ПРИНЦИП ВЫБОРА СВАРОЧНЫХ МАТЕРИАЛОВ ДЛЯ ПОЛУЧЕНИЯ СВАРНЫХ СОЕДЕНЕНИЙ ИЗ СТАЛЕЙ ОДНОГО И РАЗНОРОДНЫХ СТРУКТУРНЫХ КЛАССОВ
Методические указания
Для выполнения Практической работы №5
«Определение ферритной фазы в металле шва при сварке разнородных сталей»
Содержание
Общие принципы выбора сварочных материалов……………………………………….…3 |
Классификация сталей и их сочетания в разнородных сварных соединениях…………...4 Принцип выбора сварочных материалов для получения сварных соединений из сталей одного и разнородных структурных классов……………………………………………….7 |
Диаграмма Шеффлера…………………………………………………………………….....11 |
Индивидуальные задания………….…....…………………………………………………...22 |
Список литературы……………...…………………………………………………………...23 |
ОБЩИЕ ПРИНЦИПЫ ВЫБОРА СВАРОЧНЫХ МАТЕРИАЛОВ
Общие принципы выбора сварочных материалов характеризуются следующими основными условиями:
1) обеспечение требуемой эксплуатационной прочности сварного соединения, т.е. определенного комплекса и уровня механических свойств металла шва в сочетании с основным металлом;
2) обеспечение необходимой сплошности металла шва (без пор и шлаковых включений или с минимальными размерами и количеством указанных дефектов на единицу длины шва);
3) отсутствие горячих и холодных трещин, т.е. получение металла с достаточной технологической прочностью;
4) получение комплекса специальных свойств металла шва (жаропрочности, жаростойкости, коррозионной стойкости и т.д.). Это условие необходимо соблюдать только при сварке легированных сталей специального назначения и при наплавке слоев с особыми свойствами;
|
|
5) обеспечение необходимой технологичности электродов, т. е. их пригодности для сварки в различных пространственных положениях, универсальности по роду применяемого тока, производительности, характеризуемой коэффициентами наплавки и расплавления, и т. д.
Эти показатели определяются для каждой марки электродов опытным путем и легко могут быть установлены по справочным материалам.
Рациональный выбор сочетаний различных марок сталей и сварочных материалов при проектировании сварных конструкций является сложной инженерной задачей, при решении которой необходимо учитывать кроме состава и свойств материалов также технико-экономические, технологические, эксплуатационные и другие факторы.
Назначение электродов для сварки разнородных соединений производится в зависимости от вида конструкций, условий и ресурса их эксплуатации, технических возможностей производства и т. д.
При выборе для сварных конструкций сталей и сварочных материалов разных структурных классов следует учитывать возможность существенного развития в сварных соединениях структурной, химической и механической неоднородностей, а также наличия поля остаточных сварочных напряжений, которые при различии коэффициентов линейного расширения не могут быть сняты термической обработкой. Эти факторы могут значительно снижать работоспособность и надежность разнородных сварных конструкций.
|
|
Строго говоря, не существует совершенно однородных сварных и наплавленных соединений, так как между швом и основным металлом (или наплавленным металлом и подложкой) всегда имеется какая-то неоднородность: химическая, структурная, механическая и т. д. Однако в технике и в литературе принято называть разнородными или комбинированными сварные соединения, в которых имеются стали различных структурных классов или одного структурного класса, но с различным легированием (разных марок), а также биметаллические соединения.
Укрупненно разнородные сварные соединения можно разделить на пять основных групп:
1)соединения из сталей разных структурных классов;
2)из сталей одного структурного класса различного легирования (разных марок);
3) из сталей одного структурного класса со швом другого структурного класса;
|
|
4) из биметаллов;
5) комбинированные сочетания из перечисленных выше четырех групп.
КЛАССИФИКАЦИЯ СТАЛЕЙ И ИХ СОЧЕТАНИЯ В РАЗНОРОДНЫХ СВАРНЫХ СОЕДИНЕНИЯХ
Номенклатура марок сталей, применяемых в настоящее время в различных отраслях промышленности для изготовления сварных конструкций, исключительно широка, а все возможные сочетания из их разнородных соединений практически трудно перечислить. Поэтому для упрощения задачи выбраны наиболее распространенные (преимущественно стандартизированные) марки сталей, которые разделены исходя из структурного состояния на три основных класса:
1) перлитные (углеродистые и низколегированные);
2) ферритные и феррито-мартенситные (высокохромистые);
3) аустенитные и феррито-аустенитные (хромоникелевые).
Каждый класс разделен, в свою очередь, на группы, в которые включены стали с относительно близкими свойствами, свариваемостью и служебными характеристиками (табл. 1).
Разделение высоколегированных сталей на группы (кислотостойкие, жаростойкие, жаропрочные) произведено в соответствии с их основными служебными свойствами и в некоторой степени условно, так как кислотостойкие стали одновременно являются жаростойкими до определенных температур, а жаростойкие являются также коррозионностойкими в определенных средах и т. д.
|
|
Не перечисленные в табл. 1 стали по аналогии структурного состояния и свойств могут быть отнесены к одной из групп соответствующего класса, а следовательно, приведенные рекомендации по выбору электродов, температуры подогрева и отпуска сварных разнородных соединений могут быть также использованы и для других конкретных сочетаний сталей, не перечисленных в приведенных далее таблицах.
Стали, перечисленные в таблице 1, можно комбинировать в сварных соединениях в следующих сочетаниях:
1)перлитные с перлитными (углеродистыми и низколегированными);
2)ферритные и феррито-мартенситные с ферритными и феррито-мартенситными (высокохромистыми);
3)аустенитные и феррито-аустенитные с аустенитными и феррито-аустенитными (хромоникелевыми);
4)перлитные (углеродистые и низколегированные) с ферритными и феррито-мартенситными (высокохромистыми);
5)перлитные (углеродистые и низколегированные) с аустенитными и феррито-аустенитными (хромоникелевыми);
6)ферритные и феррито-мартенситные (высокохромистые) с аустенитными и феррито-аустенитными (хромоникелевыми).
Таблица 1
Классификация сталей
Класс | Группа | Марка | Стандарт или технические условия |
1 | 2 | 3 | 4 |
Перлитные
| I
| Малоуглеродистые Ст.0, Ст.1, Ст.2, Ст.З, Ст.4, БСт.О, БСт.1, БСт.2, БСт.З, БСт.4 ВСт.2, ВСт.З, ВСт.4 | ГОСТ 380— |
08, 10, 15, 20, 25 | ГОСТ 1050— | ||
15Л, 20 Л, 25 Л | ГОСТ 977— | ||
12К, 15К, 16К, 18К, 20К | ГОСТ 5520— | ||
II | Среднеуглеродистые инизко легированные Ст.ЗГ, БСт.ЗГ, ВСт.ЗГ Ст.5, БСт.5, ВСт.5 Ст.5Г, БСт.БГ, ВСт.5Г | ГОСТ 380— | |
15Г, 20 Г, 25Г, 30 Г, 30 | ГОСТ 1050— | ||
14Г, 19Г, 09Г2, 14Г2, 18Г2, 12ГС, 16ГС, 17ГС, 09Г2С, 10Г2С1, 18Г2С, 25Г2С, 10ХСНД, 15ХСНД, 14ХГС, 15ГФ | ГОСТ 5058— | ||
15Х, 15ХА, 20Х, ЗОХ, 10Г2, 18ХГ, 18ХПУ16ХСН, 15ХФ, 20ХФ, 20ХН, 15НМ, 20НМ, 13Н2ХА, 12ХН2, 12ХНЗА, 20ХНЗА, 12Х2Н4А, 20Х2Н4А, 15ХГНТ,ЛГ53ГГНТА, 18ХГН, 20ХГСА, 15Х2ГН2Т, 15Х2ГН2ТА, 20ХН4ФА, 18Х2Н4ВА | ГОСТ 4543— | ||
ЗОЛ | ГОСТ 977— | ||
20ГЛ, 27ГЛ, 20ГСЛ, З0ГСЛ, 08ГДНФЛ, 13ХНДФТЛ, 12ДН2ФЛ | ГОСТ 7832— | ||
22К | ТУ 24-10-002—70 | ||
III | Низколегированные специальные АК25, АК27, АК28, АЛ5 | ТУ | |
IV | Среднеуглеродистые и низколегированные повышенной прочности Ст.6, БСт.6 | ГОСТ 380— | |
35, 40, 45, 50, 55, 35Г, 40Г, 45Г, 50Г | ГОСТ 1050— | ||
35ГС | ГОСТ 5058— | ||
35Х, 38ХА, 40Х, 45Х, 50Х, 35Г2, 40Г2, 45Г2, 50Г2, ЗОХГТ, 40ХГ, 35ХГ2, ЗЗХС, 38ХС, 40ХС, 27СГ, 35СГ, 36Г2С, 38ХВА, 40ХФА, З0ХНЗА, 40ХН, 45ХН, 50ХН, 25ХГСА, З0ХГС, З0ХГСА, 35ХГСА, 25Х2ГНТА, З0ХГСНА, З0ХГНА, 38ХГН, ЗОХ2ГН2, З0ХНВА, 38ХНВА, 40ХНВА, 40ХНМА, З0Х2НВА, 38ХЗНВА, 25Х2Н4ВА, ЗОХН2ВФА, 38ХЮ, З0Х2НВФА, 38ХНЗМФА, 38ХНЗВА, 38ХНЗВФА | ГОСТ 4543— | ||
1 | 2 | 3 | 4 |
Перлитные |
IV | 35Л, 40Л, 45Л, 50Л, 55Л | ГОСТ 977— |
35ГЛ, 40ГЛ, 32Х06Л, 35ХГСЛ, 40ХЛ, 35НГМЛ, 40ГФЛ, 12ДХН1МФЛ, ЗОХНМЛ, 40ХНЛ, 40ХНТЛ | ГОСТ 7832— | ||
V | Теплоустойчивые хромомолибденовые 15ХМ, З0ХМ, З0ХМА, 35ХМ, 38ХМА, 38ХМЮА | ГОСТ 4543- | |
12МХ | ГОСТ 10500— | ||
20ХМЛ, 35ХМЛ | ГОСТ 7832— | ||
20ХМУ, 25ХМ | ТУ ЛКЗ— 57/50 | ||
VI | Теплоустойчивые хромомолибдено-ванадиевые и хромомолибдено-вольфрамовые 12Х1МФ, 25Х1МФ, 25Х2М1Ф, 20ХЗМВФ (ЭИ415) 18ХЗМФ, 25Х1М1Ф | ГОСТ 10500—63 | |
15Х1М1Ф | МРТУ 14-4-21—67 | ||
15Х1М1ФЛ | МВН 632—63 | ||
20ХМФЛ, 25Х2МФЛ | ТУМТЭ и ТМ 2—67 | ||
Ферритные и феррито-мартенситные | VII | Высокохромистые нержавеющие 08X13, Х14, 12X13, 2X13, 3X13, 1Х13НЗ | ГОСТ 5632— |
10Х13Л, 20Х13Л, 5Х14НДЛ | ГОСТ 2176— | ||
VIII | Высокохромистые кислотостойкие и жаростойкие 08Х17, 08Х17Т, 08Х25Т, 08Х28, 14Х17Н2 | ГОСТ 5632— | |
14Х17Н | ЧМТУ 1-794— | ||
15Х25ТЛ, 10Х16Н4Б, 10Х17НЗСЛ | ГОСТ 2176— | ||
IX | Высокохромистые жаропрочные •15Х11МФ, 18Х12ВНМФ, 18Х12В2МФ, 18Х12ВМБФР | ГОСТ 5632—61 | |
15Х11МФБЛ, ХИЛА | ТУ 49-2004- 59ЛМЗ | ||
Аустенитные и феррито-аустенитные | X | Аустенитные кислотостойкие 08Х18Н10, 08Х18Н10, 08Х18Н9, 2Х18Н9, 08Х18Н10Е, 08Х18Н10Т, 08Х18Н10Т, 08Х18Н9Т, 08Х18Н11, 08Х18Н12Т, 08Х18Н12Б, 08Х17Н13М2Т, 08Х17Н13МЗТ, 08Х17Н16МЗТ, 08Х10Н20Т2 | |
5Х18Н9Л, 10Х18Н9Л, 10Х18Н9ТЛ, 5Х18Н11БЛ, 10Х18Н12МЗТЛ | |||
XI | Аустенитные кислотостойкие повышенной прочности 08Х18Н12ТФ (ЭИ953), 08Х20Н12АБФ | ЧМТУ 1-794—69 | |
08Х18Н22В2Т2 (48АН-1) | ВТУ 590—59 | ||
XII | Аустенитные жаростойкие 08Х23Н18, Х23Н18, Х23Н13, 08Х20Н14С2, 08Х20Н14С2, 08Х25Н20С2, 4Х18Н25С2 | ГОСТ 5632—61 | |
15Х23Н18Л, 15Х25Н19С2Л, З0Х24Н12СЛ, 25Х23Н7СЛ | ГОСТ 2176— 67 | ||
XIII XIII | Аустенитные жаропрочные 1Х14Н16Б, 1Х14Н16БР, 1Х14Н18В2Б, 1Х14Н18В2БР, 4Х14Н14В2М, 1Х16Н13М2Б, Х16Н15МЗБ, ЗХ19Н9МВБТ, ХН35ВТ (ЭИ612), ХН35ВТР, ХН35ВМТ (ЭИ692) | ГОСТ 5632— | |
1 | 2 | 3 | 4 |
Аустенитные и феррито-аустенитные |
XIII
| Х15Н25М6 (ЭИ395) | МПТУ 2362— |
15Х18Н22В6М2Л, 20Х21Н46В8Л | ГОСТ 2176— | ||
XIV | Феррито-аустенитные высокопрочные и кислотостойкие 08Х22Н5Т, 1Х21Н5Т, ОХ21Н6М2Т, Х28АН | ГОСТ 5632— | |
Х25Н6АТМФ (ЭИ954) | ЧМТУ 1-794— | ||
10Х25Н5ТМФЛ | ГОСТ 2176— |
ПРИНЦИП ВЫБОРА СВАРОЧНЫХ МАТЕРИАЛОВ ДЛЯ ПОЛУЧЕНИЯ СВАРНЫХ СОЕДЕНЕНИЙ ИЗ СТАЛЕЙ ОДНОГО И РАЗНОРОДНЫХ СТРУКТУРНЫХ КЛАССОВ
При сварке комбинированных соединений из сталей одного структурного класса, но разного легирования (разных марок), предпочтительнее использование однородных по структурному классу сварочных материалов, при этом режимы предварительного подогрева, сварки и отпуска выбираются исходя из общих положений для сварки сталей данного класса с учетом свариваемости наиболее легированной и, как правило, хуже сваривающейся стали, входящей в данное соединение.
До настоящего времени не существует единого общепризнанного определения понятия свариваемости металлов и сплавов, исчерпывающего всю сложность этой характеристики, а также универсальной методики ее оценки.
Предлагаются понятия физической, металлургической, технологической и других видов свариваемости, а в литературе опубликовано и в практике используются свыше 150 способов ее оценки. Это обусловлено тем, что сварка сопровождается химическими и физическими процессами, происходящими в металлах соединения, которые изменяют исходное состояние свариваемых металлов, создавая различную степень местной неоднородности химического состава, фазового состояния, кристаллической структуры, механических, химических и физических свойств, а также поля напряжений, что определяет различную работоспособность и надежность сварных соединений.
Общее понятие свариваемости должно учитывать комплексно все эти явления и процессы, а универсальная методика ее оценки — характеризовать их в совокупности, что практически не представляется возможным. Поэтому испытания по оценке свариваемости металлов и сплавов производят по различным методикам, каждая из которых выявляет одну или несколько характеристик свариваемости, имеющих первостепенное значение в каждом конкретном случае.
Под физической свариваемостью понимается совокупность таких свойств металлов и сплавов, как способность их к.взаимной растворимости и диффузии в твердом и жидком состояниях, совместной кристаллизации расплавленных основного и присадочного металлов и т. д. Однако эти свойства еще не определяют полностью возможности получения сварных соединений, удовлетворяющих во всех случаях требованиям эксплуатационной надежности и долговечности сварных конструкций.
Поэтому предлагается понятие технологической свариваемости как комплексной характеристики металла, отражающей его реакцию на процесс сварки и определяющей его относительную техническую пригодность для выполнения заданных сварных соединений, удовлетворяющих условиям последующей их эксплуатации.
При сварке разнородных металлов следует учитывать свариваемость каждого из них в данном сочетании.
Чем меньше количество применимых к данному металлу способов сварки и уже для каждого способа сварки пределы оптимальных режимов, обеспечивающих возможность получения сварных соединений требуемого качества, тем хуже его технологическая свариваемость. Важнейшим фактором, влияющим на свариваемость стали, является ее химический состав, который в значительной мере определяет реакцию стали в околошовной зоне на термодеформационный цикл сварки.
Кроме химического состава на свариваемость стали оказывает влияние большое количество металлургических, технологических и других факторов: ликвация вредных примесей, в первую очередь серы и фосфора, засоренность газами и неметаллическими включениями, склонность к росту зерен при перегреве, чувствительность к концентраторам напряжений, склонность к термическому старению, образованию холодных и горячих трещин, переходная температура хрупкости (порог хладноломкости) и т.д. Если к этому добавить, что свариваемость также зависит от толщины металла, жесткости конструкции и т. п., то становится очевидным, что эта сложная металлургическая и технологическая характеристика металла не может оцениваться только по его химическому составу.
Из этого, однако, не следует, что влияние каждого фактора равноценно.
Превалирующая роль химического состава стали по влиянию на свариваемость очевидна, и в первом приближении она всегда оценивается по этой характеристике.
Упрощенно и приблизительно химический состав металла шва можно рассчитать по следующей формуле
[Х]мш = Y[Х]ом + (1 - Y)[Х]нм
где Y - доля участия основного металла в металле шва;
(1 - Y) - доля участия наплавленного металла (электродного, проволоки, присадки) в металле шва;
[Х]мш – концентрация элемента Х в металле шва;
[Х]ом – концентрация элемента Х в основном металле;
[Х]нм - концентрация элемента Х в наплавленном металле, получаемая как результат взаимодействия электродного стержня (проволоки, присадки) покрытия и изменений состава металла, вызываемых процессом сварки
Допустимая доля участия в шве проплавленного основного металла зависит от сочетания свариваемых сталей и состава используемых сварочных материалов, а так же от разделки кромок и слоя шва. Приближенно долю участия основного металла в формировании шва можно оценить по данным таблицы 2.
Металл шва сварного соединения, выполненного из сталей разных структурных классов, всегда отличается по составу и структуре хотя бы от одной из сваренных сталей, и гетерогенность сварного соединения существенно влияет на его технологическую и эксплуатационную прочность.
При сварке сталей разных структурных классов необходимо всегда выбирать режимы сварки, обеспечивающие минимальное проплавление и перемешивание основного металла с наплавленным металлом.
Степень проплавления одной из кромок относительно другой (К) в разнородном соединении зависит от теплопроводности свариваемых металлов. Например, проплавление аустенитных сталей на 30—40% больше, чем перлитных и ферритных (при одинаковых режимах сварки), поэтому для аустенитных сталей К≈0,6. Химический состав металла шва в значительной мере определяет и его структуру. Пример практического использования коэффициента К при расчете состава металла шва приведен ниже.
Таблица 2
Дата добавления: 2021-03-18; просмотров: 483; Мы поможем в написании вашей работы! |
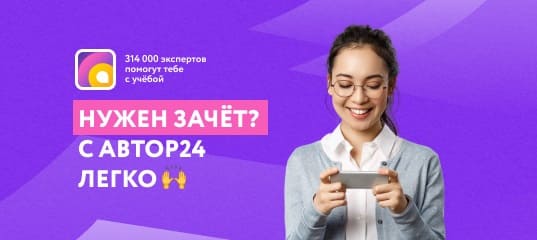
Мы поможем в написании ваших работ!