Углеродистые и легированные стали специального назначения
Рессорно-пружинная сталь. Рессорно-пружинная сталь (ГОСТ 14959—79*) выпускается в виде горячекатаного проката или кованой (диаметром или толщиной до 250 мм), а также в виде калиброванных прутков круглого, квадратного и профильного сечений, мотков и полос со специальной отделкой поверхности.
Рессорно-пружинная сталь выпускается качественной и высококачественной, а также углеродистой (65, 70, 80, 85, 60Г, 65Г, 70Г) и легированной (55С2, 55С2А, 60С2, 70С3А, 60С2Г, 50ХГ, 50ХГА и др.).
Цифры в маркировке углеродистых сталей указывают среднюю массовую долю углерода в сотых долях процента; буква Г, стоящая справа после цифры, — повышенное содержание марганца (0,7 … 1,2 %). В обозначении легированных сталей цифры, стоящие впереди марки, указывают массовую долю углерода в сотых долях процента.
Для примера рассмотрим химический состав стали марки 60С2Н2А. Массовая доля углерода составляет 0,56 … 0,64 %, кремния — 2 %, никеля — 2 %. Буква А, стоящая в конце марки, указывает, что сталь высококачественная, т. е. имеет пониженную массовую долю вредных примесей — серы и фосфора (их суммарная массовая доля составляет 0,05 %).
Рессорно-пружинные стали поставляются по строго заданным нормируемым характеристикам. Нормируемыми характеристиками являются химический состав, механические свойства и назначение.
По нормируемым характеристикам эти стали подразделяются на категории: 1, 1A, 1Б, 2, 2А, 2Б, 3, 3А, 3В, 3Г, 4, 4А, 4Б.
|
|
Сталь категорий 1, 1A, 1Б, 4, 4А и 4Б в зависимости от вида последующей обработки подразделяется на подгруппы:
- а — для горячей обработки (ковка, штамповка);
- б — для холодной механической обработки (строгание, точение, фрезерование);
- в — для холодного волочения (подкат).
Рессорно-пружинные стали обладают высокими механическими свойствами как в сыром, так и в термически обработанном состоянии. Углеродистые и марганцовистые стали имеют пределы прочности при растяжении σв = 1 000 … 1 130 МПа (100 … 115 кгс/мм2), относительное удлинение δ = 7 … 9 %, твердость 230 … 250 НВ. Кремнистые, кремнисто-хромистые и кремнистоникелевые стали имеют более высокие механические свойства по сравнению с углеродистыми и марганцовистыми сталями. Например, сталь марки 60С2Н2А имеет предел прочности при растяжении σв = 1 500 МПа (150 кгс/мм2), твердость 420 … 475 НВ, относительное удлинение δ = 19 %.
Рессорно-пружинная сталь обладает высокой ковкостью, ограниченной свариваемостью, высокой прокаливаемостью и отсутствием отпускной хрупкости.
В нормативно-технической документации и на чертежах рессорно-пружинная сталь обозначается следующим образом:
что означает — сталь горячекатаная, круглая, диаметром 100 мм, обычной точности прокатки по ГОСТ 2590—2006 марки 65Г, для горячей обработки подгруппы а, категории 4А.
|
|
Аналогично обозначаются и другие виды проката этих сталей.
Из рессорно-пружинной стали изготавливают рессоры, пружины общего назначения, пружины клапанов автомобилей, амортизаторов, замковые шайбы, диски сцепления, эксцентрики, бандажи, тормозные барабаны и ленты, фрикционные диски, шайбы пружинные, торционные валы и другие детали, от которых требуется высокая упругость и износостойкость, в том числе тяжело нагруженные пружины и рессоры для большегрузных автомобилей, тракторов и железнодорожных вагонов.
Подшипниковая сталь. По ГОСТ 801—78 предусматривается выпуск подшипниковой стали горячекатаной, катаной, калиброванной и со специальной отделкой поверхности в виде круга, полосы, квадрата, труб, ленты, проволоки (ШХ4, ШХ6, ШХ9, ШХ15, ШХ15СГ).
В маркировке этих сталей приняты следующие обозначения:
- буквы ШХ — подшипниковая хромистая;
- буквы С, Г — легирующие элементы (кремний и марганец);
- цифры показывают количество хрома в десятых долях процента.
В маркировке отдельных сталей указывается способ выплавки:
- буквой Ш обозначают электрошлаковый переплав;
- буквой В — вакуумирование;
- буквой Д — двойная очистка (например, ШХ9-Ш; ШХ15-ШВ; ШХ15-ШД).
Подшипниковая сталь в зависимости от дальнейшей обработки подразделяется на следующие группы:
|
|
- для горячей обработки давлением (штамповка, ковка);
- для холодной высадки;
- для холодной штамповки.
Подшипниковые стали имеют высокие механические свойства (особенно после закалки): твердость, прочность, ударную вязкость, износостойкость и теплостойкость.
Например, сталь марки ШХ15СГ в состоянии поставки имеет следующие свойства:
- предел прочности при растяжении σв = 590 … 730 МПа (60 … 73 кгс/мм2),
- твердость 179 … 217 НВ, ударную вязкость 44 Дж/см2;
- после закалки при температуре 810 … 840 °С,
- охлаждения в масле и последующего отпуска при температуре 150 °С — твердость 61 … 65 НRC,
- предел прочности при растяжении σв = 1 960 … 2 300 МПа (196 … 230 кгс/мм2).
Подшипниковая сталь имеет высокие технологические свойства: ковкость, обрабатываемость резанием, шлифуемость, прокаливаемость и низкую склонность к отпускной хрупкости; свариваемость ограниченная. Из этой стали изготавливают шарики, ролики, кольца, втулки, плунжеры, нагнетательные клапаны, корпуса распылителей и другие детали, от которых требуется высокая твердость, износостойкость и контактная прочность.
|
|
Подшипниковая сталь, легированная кремнием и марганцем, идет на изготовление подшипников, работающих при повышенных температурах.
Конструкционная сталь повышенной и высокой обрабатываемости резанием (автоматная). По ГОСТ 1414—75 выпускают следующие группы конструкционных сталей повышенной и высокой обрабатываемости резанием:
- углеродистая сернистая (А11, А12, А20, А30, А35);
- сернисто-марганцевая (А40Г);
- сернисто-марганцевая свинецсодержащая (АС35Г, АС45Г2, А35Е, А45Е);
- легированная свинецсодержащая (А12ХМ, АС14ХГН, АС19ХГН, АС20ХГНМ, АС30ХМ, АС38ХГНМ, АС40ХГНМ) и другие группы.
В маркировке этой группы сталей приняты следующие обозначения:
- буква А — сталь автоматная;
- АС — автоматная свинецсодержащая;
- буква Е указывает на наличие в стали селена.
Цифры, стоящие после букв, указывают на массовую долю свинца. Остальные условные обозначения такие же, как у легированных конструкционных сталей.
Сталь конструкционная повышенной и высокой обрабатываемости резанием выпускается в виде горячекатаного круглого, квадратного и шестигранного, катаного и калиброванного проката, как термически обработанного (Т), так и без термической обработки, а также нагартованного (Н). В зависимости от назначения эта сталь подразделяется на группы:
- а — для горячей обработки давлением;
- б — для холодной механической обработки;
- в — для холодного волочения (подкат).
В зависимости от химического состава конструкционная сталь повышенной и высокой обрабатываемости резанием имеет следующие пределы механических свойств: предел прочности при растяжении σв = 580 … 800 МПа (58 … 80 кгс/мм2) (для некоторых марок стали σв = 1 000 … 1 200 МПа); твердость по Бринеллю 187 … 241 НВ; относительное удлинение δ = 8 … 12 % (для некоторых марок стали σ = 20 %).
Автоматные стали обладают высокими технологическими свойствами: ковкостью, свариваемостью и особенно обрабатываемостью резанием. Последнее свойство достигается путем специальных металлургических процессов, предусматривающих введение в конструкционную сталь серы, свинца и селена. Эти добавки в процессе обработки резанием создают как бы внутреннюю смазку, которая снижает трение в месте контакта резца с заготовкой, при этом процесс резания идет мягко, создаются условия измельчения стружки. Вредное влияние серы в этих сталях нейтрализуется повышенным содержанием марганца.
Конструкционные стали повышенной и высокой обрабатываемости резанием обладают повышенными вязкостью, пластичностью и усталостью, поэтому имеют ограниченное применение.
Углеродистые сернистые стали используют для крепежных малонагруженных деталей, к которым предъявляются требования высокой точности и шероховатости поверхности. Другие группы автоматных сталей используют для деталей, работающих при более высоких напряжениях и нагрузках. Например, стали марок А12, А20, А30 и А40Г идут на изготовление осей, валиков, зубчатых колес, шестерен, пальцев, винтов, болтов, втулок, колец, ходовых винтов и других деталей сложной формы, получаемых на станках-автоматах и требующих высокого качества поверхности. Первые две из указанных марок подвергаются цементации, а последующие марки улучшаются закалкой и отпуском.
Сталь для отливок. В зависимости от назначения, механических свойств и химического состава отливки подразделяются на три группы:
- общего назначения;
- ответственного назначения;
- особо ответственного назначения.
Отливки изготовляются из сталей следующих марок (ГОСТ 977—88): 15Л, 20Л, 30Л, 35Л, 40Л, 50, 55Л, 20ГЛ, 20Г1ФЛ, 10ФЛ, 30ХГСФЛ, 45ФЛ, 32Х06Л, 40ХЛ, 35ХМЛ, 35ХГСЛ, 35ХГМЛ, 20ДХЛ, 20ХГСНДМЛ, 08ГДНФЛ, 13ХНДФТЛ, 12ДН2ФЛ, 12ДН1МФЛ, 23ХГС2МФЛ, 25Х2Г2ФЛ.
Принцип маркировки литейных сталей аналогичен маркировке углеродистых и легированных качественных конструкционных сталей, но в конце маркировки ставится буква Л (сталь литейная).
В нормативно-технической документации и на чертежах литейные стали обозначаются следующим образом: отливка 12ДХН1МФЛГОСТ 977—88, что означает: отливка из стали марки 12ДХН1МФЛ группы особо качественного назначения, ГОСТ 977—88.
Аналогично обозначаются и другие марки сталей. Химический состав сталей обусловлен соответствующими марками. Механические и технологические свойства отливок зависят от выбранных для этих целей марок сталей.
Сталь низколегированная строительная. По ГОСТ 19281—89* выпускается низколегированная строительная сталь следующих групп и марок:
- марганцевая — 14Г2, 0912;
- марганцовистая с медью — 09Г2Д;
- кремнемарганцовистая — 12ГС, 16ГС, 17ГС, 17Г1С, 09Г2С, 10Г2С1;
- кремнемарганцовистая с медью — 09Г2СД, 10Г2С1Д;
- марганцевованадиевая — 15ГФ, 15Г2СФ;
- марганцевованадиевая с медью — 157ГФД, 15Г2СФД;
- марганцевованадиевая с азотом — 14Г2АФ, 16Г2АФ, 18Г2АФ;
- марганцевованадиевая с азотом и медью — 14Г2АФД, 16Г2АФД, 15Г2АФДжс, 18Г2АФДпс;
- марганцевониобиевая — 10Г2Б, 12Г2Б.
В маркировке низколегированных строительных сталей принят тот же принцип, что и для легированных конструкционных сталей.
Сталь низколегированная выпускается в виде толстолистового и широколистового проката в рулонах, лентах и листах, применяемых для сварных строительных конструкций (в машиностроении — для несварных конструкций) без термообработки: трубопроводов, емкостей для хранения и транспортировки жидкостей и т. д.
Предел прочности этой стали σв = 440 … 600 МПа, относительное удлинение δ = 20 … 23 %, ударная вязкость составляет 30 … 44 Дж/см2.
В нормативно-технической документации принято следующее обозначение:
что означает: сталь широкополосная универсальная, толщиной 40 мм, шириной 500 мм (ГОСТ 82—70*), с ребровой кривизной по классу А, марки 10Г2С1 (ГОСТ 19281—89*), категории 5.
Низколегированная строительная сталь применяется для изготовления ферм, обвязки вагонов, элементов сварных строительных конструкций, листовых конструкций, днищ сосудов, а также арматуры железобетонных изделий. В зависимости от химического состава марок сталей строительные конструкции могут работать при температуре 40 … 70 °С, а из отдельных марок — при отрицательных температурах и под давлением.
Цветные металлы.
ЦВЕТНЫЕ МЕТАЛЛЫ И СПЛАВЫ: КЛАССИФИКАЦИЯ, АССОРТИМЕНТ И СВОЙСТВА.
К цветным металлам относятся все металлы, кроме железа и сплавов на его основе – сталей и чугунов, которые называются черными. Сплавы на основе цветных металлов используют в основном как конструкционные материалы со специальными свойствами: коррозионно-стойкие, подшипниковые (обладающие низким коэффициентом трения), тепло- и жаропрочные и др.
В маркировке цветных металлов и сплавов на их основе нет единой системы. Во всех случаях принята буквенно-цифровая система. Буквы указывают на принадлежность сплавов к определенной группе, а цифры в разных группах материалов имеют разное значение. В одном случае они указывают на степень чистоты металла (для чистых металлов), в другом – на количество легирующих элементов, а в третьем обозначают номер сплава, которому по гос. стандарту должны соответствовать определенный состав или свойства.
Медь и ее сплавы
Техническая медь маркируется буквой М, после которой идут цифры, связанные с количеством примесей (показывают степень чистоты материала). Медь марки М3 содержит примесей больше, чем М000. Буквы в конце марки означают: к – катодная, б – безкислородная, р – раскисленная. Высокая электропроводность меди обуславливает ее преимущественное применение в электротехнике как проводникового материала. Медь хорошо деформируется, хорошо сваривается и паяется. Ее недостатком является плохая обрабатываемость резанием.
К основным сплавам на основе меди относятся латуни и бронзы. В сплавах на основе меди принята буквенно-цифровая система, характеризующая химический состав сплава. Легирующие элементы обозначаются русской буквой, соответствующей начальной букве названия элемента. Причем часто эти буквы не совпадают с обозначением тех же легирующих элементов при маркировке стали. Алюминий – А; Кремний – К; Марганец – Мц; Медь – М; Никель – Н; Титан –Т; Фосфор – Ф; Хром –Х; Бериллий – Б; Железо – Ж; Магний – Мг; Олово – О; Свинец – С; Цинк - Ц.
Порядок маркировки литейных и деформируемых латуней разный.
Латунь - сплав меди с цинком (Zn от 5 до 45%). Латунь с содержанием от 5 до 20% цинка называется красной (томпаком), с содержанием 20–36% Zn – желтой. На практике редко используют латуни, в которых концентрация цинка превышает 45%. Обычно латуни делят на:
- двухкомпонентные латуни или простые, состоящие только из меди, цинка и, в незначительных количествах, примесей;
-многокомпонентные латуни или специальные – кроме меди и цинка присутствуют дополнительные легирующие элементы.
Деформируемые латуни маркируются по ГОСТ 15527-70.
Марка простой латуни состоит из буквы «Л», указывающей тип сплава - латунь, и двузначной цифры, характеризующей среднее содержание меди. Например, марка Л80 - латунь, содержащая 80 % Cu и 20 % Zn. Все двухкомпонентные латуни хорошо обрабатываются давлением. Их поставляют в виде труб и трубок разной формы сечения, листов, полос, ленты, проволоки и прутков различного профиля. Латунные изделия с большим внутренним напряжением (например, нагартованные) подвержены растрескиванию. При длительном хранении на воздухе на них образуются продольные и поперечные трещины. Чтобы избежать этого, перед длительным хранением необходимо снять внутреннее напряжение, проведя низкотемпературный отжиг при 200-300 C.
В многокомпонентных латунях после буквы Л пишут ряд букв, указывающих, какие легирующие элементы, кроме цинка, входят в эту латунь. Затем через дефисы следуют цифры, первая из которых характеризует среднее содержание меди в процентах, а последующие - каждого из легирующих элементов в той же последовательности, как и в буквенной части марки. Порядок букв и цифр устанавливается по содержанию соответствующего элемента: сначала идет тот элемент, которого больше, а далее по нисходящей. Содержание цинка определяется по разности от 100%.
Латуни в основном применяются как деформируемый коррозионно-стойкий материал. Из них изготавливают листы, трубы, прутки, полосы и некоторые детали: гайки, винты, втулки и др.
Литейные латуни маркируются в соответствии с ГОСТ 1711-30. В начале марки тоже пишут букву Л (латунь), после которой пишут букву Ц, что означает цинк, и число, указывающее на его содержание в процентах. В легированных латунях дополнительно пишут буквы, соответствующие введенным легирующим элементам, и следующие за ними числа указывают на содержание этих элементов в процентах. Остаток, недостающий до 100 %, соответствует содержанию меди. Литейные латуни используют для изготовления арматуры и деталей для судостроения, втулок, вкладышей и подшипников.
Бронзы(сплавы меди с различными элементами, где цинк не является основным). Они подобно латуням подразделяются на литейные и деформируемые. Маркировка всех бронз начинается с букв Бр, что сокращенно означает бронза.
В литейных бронзах после Бр пишут буквы с последующими цифрами, которые символически обозначают элементы, введенные в сплав (в соответствии с таблицей 1), а последующие цифры обозначают содержание этих элементов в процентах. Остальное (до 100 %) – подразумевается медь. Иногда в некоторых марках литейных бронз в конце пишут букву «Л», что означает литейная.
Большинство бронз обладает хорошими литейными свойствами. Их применяют для различного фасонного литья. Чаще всего их используют как коррозионно-стойкий и антифрикционный материал: арматура, ободы, втулки, зубчатые колеса, седла клапанов, червячные колеса и т.д. Все сплавы на основе меди имеют высокую хладостойкость.
Алюминий и сплавы на его основе
Алюминий выпускают в виде чушек, слитков, катанки и т.п. (первичный алюминий) по ГОСТ 11069-74 и в виде деформируемого полуфабриката (листы, профили, прутки и т.п.) по ГОСТ 4784-74. По степени загрязненности тот и другой алюминий подразделяется на алюминий особой чистоты, высокой чистоты и технической чистоты. Первичный алюминий по ГОСТ 11069-74 маркируют буквой А и числом, по которому можно определить содержание примесей в алюминии. Алюминий хорошо деформируется, но плохо обрабатывается резанием. Прокаткой из него можно получить фольгу.
Сплавы на основе алюминия подразделяются на литейные и деформируемые.
Литейные сплавы на основе алюминиямаркируются по ГОСТ 1583-93. Марка отражает основной состав сплава. Большинство марок литейных сплавов начинаются с буквы А, что означает алюминиевый сплав. Затем пишут буквы и цифры, отражающие состав сплава. В ряде случаев алюминиевые сплавы маркируют буквами АЛ (что означает литейный сплав алюминия) и цифрой, означающей номер сплава. Буква В, стоящая в начале марки показывает, что сплав высокопрочный.
Применение алюминия и сплавов на его основе очень разнообразно. Технический алюминий применяют в основном в электротехнике в качестве проводника электрического тока, как заменитель меди. Литейные сплавы на основе алюминия широко применяются в холодильной и пищевой промышленности при изготовлении деталей сложной формы (различными методами литья), от которых требуется повышенная коррозионная стойкость в сочетании с небольшой плотностью, например, поршни некоторых компрессоров, рычаги и другие детали.
Деформируемые сплавы на основе алюминия также находят широкое применение в пищевой и холодильной технике для изготовления различных деталей методом обработки давлением, к которым предъявляются также повышенные требования к коррозионной стойкости и плотности: различные емкости, заклепки и т.п. Важным достоинством всех сплавов на основе алюминия является их высокая хладостойкость.
Титан и сплавы на его основе
Титан и сплавы на его основе маркируются в соответствии с ГОСТ 19807-74 по буквенно-цифровой системе. Однако какой-либо закономерности в маркировке не имеется. Единственной особенностью является наличие во всех марках буквы Т, которая свидетельствует о принадлежности к титану. Числа в марке означают условный номер сплава.
Технический титан маркируется: ВТ1-00; ВТ1-0. Все остальные марки относятся к сплавам на основе титана (ВТ16, АТ4, ОТ4, ПТ21 и др). Главным достоинством титана и его сплавов является хорошее сочетание свойств: относительно низкой плотности, высокой механической прочности и очень высокой коррозионной стойкости (во многих агрессивных средах). Основной недостаток – высокая стоимость и дефицитность. Эти недостатки сдерживают применение их в пищевой и холодильной технике.
Сплавы титана применяются в ракетной, авиационной технике, химическом машиностроении, в судостроении и транспортном машиностроении. Они могут использоваться при повышенных температурах до 500-550 градусов. Изделия из сплавов титана изготавливают обработкой давлением, но могут быть изготовлены и литьем. Состав литейных сплавов обычно соответствует составу деформируемых сплавов. В конце марки литейного сплава стоит буква Л.
Магний и сплавы на его основе
Технический магний из-за его неудовлетворительных свойств не находит применения в качестве конструкционного материала. Сплавы на основе магния в соответствии с гос. стандартом делятся на литейные и деформируемые.
Литейные сплавы магнияв соответствии с ГОСТ 2856-79 маркируют буквами МЛ и числом, которое обозначает условный номер сплава. Иногда после числа пишут строчные буквы: пч – повышенной чистоты; он – общего назначения. Деформируемые сплавы магния маркируют в соответствии с ГОСТ 14957-76 буквами МА и числом, обозначающим условный номер сплава. Иногда после числа могут быть строчные буквы пч, что означает повышенной чистоты.
Сплавы на основе магния обладают подобно сплавам на основе алюминия хорошим сочетанием свойств: низкой плотностью, повышенной коррозионной стойкостью, относительно высокой прочностью (особенно удельной) при хороших технологических свойствах. Поэтому из сплавов магния изготавливают как простые, так и сложные по форме детали, от которых требуется повышенная коррозионная стойкость: горловины, бензиновые баки, арматура, корпусы насосов, барабаны тормозных колес, фермы, штурвалы и многие другие изделия.
Олово, свинец и сплавы на их основе
Свинец в чистом виде практически не используется в пищевой и холодильной технике. Олово применяется в пищевой промышленности в качестве покрытий пищевой тары (например лужение консервной жести). Маркируется олово в соответствии с ГОСТ 860-75. Имеются марки О1пч; О1; О2; О3; О4. Буква О обозначает олово, а цифры – условный номер. С увеличением номера увеличивается количество примесей. Буквы пч в конце марки означают – повышенной чистоты. В пищевой промышленности для лужения консервной жести применяют олово чаще всего марок О1 и О2.
Сплавы на основе олова и свинца в зависимости от назначения подразделяются на две большие группы: баббиты и припои.
Баббиты – сложные сплавы на основе олова и свинца, которые дополнительно содержат сурьму, медь и другие добавки. Они маркируются по ГОСТ 1320-74 буквой Б, что означает баббит, и числом, которое показывает содержание олова в процентах. Иногда кроме буквы Б может быть другая буква, которая указывает на особые добавки. Например, буква Н обозначает добавку никеля (никелевый баббит), буква С – свинцовый баббит и др. Следует иметь в виду, что по марке баббита нельзя установить его полный химический состав. В некоторых случаях даже не указывается содержание олова, например в марке БН, хотя здесь его содержится около 10 %. Имеются и безоловянистые баббиты (например свинцово-кальциевые), которые маркируются по ГОСТ 1209-78 и в данной работе не изучаются.
Баббиты являются наилучшим антифрикционным материалом и применяются в основном в подшипниках скольжения.
Припои в соответствии с ГОСТ 19248-73 подразделяются на группы по многим признакам: по способу расплавления, по температуре расплавления, по основному компоненту и др. По температуре расплавления они подразделяются на 5 групп:
1. Особолегкоплавкие (температура плавления tпл ≤ 145 °С);
2. Легкоплавкие (температура плавления tпл > 145 °С ≤ 450 °С );
3. Среднеплавкие (температура плавления tпл > 450 °С ≤ 1100 °С );
4. Высокоплавкие (температура плавления tпл > 1100 °С ≤ 1850 °С );
5. Тугоплавкие (температура плавления tпл > 1850 °С).
Первые две группы применяются для низкотемпературной (мягкой) пайки, остальные – высокотемпературной (твердой) пайки. По основному компоненту припои подразделяют на: галлиевые, висмутовые, оловянно-свинцовые, оловянные, кадмиевые, свинцовые, цинковые, алюминиевые, германиевые, магниевые, серебряные, медно-цинковые, медные, кобальтовые, никелевые, марганцевые, золотые, палладиевые, платиновые, титановые, железные, циркониевые, ниобиевые, молибденоыве, ванадиевые.
Задание. Составить опорный конспект.
Дата добавления: 2021-03-18; просмотров: 257; Мы поможем в написании вашей работы! |
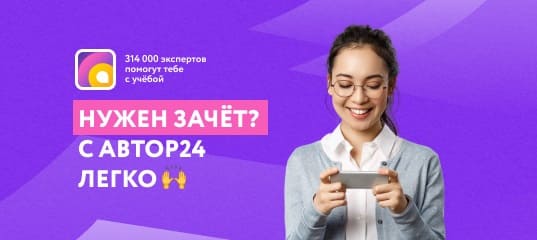
Мы поможем в написании ваших работ!