Плоскопараллельные концевые меры длины (КМД)
МИНОБРНАУКИ РОССИИ
ФГБОУ ВПО Ижевский государственный технический университет
имени М.Т. Калашникова
Кафедра КТПМП
Лабораторная работа №2
«Методы и средства измерений линейных величин. Универсальные измерительные инструменты и приборы. Часть 1»
МЕТОДИЧЕСКИЕ УКАЗАНИЯ
к лабораторным работам по дисциплине
«Нормирование точности»
Ижевск, 2013
Составители: к.т.н., вед. инженер Института механики Бармина Н.А.
ст. преподаватель кафедры КТПМП Береснева А.В.
к.т.н., доцент кафедры КТПМП Попова Е.И.
доцент кафедры КТПМП Попова З.Е.
Методические указания к лабораторным работам по дисциплине «Нормирование точности» для студентов направлений 150900.62 и 151900.62 и специальности 151001 очной и заочной форм обучения. – Ижевск, 2013г. – 24 с.
Протокол от 10.01.2013г. №_110_
Заведующий кафедрой КТПМП Гольдфарб В.И.
______.______.20___г.
Рецензенты:
Методические указания предназначены для проведения лабораторных работ по дисциплине «Нормирование точности» направлений 150900.62, 151900.62 и специальности 151001 очной и заочной форм обучения.
Методические указания содержат описания схем, методов и средств измерений геометрической точности изделий машиностроения.
|
|
ЛАБОРАТОРНАЯ РАБОТА №2
«Методы и средства измерений линейных величин. Универсальные измерительные инструменты и приборы. Часть 1»
Цель работы: изучить методы и средства контроля линейных величин, освоить методику измерений при помощи универсальных измерительных инструментов.
К универсальным измерительным инструментам для измерения линейных величин относят: штангенинструменты, микрометрические инструменты, скобы рычажные и индикаторные, наборы концевых мер длины, микроскопы, оптиметры, микрокаторы, нутромеры, индикаторные головки и др.
Выбор универсальных средств измерений
Средства измерений выбирают в зависимости от точности контролируемого параметра и допускаемой погрешности измерений искомого размера, установленной ГОСТ 8.051-81. Кроме того, учитывают конструктивные особенности, программу выпуска и габариты контролируемого изделия.
Согласно ГОСТ 8.051-81, величина допуска размера является определяющей характеристикой для подсчета допускаемой погрешности измерений [Δизм], которая может быть принята от 1/5 до 1/3 допуска (Т). Установлены следующие зависимости между ними: для IT10 и грубее - [Δизм] до 20% от допуска изготовления; для IT6-IT9 – до 30%; для IT2-IT5 – до 35% от допуска Т.
|
|
Выбор средства измерений состоит в сравнении его основной погрешности с допускаемой погрешностью измерения; при этом основная погрешность должна бать меньше (или равна) допускаемой погрешности измерения. Однако, следует учитывать, что чрезмерная точность измерений то же нецелесообразна, так как приводит к необоснованному удорожанию и усложнению процесса измерений. Поэтому не рекомендуется выбирать инструмент, чья основная погрешность меньше 1/20 х [Δизм]. Величину основной погрешности выбранного средства измерений следует выяснить в Приложении 2 [5].
Пример. Ступень вала с диаметром Æ36h9(-0,062) и длиной 50±IT14/2(±0,31). Необходимо выбрать измерительный инструмент для контроля этих размеров.
Решение. Допуск диаметрального размера равен 0,062 мм или 62 мкм. Величина допускаемой предельной погрешности измерения для размера изготовленного по IT9 определяется по формуле [Δизм] = 0,062 х 1/4 ≈ 0,016 мм. Из таблицы Приложения 2 [5] «Метрологические характеристики универсальных измерительных инструментов и приборов» выбираем микрометр гладкий с диапазоном измеряемых размеров от 25 до 50 мм, второго класса точности МК50-2, у которого основная погрешность равна ±4 мкм и следовательно меньше чем [Δизм]. Для измерения длиннового размера изготовленного по IT14 при [Δизм] = 0,62 х 1/5 ≈ 0,16 мм выбран штангенглубиномер ШГ-160-0,05, основная погрешность которого (согласно таблице из приложения 1) составляет (±0,05мм).
|
|
Задание 1 Измерить указанные на эскизе линейные размеры заданной детали, предварительно выбрав необходимые универсальные средства измерений по таблице в приложении (описание предлагаемых в данной лабораторной работе инструментов и приборов см. далее). Заполнить таблицу из приложении. Сделать заключение о годности по каждому размеру.
Штангенинструменты
В совокупности штангенинструменты позволяют измерить наружные и внутренние размеры (диаметры отверстий и валов; глубину пазов, отверстий; расстояние между плоскостями, высоту выступов и т.п.) и производить разметку. Штангенинструменты изготовляют с ценой деления по шкале нониуса 0,1; 0,05 или, реже, 0,02 мм. Устройство штангенинструментов показано на рис. 2.1.
|
|
![]() |
а)
в)
б) г)
Рис.2.1. Штангенциркуль (тип II)–ШЦII(а), штангенглубиномер–ШГ(б), штангенциркуль (тип I)─ШЦ I (в), штангенрейсмас–ШР(г)
1, 2 – губки для разметочных работ и наружных измерений;
3 – стопорный винт;
4 – штанга;
5, 6, 7, 8 – микрометрическое устройство, служащее для плавного перемещения каретки и создания нормального давления;
9 – каретка со шкалой нониуса;
10, 11 – губки для наружных и внутренних измерений;
12 – основание – база для измерений штангенглубиномером;
13 – чертилка для производства разметочных работ или измерительный наконечник;
14 – хомутик для крепления чертилки.
В последнее время стали широко использоваться штангенинструменты с ценой деления 0,01 мм и 0,02 мм, без шкалы нониуса, но с цифровой (ШЦЦI рис. 2.2 а) или стрелочной индикацией (ШЦКI рис. 2.2 б). Снятие показаний при такой конструкции приборов обычно не вызывает затруднений.
а) б)
Рис. 2.2 Штангенциркули (тип I со встроенным глубиномером).
ШЦЦI (а) и ШЦКI (б)
Отсчетное устройство нониусных штангенприборов – штанга с нанесенной на ней шкалой с интервалом 1 мм и свободно перемещающаяся по штанге рамка, на скосе которой (напротив миллиметровой шкалы) нанесена вспомогательная шкала, называемая нониусом (нониус служит для отсчета дробных долей миллиметра).
Каждое пятое деление шкалы штанги отмечено удлиненным штрихом, а каждое десятое – штрихом более длинным, чем пятое, и числом, соответствующим расстоянию в сантиметрах от нулевого штриха.
Штангенприборы модулей 1 и 2 выпускаются с отсчетом по нониусу 0,1 и 0,05 мм. Модуль шкалы нониуса показывает, через какое число делений миллиметровой шкалы штанги будут располагаться штрихи нониуса, смещенные на величину отсчета по нониусу.
а) б)
в)
г)
Рис. 2.3. Шкалы штангенприборов: с отчетом по нониусу 0,1 мм модулей а –1, б – 2;
с отсчетом по нониусу 0,05 мм модулей в – 1, г – 2.
Штангенприбор модуля 1 с отсчетом по нониусу 0,1 мм (рис. 2.3 а) имеет шкалу длиной 9 мм с десятью делениями. Расстояние между двумя соседними штрихами шкалы нониуса составляет 0,9 мм, что короче на 0,1 мм интервала деления шкалы штанги, равного 1 мм. При совмещении нулевого штриха шкалы нониуса с нулевым штрихом шкалы штанги (основной шкалы), первый за нулевым штрих нониуса окажется смещенным относительно первого штриха штанги на 0,1 мм; соответственно, второй штрих шкалы нониуса – на 0,2 мм от соответствующего деления на штанге, а десятый (последний штрих) – уже на 1 мм; следовательно, десятый штрих шкалы нониуса точно совпадет с девятым штрихом основной шкалы (что соответствует 9 мм). Если при измерении размера детали шкала нониуса оказалась сдвинутой относительно шкалы штанги так, что ее первый штрих (не считая нулевого) совпал с первым штрихом шкалы штанги, размер детали определяют, суммируя отсчет по шкале штанги (ноль) и отсчет по шкале нониуса (1х0,1=0,1 мм), т.е. 0+0,1=0,1 мм.
Таким образом, для определения размера детали необходимо отсчитать по шкале штанги целое число миллиметров и прибавить к нему доли миллиметра, полученные умножением цены деления нониуса на порядковый номер штриха нониусной шкалы, совпавшего со штрихом штанги (нулевой штрих нониуса не учитывают).
Штангенприбор модуля 1 с отсчетом по нониусу 0,05 мм (рис. 2.3 в) имеет длину шкалы нониуса 19 мм, разделенную на 20 частей. При этом одно деление шкалы нониуса составляет 19:20=0,95 мм, что меньше целого миллиметра на 0,05 мм. Отсчет показаний при измерении размеров аналогичен отсчету по шкале нониуса 0,1 мм.
Предпочтительными и более удобными являются штангенприборы модуля 2 с «растянутой» шкалой, отсчетами по нониусу 0,1 мм (рис. 2.3 б) и 0,05 (рис. 2.3 г). Растянутый нониус с величиной отсчета 0,1 мм имеет длину 19 мм, поэтому одно деление шкалы нониуса составляет 1,9 мм, оно короче 2-х деления шкалы штанги на 0,1мм. Штангенприбор модуля 2 с отсчетом по нониусу 0,05 мм имеет длину шкалы 39 мм, разделенную на 20 частей, т.е. одно деление нониуса равно 39:20=1,95 мм, что короче на 0,05 мм двух делений шкалы штанги. Обычно на шкале нониуса с отсчетом 0,05 мм цифры нанесены через каждые пять делений:
0; 25; 50; 75; 1 (обозначающих 0; 0,25; 0,50; 0,75; 1 мм).
Примеры установки штангенинструментов относительно измеряемых поверхностей изображены на рис. 2.4.
![]() |
а)
б) в)
Рис. 2.4. Схемы измерения штангенциркулем (а),
штангенглубиномером (б), штангенрейсмасом (в)
При измерении штангенциркулями (ШЦ) или штангенглубиномерами (ШГ) эти инструменты обычно держат в руках и перемещают относительно контролируемой детали (на рис. 2.4 а и 2.4 б показано правильное их расположение относительно измеряемых поверхностей). Штангенрейсмасы (ШР) – это группа штангенинструментов, предназначенных для измерения линейных размеров относительно плоскости плиты или другой плоской протяженной поверхности, на которую устанавливается объект измерения и ШР своим основанием (рис. 2.4 в). Для измерения размеров различных типов (например: размеров типа «А» и «В» рис. 2.4 в), ШР может быть оснащен сменными наконечниками, наряду с чертилкой 13 (рис. 2.1 в). Перед началом работы рекомендуется проверить настройку «нуля»: у ШЦ при сомкнутых губках 10, 11 или 1, 2 (рис. 2.1 а); у ШГ при совмещении плоскости основания 12 и измерительного торца штанги 4 (рис. 2.1 б); у ШР при касании измерительного наконечника 13 плоскости установочной плиты (рис.2.1б).
Микрометрические инструменты
Микрометрические инструменты основаны на использовании высокоточной винтовой пары, позволяющей преобразовать сравнительно небольшое поступательное перемещение микровинта во вращательное движение заметно большей величины нониусного барабана с круговой шкалой установленного на микровинте. Область применения микрометрического инструмента зависит от типа инструмента. Микрометры гладкие (МК) и микрометры зубомерные (МЗ) используются для измерения наружных элементов деталей (призматических, цилиндрических или фасонных), глубиномеры микрометрические (ГМ) – для измерения глубин и высот, нутромеры микрометрические (НМ) – для измерения размеров отверстий.
Устройство микрометрических инструментов показано на рис. 2.5 и рис. 2.6.
а)
б)
в) Рис. 2.5. Микрометры гладкие МК:
а – с пределами измерения 0-25 мм (а),
б – с пределами измерения 25-50 мм,
в – микрометр электронный МКЦ с пределами измерения 0-25 мм;
1 – скоба; 2 – пятка; 3 – микрометрический винт (микровинт); 4 – стопор;
5 – стебель; 6 – нониусный барабан с круговой шкалой; 8 – трещоточное устройство для создания нормального давления; 9 – установочный калибр.
Закрепление барабана на микровинте осуществляется разными способами в зависимости от конструктивных особенностей инструмента. Цена деления – 0,01 мм, пределы измерения для микрометров могут быть – 0-25 мм, 25-50 мм, 50-75 мм и т.д. с интервалом в 25 мм. Пределы измерения микрометрического глубиномера от 0 до 25 мм (при смене измерительных наконечников от 0 до 100 мм). Основная погрешность микрометрических инструментов в зависимости от диапазона измерений и класса точности может составить ±2,5 мкм для пределов измерения 0 - 25 мм, и до ±50 мкм для размеров 400…500 мм.
б)
а)
Рис. 2.6. Глубиномер микрометрический (а) и нутромер микрометрический (б).
1 – основание; 2 – стебель; 3 – измерительный наконечник; 4 – трещотка (муфта предохранительная с усилием 7±2 Н); 5 – нониусный барабан; 6 – стопор.
В отсчетном механизме прибора микрометрическая винтовая пара используется как увеличивающее устройство, преобразующее небольшие продольные перемещения винта в существенно бóльшие перемещения круговой шкалы 5 (рис. 2.5), что и позволяет производить измерения с достаточной дискретностью показаний (0,01 мм). Один полный оборот нониусный барабан совершает, если микрометрический винт перемещается в осевом направлении на один шаг равный 0,5 мм.
![]() |
а) 8,28 мм б)3,62 мм
Рис. 2.7. Примеры расчета размера по шкале микрометра
На стебле 2 отсчитывается количество делений, не считая нулевого, с интервалом 0,5 мм (на рис. 2.7а их 16, следовательно, 16х0,5=8,0 мм, а на рис. 2.7б их 7, следовательно, 7х0,5=3,5мм). После этого по шкале нониусного барабана отсчитываются десятые и сотые доли миллиметра (а – 0,28 мм, б –0,12 мм). Затем показания на стебле и на барабане складываются между собой и получается результат. Таким образом значения измеряемых размеров на рис. 2.7а и 2.7б равны 8,0 + 0,28 =8,28 мм и 3,5 + 0,12 = 3,62 соответственно.
Подготовка микрометра к работе производится в следующей последовательности:
1. Микрометр освобождают от смазки, тщательно протирают измерительные поверхности.
2. Проверяют нулевое показание нониусного барабана 6 (рис. 2.5). Для этого, вращая микрометрический винт 3 за корпус трещотки 8, приводят в соприкосновение измерительные поверхности пятки 2 и микровинта 3 (для микрометров с пределами измерения 0-25 мм) или между торцами пятки и микровинта устанавливают концевую меру или специальный цилиндрический установочный калибр 9, равный 25 мм (для микрометров с пределами измерения 25-50 мм). При соприкосновении измерительных поверхностей нулевой штрих, нанесенный на скошенном крае нониусного барабана 6, должен устанавливаться против продольного длинного штриха на стебле.
3. Если такого совпадения нет, то необходимо настроить микрометр на «нуль». Для этого, заклинив микровинт стопорным устройством 4 (см. рис 2.5) и вращая корпус трещотки 7 против часовой стрелки на 1-1,5 оборота, выводят микровинт из соединения с нониусным барабаном, устанавливая его нулевой штрих напротив продольного штриха стебля. Вращая корпус трещотки в обратную сторону, вводят микровинт в зацепление с торцем нониусного барабана. Освобождают стопор и снова проверяют правильность установки. В некоторых современных конструкциях микрометров закрепление барабана на микровинте осуществляется радиально расположенным ввертышем (винтом). Прцедура поднастройки «нуля» в этом случае производиться аналогично, но при слегка вывернутом винте.
Плоскопараллельные концевые меры длины (КМД)
В соответствии с ГОСТ 9038-73 плоскопараллельными концевыми мерами называют меры в форме прямоугольных параллелепипедов или круглых цилиндров с двумя плоскими параллельными измерительными плоскостями (рис. 2.8.).
Концевые меры являются основным средством сохранения единства мер в машиностроении и служат для передачи размера от государственного эталона длины до изделия. С помощью КМД производятся установка, градуирование и поверка измерительных инструментов и приборов, их широко используют в лабораторной цеховой практике измерения линейных величин, а также для точных разметочных работ, наладки станков и приспособлений. Концевые меры изготовляются из хромистой стали с коэффициентом линейного расширения a=(11,5±1)*10-6, твердого сплава a=(5-6)*10-6 или кварца. Плитки подвергаются закалке до твердости не ниже 62 HRC. Материал концевых мер должен быть стабильным. Изменение размеров концевых мер в течение 12 месяцев не должно превышать на 1 м длины:
± 0,3 мкм для концевых мер класса 0
± 1,0 мкм для концевых мер класса 1
± 2,0 мкм для концевых мер класса 2-3
Основные характеристики концевых мер:
1. Средняя длина – длина перпендикуляра, опущенного из середины измерительной поверхности меры на ее противоположную поверхность (рис. 2.9.).
2. Отклонение от плоскопараллельности, которое определяется наибольшей по абсолютной величине разностью между длиной меры в любой точке и средней длиной.
Рис. 2.8. Плоскопараллельные концевые меры длины.
Общий вид
Рис. 2.9. Плоскопараллельная концевая мера длины. Размеры между рабочимт и нерабочими поверхностями
По ГОСТ 9038-73 плитки выпускаются с градациями размеров через 0,001; 0,01; 0,1; 0,05; 10; 25; 50; 100 и 1000 мм и комплектуются в 15 различных наборов с содержанием от 2-х до 112 плиток. Основные наборы: №1 – 83 меры, №3 – 112 мер, №14 - 42 меры (с четырьмя защитными)
По точности изготовления, т.е. по допустимым отклонениям длины и отклонениям от плоскопараллельности, концевые меры делятся на четыре класса 0, 1, 2, 3-й. Для мер, находящихся в эксплуатации, предусмотрены дополнительно 4-й и 5-й классы (ГОСТ 8.116-75).
В зависимости от предельной погрешности при аттестации размеров мер их делят на пять разрядов: с 1-го по 5-й. В аттестате указывается номинальный размер концевой меры, отклонение номинального размера и разряд, к которому отнесен проверяемый набор мер. Применение концевых мер по разрядам с учетом поправок к их номинальным размерам повышает точность измерения.
Плоскопараллельные меры обладают способностью прочно сцепляться друг с другом при надвигании измерительной поверхности одной плитки на измерительную поверхность другой. Эта способность концевых мер сцепляться измерительными поверхностями называется притираемостью, позволяет составлять блоки из нескольких концевых мер разных размеров. Притираемость концевых мер объясняется молекулярным притяжением, когда они покрыты тончайшей пленкой смазывающей жидкости (толщина пленки не превышает 0,2 мкм), что незначительно влияет на точность размера блока концевых мер.
Наборы концевых мер комплектуются так, чтобы из наименьшего количества концевых мер можно было составлять блоки с малыми градациями (с интервалами 0,01 мм и 0,001 мм). При составлении блока из концевых мер следует стремиться, чтобы блок состоял из возможно меньшего количества мер. Составлять блок более чем из пяти мер обычно не рекомендуется.
Перед составлением блока делают его предварительный расчет, подбирая в первую очередь концевые меры, имеющие тысячные доли, затем сотые и десятые доли миллиметра и т.д.
Пример: требуется составить блок для размера 28,785 мм.
28,785
Первая мера 1,005
Остаток 27,78
Вторая мера 1,28
Остаток 26,5
Третья мера 6,5
Остаток (четвертая мера) 20
Приемы составления блока сводятся к следующему:
1. Очистить концевые меры от смазки ваткой, промыть авиационным бензином и насухо протереть салфеткой.
2. Наложить одну из мер на другую по рабочим граням примерно на треть длины рабочей поверхности и, плотно прижимая пальцами, подвигать вдоль большой оси до полного контакта рабочих поверхностей. Если с помощью легкого усилия не удается разъединить собранный блок, меры считаются притертыми. После притирки двух концевых мер к ним притирают третью и т.д., причем в начале притираются между собой меры малых размеров, собранный из них блок притирается к мере среднего размера, а затем уже к плитке большего размера.
Во избежание лишней промывки концевых мер и повреждения их рабочих поверхностей следует при работе с ними соблюдать следующие правила:
1) не брать рабочие поверхности промытых концевых мер руками, а только чистой салфеткой;
2) концевые меры размером свыше 5,5 мм класть на стол нерабочими поверхностями;
3) не притирать рабочую поверхность концевой меры к нерабочей, что вызывает появление царапин на рабочих поверхностях.
После окончания работы блок следует разобрать, концевые меры промыть авиационным бензином, тщательно протереть, смазать вазелином и положить в соответствующие ячейки футляра набора.
Для производства с помощью концевых мер различных измерений и разметки выпускают в соответствии с ГОСТ 4119-76 наборы принадлежностей к концевым мерам (рис. 2.11), в которые входят:
Державки со струбцинами для измерений
с верхним пределом 60, 110, 210, 330 мм – 4 шт.
Основание – 1 шт.
Плоскопараллельные боковики размером 10 мм – 2 шт.
Радиусные боковики размером 2 мм – 2 шт.
Радиусные боковики размером 5 мм – 2 шт.
Радиусные боковики размером 10 мм – 2 шт.
Радиусные боковики размером 15 мм – 2 шт.
Радиусные боковики размером 20 мм – 2 шт.
Центровой боковик – 1 шт.
Чертильный боковик –1 шт.
Трехгранная линейка 175 мм – 1 шт.
Сухари зажимные для крепления стяжками блоков с боковиками – 2 шт.
Плитки с рисками – 2 шт.
На рис. 2.10 показаны возможные примеры принадлежностей в сочетании с концевыми мерами.
![]() |
Рис. 2.10.
Блоки концевых мер в сочетании с притертыми на их концах боковиками и закрепленные для прочности соединения в державке позволяют измерять наружные и внутренние диаметры цилиндрических деталей и могут быть также использованы в качестве скобы или пробки для контроля различных линейных размеров (рис. 2.11). При составлении блока из концевых мер с боковиками для внутренних измерений необходимо учитывать размер, промаркированный на боковиках.
С помощью блока концевых мер чертильного боковика, закрепленного в державке, укрепленной в основании, можно производить разметку.
![]() | ![]() | ||
а) б)
Рис. 2.11.
Задание 2. Изучить и применить на практике плоскопараллельные концевые меры длины.
1. Изучить состав и характеристики набора концевых мер длины; основные характеристики записать в отчет;
2. Познакомиться с правилами работы с концевыми мерами длины;
3. По заданию преподавателя рассчитать и собрать блок концевых мер длины на определенный размер.
Дата добавления: 2021-03-18; просмотров: 230; Мы поможем в написании вашей работы! |
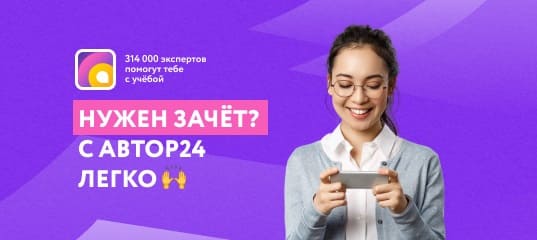
Мы поможем в написании ваших работ!