Технические условия на дефектацию деталей
Для обеспечения качества и эффективности ремонта дефектацию и сортировку надо проводить в строгом соответствии с техническими условиями, содержащимися в руководствах по КР.
Технические условия составляются в виде карт, которые по каждой детали в отдельности содержат следующие требования:
1. Общие сведения о детали – эскиз с указанием мест расположения дефектов; основные размеры деталей; материал и твердость основных поверхностей (все на рабочем чертеже).
2. Перечень возможных ее дефектов. Возможные дефекты – на основе опыта эксплуатации и ремонта автомобилей аналогичных моделей
3. Способы выявления дефектов – по опыту автомобилестроения и АПР с учетом научно-исследовательских работ.
4. Допустимые без ремонта размеры деталей.
5. Рекомендуемые способы устранения дефектов – по опыту технологии восстановления деталей отечественного и зарубежного АРП.
При разработке технологических условий на дефектацию деталей сложно определить допустимый размер детали (если неизвестна величина допустимого износа).
Допустимый диаметр вала при КР
d доп = d н - И доп ,
где dн - номинальный диаметр нового вала, мм
Идоп – величина допустимого износа вала, мм
Допустимым износом детали называется такой ее износ, при котором деталь, установленная при КР на автомобиль, проработает до следующего КР, и ее износ не превысит предельного износа (деталь будет безотказно работать в течение межремонтного пробега).
|
|
Детали с допустимыми износами можно использовать при сборке методами групповой взаимности или регулировки.
Для определения допустимого износа надо знать предельный износ детали.
Предельным износом называется такой износ детали, при котором ее дальнейшее использование невозможно. При этом деталь требует восстановления или замены.
Методика определения допустимого износа была разработана профессором В.В.Ефремовым.
Можно принять, что зависимость износа детали от наработки имеет линейный характер.
Идоп = Ипр – Им ,
где Им – величина износа детали за межремонтный пробег автомобиля (средняя арифметическая величина износа партии деталей, снятых с автомобилей).
Методы контроля, применяемые для дефектации деталей
Дефектацию деталей проводят в специальном порядке:
1. внешний осмотр деталей с целью обнаружения дефектов, видимых невооруженным глазом (трещин, пробоин, изломов, задиров, рисок, коррозии);
|
|
2. контроль деталей на специальных приспособлениях для обнаружения дефектов, связанных с нарушением взаимного расположения рабочих поверхностей и физико-механических свойств металла деталей;
3. контроль наличия скрытых дефектов (невидимых трещин, внутренних пороков);
4. контроль размеров и геометрической формы рабочих поверхностейдеталей.
Контроль взаимного расположения рабочих поверхностей
1. Контроль несоосности шеек валов (взаимного биения шеек) заключается в том, что замеряется радиальное биение каждой шейки, затем берется разность этих показаний. Вал при этом установлен в центрах, биение замеряется индикатором.
Радиальное биение шейки измеряется в следующей последовательности: стержень индикатора упирается в вал, обеспечивается натяг (1…2 оборота), вал поворачивается до тех пор, пока стрелка не займет крайнее положение. Индикатор устанавливается на ноль. Вал поворачивается на 1800 и определяется новое положение стрелки. Разность двух показаний есть радиальное биение шейки вала.
2. Контроль неперпендикулярности фланца к оси вала (торцовое биение) – разность наибольшего и наименьшего показаний индикатора (последовательность замера та же).
|
|
3. Контроль несоосности отверстий в корпусной детали производится на оптическом, пневматическом и индикаторном приспособлениях. При проверке несоосности на индикаторном приспособлении замеряют величину радиального биения отверстия. Радиальное биение – удвоенная величина несоосности (смещения осей) отверстий. Несоосность отверстий контролируют в блоках цилиндров, картерах КП, картерах редукторов и пр.
4. Контроль межцентровых расстояний и непараллельности осей отверстий производят путем измерения расстояний а1 и а2 между внутренними образующими контрольных оправок при помощи штихмаса или индикаторного нутромера.
Межцентровое расстояние
а1 + а2 d1+d2
А = ________ + _______ ,
2 2
где d1, d2 - диаметр контролируемых отверстий
5. Контроль неперпендикулярности осей отверстий производят при помощи оправки с индикатором или специальным калибром путем замера зазоров п1 и п2 на длине L. Величина неперпендикулярности в первом случае – разность показаний индикатора в 2-х положениях, а во втором – разность зазоров.
|
|
6. Контроль неперпендикулярности оси отверстий к плоскости осуществляется специальным индикаторным приспособлением или специальным калибром. В первом случае – это разность показаний индикатора при вращении его относительно оси отверстия, во втором – измерение зазором в двух диаметрально противоположительных точках и разность этих п1 и п2.
Дата добавления: 2021-01-20; просмотров: 113; Мы поможем в написании вашей работы! |
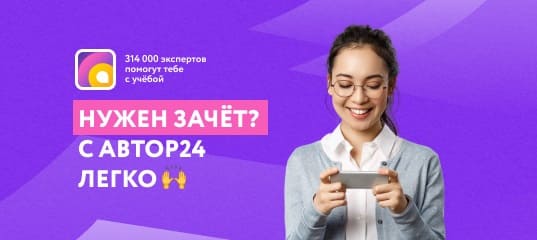
Мы поможем в написании ваших работ!