Разработка чертежа путевой схемы
Когда после прочтенного выбрали путевую схему для вашего макета необходимо ее нанести на бумагу. Начертите схему на бумаге и обозначьте станции – станционные пути, стрелочные переводы, перегоны, рельеф местности мосты, туннели, и все то, о чем мечтаете иметь на макете.
Следующим этапом – эскиз того же но уже в определенном масштабе, по отношению к подмакетнику (рекомендуемый масштаб 1:10). Учтите, что радиусы кривых должны быть как можно больше, подъем пути ~ 3 см х 1 м и длина главного пути на станции – локомотив + 3 – 4 4-х осных вагона ЦМВ. Стрелочные переводы чертите при α = 15° . Из этих рассуждений решите какой типоразмер примените. Самые распространенные типоразмеры в России – НО и ТТ. В меньшем количестве применяется типоразмер N.
Сейчас начните чертить вашу путевую схему. Размеры всех элементов пути и радиусы кривых должны быть строго выдержаны. Величины подъемов – 3 см х 1 м пути необходимо строго выдерживать. На пересечениях путей минимальная высота для прохода подвижного состава должна быть 70-80 мм + толщина строения верхнего пути. Для достижения больших высот можно использовать движения по спирали, как показано на рис. 27.
Рис. 27 Схема движения пути по спирали
На рисунке показана схема путей макета витринного типа, со скрытым путевым развитием, где можно останавливать и отправлять другой поезд и тем создавать впечатление реального движения.
|
|
Расчет радиуса спирали r (рис. 28, а) можно рассчитать по следующей формуле
, где L – длина пути
Если знаем, что на 1 м пути необходимо поднять путь на 3 см, а если нам нужно на 9 см, то длина пути =
Следовательно,
Рис. 28 Расчет радиуса кривой «r» при заданном подъеме пути «h»
Чтобы уменьшить диаметр кривой можно построить овальный путь (рис. 28 б). L рассчитаем по формуле
g ‑ длина прямого участка пути .
Если вы ограничены длиной овала определяем другой радиус кривой.
При таких расчетах как правило расчетный радиус кривой не совпадает с радиусами пути изготовленными заводами. Тогда лучше всего применить рельсы типа «флекс» - которые можно согнуть по кривой любого радиуса. Чтобы упростить точное вычерчивание путевой схемы макета, многие изготовители моделей железных дорог выпускают пластмассовые линейки – шаблоны с прорезями длин и конфигурацией изготовляемых ими элементов пути. При их использовании облегчите себе подсчет количества отдельных рельсовых элементов. На вычерченной путевой схеме обозначьте начало и конец радиусных кривых, высоту пути над условной нулевой отметкой – начало и конец подъема. Пронумеруйте пути и стрелочные переводы (см. рис. 21-22-23 и 26). Определите количество всех путевых элементов, которые вам будут нужны. Приобретите их и соберите путевую схему на полу. Помните пословицу «семь раз отмерь и потом только отрежь» – это очень кстати в вашем случае. Вычерченную вашу путевую схему размножьте себе в нескольких экземплярах, т.к. они будут необходимы при изготовлении решетки подрамника, нижнего строения пути и разделение пути на участки и еще в других случаях.
|
|
4. КОНСТРУКЦИЯ И ИЗГОТОВЛЕНИЕ ПОДМАКЕТНИКА
Для устройства небольших макетов в размером сторон до 1-1,5 м в качестве основания часто применяют древесностружечную плиту, которая хорошо тем, что не коробится, весьма легко обрабатывается режущим инструментом, хорошо держит детали, приклеенные казеиновым, столярным или синтетическими клеями. Изготовление подмакетника из ДСП потребует немного времени. После того как плита обрезана по нужным размерам, ее следует окантовать по периметру деревянными брусками, приклеив их по торцам и дополнительно укрепив шурупами с потайными головками. Во избежание расслоения плиты до приклеивания брусков нужно разметить места для шурупов и просверлить на полную глубину отверстия диаметром, меньшим, чем диаметр шурупа. Деревянные бруски наряду с повышением прочности придадут подмакетнику впечатление законченности конструкции. Лицевую сторону брусков можно офанеровать декоративным шпоном и покрыть мебельным лаком или оклеить синтетической пленкой, имитирующей фанеровку. Тщательно отделанные лицевые поверхности всегда производят хорошее впечатление и весь макет в целом выглядит солиднее.
|
|
Подмакетник из ДСП относительно прост, но его нельзя считать наилучшим из-за того, что он тяжел и, кроме того, плита представляет собой огромную мембрану, которая очень усиливает шум проходящих по макету поездов.
В любительской практике для устройства макетов различных размеров и конфигураций широко применяют более сложные подмакетники рамной конструкции. Длина рамы не должна превышать 2,5 м при ширине 2 м, так как рамы больших размеров трудно сделать прочными, сохраняющими жесткость и строгую плоскостность. Если требуется построить подмакетник больших размеров, то его целесообразно сделать из нескольких рам, плотно и жестко соединяющихся между собой и имеющих каждая в отдельности стойки.
|
|
Раму подмакетника (рис. 29) собирают из деревянных брусков и обязательно снабжают двумя диагоналями и несколькими поперечинами, благодаря которым подмакетник станет прочным на изгиб и не даст перекосов в горизонтальной плоскости.
Рис. 29 Рамная конструкция подмакетника
Диагональные и поперечные бруски будут опорой для отдельных узлов и элементов будущего макета. Соединение деревянных брусков требует навыков и прежде всего умения правильно разместить составные элементы, чтобы они точно и плотно прилегали друг к другу. Моделисту надо выработать привычку не делать без разметки даже самого простого соединения.
В качестве связей отдельных деталей подмакетника могут быть применены различные типы соединений. Самое простое соединение – соединение впритык (рис. 30, а). Оно может быть достаточно прочным, если соединяемые концы строго прямоугольны. Торцы обрабатывают рубанком, а прямоугольность проверяют угольником. Соединение крепят деревянными шипами или шурупами, а соединяемые плоскости приклеивают. Соединение в ус (рис. 30, б) отличается от предыдущего тем, что сопрягаемые концы деталей срезают под углом 45°. Усиленное соединение в ус (рис. 30, в) по конструкции – это обычное соединенное с внутренней стороны угла небольшим квадратным или треугольным деревянным бруском. Соединение под углом сквозным шипом (рис. 30, г) является весьма прочным. В зависимости от толщины брусков делают один или несколько шипов. Примыкание под углом сквозным шипом – соединение конца одного бруска с продольной стороной другого, в котором делают сквозную проушину (рис. 30, д), применяют при установке поперечин подмакетника. Для большей прочности шип можно расклинить. При этом гнездо (проушину) делают немного расширяющейся к наружной стороне рамы. Для усиления соединения в тонкие пропилы шипа вбивают клинышки, предварительно смазанные клеем. Диагональные и поперечные планки в местах пересечений соединяют посредством направленных навстречу друг другу вырезов, сделанных на половину глубины соединяемых досок. Такое крепление называют – соединение накладкой вполдерева (рис. 30, е).
Рис. 30 Соединение деревянных деталей: а – впритык: б – в ус; г – сквозным шипом; д – примыкание под углом сквозным шипом; е – накладкой вполдерева
Угловые соединения рамы усиливают фанерными или металлическими прямоугольниками (или треугольниками) с размерами сторон 200 мм. Толщина фанерного угольника должна быть не менее 10 мм. Угольник следует «утопить» в раму на толщину материала, из которого он изготовлен, для чего на брусках рамы делают соответствующие вырезы. Фанерный угольник крепят шурупами на клею.
Разметку и отпиливание брусков под углом лучше всего производить при помощи несложного приспособления – ярунка (рис. 31), собираемого из трех толстых досок. Стенки должны быть совершенно параллельны друг другу. В них делают отвесный пропил, достигающий дна и направленный под углом 45° к стенкам. Второй такой же пропил выполняют, немного отступив, под тем же углом, но направленным в противоположную сторону. Наконец, третий пропил (средний) производят под прямым углом к стенкам и дну. Это приспособление облегчает работу при постройке подмакетника и при дальнейшем строительстве макета, когда потребуется множество брусков различных размеров и линий обрезов.
Рис. 31 Ярунок
Рис. 32 Металлический каркас подмакетника
Раму подмакетника собирают из сосновых хорошо просушенных брусков сечением 80 х 30 мм, для диагоналей и поперечин будут бруски сечением 60 х 20 мм. Бруски ставят на «ребро», что позволяет получить более жесткую конструкцию. Собранный подмакетник после высыхания клея покрывают масляным лаком или натуральной олифой для повышения влагоустойчивости конструкции. С нижней стороны подмакетник закрывают съемными листами фанеры или какого-либо отделочного пластика для того, чтобы защитить от проникновения пыли в электрические устройства. При необходимости на подмакетнике следует установить гнезда для крепления металлических или деревянных опор – ножек. Для этого вдоль узких сторон подмакетника, немного отступив от краев, прикрепляют бруски толщиной 50-60 мм с отверстиями для ножек. Вместо ножек иногда делают складные козлы, на которых устанавливают подмакетник. Устройства для крепления ножек или козлы могут оказаться нужными, если, например, макет будет экспонироваться на выставке и т.п.
Рис. 33 Шарнирные устройства для откидных подмакетников
Некоторые любители предпочитают изготавливать подмакетник из алюминиевого уголка. Рама может быть построена по принципу деревянной. Однако при больших размерах конструкции, собранной в одной плоскости, трудно избавиться от перекосов в моменты перемещения подмакетника, что приведет к появлению трещин в рельефе, перекосу рельсовых путей, нарушению электрических соединений и др. Подмакетник из уголка будет соответствовать необходимым требованиям, если его построить в виде объемной конструкции (рис. 32), в которой будут косые связи боковых сторон, придающие конструкции жесткость. Сооружая макет металлической конструкции, особое внимание следует обращать на хорошую изоляцию электрических устройств и цепей от коротких замыканий.
Для убираемых в шкаф или нишу откидных подмакетников потребуется сделать шарнирные и направляющие устройства, которые позволят легко переводить макет из вертикального в рабочее горизонтальное положение (рис. 33). Для изготовления этих устройств потребуется металлический уголок, полоса толщиной 8-10 мм, стальной труток диаметром 8-10 мм, подшипники, несколько болтов с гайками, деревянные бруски сечением 50 х 50 мм и др., в зависимости от принятой конструкции.
Еще несколько практических советов. В большинстве случаев у макетов, которые необходимо убирать, целесообразно иметь складывающиеся или вообще убирающиеся ножки. Одним из вариантов убирающихся ножек показан на рис. 34. Ножка выполнена из деревянного бруска 50 х 50 мм. Хомут, который ее обхватывает во внутреннем углу рамы изготавливают из 2-3 мм стальной полосы. На угол, как показано на рис. 34 приварена гайка М 10, через которую болтом М 10 х 30 наглухо закрепляем ножку. С нижней части ножек из-за неровности полов необходимо делать регулирующиеся болты. М 10 х 50. Сначала в нижнем конце ножки высверливаем отверстие Ф 12 мм на глубину 50-60 мм. Расширяем отверстие на высоту гайки М 10 и вклеиваем ее туда при помощи эпоксидной смолы. На болт М 10 х 50 ( с резьбой по всей длине) наворачиваем контргайку и вворачиваем в ножку. После установки рамы в горизонтальную плоскость затягиваем контргайки и можем приступить к следующей работе – к соединению двух щитов.
Рис. 34 Крепление стойки подмакетника
Соединение двух щитов должно быть крепким и точным. Не должно быть никаких сдвигов по отношении друг друга и репсовые нити должны сходиться как по боковым и вертикальным уровням. На рис. 35 показаны два варианта. Вариант а) не удовлетворяет требованиям. Дерево является относительно мягким материалом. От собственного веса щита может произойти смятие и при затяжке болта это нельзя исправить. Вариант б) надежный и решение правильное. Металлические фланцы центрируются болтом, такого же диаметра, как внутренние отверстия фланцев. Размеры фланцев и болта необходимо подбирать по величине и весу щитов.
Подъем пути на большие высоты по спиральному пути журнал «Eisenbahn maqazin» за 1991 год опубликовал несколько интересных решений. На рис. 36 показано изготовление и сборка пути с помощью вертикальных стержней, на которых нарезана резьба (М 10 – М 12). Стержни закреплены на раме и на них крепят сегменты пути с перекрышей и постепенно поднимая путь на нужную высоту. Размеры на рис. 36, б относятся к типоразмеру «НО».
Рис. 35 Скрепление щитов: а – не удовлетворяющее требованиям; б – удовлетворяющее всем требованиям
Рис. 36 Подъем пути на большую высоту по спиральному пути: а – этап изготовления; б – размеры этажей пути
На рис. 37, а показано другое исполнение спирального подъема пути. Принцип такой же как показано на рис. 36, а, но вместо стержней применили подставки, к которым крепятся радиусные сегменты. Самое простое решение спирального пути показано на рис. 37, б. Такое решение имеет перед предыдущим решением преимущество своей простотой в изготовлении.
Рис. 37 Подъем пути с помощью спирали: а – сегменты с приставками; б - с прямыми сегментами
5. ПЕРЕНОС ПУТЕВОЙ СХЕМЫ НА ПОДМАКЕТНИК И ИЗГОТОВЛЕНИЕ КАРКАСА ПОД ПУТИ
Пространственное размещение путевой схемы на подмакетнике является важным этапом при строительстве макета. От точности вычерчивания и изготовления каркаса под путь зависит движение по макету подвижного состава. Каркас под путевую схему должен быть жестким и его осевая линия должна проходить точно под осевой линии пути. Все железные дороги из-за неровности земной поверхности вынуждены строить железнодорожный путь в плане в виде сочетаний прямых и кривых, а в профиле – горизонтальных и наклонных участков. Пространственное размещение путевой схемы следует начинать с перенесения рельсовой схемы перегонов и станций с чертежа на плоскость макета, на которой закрепим плотную бумагу (ватман) или еще лучше картон толщиной 1,5-2 мм. После этого необходимо вычертить ширину балластной призмы на путевых участках и на станциях. Край призмы относим на столько от края подмакетника чтобы установить в последующем все постройки, которые предусмотрели ранее. Ширина определена нормой NEM 122 (Верхнее строение пути), где обозначено буквой «б»
Норма NEM 122 « Верхнего строения пути» для дороги нормальной колеи 1250-1700 мм:
1. Эта норма определяет сечение верхнего строения пути с учетом размеров балластной призмы и земляного полотна настоящих железных дорог. Норма указывает также уклоны нижнего строения пути.
2. Норма приведена для однопутной линии на прямом участке. В других сложных случаях (при наличии подпорных стенок, скальных вырубок и т.п.) необходимо учитывать эти основные рекомендации.
3. Для участков с большим числом путей руководствоваться основными рекомендациями в норму NEM 112 (Межпутьевое расстояние).
4. Наклон рельсового полотна на кривых определять по нормам NEM 114
5. С боку полотна проходят обочины – эти места для размещения сигналов, столбов контактной сети и т.п. И очень важно, чтобы эти устройства не попадали в габарит приближения подвижного состава NEM 102 и 103.
В последнее время популярно стало изготовление макетов и диорам узкоколейных дорог, что привело в 1991 г. появлению нормы NEM 123 «Сечение верхнего строения пути для узкоколейных дорог».
В пояснительной записке к этой норме можно прочитать, что эти рекомендации распространяются только на верхнее строение пути узкоколейных моделей (в т.ч. и садовых). Эскиз приведен для однопутного узкоколейного прямого участка пути. Если дорога прокладывается в сложных условиях рельефа местности, то размер С устанавливается самостоятельно.
В норме оговорены три группы узкоколейных дорог, классифицированных по ширине колеи прототипа (m, e, i,). В свою очередь эти размеры определены нормой NEMO10, (таблицу приводим).
Уклон рельсового полотна на кривых также берется в соответствии с рекомендациями NEM 114. Размещение сигналов, столбов контактной сети и т.п. – на обочине полотна с учетом габарита приближения строений по NEM 104.
Затем по контуру прямых и кривых участков пути из фанеры (толщиной 4-6 мм размер С) выпиливают полосы, служащие основанием железнодорожного пути, по ширине они должны соответствовать основным площадкам насыпей и выемок. Полосы закрепляют к подмакетнику по разметке на нужной высоте при помощи деревянных брусков соответствующего размера. Основания путей надо располагать на макете так, чтобы их середина совпадала с осью железнодорожного пути или междупутья на двухпутных участках. Будучи укрепленными на брусках различной высоты, они образуют основу будущих насыпей с подъемами и уклонами.
Во избежание самопроизвольного расцепления вагонов и схода поезда с рельсов на макете не допускаются переломы профиля пути. Сопрягаемые элементы профиля (подъемы и спуски) соединяют круговыми кривыми, а при малой разности сопрягаемых элементов устраивают горизонтальные площадки (рис. 38, б). Устройство прямых на горизонтальных площадках обязательно между сопряжениями спусков (подъемов) с кривыми участками пути в горизонтальной плоскости. Горизонтальные участки пути – площадки – соединяют с наклонными участками отрезками меньшей крутизны или круговыми кривыми (рис. 38, а). Для правильного сопряжения элементов профиля укладку путей проверяют шаблонами.
Рис. 38 Профиль железнодорожного пути: а – сопряжение элементов профиля; б - профиль наклонного участка
Если подмакетник построен в виде рамы, то для путей, проходящих в нулевом уровне, следует сделать твердое основание.
За нулевой уровень на макете обычно принимают плоскость, расположенную на верхней кромке рамы подмакетника, или плоскость плиты, на которой собирают макет. Там, где будут расположены станции, размеры основания должны соответствовать всей площади станции и прилегающей территории. Станционные площадки изготавливают из листов фанеры или аргиллита и крепят к раме подмакетника на требуемом уровне при помощи поперечных реек, которые в свою очередь закрепляют на боковых или диагональных брусках рамы. Для станций и разъездов, расположенных выше нулевого уровня, также устраивают жесткие площадки, которые крепят к подмакетнику при помощи вертикальных стоек и стенок, придающих большую жесткость второму, третьему и другим уровням макета. В тех участках макета, где рельсовый путь уходит в тоннели, заранее устанавливают каркасы тоннельных порталов, которые оформляют при отделке макета (рис. 39).
Рис. 39 Конструкция каркаса макета
На время монтажа макета станционные площадки нужно оставлять съемными, так как в процессе работы возникает необходимость пропилить различные отверстия – люки для установки стрелочных приводов, реле сигналов, расцепителей, монтажа электрических цепей и т.д. Рельеф макета может быть и таким, зато часть путей придется расположить в выемке, ниже нулевого уровня. На подмакетниках, сделанных из плит, для размещения путей ниже нулевого уровня возможности нет. В этом случае следует искусственно приподнять нулевой уровень на макете.
Насыпи и выемки являются связующими элементами профиля пути со станционными площадками. И те, и другие должны естественно и гармонично сочетаться с окружающим рельефом местности. При устройстве горизонтальных и наклонных насыпей нужно применять деревянные бруски в виде равносторонней трапеции (рис. 40, а).
Высота брусков, их боковые стороны задают размеры насыпи и направление откосов. Трапециевидные бруски при помощи шурупов крепят к подмакетнику на определенном расстоянии друг от друга по оси рельсовой колеи. Подъемы и уклоны делают при помощи таких же брусков, но различающихся по высоте. Уменьшение или увеличение высоты возможно только за счет уменьшения или увеличения основания трапеции. Верхняя часть бруска во всех случаях должна быть одинаковой и равняться ширине основной площадки насыпи. Сверху на бруски прикрепляют фанерные полосы – основания для верхнего строения пути.
Рис. 40 Бруски для изготовления насыпи (а) и установки сигналов (б)
При строительстве насыпей, полунасыпей, выемок и полувыемок не следует забывать об имитации водоотводных устройств – канав, кюветов. Если они воспроизведены на макете в определенных местах, макет только выигрывает от таких подробностей и будет свидетельствовать о серьезном подходе автора к его постройке. Хотя водоотводные сооружения относятся к категории инженерных сооружений, о них целесообразно напомнить в этом разделе, так как формирование их на макете должно начаться в процессе изготовления рельефа.
Откосные стороны насыпей закрывают полосами картона, которые приклеивают или прибивают небольшими гвоздями к боковинам брусков. Чтобы скрепить стыки боковин с основной плоскостью насыпи и с углублением для водоотводного устройства, на всю насыпь с прилегающими участками макета столярным клеем ПВА наклеивают широкие полосы из марли или полотняной ткани с некоторым нахлестом одной полосы на другую.
После высыхания клея поверхности откосов офактуривают смесью столярного клея и мелких древесных опилок при помощи широкой кисти. В некоторых местах поверхность дополнительно присыпают мелкими опилками для того, чтобы придать ей неоднородность. При покраске поверхности, используя оттенки одного цветового тона краски, эти неоднородности можно художественно усилить. Так как основа насыпи является пустотелой, в процессе ее сооружения нужно наметить места, где впоследствии будут установлены сигналы, и закрепить на них деревянные бруски – опоры для светофоров, семафоров и др. (рис. 40, б). Нижнее строение пути в разрезе показано на рис. 41, доска с нулевым уровнем, уровень строений, глубина канав и сечение насыпью.
Рис. 41 Нижнее строение пути на макете
6. СОЗДАНИЕ РЕЛЬЕФА МЕСТНОСТИ НА МАКЕТЕ
Неотъемлемой частью макета являются возвышения и холмы, которые в определенных местах разрезают путевыми выемками. Кроме того, возвышения на макете несут и другую побочную функцию: они скрывают часть путей, которые сознательно убирают из виду. Возвышенности можно сделать следующим способом. Из газетной бумаги делают плотные комки в виде шаров, которые на клею укладывают в том месте, где будет возвышенность (рис. 42). Комки также склеиваются друг с другом. Один слой комков наклеивают на другой и создают приблизительную форму желаемой возвышенности или даже горы с определенными склонами и уступами. Затем всю высохшую массу бумажных комков оклеивают лоскутами хорошо промокаемой бумаги величиной с блюдце, смазанными с обеих сторон клеем. Каждый следующий лоскут должен заходить на предыдущий приблизительно на 2 см. На первый слой бумаги, образующий поверхность возвышенности, наклеивают марлю или нестирильный бинт, а затем еще два слоя бумажных лоскутов. Для наклеивания бумаги и марли можно применить синтетические клеи ПВА или «Бустилат», которые сохнут довольно долго. Чтобы придать поверхности возвышенности более интересную и естественную форм, пока окончательно не просох клей, в отдельных местах можно усилить неровности, слегка надавливая на поверхность твердыми предметами. В этой стадии работы хорошо вклеить в определенные места яркие фактурные детали, имитирующие осыпи, сбросы, срезы поверхности, застрявшие «в давние времена» валуны, для чего используют самые неожиданные материалы – сосновую кору, скорлупу грецкого ореха, обломки пемзы, обрезки корковой пробки и т.п.
Рис. 42 Изготовление возвышенности с использованием бумажных комков
После высыхания клея поверхность покрывают грунтом, состоящим из того же клея с добавлением серой и зеленой краски. Можно использовать анилиновые красители для хлопчатобумажных тканей. После грунтования поверхность готова для дальнейшей работы по офактуриванию. Подобным образом можно создавать рельеф пересеченной местности с небольшими возвышенностями, оврагами и др.
Поверхности склонов, холмов, возвышенностей и т.д. можно сделать, наклеивая на бумажные комки полотняную ткань, пропитанную клеем. Ее поверхность легко принимает необходимую форму, например форму оврага или обрыва. Ткань вдавливают в нужных местах и после высыхания она сохраняет заданную форму. Комки бумаги, создав на первом этапе определенные высоты рельефа, в конечном итоге приобретают значение заполнителей пустот, усиливающих прочность сделанной поверхности.
Рельеф местности на макете должен быть увязан с темой макета, его путевой схемой, искусственными сооружениями, а пейзаж дополнять и украшать общую картину. Рельеф может быть использован, чтобы скрыть от зрителя часть железнодорожных путей, перегружающих макет большим количеством рельсов.
Если внутри возвышенности скрыты рельсовые пути, то ее постройку начинают с изготовления жесткого каркаса из дерева и фанеры с тоннелем внутри. При устройстве участков пути, скрытых в тоннелях, необходимо предусмотреть возможность доступа к этим участкам извне на случай ремонта пути или схода с рельсов подвижного состава. Для этого на плоскости подмакетника пропиливают окна, позволяющие снизу подобраться рукой к тоннельным путям. Эти окна прикрывают легкосъемными щитками, предотвращающими падение подвижного состава при сходе с рельсов.
Возможны и более сложные методы создания рельефа, когда, например, верхнюю часть возвышенности делают съемной, что упрощает монтажные и ремонтные работы на скрытой в тоннеле части пути. Вспомните изображение рельефа местности на географических картах при помощи горизонталей. На большом листе бумаги в натуральную величину макетной возвышенности изображают будущий ее рельеф. Расстояние между горизонталями в зависимости от размеров возвышенности берут равным 30-80 мм. Горизонтали переносят на фанеру толщиной 3-4 мм и по их контурам выпиливают лобзиком извилистые полосы или замкнутые фигурные кольца с шириной полос 70-100 мм, у которых наружный обрез соответствует определенной линии горизонтального среза будущей возвышенности. Подготовленные таким образом полосы и кольца в той же последовательности крепят друг над другом на дистанционных брусках гвоздями или шурупами, образуя жесткий каркас возвышенности (рис. 43, а). Если возвышенность должна быть разъемной, то одну из горизонталей выпиливают в двух экземплярах и при монтаже каркаса накладывают одну на другую так, чтобы одна из горизонталей заканчивала нижнюю часть каркаса, а вторая, подобная горизонталь, начинала верхнюю часть возвышенности. Место соприкосновения этих двух одинаковых деталей и будет стыковочной плоскостью снимаемой части с основанием возвышенности. Верхняя горизонталь всего каркаса может представлять собой площадку, на которой в дальнейшем размещают детали пейзажа. Собранный каркас оклеивают в направлении снизу вверх полосами картона, а после высыхания клея обтягивают снаружи несколькими слоями бумажных лоскутов в сочетании с тканью или марлей.
Рис. 43 Каркасы рельефа, изготовленные: а – методом горизонталей; б – путем применения жестких вертикальных ребер; в – в виде нервюр
Для задних планов макетов, скрывающих в тоннелях часть рельсового пути, можно рекомендовать изготовление каркаса возвышенности при помощи вертикальных ребер, которые выпиливают из фанеры (рис. 43, б). Задняя часть макета обычно скрыта от глаз зрителя, поэтому часть возвышенности, обращенную к фону, для удобства эксплуатации закрывают легкосъемным щитом.
Достаточной жесткостью и небольшой массой отличается конструкция каркаса рельефа, выполненная в виде комбинации вертикальных ребер (рис. 43, в). Горизонтальные полосы могут служить основанием железнодорожных путей.
При любом способе обтяжки на клеевой основе поверхности макета в переходных местах от плоскости подмакетника или станционной площадки к склеенной поверхности возвышенности, насыпи, выемки и т.д. после высыхания клея возникают сильные поверхностные натяжения, которые приводят к образованию трещин. Поэтому при обтяжке макета в этих местах нужно наклеивать дополнительные полосы из полотняной ткани.
Для грунтовки и более детальной отделки поверхностей можно использовать смесь гипсовой кашицы, клейстера и порошковой краски в соотношении 10 частей гипса и 1 часть крахмала (масса красящего компонента не учитывается). Из крахмала заваривают обычный клейстер и в него постепенно подсыпают гипсовый порошок. Смесь доводят до густоты сметаны и к ней добавляют красящий порошок (зеленый с серым или желтый с коричневым). Образовавшуюся массу наносят на поверхность рельефа кистью, предназначенной для масляной живописи. В сочетании с клейстером гипсовая кашица не так быстро твердеет и некоторое время остается эластичной. Это качество особенно важно при усадке и растяжении макета, зависящих от изменения влажности и температуры.
Создавая рельеф местности, многие моделисты применяют пенопласт – легкий, хорошо поддающийся обработке материал. Из пенопласта делают отдельные части насыпей, примыкающие к мостам и путепроводам. Он хорош как декоративный материал при имитации открытых скальных пород; очень похожа на каменные осыпи пенопластовая крошка.
Однако вряд ли целесообразно применять пенопласт для заполнения объемов гор, возвышенностей, которые лучше строить на каркасах, а пенопласт использовать для отделки наружных поверхностей. Пенопласт хорошо растворяется ацетоном, растворителем 646, давая сильную усадку. Пользуясь этим свойством, на пенопластовой заготовке можно создать русла небольших ручьев, сгладить склоны оврагов, осыпей. Наносить растворитель на пенопласт надо небольшими дозами, постепенно, так как процесс изменения его формы продолжается некоторое время после окончания обработки до тех пор, пока весь впитавшийся в пенопласт растворитель не испарится. Поверхность мелкопористого пенопласта после обработки растворителем заплывает и поры пропадают. Для подачи необходимой дозы растворителя следует применять шприц объемом 5 см³ с иглой. Пенопласт хорошо обжигается огнем, образуя причудливые неровности, которые на макете могут стать берегами речек, прудов, неровностями земли. Обработку пенопласта растворителем и его обжиг допускается проводить только на открытом воздухе, так как и в том, и в другом случае происходит выделение вредных паров и дыма. Пенопласт склеивают нитроклеями, во избежание образования раковин в местах склейки лучше пользоваться загустевшим клеем, который обеднен растворителем. Пенопласт можно также склеивать клеем ПВА. Участки макета, сделанные из пенопласта, можно окрашивать темперой на казеиновой основе и масляными художественными красками, в которые рекомендуется добавлять немного сиккатива, чтобы окрашенные поверхности не блестели и имели более естественную матовую фактуру.
Следует обратить внимание моделистов на то, что в работе по созданию рельефа на макете и по его отделке нужно очень осмотрительно пользоваться водорастворимыми клеями и красками, которые при некоторых обстоятельствах могут стать аккумуляторами влаги. Проникнув во внутренние узлы макета, сырость вызовет коррозию металлических и гниение деревянных деталей готового макета. Поэтому хорошо просушенные участки рельефа в местах склеек целесообразно покрыть олифой, которая остановит проникновение влаги.
Формируя поверхность макета, нужно постоянно думать о массе будущего сооружения, так как нередко случается, что подмакетник становится неподъемным после того, как сделан рельеф.
При создании рельефа местности на макете можно также использовать монтажную пену (типа «Макрофлекс»). Она представляет собой пенополиуретановый герметик, который практически не впитывает влагу, не течет, не теряет своих свойств в течение длительного времени. Обладая высокой адгезией, пена липнет буквально ко всем материалам кроме жирных поверхностей, силикона, полиэтилена и аналогичных веществ.
Пена (или герметик) обычно упакован в баллончики-тубусы по 0,75 л, которые укомплектованы трубкой-насадкой. При выходе из баллончика получается около 30 литров очень легкой пены с объемным весом 30 кг/м.куб. Поскольку раствор пены в баллончике сильно газирован, то после нанесения слоя пены в свободном состоянию, она продолжает увеличиваться в объеме. Именно это свойство используется при герметизации швов, когда пена сама заполняет все неровности. В нашем случае надо учитывать такие свойства.
Рис. 44 Создание рельефа местности на макете при помощи монтажной пены
С помощью пены можно изготовить рельеф местности (холмы, горы и прочее) на макете по принципу «скорлупы». Полученный по такой технологии рельеф обладает рядом преимуществ перед технологией папье-маше, например. Во-первых, такой рельеф очень легкий, во-вторых, процесс изготовления значительно быстрее и менее трудоемок, в-третьих, жесткость такого рельефа достаточно высока, а свойства материала (пена) позволяют конструировать любые поверхности в любой плоскости. И так мы делаем рельеф на макете. Проложены основные магистрали и теперь их надо закрыть «горами».
Для этого делаем каркас из проволоки (рис. 44). Он может быть выполнен из любой мягкой проволоки (алюминиевой или медной толщиной 0,8-1,5 мм). Никаких нагрузок в данном случае каркас не несет – он только обеспечивает форму поверхности на период нанесения слоя пены и в дальнейшем использоваться на самом макете не будет. Можно даже сплести мягкую сетку для многоразового использования на макете. Сама пена достаточно прочна в застывшем состоянии. На уже готовый к покрытию ландшафт накладываем заготовку из проволоки и подгоняем точно по размеру, чтобы все внутренние размеры обеспечили движение составов в туннелях и пр. После этого каркас снимаем с макета, закрываем его полиэтиленовой пленкой и наносим в несколько слоев пену. Перед применением баллончик следует тщательно взболтать, привернуть прилагаемое сопло к вентилю, затем повернуть баллончик дном вверх. Регулировать количество подаваемой пены можно нажатием или загибанием кнопки сопла на баллончике.
После работы насадку следует промыть ацетоном. Чтобы удалить остатки пены, иначе повторное использование баллончика будет невозможно. Желательно подготовить для работы сразу несколько таких рельефных «скорлупок», чтобы использовать баллончик полностью, поскольку из-за сильной вязкости пены всегда есть вероятность, что повторное использование баллончика будет невозможно.
После того как пена застынет ножом можно придать окончательный вид данной возвышенности. Застывание пены длится несколько часов, после чего она твердеет и ее можно механически обрабатывать: резать ножом, обрабатывать рашпилем или шкуркой. В поверхности вырезаем отверстия для туннелей, необходимые технологические проемы (если они требуются) для установки зданий или сооружений. Если рельеф предусматривает какие-то плоскости, то заблаговременно можно подготовить куски пенопласта требуемой формы и при заливке пеной эти куски вдавить в нее. После затвердевания это будет монолитная масса.
Далее полученную заготовку – «скорлупу» снимаем с каркаса, грунтуем и окрашиваем водоэмульсионными красками в нужный цвет.
Крепить конструкцию к подмакетнику можно при помощи шурупов или клея.
Меры безопасности при работе с монтажной пеной:
Работать при распылении лучше в защитных очках и обязательно в резиновых перчатках. Избегать попадания пены на кожу. Если состав попал в глаза, то надо промыть их большим количеством воды, после чего немедленно обратиться к врачу. При работе с пеной надо иметь хорошую вентиляцию в помещении и следить за тем, чтобы вблизи не было открытого огня.
Брызги пены, попавшие случайно на другие поверхности можно удалить раствором ацетона.
Детям пользоваться пеной запрещено.
Многие моделисты в последние годы пользуются при моделировании скал гипсом. Сравнительный анализ горных поверхностей, выполненных способом из склеенных кусков пенопласта (формирование требуемой поверхности горячим ножом или паяльником) и гипсовых рельефов безусловно показали преимущество последнего по оптике (рис. 45). Конечно, применение на переносном макете или модуле гипсового Монблана повлечет необходимость усиленной физической подготовки обладателя сей конструкции. Поэтому бесспорным является преимущественное использование этой технологии на стационарных макетах или ненормированных модулях, не предназначенных для переноски.
Рис. 45 Модель скальной породы из гипса
Как профессиональный метод в США длительное время осваивается изготовление скал из алебастры или модельного гипса. Почти 20 лет спустя этот метод попадает в Германию и вот теперь очень скромно такие попытки начинаются в России. Одним из самых больших препятствий для моделиста в этом методе является определенная художественная подготовка. Но даже при минимальном опыте можно получить хороший результат, следуя советам и постоянно учась. В любом случае следует очень хорошо подружиться с фотоаппаратом, почаще обращаться к фотоальбомам с пейзажами и внимательно вглядываться в окружающий мир.
На иллюстрациях можно увидеть весь процесс горообразования. На основу макета (в данном случае это небольшой модуль) к поперечным ребрам прибиваем мелкими гвоздями алюминиевую сетку. Возможна замена этого материала. Основное требование – сетка должна быть прочной и держать, придаваемую ей форму. При этом надо помнить, что гипс при затвердевании дает усадку на 10-15 мм по требуемому контуру. Заполнять сетку следует раствором гипса, доведенного до консистенции жидкой каши.
Раствор продавливаем в закрепленную решетку и обязательно следите за тем, чтобы решетка полностью покрывалась раствором, чтобы образовывалась «железобетонная» структура – это очень важно для придания механической прочности. Далее надо нанести дополнительный слой, чтобы получить возможность работать ножом и стамеской для горообразования и получения объемной фактуры. Работать надо быстро и постарайтесь израсходовать весь разведенный раствор. Узким шпателем следует чуть разровнять необходимые места (рис. 46).
Рис. 46 Сечение скальной поверхности: 1 – основа; 2 – сетка; 3.1 – контур гипсового слоя; 3.2 – контур после обработки
Через 1-2 часа после затвердевания можно приступать к работе штихелем и стамеской (рис. 47, а). Если помещение влажное и температура невысокая, то гипс может позволит работать в течение нескольких часов. При избыточном высыхании – используйте мокрую тряпку, которой следует наложить на поверхность, для придания эластичности.
Обязательно пользуйтесь хорошо заточенным инструментом (штихели шириной 12, 25 и 35 мм с ручками). Эти столь широкие штихели наиболее оптимальны для получения оптически верной проработки деталей. Существует некоторая закономерность в масштабировании, при которой излишне проработанная поверхность получается мало правдоподобной. При обработке заготовку хорошо закрепите на столе или макете. Итак, несколько приемов обработки. При прямом скалывании или же соскабливании мы получим относительно гладкую скальную поверхность, с другой стороны, при скалывании и последующем подклеивании сколотых кусочков в различных положениях возникает очень правдоподобная картина эрозийной структуры. Этим же путем можно сформировать расщелины.
Обработку следует производить в горизонтальном направлении, чтобы показать горизонтальные пласты с уклонами, наблюдаемые в природе.
Иногда при скалывании могут образоваться пустоты из-за погрешностей в заливке гипса. Можно их заделать кусочками строительного мусора, но есть и иной путь. Внимательно вглядитесь в скальный пейзаж. Очень часто встречаются пещеры и гроты. Можно даже заранее позаботиться о создании такой структуры, предварительно «встроив» в гипс шарик из бумаги, который после высыхания легко удаляется из монолита.
Обнаружившиеся и возникшие мелкие поры и раковины на поверхности следует обязательно зашпаклевать.
Перед дальнейшей работой всю поверхность надо обработать краской из аэрографа. Можно использовать и водно-дисперсионные краски высокой консистенции. Цвет – очень светло-серый, преобладание белого цвета с редкими прожилками черного и охры. После просушки надо смешать темные тона краски, добавив к темнейшим красно- и черно-коричневую.
Рис. 47 Изготовление фрагментов местности макета из камня методом литья, гипса в силиконовые формы: а – карьер; б – подпорка стенки; в – собранные формообразующие камушки подготовленные для заливки силиконом; г – гипсовые отливки уложены на подготовленное место на макете
Для придания плавных цветовых переходов можно после нанесения краски взять ведро с водой и губкой осветлить большую часть перенасыщенных тонов. После просушки поверхность можно обрызгать матовым лаком, а острые кромки, сделанные из сухой крошки подкоптить пламенем свечи. Очень осторожно следует красить острые кромки толстым слоем краски, т.к. они могут исчезнуть под слоем. Тут же можно нанести растительность в расщелины.
С появлением практики по указанной технологии можно будет изготавливать не только гранитные скалы, но и сланцы.
Один совет: ваше производство должно быть безотходным и безвредным для самого макета. При скалывании образуются отходы и пыль при обработке. Поэтому постройку железнодорожного пути и другие работы, чувствительные к грязи следует выполнять после окончательной обработки гипсовой поверхности, а опасные участки накрывать бумагой. Это защитить чувствительные объекты от попадания гипсовой крошки и пыли.
Неоспоримое преимущество описанного метода состоит в том, что ландшафт и скалы на макете образуются без швов, поскольку очень трудно соединить несколько разных цветовых оттенков и на макете это смотрится убого. Здесь поможет правильный выбор цветовой гаммы всего макета
В модельной практике имеется еще один метод применения гипса. Это литье гипса в силиконовые формы.
Конечно, речь не идет о монументальных произведениях, но вот на своем комнатном модуле или клубном макете можно изготовить вполне достоверные скальные пейзажи, отлить требуемое число порталов туннелей или упорных стенок, уникальных виадуков или неповторимых по красоте опор.
Итак метод литья в гибкие (силиконовые) формы. Работа начинается с поисков подходящего камня с нужной поверхностью, который станет прототипом для будущего скалистого склона, разреза карьера (рис. 47, а) и т.д. Здесь требуется только фантазия и внимательный взгляд под ноги и не по сторонам. Для нужной формы вообще-то подойдет 1-2 камня с интересной поверхностью. Потом эти отливки можно раскалывать, вертеть вокруг своей оси, тем самым добиваясь неповторимой поверхности. Надо помнить, что если требуется создать каменный хаос дикой природы, то поверхность может быть любой, но если карьер создан в результате деятельности человека, то на его стенах должны быть видны следы машинного воздействия.
Изготовление формы для скалистой поверхности.
На очищенную поверхность камня аккуратным слоем нанести силиконовый герметик (это может быть латекс, силиконовая мастика, герметик «Момент» и т.п.), применяемый для герметизации швов и в настоящее время появившийся в продаже в хозяйственных магазинах. Если возникнет проблема с отлипанием его от формы, смажьте поверхность камня легким слоем вазелина, тщательно втерев его во все расщелины. После застывания до «отлива» первого слоя (в основном это 12-25 мин.) надо проложить слой марли и повторить заливку, чтобы обеспечить необходимую механическую прочность вашей форме. Форма получается выпуклая и проблем с литьем не будет.
Изготовление формы для подпорной стенки из мелких фрагментов (рис. 47, б). В качестве основного формообразующего элемента следует найти мелкие камушки по форме и структуре подходящие для имитации каменной стенки. Даже это может быть порезанный на кусочки лист пенополиуретана с характерной «известняковой» поверхностью. На заранее подготовленный лист картона, ДСП выклеиваете слои заготовки (рис. 47, в).
Литье
Используйте гипс строительный или медицинский. Я воспользовался «Шпатлевкой заполняющей» (Оптимист, целлюлозная шпатлевка на гипсовой основе, пр-ва Турция). Последний материал мне понравился, так как обладает хорошей заполняющей способностью, не дает трещин, поскольку имеет целлюлозное наполнение.
Разводить гипс необходимо до концентрации блинного тесла (примерно до двух частей гипса на 1 часть воды). В воду можно сразу добавить какой-либо краситель (гуашь или водные краски), чтобы получить сразу основной цвет каменного массива (желто-коричневый тон для известняковых пород, а серо-зеленый, например для гранитных скал).
Перед заливкой форму следует намазать мыльным раствором, чтобы облегчить извлечение застывшей массы.
Как только гипс в форме начинает сохнуть, то еще не высохшую отливку прямо в форме можно сразу аккуратно приложить на заранее подготовленное место на рельефе макета (рис. 47, г). Перед этим это место следует смочить. Таким образом можно сразу закрепить отливку на макете.
Возникшие раковины, трещины и даже расколовшиеся отливки не должны вас огорчать, так как раковины заделываются тут же с помощью пальца и разведенного раствора для литья, а расколовшиеся куски пристраиваются куда-нибудь еще в рельеф, заполняя поверхность.
Приклеивать отливки можно и потом, после полного высыхания, с помощью какого-либо быстросохнущего клея, но помните, что он должен быстро застывать, так как ваш каменный склон имеет большую крутизну, и долгосохнущий клей создаст много хлопот по удержанию «каменных глыб».
Отделка и окраска
Этот раздел достаточно краток – любые матовые краски на водной, эмульсионной или акриловой основе «земных» тонов, цвета камня от красного, желто-коричневого до черного. Слабый темно-коричневый тон следует нанести в местах над обвалом камней, а сам обвал образуется из остатков гипсовой крошки после литья. Только ее надо отсортировать и просеять. Перед окраской обязательно следует поработать штихелем над рельефностью разломов, стыков, острых кромок и т.д.
Покраска подпорных стенок из камня и порталов туннелей также не сложна.
Если на макете показана холмистая местность, то для прохождения путей под возвышенностями или горами делают туннели (однопутные или двухпутные). Размеры отверстий туннелей принимают по схемам, показанным на рис. 49. Входы в туннель оформляют порталами (рис. 48), которые сооружают из камня или бетона. Как и в макетах других сооружений, эти материалы заменяет органическое стекло и полистирол.
Рис. 48 Портал туннеля
Рис. 49 Схема построения отверстия тоннеля
Для успешной эксплуатации вашего будущего макета все время строительства нельзя забывать об одной из основных норм, (Габарит приближения строений NEM 102).
Габарит приближения строений на прямых участках, устанавливает ограничительный контур, внутрь которого не должны заходить элементы зданий, инженерных и искусственных сооружений, устройств сигнализации, опор, подвесок контактной сети. Исключение составляет размещение в нижней части габарита различных исполнительных механизмов, - приводов стрелочных переводов, расцепителей и пр., а также настилов переездов и переходов. Пространство, в котором допускается размещение этих элементов, определено нормой «Габарит подвижного состава» NEM 301.
Рис. 50 Шаблон NEM 102
Чтобы облегчить себе труд, рекомендую изготовить шаблон, который все время под рукой.
Рис. 50 Шаблон для приближения строений 1:1
СОДЕРЖАНИЕ
В В Е Д Е Н И Е................................................................................................ 3
ЧТО НЕОБХОДИМО РЕШИТЬ ПЕРЕД НАЧАЛОМ СТРОИТЕЛЬСТВА МАКЕТА............................................................................................................................. 7
1. РАЗМЕРЫ МАКЕТА И ЕГО СОХРАННОСТЬ..................................... 7
2. ВЫБОР ТЕМЫ МАКЕТА........................................................................ 23
3. РАЗРАБОТКА КОНСТРУКТОРСКОЙ ДОКУМЕНТАЦИИ............ 27
3.1 Разработка путевой схемы макета..................................................... 27
3.2 Разработка чертежа путевой схемы.................................................. 40
4. КОНСТРУКЦИЯ И ИЗГОТОВЛЕНИЕ ПОДМАКЕТНИКА............. 43
5. ПЕРЕНОС ПУТЕВОЙ СХЕМЫ НА ПОДМАКЕТНИК И ИЗГОТОВЛЕНИЕ КАРКАСА ПОД ПУТИ................................................................................. 53
6. СОЗДАНИЕ РЕЛЬЕФА МЕСТНОСТИ НА МАКЕТЕ........................ 60
Дата добавления: 2021-02-10; просмотров: 47; Мы поможем в написании вашей работы! |
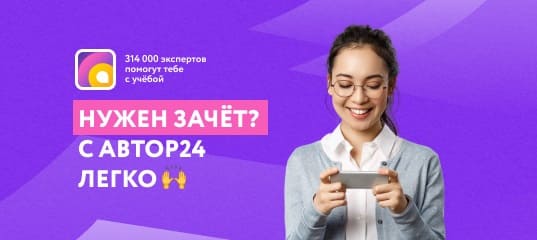
Мы поможем в написании ваших работ!