Доля участия основного металла в составе шва
при ручной дуговой сварке и наплавке в %
№ слоя шва | При сварке с учетом угла разделки кромок | При наплавке | ||
15° | 60° | 90° | ||
1 | 48—50 | 43—45 | 40—43 | 30—35 |
2 | 40—43 | 35—40 | 25—30 | 15—20 |
3 | 36—39 | 25—30 | 15—20 | 8—12 |
4 | 35—37 | 20—25 | 12—15 | 4—6 |
5 | 33—36 | 17—22 | 8—12 | 2—3 |
6 | 32—36 | 15—20 | 6—10 | <2 |
7—10 | 30—35 | — | — | — |
Работами Г.Л.Петрова доказано, что в пределах одного валика состав шва достаточно однороден вследствие интенсивного перемешивания металла в сварочной ванне, кроме узкого слоя шириной 0,2—0,4 мм, примыкающего к линии сплавления шва с основным металлом. Для обеспечения технологической и эксплуатационной прочности разнородных сварных соединений необходимо, чтобы в шве не было хрупких прослоек и малопрочных участков.
Предварительная оценка структуры и свойств различных участков шва при определенных степенях проплавления основного металла и использовании различных сварочных материалов может производиться по структурной диаграмме Шеффлера. Образование, строение и свойства зоны сплавления разнородных соединений зависят от двух факторов: от характера процессов кристаллизации разнородных материалов, определяющих структуру зоны и образование кристаллизационных прослоек переходного состава, а также процессов диффузии определяющих образование и развитие диффузионных переходных прослоек.
|
|
Как было отмечено выше, ширина кристаллизационных прослоек составляет 0,2—0,4 мм, и они имеют переходный состав между швом и основным металлом. При определенных размерах переходной зоны ширина хрупких прослоек в ней зависит от состава металла шва. Поэтому выбор электродов для сварки сталей разных структурных классов должен производиться с таким расчетом, чтобы образующиеся в процессе сварки переходные прослойки имели минимальные размеры и хрупкость, а в процессе эксплуатации при повышенных температурах не имели тенденции к быстрому развитию.
В зоне сплавления разнородных сварных соединений наряду с кристаллизационными прослойками могут образовываться и развиваться диффузионные прослойки в процессе сварки, термической обработки и эксплуатации изделий при повышенных температурах, что часто приводит к разрушениям разнородных соединений вблизи зоны сплавления. В стали наиболее подвижным легирующим элементом является углерод, перераспределение которого и определяет в основном образование диффузионных прослоек в зоне сплавления сварных соединений. Скорость диффузии углерода в ферритной фазе значительно больше, чем в аустенитной. Вследствие диффузии углерода образуются обезуглероженные и науглероженные зоны вблизи линии сплавления, что легко устанавливается металлографическим анализом, измерением твердости и методом радиоактивных изотопов.
|
|
Диффузия углерода начинает проявляться при воздействии температуры от 425° С, а при температуре выше Ас3 образовавшиеся диффузионные прослойки начинают исчезать.
Диффузионные прослойки возникают в сварных соединениях: аустенитных сталей с перлитными; перлитных сталей разного легирования; высокохромистых сталей с перлитными; аустенитных сталей с аустенитными швами, легированными более стойкими карбидообразующими элементами, и т.д.
Диффузия углерода наблюдается при его содержании выше предела растворимости и для многокомпонентных систем определяется не градиентом концентрации, а градиентом химического потенциала системы, так как всякая система стремится к минимальной свободной энергии. Поэтому диффузия элемента не всегда направлена в область меньших концентраций.
Отклонение от поведения идеальных растворов может быть настолько велико, что градиент концентрации и градиент химического потенциала или градиент активности могут быть различного знака, что приводит к отрицательной «восходящей» диффузии.
|
|
Образование диффузионных прослоек происходит: в процессе сварки при контакте жидкого металла с твердым основным вследствие большой растворимости углерода в жидком растворе железа; при охлаждении с высоких температур затвердевшего металла после сварки; при термической обработке сварных соединений или при их эксплуатации при температуре выше 425° С.
Процессы диффузии в твердом состоянии обусловлены «реактивной» диффузией при различном содержании карбидообразующих элементов в основном и наплавленном металлах, а также различной растворимостью углерода в ферритной и аустенитной фазах при контакте перлитной или ферритной стали с аустенитной.
Работами В.Н.Земзина, Г.Л.Петрова, Б.И.Брука, Л.С.Лившица показано, что диффузионные прослойки в зоне сплавления разнородных сварных соединений, выполненных при небольших значениях погонной энергии, характерных для ручной дуговой сварки, выражены незначительно в исходном состоянии после сварки.
Ю.Н.Готальский и Т.А.Струина показали, что при режимах ручной дуговой сварки, применяемых для соединения разнородных сталей, в зоне сплавления неаустенитного металла с аустенитным не обнаруживается изменения концентрации углерода в исходном состоянии после сварки.
|
|
При автоматической и электрошлаковой сварке с большими значениями погонной энергии и малой скоростью охлаждения диффузионные прослойки могут быть значительными в исходном состоянии. Наиболее сильно диффузионные прослойки развиваются после отпуска или при работе разнородных сварных соединений в интервале температур 425—700° С.
Снижение концентрации углерода на границе сплавления перлитных и ферритных сталей происходит за счет его перехода в аустенитную сталь, где термодинамическая активность углерода ниже. Разность концентраций углерода в растворе на границе сплавления и в слоях перлитных и ферритных сталей, удаленных от границы сплавления, служит движущей силой образования обезуглероженной и науглероженной зон, ухудшающих свойства разнородных сварных соединений при длительном нагреве их выше температуры 425° С. При длительных выдержках выше 650° С в обезуглероженной зоне происходит сильный рост ферритных зерен вследствие процесса собирательной рекристаллизации.
Чем более сильные карбидообразующие элементы содержит металл шва (Сг, W, V, Nb, Тi), тем сильнее обезуглероживается околошовная зона и тем быстрее происходит рост зерен в обезуглероженной зоне вследствие собирательной рекристаллизации и, наоборот, если шов легирован слабыми карбидообразователями (например, Мn), то даже при содержании углерода в обезуглероженной прослойке около 0,02%, собирательная рекристаллизация значительно замедляется. Термические напряжения и деформации в околошовной зоне оказывают большое влияние на процесс собирательной рекристаллизации. Поэтому в сварных соединениях аустенитной стали с перлитной или ферритной вследствие большой разности коэффициентов теплового расширения рост зерен в обезуглероженной зоне происходит интенсивнее, чем в сварных соединениях перлитной стали с высокохромистой ферритной или в соединениях перлитной стали, выполненных электродами на никелевой основе, т.е. в случаях когда различие в коэффициентах теплового расширения минимально.
Для сварных соединений разных структурных классов, эксплуатирующихся при повышенных температурах (выше 350° С) важно, чтобы швы были удалены от участков повышенной жесткости и максимальных рабочих напряжений. В шве и околошовной зоне разнородных сварных соединений должны быть сведены к минимуму концентраторы напряжений, для чего целесообразна механическая обработка наружной и внутренней поверхностей швов с обеспечением плавных переходов от шва к основному металлу.
ДИАГРАММА ШЕФФЛЕРА
Диаграмма Шеффлера является не равновесной, а реальной эмпирической диаграммой, построенной для металла шва в исходном состоянии после сварки при обычных усредненных режимах, применяемых при ручной дуговой сварке. Эта диаграмма не учитывает возможных изменений количества феррита при изменении скоростей охлаждения за счет изменения сварочных режимов или за счет последующей аустенизации или стабилизации металла шва и т. д. Кроме того, точность определения феррита по диаграмме Шеффлера зависит от применяемых коэффициентов, характеризующих аустенито- и ферритообразующую способность легирующих элементов, которые многими авторами оцениваются различно. По-видимому, это обусловлено тем, что ряд элементов имеет переменную валентность и их ферритообразующая способность может изменяться в зависимости от конкретного состава сплава.
Поэтому магнитные и металлографические методы определения феррита в шве дают более точные результаты. Тем не менее, с практически приемлемой степенью точности оценку структурного состояния металла в зависимости от его химического состава по диаграмме Шеффлера можно производить.
По химическому составу металла подсчитывается эквивалентное содержание хрома и никеля, для чего используются эмпирические коэффициенты.
Структурное состояние металла определяется точкой пересечения на диаграмме эквивалентных значений хрома и никеля, полученных расчетом.
При использовании подавляющего большинства типов электродов можно получить в пределах предусмотренного стандартом состава наплавленный металл с различной структурой. Для ряда типов электродов структура наплавленного металла может быть как однофазной, так и двухфазной, для других — только двухфазной, но содержание второй фазы может изменяться в широких пределах. Это оказывает решающее влияние на склонность наплавленного металла к образованию горячих трещин, его жаропрочность, склонность к охрупчиванию при высоких температурах и т. д. Именно это обстоятельство привело к необходимости разработки марок электродов с переменными расчетными составами покрытий, обеспечивающими содержание ферритной фазы в наплавленном металле в заданных пределах в зависимости от исходного состава проволоки и материалов покрытия.
В связи с этим, для оценки химического состава и структуры высоколегированного металла (основного и наплавленного) в литературе часто пользуются отношением эквивалентного содержания хрома и никеля, которое называют хромоникелевым эквивалентом
.
В работе Закса И.А. «О структурной диаграмме Шеффлера и хромоникилевом эквиваленте» показано, что данное отношение не характеризует по диаграмме Шеффлера определенного структурного состояния металла, так как равные значения эквивалента могут отвечать различным структурным состояниям металла не только для разных типов электродов, но и в пределах одного типа.
, поэтому, все точки, лежащие на данной прямой, отвечают одинаковым значениям хромоникелевого эквивалента, но располагаются при этом в различных структурных областях, так как линии, разграничивающие структурные области, не параллельны линиям эквивалентов
и пересекаются с ними.
Значения хромоникелевых эквивалентов, которые для всех типов электродов, марок сварочных проволок и сталей будут одинаково характеризовать структурное соотношение фаз в металле, могут рассчитываться
по формуле
где и
— рассчитанное по химическому составу металла с учетом эквивалентных коэффициентов суммарное содержание феррито- и аустенитообразующих элементов, называемых соответственно эквивалентами хрома и никеля, которые могут быть вычислены по формулам:
— величина участка, отсекаемая на оси абсцисс диаграммы Шеффлера соответствующей линией от начала координат.
Соответственно хромоникелевый эквивалент для однофазной аустенитной стали , а для однофазной ферритной
.
Все промежуточные значения хромоникелевого эквивалента соответствуют двухфазному состоянию металла. Структурное состояние хромоникелевых аустенитных сталей может быть определено расчетом без нахождения координат точек по диаграмме Шеффлера.
Граничные условия существования металла с однофазной аустеннтной и двухфазной аустеннто-ферритной структурой, соответствующие феррита, выражаются линейной зависимостью
.
Если эквивалент хрома меньше расчетного содержания хрома
то сталь имеет однофазную аустенитную структуру, а если больше, то двухфазную аустенито-ферритную структуру, и количество феррита рассчитывается по формуле
.
Пример. Определить содержание феррита по диаграмме Шеффлера и расчетом при условии, что наплавленный металл имеет следующий химический состав (в вес. %):
1. Эквиваленты никеля и хрома по формулам составляют:
.
Рассчитанные координаты точки соответствуют на диаграмме аустенито-ферритной структуре металла с содержанием 17% феррита.
2. Расчетное содержание хрома по формуле составляет
,
т. е. эквивалент хрома, определенный по диаграмме, больше расчетного
, следовательно, наплавленный металл имеет двухфазную структуру и содержание феррита по формуле составляет
.
Полученные результаты по диаграмме (17%) и расчетом (~16%) достаточно близки и практически равноценны.
Однако, при наличии в наплавленном металле ферритообразующих элементов, являющихся одновременно сильными карбидообразователями, следует учитывать возможность образования стойких карбидов, так как это существенно изменяет величины эквивалентных значений никеля и хрома по сравнению с получаемыми расчетом по формулам без учета образующихся карбидов.
Пример. Определить содержание феррита в наплавленном металле по диаграмме Шеффлера без учета и с учетом образования карбидов, если наплавленный металл имеет следующий химический состав (в вес. %):
1. Эквивалентные значения хрома и никеля по формулам без учета образования карбидов ниобия составляют:
2. Рассчитанные координаты точки соответствуют по диаграмме Шеффлера аустенито-ферритной структуре наплавленного металла с содержанием феррита 6%.
3. При наличии в наплавленном металле ниобия будут образовываться карбиды со стехиометрическим отношением
.
4. Считая, что предел растворимости углерода в твердом растворе составляет 0,02%, определяем количество избыточного углерода, способного образовывать карбиды ниобия,
.
5. Полученное количество углерода способно израсходовать ниобия на образование карбидов
.
6. Количество свободного ферритообразующего ниобия составит
.
7. Эквивалентные значения хрома и никеля по формулам с учетом образования карбидов ниобия составляют:
8. Расчетные координаты точки соответствуют по диаграмме Шеффлера аустенито-ферритной структуре наплавленного металла с содержанием феррита 11%, т. е. почти в два раза больше первоначально рассчитанного количества.
Изложенные выводы сделаны без учета возможности попадания составов металла в области мартенситной или феррито-мартенситной структур, как это имеет место, например, для высокохромистого металла, наплавленного электродами типов ЭФ-Х13, ЭФ-Х11ВМНФ и др. Если рассчитанная с учетом эквивалентных коэффициентов сумма аустенитообразующих элементов ( ) для искомого состава отвечает неравенствам:
или
,
где — отрезки, отсекаемые линиями аустенито-мертенситной области на осях координат диаграммы Шеффлера, то, подставляя соответствующие значения
в неравенства, получим дополнительное условие к уравнению для двухфазной феррито-мартенситной структуры
.
Одна из проблем, возникающих при сварке аустенитных сталей, связана с появлением так называемых локальных разрушении при термической обработке сварных соединений, а также в процессе их эксплуатации при повышенных температурах.
Межкристаллические хрупкие разрушения сварных соединений в околошовной зоне на расстоянии одного или нескольких зерен от линии сплавления, названные локальными разрушениями, обнаруживаются главным образом в условиях длительной эксплуатации при температурах выше 565– 580 0С. Эти разрушения наблюдались также при термической обработке жестких сварных узлов из аустеничных сталей при медленном нагреве в интервале температур 600 – 800 0С.
Вероятными причинами возникновения локальных разрушений можно считать:
1. Снижение пластичности металла околошовной зоны при воздействии термодеформационного цикла сварки вследствие развития диффузионных процессов, приводящих к повышению концентрации поверхностно-активных элементов на границах зерен, а также выделении при длительном воздействии температур в интервале 600-8000С дисперсных карбидов внутри зерен, что приводит к их упрочнению. Дальнейшее развитие этих процессов (коагуляция интерметаллидов и карбидов) дополнительно снижает общую деформационную способность металла вблизи зоны сплавления. Стали, легированные сильными карбидообразующими элементами, обладают повышенной склонностью к локальным разрушениям.
2. Неоднородность механических свойств металла шва, околошовной зоны и основного металла, не подвергавшегося воздействию термического цикла сварки. При более высокой прочности металла шва вследствие наличия в нем ферритной или карбидной фазы, а также явления «самонаклепа» (при сварке многослойных швов) происходит концентрация деформаций в околошовной зоне, имеющей пониженную пластичность, что способствует образованию и развитию хрупких трещин.
3. Высокие остаточные сварочные напряжения, которые могут суммироваться с рабочими, компенсационными и другими напряжениями, возникающими при эксплуатации.
Для повышения стойкости против локальных разрушений сварных соединений из аустенитных сталей, подвергаемых термической обработке или предназначенных для работы при повышенных температурах, применяются следующие меры:
1. Используются стали, не содержащие титана, ниобия и других сильных карбидообразующих элементов (08Х18Н10, Х18Н9, 08Х18Н11 и др.), или стали, легированные молибденом (Х16Н9М2, Х16Н12М2 и др.), который распределяется преимущественно по границам зерен и упрочняет их. Легированные молибденом стали имеют достаточно высокую горячую пластичность и жаропрочность.
2. Слитки для изготовления поковок, труб и листов выплавляются с небольшим количество феррита (1—4%) в исходной литой структуре. При ковке, прокатке и последующей аустенитизации ферритная фаза растворяется и структура металла становится однофазной аустенитнои. При сварке в участках околошовной зоны, нагревающихся до температур устойчивого существования феррита (1300—1400° С), происходит его выделение и структура металла снова становится двухфазной, что повышает его стойкость против образования горячих трещин и локальных разрушений.
3. Для сварки пользуются электроды, обеспечивающие более пластичный металл шва. По аналогии с основным металлом предпочтительнее применять электроды, обеспечивающие наплавленный металл легированный молибденом
4. После сварки изделия подвергаются высокотемпературной термической обработке для снятия остаточных сварочных напряжений и гомогенизации (растворения феррита, карбидов и интерметаллидов).
Правильный выбор основного металла и электродов в сочетании с термической обработкой сварных соединений обеспечивает надлежащую их стойкость против локальных разрушений.
Пример. Необходимо выбрать электроды для сварки аустенитной стали ОХ18Н10 с перлитной сталью 10ХСНД, имеющих следующий химический состав (в %): 08Х18Н10 — ; 10ХСНД—
.
Толщина свариваемых листов 8 мм, соединение стыковое с V-образной разделкой кромок (60о), сварка выполняется в три слоя.
1. Определяем долю участия основного и наплавленного металлов в первом (корневом) слое шва.
При сварке первого слоя стыкового шва с углом разделки 60° доля участия основного металла составляет 45%. Вследствие различной теплопроводности свариваемых сталей, степень проплавления ( ) перлитной стали 10ХСНД составит примерно 40% и аустенитной ОХ18Н10 соответственно 60% от доли основного металла, т.е.:
доля стали 10ХСНД
08Х18Н10 .
наплавленного металла 100 — (18 + 27) = 55%.
2. Выбираем для сварки электроды марки (тип ЭА-1а), обеспечивающие наплавленный металл, близкий по составу к стали ОХ18Н10. Химический состав металла, наплавленного выбранными электродами, следующий (в %):
.
3. Вычисляем химический состав первого слоя металла шва:
,
где — соответственно содержание углерода или другого
определяемого элемента в металле шва, основном и наплавленном металлах; —доля участия основного металла в металле шва.
Тогда химический состав металла шва при сварке первого слоя будет (в %):
4. Вычисляем эквиваленты хрома и никеля по формулам:
Полученные результаты расчета наносим на диаграмму Шеффлера, из которой видно, что в структуре металла шва будет образовываться мартенсит, что может привести к образованию трещин.
Следовательно, выбранные электроды марки с указанным составом наплавленного металла непригодны для сварки сталей ОХ18Н10 и 10ХСНД.
5. Выбираем электроды, дающие наплавленный металл, с более высоким содержанием хрома и никеля – марки , который при перемешивании с расплавленной низколегированной сталью может обеспечить получение в шве двухфазной аустенитно-ферритной структуры, стойкой против образования трещин.
Выбранные электроды имеют следующий химический состав наплавленного металла (в %): :
7. Вычисляем эквиваленты хрома и никеля второго слоя металла шва (в %):
Полученные эквиваленты хрома и никеля соответствуют по диаграмме Шеффлера двухфазной аустенитно-ферритной структуре с содержанием 6 – 7% феррита.
Следовательно, выбранные электроды марки с указанным составом наплавленного металла пригодны для сварки первого слоя шва. Это может быть подтверждено также расчетом по формулам без структурной диаграммы Шеффлера.
Расчетное содержание хрома, отвечающее граничным условиям существования металла с однофазной и двухфазной аустеннто-ферритной структурой, составляет
Так как эквивалент хрома , т. е. больше расчетного
, то металл шва имеет двухфазную аустенито-ферритную структуру и количество феррита
.
Полученный результат достаточно близок и практически равноценен определенному по диаграмме Шеффлера,
8. Определяем долю участия основного и наплавленного металлов в последующих слоях шва.
Доля основного металла в формировании шва будет уменьшаться по мере увеличения количества его слоев и для последнего, третьего слоя будет составлять около 30%, следовательно:
доля стали 10ХСНД
08Х18Н10
наплавленного металла
9. Вычисляем химический состав третьего слоя шва (в %):
10. Вычисляем эквиваленты хрома и никеля третьего слоя металла шва (в %):
Полученные значения эквивалентен хрома и никеля соответствуют по диаграмме Шеффлера аустенитно-ферритиой структуре с содержанием феррита
т. е. практически совпадает с результатом, определенным по диаграмме Шеффлера.
Кроме возможности образования трещин в швах необходимо учитывать при выборе электродов для сварки разнородных сталей также возможность, образования хрупких кристаллизационных и диффузионных прослоек в зоне сплавления. Ширина этих прослоек в большой степени зависит от состава металла шва и в первую очередь от содержания в нем никеля.
Влияние содержания в шве никеля на ширину хрупких кристаллизационных прослоек вблизи зоны сплавления с перлитной сталью наглядно иллюстрируется схемой. Если условно принять, что мартенситная структура в зоне переходных кристаллизационных прослоек будет образовываться при содержании никеля менее 5—6%, то ширина этих прослоек будет тем меньше, чем больше содержание никеля в используемых для сварки электродах.
При применении электродов с никелевой основой (например, с покрытиями марок ЦТ-28, ЦТ-36, АНЖР-1, изготавливаемых на основе проволок Св-06Х15Н60М15, ЭП-705 и ЭП-606 соответственно), хрупкие кристаллизационные прослойки практически будут отсутствовать.
Следовательно, для уменьшения ширины хрупких кристаллизационных прослоек в зоне сплавления перлитной стали с аустенитным швом необходимо применять электроды с большим запасом аустенитности. При относительно постоянном содержании хрома в подавляющем большинстве применяемых марок электродов—в пределах 15—20%, запас аустеннтности наплавленного металла зависит, в основном от содержания никеля в электродах.
В зоне сплавления перлитных сталей с аустенитными наряду с образованием кристаллизационных прослоек создаются особо благоприятные для образования и развития диффузионных прослоек вследствие наличия резкой структурной, химической и механической неоднородности, а также различия теплофизических свойств перлитных и аустенитных сталей.
Снижение интенсивности развития диффузионных прослоек достигается, как указывалось выше, применением перлитных сталей, легированных карбидообразующими элементами, или путем наплавки на кромки нестабилизированной стали облицовочного переходного слоя электродами, обеспечивающими стабилизированный направленный металл.
Вместе с этим существенное влияние на развитие диффузионных прослоек в зоне сплавления перлитной стали с аустенитным швом оказывает химический состав металла шва и в первую очередь содержание в нем никеля.
С повышением содержания никеля в шве до 25% (электроды типа ЭА-ЗМ6) ширина обезуглероженной зоны стали 30 после длительных выдержек при температурах 600 и 700°С уменьшается примерно в два раза по сравнению с аустенитным содержащим до 10% никеля, а при содержании никеля в шве 60% (электроды марки ЦТ-28) уменьшение обезуглероженной зоны еще более значительно (примерно в три раза).
Аналогичные результаты получены и после кратковременных выдержек при 700° С.
Исследованиями Ю. Н. Готальского установлено, что количество никеля в металле аустенитного шва, необходимое для исключения диффузионных прослоек в зоне его сплавления с перлитной сталью, увеличивается с возрастанием температуры длительного нагрева сварного соединения.
При температурах эксплуатации до 350о С необходимое количество никеля обеспечивается даже при минимальном его содержании в аустенитном металле шва (8—10%). Поэтому в данном случае содержание никеля определяется только исходя из необходимости получения металла шва, стойкого против образования трещин, с учетом его разбавления перлитной сталью.
При температуре эксплуатации сварных соединений до 450о С металл шва должен содержать не менее 19% никеля, при 550оС—не менее 31% и выше 550° С—не менее 47%. Соответственно металл, наплавленный электродами, должен иметь более высокое содержание никеля, чтобы обеспечить необходимое количество никеля в шве с учетом его разбавления основным металлом.
Состав перлитных сталей и термическая обработка сварных соединений также оказывают влияние на свойства хрупких прослоек. Чем больше углерода в перлитной стали, тем выше твердость образующихся хрупких прослоек. Поэтому при сварке перлитных сталей, имеющих повышенное содержание углерода, с аустенитными сталями также рационально применение электродов, обеспечивающих наплавленный металл с более высоким содержанием никеля, так как это оказывает одновременно благоприятное влияние как на уменьшение образующихся кристаллизационных и диффузионных прослоек, так и на снижение их твердости и хрупкости.
Л.С.Лившицем предложена методика расчета необходимого количества легирующих карбидообразующих элементов в перлитной стали, чтобы при имеющемся в ней количестве углерода обеспечить равенство концентраций растворенного углерода в стали и в контактирующем с ней аустенитном металле шва.
Обеспечение этого условия исключает диффузию углерода в зоне сплавления при длительном тепловом воздействии. При температурах эксплуатации до 550о С для исключения появления диффузионных прослоек в зоне сплавления аустенитного шва, содержащего никеля до 35%, с неаустенитной свариваемой сталью необходимо, чтобы последняя содержала не более 0,15% углерода и сумма карбидообразующих элементов составляла не менее 2,5% .
В случае применения менее легированной стали необходимо, чтобы содержание никеля в шве было более 35%. При температурах эксплуатации выше 550° С содержание углерода в неаустенитной стали должно быть не более 0,15%, а сумма карбидообразующих элементов — не менее 5%. При отсутствии прямой возможности соблюдения этих рекомендаций в разнородном соединении следует использовать указанные выше переходные вставки или облицовочные наплавки на кромки неаустенитной стали.
ИНДИВИДУАЛЬНЫЕ ЗАДАНИЯ
1. Определить в соответствие с предложенным в таблице вариантом:
- структурное состояние свариваемых материалов и выбранного сварочного электрода по диаграмме Шеффлера;
- количество слоев и химический состав металла шва каждого слоя;
- структуру металла шва расчетным путем и по диаграмме Шеффлера, сравнить;
- сделать выводы о правильности выбора сварочных электродов, предложить технологические мероприятия по повышению качества швов при сварке выбранными материалами.
№ п/п | Марки свариваемых материалов | Толщина, мм | Угол разделки кромок стыкового соединения, град | Отметить особенности сварки заданных сталей |
1 | 10ХСНД с 08Х18Н10Т | 16 | Х-образная 60о | Сварные соединения из сталей перлитного класса |
2 | 10ХСНД с 45Г17Ю3Х | 8 | V-образная 60о | Сварные соединения из сталей ферритного класса |
3 | 10Г2С с Х17Н13М3Т | 20 | Х-образная 60о | Сварные соединения из сталей феррито-мартенситного класса |
4 | 08ГДНФЛ с 15ХМ | 6 | Без разделки | Сварные соединения из сталей мартенситного класса |
5 | 08Х18Н10 с45Г17Ю3 | 25 | Х-образная 60о | Сварные соединения из сталей перлитного класса |
6 | Х25Н6АТМФ с Х18Н9Т | 20 | Х-образная 60о | Сварные соединения из сталей аустенитного класса |
7 | 20ГЛ с Х13Н3 | 20 | К-образная 45о | Сварные соединения из сталей перлитного |
8 | 25ХГСА с 09Г2 | 10 | V-образная 60о | Сварные соединения из сталей ферритного и аустенитного класса |
9 | 08Х21Н6М2Т с 08Х22Н5Т | 8 | V-образная 60о | Сварные соединения из сталей перлит-ного |
10 | 08Х18Н10Т с 08Х18Н10Т | 16 | Х-образная 60о | Сварные соединения из низко и сред-нелегированных закаливающихся сталей |
11 | 10ХСНД с 15ХСНД | 14 | Х-образная 60о | Сварные соединения из сталей перлитного и аустенитного класса |
12 | 30ХГС с 25Х2Н4ВА | 10 | V-образная 60о | Сварные комбинированные соедине-ния из сталей аустенитного класса |
13 | 12Х2Н4А с 20Х | 16 | Х-образная 60о | Сварные соединения из сталей феррито-аустенитного класса |
14 | 20ХМЛ с 35ХМЛ | 25 | Х-образная 60о | Сварные соединения из сталей феррито-аустенитного класса |
15 | Ст.35 с Ст.45 | 10 | V-образная 60о | Сварные соединения из сталей феррито-мартенситного класса |
В особенностях сварки заданных сталей отразить следующие вопросы:
- оценка свариваемости сталей;
- особенности сварки сталей данного структурного класса;
- выбор сварочных материалов (электродов);
- особенности технологии и техники сварки.
СПИСОК ЛИТЕРАТУРЫ
1. Овчинников В.В., Гуреева М.А. Современные материалы для сварных конструкций. М. Издательский центр «Академия», 2013. -304 с.
2. Чернышол Г.Г. Технология электрической сварки плавлением. М. Издательский центр «Академия», 2006. -448 с.
3. Акулов А.И., Бельчук Г.А., Демянцевич В.П. Технология и оборудование сварки плавлением. М., «Машиностроение», 1977. - 432 с.
4. Закс И.А. Сварка разнородных сталей. Выбор электродов, режимов подогрева и отпуска. Справочное пособие. Л., «Машиностроение», 1973. - 208 с.
5. Петров Г.Л. Сварочные материалы. Л., «Машиностроение», 1972. - 280 с.
Уважаемые студенты!
В связи с распоряжением по дистанционному обучению, Вам придется делать эту работу в соответствии с данными методическими указаниями.
Литература, приведенная в списке под №№ 1 и 2, имеется в библиотеке колледжа. Её можно будет найти по интернету на сайте колледжа. Остальную литературу постарайтесь найти в интернете.
Со всеми вопросами обращаться по телефону 89115616670 или по электронному адресу: maii53@mail.ru
С уважением преподаватель Макаров Александр Иванович.
P.S. Учитывая, что работа большая, ее можно будет прислать ко мне на почту 18.04. 2020г. И не забывайте про контрольную работу. Так же присылайте на почту до 18.04.2020г.
Дата добавления: 2021-03-18; просмотров: 1739; Мы поможем в написании вашей работы! |
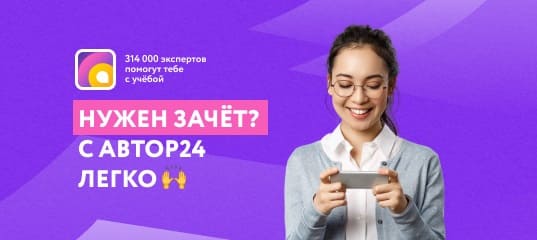
Мы поможем в написании ваших работ!