Эксплуатация судовых энергетических установок
ВВЕДЕНИЕ
Для успешного функционирования судоходной компании в условиях рынка квалифицированные и грамотные сотрудники имеют не меньшее значение, чем наличие современного флота. Поэтому теоретическая и практическая подготовка будущих специалистов должна быть полной и разносторонней.
Целью прохождения данной практики являлось закрепление знаний и навыков. Теоретически мы уже получили представление о судне, представляющем собой сложное инженерное сооружение, предназначенное для транспортных и производственных целей: рассчитывали план загрузки судна различными грузами с учетом их физико-химических, изучали устройство и конструктивные особенности судна.
Данная практика позволила нам ознакомиться с судном, с его оборудованием и с теми людьми, которые обеспечивают его жизнедеятельность.
Производственная плавательная практика была пройдена в ООО «Рыболовецкий колхоз им. В.И. Ленина» судно БМРТ «Сергей Новоселов».
Общее ознакомление с судном
Судомеханическая служба обеспечивает эксплуатацию судовых технических средств, находящихся в ее ведении в соответствии с расписанием по заведованиям и выполнение требований наставления по борьбе за живучесть судна.
В состав судомеханической службы входят: судовые механики, электромеханики, мотористы, другие специалисты, обслуживающие главные и вспомогательные механизмы, устройства и системы.
|
|
Организация любого трудового процесса на судах должна предусматривать необходимые мероприятия, обеспечивающие безопасность работающих.
Правильно организовать рабочие места и провести расстановку рабочей силы, а также обеспечить всех работающих спецодеждой и необходимыми индивидуальными защитными средствами – одна из главных обязанностей администрации судна. К основным мероприятиям по организации рабочих мест относятся: обеспечение безопасного доступа к рабочему месту, а в случае эвакуации – к спасательным средствам, обеспечение правильной передачи команд и распоряжений, устройство необходимых ограждений, защитных устройств, надписей, обеспечение работающих необходимым инструментом, приспособлениями и такелажем, осуществление специальных мероприятий в зависимости от специфики работ.
Палуба на рабочих местах, где по роду работ может быть скользко, должны иметь рифленую или ячеистую поверхность.
Рациональное планирование рабочих мест предполагает, прежде всего установление удобных и безопасных зон для выполнения трудовых операций и соответствующее размещение всего необходимого для работы оборудования.
Приспособления устанавливаются на палубе или стеллажах так, чтобы при качке судна, толчках или вибрации они не опрокидывались. Все тяжелые запасные части, приспособления надежно крепятся в положении по-походному в специально предусмотренных для этой цели местах.
|
|
Рабочие места нельзя размещать в опасных зонах. Эти зоны по характер у действия опасных факторов определяются временем и размерами, а следовательно, могут быть как постоянными, так и временными, то есть изменяющимися в размерах от времени и характера действия опасного фактора. Администрация судна, организуя работу вблизи опасных зон, обязана проверить наличие необходимых оградительных и защитных устройств, знаков и надписей. При отсутствии или неисправности – постоянных ограждений – устанавливаются временные. Согласно правилам ТБ ограждения устанавливаются на все открытые проемы в палубах, на рабочих местах, площадках, расположенных не выше 0,5 м. Кроме того, ограждаются все движущиеся части оборудования, а также трассы, расположенные в проходах и вблизи рабочих мест, места возможного прорыва горячей воды, пара, ядовитого газа и разброса твердых частиц. Ограждения проемов и площадок, расположенных на высоте, должны устанавливаться таким образом, чтобы исключить возможность травмирования работающих.
|
|
Организация труда машинной команды строится с учетом положений Устава службы на судах морского флота.
Главным лицом, ответственным за правильную организацию технической эксплуатации судна в целом, является капитан. Заместителем капитана по технической части является старший механик. Он составляет расписание по вахтам и заведованиям судомеханической части, планирует и организует труд машинной команды. Под организацией труда на судне подразумевается рациональное разделение функций членов машинной команды по технической эксплуатации установки. В условиях современного судна эти функции разделяются на контроль за процессами, протекающими в установке, и управление ими, и на ремонт судового оборудования. Первую функцию выполняют в процессе несения вахт, а вторую — в процессе судовых работ. Трудозатраты на контроль и регистрацию параметров можно снизить путем концентрации всех контрольно-измерительных приборов и сигнальных устройств на едином пульте управления. Это обеспечивается широким внедрением дистанционных контрольно-измерительных приборов, аппаратуры с автоматической записью параметров, систем предупредительной сигнализации и аварийной защиты. Для снижения трудозатрат на управление применяют автоматизацию процессов управления главными двигателями и вспомогательными механизмами путем внедрения систем дистанционного автоматизированного управления (ДАУ) и автоматических устройств обслуживания механизмов в условиях работы на переменных режимах. Контроль и управление значительно упрощаются при комплексной автоматизации установки. В этих условиях возможно уменьшение численности экипажа и применение более прогрессивных форм организации труда.
|
|
Такими формами могут быть:
обычное вахтенное обслуживание, но с уменьшенной численностью вахтенных вплоть до одного человека; вахтенное обслуживание в дневное время и безвахтенное в ночное. В этом случае надежность механизмов и средств автоматики должна обеспечивать их бесперебойную работу в течение не менее 16 ч, а регистрирующие устройства должны обеспечивать фиксацию параметров в объеме машинного журнала. На случай возможных аварий предусматривается система вызова дежурного специалиста в машинное отделение.
Несмотря на возможность уменьшения численности вахтенного персонала на комплексно-автоматизированных судах, для значительного уменьшения количественного состава машинной команды особых возможностей пока нет. Это объясняется тем, что наряду со снижением трудоемкости работ по контролю и управлению доля трудозатрат на техническое обслуживание установки даже несколько увеличивается. Так как доля трудозатрат на контроль и управление составляет примерно 35% общей суммы, а уменьшение ее при комплексной автоматизации 70 - 80%, то, следовательно, трудозатраты в целом уменьшаются всего на 20 - 30%. Профилактические и ремонтные работы составляют основную часть трудозатрат экипажа, что объясняется необходимостью значительного применения ручного труда.
Путями для снижения трудоемкости судовых работ являются: внедрение средств механизации, уменьшение объема профилактических и ремонтных работ, выполняемых силами судового экипажа, комплектация механизмов в необходимом количестве сменно-запасными деталями, дальнейшее повышение надежности судового оборудования. Механизация трудоемких процессов предусматривает, наряду с применением механизированного инструмента по очистке и окраске, использование механизированных приспособлений для монтажных и демонтажных работ на главных двигателях, вспомогательных механизмах и судовых устройствах, химических способов очистки цистерн и теплообменных аппаратов. Работы по техническому обслуживанию судового оборудования наряду с судовым экипажем осуществляют береговые ремонтные организации. Поэтому ССХ при составлении плана-графика профилактических и ремонтных работ по судну планирует береговым организациям работы, выполнение которых требует специального оборудования и квалификации исполнителей. Судовая команда в условиях плавания должна выполнять комплекс профилактических работ, сроки исполнения которых не совпадают с периодичностью заводского ремонта. Значительному упрощению ремонтных работ в судовых условиях способствует наличие необходимого комплекта сменных деталей. Дальнейшего снижения трудоемкости профилактических и ремонтных работ достигают проектированием и изготовлением судовой техники, обладающей высокой надежностью, большим моторесурсом, удобством в эксплуатации и ремонте. Существуют различные формы организации профилактических и ремонтных работ, о чем подробнее будет изложено далее.
Нормативно-организационная документация машинной команды
Техническая документация отражает технико-эксплуатационные показатели работы энергетической установки, оценивает деятельность обслуживающего персонала, устанавливает порядок технического обслуживания установки, учет топлива, масла и расходных материалов.
На судне должна быть основная (контролирующая) и исполнительная (по эксплуатации и ремонту) техническая документация.
К основной технической документации относятся: формуляры технического состояния главного двигателя и вспомогательных механизмов; правила технической эксплуатации и инструкции заводов-строителей; нормы расхода топлива и смазки; акты осмотров Регистра: табель снабжения судов морского флота, инвентарные книги сменно-запасных частей и деталей, инструментов, приспособлений и подъемно-такелажных средств; рабочие чертежи и технические условия изготовления и приемки сменно-запасных частей и деталей; сборочные чертежи главных и вспомогательных двигателей и их деталей; правила техники безопасности и противопожарной безопасности; приказы ММФ и циркуляры пароходств.
К исполнительной документации относятся: вахтенный машинный журнал; технический отчет; результаты индицирования и регулирования двигателей; месячный машинный отчет; графики планово-предупредительных ремонтов и осмотров; ведомости отчетности по запчастям, инструментам и материалам; ремонтные ведомости; акты инспекторских осмотров.
Основная документация. Технический формуляр главного двигателя отражает техническое состояние дизеля и является статистическим документом, в который заносят:
- общие конструктивные данные и основные паспортные характеристики;
- выявленные в процессе эксплуатации износы, дефекты, отказы, повреждения;
- профилактические и ремонтные работы, выполненные силами судовой команды и БРБ;
- учет количества наработанных часов.
На основании этих записей принимают профилактические меры, поддерживающие главный двигатель в надлежащем техническом состоянии. Записи дают технически обоснованные данные для ремонта двигателя.
Технические формуляры на отдельные механизмы прилагаются к механизму при выпуске его с завода-строителя. В них содержатся сведения о приеме механизма на заводе с указанием паспортных характеристик и результатов испытаний, основные требования по эксплуатации механизма, рекомендуемые параметры рабочих сред (для двигателей рекомендуемые сорта топлива и масла). В процессе эксплуатации в формуляр заносят сведения о работе и ремонте механизма.
Инструкции заводов-строителей и правила технической эксплуатации служат руководством для обслуживающего персонала в его практической работе с главными и вспомогательными двигателями, механизмами, системами трубопроводов и различными устройствами. В этих документах указывается строго обусловленный порядок обслуживания и ремонта. Указания в инструкциях заводов-строителей обязательны для выполнения и в тех случаях, если они расходятся с отдельными положениями правил технической эксплуатации.
Нормы расхода топлива и смазки задает ежеквартально отдел теплотехники пароходства на основании теплотехнических, стендовых и ходовых испытаний энергетической установки головного образца серии судов. Эти нормы рассчитывают соответственно заданной эксплуатационной мощности и технической скорости на судо-час работы судна. При температуре наружного воздуха +15° С и ниже к норме расхода топлива прибавляют так называемую зимнюю надбавку. В ходовом режиме при наличии утилизационного котла надбавку не устанавливают. Норму смазки задают на судо-час работы судна на ходу и стоянке.
Исполнительная документация. Вахтенный машинный журнал является первичным документом, отражающим техническую эксплуатацию энергетической установки. В нем регулярно по вахтенно регистрируют основные данные, характеризующие условия работы и изменения, происходящие с главными параметрами СЭУ. Журнал предназначен для составления материальной отчетности по топливу, маслам, расходным материалам и сведениям по эксплуатации и ремонту всех механизмов судна. Он является юридическим документом, используемым при рассмотрении причин аварий и несчастных случаев. При ведении журнала руководствуются инструкцией, напечатанной в начале журнала.
Технический отчет составляет старший механик за определенный срок работы энергетической установки и представляет в ССХ.
В техническом отчете указывают:
- рейсы, совершенные за отчетный период;
- число миль, пройденное в грузу и балласте;
- число часов работы главного двигателя и дизель генераторов за это время и с начала эксплуатации;
- состояние всего технического оборудования;
- результаты индицирования, выявленные дефекты газораспределения по диаграммам и меры, принятые к их устранению;
- результаты водоконтроля котлов;
- перечень работ по ППР и осмотру;
- фамилии механиков, обслуживающих энергетическую установку.
К техническому отчету прилагают: индикаторные диаграммы; накладные и паспорта на топливо и масло; акты о плавании судна в штормовую погоду, на мелководье, в битом льду; акты аварий, несчастных случаев и происшествий; планы различных мероприятий.
Результаты индицирования и регулирования двигателей представляют после каждого рейса.
Индикаторные диаграммы снимают на установившемся режиме работы двигателя при ходе судна в грузу и в балласте. Установившимся считается режим, при котором частота вращения вала двигателя, температура масла и охлаждающей воды становятся стабильными, т. е. после 2-4 ч работы двигателя не наблюдается их изменение.
По результатам планиметрирования и визуального изучения индикаторных диаграмм с учетом значений показателей двигателя, характеризующих его тепловой процесс, выявляют дефекты регулирования топливной аппаратуры и газораспределения и принимают меры по устранению дефектов.
Индикаторные диаграммы, на которых указана их площадь, длина и масштаб пружины индикатора, наклеивают на специальный бланк.
Месячный машинный отчет является основным документом, отражающим расходование горюче-смазочных материалов и регистрирующим среднесуточные значения параметров энергетической установки. Кроме того, в этом отчете отражается время работы главных и вспомогательных механизмов, средняя скорость судна, условия плавания и состав машинной команды, обслуживающей установку.
Перечисленные показатели работы энергетической установки и судна каждый день заносят в машинный отчет по данным вахтенного машинного журнала.
На основании ежесуточных показателей определяют число часов работы и стоянки главного двигателя, расход топлива и масла, а также число пройденных миль за отчетный месяц.
К месячному машинному отчету прилагают: заполненные бланки индицирования с наклеенными индикаторными диаграммами для каждого рабочего состояния судна (в грузу, балласте), накладные на принятое топливо, паспорта на принятые в течение месяца топливо и масло, двусторонние акты приема-сдачи топлива и масла другим судам или базам.
На основании месячного машинного отчета рассчитывают нормы расхода топлива, смазочных материалов и чистой технической скорости.
Для удобства нормирования и сравнительной оценки работы энергетической установки расчеты производят в условном топливе, теплота сгорания которого QS принимается равной 29288кДж. Для пересчета расхода натурального топлива в условное используют калорийные эквиваленты, устанавливающие соотношение между значением QS натурального и условного топлива.
Значения калорийных эквивалентов Экал. составляют для топлива: дизельного-1,454, моторного-1,35, мазута-1,4.Так как норма расхода топлива установлена в зависимости от мощности, развиваемой двигателем в условиях эксплуатации, то для расчета топливо использования необходимо определить фактическую мощность двигателя, отражающую его среднемесячную загрузку.
Учитывая, что номинальная мощность двигателя в эксплуатации по производственным, навигационным и метеорологическим причинам не выдерживается, для оценки среднемесячной загрузки двигателя определяют средневзвешенную мощность по результатам индицирования двигателя в различных условиях плавания.
Величину средневзвешенной мощности нормируют для данного судна на основании материалов теплотехнических испытаний. Фактическая средневзвешенная мощность для выполнения рейсовых заданий должна соответствовать нормативной средневзвешенной мощности.
Так как мощность двигателя и развиваемая судном скорость взаимосвязаны, то для оценки производственных показателей работы судна необходимо определение его скорости и соответствие ее заданным нормам.
Чистую техническую скорость задает судну служба эксплуатации пароходства. Фактическую скорость судна в течение месяца определяют по данным месячного машинного отчета. Сравнение фактической скорости с заданной позволяет установить результат выполнения нормативной скорости.
В соответствии с заданными эксплуатационными значениями мощности и скорости судна рассчитывают норму расхода топлива на ходу. При этом учитывается, что на режиме среднего хода расход топлива составляет 50% нормы полного хода, на режиме малого хода и маневрах-25%. За время стоянки судна также рассчитывают нормы расхода топлива.
Результаты топливо использования получают путем сравнения фактического расхода условного топлива с нормой расхода условного топлива на месяц. Расход условного топлива по нормам рассчитывают после определения средневзвешенной частоты вращения вала главного двигателя, средневзвешенной мощности, а также времени хода, стоянки с грузовыми операциями, стоянки без грузовых операций и времени на отопление в зимнее время. Зная норму условного топлива, израсходованного за месяц, и сравнивая ее с фактическим расходом условного топлива, определяют экономию (в тоннах или процентах). В случае перерасхода топлива указывают причины и мероприятия, направленные на повышение экономичности энергетической установки.
Графики ППР и осмотров являются основным отчетным документом судовой администрации о проведении ремонта энергетической установки без вывода судна из эксплуатации. Ремонтные ведомости являются первичным техническим документом, составляемым судовой администрацией под контролем ССХ перед постановкой судна на заводской ремонт в пределах утвержденного пароходством лимита или выделяемых ассигнований на ремонт.
Обязанности и права вахтенного механика
Вахтенный механик – Обязан:
Вахтенный механик непосредственно ответственен за М/О и полностью отвечает за безопасность и экономичность работ Главного и Вспомогательных двигателей на протяжении всей вахты. Прежде чем вахтенный механик возьмёт на себя ответственность за следующий период несения вахты, и сделает записи в журнал несения вахт, вахтенный механик должен выполнить полную проверку М/О и сделать запись в журнале. Прежде чем покинуть М/О и переключить управление М/О в без вахтенный режим, вахтенный механик должен выполнить окончательную проверку М/О не ранее чем за 30 минут до окончания рабочей смены и сделать заключительные записи в журнале несения вахт. Вахтенный механик не имеет права оставить М/О, в том случае, если он не может гарантировать работоспособность механизмов и сигнальных датчиков, и рабочем состоянии всех тревог. Проверки должны включать в себя и функции системы обнаружения пожара.
Передача вахты.
Вахтенный механик не должен быть освобожден от своих обязанностей, пока несение вахты формально не принята другим вахтенным механиком. При передаче вахты, вахтенный механик должен сообщить новому вахтенному обо всех вопросах, касающихся статуса всей машины.
UMS (Unattended Machinery Space) – Оставление М/О
Это – уведомитель вахтенного и/или ст. Механика о любом сбое или неисправности любого вышедшего из-под контроля механизма или системы аварийной сигнализации. После получения такой информации вахтенный и/или ст. Механик после консультаций с Капитаном решат, необходимо ли вернуться в М/О для продолжения несения вахты. Когда судном управляет UMS, механик прибывший на обход в М/О должен:
Сообщить на мостик о своём пребывании в М/О;
Сообщать на мостик по телефону с промежутками, не превышая 15 минут, или сработает тревога;
Сообщить на мостик об убытии из М/О, чтоб UMS возобновило свою работу.
Судовое заведывание и функциональные обязанности 4-го (3-го) механика. 2-ойи 3-ий Помощники Инженера (3-ий Механик)
Обязанности и ответственность
1.Запланировать все обязанности и рабочие места, назначенные на него.
2.Помогать 2-му механику с планированием обслуживания.
3.Поддерживать Судовую организацию и организацию Безопасности.
4.Замещать 2-го механика, когда необходимо.
5.Замещать Электрика, когда необходимо.
Особая ответственность
1.Держать и принять эффективное управление рабочего времени машинного отделения.
2.Чтобы диагностировать неисправности машины, примените средства судебной защиты, где только возможно, и сообщить.
3.Выполнить обслуживание как направлено.
4.Принимать особую ответственность за пункты и системы машины как направлено 2-м механиком, который может включать:
Главный Двигатель, включая всё оборудование с ним связанное, оборудование системы впрыскивания топлива и клапаны головки цилиндра
Двигатели генератора/Генератора переменного тока
Очистка смазочных и горючего
Все оборудование сжатого воздуха, установленные и портативны еe. Систем охлаждения
воздушного кондиционирования
Вся безопасность и противопожарная машина
Химикаты котловой воды и анализ котловой воды, чтобы гарантировать, что обращение котловой воды эффективно.
5.Иметь знание электрических систем и замещать Электрика в случае необходимости.
6.Наблюдать все установленные законом требования относительно загрязнения.
7.Выполнитьобязанности как требуется.
ПАМЯТКА:
У 4-го механика та же самая Особая ответственность; Главный инженер определит распределение этих обязанностей.
3-ий Помощник Инженера(4-ый Механик)
1.Запланировать все обязанности и рабочие места, назначенные на него.
2.Поддерживать Корабельную организацию и организацию Безопасности.
3.Замещать 2-ого Помощника Инженера, когда необходимо.
Особая ответственность
Особая ответственность -точно то же самое как таковые из 2-ого Помощника Инженера. Главный инженер определит распределение этих обязанностей.
Заведование:
1)Гидрофор.
2)Опреснительная установка.
3)Топливный сепаратор.
4)Масляный сепаратор (для В.Д.Г.)
5)Сепаратор льяльных вод.
6)Насосы для перекачки тяжёлого и дизельного топлив.
7)Воздушный компрессор хозяйственных нужд.
8)Вспомогательный котёл.
9)Утилизационный котёл.
10)Вспомогательные и аварийные двигатели.
11)Брашпили, шпили.
12)Грузовые краны.
13)Судовые аккумуляторы.
14)Двигатель спасательной шлюпки.
А так же:
15) Ежедневно замерять количество топлива и вести его учёт.
16) Производить замеры и знать количество фекальных масс.
17) Производить замеры топливных и масляных протечек.
18) Производить обслуживание всех судовыхмеханизмов на вахтенном уровне.
19) Оказывать содействие в работах по обслуживанию и ремонту судовых механизмов.
20) Знать политику работодателя и компании.
Участие в работах, типичных для машинной команды
Члены машинной команды, участвующие в судовых работах, перед выполнением каждой операции должны проходить инструктаж по технике безопасности на рабочем месте.
С внедрением на судах непрерывной системы технической эксплуатации большой объем судовых работ составляют разборка, ремонт и монтаж механизмов, выполняемые согласно графику профилактических осмотров и ремонтов.
Важную роль в обеспечении безопасности при ремонтных работах играет подготовка к выполнению ремонтных операций. Если в связи с ремонтом требуется снятие трапов, поручней, решеток, следует протянуть леер и вывесить табличку, запрещающую проход.
Дополнительное освещение должно отвечать требованиям безопасности и использоваться с соблюдением мер предосторожности. Переносная лампа должна надежно закрепляться, провод должен быть защищен от возможных повреждений. При работах в местах, где переборки и настил хорошо проводят электричество (внутри котлов, в картере двигателя, междудонных отсеках, цистернах), разрешается применять только переносное освещение напряжением не выше 12 В. Инструмент для выполнения работ должен соответствовать требованиям техники безопасности.
При демонтажных работах широко применяют грузоподъемные механизмы, которые перед использованием необходимо проверить. Механизмы, имеющие повреждения, применять запрещается.
Стропы не должны иметь повреждений и должны надежно крепиться на демонтируемой детали. Поднимать детали следует плавно, без рывков. Запрещается поднятую деталь оставлять на весу и стоять под грузом или находиться к нему ближе, чем на 1 м. Ослаблять или снимать тросы можно только после того, как деталь полностью опущена и закреплена. Во время работ на верхних решетках их следует застелить брезентом во избежание падения инструментов и деталей вниз.
Разбирать и ремонтировать оборудование и механизмы следует в строгом соответствии с инструкциями и утвержденной технологией. Нарушение последовательности операций при разборке, сборке и ремонте может явиться причиной разрушения обслуживаемого узла с нанесением травм членам машинной команды, выполняющим работу.
Устройства и механизмы, входящие в состав энергетической установки, монтируют и ремонтируют с соблюдением специальных правил техники безопасности, с которыми участвующие в выполнении ремонта должны быть ознакомлены механиком - руководителем ремонтных работ.
Особое место в судовых работах занимает химическая очистка систем и устройств. При использовании химикатов должны быть приняты меры предосторожности, исключающие отравление, поражение кожи и слизистых оболочек у членов экипажа, выполняющих работу. При работе с химическими растворами следует пользоваться спецодеждой и противогазовыми защитными средствами. Кроме того, должны выполняться мероприятия противопожарной безопасности. В цистернах можно работать после специального разрешения старшего механика. После вскрытия люков и горловин их ограждают. Освещение цистерн топлива и масла разрешается только взрывобезопасными низковольтными фонарями.
Цистерну перед ремонтом необходимо полностью освободить от остатков нефтепродуктов или воды, проветрить и дегазировать, пропарить, промыть щелочным раствором и горячей водой.
Если в цистерне находятся люди, у горловины должен быть выставлен дежурный для оказания помощи находящимся внутри цистерны. Перед закрытием горловины и люков следует убедиться в том, что в цистерне не осталось людей.
При выполнении работ по очистке и окраске поверхностей корпуса, механизмов и устройств должны соблюдаться специальные правила техники безопасности.
В заключение следует отметить, что какими бы полными не были правила техники безопасности при эксплуатации судовой техники, они не могут предусмотреть всех ситуаций, возникающих в процессе эксплуатации судового оборудования. Поэтому в технической эксплуатации командный и рядовой состав машинной команды должен ответственно относиться к любой операции, что обеспечит безопасность обслуживания и предотвратить случаи производственного травматизма.
Организация трудового процесса
Организация любого трудового процесса на судах должна предусматривать необходимые мероприятия, обеспечивающие безопасность работающих.
Правильно организовать рабочие места и провести расстановку рабочей силы, а также обеспечить всех работающих спецодеждой и необходимыми индивидуальными защитными средствами – одна из главных обязанностей администрации судна. К основным мероприятиям по организации рабочих мест относятся: обеспечение безопасного доступа к рабочему месту, а в случае эвакуации – к спасательным средствам, обеспечение правильной передачи команд и распоряжений, устройство необходимых ограждений, защитных устройств, надписей, обеспечение работающих необходимым инструментом, приспособлениями и такелажем, осуществление специальных мероприятий в зависимости от специфики работ.
Полы на тех рабочих местах, где по роду работ может быть скользко, должны иметь рифленую или ячеистую поверхность.
Рациональное планирование рабочих мест предполагает прежде всего установление удобных и безопасных зон для выполнения трудовых операций и соответствующее размещение всего необходимого для работы оборудования.
Приспособления устанавливаются на палубе или стеллажах так, чтобы при качке судна, толчках или вибрации они не опрокидывались. Все тяжелые запасные части, приспособления надежно крепятся в положении по-походному в специально предусмотренных для этой цели местах.
Рабочие места нельзя размещать в опасных зонах. Эти зоны по характеру действия опасных факторов определяются временем и размерами, а следовательно, могут быть как постоянными, так и временными, то есть изменяющимися в размерах от времени и характера действия опасного фактора.
Администрация судна, организуя работу вблизи опасных зон, обязана
проверить наличие необходимых оградительных и защитных устройств, знаков и надписей. При отсутствии или неисправности – постоянных ограждений – устанавливаются временные. Согласно правилам ТБ ограждения устанавливаются на все открытые проемы в палубах, на рабочих местах, площадках, расположенных не выше 0,5 м. Кроме того, ограждаются все движущиеся части оборудования, а также трассы, расположенные в проходах и вблизи рабочих мест, места возможного прорыва горячей воды, пара, ядовитого газа и разброса твердых частиц. Ограждения проемов и площадок, расположенных на высоте, должны устанавливаться таким образом, чтобы исключить возможность травмирования работающих.
Правила техники безопасности.
1. Общие требования ТБ.
2. ТБ при работе судов в открытом море.
3. Функции по охране труда капитана судна, старшего помощника
На всех опасных местах на судне необходимо вывешивать хорошо видимые плакаты, наносить предупредительные надписи и знаки безопасности. Инструкции, предупредительные надписи и плакаты по ТБ должны быть составлены на русском и на национальном языках республики, к порту которой приписано судно, причем, причем оба текста должны быть тождественны.
Как правило, вблизи механизмов, устройств и установок должны быть вывешены инструкции по безопасной их эксплуатации.
Каждый поступающий на судно член экипажа должен пройти вводный инструктаж по ТБ по ГОСТ 12.0.004-78 «Организация обучения работающих безопасности труда». Далее с поступающим проводится первичный инструктаж на рабочем месте в 2 этапа. Причем, второй этап – на рабочем месте с индивидуальным показом безопасных методов труда. Далее в течение 2...5 смен проводятся работы на рабочем месте под наблюдением квалифицированного работника; после чего оформляется в судовом журнале по ТБ допуск к самостоятельной работе.
Не реже 1 раза в 3 месяца начальники судовых служб проводят повторный инструктаж по ТБ всех своих подчиненных.
Внеплановый инструктаж по ТБ проводят начальники судовых служб при:
- изменении Правил ТБ,
-изменении технологического процесса, замене или модернизации оборудования,
- нарушении работником требований ТБ,
-перерывах в работе более 60 дней (для работ, к которым предъявляются повышенные требования ТБ -более 30 дней).-пересадка с судна на судно в море,
-выполнение погрузочно-разгрузочных работ на другом судне,
-привлечение к работам на подвахте по другому виду работ.
Текущий инструктаж проводят с работниками перед производством работ, на которые оформляют наряд-допуск (работы с повышенной опасностью). Перечень работ с повышенной опасностью определяет судовладелец. Ответственным руководителем работ с повышенной опасностью на судне является начальник судовой службы.
Проведение всех видов инструктажа кроме текущего, оформляется в судовом журнале проф.работы по ТБ с обязательной подписью получившего инструктаж и лица, его проводившего. Командный состав судна обязан ежегодно проходить проверку знаний по ОТ, проводимой работниками служб ТБ – членов комиссии по проверке знаний по специальности.
Судовладелец организует ежегодную проверку знаний судовых специалистов не относящихся к командному составу (обычно на судне). Контроль и непосредственная ответственность за соблюдение Правил ТБ во время всех видов судовых работ возлагается на лицо командного состава, непосредственно возглавляющего его работу.
При производстве ремонтных работ на судне, ответственность за соблюдение Правил ТБ возлагается на старшего помощника капитана илист. Механика, а также начальника судовых служб, в зависимости от характера ремонтных работ. При производстве погрузочно-разгрузочных работ на борту другого судна, ответственность за соблюдение Правил ТБ возлагается на ст. Помощника капитана этого судна.
Если действие лица, находящегося на судне, угрожает безопасности судна, здоровью окружающих, капитан может принять все необходимые меры, вплоть до изоляции в отдельном помещении.
При возникновении несчастного случая он подлежит расследованию и учету в соответствии с «Положением о расследовании и учете несчастных случаев на производстве». Регистрацию Н.С. на судне ведет ст. Помощника капитана в журнале регистрации Н.С. ответственность за своевременное расследование Н.С. несет капитан судна.
Все рабочие места, расположенные на высоте 0,75 м и более должны иметь ограждение. Во всех местах возможного пребывания и перемещения людей (палубы, служебные и санитарно-бытовые помещения) должны предусматриваться штормовые поручни. Все рабочие места и проходы должны быть очищены от посторонних предметов, снега, льда, рыбных отходов и т.п., при необходимости палубы следует посыпать песком. Запрещается ношение колец, серег и других украшений.
Общее ознакомление
Практику проходил на судне «Сергей Новоселов» (рис. 1).
Рис. 1. БМРТ «Сергей Новоселов»
Характеристика судна
БМРТ «Сергей Новоселов»
Экипаж - 100 человек
Район плавания - Тихий океан,
Водоизмещение - полное (по грузовую марку) 3800 т
Валовая вместимость - 3834
Чистая вместимость - 1150
Длина, наибольшая - 83,9 м
Длина по KBJI - 79,20 м
Длина между перпендикулярами 75,00 м
Ширина на миделе - 14,00 м
Высота борта до главной палубы па миделе - 7, 40 м
Высота до верхней палубы па миделе - 10,20 м
Осадка по конструктивную ватерлинию - 5,40 м
Осадка средняя при выходе на промысел - 5,57 м
Осадка средняя порожнем - 4,3 1 м
Наибольшая допустимая осадка - 5,72 м
Высота надводного борта
(определена по условиям непотопляемости) - 1,72 м
Якорь «Холла» - 3 х 200 кг
Длина якорь-пени - 2 х 250 м
Калибр якорь-цепи - 43 мм
Вес одной смычки якорь-цепи - 1085 кг
Позывные судна - ЕМАХ
Главный двигатель и его характеристика:
Марка, тип двигателя – ССУ 64Н 40/46
Количество цилиндров - 6-ти цилиндровый
Общая мощность главного двигателя – 5152 кВт.
Эксплуатация судовых энергетических установок
Технико-экономические показатели эксплуатации судовой энергетической установки
Регулирование двигателей должно обеспечивать равномерное распределение нагрузки по всем рабочим цилиндрам, нормальную температуру выпускных газов, максимальное давление цикла, бездымное сгорание топлива при номинальной мощности двигателя. Регулирование двигателей выполняется при установившемся режиме работы и постоянной нагрузке.
Основными операциями по регулированию двигателей являются:
1. Регулирование зазоров в клапанах.
2. Проверка и регулирование фаз газораспределения.
3. Регулирование угла опережения подачи топлива.
4. Проверка и регулирование топливной аппаратуры.
5. Проверка распределения нагрузки по цилиндрам.
6. Проверка «нулевого» положения топливных насосов.
Регулировка параметров рабочего процесса
Регулировка параметров рабочего процесса должна производиться в соответствии с указаниями инструкции по эксплуатации. Подрегулировку параметров следует производить на установившемся режиме при мощности и частоте вращения дизеля, максимально близких к заданным.
Неравномерность распределения параметров рабочего процесса по цилиндрам, характеризуемая отклонением от среднего значения, не должна превышать указанных ниже значений, если в инструкции не оговорены другие отклонения:
1. среднее индикаторное давление ±2,5%;
2. максимальное давление сгорания ±3,5%;
3. давление конца сжатия ±2,5%;
4. среднее давление по времени ±3%;
5. температура выпускных газов ±5%;
Примечание. При контроле температуры выпускных газов на дизеле с импульсной системой наддува следует ориентироваться не на ее отклонение от среднего значения по цилиндрам, а на отклонение от результатов стендовых или ходовых испытаний.
Регулирование параметров рабочего процесса путем изменения цикловой подачи топлива или угла опережения подачи топлива, допускается только в тех случаях, когда имеется уверенность в исправной работе топливной аппаратуры (топливных насосов и форсунок), механизма газораспределения, а также в исправности контрольно-измерительных приборов. Рекомендуется каждый раз до выполнения регулировочных работ проверять работоспособность форсунки (путем ее замены). Регулировка на основании случайных замеров или замеров на кратковременных недостаточно установившихся режимах запрещается.
После выполнения регулировочных работ, связанных с возможностью нарушения нулевой подачи топливных насосов высокого давления, она должна быть проверена и установлена до пуска дизеля.
Результаты регулировки необходимо заносить в журнал индицирования. Запись о регулировке вносится в машинный журнал.
Инструмент, приспособления, материалы для технического обслуживания и ремонта судовой энергетической установки, других механизмов
Современная практика ориентируется на применении электронных индикаторов, обладающих практически неограниченными возможностями по частоте (до 2000 об/мин) и погрешность используемых датчиков давления ограничивается 0,2%. Классическим примером электронного индикатора давления может служить «MIPCalculator» фирмы Аутроника, предоставленный далее на рисунке;
В комплект индикатора входят:
Персональный компьютер с программным обеспечением по обработке индикаторных диаграмм и принтером;
Переносные или стационарно устанавливаемые теизодатчики давления газов с пределами измерения до 10,15 или 20 Мпа и точностью ±1%; допустимая температура 300ºС.
Переносной теизодатчик давления топлива с пределами измерения 0 –100 или 200 МПа и точностью ±1%. Допустимая температура 150º.
Теизодатчик давления надувочного воздуха, точность ±0,5%;
Индуктивный датчик для точного определения положения рабочего поршня и скорости вращения вала. На моховик или вал двигателя одевается лента со штырями, расположенными по окружности через каждые 12 градусов, и штырем, соответствующим положению поршня цилиндра N1в ВМТ. При прохождении штырей мимо датчика в нем индуцируется ЭДС с амплитудой в 5 Вольт. В компьютере расстояние между соседними штырями делится на 12 частей и, благодаря этому компьютер обрабатывает индикаторную диаграмму с частотой в 1 градус п.к.в.
Снятые с двигателя диаграммы обрабатываются в компьютере и по запросу оператора на экране монитора высвечиваются как сами диаграммы, так и результаты обработки, включающие:
По индикаторной диаграмме:
Среднее индикаторное давление;
Макс. Давление сгорания;
Давление сжатия;
Давление за 36º после ВМТ, позволяющие судить о степени догарания топлива по ходу расширения;
α Pmax–положение точки α Pmax по отношению к ВМТ, позволяющее судить о том, как сориентировано сгорание топлива;
мощность цилиндра;
давление надувочного воздуха;
По диаграмме давления впрыска:
максимальное давление впрыска;
давление начала впрыска (открытия иглы);
угол опережения;
продолжительность подачи топлива.
В памяти компьютера могут сохранятся ранее снятые диаграммы, полученные на двигателе в исправном состоянии и в типичных для него условиях работы (режим, внешние условия, топливо). В дальнейшем они могут использоваться в качестве эталонных. В последние годы появились переносные, очень компактные электронные индикаторы, включающие блок питания и обработки сигналов от датчиков и элементы памяти. Зашифрованные в памяти измерения в последующем переносятся в компьютер ив нем осуществляется их обработка.
Оценивая индикаторы, важно также отметить, что наличие длинного индикаторного канала вызывает определенные искажения в измеряемые давления. Более того, канал при длительной работе забивается отложением кокса, нарушающими процесс передачи импульса давления газов из камеры сгорания, что, в свою очередь вносит искажения в величину фиксируемых давлений.
Конструкторы пытались избавиться от канала, опустив датчик в камеру сгорания. Но это требовало перехода на новые конструктивные решения и материалы для чувствительного элемента, которые в течение длительного времени выдерживали бы температуры более 500-600ºС.Фирмой MANB&W, для новых двигателей с электронным управлением в целях осуществления непрерывного контроля, за рабочими процессами в цилиндрах был разработан теизодатчик, вставляемый в просверленный в крышке цилиндра канал и прочно удерживаемый в контакте с металломкрышки. Канал глухой и соприкосновение датчика с горячими и агрессивными газами отсутствует, температуры в месте его установки не превышают 200º.
Пневмоиндекаторы
Принцип работы -измерение давления в камере сгорания при подаче воздуха через расходомерное устройство, в котором поддерживается постоянный перепад. Прибор позволяет обнаружить на ранней стадии повреждения цилиндро-поршневой группы с большей точностью, чем другими методами при меньших затратах. Подсоединение прибора -через индикаторный кран или специальный переходник, устанавливаемый вместо форсунки. Для определения углов подачи ТНВД пневмоиндикатор подсоединяется к нагнетательному штуцеру насоса. Прибор используется также для определения плотности, путем измерения максимального давления, при проворачивании ВПУ.ПИ-2М удобен в эксплуатации и обладает небольшими габаритами.
Индикаторная диаграмма
Процессы, происходящие в цилиндрах поршневого двигателя, помимо круговой диаграммы, могут быть изображены в виде индикаторной диаграммы, названной так потому, что ее вычерчивает особый прибор - индикатор (от латинского слова - indico, что значит указываю, определяю). Индикаторная диаграмма - это графическое отображение изменения давления газа в цилиндре поршневого двигателя в зависимости от перемещения поршня или утла поворота кривошипа. Если индикатор вычерчивает кривую линию, которая показывает, как изменяется давление в цилиндре в зависимости от угла поворота кривошипа, то такая диаграмма называется развернутой.
Положение любой точки на кривой этой диаграммы определяет величину давления в цилиндре при соответствующем угле поворота вала. Развернутая индикаторная диаграмма показывает, например, что наибольшее давление в цилиндре дизеля 10Д100 8,72 МПа (89 кгс/см2) достигается при угле поворота кривошипа нижнего коленчатого вала, равном 7° после в. м. т.
По этой диаграмме может быть получена (пересчетом) кривая изменения температуры газов в цилиндре в зависимости от угла поворота кривошипа. На так называемой свернутой индикаторной диаграмме (рис. 25) изменение давления дано в зависимости от положения поршня.
Рис. 25. Индикаторная диаграмма дизеля без наддува Участок 3—А, выделенный на рис. 26, а, соответствует горению топлива при постоянном объеме. Такой процесс, называемый изохорным (слово «изохорный» происходят от греческих слов isos—равный, одинаковый и chora—место, пространство, занимаемое чем-нибудь), возможен только при очень быстром, почти мгновенном сгорании топлива. Однако практически в двигателе с самовоспламенением от сжатия вся порция жидкого топлива не может быть впрыснута в цилиндр мгновенно и тем более мгновенно сгореть.
Рис.26. Графическое изображение процессов горения в координатах p-V (давление - объем): а) сгорание смеси при постоянном объеме (изохорный процесс); б) сгорание смеси при постоянном давлении (изобарный процесс)
Поэтому часть топлива сгорает не при постоянном объеме, а за время перемещения поршня на величину AS (рис. 26, б). В этот период постепенного (а не мгновенного!) сгорания топлива давление газов в цилиндре не повышается, а остается постоянным (изобарный процесс, слово «изобарный» происходит от isos и греческого baros, что означает вес, тяжесть), так как при перемещении поршня одновременно увеличивается объем газов в цилиндре. На рис. 26, б (справа) выделена линия А - 4, изображающая горение топлива при постоянном давлении. Рабочий цикл дизеля называется циклом со смешанным сгоранием (линия 3-А-4 на рис. 25), так как на линии 5-Б имеет место изохорическое сгорание, а на линии А-4 -изобарическое. Для большей наглядности отдельные участки индикаторной диаграммы четырехтактного дизеля без наддува представлены на рис. 27.
Рис. 27. Графическое изображение отдельных участков индикаторной диаграммы для дизеля без наддува и соответствующие положения поршня в цилиндре
Из всех процессов, с которыми мы познакомились, только во время одного процесса А-Б (см. рис. 25) совершается полезная работа. Остальные процессы являются вспомогательными, и на их выполнение затрачивается некоторая часть полезной работы, создаваемой в соседних цилиндрах.
Рассмотрим более подробно процесс, происходящий от точки 3 до точки 4.Как указывалось выше, в конце сжатия в цилиндр подается топливо, которое воспламеняется. Предположим, что сгорание внутри цилиндра дизеля происходит настолько быстро, что поршень почти не успевает переместиться (см. рис. 26, а), т. е. будем считать, что объем цилиндра, ограниченный поршнем, практически за это время не изменится. Это, как указывалось, означает, что процесс горения топлива осуществляется при постоянном объеме, т. е. работа по перемещению поршня не совершается (работа равна нулю). На что же в таком случае идет тепло, выделяющееся при сгорании? Оно идет на нагревание рабочего тела. А с повышением температуры рабочего тела возрастает давление в цилиндре, объем которого в данном случае не меняется. В действительной индикаторной диаграмме изохорный и изобарный процессы четко не разграничены, а наоборот, первый постепенно переходит во второй, т. е. процесс сгорания происходит сложнее. Свернутая индикаторная диаграмма двухтактного дизеля показана на рис. 28. Легко видеть, что в отличие от четырехтактного дизеля, здесь отсутствуют такты впуска воздуха и выпуска.
Рис. 28. Индикаторная диаграмма двухтактного двигателя
По мере развития тепловых двигателей и увеличения их быстроходности совершенствовались и индикаторные приборы. Простые по устройству механические индикаторы уступили место более сложным, которые позволяют не только получать индикаторные диаграммы отдельных процессов и судить о правильности их протекания, но даже наблюдать эти процессы непосредственно на экране (визуальные наблюдения).
Среднее Индикаторное Давление.
Во время перемещения поршня давление газов в цилиндре изменяется. Сила давления газов на поршень в связи с этим также является величиной переменной. Работа, как мы знаем, равна произведению силы да путь (перемещение). Таким образом, работа газов за рабочий цикл может быть подсчитана как сумма произведений давления в цилиндре на каждом маленьком участке (где это давление можно принять постоянным) на перемещение поршня на этом участке. Эта сумма соответствует площади индикаторной диаграммы. Таким образом, площадь диаграммы, очерченная линией 3-4-5-3 (см. рис. 25), выражает полезную работу газов, которую они совершают в цилиндре за один рабочий цикл. Однако оценивать работу цикла по площади индикаторной диаграммы во многих случаях неудобно.
Поэтому введено понятие среднего индикаторного давления. Условно приняли, что величина этого давления не изменяется, т. е. является постоянной (рис.29) в течение хода поршня.
Рис. 29. Определение среднего индикаторного давления
Тогда графически среднее индикаторное давление представляет собой высоту заштрихованного прямоугольника, площадь которого равна площади индикаторной диаграммы, а основание равно длине диаграммы. Средним индикаторным давлением называют условное, постоянное по величине давление, при котором работа за один цикл равна работе газов в цилиндре. В тепловозных дизелях среднее индикаторное давление pi находится в пределах 0,58-1,76 МПа (6-18 кгс/см2). Прежде чем перейти к подсчету работы и мощности дизеля, выясним, что такое энергия.
ПОНЯТИЕ ОБ ЭНЕРГИИ
Слово энергия происходит от греческого слова energia, что значит действие, деятельность. Различают энергию кинетическую и потенциальную. Кинетической энергией обладает любое движущееся тело: поезд, вода, ветер, пуля. Потенциальной, или скрытой, энергией обладает тело, находящееся на высоте.
Поднимем, например, боек молота на некоторую высоту и будем удерживать его в этом положении посторонней силой. На поднятие бойка нам пришлось затратить работу, которую нетрудно подсчитать, если его массу умножить на высоту подъема. Пока боек поднят, он обладает запасом потенциальной энергии, накопленной по мере того, как его поднимали. Если теперь отпустить боек, то вовремя падения потенциальная энергия переходит в кинетическую (энергию движения). Исчезнуть энергия не может: она только переходит из одного вида в другой. Это утверждение основано на известном законе сохранения энергии. На первый взгляд кажется, что когда, например, катящийся с горки вагон останавливается, то запас его кинетической энергии куда-то «исчезает». На самом деле кинетическая энергия переходит в тепловую при трении деталей тормозных устройств. Мы не замечаем этого потому, что нагревание окружающей среды незначительно. Зато мы можем увидеть покраснение тормозных колодок при резком торможении поезда.
Каждый вид энергии может переходить в другой, причем определенное количество «исчезнувшей» энергии одного вида даст эквивалентное (равноценное) ему количество энергии другого вида. Иными словами, каждая единица теплоты может дать строго определенное количество работы, и, наоборот, каждая единица работы может дать определенное количество теплоты. При работе двигателя внутреннего сгорания каждый килограмм жидкого топлива при сгорании выделяет определенное количество теплоты. Тепловой эффект любого вида топлива, в частности дизельного, характеризуется теплотой сгорания, т. е. тем количеством теплоты, которое выделяется при полном сгорании 1 кг данного топлива. Чем же измеряется теплота сгорания топлива? Количество теплоты измеряют в джоулях подобно тому, как сила измеряется в ньютонах, а длина - в метрах. Установлено, что 1 кг дизельного топлива при полном сгорании способен выделить тепла до 42 500 кДж (10 151 ккал). Сходство между теплотой и работой в том, что они подобны. Это вытекает из одного из основных законов термодинамики-науке о превращении теплоты и работы друг в друга.
Контрольно–измерительное оборудование для технического обслуживания, диагностики и ремонта судовой энергетической установки, других механизмов
У большинства двигателей можно проверить ось коленчатого вала, т.е. определить наличие возможного упругого прогиба его в процессе эксплуатации судна. В этом случае задача сводится к определению положения рамовых подшипников коленчатого вала, т.е. к определению просадокрамовых подшипников. Тем самым учитывается, что одна только проверка прилегания вала к рамовым подшипникам не дает еще основания считать, что вал равномерно нагружает все подшипники. Он, находясь даже под статическим действием одних сил собственного веса, может прогибаться так, что не будет касаться всех рамовых подшипников. Поэтому правильнее считать, что упругий прогиб коленчатого вала определяется величиной просадок его рамовых подшипников и шеек и тем самым, будет зависеть от износа последних.
При нормальных условиях работы двигателя неравномерность износа (просадки) отдельных рамовых подшипников вызывается разной по величине рабочей нагрузкой, приходящейся на них. Например, крайний (носовой) подшипник испытывает нагрузку лишь от работы одного цилиндра, тогда как на второй подшипник действует нагрузка от двух смежных цилиндров, что ведет к более интенсивному его износу.
К сказанному можно еще добавить, что при проверке зазоров в рамовых подшипниках можно узнать только величину зазора между верхним вкладышем и валом, но не то, какая доля этого зазора приходится на износ нижнего вкладыша, приводящего именно к проседанию вала.
Единственным критерием величины упругого прогиба вала принято считать просадку его на рамовых подшипниках, точнее, величину просадок этих подшипников (рамовых шеек) вала.
Таким образом, в процессе эксплуатации и ремонта производится определение просадки вала путем проверки положения рамовых шеек контрольными скобами и определение расхождения щек коленчатого вала снятием раскепов. Проверка просадки вала контрольной скобой состоит в следующем.
Рис. 1. Проверка положения рамовой шейки просадочной скобой
Скобу устанавливают над рамовой шейкой у замков крышки подшипника (рис.1). Замеряя расстояние, а между язычком скобы и шейкой вала и сравнивая этот размер с размером, полученным ранее, определяют величину просадки оси коленчатого вала в вертикальной плоскости. Замеряя расстояние б, проверяют возможное отклонение оси вала в горизонтальной плоскости, т.е. с борта на борт. Число таких замеров должно быть не менее двух на всей длине каждой рамовой шейки. Обычно двигатель имеет для рамовых подшипников контрольные скобы, изготовленные заводом-строителем, на которые набивают цифры замеров, полученные после заводской укладки вала. Замеры, полученные в процессе эксплуатации, сравниваются с заводскими и таким образом определяются изменения в положении коленчатого вала. При ремонте рамовые подшипники не всегда перезаливаются. Поэтому при проверке вала и шабровке подшипников замеры, снятые скобой, не будут равны замерам, указанным на скобе, но должны быть обязательно им пропорциональны. Выявление упругого изгиба вала по расхождению щек мотыля основано на определении изменения расстояний между щеками мотылей коленчатого вала, т.е. на измерении раскепов.
Рис. 2. Схема измерения раскепов между щеками мотылей коленчатого вала:а-раскепы со знаком (+), б-раскепы со знаком (-).
Наличие раскепа (рис.2) указывает на прогиб оси вала. Если середина вала будет лежать ниже крайних подшипников, то при верхнем положении шатунной шейки щеки мотыля разойдутся, (рис.2,а) и наоборот, если концы вала будут лежать ниже средних подшипников, то щеки разойдутся при нижнем положении мотыля (рис.2,б). Следовательно, по расхождению щек можно судить о направлении деформации вала в районе данного мотыля.
Так, если расстояние между щеками мотыля в верхней мертвой точке больше, чем в нижней, то ось вала изгибается выпуклостью вниз. В этом случае раскеп принято считать положительным, и пишется он со знаком плюс (+). Если расстояние между щеками мотыля в нижней мертвой точке больше, чем в верхней, то ось вала изгибается выпуклостью вверх -раскеп отрицательный и имеет знак минус (-). Если раскеп имеет положительный знак, то подшипники данного мотыля должны быть подняты, если отрицательный -опущены.
Рис. 3. Индикатор для измерения раскепов.
Раскепы измеряют микрометрическим штихмасом (с точностью до 0,01 мм) или индикатором (рис.3). Точки, между которыми производится замер, должны находиться посередине оси щек и отстоять от оси вала на расстоянии, равном радиусу шейки. Для того чтобы были видны изменения раскепов при последующих проверках по сравнению с предыдущими, точки, между которыми производятся замеры, должны быть одними и теми же. Поэтому в документации к проверке записываются положения точек замеров или прилагается эскиз с указанием мест их расположения. Замеры производятся при четырех положениях мотыля 0, 90, 180, 270. Если проверка ведется индикатором, то при проворачивании вала его рекомендуется оставлять на месте.
Во время поворота колен вала при измерении раскепа индикатор удерживается только силой трения, возникающей от давления пружины индикатора. Не следует дотрагиваться до индикатора и поворачивать его во время снятия показаний. Показания индикатора при повернутом вниз циферблате можно прочесть с помощью зеркальца. Если кривошипно-шатунный механизм двигателя собран, то при замерах раскепа мотыль несколько не доводят до верхней и нижней мертвых точек, т.к. при положении мотыля точно в н. м. т., а затем 90, 195 и 270. Штихмас нужно снимать после каждого замера раскепы, мм.
Рис. 4. Номограмма раскепов коленчатого вала:1 -допустимые раскепы; 2 -допустимые отклонения раскепов; 3 -требуется выравнивание линии вала; 4 -недопустимые величины раскепов.
Расхождение щек не должно превышать 0,0001S для всех мотылей, где S -ход поршня, мм. Пределом расхождения щек для двигателя, находящегося в эксплуатации, как указывалось, считается 0,00015S. При таком расхождении желательно произвести переукладку вала. Если расхождение щек превышает 0,00025S, то эксплуатацию двигателя нужно признать недопустимой.
Для решения вопроса о допустимости величины измеренного раскепа можно пользоваться номограммой раскепов коленчатых валов (рис.4).
Просадка коленчатого вала может быть изображена в виде кривой (рис.5). На этой номограмме показано влияние веса движущихся частей на ось коленчатого вала при навешенном механизме движения. Если при снятом механизме движении раскепы коленчатого вала резко изменились, это указывает на не плотность прилегания шеек вала к рамовым подшипникам. При укладке вала следует составлять подобную номограмму и руководствоваться ею при выравнивании оси коленчатого вала во время последующих ремонтов.
Рис.5. Номограмма просадки коленчатого вала:
а -номограммы замеров раскепов;
б -приведенная ось вала с учётом просадок рамовых подшипников;
-замеры принавешенном механизме движения;
-замеры при снятом механизме движения.
Зная относительный износ отдельных подшипников, лучше укладывать вал так, чтобы придавать преднамеренный подъем сильно изнашивающимся подшипникам. А так как больше других обычно изнашиваются средние подшипники, то стрелка прогиба вала, уложенного на приподнятых подшипниках, должна быть противоположна (иметь противоположный знак) по отношению к стрелке прогиба до ремонта.
Выравнивание оси коленчатого вала производится, как правило, с подъемом коленчатого вала. Однако на некоторых ДВС допускается выравнивание оси вала путем замены одного-двух подшипников без подъема вала.
Ремонт распределительных валов. У высокооборотных дизелей распределительные валы выполняются за одно целое с кулачками. У дизелей мало- и среднеоборотных обычно кулачковые шайбы делаются съемными. Распределительные валы этих дизелей имеют значительную длину. Поэтому они с целью удобства монтажа и демонтажа для ремонта выполняются составными. В силу различия конструкции распределительных валов высоко- и малооборотных двигателей методы дефектации валов и способы их исправления несколько различны.
Во время ремонта высокооборотного двигателя при дефектации распределительного вала осматривают все его рабочие поверхности и выявляют заусенцы, забоины, трещины, выкрашивания, следы коррозии; измеряют шейки вала; проверяют профиль кулачков и устанавливают степень износа шеек вала и степень изменения геометрической формы кулачков; проверяют прогиб вала. По результатам наружного осмотра и измерений в соответствии с данными технических условий ведется дефектация вала, и устанавливаются возможные способы его ремонта.
При установке прокладок необходимо удостовериться в их исправности. Прокладки должны иметь одинаковую толщину: складки, разрывы и морщины на них не допускаются. Медные использованные прокладки, годные к постановке, обязательно отжигать.
Гайки необходимо затягивать равномерно, без применения ударов, чтобы избежать деформации деталей. Последовательность и величина усилия затяжки гаек регламентируются специальной инструкцией. Шплинтовка ответственных деталей, например, шатунных болтов, анкерных связей, производится только новыми не бывшими в употреблении штатными шплинтами соответствующих размеров и материала. Контрольные и установочные штифты, шпильки и болты заводят на место до закрепления детали или узла.
Необходимо обращать внимание на бирки, марки, риски, определяющие правильное положение собираемых деталей и узлов, и на то, чтобы крепежные детали соответствовали им.
Трубопровод перед установкой очищают, промывают, продувают сжатым воздухом и устанавливают только тогда, когда есть полная уверенность в том, что он внутри совершенно чист. Войлочные сальники должны быть чистыми, упругими, без утолщений и повреждений. Перед установкой на место сальники пропитывают в нагретом масле.
Во время сборочных работ в МО необходимо соблюдать чистоту. Особенно тщательно следует предохранять от попадания грязи и песка на трущиеся поверхности детали, а также поверхности пришабренные, притертые, полированные и шлифованные. При сборке особое внимание следует уделять точности пригонки отдельных деталей двигателя, правильности взаимного положения их осей и плоскостей, центровки и точности регулировки двигателя после сборки. Малооборотные судовые дизели, как правило, оборудованы механическими индикаторными приводами, которые позволяют снимать с каждого цилиндра индикаторные диаграммы и затем по ним определять среднее индикаторное давление. Запись диаграмм осуществляется с помощью механического индикатора «Майгак», схема и внешний вид которого показаны на рисунке 2.5.
Индикатор устанавливается на индикаторный кран и закрепляется гайкой 9. Уплотнение достигается благодаря конической посадке корпуса индикатора и крана. Шнур 2 с помощью крючка на его конце подсоединяется к кольцу на тросике индикаторного привода. При включении привода шнур вместе с тросиком совершает возвратно-поступательные движения синхронно с движением поршня в данном цилиндре. Барабан 4 в нижней части имеет шкив, на который намотан шнур, а внутри -спиральную пружину, удерживающую шнур все время в натянутом состоянии. Движение шнура приводит к вращению барабана синхронно с движением поршня.
На барабан устанавливается и закрепляется держателем специальная мелованная бумага размером 50x140 мм. Нажим пера 3 (сменный бронзовый штифт) регулируется специальным винтом. При движении барабана и пишущего механизма на бумаге записывается индикаторная диаграмма. Измерение давления осуществляется поршнем 1 диаметром9,06 мм, который перемещается во втулке 8. Поршень через шток 7 нагружен пружиной б, имеющей строго определенную жесткость. В комплект индикатора входит набор пружин (8-10 шт.) с различной жесткостью. При воздействии давления на поршень шток 7 перемещается вверх, пружина растягивается. Со штоком связана система рычагов 5, обеспечивающая перемещение пишущего пера строго вертикально.
Каждая пружина имеет номер, по которому в прилагаемой к индикатору таблице определяется максимальное давление, которое можно измерить, и масштаб давлений. Масштаб mp имеет размерность мм/бар и показывает на сколько мм перемещается перо при воздействии на поршень давления в 1 бар.
Эксплуатация главных и вспомогательных двигателей и их систем управления
Настоящие Правила относятся к судовым дизелям всех типов и назначений, а также к системам, механизмам и аппаратам, обеспечивающим их функционирование. В тех случаях, когда отдельные предписанные операции не могут быть выполнены из-за конструктивных особенностей дизеля или его систем, они опускаются. При эксплуатации дизелей должны выполняться общие требования, изложенные в части I Правил.
Техническое использование судовых дизелей
1.Подготовка дизельной установки к действию и пуск дизеля
1.1. Подготовка дизельной установки к действию должна обеспечить приведение дизелей, обслуживающих механизмов, устройств, систем и трубопроводов в состояние, гарантирующее их надежный пуск и последующую работу.
1.2. Подготовка дизеля к работе после разборки или ремонта должна производиться под непосредственным наблюдением механика, в заведовании которого находится дизель. При этом необходимо убедиться в том, что:
1. все разбиравшиеся соединения собраны и надежно закреплены, обратив особое внимание на стопорение крепежных элементов;
2. выполнены необходимые регулировочные работы. Особое внимание должно быть обращено на установку нулевой подачи топливных насосов высокого давления;
3. все штатные контрольно-измерительные приборы установлены на место, соединены с контролируемой средой и не имеют повреждений;
4. при прокачке маслом при открытых картерных щитах смазка поступает ко всем подшипникам и другим точкам смазки;
5. защитные крышки, щиты и кожухи установлены на место и надежно закреплены;
6. трубопроводы топливной, масляной, водяной и воздушной систем, а также рабочие полости дизеля, топливных и масляных фильтров, теплообменных аппаратов и вспомогательные механизмов не имеют пропусков рабочих сред. Особое внимание должно быть обращено на отсутствие протечки охлаждающей воды через уплотнения цилиндровых втулок, а также на возможность попадания топлива, масла и воды в рабочие цилиндры или в продувочный (всасывающий) и выпускной ресиверы дизеля;
7. выполнена проверка форсунок дизеля на плотность и качество распыла топлива.
После перечисленных выше проверок должны быть выполнены операции, предусмотренные для подготовки дизельной установки к действию после непродолжительной стоянки (см. пп 1.3-1.9.11).
1.3. Подготовка дизельной установки к действию после непродолжительной стоянки, во время которой не выполнялись работы, связанные с разборкой, должна производиться вахтенным механиком и включать в себя операции, предусмотренные пп. 1.4.1-1.9.11. При экстренном пуске время подготовки можно сократить только за счет прогрева.
1.4. Подготовка масляной системы. При подготовке системы необходимо:
1. Проверить уровень масла в сточных цистернах или в картерах дизеля и редуктора, в маслосборниках и гравитационных цистернах турбокомпрессоров наддува, в масляных сервомоторах, в лубрикаторах, в регуляторе частоты вращения, в корпусе упорного подшипника, в цистерне смазки распределительного вала. При необходимости пополнить их маслом.
2. Убедиться в исправности устройств автоматического пополнения и поддержания уровня масла в цистернах, лубрикаторах.
3. Перед проворачиванием дизеля подать масло в рабочие цилиндры и к другим местам лубрикаторной смазки, а также ко всем точкам ручной смазки.
4. Подготовить к работе масляные фильтры и маслоохладители, установить клапаны на трубопроводах в рабочее положение. Пуск дизеля и его работа с неисправными масляными фильтрами запрещается. Дистанционно управляемые клапаны должны быть опробованы в действии.
5. При температуре масла ниже рекомендованной инструкцией по эксплуатации его необходимо подогреть. При отсутствии специальных нагревательных устройств масло прогревают путем прокачки его через систему во время прогрева дизеля (см. п. 1.5.4). Температура масла при прогреве не должна превышать +45°С.
1.5. Подготовка системы водяного охлаждения. При подготовке системы необходимо:
1. Подготовить к работе охладители и подогреватели воды, установить клапаны и краны на трубопроводах в рабочее положение, опробовать в действии дистанционно управляемые клапаны.
2. Проверить уровень воды в расширительной цистерне контура пресной воды и в цистернах автономных систем охлаждения поршней и форсунок. При необходимости пополнить системы.
3. Подготовить к работе и пустить автономные или резервные насосы пресной воды охлаждения цилиндров, поршней, форсунок. Проверить действие средств автоматизированного (дистанционного) управления основными и резервными насосами. Довести давление воды до рабочего, выпустить из системы воздух. Прокачку дизеля пресной водой производить в течение всего времени подготовки дизеля.
4. Прогреть охлаждающую пресную воду имеющимися средствами до температуры около 45°С на входе. Темп прогревания должен быть по возможности медленным. Для малооборотных дизелей скорость прогрева не должна превышать 10°С в час, если в инструкции по эксплуатации нет других указаний.
1.6. Подготовка топливной системы. При подготовке системы необходимо:
1. Спустить отстой из расходных топливных цистерн, проверить уровень топлива и при необходимости пополнить цистерны.
2. Подготовить к работе топливные фильтры, регулятор вязкости, подогреватели топлива, расходомеры.
3. Установить в рабочее положение клапаны на топливном трубопроводе, опробовать в действии дистанционно управляемые клапаны.
Подготовить к работе и пустить автономные насосы топливоподкачивающий и охлаждения форсунок. После подъема давления до рабочего убедиться в отсутствии воздуха в системе. Проверить действие средств автоматизированного (дистанционного) управления основными и резервными насосами. Если во время стоянки проводились работы, связанные с разборкой и опорожнением топливной системы, заменой или разборкой топливных насосов высокого давления, форсунок или форсуночных труб, удалить воздух из системы высокого давления путем прокачки насосов при открытых деаэрационных клапанах форсунок либо другим способом.
4. Если дизель конструктивно приспособлен для работы на высоковязком топливе, включая пуск и маневрирование, и был остановлен на высоковязком топливе на длительное время. обеспечить постепенный прогрев топливной системы (цистерн, трубопроводов, топливных насосов высокого давления, форсунок) путем включения обогревающих устройств и непрерывной циркуляции подогреваемого топлива. Перед пробными пусками дизеля температура топлива должна быть доведена до значения. обеспечивающего необходимую для качественного распыливания вязкость (9-15 сСт). Темп прогрева топлива не должен превышать 2°С в минуту, а время циркуляции топлива в системе должно быть не менее одного часа, если в инструкции по эксплуатации не содержатся другие указания.
1.7.Подготовка систем пуска, продувки, наддува, выпуска. При подготовке систем необходимо:
1. Проверить давление воздуха в пусковых баллонах, продуть из баллонов конденсат, масло. Подготовить к работе и пустить компрессор, убедиться в его нормальной работе. Проверить действие средств автоматизированного (дистанционного) управления компрессорами. Пополнить баллоны воздухом до номинального давления. Запорные клапаны на пути от баллонов к стопорному клапану дизеля открывать плавно. Продуть пусковой трубопровод при закрытом стопорном клапане дизеля.
2. Спустить воду, масло, топливо из ресивера продувочного воздуха, впускного и выпускного коллекторов, подпоршневых полостей, воздушных полостей воздухоохладителей, газовых и воздушных полостей турбокомпрессоров наддува.
3. Убедиться в том, что все запорные устройства газоотвода дизеля открыты.
Эксплуатация насосных систем и их систем управления
Все насосы, используемые на судах, делятся на две основные группы, а именно, объемные и центробежные.
В объёмных насосах объём рабочей камеры увеличивается при подъеме поршня, создается вакуум. В этот вакуум жидкость поступает через всасывающий патрубок. Затем поршень идет вниз, уменьшая объем камеры насоса, жидкость выталкивается через впускной клапан.
Простой поршневой объемный насос простого действия состоит из поршня, двигающегося вверх-вниз внутри камеры. Камера имеет невозвратные всасывающий и выпускной клапаны. Когда поршень идет вверх, в камере создается вакуум, жидкость поступает в камеру через всасывающий клапан, далее поршень идёт вниз, создавая давление в жидкости.
Поршневой насос двойного действия работает на том же принципе, что и простого действия. Его камера имеет всасывающий и возвратный клапаны в верхней и нижней своей части, жидкость может поступать и выталкивается при каждом ходе поршня.
Шестеренчатый насос –пример вращающегося объемного насоса, применяемого для перекачки смазочных масел и топлива, представляет собой взаимосоединенные шестерни, которые вращаются и каждый зуб, создавая давление, выталкивая жидкость. Жидкость, поступающая в эту полость, продвигается вокруг шестернями и выталкивается в выпускной патрубок.
Центробежный насос имеет крыльчатку, вращающуюся с большой скоростью внутри корпуса, жидкость поступает через всасывающий патрубок и выталкивается центробежной силой, возникающей при вращении крыльчатки в этом корпусе. Жидкость поступает через всасывающий патрубок в центре корпуса и выталкивается через выпускной.
Обслуживание судовых механических систем и их систем управления
В процессе эксплуатации детали судовых механических систем, машин и механизмов подвержены естественному износу, что приводит к изменению технико-эксплуатационных показателей судового оборудования. Поддержание и восстановление этих показателей являются задачей технического обслуживания, которую решают путем проведения ремонтов, профилактических вскрытии, осмотров и ревизий судовых механизмов, моточисток, наладок, регулировок, своевременного обеспечения материалами, сменными деталями, инструментом, средствами механизации работ в судовых условиях.
Ремонт судовых механических систем в зависимости от требуемых для его выполнения оборудования, оснастки и квалификации исполнителей можно разделить на два вида: промышленный и непромышленный. Промышленный ремонт может быть выполнен только в заводских условиях с выводом судна из эксплуатации, непромышленный может проводиться в судовых условиях в процессе эксплуатации.
Четкое разделение судовых работ на промышленные и непромышленные позволяет по каждому судну установить номенклатуру ремонтных работ, для выполнения которых требуется заводское оборудование. Определение необходимой периодичности этих работ позволяет установить рациональные сроки работы судна без заводского ремонта.
В настоящее время разработаны теоретические основы организации планово-предупредительного ремонта (ППР), позволяющие обоснованно устанавливать его периодичность.
Основные выводы этой теории состоят в следующем:
- оптимальная периодичность ППР позволяет без дополнительных затрат труда и средств значительно увеличить эксплуатационный период машин, механизмов и устройств. Примерная оптимальная периодичность составляет 0,4 - 0,6 средней продолжительности безотказной работы;
- ППР целесообразно применять только для узлов и деталей, работающих на износ (например, деталей ЦПГ, подшипников, движущихся деталей насосов и т. д.);
- ППР должен проводиться через строго определенные промежутки времени работы механизма независимо от его технического состояния; для судового оборудования с различной степенью надежности одинаковая периодичность ППР нецелесообразна;
- ППР не исключает внезапных выходов из строя элементов судовой техники, а только уменьшает их возможность.
Дата добавления: 2020-12-22; просмотров: 888; Мы поможем в написании вашей работы! |
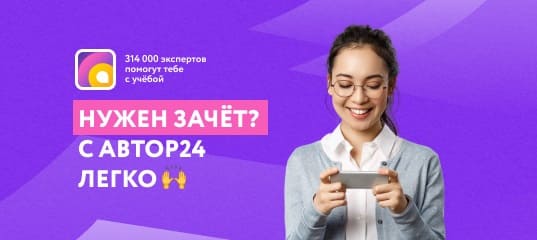
Мы поможем в написании ваших работ!