Система уплотнения ротора нагнетателя
Система уплотнения ротора нагнетателя предназначена для предотвращения прорыва газа из проточной части нагнетателя в подшипниковые узлы и далее по промежуточному валу к горячим частям двигателя. В ЦБН применяются масляный уплотнения и «сухие» газодинамические уплотнения.
Масляные уплотнения применяются на ЦБН более старого образца, таких как Н-370-18-1. Принцип работы таких уплотнений следующий: в камеру между торцевым уплотнением и опорным подшипником подводится масло с давлением на 0,1–0,3 МПа больше, чем давление газа в камере после лабиринтного уплотнения. Система регулирования уплотнения нагнетателя поддерживает необходимое превышение давления уплотняющего масла под давлением газа.
Масло к опорному подшипнику и к уплотнению нагнетателя подается двумя винтовыми насосами с приводом от электродвигателей переменного тока. Один из насосов является рабочим, другой резервным. К маслонасосам уплотнения масло поступает из маслосистемы турбоагрегата с давлением 0,2¸0,5 МПа. Все масло от МНУ, прежде чем попасть на смазку опорного подшипника и уплотнение, пропускается через гидроаккумулятор, установленный над нагнетателем на 2 м выше уплотнительной камеры. Гидроаккумулятор предназначен для обеспечения уплотнения и смазки в течение 10 мин в случае остановки МНУ, вызванной исчезновением электропитания двигателей. Этого времени достаточно для аварийной остановки ГПА и стравливания газа из нагнетателя.
|
|
Постоянная разность давлений масла и газа (перепад «масло-газ») поддерживается регулятором перепада давления за счет сброса части масла, нагнетаемого МНУ в линию перед маслоохладителями.
В нагнетателе уплотняющее масло проходит в основном через опорный вкладыш подшипника и частично через торцевое уплотнение в маслосборную камеру, находящуюся под давлением газа. Из нее масло стекает в поплавковую камеру и по мере ее заполнения отводится в ГО. В ГО масло разбивается на тонкие струи и растекается по перегородкам, на которых происходит выделение растворенного в масле газа. Чистое масло, скапливающееся в нижней части ГО, через гидрозатвор направляется в маслобак. А выделяющийся из масла газ сбрасывается в атмосферу через свечу. На рисунке 22 показана схема работы масляных уплотнений.
Рисунок 22 – Система уплотнения нагнетателя Н-370-18-1:
На рисунке обозначены: МНУ – маслонасосы уплотнения, АМ – гидроаккумулятор масла; РПД – регулятор перепада «масло-газ», ПК – поплавковая камера, ГО – газоотделитель, СП – сигнализатор помпажа.
Для уменьшения уноса масла из маслосборной камеры в сторону колеса нагнетателя и далее в газопровод из ПК отводят небольшое количество газа во всасывающий патрубок нагнетателя. Количество отводимого газа регулируют дросселем. В результате образуется поток газа, который увлекает масло из маслосборной камеры в ПК. Фильтр, установленный в верхней части ПК, препятствует уносу масляных паров во всасывающий патрубок нагнетателя.
|
|
Появление «сухих» газодинамических уплотнений позволило отказаться от использования масла, что исключило попадание масла в транспортируемый газ. Основной рабочей частью уплотнительной ступени СГУ является уплотнительная пара: торец и седло, показанная на рисунке 23.
Рисунок 23 – Принципиальная схема уплотнительной пары
Торец (выполняется из высококачественного графита с антифрикционными пропитками) подвижен в осевом направлении, закреплен внутри корпуса от проворота фиксатором из нержавеющей стали и нагружен в осевом направлении набором пружин. Торец прижимается к вращающемуся седлу (выполняется из твердосплавного материала, такого как карбид вольфрама и титана), закрепленному с помощью роторной втулки на валу компрессора. Седло в осевом направлении неподвижно, на его рабочей поверхности выполняются динамические пазы одностороннего или реверсного направления глубиной несколько микрон. Уплотнительные поверхности подвижного и неподвижного колец притерты, неплотность не превышает 1 мкм.
|
|
У подвижного кольца газового затвора поверхность контакта разделена на две зоны. Зона, расположенная ближе к оси – плоская, а остальная периферийная часть имеет спиральные канавки, выполненные методом химического травления или ионного бомбардирования, как показано на рисунке 24.
Рисунок 24 – Поверхность вращающегося кольца СГУ
При вращении седла газ захватывается канавками и нагнетается к внутреннему диаметру канавки. В этом месте поток газа встречается с уплотнительной перегородкой, которая создает сопротивление потоку, что приводит к увеличению давления. Вследствие этого происходит отжатие торца, он «всплывает» на газовом слое. Устанавливается уплотнительный зазор величиной несколько микрон, через который дросселируется малое количество рабочего газа. Зазор между радиальными торцами устанавливается тогда, когда закрывающие силы гидростатического давления и усилие пружины равняются открывающим усилиям, создаваемым в газовой пленке.
Наиболее широкое распространение в промышленности получили торцевые уплотнения типа «Тандем», показанное на рисунке 25.
|
|
Рисунок 25 – Торцевое уплотнение типа «Тандем»
Конструктивно состоит из двух уплотнений, расположенных в одном картридже. Идеально подходит с точки зрения надежности и безопасности при магистральном транспорте природного газа. Все рассматриваемые ниже требования к эксплуатации и разработке систем СГУ будут относиться, в основном, к типу «Тандем».
Первичный газовый затвор действует как основной, а вторичный является резервным. Отфильтрованный газ подается в полость между картриджем уплотнения и внутренним лабиринтом. Большая часть этого газа будет перетекать обратно в компрессор по внутреннему лабиринту, обеспечивая отсутствие жидкости и механических частиц в уплотняющей полости, которые могут повредить газовый затвор. Небольшая часть подаваемого газа будет перетекать через уплотняющий зазор в полость между картриджами первой и второй ступени. Эта полость вентилируется, и утечка отводится на свечу. Картридж второй ступени будет уплотняться газовой утечкой из первой ступени или разделительным газом (опционально, если предъявляются повышенные требования к безопасности процесса) и функционирует как резервное уплотнение.
Для изоляции газового уплотнения от подшипниковых камеры и предотвращения попадания масла на уплотнительные поверхности служит барьерное уплотнение. Оно также выполняет функцию уплотнения «последнего шанса» на случай катастрофических разрушений газовых затворов 1 и 2 ступени. Конструктивно обычно выполняется в виде лабиринтного уплотнения или сегментного графитового кольца. Уплотнение достигается за счет подачи буферного воздуха. Графитовое кольцо дает некоторое преимущество, в основном за счет более низких требований к расходу буферного газа (воздуха), по сравнению с лабиринтными барьерными уплотнениями, т.к. имеет меньший зазор с валом компрессора.
Схема работы газодинамических уплотнений показана на рисунке 26.
Рисунок 26 – Схема работы подшипников и уплотнений
Перекачиваемый газ поступает по линии 1 через патрубок во всасывающую полость «С». Сжатый в компрессоре газ, из полости «D», по линии нагнетания 2 поступает в станционный трубопровод.
Для снижения осевых нагрузок на опорно-упорный подшипник полость «С» соединена с задуммисной камерой «S» линией 10. Это обеспечивает выравнивание давлений в этих полостях. Окончательное выравнивание давлений перед торцовыми уплотнениями происходит в камерах «Z» и «Т», которые соединены между собой уравнительной линией 9.
По линиям 3 очищенный уплотняющий газ подается в камеры «Е» и «F» перед 1-й ступенью уплотнения с давлением, превышающим давление всасывания компрессора.
Для продувки полостей камер «Е» и «F» при пусконаладке системы уплотнений предусмотрены линии 4 слива конденсата. При работе компрессора линии 4 не используются.
За счет более высокого давления уплотняющий газ поступает из камер «Е» и «F» в камеры «Т» и «Z» и предотвращает попадание технологического газа из проточной части компрессора в уплотнение.
Отвод газа после первых ступеней торцовых уплотнений осуществляется из полостей «НН» и «G» по линиям 5.
Отвод газа после вторых ступеней торцовых уплотнений осуществляется по линиям 6 из полостей «К» и «L».
Подвод охлаждающего воздуха в опорный подшипник осуществляется по линии 7 в полость «Р».
В опорно-упорный подшипник охлаждающий воздух подается по линиям 8 в полость «R» и штуцер кожуха упорного подшипника.
Отвод воздуха из подшипников происходит по линиям 12 и 13.
Дата добавления: 2020-12-22; просмотров: 237; Мы поможем в написании вашей работы! |
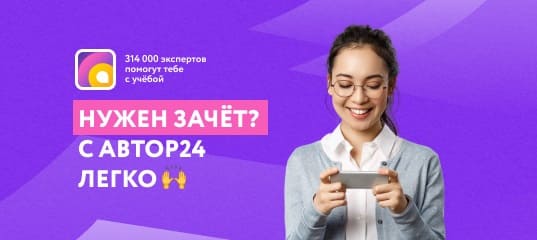
Мы поможем в написании ваших работ!