Изучение технической документации
ГБОУ ВО МО Университет Дубна, Лыткаринский промышленно-гуманитарный колледж
ОТЧЕТ
по производственной практике ПП04.01
Специальность:
15.02.08 Технология машиностроения (базовой подготовки)
ПМ04 Выполнение работ по профессии рабочего 18466 Слесарь механосборочных работ
МДК 04.01. Выполнение работ по профессии Слесарь механосборочных работ
72 часа.
сдала: студентка группы 715
Ширяева М.В.
проверил: Горемыкин О.Н.
Лыткарино 2020 г.
Содержание:
1. Введение ______________________________________________________ 3
2. Механосборочные работы_________________________________________ 4
2.1. Техника безопасности при выполнении слесарных работ______________ 4
2.2. Изучение технической документации______________________________ 7
2.3. Разборка оборудования__________________________________________ 8
2.4. Очистка и промывка деталей_____________________________________ 10
2.5. Дефектация деталей____________________________________________ 12
2.6. Восстановление деталей_________________________________________ 14
2.7. Сборка коробки передач металлорежущего станка__________________ 17
2.8. Испытание коробки передач металлорежущего станка после ремонта__ 18
3. Заключение_____________________________________________________ 20
4. Список используемой литературы__________________________________ 21
![]() |
Введение
Мы проходили практику в НИЦ ЦИАМ – ФИЛИАЛЕ ФГУП «ЦИАМ ИМ. П.И.
БАРАНОВА» с 22.06.2020 по 03.07.2020 года. Данное предприятие –
единственная в стране научная организация, осуществляющая полный цикл
|
|
исследований, необходимых при создании авиационных двигателей и
газотурбинных установок на их основе, а также научно-техническое
сопровождение изделий, находящихся в эксплуатации. Целью практики
являлосьполучение новых знаний и навыков, отработка общих и
профессиональных компетенции на практике, освоенных в период
теоретического обучения, обучение безопасным приемам работы при
выполнении слесарных механосборочных работ.
При прохождении практики мы изучили и реализовали следующие вопросы:
1. Безопасные приемы работы при выполнении слесарных механосборочных работ.
2. Слесарные механосборочные работы согласно техническому заданию:
2.1. Разборка, дефектовка, восстановление и ремонт коробки передач металлорежущего станка
Механосборочные работы
Механосборочные работы являются заключительным этапом в производственном процессе. Они могут быть выполнены различными способами и средствами в зависимости от масштаба производства.
Сборочная единица представляет собой соединение двух или более деталей машин в простейшую сборку, например, вал с пригнанной шпонкой, шкив установленный на валу, корпус с шариковым подшипников и т.д.
|
|
Подузел представляет собой соединение нескольких деталей или сборочных единиц.
Узел — соединение нескольких деталей, одного или нескольких комплектов или подузлов. Характерной особенностью узла является его технологическая законченность. Узлы при сборке станков или машин комплектуют в сборочные группы. Изделием называется продукт конечной стадии производства.
Технологический процесс, как правило, состоит из следующих стадий:
1. Ручная слесарная обработка и подготовка к сборке отдельных деталей: зачистка заусенцев, снятие фасок и т.д.
2. Соединение деталей в комплекты, подузлы, узлы и агрегаты.
3. Общая сборка — сборка всей машины или механизма.
Техника безопасности при выполнении слесарных работ.
До начала работы:
1. Наденьте спецодежду, застегните на все пуговицы. Волосы должны быть убраны под головной убор.
2. Проверьте состояние рабочего места.
3. Проверьте состояние молотков и кувалд.
4. Проверьте состояние напильников, шаберов, ножовок и т.д.
5. Проверьте состояние штепселей, розеток и шланговых проводов.
6. Разложите инструменты на верстаке в строгом порядке.
7. Проверьте устойчивость верстака, надежно закрепите на нем тиски, губы тисков должны иметь насечку.
|
|
Во время работы:
1. При работе с зубилом или крейцмесселем надевайте защитные очки.
2. Не выбивайте сломанный метчик зубилом или крейцмесселем.
3. Не сдувайте с обрабатываемой детали опилки (можно засорить глаза).
4. Устанавливайте деталь в тисках надежно, чтобы деталь не могла выскочить при обработке. При рубке направляйте отлетающие куски материала на щит или в сторону от работающих.
5. При зажиме гаек, ключей не ударяйте по ключу молотком, не удлиняйте ключ трубой, или другим ключом.
6. При пользовании пневматическим или электрическим инструментом убедитесь в его исправности.
7. При работе с электродрелью, надевайте резиновые перчатки.
8. При работе паяльником 127, 220 в, проверьте заземление.
9. Проверяйте электропровод и штепсель электроинструментов, они должны иметь исправную изоляцию.
10. При работе пневмоинструментом, надежно закрепляйте шланг к инструменту и к трубопроводу.
11. При работе на наждачных точилах, убедитесь в его исправности.
12. Не затачивайте больших деталей, можно разорвать круг.
13. При работе на сверлильном станке, ознакомьтесь с инструкцией для работы на сверлильном станке.
14. При ремонте водопровода или канализации, проверьте водопроводную сеть, отключите ремонтируемые участки, вывесите на задвижках или вентилях знак «Не включать, ремонт».
|
|
15. При поручении незнакомой работы – получите дополнительный инструктаж.
ЗАПРЕЩАЕТСЯ:
а) работать неисправным инструментом;
б) производить заточку инструмента при неисправном круге;
в) оставлять заточный станок работающим;
г) оставлять включенными в сеть электроинструменты и другие потребители тока;
д) доверять работу паяльной лампой, электроинструментом и на станке посторонним лицам;
е) работать со шнуром и вилкой (штепселем), имеющим повреждение изоляции.
По окончанию работы:
1. Отключите электроинструменты, заточный или сверлильный станок (если на нем работал).
2. Приведите в порядок станок, верстак.
3. Уберите все инструменты на место.
4. Доложите о выполненной работе директору филиала.
Изучение технической документации
К ремонтной документации относят: общее руководство по ремонту, руководство по среднему ремонту, руководство по капитальному ремонту, общие технические условия на капитальный ремонт, чертежи ремонтные, каталог деталей и сборочных единиц, нормы расхода запасных частей, нормы расхода материалов.
Для организации восстановления деталей путем ремонта или их воспроизводства в ремонтно-механическом цехе рекомендуется на каждый вид оборудования составлять альбомы, в которые должны входить: характеристика оборудования; спецификация быстроизнашивающихся деталей; технические условия на ремонт, схемы управления, защиты, смазки; рабочие чертежи сборочных единиц и деталей; спецификация стандартных изделий (подшипников, манжетных уплотнений и др.).
Технический документ — совокупность специальных данных и сведений о каком-либо устройстве или производственном процессе, изложенных в строгой форме и профессиональным языком.
Основными видами технических документов являются:
· чертеж – изображение предмета на плоскости, выполненное особыми графическими приемами.
· сборочный чертеж – изображение сборочной единицы, которое дает представление о расположении и взаимной связи ее составных частей и обеспечивает возможность осуществления сборки и контроля.
· габаритный чертеж – технический документ, содержащий упрощенное изображение изделия с указанием габаритных, установочных и присоединительных размеров.
· техническое описание – содержит сведения о наиболее характерных особенностях конкретного изделия.
· спецификация – документ, определяющий состав изделия, сборочной единицы, комплекса или комплекта.
· пояснительная записка – текстовый технический документ, содержащий описание устройства и принципа действия разрабатываемого изделия, а также новации принимаемых технических решений.
При решении вопроса о возведении, реконструкции зданий и ремонте объектов капительного строительства создается проектно-сметная документация:
· генеральный план – изображение всего участка строительства, на котором в контурах вида сверху представлено размещение существующих и проектируемых объектов;
· паспорт проекта – документ, в котором дается схематическое изображение объекта, краткое описание и даются основные технические показатели.
Разборка оборудования
Машину или оборудование разбирают в последовательности, предусмотренной технологическим процессом в целом для них и для отдельных механизмов, агрегатов и узлов. При разборке с машины или оборудования снимают целые узлы.
Разборку оборудования производят с соблюдением следующих основных правил:
1. Разборке подлежит лишь агрегат или узел, предназначенный для ремонта, поскольку при разборке нарушается необходимая плотность соединений с натягом и приработка подвижных деталей. Только капитальный ремонт требует полной разборки машины.
2. В процессе разборки сложных и ответственных механизмов и узлов следует составлять их схемы и делать зарисовки с целью облегчения последующей сборки.
3. Разборку следует начинать со снятия кожухов, крышек, защитных щитков, ограждений и т. п. для открытия доступа к разбираемым агрегатам и узлам.
4. Крупные детали укладывают на подставки возле ремонтируемой машины.
5. Детали каждого разбираемого механизма или узла складывают в отдельные ящики, следя за тем, чтобы не попортить обработанные поверхности деталей.
6. Разборка должна вестись соответствующими инструментами и приспособлениями, использование которых исключает порчу годных деталей.
7. С целью облегчения снятия насаженной с натягом детали ее можно нагревать горячим маслом, паром, огнем, а охватываемую деталь охлаждать с помощью твердой углекислоты или жидкого воздуха.
8. Резьбовые соединения разбирают с помощью гаечных и специальных ключей различных конструкций, отверток, шпильковерток и др.
9. Неподдающееся из-за коррозии разборке резьбовое соединение погружают в керосин или смачивают керосином и разбирают по прошествии нескольких часов.
10. Остаток сломанного винта или шпильки удаляют одним из следующих способов:
- при наличии выступающей резьбовой части на нее навинчивают гайку и контргайку и вращают гайку;
- при наличии выступающего на небольшую величину стержня винта или шпильки на его торце прорезают ножовкой или вырубают шлиц и отверткой выворачивают оставшуюся часть;
- торец сломанной части резьбовой детали запиливают ровно и накернивают по центру, после чего сверлом, диаметром несколько меньшим, чем внутренний диаметр резьбы, высверливают оставшуюся часть;
- к застрявшему концу резьбовой детали приваривают либо гайку меньшего диаметра через ее отверстие, либо стержень, и с их помощью вывертывают сломанную часть.
11. Заклепочные соединения разбирают, либо срубая головку заклепки и бородком выбивая стержень, либо засверливая накерненную головку сверлом несколько меньшего диаметра, чем диаметр стержня заклепки.
12. Узлы и механизмы с тяжелыми деталями разбирают с применением грузоподъемных приспособлений или подъемных кранов.
Очистка и промывка деталей
Очистку деталей от ржавчины, старой краски, затвердевшего смазочного материала, нагара и др. осуществляют следующими способами:
· механический — производят ручными или механизированными щетками, шарошками, скребками, шаберами, различными машинками;
· абразивный — производят пескоструйную или гидропескоструйную обработку деталей;
Термический — производят нагрев поверхности детали пламенем паяльной лампы или газовой горелки;
Химический — используют специальные пасты и смывочные растворы, в состав которых входят каустическая сода, негашеная известь, мел, мазут и др.
Промывку деталей производят водными щелочными растворами и органическими растворителями сначала в горячем растворе, затем в чистой горячей воде. После этого деталь тщательно высушивают сжатым воздухом и салфетками.
Промывку деталей осуществляют вручную, в баках методом погружения, в моечных машинах, ультразвуком.
Ручной способ. Промывку ведут в двух ваннах, заполненных органическим растворителем (керосином, бензином, дизельным топливом, хлорированными углеводородами). Первая ванна предназначена для замачивания и предварительной промывки, вторая — для окончательной промывки. При этом используются щетки, крючки, скребки, обтирочный материал и др.
Методом погружения в баках промывку производят в стационарном или передвижном баке, оборудованном сеткой, на которую укладывают детали, и трубкой с электроспиралью или змеевиком для подогрева моющего раствора до температуры 80—90 °С. В качестве моющих используют водные растворы различных комбинаций из мыла, кальцинированной соды, каустической соды и др.
В моечных машинах стационарных или передвижных различных конструкций промывку производят нагретыми до 70—90 °С моющими растворами приведенного выше состава, направляемыми на детали под давлением через специальные сопла.
Ультразвуковую промывку производят в специальной ванне с подогревом моющей жидкости (щелочные растворы или органические растворители). В ванне размещается источник ультразвуковых колебаний, создающий упругие волны высокой частоты, которые ускоряют отрыв загрязнений от поверхности детали.
Меры безопасности, которые необходимо соблюдать при очистке и промывке деталей, состоят в следующем:
В помещение, где производится промывка, должно иметь приточно-вытяжную вентиляцию;
Рабочих, занятых промывкой токсичными моющими средствами, следует обеспечить защитными пастами для рук, очками, резиновыми перчатками, фартуками, сапогами;
При использовании горючих моющих средств не допускается применение электроинструмента и открытого пламени.
Дефектация деталей
Дефектация — это комплекс работ по определению состояния деталей и возможности их повторного использования. Она необходима для выявления у деталей дефектов, возникающих в результате изнашивания, коррозии, усталости материала и других процессов.
Под дефектом понимается каждое отдельное несоответствие детали установленным требованиям. Дефекты в общем случае подразделяются по ряду
классификационных групп:
· • по возможности обнаружения — на явные и скрытые;
· • значимости — на малозначительные, значительные и критические;
· • причинам возникновения — на конструктивные, технологические и
эксплуатационные;
· • по возможности устранения — на устранимые и неустранимые.
Явные — дефекты, которые определяются визуально либо предусмотренными в
нормативно-технической документации методами и средствами
Скрытые — дефекты, для обнаружения которых применяются специальные методы контроля.
Критические — дефекты, при наличии которых использование деталей по
назначению невозможно.
Значительные — дефекты, которые существенно влияют на использование
деталей, их долговечность.
Малозначительные — дефекты, которые существенно не влияют на использование деталей, их долговечность.
Конструктивные — дефекты, появление которых обусловлено нарушением правил разработки изделия.
Технологические — дефекты, появление которых обусловлено нарушением правил изготовления и ремонта изделия.
Эксплуатационные — дефекты, появление которых обусловлено эксплуатацией
изделия.
Устранимые — дефекты, устранение которых технически возможно и экономически целесообразно.
Неустранимые — дефекты, устранение которых технически невозможно или
экономически нецелесообразно.
Типовыми дефектами деталей сельскохозяйственной техники, которые появляются в результате трения и динамических нагрузок, являются:
• уменьшение (увеличение) размеров рабочих поверхностей деталей, их массы и объема из-за физического изнашивания;
• изменение пространственной геометрии деталей и сборочных единиц в результате изгиба, скрученности, коробления из-за динамических нагрузок;
• нарушение конструктивной целостности деталей из-за трещин, обломов, пробоин;
• снижение механических и эксплуатационных свойств материала детали из-за изменения его химического состава, структуры;
• нарушение целостности или свойств покрытий, защищающих элементы машин от агрессивного воздействия окружающей среды.
Последовательность дефектации:
1. Деталь подвергается внешнему осмотру с целью обнаружения явных дефектов (коррозия, трещины, вмятины и т. д.), а также дефектов с признаками явного брака (поломки, сколы, пробоины и т. п.).
2. Деталь проверяют на специальных приспособлениях и приборах для выявления микротрещин, определения степени смещения поверхностей относительно друг друга, измерения твердости, упругости и т. д.
3. Производится обмер рабочих поверхностей деталей.
Такая последовательность дефектации позволяет избежать лишних работ в тех случаях, когда деталь имеет признаки явных дефектов или брака.
Восстановление деталей
Способы восстановления условно делят на две категории: способы наращивания и способы обработки.
Газовая сварка применяется для самых разных элементов, выполненных как из серого чугуна, так и из стали толщиной до 3 мм (тонколистовая) х общий срок эксплуатации.
Электродуговая сварка, если сравнивать ее с газовой, то она экономичнее и обеспечивает лучшую надежность стыка. Это более рациональный способ восстановления детали, особенно при правильной подготовке, в рамках которой нужно сделать следующее:
· очистить и разделать кромки;
· пройтись по поверхности стальной щеткой для очистки налипших частиц, напильником и наждачкой для абразивного эффекта, пескоструйной машиной для шлифовки – чтобы удалить неровности;
· промыть с помощью керосина или бензина, протравить щелочным составом;
· скосить кромки (если свариваются листы) под углом 60-70 градусов, выровнять края пробоин или изломов.
Способ восстановления деталей наплавкой актуален тогда, когда в процессе эксплуатации определенные элементы постоянно контактируют друг с другом и поверхность хотя бы одного из них необходимо защитить от истирания. Для этого наваривается два-три слоя более твердых материалов, значительно продлевающих общий срок эксплуатации.
Ремонт и восстановление деталей металлизацией заключается в покрытии основного материала новым – защитным, расплавленным. При его реализации характерны следующие особенности:
· присадка распыляется струей воздуха (или другого газа под давлением);
· наносимая добавка оседает на поверхности (предварительно обезжиренной) в виде малых окисленных частиц;
· полученная таким образом прослойка является пористой, а не монолитной структурой.
Для улучшения качества сцепления поврежденная заготовка должна быть заранее очищена не только от масла, но и от грязи, а также отшлифована с помощью пескоструйной машины. Чем тверже используемый присадочный материал, тем надежнее будет конечный результат.
Гальванические покрытия.
Одним из классических способов восстановления и упрочнения деталей стало хромирование, то есть нанесение слоя хрома толщиной до 0,3 мм. Благодаря этому можно не только вернуть исходную геометрию истертого элемента, но и повысить его твердость.
Твердое никелирование.
При нем заводские размеры возвращаются благодаря осаждению на изношенном слое специального никельфосфорного состава. Он укладывается на определенные участки заготовки, по специальной маске, электрическим или химическим путем. Последний легче в реализации, так как при его осуществлении можно с помощью специализированных реагентов выделить нужную присадку из раствора солей.
Давлением.
Под давлением на практике возможны следующие виды восстановления деталей оборудования:
· правка рычагов, а также валов, как коленчатых так и гладких;
· осадка зубчатых колес, используемых пальцев, истертых втулок;
· накатка для практического повышения диаметров цапф, шеек направляющих осей за счет образования канавок и поднятия гребешков;
· обжатие вкладышей подшипников;
· вдавливание шлицевых валиков;
· раздача роликов машин, поршней, подобных им комплектующих.
Пластмассой.
Эти материалы часто используются для получения качественного и прочного соединения неметаллических поверхностей. В числе наиболее часто применяемых текстолит, стиракрил (очень быстро твердеет, поэтому так удобен), а также различные древесно-слоистые составы.
Склеивание – это вполне актуальная операция, которая в целом ряде случаев является отличной альтернативой свалке, клепке, соединению болтами. В качестве составляющей части технологического процесса восстановления деталей обладает следующими преимуществами:
· скрепляет разные по структуре материалы;
· не повышает конечный вес заготовки, а зачастую даже снижает его;
· обеспечивает герметичность шва и дает ему антикоррозионные свойства;
· минимизирует стоимость проведения обслуживания.
Дата добавления: 2020-11-23; просмотров: 152; Мы поможем в написании вашей работы! |
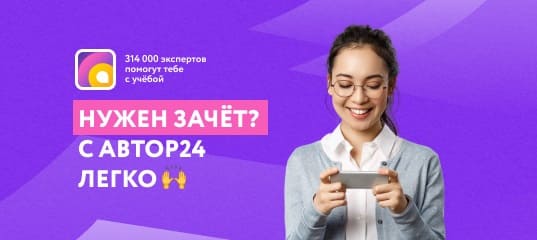
Мы поможем в написании ваших работ!