Легированные инструментальные стали
Основными требованиями, предъявляемыми к инструментальным сталям, являются высокая твердость, износостойкость, ударная вязкость и прокаливаемость. Кроме того, в зависимости от условий работы могут предъявляться специфические требования. Например, режущий инструмент, работающий при высокой скорости резания, должен обладать высокой износостойкостью при температуре 500 … 600 °С, а инструмент, работающий при низких режимах резания, требует износостойкости при температуре до 200 °С. Ручной инструмент (напильники, плашки, метчики и др.) должен иметь высокую износостойкость при нормальных условиях. К штампам, работающим при горячем деформировании, предъявляются требования горячей твердости, адгезии, жаропрочности, упругости и ударной вязкости.
Высокие требования из-за специфики и условий работы различных инструментов создаются наличием тех или иных легирующих элементов.
Легированные инструментальные стали поставляются в виде горячекатаного калиброванного проката, поковок, шлифованного прутка, полосы, кованых заготовок и валков.
Массовая доля вредных примесей (серы и фосфора) в легированных инструментальных сталях не должна превышать 0,03 % каждого элемента. В стали, полученной методом электрошлакового переплава, массовая доля серы допускается не более 0,015 %.
В состоянии поставки твердость легированной инструментальной стали колеблется в зависимости от химического состава в пределах 217 … 269 НВ. Все инструментальные легированные стали улучшаются закалкой. Твердость инструмента, изготовленного из легированной стали, после закалки будет следующая: режущего инструмента — 60 … 64 НRС, измерительного — 50 … 58 НRC.
|
|
В связи с тем что в процессе работы к инструменту, изготовленному из легированных инструментальных сталей, предъявляются различные требования, эти стали подразделяются на следующие группы:
- сталь для режущего и измерительного инструмента;
- сталь для штампового инструмента;
- быстрорежущие инструментальные стали.
Кроме того, легированные стали подразделяют на качественные, высококачественные и особовысококачественные (последние две группы указываются в маркировке).
Сталь для режущего и измерительного инструмента. Для этих целей применяются средне- и высокоуглеродистые и низко- и среднелегированные стали. Массовая доля углерода в этих сталях колеблется в пределах 0,7 … 1,0 %, а отдельные марки содержат до 1,4 %.
Стали для режущего и измерительного инструмента подразделяются на стали неглубокой и глубокой прокаливаемости.
Стали неглубокой прокаливаемости включают в себя хромистые, хромованадиевые, хромовольфрамовые и ванадиевые стали. Массовая доля легирующих элементов колеблется в пределах 1 … 5 %, массовая доля углерода — 0,6 … 1,1 %. Характерной особенностью этих сталей из-за малого содержания легирующих элементов является низкая прокаливаемость. Инструмент, изготовленный из этих сталей, при закалке охлаждается в воде и имеет мягкую незакаленную сердцевину. В связи с этим стали неглубокой прокаливаемости идут на изготовление режущего и измерительного инструмента сечением до 25 мм, что при закалке предотвращает коробление и способствует прокаливаемости по всему сечению инструмента.
|
|
Марки стали этой группы: 7ХФ, 8ХФ, 9ХФ, 11ХФ, 11ХФ (11Х), 13Х. Из сталей этих марок изготавливают резьбовые калибры, метчики, плашки, развертки, протяжки и другой специальный инструмент и технологическую оснастку.
Стали глубокой прокаливаемости содержат 1 … 4 % легирующих элементов; отдельные марки имеют до 8 … 10 % легирующих элементов. Основной легирующий элемент, повышающий прокаливаемость, — хром. Его массовая доля, как правило, составляет 1,0 … 1,5 %. Также прокаливаемость повышают кремний и марганец, однако наличие этих элементов в стали затрудняет технологию закалки.
Марки сталей этой группы: 9X1 (9X), 12X1 (20X), 9ХС, ХГС, 9ХВГ, ХВГ, ХВСГ, 9Х5ВФ (120X), 8Х4В3М3Ф2.
|
|
Из этих сталей изготавливают те же инструменты, что и из сталей неглубокой прокаливаемости, а также холодновысадочные матрицы, пуансоны, клейма, штемпели и другие ответственные детали, от которых требуется повышенная износостойкость.
Сталь для штампового инструмента. Для изготовления инструментов, деформирующих металл, предназначены штамповые стали, которые подразделяются на следующие группы:
- для деформации в холодном состоянии (Х6ВФ, Х12, Х12ВМ, Х12М, Х12Ф1, 7ХГ2ВФ, 6ХВ3МФС);
- для деформации в горячем состоянии (7Х3, 8Х3, 5ХНМ, 5ХНВ, 5ХНВС, 5ХГМ, 4ХМФС, 4Х5В2ФС, 4Х5МФС);
- для ударного инструмента (4ХС, 6ХС, 4ХВ2С, 6ХВ2С, 3Х2Н2МВФ);
- сталь инструментальная валковая (9Х2, 90ХФ, 9Х2МФ, 55Х, 60ХН).
Стали для холодного деформирования должны иметь высокие твердость и прочность, высокую износостойкость, удовлетворительную вязкость и высокую прокаливаемость.
Стали для горячего деформирования должны обладать высоким сопротивлением пластической деформации, высокой теплостойкостью и высокой разгаростойкостью, т. е. высоким сопротивлением термической усталости.
Быстрорежущие инструментальные стали. Быстрорежущими называют высоколегированные стали, предназначенные для изготовления режущего инструмента, работающего при высоких режимах резания. ГОСТ 19265—73 предусматривает поставку инструментальной быстрорежущей стали в виде горячекатаного, калиброванного проката, кованой, в виде полос и прутков со специальной отделкой поверхности следующих марок: Р9, Р18, Р6АМ5, Р6М5К5, 11Р3АМ3ФА, Р6АМ5Ф2, Р12Ф3, Р18К5Ф2, Р9М4К8.
|
|
В маркировке быстрорежущих сталей приняты следующие обозначения:
- буквой Р (от англ. rapid — скорый) обозначаются все быстрорежущие стали. Цифра, стоящая справа после буквы Р, указывает на среднюю массовую долю основного легирующего элемента — вольфрама.
- Буква К обозначает кобальт,
- М — молибден,
- А — азот.
В обозначении марок быстрорежущих сталей не указывается массовая доля хрома, молибдена до 1 % включительно и ванадия в сталях марок Р9, Р18, Р6АМ5, Р9К5, Р6М5К и Р9М4К8.
Все быстрорежущие стали содержат 0,70 … 1,12 % углерода в зависимости от марки, 3,8 … 4,4 % хрома, 0,4 % никеля.
Быстрорежущие стали имеют высокую красностойкость до 620 °С, ударную вязкость в состоянии поставки 18 … 26 Дж/см2, твердость 220 … 260 НВ, предел прочности при растяжении σв = 840 … 940 МПа (84 … 94 кгс/мм2). Высокая красностойкость и горячая твердость создаются легирующими элементами — вольфрамом, ванадием, хромом и молибденом.
Из быстрорежущих сталей делают цельные токарные, строгальные резцы, фрезы, развертки, модульные фрезы, долбяки, протяжки, сверла, метчики и плашки. Кроме того, быстрорежущие стали идут на изготовление различного штампового инструмента (пуансоны, матрицы, ножи для ножниц, машинные ножовки по металлу) и другого инструмента.
Быстрорежущие инструментальные стали способны самозакаливаться на воздухе. В связи с этим при ковке эти стали охлаждают в нагревательных колодцах или в соляных ваннах. При медленном охлаждении в колодцах происходит укрупнение зерен сорбитообразного перлита и карбидов. Кроме того, с целью улучшения обрабатываемости резанием быстрорежущим сталям производят изотермический отжиг. В результате этих операций твердость достигает 200 … 255 НВ.
При последующей ступенчатой закалке при температуре 1 270 … 1 290 °С и трехкратном отпуске при температуре 550 … 570 °С достигаются высокие прочность, твердость и ударная вязкость, а также высокие режущие свойства инструмента. Структура после закалки: карбиды, мартенсит и остаточный аустенит. Остаточный аустенит несколько снижает твердость, и его устраняют многократным отпуском и обработкой холодом. После этих операций он превращается в мартенсит.
По режущим свойствам эти стали бывают нормальной и повышенной производительности. Нормальную производительность имеют стали марок Р18, Р12, Р9, Р9Ф5 (вольфрамовые), Р6М3, Р6М5 (вольфрамомолибденовые); твердость этих сталей равна 98 НRА, теплостойкость — 620 °С. Стали марок Р10К5Ф5, Р18К5Ф2 (с повышенной массовой долей ванадия и содержанием кобальта) имеют повышенную производительность; твердость этих сталей — более 64 НRС, теплостойкость — 630 … 640 °С. Стали последней группы применяют для обработки высокопрочных сталей с аустенитной структурой и других твердых конструкционных материалов.
Высоколегированные стали
Общая характеристика высоколегированных сталей и сплавов. Практикой установлено, что коррозию можно приостановить путем легирования конструкционных сталей и чугунов хромом или хромом и никелем и другими легирующими элементами. Эти легирующие элементы в активных средах переходят в пассивное состояние, на их поверхности возникают тонкие оксидные пленки и поверхность приобретает высокую коррозионную стойкость.
Легирование стали никелем дает возможность получать компонентную (аустенитную) структуру, которая обладает более высокой коррозионной стойкостью, чем хромистые и хромоникелевые стали.
Высоколегированные стали и коррозионно-стойкие, жаростойкие, жаропрочные сплавы (ГОСТ 5632—72) выпускаются на железной, железоникелевой и никелевой основах и поставляются в виде сортового и фасонного проката, калиброванного прутка, прутка со специальной отделкой поверхности, листа тонкого и толстого, полосы, поковок и кованых заготовок, проволоки и труб. Они предназначены для изготовления различных деталей, механизмов и конструкций для работы в коррозионно-активных средах и при высоких температурах.
Высоколегированные стали и сплавы получают методом электрошлакового (ЭШ), вакуумно-дугового (ВД) переплавов и индукционной электроплавкой (ЭП) и в зависимости от основных свойств подразделяют на следующие группы:
- коррозионно-стойкие;
- жаростойкие;
- жаропрочные.
Коррозионно-стойкие стали и сплавы. Коррозионно-стойкими называют такие конструкционные материалы, которые сопротивляются химическому и электрохимическому воздействию окружающей среды.
Коррозионно-стойкие стали и сплавы обладают стойкостью против химической и электрохимической коррозии (атмосферной, почвенной, щелочной, кислотной, межкристаллитной и коррозии под напряжением).
По содержанию углерода коррозионно-стойкие стали и сплавы выпускают низкоуглеродистыми (массовая доля углерода менее 0,3 %) и среднеуглеродистыми (массовая доля углерода более 0,3 %).
Наиболее стойкими против коррозии являются такие химические элементы, как хром и никель, поэтому эти химические элементы являются постоянными легирующими элементами при получении коррозионно-стойких сталей и сплавов. Практика показывает, что устойчивая коррозионная стойкость у сталей и сплавов образуется при массовой доле хрома 12,5 % и выше.
Структура и свойства хромистых сталей зависят от массовой доли хрома и углерода. При содержании хрома 13; 17 и 25 % и при наличии 0,1 … 0,4 % углерода стали приобретают высокую жаростойкость (окалиностойкость).
Хромистые стали имеют высокие технологические свойства: деформируемость, свариваемость и улучшаемость, поэтому основная группа коррозионно-стойких сталей производится на основе хрома, а отдельные марки на основе хрома и никеля, а также титана. Титан и никель вводят для измельчения зерна, а отдельно никель для увеличения прочности, твердости и ударной вязкости.
Наиболее широкое применение получили коррозионно-стойкие хромистые стали следующих марок: 12Х12, 20Х13, 30Х13, 40Х13, 08Х13 и др.
Стали марок 12Х13 и 20Х13 хорошо деформируются и свариваются. Стали марок 30Х13 и 40Х13 свариваются ограниченно, так как средняя массовая доля углерода и высокое содержание хрома способствуют образованию при сварке трещин в районе околошовной зоны основного металла. Эти стали хорошо куются и штампуются в горячем состоянии, так как при высокой температуре они пластичны.
Стали марок 20Х13, 30Х13, 40Х13 — мартенситного класса, а стали 12Х13 — ферритного класса.
Эти стали широко используются как конструкционный и коррозионно-стойкий материал. Их используют для изготовления лопаток различных турбин, компрессоров, клапанов, арматуры нефтеустановок и аппаратов, а стали 30Х13 и 40Х13 — для режущего и измерительного инструмента, пружин, деталей карбюраторов и других деталей, работающих при температуре до 400 °С.
Детали, изготовленные из этих сталей, подвергаются закалке и низкому, среднему и высокому отпуску в зависимости от марки и требуемых свойств.
Сталь марки 40Х13 широко применяется для изготовления хирургического и бытового инструмента.
Хромоникелевые стали в зависимости от химического состава, массовой доли хрома и никеля выпускаются следующих классов: аустенитный, аустенитно-ферритный и аустенитно-мартенситный. Стали с содержанием 18 % хрома и 9 … 10 % никеля образуют структуру аустенита. Эти стали имеют коррозионную стойкость при высоких температурах в различных рабочих средах, в том числе в растворах кислот, обладают высокой обрабатываемостью давлением и свариваемостью. Аустенитные стали получили наиболее широкое применение в химической промышленности и строительстве.
К недостаткам аустенитного класса сталей относят низкие обрабатываемость резанием и литейные свойства, поэтому они широко применяются как конструкционный материал в сварных конструкциях и изделиях, получаемых обработкой давлением.
Наиболее широкое применение нашли стали аустенитного класса О4Х18Н10, О8Х18Н10, О8Х18Н10Т и многие другие, всего около 30 марок. Титан вводится в сталь с целью устранения межкристаллитной коррозии. Аустенитные стали подвергаются закалке при температуре 1 050 … 1 100 °С. Охлаждение изделий производят в масле. После закалки предел прочности при растяжении σв = 500 … 600 МПа (отдельные марки достигают прочности 1 000 … 1 200 МПа), относительное удлинение δ = 35 … 40 %.
Стали аустенитно-ферритного класса в своем составе кроме хрома и никеля содержат титан и кремний. Они имеют более высокие антикоррозионные свойства в активных средах, а также высокие технологические свойства. Наиболее широкое применение нашли аустенитно-ферритные стали марок 12Х21Н5Т, ОХ22Н5Т, Х28АН и др., всего примерно 10 марок.
Закалку этих сталей производят при температуре 950 … 1 000 °С, охлаждение осуществляют в масле. После закалки проводят операцию старения при температуре 500 °С. Предел прочности этих сталей σв = 950 … 1 200 МПа, относительное удлинение δ = 4… 12 %.
Стали аустенитно-мартенситного класса кроме хрома в своем составе имеют алюминий и марганец и пониженную массовую долю никеля (1 … 9 %). Стали этого класса используются как коррозионно-стойкий конструкционный материал для работы в активных, окислительных рабочих средах и имеет более высокие, по сравнению с рассмотренными ранее сталями, механические и химические свойства. Предел прочности в зависимости от химического состава — 1 200 … 1 900 МПа, относительное удлинение — 3 … 10 %.
Марки сталей аустенитно-мартенситного класса: 2Х13Н4Г9, Х15Н9Ю, ОХ17Н7Ю, ОХ17Н7Ю1, 09Х15Н8Ю, 2Х17Н2 и др.
Закалку этих сталей производят при температуре 975 °С, охлаждение осуществляют в масле. После закалки проводят обязательные операции обработки холодом, старение и упрочнение при холодной прокатке.
Жаростойкие стали и сплавы. Известно, что образование окалины на поверхности металла происходит под воздействием температуры и кислорода рабочей среды. Чем выше температура рабочей среды, тем активнее идет процесс образования окалины. Между тем, сама образовавшаяся окалина может препятствовать дальнейшему окислению металла. Это может быть достигнуто тогда, когда оксидная пленка плотная, без трещин и пор.
Практика показывает, что оксидная пленка железа, вольфрама и других элементов обладает низкими защитными свойствами. Через пленки этих металлов легко диффундирует кислород, и происходит образование окалины на большую глубину; окалина растрескивается, становится пористой, металл сгорает.
Хром, алюминий, никель, кремний имеют плотную оксидную пленку, и, кроме того, пленки этих металлов под воздействием температуры не трескаются. Окислившись, поверхность металла детали под воздействием температуры и кислорода в начальный период нагрева становится теплостойкой. Образовавшаяся на поверхности оксидная пленка защищает металл от дальнейшего разрушения.
Максимальная массовая доля хрома (10 %) при температуре 800 … 900 °С обеспечивает устойчивую окалиностойкость. При массовой доле хрома 20 … 25 % рабочая температура может достигать 1 000 … 1 100 °С.
Свойство окалиностойкости обеспечивает не структура стали, а только ее химический состав. В практике нашли применение следующие марки жаростойких сталей: 4Х9С2, 1Х12СЮ, 4Х10С2М, 3Х13Н7С2, Х20НМС2, 4Х18Н25С2, ОХ18Н10Т и др., всего приблизительно 60 марок.
Жаростойкие стали применяют для изготовления деталей, работающих в активных рабочих средах и при высоких температурах с незначительной механической нагрузкой: клапанов автомобильных, тракторных двигателей и дизелей; теплообменников, колосников, труб, электродов свечей зажигания, печных конвейеров, ящиков для цементации, муфелей, реторт, выхлопных систем и других деталей и конструкций в химическом, нефтехимическом и газовом производстве.
Жаропрочные стали и сплавы. Жаропрочность сталей всегда сопровождается их жаростойкостью (окалиностойкостью), т. е. все жаропрочные стали должны быть, прежде всего, жаростойкими.
Рассматривая жаропрочность конструкционного материала, следует знать, что с повышением температуры прочностная характеристика любого конструкционного материала уменьшается, в том числе у обычной конструкционной углеродистой стали. Следовательно, жаропрочность характеризуется двумя показателями: температурой и временем. При этом, если показатель времени брать за основополагающий фактор, то жаропрочность следует характеризовать длительной прочностью. При определении длительной прочности при высокой температуре будем наблюдать ползучесть испытуемого образца, и эта ползучесть увеличивает жаропрочность. На жаропрочность конструкционных материалов влияет их структура и легирующие элементы. Классы структур в этих сталях бывают перлитные, аустенитные и мартенситные. В качестве легирующих элементов в хромоникелевых сталях применяют кремний, марганец, молибден, вольфрам, ванадий и ниобий с различной мас совой долей в зависимости от назначения стали.
По назначению жаропрочные легированные стали подразделяются на клапанные, котельные, котлотурбинные, для реактивной техники. Из этих сталей делают различные детали и конструкции, такие как клапаны машинных двигателей, трубы паро- и газопроводов, аппараты и котлы сверхвысокого давления, лопатки паровых и газовых турбин, вкладыши сопел, крепежные детали и др.
Дата добавления: 2021-03-18; просмотров: 196; Мы поможем в написании вашей работы! |
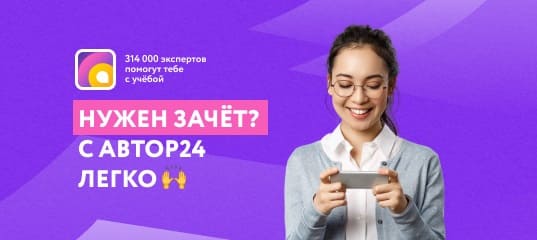
Мы поможем в написании ваших работ!