Характеристика процессов трения и изнашивания деталей подшипников
Подшипники коленчатых валов автотракторных двигателей работают в условиях граничной, полужидкостной и гидродинамической смазок.
По ГОСТ 27674 – 88 - смазка это действие смазочного материала, в результате которого между двумя трущимися поверхностями уменьшаются износ и повреждения поверхностей деталей и коэффициент трения. Классификация включает несколько видов смазки. Применительно к подшипникам коленчатого вала выделяют следующие виды смазки.
Граничная смазка – смазка, при которой трение и изнашивание поверхностей, находящихся в относительном движении, определяются свойствами поверхностей и свойствами смазочного материала, отличными от объёмной вязкости смазочного материала.
Гидродинамическая смазка – жидкостная смазка, при которой полное разделение поверхностей трения осуществляется в результате давления, самовозникающего в слое жидкости при относительном движении поверхностей.
Полужидкостная смазка – смазка, при которой осуществляется частично гидродинамическая, частично граничная смазки.
В условиях граничной смазки подшипники работают короткое время только в моменты пуска двигателя. Условия полужидкостной смазки возникают при работе двигателя на режимах, при которых максимальные нагрузки сочетаются с низкой частотой вращения коленчатого вала. Гидродинамическая смазка обеспечивается в условиях нормального режима работы двигателя. Вид смазки зависит от большого числа факторов.
|
|
Несущая способность подшипника
Параметром, характеризующим несущую способность подшипника, является коэффициент нагруженности (безразмерное число Зоммерфельда). Коэффициент нагруженности определяется по формуле
, (1)
где - среднее давление в подшипнике, Па;
– относительный зазор;
– динамическая вязкость, Па с;
– угловая скорость вала, рад/с.
Коэффициент нагруженности показывает, в каких условиях смазки работает подшипник. По его величине определяется минимальная толщина слоя смазки.
Минимальная толщина масляного слоя в подшипнике на режиме жидкостного трения равна
(2)
Взаимосвязь коэффициента нагруженности и относительного эксцентриситета, учитывающая конструктивные особенности подшипника (отношение длины подшипника к диаметру), показана на диаграмме рисунка 3.
Рисунок 3 Изменение коэффициента нагруженности в зависимости от эксцентриситета
Запас надёжности по толщине масляного слоя
Нарушение режима жидкостного трения будет в случае, если минимальная толщина масляного слоя достигнет значения, называемого критическим - .
|
|
Критическое значение определяется по формуле
, (3)
где и
шероховатости поверхностей вала и вкладыша.
Критической несущей способностью называют величину коэффициента нагруженности, при которой минимальная толщина масляного слоя достигает такого значения, что наступает соприкосновение неровностей профиля поверхностей вкладыша и вала, то есть
=
(4)
Запас надёжности работы подшипника по толщине масляного слоя определяется как отношение критического коэффициента нагруженности к рабочему:
(5)
При работе двигателя режим работы подшипников постоянно изменяется: изменяется нагрузка на подшипник, изменяется частота вращения коленчатого вала, в зависимости от температуры смазочного масла меняется его вязкость.
Для оценки работоспособности подшипников определяют несущую способность в диапазоне изменения параметров режима работы подшипника.
Из всех аргументов функции коэффициента нагруженности в процессе эксплуатации двигателя изменяется только один – относительный зазор в подшипнике. По мере увеличения зазора будет увеличиваться коэффициент нагруженности, будет увеличиваться и относительный эксцентриситет, минимальная толщина масляного слоя будет уменьшаться.
|
|
Зазор в подшипнике, при котором минимальная толщина масляного слоя достигнет критического значения, называется предельным.
Методика выполнения работы
Исходные данные для расчёта приведены в таблице 2.
Таблица 2 – Размеры деталей и параметры режима работы шатунных подшипников коленчатого вала двигателя ЗМЗ 40524.10
Параметры | Значения |
Диаметр нижней головки шатуна, мм | 60+0,019 |
Диаметр шейки вала, мм | 56-0,025-0,044 |
Толщина вкладыша, мм | 2,017 |
Ширина подшипника, мм | 26 |
Шероховатость поверхности вала, мкм | 1,3 |
Шероховатость поверхности вкладыша, мкм | 3,5 |
Диапазон средней нагрузки на подшипник, МПа | 1,5 – 4 |
Диапазон частоты вращения коленчатого вала, 1/мин. | 1000 – 3000 |
Динамическая вязкость масла, Па с. | 0,005 – 0,02 |
3.1 Определение несущей способности.
Коэффициент нагруженности определяется по формуле (1). Последовательность расчётов:
|
|
Нагрузка на подшипник: =4 МПа,
Зазор в подшипнике : минимальный Δмин.=60-2,007 2-55,975=0,011мм,
максимальный Δмакс.=60,019-2,007 2-55,956=0,049 мм.
Для расчёта принимают средний зазор Δсредн.=0,03мм.
Относительный зазор: =0,03/56=0,00054
Динамическая вязкость масла: =0,01 Па с.
Угловая скорость вала: =40рад/с.
Коэффициент нагруженности равен:
0,29.
Затем определяют критический коэффициент нагруженности. Определение критического значения коэффициента нагруженности начинают с определения критического значения минимальной толщины масляного слоя:
=1,3+3,5=4,8 мкм
Затем определяют значение относительного эксцентриситета:
=(0,015-0,0048)/0,015 = 0,68
По диаграмме Зоммерфельда (рис. 3) с учётом длины подшипника (k=l/d=26/56=0,46) определяют значение критического коэффициента нагруженности, =~0,8
3.2 Определение запаса надёжности по толщине масляного слоя
Запас надёжности работы подшипника определяется по формуле (5), тогда запас надёжности работы подшипника по толщине масляного слоя:
= 0,8/0,29 = 2,76
Так как двигатель работает в широком диапазоне нагрузки и частоты вращения коленчатого вала, запас надёжности работы подшипника определяется в диапазоне изменения всех параметров режима работы.
3.3 Влияние нагрузки на работоспособность подшипников
Для анализа влияния нагрузки на коэффициент запаса надёжности рассчитывают коэффициент запаса надёжности при 10 -15 значениях давления в диапазоне изменения нагрузки. Так как коэффициент запаса надёжности зависит не только от нагрузки на подшипник, но и от частоты вращения вала, расчёт производят на нескольких частотах (3 – 4 варианта – минимальной, средней и максимальной).
В таблице 3 приведены результаты расчёта коэффициента запаса надёжности при номинальном зазоре в подшипнике (0,03 мм) и вязкости масла 0,01 Па с.
Таблица 3 – Зависимость коэффициента запаса надёжности от нагрузки
Давление, МПа | Запас надёжности | |||
1200 об/мин. | 1800 об/мин. | 2400 об/мин. | 3000 об/мин. | |
1,5 | 3,72 | 5,58 | 7,43 | 9,29 |
1,7 | 3,28 | 4,92 | 6,56 | 8,20 |
1,9 | 2,93 | 4,40 | 5,87 | 7,34 |
2,1 | 2,65 | 3,98 | 5,31 | 6,64 |
2,3 | 2,42 | 3,64 | 4,85 | 6,06 |
2,5 | 2,23 | 3,35 | 4,46 | 5,58 |
2,7 | 2,06 | 3,10 | 4,13 | 5,16 |
2,9 | 1,92 | 2,88 | 3,84 | 4,81 |
3,1 | 1,80 | 2,70 | 3,60 | 4,50 |
3,3 | 1,69 | 2,53 | 3,38 | 4,22 |
3,5 | 1,59 | 2,39 | 3,19 | 3,98 |
3,7 | 1,51 | 2,26 | 3,01 | 3,77 |
3,9 | 1,43 | 2,14 | 2,86 | 3,57 |
На рисунке 4 дано графическое представление результатов расчёта. Как видно из графика, запас надёжности уменьшается по мере увеличения нагрузки, однако гидродинамическая смазка (коэффициент запаса надёжности больше единицы) обеспечивается во всём диапазоне нагрузки и частоты вращения коленчатого вала.
Рисунок 4 – Зависимость коэффициента запаса надёжности от нагрузки на подшипник и частоты вращения вала
Анализ влияние нагрузки на подшипник на минимальную толщину масляного слоя производится аналогично анализу влияния режима работы подшипника на коэффициент запаса надёжности. Для этого рассчитывают минимальную толщину масляного слоя при 10 -15 значениях давления в диапазоне изменения нагрузки. Так как минимальная толщина масляного слоя зависит не только от нагрузки на подшипник, но и от частоты вращения вала, расчёт производят на нескольких частотах (3–4 варианта) в диапазоне изменения скоростного режима.
Для определения минимальной толщины масляного слоя сначала определяют величину коэффициента нагруженности, затем по диаграмме Зоммерфельда (исходя из коэффициента нагруженности) определяют значение относительного эксцентриситета и затем минимальную толщину масляного слоя.
Для сокращения времени нахождения величины относительного эксцентриситета вместо диаграммы Зоммерфельда в учебных целях можно использовать аналитические выражения, полученные аппроксимацией кривых графика рисунка 3 для наиболее распространённых отношений длины подшипника к его диаметру:
для =0,3
;
для =0,4
;
для =0,5
.
В таблице 4 приведены результаты расчёта минимальной толщины масляного слоя при номинальном зазоре в подшипнике (0,03 мм) и вязкости масла 0,01 Па с. при различной нагрузке на подшипник и частоте вращения коленчатого вала.
Таблица 4 – Минимальная толщина масляного слоя при различной нагрузке на подшипник и частоте вращения коленчатого вала
В миллиметрах
Давление МПа | Минимальная толщина масляного слоя | |||
1200 об/мин. | 1800 об/мин. | 2400 об/мин. | 3000 об/мин. | |
1,5 | 0,0070 | 0,0081 | 0,0090 | 0,0097 |
1,7 | 0,0067 | 0,0078 | 0,0086 | 0,0093 |
1,9 | 0,0064 | 0,0075 | 0,0083 | 0,0089 |
2,1 | 0,0061 | 0,0072 | 0,0080 | 0,0086 |
2,3 | 0,0059 | 0,0069 | 0,0077 | 0,0084 |
2,5 | 0,0057 | 0,0067 | 0,0075 | 0,0081 |
2,7 | 0,0055 | 0,0065 | 0,0073 | 0,0079 |
2,9 | 0,0054 | 0,0063 | 0,0071 | 0,0077 |
3,1 | 0,0052 | 0,0062 | 0,0069 | 0,0075 |
3,3 | 0,0051 | 0,0060 | 0,0068 | 0,0073 |
3,5 | 0,0049 | 0,0059 | 0,0066 | 0,0072 |
3,7 | 0,0048 | 0,0057 | 0,0065 | 0,0070 |
Рис 5– Зависимость минимальной толщины масляного слоя от нагрузки на подшипник при разной частоте вращения коленчатого вала
На рисунке 5 дано графическое представление результатов расчёта. Как видно из графика, минимальная толщина масляного слоя существенно уменьшается с увеличением давления на подшипник. При низкой частоте вращения вала и максимальном давлении минимальная толщина масляного слоя достигает критического значения.
3.4 Влияние частоты вращения вала на работоспособность подшипников
Для анализа влияния частоты вращения вала на коэффициент запаса надёжности рассчитывают коэффициент запаса надёжности при 10-15 значениях частоты вращения в диапазоне изменения скоростного режима.
Таблица 5 – Зависимость коэффициента запаса надёжности от частоты вращения вала нагрузки при различной нагрузке на подшипник
Частота вращения вала об/мин. | Запас надёжности | |||
1,5 МПа | 2,3 МПа | 3,1 МПа | 4,0 МПа | |
1000 | 3,10 | 2,02 | 1,50 | 1,16 |
1200 | 3,72 | 2,42 | 1,80 | 1,39 |
1400 | 4,34 | 2,83 | 2,10 | 1,63 |
1600 | 4,96 | 3,23 | 2,40 | 1,86 |
1800 | 5,58 | 3,64 | 2,70 | 2,09 |
2000 | 6,19 | 4,04 | 3,00 | 2,32 |
2200 | 6,81 | 4,44 | 3,30 | 2,56 |
2400 | 7,43 | 4,85 | 3,60 | 2,79 |
2600 | 8,05 | 5,25 | 3,90 | 3,02 |
Так как коэффициент запаса надёжности зависит не только от скоростного режима, но и от нагрузки на подшипник, расчёт производят при нескольких величинах нагрузки (3–4 варианта) в диапазоне изменения нагрузочного режима.
В таблице 5 приведены результаты расчёта зависимости коэффициента запаса надёжности (при номинальном зазоре в подшипнике 0,03 мм и вязкости масла 0,01 Па с) от частоты вращения вала.
Рисунок 6 – Зависимость коэффициента запаса надёжности от частоты вращения вала и нагрузки на подшипник
Таблица 6 – Зависимость минимальной толщины масляного слоя от частоты вращения вала при различной нагрузке
Частота вращения вала об/мин. | Минимальная толщина масляного слоя, мм | ||||
1,5 МПа | 2,3 МПа | 3,1 МПа | 4,0 МПа | ![]() | |
1000 | 0,0065 | 0,0055 | 0,0048 | 0,0043 | 0,0048 |
1200 | 0,0070 | 0,0059 | 0,0052 | 0,0047 | 0,0048 |
1400 | 0,0074 | 0,0063 | 0,0056 | 0,0050 | 0,0048 |
1600 | 0,0078 | 0,0066 | 0,0059 | 0,0053 | 0,0048 |
1800 | 0,0081 | 0,0069 | 0,0062 | 0,0056 | 0,0048 |
2000 | 0,0084 | 0,0072 | 0,0064 | 0,0058 | 0,0048 |
2200 | 0,0087 | 0,0075 | 0,0067 | 0,0060 | 0,0048 |
2400 | 0,0090 | 0,0077 | 0,0069 | 0,0063 | 0,0048 |
2600 | 0,0092 | 0,0080 | 0,0071 | 0,0065 | 0,0048 |
2800 | 0,0095 | 0,0082 | 0,0073 | 0,0067 | 0,0048 |
3000 | 0,0097 | 0,0084 | 0,0075 | 0,0068 | 0,0048 |
На рисунке 7 дано графическое представление результатов расчёта. Как следует из графика, минимальная толщина масляного слоя достигает критической только в случае максимальной нагрузки при низких частотах вращения коленчатого вала.
Рисунок 7 – Зависимость минимальной толщины масляного слоя от частоты вращения вала при различной нагрузке
3.5 Влияние вязкости смазочного масла
Анализ влияния вязкости смазочного масла на работоспособность подшипника производится аналогично исследованиям влияния нагрузки и частоты вращения коленчатого вала.
Таблица 7 - Зависимость минимальной толщины масляного слоя от вязкости масла
Вязкость масла, Па с | Минимальная толщина масляного слоя, мм | |||
F=1,5 n=1000 | F=1,5 n=3000 | F=4 n=1000 | F=4 n=3000 | |
0,006 | 0,0049 | 0,0076 | 0,0030 | 0,0051 |
0,007 | 0,0053 | 0,0081 | 0,0033 | 0,0056 |
0,008 | 0,0056 | 0,0086 | 0,0036 | 0,0059 |
0,009 | 0,0060 | 0,0090 | 0,0038 | 0,0063 |
0,01 | 0,0063 | 0,0093 | 0,0041 | 0,0066 |
0,011 | 0,0065 | 0,0097 | 0,0043 | 0,0068 |
0,012 | 0,0068 | 0,0100 | 0,0045 | 0,0071 |
0,013 | 0,0070 | 0,0103 | 0,0047 | 0,0073 |
0,014 | 0,0072 | 0,0105 | 0,0048 | 0,0075 |
0,015 | 0,0074 | 0,0108 | 0,0050 | 0,0077 |
0,016 | 0,0076 | 0,0110 | 0,0051 | 0,0079 |
0,017 | 0,0078 | 0,0112 | 0,0053 | 0,0081 |
0,018 | 0,0080 | 0,0114 | 0,0054 | 0,0083 |
Изменяемым параметром в данном случае является вязкость смазочного масла (расчёт проводится для 10 – 15 значений вязкости в диапазоне, указанном в задании) для 3 вариантов режима работы подшипника:
– минимальная нагрузка, минимальная частота вращения вала;
– минимальная нагрузка, максимальная частота вращения вала;
– максимальная нагрузка, минимальная частота вращения вала;
– максимальная нагрузка, максимальная частота вращения вала;
В таблице 7 приведены результаты расчёта зависимости минимальной толщины масляного слоя (при номинальном зазоре в подшипнике 0,03 мм) от вязкости масла при различной нагрузке и частоте вращения вала.
На рисунке 8 дано графическое представление результатов расчёта.
Рисунок 8 – Зависимость минимальной толщины масляного слоя от частоты вращения вала при различной нагрузке
3.6 Анализ изменения работоспособности подшипника по мере изнашивания деталей
В процессе изнашивания поверхностей шейки вала и вкладыша увеличивается величина зазора в подшипнике. Это приводит к изменению положения центра вала относительно центра подшипника, минимальная толщина смазочного слоя уменьшается. Увеличение зазора приводит к полужидкостной, а затем и к граничной смазке в подшипнике. Величину зазора, при котором толщина масляного слоя достигает критического значения, называется предельной.
Для анализа влияния величины зазора в подшипнике и определения предельного зазора проводят анализ изменения толщины масляного слоя в зависимости от величины зазора во всём диапазоне нагрузочных и скоростных режимов работы подшипника. Для этого рассчитывают минимальную толщину масляного слоя при 10-15 значениях величины зазора в пределах от номинального до предполагаемого предельного (из литературных данных). Расчёт производят для 4 вариантов режима работы подшипника:
– минимальная нагрузка, минимальная частота вращения вала;
– минимальная нагрузка, максимальная частота вращения вала;
– максимальная нагрузка, минимальная частота вращения вала;
– максимальная нагрузка, максимальная частота вращения вала;
В таблицах 8 и 9 приведены результаты расчёта величины минимальной толщины масляного слоя при различной величине зазора в подшипнике и различной нагрузке на подшипник. Расчёты произведены для двух частот вращения коленчатого вала - 1200 об. в минуту и 2400 об. в минуту. На рисунках 8 и 9 приведена графическая иллюстрация результатов расчёта.
Таблица 8 – Величина минимальной толщины масляного слоя при различной величине зазора в подшипнике и различной нагрузке на подшипник (частота вращения коленчатого вала 1200 об. в минуту)
Зазор мм | Относит. зазор | Минимальная толщина масляного слоя, мм | |||
1,5 МПа | 2,3 МПа | 3,1 МПа | 4,0 МПа | ||
0,03 | 0,0005 | 0,0070 | 0,0059 | 0,0052 | 0,0047 |
0,04 | 0,0007 | 0,0074 | 0,0061 | 0,0053 | 0,0047 |
0,05 | 0,0009 | 0,0076 | 0,0062 | 0,0053 | 0,0046 |
0,06 | 0,0011 | 0,0077 | 0,0061 | 0,0052 | 0,0045 |
0,07 | 0,0013 | 0,0076 | 0,0060 | 0,0050 | 0,0043 |
0,08 | 0,0014 | 0,0075 | 0,0059 | 0,0048 | 0,0041 |
0,09 | 0,0016 | 0,0074 | 0,0057 | 0,0047 | 0,0039 |
0,1 | 0,0018 | 0,0072 | 0,0055 | 0,0045 | 0,0037 |
0,11 | 0,0020 | 0,0071 | 0,0053 | 0,0043 | 0,0036 |
0,12 | 0,0021 | 0,0069 | 0,0051 | 0,0041 | 0,0034 |
0,13 | 0,0023 | 0,0067 | 0,0049 | 0,0040 | 0,0033 |
0,14 | 0,0025 | 0,0065 | 0,0048 | 0,0038 | 0,0032 |
0,15 | 0,0027 | 0,0063 | 0,0046 | 0,0037 | |
0,16 | 0,0029 | 0,0061 | 0,0045 | 0,0037 | |
0,17 | 0,0030 | 0,0060 | 0,0044 | 0,0036 | |
0,18 | 0,0032 | 0,0058 | 0,0043 | 0,0036 | |
0,19 | 0,0034 | 0,0057 | 0,0042 | 0,0036 | |
0,2 | 0,0036 | 0,0055 | 0,0042 | ||
0,21 | 0,0038 | 0,0054 | 0,0042 | ||
0,22 | 0,0039 | 0,0053 | 0,0042 | ||
0,23 | 0,0041 | 0,0053 | 0,0042 | ||
0,24 | 0,0043 | 0,0052 | |||
0,25 | 0,0045 | 0,0052 |
Рисунок 9 – Зависимость величины минимальной толщины масляного слоя от величины зазора в подшипнике при различной нагрузке на подшипник ( частота вращения коленчатого вала 1200 об. в минуту)
Таблица 9 – Величина минимальной толщины масляного слоя при различной величине зазора в подшипнике и различной нагрузке на подшипник (частота вращения коленчатого вала 2400 об. в минуту).
Зазор мм | Относит. зазор | Минимальная толщина масляного слоя, мм | |||
1,5 МПа | 2,3 МПа | 3,1 МПа | 4,0 МПа | ||
0,03 | 0,0005 | 0,0090 | 0,0077 | 0,0069 | 0,0063 |
0,04 | 0,0007 | 0,0098 | 0,0083 | 0,0073 | 0,0065 |
0,05 | 0,0009 | 0,0103 | 0,0086 | 0,0075 | 0,0066 |
0,06 | 0,0011 | 0,0106 | 0,0087 | 0,0075 | 0,0066 |
0,07 | 0,0013 | 0,0108 | 0,0088 | 0,0075 | 0,0065 |
0,08 | 0,0014 | 0,0108 | 0,0087 | 0,0074 | 0,0064 |
0,09 | 0,0016 | 0,0108 | 0,0086 | 0,0073 | 0,0062 |
0,1 | 0,0018 | 0,0108 | 0,0085 | 0,0071 | 0,0060 |
0,11 | 0,0020 | 0,0107 | 0,0083 | 0,0069 | 0,0058 |
0,12 | 0,0021 | 0,0106 | 0,0082 | 0,0067 | 0,0056 |
0,13 | 0,0023 | 0,0104 | 0,0080 | 0,0065 | 0,0055 |
0,14 | 0,0025 | 0,0103 | 0,0078 | 0,0063 | 0,0053 |
0,15 | 0,0027 | 0,0101 | 0,0076 | 0,0062 | 0,0051 |
0,16 | 0,0029 | 0,0099 | 0,0074 | 0,0060 | 0,0050 |
0,17 | 0,0030 | 0,0097 | 0,0072 | 0,0058 | 0,0048 |
0,18 | 0,0032 | 0,0095 | 0,0070 | 0,0057 | 0,0047 |
0,19 | 0,0034 | 0,0093 | 0,0069 | 0,0055 | 0,0046 |
0,2 | 0,0036 | 0,0091 | 0,0067 | 0,0054 | 0,0046 |
Как видно из графика рисунка 9, при низкой частоте вращения коленчатого вала минимальная толщина масляного соя достигает критического значения при максимальной нагрузке уже при незначительном увеличении зазора (до 0,05 мм). Однако, на практике такие режимы встречаются крайне редко, поэтому для определения предельного зазора выбирают наиболее часто встречающиеся режимы.
На рисунке 10 показана зависимость величины минимальной толщины масляного слоя от величины зазора в подшипнике при различной нагрузке на подшипник при частоте вращения коленчатого вала 2400 об. в минуту.
Рисунок 10 – Зависимость величины минимальной толщины масляного слоя от величины зазора в подшипнике при различной нагрузке на подшипник ( частота вращения коленчатого вала 2400 об. в минуту)
Как видно из графика, в качестве предельного зазора можно установить зазор 0,16 мм.
Дата добавления: 2020-12-12; просмотров: 237; Мы поможем в написании вашей работы! |
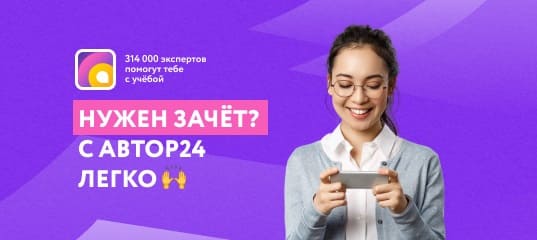
Мы поможем в написании ваших работ!