Устаткування, інструменти, матеріали
1) Розривна машина.
2) Маятниковий копер.
3) Штангенциркуль, лінійка, шліф папір.
4) Набір зразків.
5) Личні напилки, транспортир.
6) Лупа із збільшенням до 10 крат.
Вказівки по підготовці до заняття
При підготовці до заняття студентам необхідно ознайомитися в літературі з методикою механічних випробувань властивостей зварних з’єднань, причинами їх виникнення і способами усунення дефектів, а також методикою визначення показників механічних властивостей. Будову і роботу обладнання вивчити по наявним в лабораторії інструкціях з технічної експлуатації відповідного обладнання.
Порядок виконання роботи
1) Одержати в керівника роботи необхідні зразки і інструменти.
2) Заміряти товщину, ширину і робочу довжину зразків.
3) Помістити зразок у випробувальній машині.
4) Провести випробування.
5) Визначити необхідні показники механічних властивостей.
6) Результати випробувань і обчислень занести в таблицю 8.2.
7) Провести випробування наступних зразків в тому ж порядку.
Таблиця 8.2 – Результати дослідження
№ досліду | Матеріал зразка і вид зварювання | Розміри зразка, мм | Площа перерізу зразка, мм | Макс. зусилля при розриві зразка, Мпа | Тимчасовий опір розриву, МПа | Кут згину зразка, ° | Ударна в’язкість, Дж/м2 | Виявлені дефекти | Примітка | ||
товщина | ширина | довжина | |||||||||
1 | |||||||||||
2 | |||||||||||
3 | |||||||||||
4 | |||||||||||
5 |
|
|
Обробка результатів, їх аналіз та висновки
1) Зробити висновки про якість зварного з’єднання.
2) Захистити звіт по роботі.
Контрольні запитання
8.1) Які види механічних випробувань ви знаєте?
8.2) В яких випадках проводяться механічні випробування зварних з’єднань?
8.3) В чому сутність того чи іншого методу механічних випробувань?
8.4) Назвіть показники механічних властивостей.
8.5) Які дефекти зварних з’єднань Ви знаєте?
8.6) Які причини виникнення дефектів в зварних швах?
8.7) Які інші методи контролю якості зварних з’єднань Ви знаєте?
8.8) Як усунути виявлені недопустимі дефекти або виправити забракований стик?
Лабораторна робота № 9
Магн ітограф ічний метод контролю зварних з’єднань
Мета роботи
Метою роботи заняття є вивчення роботи приладів для магнітографічногоконтролю зварних з’єднань, набуття студентами практичних навиків виявлення внутрішніх дефектів зварних швів за допомогою сучасних магнітографічних дефектоскопів і оцінки якості зварних з’єднань.
|
|
Програма роботи
Студент повинен знати:
- види дефектів зварних з’єднань і причини їх утворення
- властивості магнітних методів контролю
- класифікацію і фізичні основи методів
- будову, призначення та принцип роботи магнітографічних дефектоскопів
- заходи з техніки безпеки при проведення контролю
вміти:
- приєднати прилади до мережі і перевірити їх справність до роботи
- підібрати величини сили струму (А) у намагнічуючих пристроях при контролі зварних швів
- провести контроль зварних з’єднань труб
- Охарактеризувати виявлені дефекти, вид і розмір дефекту
- зробити висновок про якість зварного шва і зварного з’єднання в цілому
Основні теоретичні положення
Магнітні і електромагнітні методи контролю діляться по способам збудження і регістрації полів. Класифікація магнітних методів контролю представлена на рис. 9.1. Для магнітного контролю використовують імпульсні, постійні, змінні (до100 Гц) і комбіновані магнітні поля.
Рисунок 9.1 - Класифікація методів контролю
|
|
Магнітні методи контролю засновані на використання потоку магнітного розсіювання Ф1 (рис.9.2, б) виникаючі в місцях розміщення дефектів при намагнічуванні потоком Ф контролює мого зварного з’єднання (рис. 9.2, а). Намагнічування проводять стаціонарними або пересувними приладами, (рис. 9.2, в,г).
Рисунок 9.2 - Магнітні методи контролю
При використанні цього метода на зварний шов накладають феромагнітну стрічку 1 (рис. 9.2, г) шириною 35 мм, після чого шов намагнічують гнучким соленоїдом або роблять обкатку дисковим магнітом із швидкістю 3-4 м/хв.. На плівці при цьому записують потоки магнітного розсіювання, які виникають в місцях розміщення дефектів. Після цього плівку 1 поміщують відтворюючий прилад (рис. 9.2, д), де записані магнітні поля розсіювання перетворюються в електричні імпульсі. Наявність дефектів визначаються по відхиленню електронного променя, орієнтуючого на осцилограмі 2 (рис. 9.2, д). в теперішній час магнітографічний удосконалений: на екрані осцилографа можна бачити відображення шва із всіма дефектами.
Для виявлення дефектів застосовується також метод порошкової дефектоскопії,заснованій на використанні магнітних порошків (наприклад, залізної окалини Fe2O3) або суспензії (суміші окалини із гасом або маслом). Порошок або суспензія повинні бути зафарбовані, які відрізняються від кольору виробу. Після намагнічування на шов наносять порошок або суспензію. В місцях дефектів, де виник носій розсіювання, утворюються добре видимі скупчення порошку, по якому і судять і наявність дефектів у виробі.(рис. 9.3)
|
|
1 – деталь; 2 – тріщина; 3 – поле розсіювання; 4 – частинки порошку; G – маса; F тр – сила тертя; F3 – сила магнітного поля дефекту; FA – сила Архімеда; FP – результуюча сила; F м – сила магнітного притягання між частинками.
Рисунок 9.3 - Схема утворення магнітного поля (а) і схема сил діючих на частинку (б)
Магнітопорошковий метод дозволяє виявити тріщини з шириною розсіювання 0,001 мм, глибиною 0,01 мм і більше.
При наявності немагнітного покриття на поверхні деталі чутливість методу зменшується. Це зменшення чутливості можна проілюструвати схемою, яка проведена на рис. 9.4.
а – без покриття; б, в – з покриттям; К1, К2, К3 – кількість порошку над тріщиною; t1, t 2 , t 3 – товщина покриття.
Рисунок 9.4 - Шліфовочні тріщини в зразках
Якщо немагнітного покриття немає, то над тріщиною порошок осідає у виді чітких ліній.
Магнітографічний метод контролю заключається у записі магнітних полів розсіювання над дефектом. На магнітну стрічку шляхом намагнічування, яка контролює дільницю деталі разом з прижиманням до її поверхні магнітної стрічки із послідовним відновленням і розшифруванням отриманого запису.
Контроль проводиться згідно ГОСТ – 25225 – 82.
Принципова схема фіксації магнітографічного контолю приведена на рис. 9.5.
.
1 – основний метал; 2 – дефект в шві; 3 – магнітна стрічка; 4 – магнітопровід; 5 – опорні ролики; 6 – обмотка; U – напруга; Ф s – магнітний потік.
Рисунок 9.5 - Схема фіксації дефектів на магнітній стрічці при магнітографічному контролі зварного шва
Цей метод застосовується в основному для перевірки суцільності зварних швів трубопроводів і конструкцій різних споруд, виготовлених із феромагнітних сталей з товщиною стінок до 18 мм.
Намагнічуючі пристрої бувають декількох видів. Найбільш розповсюджені дискові магніти і рухомі намагнічуючі пристрої (рис 9.6).
.
1 – виріб(трубопровід); 2 – контрольований шов; 3 – магнітна стрічка; 4 – дисковий електромагніт; 5- резинова прокладка; 6 – вимикач; 7 – ручка для переміщення електромагніту; 8 – електропровід.
Рисунок 9.6 - Дисковий електромагніт
Дискові електромагніти (рис. 9.6) використовують для контролю листових з’єднань конструкцій і труб товщиною стінки від 5 – 6 мм. Найбільшого розповсюдження отримав дисковий магніт ДМ – 60 із диском діаметром 60 мм. Диски служать полюсами електромагніта. Феромагнітна стрічка притискається гумовим валиком, який знаходиться між полюсами.
Для намагнічування повітряних зварних швів застосовують пересувні намагнічуючі пристрої (ПНУ), і універсальні (УНУ). Загальний вигляд ПНУ показаний на рис. 9.7
1 – виріб трубопроводів; 2 – контрольований шов; 3 – магнітна стрічка; 4 – намагнічуючий пристрій; 5 – вимикач; 6– ручка для переміщення намагнічуючого пристрою; 7 – електропровід.
Рисунок 9.7 - Рухомий намагнічуючий пристрій
Для контролю труб діаметром менше 114 мм застосовують намагнічуючі кліщі (НК), намагнічуючі вилки (НВ) і інші інструменти.
Намагнічуючий пристрій представляє собою спеціальні електромагніти, які складаються з двох довгих (до 200 мм) полюсних пластин, з’єднаних феромагнітними стержнями, які розміщені на них одною або двома контурами. Кривизна торцевих частин полюсних пластин відповідає кривизні труби або другої частини перевіряючої конструкції. В універсальних намагнічуваних пристроях полюсні пластини зміщені мають різну торців поверхні і дозволяють провіряти труби різного діаметра. намагнічуючий пристрій забезпечений чотирма роликами із немагнітного матеріалу. Режими намагнічування зварних швів приведені у таблиці 9.1.
Таблиця 9.1 - Рекомендовані величини сили струму (А) при контролі зварних швів.
Діаметр трубопроводу. мм | Товщина металу, мм |
Тип намагнічуючого пристрою | ||||||||
2 | 4 | 6 | 8 | 0 | 2 | 4 | 6 | 8 | ||
57-89 | - | 5 | 0 | 5 | 8 | - | - | - | - | НВ |
109-188 | - | 5 | 0 | 5 | 8 | 0 | - | - | - | ПНУ-М3 |
163-377 | 0 | 5 | 0 | 5 | 0 | 2 | - | - | - | ПНУ-М2 |
325-1200 | 8 | 5 | 5 | 0 | 4 | 8 | 0 | 2-36 | - | ПНУ-М1 |
166…1200 (листові металоконструкції) | 8 | 2 | 5 | 0 | 4 | 8 | 0 | 2-36 | - | УНУ |
820…1320 (листові металоконструкції) | - | - | - | - | 5 | 7 | 9 | 2 | 5 | МУН-1 |
Магнітографічний метод контролю відрізняється трьома особливостями: частинка порошку на магнітній стрічці нерухомі, що визначають лояльність їх взаємодії з полем дефекту, взаємодія що носить магнітний характер – частинки намагнічуються полем розсіювання дефекту, при проведенні контролю проводиться необхідно одночасно додатково підмагнічувати, тому магнітографічний контроль проводиться тільки способом приклаючого поля. В якості індикатора полів розсіювання від дефектів використовують магнітну стрічку. Технічні характеристики магнітних стрічок приведені в таблиці 9.2.
Таблиця 9.2 - Технічні характеристики магнітної стрічки.
Тип | Основа | Магнітний шар | ||||
Матеріал | Товщина, мкм | Товщина, мкм | Коерцитивна сила, А/м | Залишкова магнітна індукція, 10-4 Тл | Залишковий магнітний потік, 10-8 Вб | |
МК-1 | Триацетат целюлози | 40 | 20 | 7642 | 500 | 0,75 |
МК-2 | Лавсан | 5-30 | 20 | 7960 | 490-500 | 0,80 |
МКУ | - | 35 | - | 2338-12736 | 630-575 | 1,40 |
Можливість магнітографічного контролю розширюють при застосуванні універсальної комбінованої стрічки МКУ. Вона має два шари, нанесеної один на другий. В нижньому шарі застосований порошок з коефіцієнтною силою Нс = 17512 , а в другому верхньому шарі Нс = 7960 . При записі слабкі поля фіксуються у верхньому шарі, а сильні у нижньому.
Для живлення намагнічуючих пристроїв в польових умовах застосовують пересувні станції СПП – 1. Станція живлення складається із генератора постійного струму і бензодвигуна. Станція працює при температурі від - 40 до + 40 0С і відносній вологості 50 %.
Для живлення намагнічуючого пристрою в стаціонарних умовах використовують випрямлячі з напругою 50 – 60 В при силі струму 40 – 50 А.
Магнітографічні дефектоскопи, які застосовуються для відтворення магнітного запису мають блок щитування у виді магнітних головок, закріплених на барабані, що обертається від двигуна. Магнітні головки складаються із двох напівкілець, виготовлених із матеріалу з високою магнітною проникністю (рис. 9.8.)
1 – магнітна стрічка; 2 – магнітна головка; 3 – поле розсіювання над місцем запису дефекту.
Рисунок 9.8 - Схема зчитування магнітного запису дефектів.
Промисловість випускає магнітографічні дефектоскопи трьох видів індикації: імпульсні (у виді кривої), відеоіндикація (телевізійне відображення шва і дефектів) і універсальні (комбінація імпульсної і відеоіндикації на двох роздільних однопроменевих, або на одній двохпроменевій електронній трубці).
Зчитування результатів контролю з магнітної стрілки проводиться дефектоскопами. Простіша блок-схема магнітографічного дефектоскопа приведена на рис. 9.9
1 – електродвигун; 2 – блок головок; 3 – магнітна стрічка; 4 – підсилювач; 5 – генератор розгортка; 6 – електронно-променева трубка
Рисунок 9.9 - Блок-схема магнітографічного дефектоскопа
Дефектоскоп має електродвигун, який приводить у обертання барабан з декількома магнітними головками. Головки переміщуються поперек магнітного поля. Електричні сигнали із головки поступають у підсилювач і подається на електронно-променеву трубку.
Відомі дефектоскопи типу МД – 9 з імпульсивною індикацією, МД – 11 з видимим відображенням. Найбільш удосконалені дефектоскопи МДУ – 2У, МД – 10 ІМ і МГК – 1 які мають подвійну індикацію. Блок-схема дефектоскопа типу МДУ приведена на рис. 9.10.
1 – магнітна стрічка; 2 – магнітна головка; 3 – електродвигун; 4 – підсилювач відтворення; 5 – підсилювач сигналі видоіндикації; 6 – підсилювач сигналів імпульсної індикації; 7 – електронно-променева трубка з довгим післясвіченням; 8 – генератор рядкової і горизонтальної розгорток; 9 – підсилювач зварювальної розгортки; 10 – підсилювач горизонтальної розгортки; 11 – генератор кадрової розгортки; 12 – електронно-променева трубка імпульсної індикації; 13 – блок живлення.
Рисунок 9.10 - Магнітографічний дефектоскоп типу МДУ
До записі полів дефектів магнітну стрічку розмагнічують і укладають з невеликим натягом на контролює мій зварний шов деталі і прижимають її до поверхні.
При протяжці стрічки відносно відновлювальної головки на екрані електронно-променевої трубки при наявності дефекта з’являється візуальне відображення нерухомих імпульсів у виді характерних кривих. Якщо на даній дільниці шва дефектів немає, то спостерігається тільки основна лінія. Порівнюючи отриману криву із еталоном, визначають вид дефекту. На рис. 9.11 показані криві для деяких типових дефектів.
а-тріщина, б-глибокий не провар, в-широкий не провар невеликої глибини, г-непровар з шлаковими включеннями, д-сітка газових пор, е-одинична пора
Рисунок 9.11 - Імпульси від різних дефектів
Еталоном для контролю, і еталонні магнітні стрічки, записані із контрольних взірців зварних з’єднань, які призначені для настройки дефектоскопів і виявлення величини виявлених дефектів.
В якості контролюючих взірців можна використати вирізані із трубопроводу або спеціально зварні стики, а також планки шириною не менше 300 – 500 мм із розміщенням по середині зварного шва. Контрольні стики або планки повинні бути виготовлені із труб або листів тої марки і товщини що і контролюючий виріб, і тій технології цей метод зварювання, режими, зварювальні матеріали по якій виготовлені контрольні зварні з’єднання.
Дата добавления: 2020-12-12; просмотров: 82; Мы поможем в написании вашей работы! |
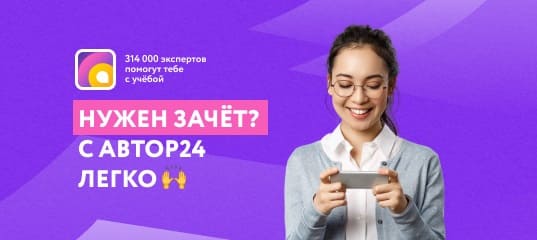
Мы поможем в написании ваших работ!