Чугун. Виды чугуна: белый, серый, ковкий, высокопрочный
Чугун – сплав железа (Fe>90%) с углеродом (C от 2,14% до 6,67%).
Углерод может содержаться в чугуне в виде графита (С) или цементита (Fe3C).
Также чугун содержит примеси кремния, марганца, фосфора и серы.
Чугуны со специальными свойствами содержат также легирующие элементы – хром, никель, медь, молибден и др.
Чугун – наиболее широко применяемый материал для изготовления литых деталей, используемых при относительно невысоких напряжениях и малых динамических нагрузках. Преимущества чугуна в сравнении со сталью – высокие литейные свойства и небольшая стоимость. Чугуны также лучше обрабатываются резанием, чем большинство сталей (кроме автоматных сталей), но плохо свариваются, обладают меньшей прочностью, жесткостью и пластичностью.
В зависимости от состояния углерода в чугуне различают:
белый чугун
серый чугун(ГОСТ 1412 - "Чугун с пластинчатым графитом для отливок")
ковкий чугун(ГОСТ 1215 - "Отливки из ковкого чугуна")
высокопрочный чугун(ГОСТ 7293 - "Чугун с шаровидным графитом для отливок")
Белый чугун
В белом чугуне весь углерод находится в связанном состоянии в виде цементита Fe3C.
У белого чугуна высокая износостойкость и твердость, однако он хрупок и плохо обрабатывается резанием, поэтому в машиностроении они находят ограниченное применение и идут, в основном, в передел на сталь.
По содержанию углерода серый чугун подразделяют на:
|
|
Доэвтектический с содержанием углерода от 2,14% до 4,3%
Эвтектический с содержанием углерода 4,3%
Заэвтектический с содержанием углерода от 4,3% до 6,67%.
В сером, ковком, высокопрочном чугунах весь углерод или большая его часть находится в виде графита различной формы (их еще называют графитными).
Серый чугун
В структуре серых чугунов графит пластинчатой формы.
Серые чугуны содержат: 3,2-3,5% углерода, 1,9-2,5% кремния, 0,5-0,8% марганца, 0,1-0,3% фосфора и менее 0,12% серы.
Отливки деталей из серых чугунов получают в кокилях – земляных или металлических формах.
Серый чугун находит широкое применение в машиностроении. Ввиду невысоких механических свойств у отливок из серого чугуна и простоты получения их применяют для изготовления деталей менее ответственного назначения, деталей, работающих при отсутствии ударных нагрузок. В частности из них делают крышки, шкивы, станины станков и прессов.
Пример обозначения серого чугуна: СЧ32-52. Буквы обозначают серый чугун (СЧ), первое число обозначает предел прочности при растяжении (32 кгс/мм2 или 320 МПа), второе число – предел прочности при изгибе.
Ковкий чугун
В структуре ковких чугунов графит хлопьевидной формы.
|
|
Ковкие чугуны содержат: 2,4-3,0% углерода, 0,8-1,4% кремния, 0,3-1,0% марганца, менее 0,2% фосфора, не более 0,1% серы.
Ковкий чугун получают из белого чугуна в результате нагрева и длительной выдержки. Эту процедуру называют графитизирующим отжигом или томлением.
Пример обозначения ковкого чугуна: КЧ45-6. Буквы обозначают ковкий чугун (КЧ), первое число - предел прочности при растяжении (45 кгс/мм2 или 450 МПа), второе – относительное удлинение в % (6%).
Высокопрочный чугун
Высокопрочный чугун содержит графит шаровидной формы.
Он имеет наиболее высокие прочностные свойства.
Высокопрочный чугун содержит: 3,2-3,8% углерода, 1,9-2,6% кремния, 0,6-0,8% марганца, до 0,12% фосфора и не более 0,3% серы.
Высокопрочный чугун получают путем модифицирования (т.е. введения добавки-модификатора – магния) жидкого расплава. Модификаторы способствуют образованию графитных включений шаровидной формы, благодаря чему механические свойства такого чугуна приближаются к свойствам угеродистых сталей, а литейные свойства выше (но ниже, чем у серых чугунов).
Из высокопрочных чугунов изготавливают ответственные детали для машиностроения - поршни, цилиндры, коленчатые валы, тормозные колодки. Также из высокопрочного чугуна изготавливают трубы.
|
|
Пример обозначения высокопрочного чугуна: ВЧ45-5. Буквы обозначают высокопрочный чугун (ВЧ), первое число обозначает предел прочности при растяжении (45 кгс/мм2 или 450 МПа), второе – относительное удлинение в %.
Легированные стали и сплавы
Стали. Общая классификация. Отличия от чугунов
Сталь – сплав железа (Fe>90%) с углеродом (C до 2,14%). Стали широко применяются в машиностроении, строительстве.
От чугунов сталь отличается более низким процентным содержанием углерода и всех постоянных примесей.
Стали более мягкие и пластичные, чем чугуны.
Помимо железа и углерода в сталях и чугунах всегда присутствует кремний (Si), марганец (Mn), сера (S), фосфор (P) и газы – кислород, азот, водород (O,N,H). Эти примеси называют постоянными.
Кроме постоянных примесей в сталях и чугунах случайным образом могут содержаться и другие элементы, которые называют случайными примесями (из руды, лома).
Иногда в железоуглеродистые сплавы для изменения их структуры и свойств специально вводят химические элементы – хром (Cr), никель (Ni), молибден (Mo), вольфрам (W), титан (Ti). Такие примеси называют легирующими, а соответствующие сплавы – легированными.
|
|
Классификация по химическому составу
По химическому составу стали подразделяют на:
Углеродистые
Легированные
Углеродистая – сталь, у которой свойства зависят, в основном, от содержания углерода. Такие стали в свою очередь подразделяют на:
Низкоуглеродистые – С<0,25%
Среднеуглеродистые – 0,25%<C<0,6%
Высокоуглеродистые – С>0,6%
Легированная – сталь, в состав которой входят специально введенные элементы для придания ей требуемых свойств.
Классификация по назначению
Стали делят по назначению на:
Конструкционные
Инструментальные
Стали специального назначения
Конструкционные стали предназначены для изготовления деталей машин, приборов и элементов строительных конструкций.
Инструментальные стали используют для изготовления режущего, измерительного инструмента, штампов для холодного и горячего деформирования.
Стали специального назначения – нержавеющие (коррозионно-стойкие), жаростойкие, жаропрочные, износостойкие и др.
Классификация по качеству
Стали подразделяют по этому признаку на:
Стали обыкновенного качества
Качественные
Высококачественные
Особо высококачественные
Под качеством здесь понимается совокупность свойств стали, определяемых металлургическим процессом ее производства.
Классификация по степени раскисления
Стали по степени раскисления классифицируют на:
Спокойные
Полуспокойные
Кипящие
При маркировке таких сталей в конце марки кипящей стали пишутся буквы "кп", полуспокойной - буквы "пс"
Раскисление – процесс удаления кислорода из жидкой стали. Нераскисленная сталь обладает недостаточной пластичностью и подвержена разрушению при горячей обработке давлением.
Классификация по структуре
Стали классифицируют в состоянии после отжига и нормализации. В отожженном (равновесном) состоянии стали подразделяют на:
Доэвтектоидные, имеющие в структуре избыточный цементит
Эвтектоидные, структура которых состоит из перлита
Завтектоидные, в структуре которых имеются вторичные карбиды, выделяющиеся из аустенита
Ледебуритные, в структуре которых содержатся первичные (эвтектические) карбиды
Аустенитные
Ферритные
Маркировка сталей
В конце марки кипящей стали пишутся буквы "кп", полуспокойной - буквы "пс".
Легирующие элементы обозначаются буквами: Н (никель), К (кобальт), Г (марганец), Х (хром), В (вольфрам), М (молибден), Ю (алюминий), С (кремний), Ф (ванадий), Р (бор). Буквы пишутся после цифры, указывающей содержание углерода. Если после буквы нет цифры, то содержание легирующего элемента в стали 1-1,5%. Исключение сделано для молибдена и ванадия, содержание которых в большинстве сталей 0,2-0,3%.
Если легирующего элемента в стали больше 1,5%, то цифра после буквы указывают его содержание в процентах. Например, марка 15Х обозначает сталь, имеющую в среднем 0,15%С и 1-1,5%Cr, сталь 35Г2 - 0,35%С и 2% Mn.
Отличие в обозначении качественных сталей от высококачественных заключается в том, что в конце марки высококачественной сстали приписывается буква А. К примеру, сталь 40ХНМ - качественная, а сталь 40ХНМА - высококачественная. Если сталь особо высококачественная, то в конце марки пишется буква Ш.
У сталей, применяемых в виде литья (в отливке), в конце марки ставится буква Л.
Шарикоподшипниковые хромистые стали обозначаются в начале буквами ШХ, содержание хрома в этих сталях указывается в десятых долях процента, а содержание углерода, одинаковое при различном содержании хрома, не указывается. Например, сталь ШХ15 содержит в среднем 1% C и 1,5% Cr.
Быстрорежущие стали обозначают буквой Р (режущие). Следующая за буквой цифра указывает содержание главного для этих сталей легирующего элемента - вольфрама.
Пример: Р6М5К4 - быстрорежущая сталь с содержанием вольфрама 6%, молибдена 5%, кобальта 4%.
Электротехнические стали (трансформаторные) обозначаются буквой Э. Следующая за буквой цифра указывает содержание легирующего элемента - кремния - в процентах.
По марочнику SAE (США) конструкционные стали: углеродистые и легированные одним и двумя элементами обозначаются четырьмя цифрами. Первая цифра указывает основной легирующий элемент, вторая - его содержание в процентах, третья и четвертая - содержание углерода в сотых долях процента. Первая цифра 1 принята для обозначения углеродистых сталей; тогда вторая цифра 0. Первые цифры: 2 обозначает никелевые стали; 3 - никелевые с хромом; 4 - молибденовые; 5 - хромистые; 6 - хромистые с ванадием; 7 - вольфрамовые; 8 - ванадиевые; 9 - кремнистые с марганцем.
Например, сталь 1045 отвечает стали 45 по ГОСТ; сталь 5140 - стали 40Х и т.д. Для сталей, легированных большим числом элементов, принято более сложное обозначение.
Легированными называют стали, в которые специально вводят те или иные химические элементы (хром, никель, кобальт, молибден, титан, вольфрам и др.). Эти элементы вводят с целью воздействия на структуру и получения требуемых свойств.
По своему воздействию на структуру стали легирующие элементы делятся на 2 класса:
- первые расширяют гамма-область и сужают альфа-область
- вторые наоборот – сужают гамма-область и расширяют альфа-область
Легированные стали классифицируют:
- по структуре в равновесном состоянии и после охлаждения на воздухе
- по типу легирующих элементов и их процентному содержанию
- по качеству
- по назначению
По структуре в равновесном состоянии разделяют на:
- доэвтектоидные
- эвтектоидные
- заэвтектоидные
После охлаждения на воздухе структура стали может измениться. По структуре в нормализованном состоянии легированные стали подразделяют на:
- перлитные
- аустенитные
- мартенситные
По типу легирующих элементов стали подразделяют на хромовые, никелевые и т.д.
Современные легированные стали – сложнолегированные.
По общему процентному содержанию легирующих элементов легированные стали разделяют на:
- низколегированные – 5-10%
- среднелегированные – 10%
- высоколегированные – более 10%
Все легированные стали являются качественными сталями. Но бывают высококачественные и особо высококачественные.
Все легированные стали подвергаются термообработке, которая существенно улучшает структуру и форму. Использование без термообработки нерационально.
По назначению стали делят на:
- конструкционные
- инструментальные
- стали специального назначения
Маркировка легированных сталей
Маркировка легированных сталей зависит от их назначения.
В основе маркировки легированных сталей лежит буквенно-цифровой метод.
В начале марки конструкционных легированных сталей (гост 4543-71) ставятся цифры, обозначающие содержание углерода в сотых долях процента.
Далее идут большие буквы, обозначающие тот или иной легирующий элемент:
Х – хром
Б - ниобий
Н – никель
Д – медь
К – кобальт
Г – марганец
М – молибден
Р – бор
Т – титан
Ю – алюминий
В – вольфрам
Ф – ванадий
А – азот
С - кремний
После буквы может стоять цифра, которая обозначает среднее округленное до целого процентное содержание соответствующего легирующего элемента.
Если цифры нет, то содержание легирующего элемента около 1% (или менее).
Если буква А стоит в середине марки стали – она означает присутствие в стали азота как легирующего элемента.
Если буква А стоит в конце марки – сталь высококачественная. У особо высококачественной стали ставится буква Ш в конце марки.
40ХН3МФА – конструкционная легированная сталь со средним содержанием углерода 0,4%, ~1% хрома, ~3% никеля, ~1% молибдена, ~1% ванадия, высококачественная.
18ХГТ – конструкционная легированная сталь с содержанием углерода 0,18% и по 1% (приблизительно) хрома, марганца и титана.
В начале марки инструментальных легированных сталей (ГОСТ 5950-2000) первая цифра – среднее содержание углерода в десятых долях процента. Если цифра не стоит, то содержание углерода в этой стали 1% и более.
Затем следуют буквы и цифры, обозначающие тоже самое, что и у конструкционных легированных сталей.
Легирующие элементы, которые вводят в инструментальные стали увеличивают теплостойкость, закаливаемость, вязкость, износостойкость.
ХВГ – инструментальная легированная сталь, углерода более 1%, приблизительно около 1% хрома, вольфрама, марганца.
Стали специального назначения маркируются несколько иначе. В начале марки – большая буква русского алфавита, обозначающая назначение стали:
А – автоматная
Э – электротехническая
Ш – шарикоподшипниковая
Р - быстрорежущая
После буквы ставятся цифры, обозначающие среднее, округленное до целого, содержание ведущего легирующего элемента. Для электротехнических сталей это кремний, для быстрорежущих (используются для изготовления режущего инструмента) – вольфрам.
Р18 – быстрорежущая сталь, 18% вольфрама
Р6М5К4 – быстрорежущая сталь, содержание вольфрама 6%, молибдена 5%, 4% кобальта.
Титан – металл серебристо-белого цвета с голубоватым отливом. Титан имеет невысокую плотность 4,507 г/см3, температура плавления 1660 ?С. Титан обладает высокой механической прочностью и высокой коррозионной и химической стойкостью - на поверхности титана образуется стойкая оксидная пленка, благодаря чему титан обладает высокой сопротивляемости коррозии в некоторых кислотах, в морской и пресной воде.
Для производства титана используют рутил, ильменит, титанит и другие руды, содержащие 10-40% двуокиси титана TiO2.
Титан имеет две аллотропические модификации: альфа-титан существует до температуры 882 oС, бета-титан существует при более высоких температурах.
Технически чистый титан (ГОСТ 19807-74) содержит 99,2-99,65% титана. Прочность технически чистого титана зависит от степени его чистоты и соответствует прочности обычных конструкционных сталей.
ВТ1-00 и ВТ1-0 – технический титан, содержит углерода, кислорода , азота , водорода, железа, кремния вместе менее 1%.
Преимущество титана и его сплавов заключается в сочетании высоких механических свойств и коррозионной стойкости с малой плотностью. В состав титановых сплавов могут входить алюминий, ванадий, марганец, молибден, хром.
Для повышения механических свойств титана его почти всегда легируют алюминием, который повышает температуру аллотропического превращения титана альфа-бета, и поэтому алюминий часто называют альфа-стабилизатором титана. Элементы, понижающие эту точку, называют бета-стабилизаторами: молибден, ванадий, хром, марганец, железо.
Также как и латуни, алюминиевые и магниевые сплавы, по технологическому назначению титановые сплавы делят на:
- литейные
- деформируемые
По прочности титановые сплавы подразделяют на три группы:
- низкой прочности (предел прочности B = 300-700 МПа)
- средней прочности (предел прочности B = 700-1000 МПа)
- высокой прочности (предел прочности B более 1000 МПа)
Титановые сплавы применяются в авиационной (самолетостроении, ракетосроении, при производстве реактивных двигателей) и химической промышленности. Также титан широко применяют в судостроении благодаря его устойчивости против воздействия морской воды.
Из сплавов на основе титана изготавливаются лопатки паровых и газовых турбин, выпускных клапанов дизельных двигателей, лопаток и дисков компрессоров, поршневых пальцев, шатунов и других деталей.
Цветные металлы и сплавы
Медь – цветной металл, обладающий высокой тепло- и электропроводностью. Медь хорошо обрабатывается давлением в холодном и горячем состоянии.
Чистая медь согласно ГОСТ 854-66 859-66 имеет 11 марок (М00б, М0б, М1б, М1, М2, М3 и т.д.) в зависимости от содержания вредных примесей в меди. Суммарное количество примесей (висмут, сурьма, мышьяк, железо, никель, свинец, олово, сера, кислород, фосфор) в лучшей марке М00б – 0,01% (то есть меди в ней 99,99%), а в марке М3 примесей 0,5%.
Одним из главным природным источником для получения меди служат сульфидные руды, содержащие халькопирит CuFeS2, называемый медным колчеданом, или другие сернистые минералы руды, например борнит 5Cu2S·Fe2S3, халькозин CuS и др.
Вторым по значению источником получения меди являются окисленные медные руды, содержащие медь в виде куприта Cu2O или азурита 2CuCO3·Cu(OH)2. Также известен теперь уже очень редкий, окисленный минерал меди – малахит CuCo3·Cu(OH)2.
Чистая медь розовато-красного цвета, плотность составляет 8,93 г/см3, температура плавления - 1083 ?С. Предел прочности чистой меди не очень высок и составляет 220 МПа. Чистую медь благодаря высокой электропроводности применяют для электротехнических целей (основная сфера применения меди). Также медь обладает высокой теплопроводностью и пластичностью.
Легирование меди обеспечивает повышение ее механических, технологических и эксплуатационных свойств. Различают три группы медных сплавов:
- латуни
- бронзы
- сплавы меди с никелем
Латуни
Латунями называют двойные (томпак, где 90% и более - меди и 10% цинка и полутомпак, где меди 79-86%Ю остальное цинк) или многокомпонентные сплавы на основе меди, в которых основным легирующим элементом является цинк. При введении других элементов (кроме цинка) латуни называют специальными по наименованию элементов, например, железофосфорномарганцевая латунь и т.п.
По сравнению с медью латуни обладают большей прочностью, коррозионной стойкостью. Механическая прочность латуней выше, чем меди, и они лучше обрабатываются (резанием, литьем, давлением). Большим их преимуществом является более низкая стоимость, так как входящий в состав латуней цинк значительно дешевле меди.
Латуни нашли широкое применение в приборостроении, в общем и химическом машиностроении.
Латуни могут содержать до 40-45% цинка. При большем содержании цинка снижается прочность латуни и увеличивается ее хрупкость. Содержание легирующих элементов в специальных латунях не превышает 7-9%.
Медноцинковые латуни в соответствии с ГОСТ 15527-70 выпускают восьми марок.
Латуни обозначают начальной буквой Л, затем ставят цифру указывающую средний процент меди в этом сплаве.
Л96 – томпак, меди 96%, цинка 4%.
Латуни более сложного состава в обозначении имеют после буквы Л другую букву, а цифры, размещенные после цифры, указывающей процент меди, указывают процент добавок в марке латуни.
Все добавляемые к латуни элементы обозначают русскими буквами:
Ц – цинк
А - алюминий
О – олово
Н – никель
К – кремний
С - свинец
Мц – марганец
Ж – железо
Ф – фосфор
Б – бериллий
Цифры, помещенные за буквами, указывают среднее процентное содержание элементов.
ЛАЖМц66-6-3-2 – алюминиевожелезомарганцовистая латунь, содержащая 66% меди, 6% алюминия, 3% железа и 2% марганца, остальное составляет цинк.
По технологическому признаку латуни, как другие сплавы цветных металлов (алюминиевые, титановые, магниевые сплавы), подразделяют на:
- литейные (ГОСТ 17711-72)
- деформируемые (ГОСТ15527-70)
Бронзы
Бронзы (медь, олово) – сплавы меди с оловом, алюминием, кремнием, марганцем, свинцом, бериллием. В зависимости от введенного элемента бронзы бывают:
- оловянными,
- алюминиевыми,
- кремнистые
- марганцовистые
- свинцовистые
- бериллиевые
Бронзы обладают высокой стойкостью против коррозии, хорошими литейными и высокими антифрикционными свойствами и обрабатываемостью резанием.
Благодаря хорошим литейным качествам из бронз отливают пушки, колокола и статуи. Также бронзы используются при изготовлении арматуры газовых и водопроводных линий и в химическом машиностроении, где важна также высокая коррозионная стойкость бронз. Малый коэффициент трения и устойчивость к износу делает бронзы незаменимыми при изготовлении вкладышей подшипников, червяков и червячных колес, шестерен и других деталей ответственных и точных приборов.
Бронзы легируют для повышения механических характеристик и придания особых свойств. Введение марганца способствует повышению коррозионной стойкости, никеля – пластичности, железа – прочности, цинка – улучшению литейных свойств, свинца – улучшению обрабатываемостью.
Бронзы маркируют русскими буквами Бр. Справа ставят обозначение элементов, входящих в состав бронзы:
О – олово
Ц – цинк
С – свинец
А – алюминий
Ж – железо
Мц – марганец
Далее идут цифры, обозначающие среднее содержание дополнительных элементов в бронзе в процентах (цифры, обозначающие процентное содержание меди в бронзе, не ставят).
БрОЦС5-5-5 – бронза содержит по 5% олова, свинца, цинка, остальное – медь (85%).
Медно-никелевые сплавы
Медно-никелевые сплавы – это сплавы на основе меди, в которых основным легирующим компонентом является никель.
Нейзильберы (медь, никель, цинк) содержат 15% никеля, 20% цинка, остальное составляет медь.
Мельхиоры (меди около 80%, никеля около 20%, небольшие добавки железа и марганца ) обладают высокой коррозионной стойкостью, в частности, в морской воде. Широко применяется для изготовления украшений, столовых и чайных приборов.
Копель (медь, 43% никеля, 0,5% марганца) – специальный термоэлектродный сплав для изготовления термопар.
Манганин (медь, 3% никель, 12% марганца) – специальный сплав с высоким удельным электросопротивлением, используемый в электротехнике для изготовления электронагревательных элементов.
Алюминий – наиболее распространенный металл в земной коре (8,8%); в чистом виде он не встречается, зато минералов, содержащих алюминий очень много. Однако алюминиевыми рудами являются далеко не все из них. Основным сырьем для получения алюминия служат бокситы и нефелины.
Производство алюминия из бокситов состоит из двух основных процессов:
1) получения глинозема Al2O3 из бокситов
2) восстановления металлического алюминия электролизом из раствора глинозема в расплавленном криолите (Na3AlF6)
Первичный алюминий (ГОСТ 11069-74) делят на следующие группы:
- алюминий особой чистоты (марка А999)
- алюминий высокой чистоты (4 марки)
- алюминий технической чистоты
ГОСТом предусмотрены восемь марок, допускающих содержание примесей 0,15-1%. Название марки указывает ее чистоту. Например, марка А8 обозначает, что в металле содержится 99,8% алюминия, а в марке А99 – 99,99%, в марке А999 – 99,999%.
Алюминий – легкий металл серебристо-белого цвета. Наиболее важным свойством алюминия, определяющим его широкое применение в технике, является его небольшая плотность - 2700 кг/м3. Таким образом, алюминий приблизительно в три раза легче, чем железо.
Вторым важным свойством алюминия является относительно высокая электропроводность – более 50% электропроводности меди. Температура плавления алюминия зависит от его чистоты и колеблется в пределах 660-667 oС.
Также алюминий обладает хорошей теплопроводностью и теплоемкостью.
Имеет высокую стойкость против атмосферной коррозии и в пресной воде. На воздухе алюминий быстро окисляется, покрываясь тонкой пленкой окиси, которая не пропускает кислород в толщу металла, что и обеспечивает его защиту от коррозии.
Алюминий хорошо обрабатывается давлением, сваривается, но плохо поддается резанию. Для устранения таких отрицательных свойств как невысокая механическая прочность, большая усадка, трудность обработки резанием в алюминий вводят различные добавки. В сплавах алюминия полностью или частично устранены эти недостатки. Сейчас в технике известны сотни различных алюминиевых сплавов.
Алюминий и его сплавы широко применяются:
- в машиностроении (применение алюминия позволяет снизить вес автомобиля, самолета)
- электротехнике (алюминий менее дефицитен и встречается в природе более широко, чем медь; для проводов в летательных и транспортных аппаратах, воздушных линий электропередач)
- металлургии (для получения в чистом виде хрома, ванадия, для раскисления стали)
- в пищевой промышленности – обертки для шоколадных конфет, алюминиевые банки для напитков и т.д.
Также как и латуни, сплавы на основе магния и титана, алюминиевые сплавы делят на:
- деформируемые
- литейные
Деформируемые алюминиевые сплавы применяют для получения листов, ленты, проволоки и различных деталей методами обработки давлением: штамповкой, прессованием, ковкой.
В зависимости от химического состава деформируемые алюминиевые сплавы делят на несколько групп.
Деформируемые алюминиевые сплавы содержат 2-3 и более легирующих компонента в количестве 0,2-4% каждого.
Деформируемые обработкой алюминиевые сплавы можно подразделить на две подгруппы:
- не упрочняемые термообработкой
- упрочняемые термообработкой
Первые характеризуются невысокой прочностью, но хорошей пластичностью. К ним относятся сплавы алюминия с марганцем и магнием, содержащие его до 6%. Эти сплавы почти всегда однофазные. Они хорошо свариваются, устойчивы против коррозии и применяются для малонагруженных деталей, изготовляемых холодной штамповкой с глубокой вытяжкой, и для свариваемых конструкций. Упрочнение этих сплавов возможно только путем холодной деформации, так как упрочнение термической обработкой не удается.
АМц содержит 1% марганца.
Из группы деформируемых алюминиевых сплавов, упрочняемых термообработкой, наиболее распространены дуралюмины (или дюралюмины) - сплавы алюминия с медью, магнием, марганцем (для повышения коррозионной стойкости сплава). Также распространены сплавы алюминия с медью, магнием, марганцем и цинком (сплавы высокой прочности).
Дуралюмины маркируют буквой Д, после которой стоит цифра, обозначающая условный номер сплава.
Дуралюмины выпускают в виде листов, прессованных и катаных профилей, прутков, труб. Особенно широко применяют дуралюмины в авиационной промышленности и строительстве.
Д1 – содержит 4% меди, примерно по 0,5% магния, марганца, кремния.
Сплавы авиаль уступают дюралюминию в прочности, но более пластичны как в горячем, так и в холодном состоянии и поэтому используются для легких конструкций, требующих гибких и других деформаций при монтаже.
Литейные алюминиевые сплавы содержат почти те же легирующие компоненты, что и деформируемые сплавы, но в значительно большем количестве (до 9-13% по отдельным компонентам). Литейные сплавы предназначены для изготовления фасонных отливок.
Выпускают 35 марок литейных алюминиевых сплавов. По химическому составу их можно разделить на несколько групп, например, алюминий с кремнием или алюминий с магнием.
Сплавы на основе алюминия и кремния называют силуминами. Силумин обладает высокими механическими и литейными свойствами: высокой жидкотекучестью, небольшой усадкой, достаточно высокой прочностью, удовлетворительной пластичностью. Сплавы на основе алюминия и магния имеют высокую удельную прочность, хорошо обрабатываются резанием и имеют высокую коррозионную стойкость.
Первый алюминиевый завод построен в 1932 году, базируясь на электроэнергии первой советской Волховской электростанции. В 1933 году построен второй алюминиевый завод в Запорожье, который использовал энергию Днепрогэса.
Магний и сплавы на его основе
Магний – сребристо-белый металл. Магний самый легкий из технических цветных металлов, его плотность 1,738 г/см3, температура плавления 650 oС. Технически чистый магний непрочный, малопластичный металл с низкой тепло- и электропроводностью. Для улучшения прочностных свойств в магний добавляют алюминий, кремний, марганец, торий, церий, цирконий и подвергают термообработке.
При хранении магния на сухом воздухе на его поверхности образуется окисная пленка, предохраняющая его при небольшом нагревании (до 200 oС) от дальнейшего окисления. В этих условиях коррозионная стойкость чистого магния превышает стойкость малоуглеродистой стали. Однако на влажном воздухе его коррозия значительно усиливается. На него практически не действует керосин, бензин и минеральные масла. Однако он не стоек в водных растворах солей (кроме фтористых) и растворяется во многих минеральных и органических кислотах.
Магний – один из распространенных металлов в земной коре. В свободном состоянии магний не встречается, а является составляющей многих горных пород в виде карбонатов, силикатов или растворен в морской и озерной воде в виде хлоридов и сульфатов.
Для производства магния используют преимущественно карналлит (MgCl2, KCl6, H2O), магнезит (MgCO3), доломит (CaCO3, MgCO3) и отходы ряда производств, например, титанового.
Технически чистый магний (первичный) содержит 99,8-99,9% магния (ГОСТ 804-72).
Мг96 – 99,96% магния
Маркировка и химический состав магниевых сплавов приведены в ГОСТ 2581-78.
Магниевые сплавы широко применяют в транспортном машиностроении, особенно в авиации и ракетостроении.
В зависимости от способа получения магниевые сплавы, подобно сплавам алюминия, латуням, титановым сплавам, подразделяют на:
- литейные – эти сплавы используют в виде отливок
- деформируемые – сплавы используют в виде проката (листов, ленты, труб) и поковок
Термическая обработка
Термическая обработка сталей. Виды термообработки: отжиг, нормализация, закалка, отпуск
Термической обработкой (термообработкой) называют совокупность операций нагрева, выдержки и охлаждения твердых сплавов с целью получения заданных свойств за счет изменения внутренней структуры.
Так как основными параметрами термической обработки являются температура и время, то любой процесс термообработки может быть представлен графиком в координатах “температура-время”. Если термическая обработка состоит только из одной операции (нагрев-выдержка-охлаждение), то она называется простой, а если из нескольких операций - сложной.
примеры графиков термообработки: простой и сложной
Графики термической обработки: простой и сложной
Основными видами термической обработки являются:
Отжиг
Нормализация
Отпуск
Старение
Закалка
Отжиг заключается в нагреве сталей до температур выше фазового превращения с последующей выдержкой и медленным охлаждением сплава вместе с печью. В результате отжига получают структуру перлит с ферритом или цементитом, и сталь приобретает высокую пластичность и низкую твёрдость.
Отжигу подвергают отливки, поковки, прокат, заготовки из углеродистой и легированной стали.
Различают следующие виды отжига: неполный, полный, низкотемпературный, диффузионный и рекристализационный.
Если после нагрева охлаждение происходит не вместе с печью, а на воздухе, то такую операцию называют нормализацией. Получаемая структура после нормализации – мелкопластинчатая перлитного класса (перлит, сорбит, троостит).
Для низкоуглеродистых сталей структура и свойства после отжига и нормализации ничем не отличаются.
При этом операция нормализации дешевле отжига.
По этой причине для низкоуглеродистых сталей рациональней проводит нормализацию.
Отличия в структуре появляются с повышением содержания углерода.
Также существенно может отличаться структура после отжига и нормализации у легированных сталей.
Закалка – нагрев стали до температур выше фазовых превращений с последующим быстрым охлаждением со скоростью выше критической. Цель закалки – придать стали большую твердость.
После закалки сталь приобретает неравновесную метастабильную структуру и обладает высокой прочностью, твердостью, износостойкостью и повышенной хрупкостью. Закалка не является окончательным видом термической обработки.
Для устранения избыточных напряжений и повышенной хрупкости сталь после закалки обязательно подвергают отпуску.
Отпуск – нагрев закаленной стали до температур ниже фазовых превращений с последующим охлаждением.
В результате отпуска структура стали переходит к более равновесному состоянию, твердость снижается, а пластичность повышается.
В зависимости от температуры нагрева отпуск подразделяется на:
низкий (150–250 оС),
средний (300-450 оС),
высокий (500-700 оС).
С увеличением температуры отпуска повышаются пластические свойства и снижается прочность стали.
Самопроизвольный отпуск закаленных сталей при незначительном нагреве или без него, наблюдающийся с течением времени называют старением.
Улучшение. Закалку в сочетании с высоким отпуском называют улучшением. Его назначение – измельчение структуры, повышение механических свойств и повышение обрабатываемости стали резани
Виды химико-термической обработки:
Цементация
Азотирование
Цианирование
Алитирование
Цементация – процесс поверхностного насыщения стали углеродом при температуре 900-950 °С.
Цементацию применяют для получения высокой твердости поверхности (до 65 HRC), повышения износостойкости и усталостной прочности. Часто цементации подвергают детали, работающие при повышенном трении, одновременно воспринимающие слабые ударные нагрузки (зубчатые колеса, шейки коленчатых валов). После цементации сердцевина стали сохраняет определенную вязкость.
Для цементации обычно применяют углеродистые и легированные стали с содержанием углерода 0,2-0,3% . Глубина цементированного слоя – 0,2-2,5 мм.
Азотирование – процесс насыщения поверхности стали или чугуна азотом в среде диссоциированного аммиака при температуре 480-700 °С.
Азотирование применяют для упрочнения верхних слоев сплавов, повышения износостойкости, а также получения антикоррозионной поверхности.
Глубина азотированного слоя 0,1-0,8 мм.
Азотированию подвергают детали машин, работающие в условиях трения и знакопеременных нагрузок – зубчатые колеса, валики, шпиндели, гильзы моторов и насосов, кулачки, мерительный инструмент.
Цианирование – процесс, при котором поверхностный слой стали одновременно насыщается азотом и углеродом.
Различают цианирование:
низкотемпературное (530-560 °С)
высокотемпературное (820-870 °С)
Низкотемпературное цианирование применяют для режущего инструмента, высокотемпературное – для мелких зубчатых колес, болтов, гаек из конструкционных сталей.
Алитирование – химико-термическая обработка алюминием стальных и чугунных изделий. В результате термодиффузии на поверхности изделий образуется пленка окиси алюминия, которая обеспечивает повышение жаростойкости изделий.
Алитирование применяют для деталей, которые работают при высоких температурах, но не подвергаются большим силовым и ударным нагрузкам, а также не работающим на истирание. Алитирование применяют для деталей термических печей, вентиляторов.
Дата добавления: 2021-01-21; просмотров: 71; Мы поможем в написании вашей работы! |
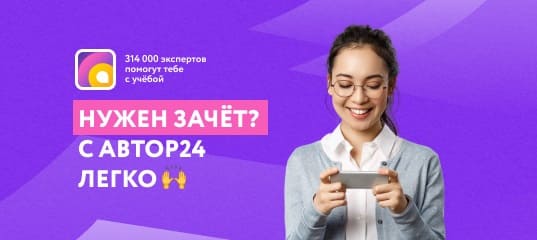
Мы поможем в написании ваших работ!