МАТЕРИАЛЫ РЕГУЛИРУЮЩИХ СИСТЕМ И ЗАЩИТЫ
КОНСТРУКЦИОННЫЕ МАТЕРИАЛЫ АКТИВНОЙ ЗОНЫ
БЕРИЛЛИЙ
Физические свойства. По совокупности физических свойств бериллий является одним из наиболее интересных и перспективных реакторных материалов. Он имеет малое сечение поглощения тепловых нейтронов (табл. 8.1). Сочетание малого сечения поглощения с высоким рассеянием и большим числом атомов в 1 см3 делает бериллий превосходным замедлителем и отражателем в реакторах; его применение приводит к уменьшению критической загрузки горючего.
Однако перспектива широкого применения бериллия ограничена рядом обстоятельств. Бериллий принадлежит к очень редким и дорогим металлам. Стоимость его почти в сто раз выше стоимости алюминия, магния, стали. Бериллий хрупок. Облучение вызывает охрупчивание и распухание. Изготовление из него тонкостенных оболочек твэлов и особенно их герметизация крайне затруднительны. Положительными свойствами бериллия являются малая плотность, относительно высокая температура плавления, небольшой коэффициент теплового расширения (см. табл. 8.1). До температуры 1513 К бериллий не претерпевает аллотропических превращений и кристаллизуется в ГПУ-решетке. Отсутствие структурных превращений в широком диапазоне температуры делает бериллий нечувствительным к циклическим изменениям температуры. Бериллий и его соединения очень токсичны. Металлический бериллий получают магниетермическим восстановлением окисла бериллия или электролизом.
|
|
Изделия из бериллия изготовляют на основе металлокерамической технологии. Из порошков горячим прессованием получают заготовки, из которых методами выдавливания, горячей прокатки, ротационной ковки изготовляют прутки, трубы, листы и другие профили.
Физические свойства бериллия | Таблица 81 |
Атомный номер | 4 |
Относительная атомная масса | ~9 |
Сечение поглощения тепловых | 9·10-31 |
нейтронов, м2 | |
Плотность, г/см3 | 1,85 |
Температура плавления, К | 1556 |
Коэффициент линейного расшире | 11,6·10-6 |
ния, град-1 | |
Температура кипения, К | 3243 |
Коэффициент теплопроводности, | 180 |
Вт/(м·К) | |
Кристаллическая структура | α-Фаза, ГПУ до 1513 К ß-Фаза, ОЦК выше 1513 К |
Параметр кристаллической решетки | а=0,228 |
α-фазы, нм | с =0,358 |
Механические характеристики. Механические свойства бериллия, особенно его пластичность, существенно зависят от температуры (рис. 8.1). Имеет место резкий спад пластичности при уменьшении температуры ниже 573—473 К — так называемый порог хладноломкости. Температура этого порога может быть смещена на 323—373 К к более низкой температуре в результате очистки бериллия от примесей и главным образом измельчения зерна. Однако никакими приемами не удается сдвинуть порог хладноломкости квазиизотропного поликристаллического бериллия ниже комнатной температуры, т. е. получить бериллий, пластичный при комнатной температуре. Длительным отжигом при температуре 1023—
|
|
1073 К и очень медленным охлаждением можно устранить падение пластичности при 873—1073 К. Указанная термическая обработка приводит к выделению интерметаллидов бериллия по границам зерен.
При выдавливании бериллия базисные плоскости гексагональной решетки ориентируются параллельно направлению выдавливания. Такая текстура вызывает резкую анизотропию свойств бериллия. Вдоль оси выдавливания пластичность бериллия возрастает, а в поперечном направлении падает. Ударным выдавливанием из литых заготовок можно изготовить трубки из бериллия. После рекристаллизационного отжига на мелкое зерно трубки имеют высокую продольную и достаточную (1—2%) поперечную пластичность. Легирование бериллия кальцием в количестве 0,4% несколько улучшает свойства труб. Вследствие низкой пластичности детали и узлы замедлителей и отражателей не рассчитаны на значительные нагрузки. Снижение пластичности бериллия при облучении не столь опасно.
|
|
Радиационная стойкость. В бериллии под действием облучения протекают ядерные реакции с образованием газообразных продуктов:
9Ве + п→ 4Не + 6Не; 6Не→ 6Li +ß-; 6Li + п →4Не + 3Н.
Гелий и тритий могут скапливаться в порах, образовывать газовые пузыри, вызывающие газовое распухание. Внедрение гелия и трития в кристаллическую решетку бериллия снижает его пластичность. Изменение свойств бериллия в результате облучения представлено в табл. 8.2. Облучение увеличивает прочность и ухудшает пластичность бериллия.
При флюенсе нейтронов 1020 см-2 и температуре облучения 973— 1023 К газовое распухание невелико и не превышает 1—2%. При тем-
Влияние облучения при 703 К на механические свойства бериллия (флюенс быстрых нейтронов 1021 см-2)
Температура испытания облученных и исходных образцов, К | σт | , МПа | δ,% | |
исходные | облученные | исходные | облученные | |
298 | 340 | 670 | 3 | 0 |
473 | 300 | 560 | 35 | 5 |
573 | 270 | 440 | 45 | 26 |
703 | 190 | 350 | 40 | 25 |
873 | 130 | 190 | 17 | 5 |
|
|
пературе 1073—1173 К газовое распухание составляет 3—5%. При указанном флюенсе нейтронов бериллий может применяться в отражателях и замедлителях до температуры 973—1073 К.
Совместимость. При наличии окисной пленки на уране и бериллии эти металлы совместимы до 873 К. При нарушении сплошности окисной пленки на бериллии он совместим с ураном до температуры 773 К. При 773 К бериллий несовместим с Fe, Ni, Zr и совместим с AI, Mg.
Коррозионная стойкость. Нормальный потенциал бериллия равен —1,85 В. Стационарный потенциал бериллия составляет—0,8 В. Это свидетельствует о способности бериллия пассивироваться. В нейтальных средах, не содержащих хлоридов и сульфатов, бериллий пассивируется в широком интервале потенциалов. В воде высокой чистоты бериллий стоек. Продукт коррозии — окись бериллия — белого цвета, очень рельефно выглядят на поверхности металла, в результате чего может создаваться впечатление, что бериллий подвергся интенсивной коррозии.
При движении воды продукт коррозии смывается с поверхности, и создается впечатление, что поток воды существенно увеличивает стойкость бериллия. В воде высокой чистоты бериллий стоек до температуры 423—473 К. При этой температуре на поверхности металла образуется темная окисная пленка. При 573 К стойкость бериллия снижается и существенно зависит от качества металла. При этом имеет место язвенная коррозия. Легирование бериллия железом несколько повышает его стойкость. При использовании бериллия при температуре воды 573—623 К ею очехловывают сплавами циркония. Присутствие в воде хлоридов и сульфатов, а также увеличение pH среды до 10—12 резко снижают стойкость бериллия. Контакт с алюминием практически не сказывается на стойкости бериллия, контакт с нержавеющей сталью несколько снижает ее. При циклическом изменении температуры в воде высокой чистоты бериллий подвергается коррозии под напряжением. Создание на поверхности бериллия окисных пленок методом анодирования увеличивает его стойкость.
При давлении в несколько десятков мегапаскалей бериллий стоек в сухом кислороде до 923 К, в водяном паре и влажном кислороде до 873 К, в углекислом газе до 973 К. При температуре 773 К бериллий стоек в натрии, содержащем до 0,01% О2. При 873 К бериллий стоек в литии и в эвтектике Pb—Bi.
Окись бериллия. Окись бериллия может применяться в качестве отражателя. Температура плавления ее велика, 2823 К. Окись бериллия — хороший изолятор. Как и у большинства керамических материалов, предел прочности при сжатии окиси бериллия в несколько раз больше, чем при растяжении. Относительно высокая теплопроводность способствует повышению ее термостойкости. Изделия из окиси бериллия изготовляют методом прессования, выдавливания, литья. Распиливание необожженной окиси бериллия осуществляется смоченными абразивными кругами, спеченной окиси бериллия — алмазными кругами. Окись бериллия стойка в воде при 573—623 К, не взаимодействует с воздухом, углекислым газом до температуры 773— 873 К. Недостаточно плотная окись бериллия при 873 К пропитывается натрием и разрушается. Под действием нейтронного облучения может иметь место газовое распухание и растрескивание окиси бериллия, обусловленное накоплением гелия и трития. Окись бериллия используют в исследовательских реакторах в качестве замедлителя и отражателя.
ГРАФИТ
Графит — одна из кристаллических модификаций углерода. Последний существует в виде двух стабильных изотопов с массовыми числами 12(98,892%) и 13(1,108%). В отечественном реакторостроении в основном используется графит марок МПГ и ГМЗ.
Физические свойства. Графит находит широкое применение в реакторах на тепловых нейтронах в качестве замедлителя и отражателя. Сечение поглощения тепловых нейтронов у графита меньше, чем у бериллия и магния (табл. 8.3). Получение графита реакторной чистоты не представляет больших технических трудностей. Графит обладает хорошими тепловыми свойствами и достаточной прочностью, хорошо
Таблица 8.3
Физические свойства графита
Атомный номер Относительная атомная масса Сечение поглощения тепловых нейтронов, м2 Плотность, г/см3 Температура плавления Коэффициент линейного расширения, град-1 Коэффициент теплопроводности, Вт/(м·К) Кристаллическая структура Параметр кристаллической решетки, нм | 6
12
4,5·10-31
1,65-1,75
Возгоняется при давлении 0,1 МПа и температуре ![]() |
поддается механической обработке. Благодаря высокой теплопроводности и низкому коэффициенту линейного расширения графит обладает хорошим сопротивлением тепловым ударам. Однако применению графита препятствуют его низкая стойкость к окислению и хрупкость. Кроме того, в результате облучения нейтронами кристаллическая решетка графита повреждается, что отражается на его физических свойствах.
Свойства графита существенно зависят от исходного материала и метода получения. Чистота графита в значительной степени зависит от чистоты исходных материалов. В реакторном графите содержание
золы не выше 0,054—0,16%, содержание бора 4·10-5 %. В случае газовой очистки эти значения могут быть снижены до 5·10-4 и 6·10-60% соответственно. При обработке графита газообразным хлором увеличивается содержание хлора в графите, что может привести к загрязнению хлором реакторного пространства в процессе эксплуатации. При высокой температуре графит не плавится, а возгоняется. До температуры возгонки кристаллическая решетка графита не изменяется.
Совершенные кристаллы графита состоят из параллельных атомных слоев (рис. 8.2). В каждом слое атомы графита образуют гексагональную сетку. Межатомное расстояние в слое равно 0,142 нм. Расстояние между слоями 0,335 нм. Слои смещены в собственной плоскости так, что над центром и под центром каждого из шестиугольников в прилегающих слоях находится атом графита. При этом любой шестиугольник в каждом третьем слое лежит над соответствующим шестиугольником в первом слое. Общепринятые параметры решетки графита приведены в табл. 8.3. Образование слоистой структуры происходит во время графитизирующего отжига при температуре ~ 3353 К. Кристаллические слои достаточно свободно перемещаются друг относительно друга. В связи с этим свойства графита существенно зависят от кристаллографического направления.
Теоретическая плотность графита равна 2,27 г/см3, плотность реакторного графита обычно лежит в пределах 1,65—1,75 г/см3. Такое различие обусловлено пористостью реакторного графита, составляющей 20 - 30%. Поры, как правило, сообщаются между собой, поэтому графит пропускает газ. Теплопроводность графита мало отличается от теплопроводности многих металлов. Распространение тепла в графите происходит главным образом вдоль базисных плоскостей, расположенных преимущественно параллельно оси выдавливания.
Механические характеристики. Механические свойства графита существенно зависят от кристаллографического напряжения. В плотноупакованных плоскостях атомы углерода связаны между собой сильными ковалентными связями, сами же плоскости связаны друг с другом относительно слабо.
В уран-графитовых реакторах из графитовых блоков сооружают кладку, через которую проходят каналы. Поэтому главное требование, которое предъявляется к графиту, состоит в том, чтобы он обладал достаточной прочностью на сжатие и мог выдерживать массу выше расположенных блоков графита. Так, предел прочности на сжатие (σB, МПа) графита, полученного по электродной технологии с мелкодисперсным наполнителем, следующим образом зависит от плотности (γ, г/см3): σB = 232 + 166γ. Предел прочности на растяжение при комнатной температуре колеблется от 7 до 21 МПа, при изгибе 7—30 МПа. Предел прочности на сжатие обычно составляет 21—35 МПа. При повышении температуры прочность графита возрастает. При температурах до 2273 К увеличение прочности происходит приблизительно по линейному закону. При температуре 3073 К прочность достигает максимального значения и примерно в два раза превышает прочность при комнатной температуре. Увеличение механической прочности с температурой связывается со снятием больших внутренних напряжений, возникающих в графите при охлаждении от температуры графитизации. Эти напряжения появляются вследствие большого различия в коэффициентах теплового расширения по направлению оси с и перпендикулярно к этой оси. Чем выше плотность графита, тем значительнее его прочность.
В области высоких температур изделия из графита деформируются под действием постоянных во времени напряжений, т. е. наблюдается явление ползучести. Скорость ползучести графита высока при температурах, близких к 2273 К. Однако в условиях облучения заметная деформация наблюдается и при более низких температурах. Для кратковременных испытаний при постоянной температуре скорость ползучести пропорциональна квадрату приложенного напряжения. Снятие напряжения приводит к частичному восстановлению длины образца. Так, после снятия нагрузки восстанавливается около 30% общей деформации, достигнутой в процессе испытаний при 2836 К.
Среда, в которой проводятся испытания, оказывает существенное влияние на полученные результаты. В частности, снижение давления аргона приводит к резкому возрастанию скорости ползучести. Скорость установившейся ползучести (v, см-1) можно оценить по следующей зависимости:
v = 40 (σ/σв)3,8 exp (— Q/RT),
где σ — растягивающее напряжение; σв — предел прочности; Q = 209 кДж/моль.
Окисление графита. При высоких температурах графит достаточно реакционноспособен. Однако с твердыми веществами графит совместим вплоть до высоких температур, когда наблюдается значительная диффузия углерода и науглероживание металлов и сплавов или возможны химические реакции восстановления углеродом. Проблемы совместимости графита сводятся к вопросам его взаимодействия с. теплоносителем. Скорость взаимодействия графита с газами обычно определяют по относительному изменению массы образцов. Влияние удельной поверхности, как правило, не учитывается, хотя известно, что она изменяется при окислении. Наиболее распространенными и перспективными газами для охлаждения реакторов являются гелий, азот, углекислый газ, воздух. Гелий не взаимодействует графитом даже в условиях облучения. При температуре ~ 2273 К может наблюдаться перенос массы графита потоком гелия в результате выкрашивания частиц графита. Такая эрозия обычно заканчивается после удаления частиц, имевших недостаточное сцепление с основным материалом. Примеси в гелии, например кислород, могут явиться причиной коррозии графита.
Коррозия графита представляет собой сложный физико-химический процесс, который может быть условно разделен на несколько этапов: 1) доставка окислителя к поверхности графита посредством молекулярной, конвективной диффузии; 2) адсорбция молекул окислителя на кристаллах графита; 3) взаимодействие адсорбированного окислителя с поверхностными атомами углерода на активных центрах с образованием комплекса Сx Oy; 4) расход комплекса Сx Oy с образованием СО н СO2 и удалением их в газовую среду.
При температурах ниже 773 К скорость коррозии определяется скоростью химической реакции. При свободном доступе кислорода к реакционной поверхности существенного влияния скорости газового потока не наблюдается. При Т >973 К скорость реакции горения графита начинает лимитироваться диффузией окислителя к реакционной поверхности. При этом скорость окисления графита К [г/(см2 ·с)] слабо зависит от температуры. Так, для графита марки ГМЗ при концентрации кислорода 0,1 % и расходе газа 3,8 л/ч получены следующие данные:
T, K 723 823 873 973 1073
Lg K -9,5 -8,5 -8,3 -8,08 -8,05
т, к | 723 | 823 | 873 | 973 | 1073 |
В диффузионной стадии продукты реакции (СO2, СО), накапливаясь у поверхности графита, вытесняют кислород. В связи с этим увеличение скорости движения газовой среды интенсифицирует доставку кислорода к поверхности и соответственно увеличивает скорость окисления графита. Это положение иллюстрируется данными, полученными при 1000 К и концентрации кислорода 0,005%:
Расход газа, л/ч 0,85 1,7 2,9
lg K -9,6 -9,3 -9,1
Расход газа, л/ | 0,85 | 1,7 | 2,9 |
При температуре 1073 К и расходе газа 3б8 л/ч зависимость скорости окисления графита марки ГМЗ от концентрации кислорода в газовой фазе (СО2, %) выражается следующим уравнением:
Скорость окисления графита уменьшается с ростом его плотности так же, как и с увеличением температуры термической обработки, интенсифицируют окисление графита примеси Fe, V, Na. В присутствии примесей окисления имеет локальный характер. С увеличением степени чистоты графита скорость его окисления снижается.
Графит с молекулярным азотом практически не взаимодействует. Основным продуктом взаимодействия графита с водородом при температурах 573—1273 К является метан. Равновесная концентрация метана в присутствии графита снижается с ростом температуры и при 1273 К и давлении 0,1 МПа близка к нулю. Облучение ионизирует водород и способствует образованию метана. Присутствие в реакторной среде паров воды интенсифицирует окисление графита. В ряде случаев для оценки стойкости графитовой кладки к окислению используют коэффициент выгорания, равный доле кислорода, взаимодействующего с углеродом при прохождении над поверхностью графита. В гелии с 0,22% объемного содержания О2 при площади графита 0,22 м2 и скорости газового потока 1,1 л/мин коэффициент выгорания при температурах 673 и 973 К составляет 0,1 и 0,8 соответственно.
При взаимодействии с СО2 протекает следующая реакция:
С + СО2 = 2СО.
Если концентрация СО в результате протекания какой-либо другой реакции превысит равновесную для рассматриваемой реакции, то вследствие интенсификации обратной реакции 2СО→С+СО2 произойдет отложение углерода. При 673—773 К процесс отложения графита незначителен.
Облученный при 323 К флюенсом нейтронов 5·1020 см-2 графит марки ГМЗ окисляется на воздухе при 873 К. в 7 раз интенсивнее, чем необлученный. Облучение при 573—623 К флюенсом 1,5·1021 см-2 не увеличивает скорости окисления. При температуре выше 1073 К предварительное облучение графита не влияет на скорость окисления. Это связывается с отжигом радиационных дефектов.
Облучение газовой среды вызывает ионизацию молекул, что также влияет на кинетику окисления графита. Этот эффект наблюдается при мощности дозы γ-излучения более 154,8 Кл/(кг·с). При этом скорость окисления возрастает в 2,6 раза.
Защита от окисления. Для защиты от окисления графитовой кладки реактора, работающей при температуре 973—1073 К, необходимо снижать объемное содержание кислорода в газовой среде до 0,05— 0,10%. Содержание Н20 при этом не должно превышать 1 %. Рекомендуется также периодически вводить в газ соединения, склонные к пиролизу: СО, СН4, светильный газ. При этом в результате пиролиза образуется защитный слой, препятствующий окислению.
В первую очередь реакция окисления протекает с участием атомов графита, имеющих повышенную энергию. Иными словами, вначале окислению подвергаются активные места в кристаллической решетке. Если активные места будут заняты, например в результате адсорбции на них атомов некоторых элементов, то эти места будут исключены из дальнейшего участия в реакции. В качестве веществ, которые можно вводить с этой целью в графит, предложены различные фосфорсодержащие соединения. Такие вещества после разложения при нагреве до определенной температуры оставляют атомы форсфора адсорбированными на активных местах решетки, что и снижает скорость окисления. Обычно для этой цели изделия из графита пропитывают фосфорсодержащим веществом и быстро обжигают при температуре 1073—1473 К в инертной атмосфере. В качестве фосфорсодержащих веществ используют как органические, так и неорганические вещества, например фосфорную кислоту, триметилфосфат и др. В результате такой обработки потери массы графита при окислении снижаются в 2—3 раза.
Для повышения стойкости графита к окислению могут быть использованы и смеси веществ, которые образуют сложные соединения типа фосфатных стекол. Для получения фосфатного стекла графитовые изделия после пропитки раствором, содержащим необходимые компоненты, обрабатывают при температуре образования стекла. Пленка из фосфатного стекла хорошо защищает от окисления графит в интервале температур 773—1223 К. Скорость окисления при этом снижается почти на два порядка. В условиях облучения защита от окисления фосфатными покрытиями неэффективна. По-видимому, это связано с повышением активности газа-окислителя при облучении, в результате чего он может взаимодействовать с атомами углерода, находящимися не только в активных местах. После прекращения воздействия облучения фосфатные покрытия вновь предохраняют графит от окисления, что указывает на сохранение покрытия в условиях облучения.
Графит практически не взаимодействует с эвтектикой Pb—Bi при температуре до 973 К. При использовании жидкого натрия в качестве теплоносителя с графитовым замедлителем возникают две проблемы: перенос массы углерода и проникновение натрия в поры графита.
Натрий при взаимодействии с графитом образует соединение со слоистой структурой. Натрий, по-видимому, располагается в пространстве между плотноупакованными слоями, причем занятым оказывается каждое восьмое межплоскостное пространство. Среднее расстояние между плотноупакованными плоскостями увеличивается на 5%, что вызывает расширение и растрескивание графита. Из-за переноса углерода натрием может происходить науглероживание аустенитной нержавеющей стали или осаждение углерода из теплоносителя в более холодных частях системы. Если графит не обработан соответствующим образом или на его поверхности не создано покрытие, препятствующее проникновению натрия, то последний должен отделяться от графита металлической оболочкой, например из сплава циркония. При этом следует учитывать образование газов в очехлованных блоках графита.
Радиационная стойкость. Облучение графита частицами высокой энергии приводит к изменению его физико-механических характеристик и размеров, что связано с деформацией кристаллической решетки графита. Под влиянием облучения происходит образование вакансий и смещенных атомов. Смещенные атомы образуют комплексы по 3—6 атомов каждый. Образуются также дислокационные петли. Это приводит к увеличению размера элементарной ячейки графита в направлении с и уменьшению параметра решетки а пропорционально флюенсу облучения. Увеличение постоянной решетки по оси с при облучении графита связано с внедрением смещенных атомов или их комплексов в межслоевое пространство графита. Сжатие решетки по оси а вызвано, вероятно, ее релаксацией на вакансиях. Повышение температуры облучения устраняет радиационные дефекты — рекомбинацию пар вакансия — смещенный атом, что приводит к уменьшению деформации кристаллической решетки графита. Так, при флюенсе нейтронов 2·1020 см-2 при увеличении температуры облучения с 333 до 573 К относительное удлинение по оси с уменьшается в 50 раз. При низкой температуре относительное изменение параметра с при облучении не превышает 15%.
Основным следствием деформации кристаллической решетки графита при облучении является изменение его макроразмеров. В поликристаллических графитовых стержнях, полученных методом выдавливания с последующим спеканием, обычно ось с преимущественно устанавливается в радиальном направлении, ось а—в продольном. Изменение параметров кристаллической решетки при облучении приводит к анизотропному изменению размеров графитовых изделий. Макроскопическое распухание не полностью соответствует увеличению кристаллической решетки графита, так как кристаллографическое расширение частично компенсируется заполнением существующих пор. С повышением температуры до 673—773 К и выше процесс заполнения пор и дополнительного спекания превосходит рост кристаллической ячейки и приводит к сжатию поликристаллического графита. Влияние температуры облучения можно наблюдать по относительному значению распухания графитовых кирпичей по высоте кладки реактора (рис. 8.3). Несмотря на то, что плотность нейтронного потока наибольшая на середине высоты кладки, распухание здесь наименьшее вследствие более высокой температуры. Максимум роста наблюдается на входной, более холодной стороне кладки. Другая особенность — неравномерное накопление радиационных нарушений в толще графита. Максимальные нарушения имеют место со стороны, примыкающей к источнику быстрых нейтронов — делящемуся урану. В прилегающих к твэлу слоях графита коэффициент теплопроводности уменьшается в 40 раз.
Облучение увеличивает ползучесть графита. В отсутствие облучения ползучесть графита не наблюдается при температуре ниже 423— 473 К. При облучении флюенсом нейтронов 1020 см-2 и температуре 353 К ползучесть при напряжении 10 МПа составляет 0,7—0,8%. Облучение снижает тепло- и электропроводность графита.
Энергия Вигнера. В результате нарушений кристаллической решетки в процессе облучения в графите накапливается скрытая энергия — энергия Вигнера (существование этого явления было предсказано Вигиером). Эта энергия может выделяться в виде тепла при нагреве графита до температуры, которая превышает температуру облучения. В этом случае имеет место повышение температуры в процессе отжига графита, облученного при низкой температуре. Отжиг графита в низкотемпературных реакторах осуществляется для снятия радиационных повреждении, так как, например, деформация графитовой кладки или втулок может затруднить эксплуатацию реактора. Радиационные повреждения можно отжечь простым нагревом. Существует несколько способов проведения такого отжига:
1)изменение циркуляции теплоносителя, с тем чтобы в определенных пределах повысить температуру графита;
2)увеличение температуры графита путем ядерного или электрического нагрева до тех пор, пока не начнется самостоятельное выделение энергии, которое постепенно распространяется на весь замедлитель;
3)медленное нагревание с удалением некоторой части выделяющейся энергии, чтобы избежать ее самопроизвольного выделения. При этом следует иметь в виду, что если нагрев при 373—473 К производится быстро и выделяющаяся тепловая энергия не успевает отводиться, то может произойти значительный перегрев кладки.
Радиационное повреждение кристаллической решетки графита приводит к изменению его механических характеристик. С увеличением флюенса нейтронов пределы прочности на сжатие и изгиб проходят через максимум, увеличиваясь по сравнению с исходным значением при флюенсе 1020 см-2 в 3—3,5 раза, а при 2· 1020—1021 см-2 в 2—2,2 раза. Экстремальное увеличение механических характеристик при малых флюенсах связано с блокированием дислокаций, вектор Бюргерса которых расположен в плоскости базиса. Это затрудняет смещение отдельных частей кристаллита друг относительно друга. Причиной блокировки дислокаций являются, вероятно, дефекты небольшого размера. Чем выше температура облучения, тем в меньшей степени возрастает прочность графита при равном флюенсе нейтронов. Предполагается, что при более высокой температуре происходит рекомбинация части вакансий и образование комплексов атомов внедрения. Оба эти фактора снижают вероятность блокировки дислокации, что и приводит к снижению прочности графита.
МАТЕРИАЛЫ РЕГУЛИРУЮЩИХ СИСТЕМ И ЗАЩИТЫ
К элементам с высоким сечением захвата могут быть отнесены Gd, Sm, Еu, В, Cd, Dy, lr, Hg, In, Er, Rh, Tm, Lu, Hf, Au, Re, Ag. Для практического применения в системах регулирования энергетических реакторов пригодны далеко не все эти элементы. Кадмий обладает плохими механическими характеристиками; Au, Re, Rh и Ir слишком дороги. Ртуть — жидкость, применение ее в системе регулирования связано с рядом трудностей. Гафний может быть применен в элементарном виде, серебро для получения лучшей комбинации физических и механических свойств используется в виде сплава с инием и кадмием. Остальные элементы используются в виде окислов или смеси окислов, обычно диспергированных в металлической матрице. Бор применяется в виде карбида в металлической или керамической матрице, а также в качестве легирующего элемента для введения в нержавеющую сталь, цирконий, титан. В большинстве случаев материалы регулирующих стержней могут работать в активной зоне только в оболочках. Гафний, нержавеющая сталь, легированная бором, могут использоваться без защитных покрытий. В настоящее время материалами для регулирующих стержней чаще всего служат бор в виде карбидов и сплавов, легированная бором сталь, гафний, сплав серебра с индием и кадмием, окислы редкоземельных элементов, диспергированных в металлических матрицах.
Соединения бора. Из соединений бора наиболее часто применяют карбид бора В4С. Это тугоплавкий материал с теоретической плотностью 2,51 г/см3. Реальная плотность обычно 2,4 г/см3. Карбид бора хрупок, но обладает высокой термостойкостью. В случае разрушения оболочки скорость растворения карбида в воде невелика. Искажения кристаллической решетки' карбида в результате нейтронного облучения частично отжигаются при температуре 973—1173 К. Нарушение кристаллической решетки происходит также из-за внедрения в нее атомов гелия, которые образуются в результате ядерной реакции
10B + п →7Li + 4Не.
Скопление гелия в порах при высокой температуре приводит к локальному увеличению давления в газовой полости, возникновению местных напряжений и трещин. Другим продуктом рассматриваемой ядерной реакции является литий. Присутствие лития в борсодержащем материале ухудшает его коррозионные свойства, так как он активно реагирует с водой.
При введении в легированную сталь бора количество его не должно превышать 3%. При более высоком содержании бора стали становятся крайне хрупкими и плохо обрабатываются. Так, введение в состав сталей 2% бора уменьшает относительное удлинение в ~ 10 раз. Накопление гелия при облучении нейтронами может привести к растрескиванию стали, легированной бором. До 90% выгорания бора нержавеющая сталь имеет хорошую коррозионную и радиационную стойкость и может применяться без защитного покрытия. Несколько меньшая коррозионная стойкость у сплавов титана, легированных бором до 1,7%. Сплавы же циркония, легированные 2% бора, нестойки в воде при 573—633 К. Легирование бором снижает пластичность титана и циркония. Облучение усиливает этот эффект.
Наряду со сплавами для изготовления регулирующих стержней широко используют дисперсионные материалы. К ним относятся бораль — карбид бора, диспергированный в алюминии, а также в нержавеющей стали, титане, цирконии. Дисперсионные материалы по сравнению со сплавами обладают лучшей радиационной стойкостью.
Гафний. Гафний и его сплавы можно применять в регулирующих стержнях без защитных оболочек. По коррозионной стойкости гафний превосходит цирконий. Гафний более пластичен, чем цирконий, и превосходит его по прочности. Гафний целесообразно применять для поглощения надтепловых нейтронов. Сечение поглощения тепловых нейтронов сравнительно невелико. Вследствие этого для поглощения значительного количества нейтронов требуются относительно массивные стержни.
Сплавы серебра. В качестве поглощающего материала можно применять сплав серебра с 15% In и 5% Cd. Как нейтронный поглотитель этот сплав сравним с гафнием и превосходит сплав Ag — 30% Cd. При поглощении нейтронов серебро превращается в кадмий, небольшая часть кадмия — в индий, а индий — в олово. Таким образом, после длительного облучения состав сплава изменяется. Рассматриваемый сплав стоек в воде с pH = 9÷10,5 при температуре 538 К. Контактной коррозии этого сплава в паре с нержавеющей сталью не наблюдается. После облучения флюенсом нейтронов 1,4·1021 см-2 изменения размеров образцов и изменения структуры не наблюдалось.
Редкоземельные элементы. Редкоземельный элемент европий целесообразно применять для изготовления регулирующих стержней, эффективность которых не должна меняться в течение длительного времени. Нуклиды, образующиеся при захвате нейтронов в таком стержпе, имеют большое сечение захвата. В связи с этим стержни, содержащие европий, будут эффективны длительное время. Однако необходимо отметить, что европий крайне дорог.
Гадолиний может быть введен в качестве легирующего элемента в нержавеющую сталь, сплавы титана. Такие сплавы с содержанием гадолиния до 25% обладают высокой коррозионной стойкостью в воде до 633 К. Твердость и хрупкость нержавеющих сталей с гадолинием возрастают с увеличением содержания последнего. Коррозионная стойкость сплавов титана снижается по мере увеличения концентрации редкоземельных элементов.
Из экономических соображений целесообразно применять редкоземельные элементы не в виде металлов, а в виде более дешевых окислов. Наиболее низкую стоимость имеет смесь окислов ряда редкоземельных элементов. Стержни из окислов редкоземельных элементов изготовляют методом порошковой металлургии: прессовкой с последущим cпеканием. Стержни из окислов редкоземельных элементов применяют обычно в оболочке из нержавеющей стали.
Окислы редкоземельных элементов могут быть диспергированы в матрице из нержавеющей стали. Наряду с окислами в регулирующих стержнях можно применять бориды редкоземельных элементов. Эти соединения инертны и имеют высокую твердость.
Выгорающие поглотители. Материалы с высоким сечением захвата нейтронов применяют не только для регулирования мощности, но и в качестве выгорающих поглотителей. Последние могут вводиться в активную зону на все время работы реактора. В процессе работы реактора расходуется ядерное горючее и уменьшается количество ядер поглотителя в результате ядерных реакций, идущих при поглощении нейтронов. Одновременно протекают два процесса: снижение общего уровня реактивности вследствие выгорания ядерного горючего и высвобождение добавочной реактивности, скомпенсированной в начале избыточным количеством поглотителя. При определенной скорости выгорания поглотителя реактор будет критичен при длительной эксплуатации активной зоны. При этом меньшую долю реактивности необходимо компенсировать регулирующими стержнями. В большинстве случаев в качестве выгорающего поглотителя применяют 10В. Соединения его диспергируются в алюминии, нержавеющей стали, графите и т. п. Кроме бора в качестве выгорающих поглотителей могут быть использованы Hf, Eu, Gd, Sm, Cd, Hg. Выгорающий поглотитель гомогенно смешивается с ядерным горючим. В этом случае, однако, может произойти нежелательное изменение ядерного топлива и будет затруднена последующая регенерация его.
Материалы защиты. Ядерный реактор является источником нейтронного, α-, ß- и γ-излучений. В связи с этим необходимо принимать меры к защите от облучения обслуживающего персонала. Для осуществления защиты реактор должен быть экранирован материалами, способными поглощать энергию излучения. Защита от α- и ß-излучений не представляет трудностей. Длины пробега этих частиц в твердых телах и в воздухе столь невелики, что специальной защиты от этих видов излучения не требуется. Иначе обстоит дело с нейтронным и γ - излучениями, так как они обладают большим проникающим действием. Способность материалов поглощать нейтроны существенно зависит от энергии нейтронов. Для поглощения нейтронов их энергия должна быть снижена по сравнению с исходным значением энергии нейтронов, освободившихся в процессе деления ядерного горючего.
Система защиты реактора должна удовлетворять следующим требованиям:
1)снижать энергию нейтронов до тепловой;
2)поглощать замедленные нейтроны (если толщина защитного слоя минимальная, то материалы защиты должны обладать значительным сечением поглощения тепловых нейтронов);
3)эффективно поглощать проникающее γ-излучение.
При выборе материала для защиты необходимо учитывать не только их физические характеристики, но и экономические показатели и технологичность материалов; для эффективного поглощения γ-излучения целесообразно применять тяжелые металлы.
Таким образом, защита реактора должна обеспечить: снижение энергии нейтронов, поглощение нейтронного и γ-излучений. Снижение энергии нейтронов — это замедление их. Характеристики материалов замедлителей были рассмотрены ранее. Любые материалы, являющиеся эффективными замедлителями нейтронов, с теоретической точки зрения пригодны к использованию в системе защиты реактора. При решении конкретных вопросов необходимо учитывать не только физические, но и другие характеристики материалов.
Благодаря высокой замедляющей способности, удобству применения в системе защиты и низкой стоимости водород следует считать особенно подходящим компонентом материалов, используемых в системе защиты. В реакторах бассейнового типа вода выполняет одновременно функции замедлителя и защиты. На ряде энергетических реакторов создают баки водяной защиты. Однако в ряде случаев применение воды в качестве материала для защиты реакторов ограничено, так как толщина требуемого слоя воды должна быть значительной, а это сказывается на общих размерах реактора. Увеличение мощности реактора связано с повышением температуры воды в системе водяной защиты. По этим причинам и ряду других соображений вместо воды в системах защиты иногда целесообразно применять другие материалы, содержащие водород (гидриды, углеводороды). Вопрос о применении в системе защиты этих материалов, а также бериллия, графита должен решаться с учетом их экономических, технологических характеристик и радиационной стойкости. Характеристики материалов с высоким сечением поглощения тепловых нейтронов рассматривались выше. Наиболее часто для этих целей в системах защиты применяют композиции, содержащие бор, в частности стали перлитного класса, легированные бором. При содержании бора 1—2% из таких сталей прокаткой могут быть изготовлены листы. При более высоком содержании бора стали становятся нетехнологичными. Прокатка их затруднена, а зачастую и невозможна.
В системе защиты от нейтронного облучения применяют бораль. Этот материал представляет собой металлокерамическую композицию, состоящую из мелкодисперсных частиц карбида бора, распределенных в основе из алюминия. Листы бораля толщиной 6 мм с каждой стороны плакируют (покрывают) слоем алюминия толщиной около 0,5 мм.
Тепловая защита предназначена в основном для уменьшения возможности попадания тепловых нейтронов в биологическую защиту. Энергия, выделяемая при поглощении этих нейтронов, вызывает нагрев материала тепловой защиты. В связи с этим необходимо подбирать материалы с соответствующими свойствами и охлаждать тепловую защиту. Обычно тепловую защиту изготовляют из чугуна, легированного 14% Ni, 5%Cu и 1—4% Сr для предотвращения роста чугуна при нагреве. Причиной роста серого чугуна является выделение в нем свободного углерода при распаде карбида железа. Для этих же целей можно применять не склонную к росту малоуглеродистую сталь. Однако получение из нее крупных отливок сложно. Более целесообразно собирать тепловую защиту из отдельных поковок, размеры которых определяются экономической целесообразностью. Обычно борсодержащие композиции и стали применяют в защите реакторов, где существенное значение имеют размер и масса защиты.
Если масса и размер защиты не являются лимитирующими факторами, в качестве основного материала защиты используют цемент и бетон. Такие решения осуществлены на большинстве энергетических и исследовательских реакторов. Стоимость бетонной защиты будет определяться не только стоимостью цемента и заполнителей, но и способом изготовления защиты, наличием и расположением в ней отверстий и т. п. Степень ослабления интенсивности флюенса нейтронов системой биологической защиты в большой степени зависит от содержания воды в материале защиты, которое, в свою очередь, определяется в основном типом используемого бетона и способом его изготовления. Поглощение нейтронов бетонной защитой может быть значительно увеличено введением бора в состав материала защиты. Для изготовления систем защиты применяют цементы, содержащие ~ 1 % В. Стоимость бетона при этом возрастает в 2—3 раза. Способность слоя бетонной защиты поглощать 7-излучение зависит от плотности материала защиты. В зависимости от состава цемента и заполнителя плотность бетона составляет 2,4—6,6 г/см3. Наименьшая плотность получается при использовании в качестве заполнителя песка и гравия, наибольшая — при использовании стальных шариков, кусков стальной проволоки, обрезков стального лома. В последнем случае стоимость бетона в 40—50 раз выше, чем при применении песка и гравия.
Конструкция бетонной защиты в зависимости от назначения может быть монолитной или же состоять из отдельных заранее изготовленных блоков. Монолитные конструкции защиты применяют для больших реакторов. Блочная конструкция целесообразна для небольших исследовательских реакторов, где необходим свободный доступ к активной зоне и которые менее опасны как источники излучения.
При монолитной конструкции бетонной защиты реактора стоимость ее возрастает вследствие применения каркасов. При укладке бетона необходимо принимать меры для равномерного распределения заполнителя с большой плотностью, например стальных шариков.
При изготовлении защиты из отдельных блоков особое внимание следует обращать на участки стыковки между блоками, чтобы обеспечить защиту от излучения. Если конструкция реактора допускает применение защиты большой толщины из бетона, воды и других неметаллических материалов, то эти материалы можно использовать одновременно для защиты от нейтронного и 7-излучений. Если размеры и масса защиты ограничены, то для поглощения γ-излучения целесообразно применять тяжелые металлы. Наиболее экономичным материалом, эффективно поглощающим γ-излучение с высокой энергией, является свинец. Применение свинца ограничивается его низкой температурой плавления. Если материал защиты нагревается до высокой температуры, вместо свинца необходимо применять вольфрам, тантал. Эти металлы крайне дороги и применение их для защиты промышленных реакторов нецелесообразно.
МАГНИЙ И ЕГО СПЛАВЫ
Физические свойства. Весьма интересными материалами для оболочек твэлов являются магний и его сплавы. Магний дешев и доступен. Недостатками магния как материала оболочек и других деталей активной зоны являются его малая коррозионная стойкость, склонность к самовоспламенению, низкая температура плавления и низкие механические свойства при повышенной температуре. Несмотря на это, магниевые сплавы широко применяют в качестве материала оболочек в двухцелевых реакторах с графитовым или тяжеловодным замедлителем, природным ураном в качестве горючего и углекислым газом в качестве теплоносителя, например в английских реакторах в Колдер-Холле, Брадуэлле и др., а также в ряде французских реакторов при температуре углекислого газа 623—673 К.
По сечению захвата тепловых нейтронов магний уступает лишь бериллию. Физические свойства магния представлены в табл. 8.4, а состав ряда магниевых сплавов для оболочек — в табл. 8.5.
Природный магний состоит из следующих изотопов: 78,8% 24Mg; 10,14% 25Mg; 11,06% 26Mg. При нейтронном облучении активируется только 26Mg. В результате протекания реакции (п,γ) образуется 27Mg с периодом полураспада 9,46 мин. Магний и его сплавы используют при изготовлении оболочек твэлов для уран-графитовых и тяжеловодных реакторов, в которых топливом служит природный уран и теплоносителем — углекислый газ. В Великобритании магниевые сплавы применены в реакторах Колдер-Холла, «Беркли» и др. Твэлы с обо-
Физические свойства магния | Таблица 8.4 |
Атомный номер | 12 |
Относительная атомная масса | 24,32 |
Сечение поглощения тепловых нейтронов, м2 | 5,9·10-30 |
Плотность, г/см3 | 1,74 |
Температура плавления, К | 924 |
Температура кипения, К | 1393 |
Коэффициент линейного расширения, град-1 | 26·10-6 |
Коэффициент теплопроводности, Вт/(м·К) | 158,3 |
Кристаллическая структура | ГПУ |
Параметр кристаллической решетки, нм | α = 0,32 |
c= 0,52 | |
Магниевые сплавы |
|
|
|
|
|
Таблица 8.5 | |||||||||||||
Сплав | Массовое содержание легирующих элементов и примесей, % | ||||||||||||||||||
|
|
|
|
|
| ||||||||||||||
Be | Si | А1 | Th | Fe | Mn | Ni | Cu | MgO | Ca | Zr | |||||||||
СССР: |
|
|
|
|
|
| |||||||||||||
11МБ | 0,5-3,2 | — | 0,04 | — | 0,04 | — | 0,001 | 0,005 | 0,2- | — | — | ||||||||
|
|
|
|
| 0,3 |
| |||||||||||||
МБ-3 | 0,04 | 0,5 | — | — | 0,01 | 0,001 | 0,001 | 0,005 | — | — | — | ||||||||
МБ-4 | 0,08-0,15 | 0,7 | — | — | 0,01 | 0,001 | 0,001 | 0,005 | — | — | — | ||||||||
Mg —А]-Ве | 0,04 | — | 0,5 | — | 0,01 | 0,001 | 0,001 | 0,005 | — | — | — | ||||||||
Mg—Th—Be | 0,04 | — | — | 3 | 0,01 | 0,001 | 0,001 | 0,005 | — | — | — | ||||||||
Mg—Ca — Zr —Be | 0,04 | — | — | — | 0,01 | 0,001 | 0,001 | 0,005 | — | 0,5 | 0,5 | ||||||||
Великобритания: |
|
|
|
|
|
| |||||||||||||
Маг цоке AL-80 | 0,01 | — | 0,8 |
|
|
|
|
|
| ||||||||||
ZA(+Be) | 0,01 |
|
|
|
|
| 0,55 | ||||||||||||
Магэан-2 | — | — | — | — | — | 0,15 | — | — | — | — | 0,55 | ||||||||
Матвеи-4 | — | — | — | — | — | 0.4 | — | — | — | — | 0,60 | ||||||||
AM 503 (S) | — | — | — | — | — | 0,7 | — | — | — | — | — | ||||||||
AM 503 | — | — | — | — | — | 1,4 | — | — | — | — | — | ||||||||
|
|
|
|
|
| ||||||||||||||
ломкой из магний-бериллиевого сплава используются в Чехословацкой АЭС А-1, созданной по совместному советско-чехословацкому проекту и усилиями специалистов и промышленности обеих стран. Температура теплоносителя СО2 в активной зоне реакторов 623— 723 К.
В твэлах с оболочкой из сплавов Mg механическую прочность обеспечивает урановый металлический сердечник. Оболочка предохраняет сердечник от коррозионного воздействия теплоносителя. Основным требованием, предъявляемым к магниевым сплавам, кроме высокой коррозионной стойкости является не столько жаропрочность (сопротивление ползучести и разрушению), сколько достаточная пластичность, препятствующая разгерметизации оболочек твэлов при деформации уранового сердечника.
Механические характеристики. Чистый магний малопластичен при температуре ниже 373 К. Относительное удлинение составляет 5— 10% и значительно колеблется в зависимости от размера зерна и текстуры. При выдержке в течение 100—200 ч при температуре 670— 720 К размер зерна в чистом магни увеличивается в сотни и тысячи раз. Это обусловливает дальнейшее снижение пластичности при комнатной температуре до относительного удлинения 2—4%.
Измельчение и стабилизация зерна в магнии могут быть достигнуты легированием его Zr, А1, Ми, Th. Так, введение в магний 0,55% Zr увеличивает относительное удлинение в 2,5—3 раза. При этом происходит и упрочнение магния. Механические характеристики советских магниевых сплавов представлены в табл. 8.6.
Ряд магниевых сплавов получают из порошков методами металлокерамики. В этом случае в сплаве присутствуют окислы. Такие материалы (ПМБ-2 и ПМБ-5, см. табл. 8.6) менее пластичны, чем литые и деформированные, но обладают повышенной прочностью и жаропрочностью.
Механические свойства Mg и сплавов Mg — Be при различной температуре, К | Таблица 8.6
| |||||||
σB, МПа | σT,Ма | δ , % | ||||||
Материал | ||||||||
293 | 573 | 773 | 2ВЗ | 573 | 293 | 573 | 773 | |
Магний | 180 | 18 | 4 | 90 | 14 | 9 | 52 | 78 |
МБ-4 | 220 | 38 | 9 | 150 | 19 | 6 | 48 | 82 |
МБ-3 | 200 | 29 | 8 | 130 | 17 | 8 | 58 | 90 |
ПМБ-2 | 260 | 80 | 28 | 190 | 48 | 5 | 16 | 52 |
ПМБ-5 | 240 | 75 | 30 | 190 | 50 | 5 | 15 | 49 |
При деформации и пластическом течении в магнии и его сплавах образуются крупные поры, полости по границам зерен. Это снижает пластичность сплавов, создает опасность газового распухания. В сплавах, применяемых в реакторостроении, это явление практически устранено и при рабочей температуре 673—773 К оболочки из этих сплавов обладают достаточной устойчивостью.
Радиационная стойкость. Температура рекристаллизации магния невелика. В связи с этим облучение не должно существенно изменять механические свойства магния и его сплавов. Так, при облучении флюенсом нейтронов 1018 см-2 при температуре 318 К. пределы Прочности и текучести сплава, легированного цирконием, возрастают соответственно на 0—11 и 2—18%, а относительное удлинение уменьшается на 10—35%. Более высокие флюенсы должны существеннее повлиять на пластичпость сплавов магния. Следует, однако, иметь в виду, что в газоохлаждаемом реакторе детали и узлы из магниевых сплавов будут иметь температуру не ниже 423—473 К. При этой температуре пластичность сплавов магния достаточно велика и радиационные повреждения не снижат ее до опасного предела.
Совместимость. Магний, совместимый с ураном до температуры 773 К, восстанавливает окислы почти всех металлов. В связи с этим взаимная диффузия металлов будет зависеть от проницаемости окисла магния. Малые количества легирующих элементов практически не сказываются на проницаемости окиси магния и совместимости его с другими металлами. До температуры 720—850 К магний и его сплавы не взаимодействуют со сплавами Zr, Сr, Ti, Ni, Pt. С алюминием магний взаимодействует при температуре выше 673 К.
Низколегированные перлитные стали не взаимодействуют с расплавленным магнием.
Коррозионная стойкость. В сухом углекислом газе при давлении до 5 МПа и температуре 853 К устойчивы сплавы, легированные 2% Be. При температуре до 793 К стойки сплавы типа магнокс. Коррозия идет по параболическому закону. Присутствие водяных паров интенсифицирует окисление. При 773 К и давлении 1,4 МПа сплавы типа магнокс устойчивы в углекислом газе, загрязненном до 1 % СО и до 0,03% водой. Увеличение содержания воды до 2% не вызывает катастрофической коррозии, так же как и увеличение содержания воздуха до 50%, С ростом давления углекислого газа скорость коррозии возрастает. Облучение флюенсом нейтронов 2·1018 см-2 незначительно влияет на скорость окисления.
При увеличении температуры сплавы магния воспламеняются в атмосфере углекислого газа. Так, при давлении 1 МПа температура воспламенения равна 913 К. Полное, сгорание материала за счет саморазогрева происходит при температуре не ниже 888 К. Оболочки твэлов из спеченных порошковых магниевых сплавов не уступают по коррозионной стойкости в углекислом газе оболочкам из литейных и деформируемых сплавов.
В нейтральных средах, в том числе и в дистиллированной воде, магний и его сплавы нестойки. Нормальный потенциал магния равен —2,38 В, т. е. магний весьма электроотрицателен и крайне активен в коррозионном отношении. Облученные элементы в оболочке из сплавов магнокс хранятся в воде в течение времени, необходимого для снижения активности к о р о т к о ж и в у щи х продуктов деления. Сильная коррозия сплавов магния за это время может привести к контакту урана с водой и загрязнению бассейна выдержки. Очистка воды от хлоридов и карбонатов до содержания их 0,02 мг/л и увеличение pH среды выше 11 почти полностью подавляют коррозию магнокса. Следует отметить, что в описываемых условиях контакт сплавов магния с нержавеющей и низколегированной сталями, графитом интенсифицирует коррозию, вызывает образование язв. Контакт с алюминием и его сплавами не интенсифицирует коррозию сплавов магния.
Магний и его сплавы нестойки к атмосферной коррозии. Для защиты изделий из сплавов магния в этом случае применяют системы покрытий. При изготовлении оболочек сплавы магния сваривают аргонодуговой, электронно-лучевой сваркой.
АЛЮМИНИЙ И ЕГО СПЛАВЫ
Физические свойства. Алюминий — элемент третьей группы третьего периода периодической системы. Физические свойства алюминия отражены в табл. 8.7. Малое сечение захвата тепловых нейтронов, низ-
Физические свойства алюминия | Таблица 8.7 |
Атомный номер | 13 |
Относительная атомная масса | 26,98 |
Сечение поглощения тепловых нейтронов, м2 | 2,15·10-29 |
Плотность, г/см3 | 2,7 |
Температура плавления, К | 933 |
Температура кипения, К | 2600 |
Коэффициент линейного расширения при температуре | 28,7·10-6 |
293—873 К, град-1 | |
Коэффициент теплопроводности при температуре 373-473 К, Вт/(м·К) Кристаллическая структура | 210-233 ГЦК |
Параметр кристаллической решетки, нм | α=0,405 |
кая плотность делают алюминий весьма перспективным для реакторостроения. Температура плавления алюминия невысока. Алюминий не претерпевает структурных превращений до температуры плавления.
Природный алюминий состоит из стабильного изотопа 27А1. При взаимодействии с нейтропшн по реакции (п, γ) образуется радиоизотоп 28А1 с периодом полураспада 2,24 мин. Из алюминия и его сплавов изготовляют оболочки твэлов, канальные трубы, трубопроводы, обечайки баков и др. Низкое сечение поглощения тепловых нейтронов алюминия позволяет в случае использования его в активной зоне работать на природном уране при значительной степени выгорания.
Наряду с чистым алюминием (содержание всех примесей 0,0002%) в реакторостроении широко применяются сплавы алюминия, которые можно разбить на несколько групп:
технический алюминий марки АД (и близкий к нему по составу алюминий производства США марки 1100) содержит ~ 0,5% примесей, в основном Fe и Si;
сплавы, легированные никелем и железом (Х8001, Х8003, А288, табл. 8.8); из этих сплавов изготавливают оболочки твэлов, эксплуатирующихся при температуре до 473 К;
Таблица 8.8
Алюминиевые сплавы производства США,
применяемые в реакторостроении
Сплав | Массовое содержание легирующих элементов и примесей. % | Сплав | Массовое содержание легирующих элементов и примесей. % | ||||||||||
Ni | Fe | Сu | Si | Mg | Cr | Ni | Fe | Сu | Si | Мg | Сr | ||
Х8001 Х8 003 | 1,0 1,5 | 0,5 1,5 | — — | 0,1-0,3 0,003 | — — | — — | A 288 6061 | 1 — | 0,5 — | —0,25 | 0,003 0,6 | —1,0 | — 0,25 |
более прочные сплавы типа 6061 (см. табл. 8.8) применяют для изготовления технологических каналов.
Значительное упрочнение алюминия может быть достигнуто введением в него окисла алюминия. Изделия из таких композиций получают методами порошковой металлургии, прессованием с последующим спеканием тонкодиспергнрованного алюминиевого порошка. Такие композиции типа САП содержат 8—10% окиси алюминия. Композиции САП состоят из алюминиевых зерен, частично охваченных пленками окисла. Керамический окисел обладает высокой твердостью и прочностью. Охватывая мелкие зерна алюминия, окись препятствует срастанию их в крупные и ограничивает ползучесть. Высокая прочность сплавов САП получается вследствие ухудшения пластичности.
Некоторые элементы, которыми легируют алюминиевые сплавы, значительно растворяются в алюминии в твердом состоянии при повышенной температуре. Растворимость их падает с уменьшением температуры. Для получения структуры алюминиевого сплава в виде твердого раствора сплав нагревают до температуры, обеспечивающей полное растворение легирующего элемента с последующим быстрым охлаждением. При такой операции — закалке — при комнатной температуре фиксируется неравновесный твердый раствор. Поскольку твердый раствор нестабилен, в результате процесса старения происходит его распад. Процесс старения может быть ускорен нагреванием до 393—443 К в течение 4—12 ч. Эта обработка называется искусственным старением или дисперсионным твердением. Старение увеличивает прочностные характеристики сплавов алюминия. Для снятия наклепа сплавы алюминия отжигают при температуре 623—673 К в течение 0,5—2 ч.
Сплавы алюминия, кроме металлокерамическнх, достаточно пластичны и в этом смысле технологичны. Из них легко изготавливать изделия методом прессования, выдавливания. Сварка сплавов алюминия встречает некоторые трудности, однако процесс этот освоен и широко применяется при изготовлений твэлов. Изделия из сплавов алюминия могут быть соединены пайкой или склеиванием. Благоприятные физические, механические, технологические характеристики сплавов алюминия позволяют широко применять их для изготовления оболочек твэлов и других элементов активной зоны. В первом уран-гра- фитовом реакторе для производства плутония был использован алюминии марки 1100. Твэлы с оболочкой из алюминиевых сплавов применяют в исследовательских реакторах, реакторах для производства плутония в Ханфорде, Саванна-Ривере в США, в экспериментальных кипящих реакторах.
К сплавам, идущим на изготовление оболочек, предъявляют требования высокой пластичности. От сплавов, идущих на изготовление каналов и других конструкций активной зоны, требуется высокая прочность.
Механические характеристики. Чистый алюминий очень пластичен и непрочен. Предел прочности его равен 50—60 МПа. Небольшое количество примесей, присутствующих в техническом алюминии, упрочняет его. Прессованные и холоднотянутые или холоднокатаные трубы из технического алюминия после отжига при температуре 673—723 К имеют следующие механические характеристики:
Предел прочности, МПа 80-110
Предел текучести, МПа 30-50
Относительное удлинение, % 20-30
Несколько более прочен американский сплав 6061, близкий к советским сплавам алюминия с магнием типа АМг. В отожженном виде в готовых трубах свойства его таковы:
293 К 473 К
Предел прочности, МПа 120-150 90-100
Предел текучести, МПа 40-60 30-40
Относительное удлинение, % 25-30 45-60
С повышением температуры прочностные характеристики сплава падают, пластические растут.
Прочностные характеристики сплавов типа Х8001, выплавленных на основе технического алюминия, являются промежуточными между характеристиками технического алюминии и сплава 6061. Скорость ползучести технического алюминия при температуре 373 К и напряжении 100 МПа составляет 10-2 %/ч. Такая же скорость ползучести имеет место при температуре 523 К н напряжении 10 МПа.
Материалы оболочек должны быть совместимы с ядерным топливом. Взаимодействие между ураном и алюминием начинается при температуре 523 К. При 573 К за 2000 ч в результате взаимодействия возникает интерметаллидный слой толщиной 0,025 мм. Двуокись урана совместима с алюминием до температуры 533 К, карбид и нитрид урана — до 813 К.
Радиационная стойкость. Вследствие низкой температуры рекристаллизации радиационные повреждения алюминия и его сплавов невелики. Имеет место повышение предела текучести и прочности при сохранении пластичности (для предварительно упрочненных материалов) или снижении ее до допустимого уровня.
Флюенс нейтронов, 1021 см-2 | 0 | 2 | 7 | 27 | 38 |
σB, МПа | 140 | 180 | 200 | 220 | 240 |
σT, МПа | 125 | 160 | 170 | 180 | 200 |
δ, % | 22 | 25 | 22 | 22 | 24 |
В связи с этим можно заключить, что нейтронное облучение скорее улучшает, чем ухудшает механические свойства алюминия и его сплавов.
Коррозионная стойкость. Максимальная температура, при которой сплавы алюминия можно применять в водоохлаждаемых реакторах, определяется коррозионной стойкостью сплавов. Весьма заманчиво с экономической и ядерно-физической точек зрения использовать сплавы алюминия для изготовления оболочек твэлов и технологических каналов кипящих реакторов. Решение этой задачи затрудняется низкой коррозионной стойкостью сплавов алюминия при температуре 523—573 К в воде и пароводяной смеси. Длительная и надежная работа изделий из алюминия и его сплавов в водоохлаждаемых реакторах при температуре ниже 523 К в значительной степени определяется их коррозионной стойкостью, которая существенно зависит от качества воды, конструктивных особенностей (наличие щелей и зазоров, контактов с другими материалами), состава сплавов, облучения и т. д. Безаварийная работа реактора, в активной зоне которого используют алюминиевые сплавы, может быть достигнута лишь при тщательном учете всех приведенных выше соображений J
Нормальный потенциал анодной реакции А1→А13+ + 3е равен — 1,663 В, что свидетельствует о высокой химической активности алюминия. В первую миллисекунду после погружения в водную среду потенциал свежезачищенного алюминия близок к нормальному значению. С течением времени потенциал алюминия смещается в положительную сторону до значений от — 0,5 до 0,0 В, что связано с образованием на его поверхности окисных пленок. В свою очередь, нарушение сплошности окисной пленки на металле, погруженном в раствор, приводит к резкому смещению потенциала алюминия в отрицательную сторону. Резкое изменение электрохимических характеристик алюминия при образовании окисной пленки наряду с другими факторами дает основание полагать, что алюминии способен пассивироваться .
Состав и структура окисных пленок. Рассмотрим состав и структуру окисных пленок, образующихся на алюминии в процессе коррозии. При контакте с воздухом на поверхности алюминия образуется так называемая воздушно-окисная пленка толщиной 0,01 мкм. Эта пленка состоит из двух слоев. Внутренний слой, прилежащий к металлу (барьерный), компактный, наружный состоит из более проминаемого окисла.
В случае контакта алюминия чистотой 99,995% с насыщенной воздухом дистиллированной водой при температуре до 363 К на поверхности металла образуется аморфная пленка окисла алюминия и поверх нее слой бемита А12О3·Н20 сорторомбической решеткой и слой байерита А12О3·3Н2О с моноклинной решеткой. Толщина пленки составляет десятые доли миллиметра и зависит от конкретных условий. При температуре выше 373 К окисиая пленка на алюминии и его сплавах состоит преимущественно из бемита.
Окис на я пленка, образующаяся на поверхности алюминия, неоднородна. Толщина ее различна на разных участках, в пленке имеются поры. Именно в порах в первую очередь протекает анодный процесс. При толщине 5—10 нм пленка окиси алюминия обладает достаточно малым электрическим сопротивлением, и на этих участках может осуществляться катодный процесс. На участках значительной толщины пленка практически не пропускает электронов и поэтому инертна. На этих участках не протекают ни катодные, ни анодные процессы. Присутствие на поверхности алюминия фазовой окисной пленки обусловливает его пассивацию. Анодная поляризационная кривая алюминия (рис. 8.4) свидетельствует о пассивации алюминия в области потенциалов от — 0,4 до — 0,75 В.
В случае нарушения сплошности пассивирующей окисной пленки, например при перемешивании среды, содержащей частицы корунда, алюминий активируется и на анодной поляризационной кривой пассивная область отсутствует. Образование на поверхности алюминия окисной пленки при окислении па воздухе или при анодировании увеличивает пассивную область до потенциала 2,0 В. При температуре, близкой к комнатной, коррозия алюминия и его сплавов протекает преимущественно с кислородной деполяризацией при диффузионном ограничении. Значение предельного диффузионного тока на алюминии в 10 раз меньше, чем на железе и меди, так как на большей части поверхности алюминия катодный процесс не идет. При комнатной температуре AI и его сплавы при стационарном потенциале находятся в пассивном состоянии. Скорость коррозии при этом мала и составляет при длительности испытаний 30 сут 0,002 г/(ма·сут), С ростом температуры до 353 К скорость коррозии увеличивается до 0,03 г/(м2·сут).
С увеличением температуры интенсифицируется образование фазовых защитных слоев. В связи с этим скорость коррозии замедляется во времени. При температуре 373 К в первые 10—20 сут испытаний толщина окисной пленки δ (см) следующим образом зависит от времени
τ (с): lg δ = — 7 + 0,5 lg τ.
При длительности испытаний свыше 10 сут коррозия алюминия типа сплава АД при 353—373 К идет по линейному закону. Окисная пленка на поверхности металла, достигнув определенной толщины, растет далее крайне медленно, и толщину ее в первом приближении можно принять постоянной. Скорость же коррозии определяется интенсивностью диффузии через окисную пленку и в рассматриваемом случае близка к 0,03 г/(м2·сут).
При температурах, близких к 473 К, на поверхности алюминия в результате протекания коррозионного процесса образуются пузыри. Эти пузыри заполнены гидроокисью алюминия, частицами непрокорродировавшего алюминия и водородом.
В деаэрированной среде (а коррозия при температурах свыше 373 К, как правило, протекает в деаэрированной среде) катодный процесс состоит в разряде иона водорода. Часть водорода при этом растворяется в металле. Молизуясь в микропорах и микрорыхлотах, водород увеличивает давление в них, образуя пузыри на поверхности металла, разрушает защитную окисную пленку и тем самым резко интенсифицирует коррозию. Регулярность кристаллической решетки на границах зерен нарушается. Очевидно, на этих участках концентрируются и несплошности в окисной защитной пленке. В связи с этим следует ожидать более интенсивной коррозии алюминия по границам зерен, что и наблюдается на практике. При легировании алюминия железом и никелем последние мало растворимы в алюминии и уже при малых концентрациях образуют интерметаллиды. Перенапряжение водорода на интерметаллидах железа, никеля меньше, чем на алюминии. Вследствие этого катодная реакция разряда ионов водорода будет протекать преимущественно на поверхности интерметаллидов. Тут же следует ожидать и молизации водорода. В результате в сплавах алюминия, легированных железом, никелем, медью, следует ожидать меньшего растворения водорода в металле и соответственно более высоких защитных свойств окисной пленки. Так, при увеличении содержания в алюминии железа перенапряжение водорода при температуре 473 К снижается:
Содержание Fe, % | 0,25 | 0,5 | 1,0 | 5 | |
Перенапряжение водорода, В | 1,34 | 1,14 | 0,85 | 0,74 | |
Заметим, что наиболее значительное уменьшение перенапряжения водорода происходит при введении в алюминий железа в количестве до 1%. Очевидно, наиболее эффективно скорость коррозии алюминия снижается, когда содержание железа увеличивается до 1%. Дальнейшее повышение содержания железа существенно слабее влияет на стойкость алюминия. Действительно, при увеличении содержания железа с 0,5 до 0,8% и с 0,8 до 5% скорость коррозии алюминия уменьшается соответственно в 1,7 и 1,5 раза.
В соответствии с изложенным сплавы алюминия, стойкие при температурах, близких к 573K, должны содержать такие легирующие элементы, как железо, никель, в количестве, близком к 1%. Такое количество никеля содержит, в частности, сплав марки Х8001, рекомендуемый для работы при температуре 573 К. Скорость коррозии этого сплава при температурах 473 и 573 К составляет соответственно 0,1 и 0,25 г/(м2·сут) и уменьшается во времени τ (сут). При 573 К выполняется следующая зависимость: lg К = 0,58 — 0,42 Ig τ.
Присутствующие в теплоносителе продукты коррозии алюминия, осаждаясь на поверхности окисных слоев, затрудняют выход продуктов коррозии в воду. При этом снижается и скорость коррозии. В связи с этим чем больше площадь нержавеющей стали в контуре, тем выше скорость коррозии сплавов алюминия, находящихся в этом же контуре.
Необходимо заметить, что при температурах ниже 373 К наиболее коррозионно-стоек чистый А1. При температурах свыше 373 К более стопки сплавы, легированные Fe, Ni, Сu.
В начальный период коррозия алюминия и его сплавов протекает по параболическому закону. По истечении некоторого периода, называемого обычно инкубационным, скорость коррозии возрастает (рис. 8.5) Коррозия при этом протекает но линейному закону.
Для алюминия чистоты 99,5% длительность инкубационного периода τ (ч) при коррозии в воде следующим образом зависит от температуры:
Ig τ = — 18,78+ (1,4· 104/T).
По этой зависимости можно в первом приближении оценивать и длительность инкубационного периода при коррозии сплавов алюминия. Существенно влияет на стойкость алюминия и его сплавов pH среды.
Пассивное состояние на алюминии может нарушаться вследствие протекания следующих реакций:
А1+О3- + 2Н+ = А13+ + Н2О + 2е
Al+O2 + ОН- = НА102 + 2е.
Минимальная скорость коррозии алюминия, очевидно, должна отвечать минимальным скоростям той или другой реакции. Эта ситуация реализуется, когда скорости этих реакций равны. В первом приближении этому отвечает равенство
С другой стороны, ионное произведение воды
Решая совместно эти уравнения, получаем, что минимальная скорость коррозии алюминия должна отвечать значениям pH = — lg W/3.
Ионное произведение воды изменится с температурой. В связи с этим изменяется с температурой и диапазон значений pH, отвечающий минимальной скорости коррозии сплавов алюминия:
Т, К 338-373 298-473 523-573
pH 5,8-6,5 4,5-5,0 3,0-3,5
При температурах 473—573 К подкисление воды фосфорной кислотой снижает скорость коррозии алюминиевых сплавов. Так, при температуре 588 К и скорости потока 5,4 м/с для
сплава X8001 связь привеса образцов ∆G (г/м2) и времени τ (сут) выражается следующими зависимостями:
для pH 5,5 lg ∆G=0,3+0,8lgτ
для pH 3,5 lg ∆G=-0,6+0,7lgτ
Содержание кислорода влияет на скорость катодного процесса и стационарный потенциал. Алюминий и его сплавы в широком диапазоне потенциалов находятся в пассивном состоянии. В связи с этим увеличение концентрации кислорода от 0,02 до 8 мг/кг практически не изменило скорости анодного процесса на алюминии чистоты 99,99% при потенциале — 0,3 В.
Соответственно изменение концентрации кислорода не должно заметно сказаться па коррозионной стойкости алюминия и его сплавов. Аналогично влиянию кислорода и влияние перекиси водорода. Присутствие в среде хлоридов влияет на электрохимическое и коррозионное поведение А1 и его сплавов.
Скорость анодного процесса при потенциале 0,05 В при 333 К практически не изменяется па образце, выдержанном в химически обессоленной воде 72 ч до концентрации хлор-иона 0,5 мг/л. При дальнейшем повышении концентрации хлор-иона скорость коррозии увеличивается линейно с концентрацией хлор-иона.
Если в воде присутствует сульфат-ион в количестве 5 мг/л, то хлор-ион не увеличивает скорости анодного процесса в тех же условиях до концентрации 2 мг/л. Сам сульфат-ион не увеличивает скорости анодного процесса до концентрации 5 мг/кг.
Ингибиторами коррозии А1 являются кремниевая кислота, хроматы.
Контактная коррозия. В любой конструкции всегда имеет место контакт разнородных материалов. При контакте с нержавеющими сталями стационарный потенциал сплавов алюминия смещается в область перепассивации, и скорость коррозии алюминия возрастает. Лишь для некоторых сплавов при строго определенном соотношении поверхностей алюминия и нержавеющей стали стационарный потенциал при контакте со сталью отвечает пассивной области. Для снижения контактной коррозии на алюминиевых изделиях методом анодирования создается защитная пленка окиси алюминия. При так называемом обычном анодировании толщина окисной пленки равна 10—20 мкм, при толстослойном—50—100 мкм. Пленка окисла имеет в последнем случае черный цвет, и этот метод анодирования называют иногда черным. Окисная пленка при толстослойном анодировании обладает хорошими антифрикционными свойствами. Окисные пленки после обычного анодирования наполняются (пропитываются) хроматами и имеют зеленый цвет.
Для предотвращения контактной коррозии алюминия между изделием из алюминия и нержавеющей сталью вставляют сменную деталь — протектор — из сплава алюминия. Находящийся в контакте с нержавеющей сталью протектор разрушается, и его заменяют. В других случаях изделия из алюминия и стали разделяют деталью из сплавов циркония или титана.
В исследовательских реакторах баки, изготовленные из сплавов алюминия, контактируют с бетоном. В бетон обычно добавляют стальной скрап. Кроме того, в бетоне имеется стальная арматура. Поверхность бетона, соприкасающаяся с алюминиевым баком, покрывают защитным покрытием. Обычно наносят несколько слоев кузбас-лака. Если сплошность защитного покрытия нарушена, алюминий может соприкасаться с бетоном и находящимися в нем арматурой или скрапом. Влага, содержащаяся в бетоне, Может иметь pH = 13÷14.
В месте непосредственного контакта с бетоном развивается интенсивная язвенная коррозия алюминия, которая может привести к сквозному поражению через несколько лет эксплуатации. Наиболее эффективным способом борьбы с такого рода коррозией является нанесение на поверхность бетона высококачественного защитного покрытия.
Существенно увеличивает скорость коррозии сплавов алюминия контакт с графитом. Так, скорость коррозии сплава марки 6061 при контакте с графитом в химически обессоленной и речной воде возросла более чем в 20 раз. Анодирование повышает в этом случае стойкость сплавов алюминия.
Щелевая коррозия. В реальных конструкциях трудно полностью избежать образования щелей и зазоров между однородными материалами. При контакте двух изделий из сплавов алюминия протекает щелевая коррозия.
Ширина зазора или щели при плотном прилегании двух металлических поверхностей составляет обычно 0,005 см.
Кислород из среды, находящейся в щели, расходуется в ходе коррозионного процесса. Поступление новых порций кислорода из объема в щель возможно только за счет диффузии. Ионы алюминия, Поступающие вследствие протекания коррозионного процесса в коррозионную среду, в щели гидролизуются:
где D= 10-5 см2/с — коэффициент диффузии кислорода; S = 5 ×10-3 см2 — сечение щели; С = 10-6 г·экв/см3 — концентрация кислорода в объеме.
Даже на расстоянии 0,1 см от края щели поступление кислорода составит лишь 5·10-13 г-экв/с.
Стационарный потенциал алюминия в насыщенной воздухом химически обессоленной воде отвечает пассивному состоянию. При уменьшении концентрации кислорода в щели скорость анодного процесса в пассивном состоянии, а соответственно и скорость коррозии остаются постоянными, близкими к 3·10-3 г/(м2·сут), что составляет 1,85·10-11 г-экв/(см2·с). Очевидно, что Поступающий вследствие диффузии в щель кислород не может обеспечить протекание
коррозии.
В результате реакции гидролиза
А13+ + ЗН2О = Al(OH)3 +3Н+
образуется ион водорода, который принимает участие в катодном процессе. Коэффициент диффузии Н+ приблизительно на два порядка выше, чем коэффициент диффузии кислорода. В связи с этим можно полагать, что значительная часть водорода, образовавшегося в результате гидролиза, будет удалена из щели вследствие диффузии Н. В соответствии с этим среда в щели может стать практически нейтральной.
Следует иметь в виду, что при попадании нейтральной коррозионной среды в щель может протекать анодная реакция с образованием алюминатов. Протекание этой реакции уменьшает количество А13+ в щели. Реакция гидролиза и образование Н+ при этом подавляются.
В рассматриваемой ситуации продукты коррозии алюминия в щели будут присутствовать в виде Н2АlO3 и А1(ОН)3. Концентрация А13+ может быть принята 10-6 моль/л. В этом случае, исходя из произведения растворимости А1(ОН)3 — 2·10-32, pH в щели должен быть 5,4, т. е. близок к нейтральной.
Вследствие ограничения поступления кислорода в щель среда в щели будет деаэрнроваиа. В деаэрированной химически обессоленной воде стационарный потенциал алюминия равен —0,7 В. При этом потенциале в нейтральной среде скорость разряда иона водорода равна 10-9 А/см2, или 10-14 моль/(см3·с), что в 1000 раз меньше скорости поступления алюминия в щель. Таким образом, можно полагать, что анодный процесс в щели компенсируется протеканием катодного процесса в объеме.
Ионы водорода в щели расходуются на протекание катодного процесса. Так как концентрация ионов Н+ и ОН- связана значением ионного произведения воды, то вследствие диссоциации молекул воды в коррозионную среду в щели поступают гидроксил-ионы. В связи с этим pH среды в щели повышается до 8.
Подщелачивание среды в щели приводит к резкому увеличению скорости коррозии. Особенно сильно развивается щелевая коррозия, когда щель образуется в результате контакта алюминия и нержавеющей стали. В таком случае творят о контактно-щелевой коррозии.
В связи с изложенным следует избегать образования щелей и зазоров в конструкциях атомных установок, где используются алюминий и его сплавы. В этой связи соединение листов и труб алюминия следует производить не внахлестку, а встык и методом сварки. При нагреве во время сварки на поверхности сплавов алюминия и нержавеющей стали образуются окисные пленки, которые снижают ток при работе гальванической пары алюминий — нержавеющая сталь.
Переход продуктов коррозии алюминия в теплоноситель. При коррозии алюминия часть продуктов коррозии остается на поверхности металла в виде защитной окисной пленки или в виде отложений, а часть переходит в теплоноситель. В статических условиях в тепло* носитель переходит меньше продуктов коррозии, чем в динамических. При скорости теплоносителя 3—6 м/с и температуре до 423 К в среду переходит до 50% продуктов коррозии.
При линейной зависимости изменения массы алюминия при коррозии от времени в раствор должна переходить основная масса продуктов коррозии.
Влияние облучения. Рассмотрим влияние облучения на коррозионную стойкость сплавов алюминия. Выше указывалось, что коррозия алюминия и его сплавов контролируется поверхностной диффузией. Элементарные ячейки кристаллической решетки, выходящие на поверхность окисла, в общем случае значительно искажены. Это связано с тем, что сама поверхность раздела является весьма серьезным дефектом кристаллической решетки. В связи с этим трудно ожидать, что дефекты кристаллической решетки, образовавшиеся в результате облучения, сколько-нибудь существенно скажутся на эффективности поверхностной диффузии и соответственно на стойкости сплавов алюминия.
В деаэрированной среде коррозия идет с водородной деполяризацией и облучение не влияет существенно па кинетику катодного процесса. В среде, содержащей кислород, облучение увеличивает скорость катодного процесса, но стационарный потенциал алюминия остается в пассивном состоянии. При этом скорость анодного процесса не изменяется. Отсюда следует вывод о том, что облучение не должно заметно изменить коррозионную стойкость алюминия и его сплавов.
Так, коррозия сплавов алюминия, легированных 0,5—2% Ni и 0,5% Fe, испытывавшихся при температуре 533 К в течение 700 ч, уменьшилась при воздействии реакторного облучения в среднем на 11,9% по сравнению с испытаниями в тех же условиях, но без облучения. Погрешность в такого рода коррозионных исследованиях близка к 10%. Возможно, что в начальный период коррозионных испытаний облучение интенсифицирует рост окисной пленки. При этом путь диффузии удлиняется и на последующих этапах испытаний скорость коррозии несколько снижается. Некоторое снижение скорости коррозии при облучении зафиксировано при испытании сплава М288 при температуре 493—523 К. При температуре 463 К зафиксировано увеличение скорости коррозии сплава Х8001 при облучении. При температуре 473 К и длительности испытаний в химически обессоленной Воде 2000 ч скорость коррозии сплавов Х8001, М288 составляет 0,2— 0,3 г/(м2·сут). Такого же порядка была скорость их коррозии и без облучения.
Увеличение скорости катодного процесса под действием облучения в кислородсодержащих средах приведет к увеличению потенциала на границе алюминий—нержавеющая сталь. Это, в свою очередь, может интенсифицировать контактную коррозию алюминия и его сплавов.
Движение теплоносителя интенсифицирует скорость коррозии алюминиевых сплавов. Особенно заметен этот эффект при температуре 553 К и выше. Так, для сплавов, содержащих 2,5% Ni и 0,4% Fe, при испытаниях со скоростью теплоносителя 2 м/с скорость коррозии увечилась от 0,37 до 0,93 г/(м3·сут). При скорости воды 5—6 м/с на алюминиевых образцах фиксируются коррозионно-эрозионные повреждения. На отдельных образцах на входе и выходе из испытательного участка глубина коррознонно-эрозионных повреждений за 2000 ч испытаний достигает 0,5—1,0 мм. Этот эффект связан, по-видимому, со смыванием с поверхности металла продуктов коррозии. В специальных экспериментах образцы сплавов алюминия выдерживали при температуре 623—673 К в воде, насыщенной продуктами коррозии алюминия, в течение педели и суток соответственно. При этом, очевидно, происходил процесс, сходный со спеканием. После этого испытание при циркуляции теплоносителя не вызвало увеличения скорости коррозии.
Увеличение скорости потока перегретого нара также снижает стойкость алюминиевых сплавов. С увеличением давления перегретого нара растет его плотность, что, видимо, приводит к увеличению скорости коррозии сплавов алюминия. Вибрация существенно снижает коррозионную стойкость сплавов алюминия.
Подводя некоторые итоги изложенному, следует заметить, что для обеспечения надежной эксплуатации сплавов алюминия (высокой коррозионной стойкости) необходимо уделять серьезное внимание составу водного теплоносителя, гидродинамическим факторам. Имеющиеся в настоящее время данные подтверждают, что сплавы алюминия могут длительно и надежно эксплуатироваться до температуры 473 К.
В исследовательских реакторах для оболочек твэлов и элементов конструкций применяют алюминий высокой чистоты, поскольку температура воды, насыщенной воздухом, не превышает 313- 343 К. Качество воды должно соответствовать следующим нормам:
Удельная электропроводность, мкСм/см | 1 |
Жесткость, мкг-экв/л | 1—2 |
Содержание, мг/л: | |
хлоридов | <0,02 |
сульфатов | <0,05 |
меди | <0,02 |
pH | 5-7 |
Алюминий высокой чистоты и сплавы типа 6061 могут применяться в реакторах, охлаждаемых речной или озерной водой, при температуре до 353—363 К.
Для работы при 443—473 К используют сплавы типа А288, X8001 (см. табл. 8.8). Нормы по качеству воды в этом случае отличаются от принятых для исследовательских реакторов по содержанию кислорода и значению pH. Вода должна содержать не более 0,02 мг/л кислорода и pH должен быть 5,5—6,5.
ЦИРКОНИЙ И ЕГО СПЛАВЫ
Физические свойства. Сплавы алюминия в настоящее время не применяют при температуре выше 473 К, так как при такой температуре коррозионная стойкость и прочность их недостаточно высоки.
Из материалов с малым сечением захвата в этой области широкое применение получили сплавы циркония. Физико-механические (табл. 8.9) и коррозионные их характеристики делают сплавы циркония весьма перспективными для изготовления оболочек твэлов.
Физико-механические свойства циркония | Таблица 8.9 |
Атомный помер | 40 |
Относительная атомная масса | 91 |
Сечение поглощения тепловых нейтронов, м2 | 1,8·10-29 |
Плотность, г/см3 | 6,5 |
Температура плавления, К | 2118 |
Температура кипения, К | 3873—3973 |
Коэффициент линейного расширения, град-1 | 5,8·10-6 |
Коэффициент теплопроводности, Вт/(м·К) | 23,7 |
Кристаллическая структура | α-Фаза, ГПУ до 1135 К |
ß-Фаза, ОЦК выше 1135 К | |
Параметр кристаллической решетки, нм | α-Фаза: |
а=0,3232 | |
с = 0,5147 | |
ß-Фаза: | |
α=0,316 | |
В реакторах канального типа сплавы циркония незаменимы для изготовления канальных труб. Применение каналов из сплавов циркония существенно снижает поглощение нейтронов по сравнению с каналами, изготовлеными из аустенитных нержавеющих сталей.
В соответствии с Директивами XXV съезда КПСС возведены Ленинградская, Курская, Чернобыльская АЭС. В канальных реакторах этих АЭС технологические каналы изготавливают из сплавов Zr + 2,5% Nb, а оболочки твэлов —из сплава Zr+1% Nb. Из этого сплава иготавливают и оболочки твэлов ВВЭР. Максимальная температура (573—623 К), при которой сплавы циркония применяются в водоохлаждаемых реакторах, определяется их коррозионной стойкостью.
Для работы в перегретом паре при температуре свыше 623 К в качестве перспективного рассматривается сплав валой(1,2% Сr, 0,1% Fe).
При облучении циркония нейтронами образуются три изотопа:
93Zr, период полураспада 1,5·106 лет, энергия ß-излучения 0,06 МэВ;
95Zr, период полураспада 64,05 сут, энергия γ-излучения 0,24 МэВ;
97Zr, период полураспада 17 ч.
Металлический цирконий получают в основном иодидным, электролитным и магнийтермическим методами. В первом случае металл наиболее чистый.
Из сплавов циркония изготовляют участки технологических каналов, находящиеся в активной зоне. В связи с этим возникает необходимость соединения сплавов циркония с нержавеющими сталями. На соединения сталь цирконий кроме напряжений, обусловленных
действием давления теплоносителя, действуют также значительные, циклически изменяющиеся напряжения, обусловленные различием коэффициентов теплового расширения циркония (5,8·10-6 град-1) и нержавеющей стали (17,5·10-6 град-1).
Соединение методом сварки в данном случае приводит к образованию в зоне сварки хрупких фаз (эвтектики и интерметаллидов), приводящих к растрескиванию соединений уже при охлаждении после сварки. Для получения соединения сталь—цирконий более перспективны такие методы, как механические, диффузионная сварка, пайка, совместное прессование, развальцовка, сварка взрывом и т. п. Наибольшее практическое использование получил метод развальцовки.
Механические характеристики. Чистый цирконий имеет невысокую прочность (табл. 8.10) и высокую коррозионную стойкость. Загрязнение циркония, особенно азотом, снижает стойкость металла. Для нивелирования вредного действия азота цирконий легируют оловом. (Из этих соображений легируют оловом и сплав оженит, который содержит по 0,1—0,3% Sn, Nb, Fe и Ni). Повышение прочностных характеристик циркония достигается легированием его Nb, Fe, Ni, Сu и др. Сплавы, легировапные 2,5% Nb, и сплавы типа циркалой-2 (1,2—1,7% Sn, 0,07—0,2% Fe, 0,05—0,15% Cr, 0,03—0,08% Ni) по механическим свойствам (см. табл. 8.10) приближаются к нержавеющим сталям. Возможность их применения в реакторах при температуре 750—900 К в среде газовых, жидкометаллических или органических теплоносителей определяется не прочностными свойствами, а коррозионной стойкостью в условиях движения теплоносителя и при облучении.
Дата добавления: 2021-01-21; просмотров: 102; Мы поможем в написании вашей работы! |
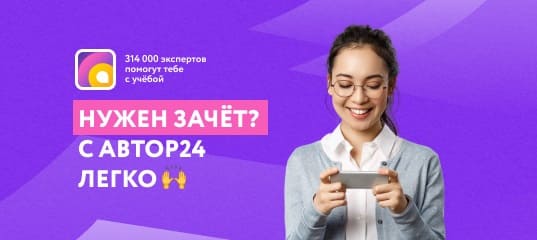
Мы поможем в написании ваших работ!