стэблером в диапазоне 2b - g > 0, А.А. Бриксом в диапазоне g1 + b - g > 0 и К.А. Зворыкиным в диапазоне h + b - g > 0.
В основу решения методом линий скольжения М.К. Шоу, Н.Г. Кук и И. Финни положили гипотезу о несовпадении максимального усилия сдвига с плоскостью сдвига. В результате было получено соотношение углов (рис. 1.6).
, (1.13)
где b1– угол отклонения направления плоскости сдвига от направления максимального напряжения сдвига.
Авторы полагают, что угол b1 зависит от условий резания, но никаких сведений о методах его определения не приводят.
П.Б. Оксли [10] применил упрощенное поле линий скольжения к модели зоны деформации ограниченной прямыми параллельными линиями скольжения наклоненными под углом сдвига f к линии среза. Используя соотношение Хенки, учитывающее упрочнение материала в зоне резания, а также связь напряжений, действующих по передней поверхности и плоскости сдвига, П.Б. Оксли получил приближенную зависимость:
f = 50 - 0,8(b - g), (1.14)
Нетрудно заметить, что приведенные выше соотношения (1.7)-(1.14) дают линейную зависимость между параметрами и большинство могут быть сведены к следующему уравнению:
f = С1 – С2(b - g), (1.14)
где С1и С2 – постоянные величины.
Таким образом, несмотря на существенные различия в полученных результатах в настоящее время накоплен определенный материал по определению положения переходной пластически деформированной зоны при стружкообразования с учетом геометрии режущего инструмента и условий трения стружки о переднюю поверхность. Математические модели стружкообразования, учитывающие механические свойства обрабатываемого материала, пока еще далеки от совершенства и не нашли практического применения.
4. Схематизация объемной деформации при стружкообразовании плоскими процессами.
Задачи формоизменения срезаемого слоя решаются исследователями, как правило, для условий плоской деформации [10, 20, 58, 91, 93, 156, 222]. Положительной стороной таких решений является простота математического аппарата. Очевидно, что такие решения справедливы только для случая, когда ширина среза намного превышает его толщину. В практике обработки материалов резанием такое соотношение выдерживается далеко не всегда. Поэтому представляется целесообразным получение решений для всего диапазона соотношений толщины и ширины среза. Такие задачи формоизменения срезаемого слоя относятся к трехмерным. Малочисленность решений трехмерных задач применительно к процессу обработки материалов резанием связана с определенными трудностями, Например, метод линий скольжения, используемый для решения плоских задач, пока еще не разработан для решения трехмерной деформации. Другой трудностью является то, что для определения кинематических соотношений условие несжимаемости среды является недостаточным, так как при задании одного граничного условия два других могут находиться в произвольных комбинациях. Следовательно, для решения трехмерной задачи требуются дополнительные условия.
Условием, накладываемым на решение задачи, может быть, например, минимум мощности, затрачиваемый на деформирование срезаемого и подрезцового слоев. Анализ показывает, что добиться полной совместности статически допустимого поля напряжений и кинематически возможного поля скоростей практически не удается. Поэтому такая задача обычно решается с использованием приближенных методов.
Один из таких приближенных методов можно получить из анализа условия несжимаемости среды:
(2.1)
Это условие можно представить в виде двух уравнений:
,
, (2.2)
где u = u ¢ + u ²
Рассмотрим формоизменение срезаемого слоя сечением А1В1ВС при несвободном резании. Определяющее влияние на процесс деформации оказывает закрытый полупериметр В1А1С (рис. 2.1, а). В соответствии со схемой деформации Зибеля, используемой в теории обработки металлов давлением, каждая частица деформируемого сечения А1В1ВС стремится перемещаться по нормалям к свободной поверхности периметра. Следовательно, сечение среза стремится к сечению стружки с контуром B1CE1D1, которое отличается от исходного сечения, как по размерам, так и по форме. Увеличение площади сечения стружки определяется коэффициентом усадки, На рис. 2.1, а контуры АВВ1А1 и В1СЕ1D показывают разновеликие площади сечения среза и стружки, а контур В1СЕ1D1 сечение стружки с учетом ее усадки.
а б в
г
Рис. 2.1 Схема формирования сечения стружки:
a – φ ¹ 0; б, в, г - φ = 0; б - < 1; в -
= 1; г -
> 1
Рис. 2.1, б, в, г иллюстрируют изменение формы сечения стружки в широком интервале изменения отношения , которое подтверждается экспериментами Ю.С. Шарина [257]. При обработке стали 30 и 18ХНВА в диапазоне соотношений
= 0,08…3,0 и υ = 0,25…2,0 м/с, действительные направления схода стружки отличались от теоретических не более чем на 10%.
Гипотеза о том,. что направление схода стружки нормально диагонали сечения среза на практике означает равенство наибольшей диагонали сечения среза ширине сечения стружки:
(2.3)
где t - глубина резания,
φ и φ1 – главный и вспомогательные углы в плане,
- угол наклона диагонали сечения среза к вспомогательной режущей кромке,
s – подача.
В соответствии с законом наименьшего сопротивления, сформулированным С.И. Губкиным [188] с определенной степенью точности можно считать, что равенство диагонали сечения среза и ширины стружки будет соблюдаться и при свободном резании.
Знание начальных и конечных размеров ширины среза позволяет судить об интенсивности деформации вдоль режущей кромки. Поскольку компоненты скорости резания, характеризующие процесс пластической деформации в двух взаимно перпендикулярных плоскостях, пропорциональны интенсивности деформаций в этих плоскостях, то выражения для определения величин y ¢ и y ² запишем в виде:
(2.4)
Подстановка y ¢ и y ² в уравнения (2.2) показывает, что условие несжимаемости выполняется при всех соотношениях величин t и s.
Полученные выражения для параметров y ¢ и y ² позволяют решать задачи применительно к трехмерной деформации срезаемого слоя методом суперпозиции двух плоских процессов, протекающих во взаимно перпендикулярных плоскостях, одна из которых ориентирована нормально к режущей кромке, а другая проходит через нее. Результирующая мощность деформации срезаемого слоя определяется векторной суммой этих двух плоских процессов.
Частным решением такой задачи является рассмотрение процесса деформации в плоскости ХОУ, ориентированной перпендикулярно диагонали, разделяющей открытый и закрытый полупериметры сечения среза, и в плоскости УOZ, проходящей через эту диагональ. В этом случае j + j1 - w = 0 и из (2.3) следует y ¢ = 1 и y ² = 0, т.е. полная мощность формоизменения срезаемого слоя равна мощности деформации в плоскости перпендикулярной диагонали сечения среза.
Отметим, что по нормали к диагонали среза толщина среза неодинакова (рис. 2.1, а) и интенсивность утолщения в каждой точке сечения среза является величиной переменной. С целью упрощения изложения материала будем пользоваться усредненной величиной толщины среза, получаемой как частное от деления площади среза на длину диагонали, разделяющей открытый и закрытый полупериметры сечения среза:
. (2.4)
Применение формулы (2.4) ограничивается условием . За пределами этого соотношения толщина среза постоянна и равна значению, вычисленному для
. Это соответствует такому режиму обработки, когда после прохождения резца остаются следы от обрабатываемой поверхности. Дальнейшее увеличение подачи не вызывает увеличения площади среза.
В тех случаях, когда для описания формоизменения срезаемого слоя используется метод суперпозиции двух плоских процессов, один из которых протекает в плоскости перпендикулярной главной режущей кромки, а другой вдоль нее, вышеприведенное ограничение отсутствует.
5. Устойчивость пластического материала в зоне резания.
Возможности непрерывного пластического течения материала при стружкообразовании ограничены. При определенных условиях резания процесс пластического деформирования становится неустойчивым выражающимся в локализации, по месту кторой в дальнейшем происходит полное или частичное разделение элементов стружки.
В результате исследований установлены материалы и диапазоны режимов резания способствующие образованию элементной, суставчатой, сливной и циклической стружек, а также механизмы их образования. Предпринимались также попытки решить задачу оценки деформируемости материалов при переходе в стружку с использованием критериев прочности [169], диаграмм пластичности [198], теории неустойчивости течения [196, 226, 250]. Математического описания процесса стружкообразования в условиях прерывистого резания пригодного для практического использования получено не было.
Задачу оценки деформируемости материала при стружкообразовании следует отнести к классу задач теории разрушения, которому предшествует неустойчивое пластическое течение.
В настоящее время общепринят механизм разрушения согласно которому нагружение тела сопровождается перемещением, образованием и исчезновением дислокаций [26, 31, 114, 176]. Объединение дислокаций может привести к зарождению микротрещин, перерастающие в местах их повышенной плотности в макротрещины. Развитие макротрещины приводит к разрушению материала.
Оценка деформируемости материала при стружкообразовании предполагает определение деформаций или напряжений их вызывающих, при которых образуется разрыв сплошности структуры в зависимости от свойств материала, напряженного состояния, истории деформирования, температурно-скоростных и других условий. Несмотря на значительные успехи в работах по дислокационному представлению о резании металлов, среди которых следует выделить монографию В.К. Старкова [176], количественная оценка деформируемости материалов в условиях стружкообразования на таком уровне пока невозможна. Поэтому в механике разрушения ограничиваются рассмотрением развития трещин в идеально-упругом или упругопластическом материале, когда основной объем находится в упругом состоянии и лишь вблизи вершины трещины материал деформируется пластически.
Развитите трещины может сопровождаться устойчивой или неустойчивой пластической деформацией. В первом случае развитие трещины может затормозиться. Во втором случае неустойчивое течение приводит к лавинообразному распространению трещины.
В теории пластичности получили развитие методы оценки устойчивости упругопластического равновесия, основанные главным образом на критериях устойчивости. Однако применение этих критериев при решении технологических задач сопряжено с математическими трудностями, связанных с тем, что при обработке материалов резанием имеют место большие деформации и перемещения. В связи с этим при анализе процесса прерывистого стружкообразования получила распространение инженерная теория устойчивости пластического деформирования, исходящая из приближенных критериев.
Р. Юти [226], изучая процесс прерывистого стружкообразования исходил из критерия, согласно которому наступление неустойчивости в деформации материала, сопровождающийся отделением элемента стружки, происходит, если добавочная работа равна нулю.
Иной разработаны критерии равнопрочности для идеально-пластических, хрупких и упрочняющихся материалов. Это позволяет предсказать в какую сторону будут отклоняться фактические значения сопротивления резанию от расчетных по теории максимальных касательных напряжений, но не дает возможность прогнозировать вид образующейся стружки.
Способность материала подвергаться пластической деформации без разрушения оценивалась по диаграмме пластичности. Предполагается, что диаграмма пластичности является единой для различных напряженных состояний.
Предлагаемая методика позволяет оценить вероятность образования суставчатых и элементных стружек, однако является очень громоздкой так как требует построения поля линий скольжения в зоне резания, определения напряжений в условной плоскости сдвига и на передней поверхности, использование тарировочного графика «коэффициент жесткости напряженного состояния – пластичность». Широкого распространения эта методика для решения прикладных задач, связанных с оценкой деформируемости материалов при стружкообразовании, не получила.
В работах [26, 250] предполагается, что пластическая неустойчивость и связанная с ней локализация деформаций при стружкообразовании наступает в тот момент, когда нарушается соответствие между упрочнением материала и приращениями напряжений вследствие деформации. Авторы отмечают, что источником неустойчивого пластического течения считается склонность к адиабатическим процессам. Такое представление является значительным шагом в изучении неустойчивого течения материала в зоне резания, так как позволяет прогнозировать деформируемость обрабатываемого материала в области высоких скоростей резания используя несложные выражения [250]. Что же касается низких скоростей резания, когда повышение температуры в зоне стружкообразования является незначительной, проявление термической нестабильности в процессе пластической деформации является сомнительной.
Проблема устойчивости деформирования жестко-пластического тела и ее связь с единственностью решения краевой задачи изучалась Р. Хиллом [189]. Р. Хилл вывел допустимый диапазон путем исключения диапазона состояний, выходящих за предел, ограниченный возможностью пластической деформации при конечной величине усилия резания.
Такой подход позволяет получить сведения о возможных границах зоны пластической деформации, но не дает возможность оценить вероятность получения прерывистой или сливной стружки при обработке реального материала.
Разработка прикладных методов оценки деформируемости материалов при различных условиях обработки резанием, т.е. способность материала образовывать тот или иной вид стружки, позволит уменьшить объем экспериментальных исследований и получить необходимую информацию о целесообразных режимах обработки на стадии проектирования технологического процесса.
6. Определение коэффициента сплошности при стружкообразовании
В работах ученых показано, что вид образующейся стружки является следствием устойчивого или неустойчивого пластического течения материала в процессе стружкообразования Неустойчивое течение, которому предшествует предварительная деформация элемента срезаемого слоя, начинается при том условии, что в каком-нибудь месте этого элемента последующее приращение деформационного упрочнения нивелируется деформационным разупрочнением. В этом случае деформация локализуется в том месте, где сопротивление течению уменьшается в наибольшей степени.
В общем случае процесс деформационного упрочнения и рае упрочнения описывается известным из теории пластичности уравнением [97]
(2.7)
Где t, Г, и Т - соответственно напряжения, степень, скорость и температура деформации материала в зоне стружкообразования.
Применительно к условиям стружкообразования склонность к адиабатическому процессу деформации возрастает в области высоких скоростей резания, когда выделяемая теплота деформации локализуется в зоне ее образования. Причем, чем выше скорость резания, тем больше проявляется неустойчивость пластического течения в результате адиабатического сдвига.
В области низких и средних скоростей резания, когда повышение температуры в зоне стружкообразования является незначительным, проявление термической нестабильности в процессе пластической деформации является сомнительным. Источник неустойчивости в этом случае имеет другую природу.
Второй член в уравнении (2.7) является всегда положительным и поэтому он не может быть источником неустойчивого течения.
Рассмотрим возможность возникновения неустойчивого течения при стружкообразовании в результате смены знака первого члена правой части уравнения (2.7).
Процесс образования любого элемента стружки на начальном этапе характеризуется нарастанием пластической деформации и, как следствие, упрочнением срезаемого слоя. Производная является положительной величиной, и процесс начальной деформации элемента стружки характеризуется устойчивым течением материала в зоне стружкообразования.
В процессе дальнейшей пластической деформации до 200% и более ресурс пластичности исчерпывается в той или иной мере в зависимости от свойств материала. Результатом этого является появление разрывов в структуре образующейся стружки [26, 176]. Зародышами разрывов служат инородные включения, поры, границы зерен и прочие ослабленные участки в структуре. Нарушение сплошности деформируемого материала снижает его сопротивление деформации, что эквивалентно его разупрочнению Производная в уравнении (2.7) принимает отрицательные значения, являясь источником неустойчивого пластического течения в зоне стружкообразования.
При низких значениях скорости резания, когда время протекания пластической деформации в зоне стружкообразования достаточно, чтобы неустойчивое течение распространилось на все сечения стружки, происходи сдвиг одного элемента стружки относительно другого. По мере роста скорости резания процесс неустойчивого течения распространяется на меньшую часть сечения стружки, что приводит к образованию ступенчатой и при высоких скоростях к сливной стружке, если при этом не имеет место явление термопластического сдвига.
Дадим количественную оценку описанным выше явлениям, для чего смоделируем разрывы, образующиеся в зоне пластической деформации, микротрещинами, условно расположенными на внешней стороне стружки и ориентированными по плоскостям сдвига (рис. 2.10).
Рис. 2.10 Моделирование разрывов
в зоне стружкообразования
Распространение зародившейся трещины происходит только в том случае, если напряжение и деформация в ее вершине достигнут критических значений. Такому напряженному состоянию материала стружки, примыкающему к вершине трещины длиной ау соответствует уравнение
, (2.14)
где - вязкость разрушения при плоском деформированном состоянии,
tр - напряжение разрушения.
(2.26)
Полученное уравнение позволяет количественно оценить степень устойчивости пластического течения материала при стружкообразовании в области низких и средних значениях скорости резания. Если значения А стремится к нулю, то процесс пластического течения является неустойчивым. Переход срезаемого слоя в стружку происходит с образованием отдельных элементов.
При значениях А близких к единице процесс пластического течения характеризуется устойчивостью с переходом срезаемого слоя в сливную стружку.
С увеличением скорости резания параметр А увеличивается, причем более интенсивно для малых толщин среза. Таким образом, увеличение скорости резания усиливает тенденцию к образованию сливной стружки. При сохранении постоянной величины сочетания параметров образуется примерно одинаковый тип стружки.
Сопоставление расчетных значений параметра А с типом образующейся стружки показывает что в области значений 0 £ А £ 0,1, образуется элементная стружка, в области 0,9 £ А £ 1,0 - сливная стружка. Промежуточным значениям параметра А соответствует ступенчатый вид стружки.
К недостаткам формулы (2.26) следует отнести то, что величина угла сдвига не всегда является известной. В общем случае угол f изменяется в пределах 20-40°. Анализ формулы (2.26) показывает, что изменение угла f в этих пределах изменяет величину А не более чем на 10%. Принимая среднее значение угла сдвига f = 30° в формуле (2.26) можно с погрешностью 5% оценить значение параметра А.
Таким образом, на стадии проектирования технологического процесса вид образующейся стружки рекомендуется определять по упрощенной формуле:
, (2.27)
где - вязкость разрушения при плоском деформированном состоянии, МПа;
а - толщина среза, м;
u - скорость резания, м/с;
t s - предел прочности обрабатываемого материала на срез, Мпа;
r - плотность обрабатываемого материала, Мпа с2/м2.
7. Угол сдвига при обработке пластичных и хрупких материалов. Определение угла сдвига при обработке пластичных и хрупких материалов с использованием методов.
При схематизации зоны стружкообразования одной плоскостью сдвига или областью с параллельными границами ее положение характеризуется углом наклона условной плоскости сдвига f (рис. 1.20, а). В схемах стружкообразования с веерообразной переходной пластической зоной ее положение определяют углом наклона конечной границы.f1. (рис. 1.20, б).
Используя различные схемы стружкообразования и гипотезы, получили соотношения для угла сдвига.
Анализируя схему сил для модели стружкообразования с единственной плоскостью сдвига и используя гипотезу о минимуме усилий резания К.А. Зворыкин получил следующее выражение для угла сдвига
,
где h - угол внутреннего трения; b - угол трения стружки о переднюю поверхность резца; g - передний угол.
А.А. Брикс вывел соотношение для модели с веерообразной зоной пластической деформации, определяющее положение ее конечной границы , (1.8)
где g1 – угол наклона касательной, проведенной к наружной границе зоны стружкообразования в точке ее пересечения с наружной поверхностью стружки.
Х. Эрнст и М.Е. Мерчант, применяя принцип минимума работы резания к модели с одной плоскостью сдвига, получили формулу: ,
Г. В. Стэблер, анализируя процесс резания и основываясь на эмпирическом законе о направлении потока стружки предложил зависимость между углами : .
X. Хукс применил другие методы аналитических исследований и получил следующее решение:
гдеВ - коэффициент, характеризующий влияние нормальных напряжений на сопротивление пластическому сдвигу;
- коэффициент трения стружки о резец.
Приведенные выше формулы получены из рассмотрения только сил, действующих на стружку. Возникающие при этом напряжения не рассматривались. Э. Х. Ли и В.В. Шафферпредположили, что напряжения, передающие силы резания от плоскости сдвига на переднюю поверхность достигают предела текучести, но вызывают деформацию лишь по одной плоскости сдвига. Из геометрии поля линий скольжения получено уравнение вида
В основу решения методом линий скольжения М.К. Шоу, Н.Г.Кук и И. Финни положили гипотезу о несовпадении максимального усилия сдвига с плоскостью сдвига. В результате было получено соотношение углов:
где - угол отклонения направления плоскости сдвига от направления максимального напряжения сдвига.
Авторы полагают, что угол зависит от условий резания, но никаких сведений о методах его определения не приводят.
П.Б. Окслиприменил упрощенное поле линий скольжения к модели зоны деформации ограниченной прямыми [параллельными линиями скольжения наклоненными под угломсдвига ф к линии среза. Используя соотношение Хенки, учитывающее упрочнение материала в зоне резания, а также связь напряжений, действующих по передней поверхности и плоскости сдвига, П.Б. Оксли получил приближенную зависимость:
Нетрудно заметить, что приведенные выше соотношения дают линейную зависимость между параметрами и большинство могут быть сведены к следующему уравнению:
где C1 и С2 - постоянные величины.
Обычно соотношение угла сдвига с другими параметрами ищется в форме:
f = f( b, g)
где β - угол трения стружки о резец,
γ - передний угол.
Влияние режимов резания, характеристик обрабатываемого материала, вида образуемой стружки и других параметров процесса резания на величину угла сдвига учитывается лишь в той степени, в какой оно связано с изменением среднего коэффициента трения. Это является одной из причин того, что расчетные значения угла сдвига существенно отличаются от экспериментальных данных.
Использование методов теории пластичности позволяет получить соотношения для угла сдвига, учитывающие непосредственное влияние на него отмеченных характеристик процесса резания.
Величину нормального (гидростатического) давления на границе пластически деформированной зоны определим из схемы сил, действующих на резец со стороны передней поверхности. Линия действия результирующей силы резания R составляет с границей зоны стружкообразования угол f + β – γ, в результате чего нормальное давление на эту плоскость составит:
Р1 = В t s tg(f + b - g), (2.28)
где τ s - предел текучести обрабатываемого материала на сдвиг,
В - коэффициент, учитывающий упрочнение материала в результате пластической деформации при переходе его в стружку.
Согласно теореме Генки [45, 97] гидростатическое давление изменится на величину пропорциональную удвоенному значению этого угла и составит:
для элементного стружкообразования
,
для сливного стружкообразования
.
Общее выражение для гидростатического давления запишется в виде
(2.29)
Приравнивая значения Рпо уравнениям (2.29) к (2.28) и, проводя, соответствующие преобразования получим:
(2.30)
Величина А, характеризующая вид образующееся стружки, оказывает сложное воздействие на угол сдвига. В целом увеличение параметра А вызывает рост угла сдвига. Увеличение параметра В приводит к уменьшению угла f при постоянном значении разности углов b - g , т.е. материалы склонные к наклепу обрабатываются резанием с меньшим углом сдвига, что подтверждается исследованиями П.Б. 0ксли [10].
Уравнение (2.35), связывающее параметры f, b и g, А и В является трансцендентным относительно угла f. Уравнения обычно решаются графически путем построения зависимости b - g = f(f) для заданных величин А и В и произвольно выбранных значений угла f. По построенной кривой b - g = f(f) находится значение угла сдвига соответствующее разности углов β – γ.
Аналитическое выражение угла сдвига через элементарные функции в данном случае является невозможным, поэтому решение уравнения (2.35) выполним приближенно. Для получения приближенного решения значение угла сдвига входящего в формулу (2.35) в виде свободного члена (не являющегося аргументом тригонометрической функции) примем постоянным и равным его среднему значению .
Такое допущение несколько искажает действительную зависимость между углами f, b и g. Погрешность решения можно устранить введением коэффициентов компенсирующих влияние изменения свободного члена f на величину разности углов.
Подставляя значение в уравнение (2.30) и решая относительно аргумента тригонометрической функции f, получим:
, (2.31)
Расчет переходно пластически деформированной зоны при стружкообразовании.
Несмотря на существенные различия в полученных результатах в настоящее время накоплен определенный материал по определению положения переходной пластически деформированной зоны пристружкообразования с учетом геометрии режущего инструмента и условий трения стружки о переднюю поверхность. Математические модели стружкообразования, учитывающие механические свойства обрабатываемого материала, пока еще далеки от совершенства и не нашли практического применения.
Оценка величины зоны пластической деформации встречает большие трудности связанные с тем, что до сих пор не получены достаточно надежные методы прогнозирования ее протяженности в направлении схода стружки.
Изучению размеров зоны пластической деформации посвящено ограниченное количество работ. Приводимые в них данные получены экспериментально для определенных материалов и режимов обработки и отличаются между собой до 200 раз, что затрудняет их использование применительно к другим условиям обработки материалов резанием. Например, П.Б. Оксли пришел к выводу, что усредненная толщина пластической области в 6-12 раз меньше длины поверхности сдвига, по данным в 2,6 раза, а по мнению Г.Л. Куфарева, В.А. Говорухина и М.Г. Гольдшмидта - только в 2 раза.
B.C. Кушнер] в своих расчетах использовал протяженность пластически деформированной зоны равную 0,3...0,5 от толщины среза. В.Ф. Бобров считает, что толщиназоны деформации изменяется от величины соизмеримой толщиной срезаемого слоя до очень малой в зависимости от условий обработки.
Существует мнение, что размер зоны пластической деформации соизмерим с величиной зерен. Основой такого утверждения является тот факт, что при малой зернистости достигается меньшая шероховатость. Используя это утверждение Е.Эдер для оценки скорости деформации при стружкообразовании принял расстояние между плоскостями сдвига, ограничивающими зону пластической деформации, равным 0,0025 мм, соответствующим среднему расстоянию между кристаллами металла.
А.У. Маргулес при точении стали с толщиной срезаа =0,1-0,25 мм и скоростью резания и = 1,6-5 м/с получил толщину пластически деформированной зоны стружкообразования в пределах 0,02-0,05 мм.
В работе без всякого обоснования ширина зоны пластической деформации была принята равной 2,5 мм.
Н.В. Талантов, исследуя закономерности пластического деформирования при обработке упрочняемых материалов со скоростями резания выше зоны наростообразования, выдвинул гипотезу, что толщина зоны стружкообразования определяется длиной участка упрочнения. Однако количественных оценок по определению его протяженности автором не дается.
Трудности определения величины зоны пластической деформации при стружкообразовании вызывают различное толкование по влиянию на нее различных факторов. Так Г.Л. Куфарев, К.Б. Окенов, В.А. Говорухин установили, что при увеличении скорости резания ширина зоны стружкообразования уменьшается, но остается достаточно большой, соизмеримой с толщиной срезаемого слоя. Н.Н. Зорев считает, что при больших скоростях резания зона стружкообразования сильно сужается и можно считать ее величиной второго порядка малости по сравнению с толщиной стружки. Аналогичного мнения придерживается В.Ф. Бобров.
По данным И.Дж.А. Армарего, Р.Х. Брауна и К. Битанса при обработке материалов резцом с малым или отрицательным передним углом пластическая зона весьма узкая с четкой границей между заготовкой и стружкой. Применение большого переднего угла приводит к развитой зоне пластического сдвига с постепенным переходом от заготовки к стружке. Эти данные не согласуются с результатами В.Ф. Боброва, который отмечает, что зона пластической деформации по своей толщине соизмерима с толщиной срезаемого слоя только при малых передних углах инструмента, больших толщинах срезаемого слоя и низких скоростях резания. При больших передних углах и высоких скоростях резания зона пластической деформации резко сужается. Такое рассогласование данных по видимому связано с различными условиями проведения экспериментов.
В настоящее время уже делаются попытки определить размеры пластически деформированной зоны расчетным путем. Известен аналитический метод определения границ зоны пластической деформации для случая плоского напряженного стостояния, основанный на использовании метода инвариантов Римана для решения квазилинейных дифференциальных уравнений в частных производных . Ввиду сложности этого метода самими же авторами делается вывод о необходимости проведения дополнительных исследований.
В.К. Старков [176] для расчета длины опережающего упрочнения перед вершиной резца предлагает формулу: , (1.26)где g – показатель распределения напряжения перед резцом, sz – действующее напряжение перед резцом, s0,2 – условный предел текучести обрабатываемого материала.
Аналитическое выражение для определения ширины зоны пластической деформации получено В.И. Садчиковым:
где: h – параметр, определяемый соотношением ,
t0, s0 – касательное и нормальное напряжения, действующие по условной плоскости сдвига.
Дата добавления: 2021-03-18; просмотров: 92; Мы поможем в написании вашей работы! |
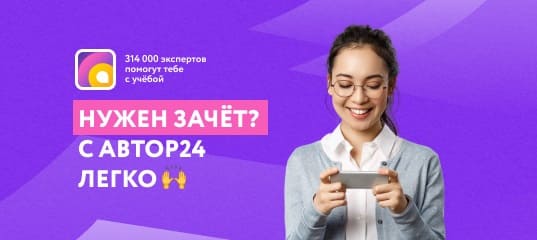
Мы поможем в написании ваших работ!