Литейно-технологические свойства материала Б16 .
ЛУГАНСКИЙ ГОСУДАРСТВЕННЫЙ УНИВЕРСИТЕТ
ИМЕНИ ВЛАДИМИРА ДАЛЯ
ИНСТИТУТ ГРАЖДАНСКОЙ ЗАЩИТЫ
КАФЕДРА ПОЖАРНОЙ БЕЗОПАСНОСТИ
КОНТРОЛЬНАЯ РАБОТА
по дисциплине "Материаловедение и технология материалов"
Студент Грибинюк В.А. _____________
Группа ГЗз-281с
Вариант № 24
Руководитель работы доц. Друзь О.Н. _____________
Дата представления работы на кафедру
на рецензию……………………………..
Регистрационный номер………………………………….Регистратор…………….
(подпись)
Защищена с оценкой …………………………………
Преподаватель …………………………… ……………..
(должность, фамилия, инициалы) (подпись)
Дата………………………
Вариант 24
1. Что такое твердый раствор? Виды твердых растворов, примеры.
2. Под действием каких напряжений происходит пластическая деформация и как при этом изменяются структура и свойства металла?
3. Вычертите диаграмму состояния железо - карбид железа, укажите структурные составляющие во всех областях диаграммы, опишите превращения и постройте кривую охлаждения (с применением правила фаз) для сплава, содержащего 0,8 % С. Какова структура этого сплава при комнатной температуре и как такой сплав называется?
|
|
4. Используя диаграмму состояния железо-цементит, определите температуру полного и нормализационного отжигов для стали 15. Охарактеризуйте эти режимы термической обработки и опишите микроструктуру и свойства стали.
5. В чем отличие ступенчатой закалки от изотермической? Каковы преимущества и недостатки каждого из этих видов закалки?
6. Выберите углеродистую сталь для изготовления сверл. Назначьте режим термической обработки, опишите сущность происходящих превращений, структуру и свойства инструмента. 29
7. Копиры должны иметь минимальную деформацию и высокую износоустойчивость поверхностного слоя при твердости 750...1000 НV. Для их изготовления выбрана сталь 38ХВФЮА. Укажите состав и определите группу стали по назначению. Назначьте и обоснуйте режим термической и химико-термической обработки, объяснив влияние легирования на превращения, происходящие на всех этапах обработки данной стали. Опишите структуру и свойства стали после обработки.
8. Для изготовления постоянного магнита сечением 50X50 мм выбран сплав ЕХ9К15М2. Расшифруйте состав и укажите группу сплава по назначению. Назначьте режим термической обработки и опишите структуру и свойства после обработки.
|
|
9. В качестве материала для заливки вкладышей подшипников скольжения выбран сплав Б16. Укажите состав и определите группу сплава по назначению. Опишите микроструктуру сплава и основные требования, предъявляемые к сплавам этой группы.
10. Термопластичные пластмассы, их особенность и область применения. Приведите примеры важнейших термопластов.
1. Твердыми растворами называют фазы, в которых один из компонентов сплава сохраняет свою кристаллическую решетку, а атомы других (или другого) компонентов располагаются в решетке первого компонента (растворителя), изменяя ее размеры (периоды). Таким образом, твердый раствор, состоящий из двух или нескольких компонентов, имеет один тип решетки и представляет собой одну фазу.
Существуют твердые растворы внедрения и твердые растворы замещения. При образовании твердых растворов внедрения атомы растворенного компонента B размещаются между атомами растворителя A в его кристаллической решетке. При образовании твердых растворов замещения атомы растворенного компонента B замещают часть атомов растворителя (компонент A) в его кристаллической решетке.
Рисунок 1 – Твердые растворы: а – замещения, б – внедрения
Поскольку размеры растворенных атомов отличаются от размеров атомов растворителя, то образование твердого раствора сопровождается искажением кристаллической решетки растворителя.
Рисунок 2 – Искажения кристаллической решетки в твердых растворах замещения:
а –атом растворенного компонента больше атома растворителя
б –атом растворенного компонента меньше атома растворителя
Твердые растворы замещения могут быть с ограниченной и неограниченной растворимостью. В твердых растворах с ограниченной растворимостью концентрация растворенного компонента возможна до определенных пределов.
В твердых растворах с неограниченной растворимостью возможна любая концентрация растворенного компонента (от 0 до 100 %). Твердые растворы с неограниченной растворимостью образуются при соблюдении следующих условий: 1) у компонентов должны быть однотипные кристаллические решетки; 2) различие в атомных радиусах компонентов не должно превышать для сплавов на основе железа 9%, а для сплавов на основе меди 15%; 3) компоненты должны обладать близостью физико-химических свойств. Однако соблюдение этих свойств не всегда приводит к образованию твердых растворов замещения с неограниченной растворимостью. На практике, как правило, образуются твердые растворы с ограниченной растворимостью.
Твердые растворы внедрения могут быть только с ограниченной концентрации, поскольку число пор в решетке ограничено, а атомы основного компонента сохраняются в узлах решетки.
Твердые растворы замещения с неограниченной растворимостью на основе компонентов: Ag и Au, Ni и Cu, Mo и W, V и Ti, и т.д.
Твердые растворы замещения с ограниченной растворимостью на основе компонентов: Al и Cu, Cu и Zn, и т.д.
Твердые растворы внедрения: при растворении в металлах неметаллических элементов, как углерод, бор, азот и кислород. Например: Fe и С.
|
|
|
|
2. Деформацией называется изменение формы и размеров тела под действием напряжений.
Напряжение - сила, действующая на единицу площади сечения детали.
Напряжения и вызываемые ими деформации могут возникать при действии на тело внешних сил растяжения, сжатия и т.д., а также в результате фазовых (структурных) превращений, усадки и других физико-химических процессов, протекающих в металлах, и связанных с изменением объема. Металл, находящийся в напряженном состоянии, при любом виде нагружения всегда испытывает напряжения нормальные и касательные.
Рисунок 3 - Схема возникновения нормальных и касательных напряжений в металле при его нагружении.
Рост нормальных и касательных напряжений приводит к разным последствиям. Рост нормальных напряжений приводит к хрупкому разрушению. Пластическую деформацию вызывают касательные напряжения.
Деформация металла под действием напряжений может быть упругой и пластической.
Пластической или остаточной называется деформация после прекращения действия вызвавших ее напряжений.
При пластическом деформировании одна часть кристалла перемещается по отношению к другой под действием касательных напряжений. При снятии нагрузок сдвиг остается, т.е. происходит пластическая деформация (рис. 4).
В результате развития пластической деформации может произойти вязкое разрушение путем сдвига.
а - ненапряженная решетка; б - упругая деформация; в - упругая и пластическая деформация; г - пластическая деформация; д, е - пластичное (вязкое) разрушение в результате среза
Рисунок 4 - Схема пластической деформации и вязкого разрушения под действием касательных напряжений
Пластическая деформация происходит в результате скольжения или двойникования. Ранее предполагали, что при скольжении одна часть кристалла сдвигается относительно другой части на целое число периодов как единое целое. Необходимое для этого напряжение получается на несколько порядков выше действительного сдвигового напряжения.
В основу современной теории пластической деформации взяты следующие положения:
· скольжение распространяется по плоскости сдвига последовательно, а не одновременно;
· скольжение начинается от мест нарушений кристаллической решетки, которые возникают в кристалле при его нагружении.
Схема механизма деформации представлена на рисунке 5 а.
В равновесном состоянии дислокация неподвижна. Под действием напряжения экстраплоскость смещается справа налево при незначительном перемещении атомов. Нижняя часть плоскости Р/S (SR) сместится вправо и совместится с нижним краем экстра- плоскости РQ.
QR- остаточная деформация.
При дальнейшем движении дислокация пройдет всю плоскость скольжения и выйдет на поверхность зерна. При этом верхняя часть зерна сдвинута относительно нижней на один межатомный период решетки (рис. 5 б).
При каждом перемещении дислокации на один шаг необходимо разорвать связь только между двумя рядами атомов в плоскости Р/S, а не между всеми атомами, расположенными выше и ниже плоскости скольжения. Необходимое сдвиговое напряжение при этом мало, равно практически действительному.
а - перемещение атомов при двихении краевой дислокации на одно межатомное расстояние; б - перемещение дислокации через весь кристалл
Рисунок 5 - Схема дислокационного механизма пластической деформации
Влияние пластической деформации на структуру и свойства металла и сплавов.
Текстура деформации создает кристаллическую анизотропию, при которой наибольшая разница свойств проявляется для направлений, расположенных под углом 45o друг к другу. С увеличением степени деформации характеристики пластичности (относительное удлинение, относительное сужение) и вязкости (ударная вязкость) уменьшаются, а прочностные характеристики (предел упругости, предел текучести, предел прочности) и твердость увеличиваются. Также повышается электросопротивление, снижаются сопротивление коррозии, теплопроводность, магнитная проницаемость.
Совокупность явлений, связанных с изменением механических, физических и других свойств металлов и сплавов в процессе пластической деформации называют деформационным упрочнением или наклепом.
Упрочнение при наклепе объясняется возрастанием на несколько порядков плотности дислокаций:
Их свободное перемещение затрудняется взаимным влиянием, также торможением дислокаций в связи с измельчением блоков и зерен, искажениями решетки металлов, возникновением напряжений.
3. Первичная кристаллизация сплавов системы железо-углерод начинается по достижении температур, соответствующих линии ABCD (линии ликвидус), и заканчивается при температурах, образующих линию AHJECF (линию солидус).
При кристаллизации сплавов по линии АВ из жидкого раствора выделяются кристаллы твердого раствора углерода в α-железе (δ-раствор). Процесс кристаллизации сплавов с содержанием углерода до 0,1 % заканчивается по линии АН с образованием α (δ)-твердого раствора. На линии HJB протекает перитектическое превращение, в результате которого образуется твердый раствор углерода в γ-железе, т. е. аустенит. Процесс первичной кристаллизации сталей заканчивается по линии AHJE.
Структура эвтектических чугунов при температурах ниже 727ºС состоит из ледебурита превращенного. Заэвтектический чугун при температурах ниже 727ºС состоит из ледебурита превращенного и цементита первичного.
а) б)
Рисунок 6: а-диаграмма железо-цементит, б-кривая охлаждения для сплава, содержащего 0,8% углерода.
Правило фаз устанавливает зависимость между числом степеней свободы, числом компонентов и числом фаз и выражается уравнением:
C = K + 1 – Ф,
где С – число степеней свободы системы;
К – число компонентов, образующих систему;
1 – число внешних факторов (внешним фактором считаем только температуру, так как давление за исключением очень высокого мало влияет на фазовое равновесие сплавов в твердом и жидком состояниях);
Ф – число фаз, находящихся в равновесии.
Сплав железа с углеродом, содержащий 0,8%С, называется эвтектоидной сталью. Его структура при комнатной температуре – перлит.
4. Критические точки Ас1 и Ас3 для стали 15:
Ас1 = 735°С; Ас3 = 860°С.
Полный отжиг заключается в нагреве доэвтектоидной стали на 30-50°С выше температуры, соответствующей точке Ас3, выдержке при этой температуре для полного прогрева и завершения фазовых превращений в объеме металла и последующем медленном охлаждении. Температура полного отжига стали 15 составляет 890-910°С. После отжига сталь имеет низкую твердость и прочность при высокой пластичности. При фазовой перекристаллизации измельчается зерно и устраняется видманштеттова структура и строчечность, вызванная ликвацией, и другие неблагоприятные структуры стали. Структура после полного отжига: перлит и феррит.
5. Конструкционные стали подвергают закалке и отпуску для повышения прочности и твердости, получения высокой пластичности, вязкости и высокой износостойкости, а инструментальные - для повышения твердости и износостойкости.
Верхний предел температур нагрева для заэвтектоидных сталей ограничивается, так как приводит к росту зерна, что снижает прочность и сопротивление хрупкому разрушению.
Основными параметрами являются температура нагрева и скорость охлаждения. Продолжительность нагрева зависит от нагревательного устройства, по опытным данным на 1 мм сечения затрачивается: в электрической печи - 1,5…2 мин.; в пламенной печи - 1 мин.; в соляной ванне - 0,5 мин.; в свинцовой ванне - 0,1…0,15 мин.
Способы закалки:
В зависимости от формы изделия, марки стали и нужного комплекса свойств применяют различные способы охлаждения (рис. 7).
Рисунок 7 - Режимы закалки
1. Закалка в одном охладителе (V1).
Нагретую до нужной температуры деталь переносят в охладитель и полностью охлаждают. В качестве охлаждающей среды используют:
· воду - для крупных изделий из углеродистых сталей;
· масло - для небольших деталей простой формы из углеродистых сталей и изделий из легированных сталей.
Основной недостаток - значительные закалочные напряжения.
2. Закалка в двух сферах или прерывистая (V2).
Нагретое изделие предварительно охлаждают в более резком охладителе (вода) до температуры ~ 300°C и затем переносят в более мягкий охладитель (масло).
Прерывистая закалка обеспечивает максимальное приближение к оптимальному режиму охлаждения.
Применяется в основном для закалки инструментов.
Недостаток: сложность определения момента переноса изделия из одной среды в другую.
3. Ступенчатая закалка (V3).
Нагретое до требуемой температуры изделие помещают в охлаждающую среду, температура которой на 30 - 50oС выше точки МН и выдерживают в течении времени, необходимого для выравнивания температуры по всему сечению. Время изотермической выдержки не превышает периода устойчивости аустенита при заданной температуре.
В качестве охлаждающей среды используют расплавленные соли или металлы. После изотермической выдержки деталь охлаждают с невысокой скоростью.
Способ используется для мелких и средних изделий.
4. Изотермическая закалка (V4).
Отличается от ступенчатой закалки продолжительностью выдержки при температуре выше МН, в области промежуточного превращения. Изотермическая выдержка обеспечивает полное превращение переохлажденного аустенита в бейнит. При промежуточном превращении легированных сталей кроме бейнита в структуре сохраняется аустенит остаточный. Образовавшаяся структура характеризуется сочетанием высокой прочности, пластичности и вязкости. Вместе с этим снижается деформация из-за закалочных напряжений, уменьшаются и фазовые напряжения.
В качестве охлаждающей среды используют расплавленные соли и щелочи.
Применяются для легированных сталей.
5. Закалка с самоотпуском.
Нагретые изделия помещают в охлаждающую среду и выдерживают до неполного охлаждения. После извлечения изделия, его поверхностные слои повторно нагреваются за счет внутренней теплоты до требуемой температуры, то есть осуществляется самоотпуск. Применяется для изделий, которые должны сочетать высокую твердость на поверхности и высокую вязкость в сердцевине (инструменты ударного действия: молотки, зубила).
6. Наиболее распространены спиральные сверла, которые представляют собой круглый стальной стержень с двумя спиральными канавками по всей длине режущей части. Торец сверла заточен под углом и образует две конические поверхности, являющиеся двумя режущими кромками.
Для изготовления сверл применяют легированную и быстрорежущую стали. Сверлами из легированной стали обрабатывают детали из мягких материалов с небольшой скоростью, а из быстрорежущей стали обрабатывают детали с большой скоростью.
Процесс сверления отличается от других видов резания металла. При сверлении приходится просверливать отверстия в сплошном металле. Сверла должны обладать высокой твердостью, а при работе в тяжелых условиях с большой скоростью — теплостойкостью. Сверла работают нижней, заостренной частью, и поэтому рабочая часть должна быть твердой, а хвостовая часть— прочной и вязкой. Рабочую и хвостовую части сверла из легированной стали обрабатывают по различным режимам, а сверла из быстрорежущей стали изготовляют составными (сварными) рабочая часть — из быстрорежущей стали, а хвостовая— из углеродистой стали 45 или Стб.
Удобнее всего нагревать сверла в соляных ваннах; нагревается только нарезная часть сверла, которая после закалки должна иметь высокую твердость. Для удобства выполнения и ускорения операции закалки сверл применяют специальные приспособления (рис. 171).
Сверла из стали 9ХС с длинными хвостовиками сначала подвергают операции улучшения хвостовика. Для этого хвостовик нагревают до 840—860° С, охлаждают в масле и отпускают при 450—500° С. Закалку рабочей части сверл проводят в приспособлении погружением рабочей части сверла в соляную ванну. Температура нагрева 850—870° С. Сверла с расчетной толщиной более 20 мм предварительно подогревают при 600—650° С.
Для уменьшения коробления (от неравномерного охлаждения) сверла при охлаждении погружают в закалочную ванну в вертикальном положении. Сверла с расчетной толщиной до 20 мм охлаждают в соляной ванне с температурой 150—180° С и после выравнивания температуры охлаждают на воздухе. Более крупные сверла охлаждают в масле.
После закалки выборочно контролируют твердость и сверла промывают в подогретом щелочном или содовом растворе. Отпуск сверл проводят в масляных или соляных ваннах или в печах с принудительной циркуляцией воздуха. Температура отпуска 160—180° С.
После отпуска сверла промывают, правят и определяют их биение и твердость. Рабочая часть сверла должна иметь твердость HRC 61—64.
На некоторых заводах используют следующий вариант термической обработки сверл: закалка и отпуск рабочей части (по режиму для стали 9ХС), закалка хвостовика с помощью т. в. ч. при 820—870° С е самоотпуском (350—450° С) до твердости ИКС 35—50.
При нагреве сварных сверл из быстрорежущей стали применяют ступенчатый режим: сначала сверла подогревают до 600-650° С в первой соляной ванне, затем их переносят во вторую ванну, где подогревают до 800—850° С, и после двойного подогрева помещают в третью ванну для окончательного нагрева до температуры закалки (для стали Р18 1270—1290° С).
до 150—200° С, затем на воздухе. После закалки хвостовик отпускают в соляной ванне при 450—500° С. Затем контролируют биение и твердость сверл. Твердость рабочей части сверл диаметром до 5 мм должна быть HRC 62—64, при диаметре более 5 мм ИКС 62—65; твердость хвостовика HRC 30—45. После правильно проведенной термической обработки рабочая часть сверла должна иметь структуру мартенсита с равномерно распределенными мелкими и средней величины карбидами.
Для улучшения режущих свойств и повышения стойкости после окончательного шлифования сверла целесообразно подвергать цианированию при 550—570° С с последующей очисткой и дополнительным контролем хрупкости, глубины и твердости цианированного слоя.
На заводе Фрезер процесс термической обработки сверл из быстрорежущей стали осуществляется на автоматическом агрегате и состоит из следующих операций: 1) первый подогрев при 400—600° С в газовой шахтной печи; 2) второй подогрев при 830— 850° С в соляной электродной ванне; 3) нагрев в хлорбариевой ванне (для стали Р18 температура 1250—1290° С, для стали Р9 температура 1220—1250° С); 4) охлаждение в щелочной ванне (450—550° С); 5) подстуживание до 70° С с принудительным дутьем; 6) промывка в горячей проточной воде (температура воды не ниже 70° С); 7) травление и промывка в 10%-ном водном растворе соляной кислоты при 30° С (для уменьшения шероховатости поверхности сверл); 8) промывка в холодной проточной воде; 9) пассивирование при температуре не ниже 70° С (для повышения коррозионной стойкости)* Затем сверла поступают в другой агрегат, где подвергаются трехкратному отпуску при 560° С по 1 ч и очистке. При термической обработке сверл на автоматическом агрегате сокращается производственный цикл, повышается производительность труда, улучшается качество сверл.
7. Кулачки должны иметь минимальную деформацию и высокую износоустойчивость (твердость поверхностного слоя HV750-1000). Для изготовления их выбран сплав 38ХВФЮА.
Кулачок должен иметь высокую твердость и износоустойчивость, для его производства используем сталь 38ХВФЮА. Она относится к специальным сталям, подвергаемым азотированию. Эти стали содержат элементы, дающие нитриды высокой термической устойчивости (CrN, MoN, A1N).
Таблица 3. - Химический состав стали 38ХВФЮА:
C | Cr | W | V | Al | Mn |
0,36-0,43% | 0,8-1,1% | 0,2-0,4% | 0,1-0,2% | 0,7-1,1% | 0,3-0,6% |
Si | Mo | P | S | Cu | Ni |
0,2-0,45% | 0,15-0,25% | 0,025% | 0,025% | 0,3% | 0,3% |
Буква А в конце стали обозначает, что она высококачественная. Это характеризует низкое содержание вредных примесей фосфора и серы.
По назначению - сталь конструкционная легированная.
Азотируемая хромоалюминиевая сталь марки 38ХВФЮА (ГОСТ 4543-61), дополнительно легированная ванадием и вольфрамом, обладает усиленной прочностью и вязкостью сердцевины, а также высокой твердостью и износостойкостью после азотирования. Она прекрасно работает при динамических нагрузках и в условиях пониженных температур. Кроме того, сталь 38ХВФЮА слабо упрочняется при нагреве и может использоваться при температурах до 300-400 градусов.
Растворяясь в феррите, фосфор резко повышает температуру перехода в хрупкое состояние или иначе - вызывает хладноломкость стали.
Сера нерастворима в железе и любое её количество образует с железом сернистое соединение - сульфид железа FeS, который входит в состав сернистой эвтектики (FeS).
Она легкоплавкая, хрупкая и расположена по границам зёрен. Это делает сталь хрупкой при 800°C и выше, т. е., в районе температур красного каления. Явление это носит название красноломкости. Вследствие красноломкости сталь с повышенным содержанием серы не поддаётся горячей обработке давлением.
Термическая обработка стали:
· - закалка 850оС, охлаждение - масло;
· - отпуск 580оС, 5 ч, охлаждение - вода.
Температура критических точек стали 38ХВФЮА:
Ас1 = 650оС;
Ас3 = 805оС.
Технология процесса азотирования стали 38ХВФЮА.
Процесс азотирования стали 38ХВФЮА состоит из предварительной термической обработки заготовки (закалки и высокого отпуска), механической обработки деталей, защиты участков, не подлежащих азотированию и непосредственно операции азотирования.
1) Предварительная термическая обработка заготовки.
Эта операция состоит из закалки и высокого отпуска стали для получения повышенной прочности и вязкости в сердцевине изделия.
До термической обработки сталь имеет перлитную структуру.
Закалка - нагрев стали выше точки Ас3, выдержке и последующем охлаждении со скоростью, превышающей критическую. Для стали 38ХВФЮА температура нагрева будет 850оС. Учитывая, что критические точки Ас1=650°C, Ас3=805°C, после нагрева мы должны выдержать и охладить сталь. Охлаждение при закалке должно обеспечивать получение структуры мартенсита и не должно вызывать закалочных дефектов: трещин, деформаций, коробления и высоких растягивающих остаточных напряжений в поверхностных слоях. Для стали 38ХВФЮА охлаждение проводим в масле. Масло как закалочная среда имеет следующие преимущества: небольшую скорость охлаждения в мартенситном интервале температур, что уменьшает возникновение закалочных дефектов и постоянство закаливающей способности в широком интервале температур среды (20-150оС). К недостаткам следует отнести повышенную воспламеняемость, недостаточную стабильность и низкую охлаждающую способность в области температур перлитного превращения, а также повышенную стоимость.
Закалка не является окончательной операцией термической обработки. Чтобы уменьшить хрупкость и напряжения, вызванные закалкой, и получить требуемые механические свойства, сталь после закалки обязательно подвергают отпуску.
Целью отпуска является изменение строения и свойств закаленной стали: повышение вязкости и пластичности. Уменьшается твердость. Кроме того, при отпуске частично или полностью устраняются внутренние напряжения.
Для данной стали необходимо провести высокий отпуск при температуре 580°С, превышающей максимальную температуру последующего азотирования и обеспечивающей получение твердости, при которой сталь можно обрабатывать резанием.
При высоком отпуске в стали ускоряются диффузионные процессы, происходит выделение избыточных атомов углерода в виде цементита, т. е., мартенсит распадается на феррито-цементитную смесь. Полное выделение углерода из мартенсита обуславливает снятие внутренних напряжений, связанных со структурными превращениями при закалке. Получится структура, сочетающая достаточно высокую твёрдость и повышенную ударную вязкость, которые в данных условиях работы необходимы.
Также следует учесть, что исходная сталь склонна к отпускной хрупкости, поэтому охлаждение должно быть быстрым. Связано это с тем, что при высоком отпуске по границам зёрен происходит образование и выделение дисперсных включений карбидов. Пограничная зона обедняется легирующими элементами. При последующем медленном охлаждении происходит диффузия фосфора к границам зерна. Пограничные зоны обогащаются фосфором, снижается прочность и ударная вязкость. Этому дефекту способствует хром, марганец и фосфор. Если же сталь охладить быстро, то границы зёрен не успеют обогатиться фосфором и хрупкости стали наблюдаться не будет.
Таким образом, сталь 38ХВФЮА подвергли улучшению (термическая обработка, состоящая из закалки и высокого отпуска). В результате получили структуру сорбит.
· 2) Механическая обработка деталей, а также шлифование и доводка, которые придают окончательные размеры детали.
· 3) Защита участков, не подлежащих азотированию, нанесением тонкого слоя (0,01-0,015 мм.) олова электролитическим методом или жидкого стекла. Олово при температуре азотирования расплавляется на поверхности стали в виде тонкой не проницаемой для азота пленки.
· 4) Азотирование.
Азотированием называется химико-термическая обработка (ХТО), заключающеюся в диффузионном насыщении поверхностного слоя стали азотом при нагревании в соответствующей среде.
Так как в данном случае в задачу азотирования входит получение высокой твердости, то обычно температуру азотирования держат на уровне 500-520оС. Длительность процесса зависит от требуемой глубины. Кроме того, следует учесть, что чем ниже температура процесса, тем меньше деформация детали при азотировании (последнее также имеет большое значение, так как на азотирование поступают детали, окончательно изготовленные, после шлифования). Принимая во внимание влияние температуры процесса (рис. 2), можно заключить, что для получения детали с максимальной твердостью и минимальной деформацией следует применять низкую температуру азотирования для стали 38ХВФЮА (510°С), при которой глубина будет невелика (0,3-0,4 мм.). И в этом случае продолжительность процесса составляет 24-48 часов, а твёрдость слоя 850-950 HV.
Азотирование очень долгий процесс, поэтому для ускорения воспользуемся методом ступенчатых циклов, заключающийся в проведении процесса не при одной, а при нескольких температурах. Вначале азотирование проведем при 500-520°С, а затем температуру повышают до 540-560°С. При этом ускоряется процесс в 1,5-2 раза и это мало отражается на твердости, которая имеет почти такое же высокое значение, как при низкой температуре изотермического цикла.
5) Окончательное шлифование и доводка изделия.
Влияние легирующих элементов на механические свойства.
Mn существенно увеличивает прокол.
Si замедляет процесс разупрочнения при отпуске, увеличивает прокол, существенно улучшает механические свойства при закалке.
Ni существенно увеличивает прокол, повышает сопротивление хрупкому разрушению (сопротивлению отрыву), понижает температуру хладноломкости, повышает вязкость в направлении, поперечном по отношению к волокну, способствует мелко зернистости стали.
Сталь 38ХВФЮА относится к перлитному классу.
До термической обработки имеет ферритно-перлитную структуру.
После термической обработки получаем структуру сорбит.
В результате термической обработки получаем вязкую сердцевину и поверхностный слой высокой твердости и износоустойчивости, что полностью соответствует предъявляемым требованиям к свойствам стали 38ХВФЮА, которые определяются условиями эксплуатации кулачков и эксцентриков.
8. Для изготовления постоянных магнитов сечением 50х50 мм выбран сплав ЕХ: а) расшифруйте состав и укажите, к какой группе сплавов относится данный сплав но назначению; б) назначьте режим термической обработки, приведите его обоснование и опишите структуру и свойства сплава после обработки; в) объясните, почему в данном случае нельзя применить сталь У12. Сплав ЕХ ГОСТ 6862-71 относится к магнитотвердым сплавам. Его химический состав: углерод C – 0,95-1,10, хром Cr – 1,3-1,6. Для получения высоких магнитных свойств сплав подвергают сложной термической обработке, состоящей из предварительной нормализации (воздушной закалки), закалки с обычной температуры в воде или масле и низкого отпуска (желательно с предварительной обработкой холодом). Первая, высокая воздушная закалка (или нормализация), необходима для растворения крупных включений карбидных фаз, которые могли образоваться при предшествующем отжиге и которые при нормальном нагреве под закалку могут не растворяться в аустените, что не обеспечит получения высоких магнитных свойств. Обработка холодом устраняет парамагнитный остаточный аустенит и тем самым повышает магнитные свойства; отпуск при 100°С хотя немного и снижает коэрцитивную силу, но стабилизирует ее величину во времени. Режимы термообработки: воздушная закалка 1050°С+закалка в масле 840-860°С+отпуск 100°С. Свойства после обработки: остаточная индукция Br – 9500 Гс, коэрцитивная сила Hc – 60 Э. Применение Стали У12 в данном случае ограничивается габаритами магнита. Поскольку Сталь ЕХ содержит хром, она имеет более высокую прокаливаемость и в связи с этим возможно изготовление больших магнитов.
9. Б16 ГОСТ 1320-74
Б16 свинцовые баббиты - применяется для изготовления баббитов в чушках, применяемых для заливки подшипников и других деталей; температура заливки 480-500°C ; температура начала расплавления 240°C; характеристика нагрузки – спокойная.
Баббит — антифрикционный сплав на основе олова или свинца, предназначенный для использования в виде слоя, залитого или напыленного по корпусу вкладыша подшипника скольжения.
В целом баббиты нашли широкое применение для заливки подшипников и для приготовления мягких припоев. В состав баббитов могут входить следующие элементы: сурьма, медь, олово, свинец, никель, теллур, кальций, натрий, мышьяк, кадмий, алюминий, магний, кремний и др.
В зависимости от содержания основных элементов баббиты условно разделяют на следующие группы: высокооловянистый Б88, оловянистый Б16, малооловянистый Б6, никелевый БН, теллуристый БТ, кальциевый БК. Кроме этого, могут быть алюминиевые, цинковые и магниевые баббиты. Баббиты плавят в электрических или пламенных тигельных печах.
Температура плавления оловянистых и оловянносвинцовистых баббитов находится в интервале 445—480° С, кальциевого — в интервале 550—600° С. Температура сплавов во время заливки, как правило, на 50—100° С выше точки ликвидуса.
Плавка баббитов может производиться в одном или в двух тиглях одновременно. Плавка в одном тигле неизбежно приводит к более высокому перегреву сплава, а это нежелательно, в то время, как плавка баббитов в двух тиглях дает возможность избежать перегрева металла, а следовательно, уменьшить угар.
Исходными шихтовыми материалами для приготовления баббитов могут быть: чистые металлы, оборотные сплавы, приготовляемые из отходов, предварительные сплавы и лигатуры. В отдельных случаях используются соли, из которых восстанавливают необходимые в сплаве элементы.
При плавке необходимо контролировать температуру, особенно в случае наличия в них меди; в таких сплавах химическое соединение, богатое медью, плавится при более высокой температуре, чем основная масса сплава, и по внешнему виду расплава очень трудно судить о том, имеются ли еще в нем твердые кристаллы. Если сплав расплавлен не полностью, то происходит ликвация твердых кристаллов (по плотности), что приводит к изменению химического состава. Некоторые нерасплавленные частицы могут затем вырасти и образовать большие грубые кристаллы, которые обнаружатся в отливке в виде твердых включений и вызовут хрупкость ее.
Сплавы олова и свинца в жидком состоянии не поглощают газов. Они образуют мало окислов, но примеси цинка и алюминия способствуют увеличению окислов.
Химический состав в % материала Б16
ГОСТ 1320 - 74
Fe | Al | Cu | As | Pb | Zn | Sb | Bi | Sn |
до 0.1 | до 0.01 | 1.5 - 2 | до 0.3 | 63.34 - 68.5 | до 0.15 | 15 - 17 | до 0.1 | 15 - 17 |
Примечание: Pb - основа; процентное содержание Pb дано приблизительно
Литейно-технологические свойства материала Б16 .
Температура плавления : | 410 °C |
Температура заливки : | 480 - 500 °C |
Механические свойства при Т=20oС материала Б16 .
Сортамент | Размер | Напр. | s в | s T | d 5 | y | KCU | Термообр. |
- | мм | - | МПа | МПа | % | % | кДж / м2 | - |
, ГОСТ 1320-74 | 147 | 86 |
Твердость Б16 , ГОСТ 1320-74 | HB 10 -1 = 30 МПа |
Дата добавления: 2021-02-10; просмотров: 159; Мы поможем в написании вашей работы! |
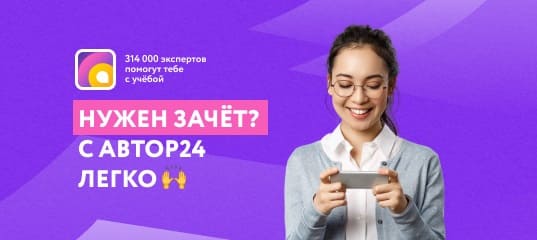
Мы поможем в написании ваших работ!