Правила безопасности при выполнении слесарных работ
Перед началом работы проверить весь инструмент, надеть спецодежду
Проверьте надежность крепления защитного кожуха ременной передачи, соединения защитного заземления (зануления) с корпусом станка. Надежно закрепите сверло в патроне. Проверьте работу станка на холостом ходу и исправность пусковой коробки путем включения и выключения кнопок. Прочно закрепите деталь на столе станка в тисках или кондукторах. Перед самым началом работы наденьте защитные очки.
При работе на тисках следует соблюдать следующие правила:
-перед началом работы осматривать тиски, обращая особое внимание на прочность их крепления к верстаку;
-не выполнять на тисках грубых работ (рубки, правки или гибки) тяжелыми молотками, так как это приводит к быстрому разрушению тисков;
-при креплении деталей в тисках не допускать ударов по рукоятке, что может привести к срыву резьбы ходового винта или гайки;
-по окончании работы очищать тиски волосяной щеткой от стружки, грязи и пыли, а направляющие и резьбовые соединения смазывать маслом;
-после окончания работ не сводить плотно губки тисков, так как это вызывает излишние напряжения в винтовых соединениях; необходимо оставлять между губками зазор 4—5 мм.
Во время работы не пользовать сверла с изношенными конусными хвостовиками .Сверло к детали подавать плавно, без усилий и рывков, и только после того, как шпиндель станка наберет полную скорость. Перед сверлением металлической заготовки необходимо накернить центры отверстий. Особое внимание и осторожность проявляйте в конце сверления.
|
|
Во избежание травм в процессе работы на станке:
- не наклонять голову близко к сверлу;
- не производить работу в рукавицах;
- не класть посторонние предметы на станину станка;
- нe смазывать и не охлаждать сверло с помощью мокрых тряпок. Для охлаждения сверла нужно пользоваться специальной кисточкой;
- не тормозить руками патрон или сверло;
- нe отходить от станка, не выключив его.
При прекращении подачи электрического тока в сети во время работы немедленно выключите электродвигатель.
Требования безопасности после окончания работы
После остановки вращения сверла удалить стружку со станка с помощью щетки. Не сдувать стружку ртом и не сметать ее руками.
Запрещается
- Самостоятельно устранять неполадки электрического оборудования.
- Хранить на рабочем месте воспламеняющиеся материалы.
- Выполнять работу, не порученную мастером.
- Прикасаться руками к электрооборудованию.
- Находиться в зоне работы абразивных, шлифовальных машин.
- Производить переноску грузов, превышающих вес более 50 кг (для
|
|
мужчин) и 15 кг (для женщин) на расстояние 25 метров.
- Находиться под поднятым грузом.
- Работать без защитных средств (каски, рукавиц и т.д.).
- Подлезать под стоящим железнодорожным составом, перелазить
через сцепления вагонов.
Электробезопасность
Не прикасаться к арматуре общего освещения и оборванным электрическим проводам, клеммам и др. легкодоступным токоведущим частям. Не открывать двери электрораспределительных шкафов (сборок) и не снимать ограждения и защитные кожуха с токоведущих частей оборудования.
Если электрооборудование не исправно, вызвать электромонтера и сообщить мастеру. Самому устранять неисправность не разрешается.
Все работы в электроустановках могут проводиться только специально обученным оперативным и оперативно-ремонтным персоналом по наряду или устному распоряжению лица, ответственного за электрохозяйство цеха (подразделения).
Научное исследование по теме «Современные технологии в организации технического обслуживания и ремонта подвижного состава»
В связи с ростом интенсивности перевозок, скоростей движения, а также возросших требований по обеспечению безопасности перевозочного процесса особое внимание уделяется качеству ремонта подвижного состава. Существенное влияние на безопасность движения поездов, наряду с традиционными причинами (надежность подвижного состава, условия эксплуатации и т.п.), оказывает также состояние технологической подготовки производства на предприятиях производящих различные виды ремонта. Увеличение программы, а иногда и объемов ремонта требует качественного изменения всей организационной структуры ремонта подвижного состава, и, в первую очередь технологической подготовки производства.
|
|
Все это обуславливает необходимость проведения комплекса исследований, направленных на совершенствование организации ремонтного производства на основе математического моделирования трудоемкости технологической подготовки производства (ТПП), что позволит еще до постановки объекта в ремонт определить объем работ по технологической подготовке производства. Кроме того, это позволит без значительных материальных и временных затрат внедрять в производство новые технологии, повысит качество ремонта подвижного состава, а следовательно и уровень безопасности движения поездов.
В процессе учебной практики мною были изучены научные статьи по теме «Современные технологии в организации технического обслуживания и ремонта подвижного состава». В которых изложены научно обоснованные технологические и технические решения по совершенствованию организации ремонтного производства на основе математического моделирования трудоемкости технологической подготовки производства методом планирования полнофакторного эксперимента, имеющие существенное значение для организации производства на железнодорожном транспорте.
|
|
На основе анализа текущего состояния парка подвижного состава, производственных показателей железнодорожного машиностроения, системы ремонта установлено, что практически единственных выходом из сложившейся ситуации является капитальный ремонт подвижного состава. Совершенствование организации ремонта подвижного состава может быть достигнуто за счет комплекса мероприятий по совершенствованию технологической подготовки производства. Первоочередным из мероприятий является разработка математической модели трудоемкости ТПП.
Определены основные факторы, влияющие на трудоемкость ТПП, и установлены их коэффициенты влияния. В результате показано, что наибольшее влияние оказывает состояние технологической подготовки производства при ремонте подвижного состава. Проведено ранжирование факторов и, выделены для исследований следующие: уровень квалификации инженерно-технических работников, уровень автоматизации ТПП и комплектность конструкторско-технологической документации.
Квинтэссенцией информатизации должен стать реально работающий в активном режиме центр ситуационного управления. Центр должен позволить высшему менеджменту отрасли принимать правильные стратегические решения, объективно и достоверно оценивать текущую ситуацию и оперативно воздействовать на те или иные сегменты управления жизнедеятельности транспорта. В связи с вышеизложенным, при интегральной автоматизации железных дорог, вопросы автоматизации и управления, связанные с оценкой качества эксплуатации подвижного состава, и, прежде всего с экономической эффективностью его использования, приобретают первостепенное значение.
Заключение
В процессе прохождения учебной практики я теоретически изучил современные технологии в организации технического обслуживания и ремонта подвижного состава. Ознакомился организацией рабочего места, и различными видами тисков. Я научился безопасным приемам труда, соблюдал меры безопасности при работе на тисках и с ручным инструментом , правила личной гигиены.
Считаю, что данная работа и учебная практика помогли мне закрепить теоретические знания, полученные в институте, и подготовиться к самостоятельной работе.
Дата добавления: 2020-11-23; просмотров: 86; Мы поможем в написании вашей работы! |
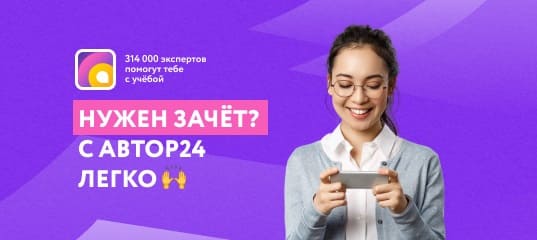
Мы поможем в написании ваших работ!