Варианты для выполнения задания
Эскиз детали на задание
Таблица 1
Варианты задания
№ варианта | Размеры, мм | ||||
А | Б | В | Г | Д | |
1 | 14 | 54 | 25 | 30 | 75 |
2 | 14 | 45 | 24 | 15 | 55 |
3 | 11 | 48 | 27 | 26 | 80 |
4 | 11 | 55 | 35 | 15 | 75 |
5 | 20 | 50 | 28 | 15 | 50 |
6 | 12 | 40 | 20 | 14 | 40 |
7 | 14 | 46 | 22 | 18 | 50 |
8 | 16 | 48 | 24 | 20 | 60 |
9 | 18 | 50 | 24 | 22 | 50 |
10 | 20 | 50 | 28 | 16 | 40 |
11 | 14 | 48 | 24 | 16 | 40 |
12 | 18 | 44 | 26 | 16 | 40 |
13 | 18 | 44 | 26 | 26 | 60 |
14 | 10 | 40 | 26 | 16 | 40 |
15 | 12 | 42 | 22 | 16 | 40 |
16 | 18 | 64 | 36 | 16 | 40 |
17 | 12 | 44 | 26 | 16 | 36 |
18 | 10 | 54 | 22 | 20 | 60 |
18 | 8 | 48 | 20 | 16 | 34 |
20 | 6 | 34 | 16 | 26 | 40 |
21 | 4 | 40 | 18 | 14 | 50 |
Радиус галтели (скругления) для всех вариантов задания принять равным 6 мм (R 6).
Номер варианта берется по номеру в списке журнала группы.
Пример выполнения задания
Шаг 1. Эскиз детали.
Рис. 1. Эскиз детали
Шаг 2. Размеры заготовки и размещение инструмента.
Сформировать размеры заготовки (длину Lз и диаметр Dз).
1) Длина заготовки.
, мм , (1)
где Д – максимальный размер детали вдоль оси ее вращения (60 мм); L1– запас по длине заготовки для ее крепления в патроне и для отрезки детали (можно принять L1 = 20мм); L2– припуск на обработку торцовой части детали (L2= 2 мм).
2) Диаметр заготовки.
, мм , (2)
где - наибольший диаметр детали (48 мм), d = 2мм – припуск на сторону.
|
|
=> размеры заготовки: 52х77 мм.
Шаг 3. Выбор расположения вершины инструмента (точка А, см. рис. 2).
Это исходное положение суппорта. В этом положении осуществляется смена инструмента. Разместим его в двадцати миллиметрах от угла заготовки. Если суппорт находится за осью шпинделя, то его удобно разместить так, как показано на рис. 2. Точку вершины инструмента определим как «0-станка». Ее координаты в системе координат станка: Xc=0, Zc=0.
Рис. 2. Заготовка и нулевая точка инструмента
Шаг 4. Расчет координат основных опорных точек
Для написания управляющей программы необходимо рассчитать координаты опорных (узловых) точек. Они рассчитываются в системе координат детали. Систему координат детали мы вправе расположить где угодно, лишь бы нам было удобно использовать ее для определения координат движения инструмента. Наиболее удобно расположить ее на оси вращения заготовки и в плоскости патрона так, как показано на рис. 3.
Рис. 3. К расчету координат основных опорных точек
в системе координат детали
Таким образом, система координат детали смещена относительно системы координат станка (см. рис. 2):
по си X – на -46 мм;
|
|
по оси Z – на -97 мм.
Значения основных опорных (узловых) точек приведены в таблице 1.
Таблица 1
Координаты основных опорных точек в системе координат детали
№ | X,мм | Z ,мм | Примечание |
А | 46 | 97 | Исходное положение вершины инструмента |
1 | 0 | 75 | |
2 | 5 | 75 | |
3 | 10 | 55 | |
4 | 18 | 55 | Начало галтели |
5 | 24 | 49 | Конец галтели |
6 | 24 | 15 | |
7 | 0 | 77 | |
8 | 26 | 77 | |
9 | 28 | 77 | Точка подхода к заготовке на ускоренной подаче |
10 | 26 | 13 | Точка подхода отрезного резца к детали на ускореннйе подаче с учетом его ширины (ширина лезвия = 2 мм) |
Теперь можно начать составлять управляющую программу.
Токарная
20 ;Заготовка D=52мм, L=77мм
30 ;"0" станка x=46мм, z=97мм
40 ;"0" детали x= -46; z= -97
; включаем шпиндель на 1000 об/мин, правое вращение:
S1000 M03
; устанавливаем первый инструмент в рабочую позицию:
T01 M06
; быстрый подвод инструмента к т.9:
G00 X28. Z77.
Кадры нумеруем с шагом 10 (чтобы потом в случае необходимости можно было вставить дополнительные кадры). Здесь первые 4 кадра – это комментарии. Они не отрабатываются, а носят информационный характер. С кадра №50 начинается непосредственно программа. Для указания координат в «мм» после значения ставим точку (иначе система ЧПУ воспримет эти значения в дискретах).
|
|
Следующий этап – подрезание торца детали. Необходимо снять 2 мм. Разбиваем припуск на 2 прохода (глубина резания – 1мм). Используем многопроходный цикл G24.
G 24 X 0. Z 76.
X 0. Z 75.
Далее нам предстоит обработать коническую поверхность. Используем многопроходный цикл G20. Поскольку припуск большой, то разбиваем его на несколько проходов (рис. 4). Глубину резания принимаем равной 2 мм, поэтому координаты X точек 12..24 следуют с шагом 2 мм.
Рис. 4. К расчету координат точек для программирования
многопроходного цикла обработки конуса
Координаты точек приведены в таблице 2. Траектория инструмента при первом проходе выделена жирными линиями. Он программируется следующим образом. Вначале необходимо сделать переход в точку №11 (X=30мм, Z=75мм) на ускоренной подаче, затем включить код G20 с указанием координат точки №12 (X=28мм, Z=55мм) и величины приращения конуса (R=-5мм):
; начало обработки конуса (цикл G20):
G00 X30. Z75.
G 20 X 28. Z 55. R -5.
В итоге инструмент опишет траекторию, указанную стрелками на рис. 4.
Таблица 2
Координаты опорных точек при обработке конуса.
|
|
№ | X ,мм | Z ,мм | № | X ,мм | Z ,мм | |
11 | 30 | 75 | 12 | 28 | 55 | |
13 | 26 | 55 | 14 | 24 | 55 | |
15 | 22 | 55 | 16 | 20 | 55 | |
17 | 18 | 55 | 18 | 16 | 55 | |
19 | 14 | 55 | 20 | 12 | 55 | |
21 | 10 | 55 | 22 | 8 | 55 | |
23 | 6 | 55 | 24 | 5 | 55 |
Последний проход выполнен глубиной 1 мм.
Поскольку код G20 модальный (сохраняет свое действие на последующие кадры программы), то для программирования остальных проходов его можно не указывать. Продолжение текста программы для обработки конуса:
X 26. Z55. R-5.
X24. Z55. R-5.
X24. Z55. R-5.
X22. Z55. R-5.
X20. Z55. R-5.
X18. Z55. R-5.
X16. Z55. R-5.
X14. Z55. R-5.
X12. Z55. R-5.
X10. Z55. R-5.
X8. Z55. R-5.
X6. Z55. R-5.
X5. Z55. R-5.
Далее необходимо проточить поверхность диаметром 48 мм. Для этого перейдем на ускоренной подаче в точку с координатами X= 48мм, Z= 56мм (за 1 мм до начала врезания). Выполнить обработку на рабочей подаче до точки
G 00 X24. Z56.
G01 Z 13.
Осталось обработать галтель. Для этого перейдем на быстрой подаче в точку X=22 мм Z=55 мм (начало галтели).
G00 X25.
GOO Z55.
G00 X22.
Галтель радиусом 6 мм обработаем в три прохода (рис. 14). На первом проходе обработаем галтель радиусом 2 мм (код G03, точки 25-26), на втором проходе – галтель радиусом 4 мм (код G02, точки 27-28), на третьем проходе – галтель радиусом 6 мм (код G03, точки 4-5). Текст программы приведен группой кадров № 300-340. в Кадре № 350 возвращаем инструмент в исходную позицию (в точку А).
Рис. 5. К обработке галтели
G 03 X 24. Z 53. R 2.
G 00 Z 51.
G 02 X 20. Z 55. R 4.
G 00 X 18.
G03 X24. Z49. R 6.
G00 X46. Z97.
Осталось только отрезать деталь. Кадром №360 отрезной резец устанавливается в рабочую позицию. Кадр №370 – быстрый подвод инструмента к месту отрезки. Кадр №380 – отрезка на рабочей подаче. Кадры №390 и №400 – отвод отрезного резца в исходную позицию (в точку А). Кадры №410 и №420 – выключение шпинделя и окончание программы.
; операция отрезная:
Дата добавления: 2021-02-10; просмотров: 96; Мы поможем в написании вашей работы! |
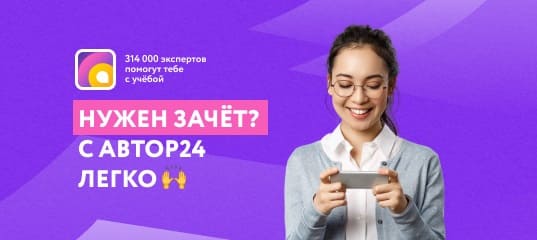
Мы поможем в написании ваших работ!