Описание технологического процесса производства труб
Описание пяти-валковой сварочной клети
Таблица 2.1 - Технические характеристики
Направление движения трубы | со стороны обслуживания направления движения «слева направо» |
Положение трубы Кромка трубы | постоянная нижняя образующая 1300 мм над уровнем пола |
Диаметр обсадных труб | 114,3 – 244,5 мм |
Толщина стенки: | 3,2 – 13,0 мм |
Длина обсадных труб: | 9,5 – 11,2 м |
Расчетная длина: | 10,0 м |
Марка стали: | 22ГФ |
предел текучести до 600 Н/мм2 при диаметре трубы 244,5 мм и толщине стенки 13,1 мм
Функциональное описание для сварочной клети
Формованный открытый трубной профиль в зоне кромок полосы кондуктивно нагревается высокочастотным сварочным оборудованием и на сварочном столе сваривается в закрытую трубу. При этом мощность высокочастотного генератора регулируется в зависимости от скорости с целью минимизации колебаний температуры.
Конструкция сварочной клети
Рисунок 2.1 - Сварочная клеть.
Сварочная клеть оснащена пятью неприводными валками: двумя боковыми валками (1), двумя верхними валками (2) и нижним валком (3).
Для обеспечения обработки труб разных размеров предусмотрены 2 пары кассет для боковых валков с соответствующими валками. Пары кассет для больших размеров труб частично поворачиваются. Это позволит свести к минимуму число держателей боковых валков для всего диапазона размеров установки.
|
|
Для различных верхних валков держатели валков (4) сконструированы независимо от размеров труб.
Для крепления нижнего валка разработан держатель валка (5), в котором может быть размещен нижний валок с соответствующими осями.
Для ускорения смены один комплект держателей валков дополнительно имеется вне линии. Кроме того, сварочная клеть состоит из рамы клети (6), верхней балки (7) и устройства демонтажа (8). Также на раме находятся наружный и внутренний гратосниматель для снятия грата, а также гратомоталка для наружного грата.
Работа сварочной клети
В сварочной клети спрессовываются кромки полосы.
Энергия нагрева кромок подается при помощи двух скользящих контактов прижатых к кромкам заготовки на определенном расстоянии от точки схождения. Ток от источника питания поступает к кромкам трубной заготовки 2. Дальше ток может идти от одного контакта к другому двумя путями: вокруг периметра трубы и вдоль одной кромки до места стыка (прямой ток) и обратно по второй кромке (обратный ток). Индуктивное сопротивление по периметру трубы будет больше, чем вдоль кромок. Поэтому ток пойдет вдоль кромок, будет их разогревать до сварочной температуры. В месте стыка кромок 3 образуется шов под действием сдавливания сварочными роликами 4, температура кромок будет наивысшей и произойдет сварка заготовки в трубу 6. При этом в зависимости от скорости, регулируется мощность высокочастотного генератора, с целью поддержания постоянной температуры сварки.
|
|
Рисунок 2.2. Схема высокочастотной сварки с подводом тока скользящими контактами:
1-контакты; 2-сформованная заготовка; 3- стык кромок; 4- сварочные ролики; 5 – ферритовый сердечник; 6- готовая труба.
Для сокращения потерь тока замыкающегося по окружности заготовки, внутри трубы в зоне точки схождения устанавливают водоохлаждаемый феррит, и на этой же штанге – резец для снятия внутреннего грата. Наружный грат снимается одним из резцов наружного гратоснимателя. Срезанный наружный грат в виде «непрерывной» сливной стружки наматывается на вилки барабана гратомоталки.
Настройка сварочной клети
Настройка сварочной клети заключается в регулировании верхних и боковых валков, а также кондуктора.
Для верхних валков предусмотрены две системы регулирования: регулирование непосредственно правого и левого валков независимо друг от друга, а также регулирование верхней балки, на которой крепятся оба верхних валка. Обе системы регулирования не зависят друг от друга что повышает эффективность регулирования параллельности кромок и очага деформации. Независимая регулировка верхних валков способствует образованию симметричного наружного грата.
|
|
Боковые валки регулируются симметрично оси сварки так, чтобы наружный грат был минимальным.
Регулировка кондуктора заключается в перемещении скользящих контактов на минимальное расстояние к точке сварки, что приводит к повышению коэффициента полезного действия.
Переоборудование сварочной клети
Замена верхних валков возможна без демонтажа боковых валков и нижнего валка, а также без разделения «непрерывной трубы».
Верхние валки выводятся на один уровень, затем привод верхней балки перемещается вверх. Эти действия можно произвести параллельно. Опорные салазки для верхних валков гидравлически перемещаются из позиции останова в позицию приема в центре клети. Верхние валки размещаются на салазках и деблокируются гидравлически. Система регулировки верхних валков перемещает их в высшую позицию, в которой верхние валки и их держатели деблокируются. Они выдвигаются вместе с опорными салазками сбоку клети и принимаются цеховым краном со специальным подвесным приспособлением.
|
|
Монтаж новых валков осуществляется аналогично в обратном порядке.
Замена боковых валков возможна без демонтажа верхних валков и нижнего валка.
Боковые валки в своих держателях перемещаются в позицию смены с помощью редукторного двигателя. В этой позиции цеховой кран может перенять их вместе с держателями.
Монтаж новых валков осуществляется аналогично в обратной последовательности.
Замена нижнего валка возможна только в том случае, если верхние валки демонтированы, а верхняя балка перемещена в верхнюю позицию.
Боковые валки выводятся наружу. Нижний валок вместе с держателем может демонтироваться цеховым краном. Держатель нижнего валка без крепления опирается только на соответствующую систему регулирования.
Описание технологического процесса производства труб
ТЭСА 140-245
Рисунок 2.3 - Схема технологического потока ТЭСЦ-5.
Рулонная сталь поступает в цех в открытых железнодорожных вагонах или на платформах, разгрузка которых производится электромостовым краном грузоподъемностью 50/12,5 тонн с клещевым захватом. Складирование рулонов производится в вертикальном положении (на торец) по плавкам, маркам стали и размерам рулонной стали.
Рулоны, проверенные ОТК, со смотровой площадки подаются электромостовым краном с клещевым захватом на линию агрегата продольной резки и устанавливаются на загрузочный стеллаж, где производится взвешивание рулона на тензометрических весах, результат измерения вводится в систему сбора данных автоматически.
После взвешивания рулон транспортируется на разматыватель для размотки, а затем на правильную машину с тянущими роликами для правки рулонной полосы, заправки и подачи ее в машину продольной резки.
Из правильной машины после обрезки переднего и заднего концов рулона полоса подается тянущими роликами в агрегат продольной резки.
В агрегате продольной резки производится продольная порезка рулонной стали на несколько полос заданной ширины и обрезка боковых кромок. Боковая обрезь, образовавшаяся в результате порезки на агрегате продольной резки, направляется в боковые проводки (трубчатой формы) кромкокрошителя для непрерывной разрезки в поперечном направлении.
Штрипсы, разделенные с помощью двух электромагнитов задаются через петлевое устройство в сепаратор во избежании наложения их друг на друга и далее в моталку. Моталка представляет барабан, состоящий из четырех сегментов сжимающихся и разжимающихся по принципу цангового зажима. Смотанные штрипсы от моталки транспортируются разгрузочной тележкой на обвязочную машину. После обвязки смотанных штрипсов и их взвешивания результат измерения вводится автоматически в систему сбора данных.
Отсортированные работниками ОТК штрипсы ремонтируются работниками АПР и задаются в производство до смены плавки. Зачистка заусенцев производится шлифмашинкой, обрезка концов штрипса – газовым резаком. При невозможности ремонта штрипсы бракуются и помещаются в изолятор брака.
Годные штрипсы, с промежуточного склада АПР, задаются в стан поплавочно электромостовым краном с клещевым захватом и устанавливаются на кантователь рулонов для кантовки с вертикального расположения оси рулона на горизонтальное и транспортируются загрузочной тележкой на загрузочный стеллаж. Загрузочная тележка разделяет штрипсы, поворачивая их при необходимости на 180о в зависимости от направления кромки (заусенцем вверх), транспортирует по одному штрипсу к промежуточному наклонному стеллажу.
Прием штрипсов, их хранение и передача на позицию размотки осуществляется на промежуточном наклонном стеллаже. Размотка штрипса и заправка его в правильную машину производится разматывателем двухбарабанного типа. Размотка штрипса может производиться сверху и снизу. Разматыватель имеет два приводных барабана для фиксирования штрипса по внутреннему диаметру.
Правка разматываемого штрипса производится правильной машиной, которая состоит из 5 правильных валков и 2 тянущих роликов. Штрипс после правильной машины подается на стыкосварочную машину с ножницами. Для обеспечения параллельности торцов перед сваркой осуществляется отрезка ножницами с нижним резом заднего и переднего концов штрипса.
Сварка концов штрипса происходит в среде защитного газа (двуокись углерода) в автоматическом режиме одновременно двумя горелками. После окончания сварки зажимы освобождают полосу и она перемещается вперед до тянущих роликов, где производится осмотр сварного соединения. При некачественной сварке стыка, склонного к разрушению, производится вырезка сварного соединения и повторная сварка концов штрипса.
Для центровки подаваемой полосы по оси стана полоса направляется на входные и выходные боковые проводки. Для образования запаса штрипса, необходимого для обеспечения непрерывного процесса формовки и сварки труб, при остановке на стыковку, полоса направляется в петлевое устройство, откуда полоса подается тянущими роликами через промежуточный стол, в формовочный стан со скоростью равной скорости сварки трубы.
Для непрерывной формовки в трубную заготовку штрипс задается в формовочный стан. Стан состоит из боковой проводки, задающей клети, клети предварительной формовки, четырех формующих клетей с открытым профилем калибра, трех клетей с закрытым профилем и промежуточных клетей с вертикальными валками.
Сформированная трубная заготовка из клетей закрытого профиля задается в сварочный узел. Производится настройка сварочного режима, установки снятия наружного грата и внутреннего гратоснимателя. Включается установка ультразвукового контроля шва.
Электросварщик труб контролирует прохождение начала трубной заготовки через установку ЛТО, стационарный спрейер, калибровочный стан, правильные клети до летучего отрезного станка.
Сварка непрерывно движущихся кромок сформованной трубной заготовки осуществляется на трубосварочной машине, состоящей из высокочастотного генератора, скользящих контактов, сварочной клети, установок снятия наружного и внутреннего грата.
Нагрев кромок трубной заготовки перед сваркой производится на высокочастотной установке токами частотой 440 кГц. Подвод электроэнергии производится скользящими медными контактами через кондуктор, укрепленный на трансформаторе. Для повышения эффективности нагрева и концентрации тока на кромках внутри трубы устанавливается ферритовый сердечник.
Степень обжатия трубной заготовки по периметру в сварочном узле должна составлять 1,0-2,5 мм для всех диаметров. Степень обжатия определяется разностью периметров трубной заготовки до сварочного узла и готовой трубы после сварочного узла. Сварка труб производится с использованием системы автоматического регулирования (CAP сварки).
Трубы, сваренные при настройке стана с нестабильным сварочным режимом, оператором ПУ отрезного станка выводятся в ручном режиме на газовый резак и отсортировываются в брак.
После настройки сварочного режима сварщик в ручном режиме выводит на газовый резак одну трубу для отбора образцов для проведения испытания на сплющивание.
Срезание наружного грата производится наружным гратоснимателем, состоящим из двух суппортов для резцов, гратомоталки и двух опорных роликов, установленных под сваренной трубой в плоскости резцов. Передний конец срезанного непрерывно наружного грата заправляестя сварщиком вручную при помощи крюка в гратомоталку.
Удаление внутреннего грата производится внутренним гратоснимателем, состоящим из штанги, задний конец которой закреплен барабанной опорой на станине формовочной клети. На переднем конце штанги прикреплена головка гратоснимателя, на которой смонтирован резцедержатель с резцом, имеющим твердосплавную пластину.
Сварной шов каждой трубы подвергается неразрушающему контролю, трубы не прошедшие УЗК автоматически выводятся из потока, увязываются в пакеты и передаются в изолятор брака
Трубы подвергаются локальной термообработке (нормализации) сварного шва. Нормализация осуществляется для снятия остаточных напряжений в зоне сварного шва, выравнивания структуры, улучшения механических свойств шва.
Оборудование ЛТО состоит из клетей с тянущими роликами, пяти индукционных нагревателей, рольганга, установки водяного охлаждения шва. Локальная термообработка производится по следующей технологии:
- нагрев зоны шва индукционными нагревателями до 900±20оС;
- охлаждение шва на воздухе при перемещении трубы до зоны водяного охлаждения;
- охлаждение шва в установке водяного охлаждения.
Трубы считаются прошедшими ЛТО, если температура нагрева сварного шва по всей их длине не выходит за пределы 900±20оС. Если указанное условие не выполняется, хотя бы на одном участке шва любой протяженности, труба признается не прошедшей ЛТО и автоматически выводится из потока на газовый резак.
Трубы после воздушного охлаждения проходят установку водяного охлаждения, предназначенную для снижения температуры сварного шва. Установка водяного охлаждения имеет водораспылительный коллектор, расположенный над трубой, в закрытом кожухе. Пар, образующийся в кожухе, вытягивается вентиляционной системой. Охлаждающая вода подается от системы охлаждения. Труба после установки водяного охлаждения должна иметь температуру не выше температуры кипения воды.
После водяного спрейера трубы поступают в калибровочный стан и правильную клеть.
После прохождения трубы через клети измеряется периметр трубы, и валки регулируются таким образом, чтобы периметр трубы после каждой клети и периметр трубы на выходе из клети соответствовали указанным в технологических картах.
Трубы, после калибровочного стана, подвергаются правке в правильной клети. Правильная клеть состоит из сварной конструкции открытого типа, в которой размещается четырехвалковая кассета. В кассете установлены четыре холостых правильных валка, имеющие свои нажимные механизмы. Кассета имеет механизм с электроприводом для перемещения ее в вертикальном и горизонтальном направлениях.
После правки труб производится маркировка индекса смены и номера партии с помощью маркировщика барабанного типа в соответствии с картами контроля.
Автоматическая порезка непрерывно движущейся бесконечной трубы на мерные длины осуществляется летучим отрезным станком, который состоит из тележки с режущей головкой, рельсов, входного и выходного зажимов, входного и выходного поддерживающих роликов и механизма для передвижения тележки.
Разрезка трубы осуществляется четырьмя режущими дисками, вращающимися вокруг трубы и имеющими одновременное радиальное перемещение. Длина труб 11 - 11,2 м, точность порезки трубы ± 5 мм. Контроль качества порезки труб производится в соответствии с картами контроля.
После отрезки первой трубы новой партии на центральный пульт автоматически передается информация о новом номере партии. На табло центрального пульта начинает высвечиваться номер новой партии и количество годных труб по мере их изготовления и количество бракованных труб. Информация по причинам брака выдается распечаткой на центральном пульте управления.
Трубы по указанию мастера участка отделки, с промежуточного склада электромостовым краном передаются на загрузочный стеллаж отрезного станка для отбора проб на сплющивание. Отрезка проб производится на отрезном станке от переднего и заднего концов каждой трубы, прошедшей ЛТО.
После порезки труб внутренний грат разрезается ножом вытяжной клети. Трубы, не прошедшие ЛТО, отбракованные УЗК, с поперечным швом, с «окнами», длиной свыше 12 м, направляются по рольгангу в автоматическом режиме на газовый резак.
Газовый резак оснащен двумя вращающимися вокруг неподвижной трубы газовыми горелками. Для отбора проб для испытаний используются две горелки, а для разрезки труб – одна горелка. На газовом резаке производится вырезка проб для проведения испытаний на сплющивание, механических испытаний, химического анализа, испытания на пластичность, металлографического анализа, а так же разрезка дефектных труб. Вырезанную пробу контролер ОТК маркирует и передает в ЦЗЛ (Центральную Заводскую Лабораторию). Результаты механических испытаний и химического анализа передаются в ОТК из ЦЗЛ по телефаксу.
Стружка внутреннего грата удаляется из трубы на автоматической установке промывки за счет напора воды при вращении трубы. Вода, оставшаяся в трубе, удаляется продувкой воздухом. Вода, после удаления стружки грата, собирается в резервуар, стружка и окалина осаждаются, а вода насосом снова подается на промывку. Время промывки обсадных труб, труб для магистральных трубопроводов 10 с. трубы после промывки передаются по рольгангу к косовалковой правильной машине.
Правка труб осуществляется на косовалковой правильной машине, имеющей три пары приводных валков и один холостой. Правка осуществляется знакопеременным изгибом, который получают за счет смещения средней пары валков относительно двух опорных валков в сочетании со знакопеременным сплющиванием. Холостой валок предназначен для облегчения подачи труб на выходной рольганг. Отслаивающаяся в процессе правки труб окалина смывается в бак-отстойник охлаждающей валки жидкостью. Бак-отстойник с окалиной убирается при помощи мостового крана.
Несколько труб подвергается пробной правке, в процессе которой правильная машина подстраивается путем корректировки смещения средней пары валков, величины сплющивания и угла разворота валков. Настройка правильной машины считается законченной, если труба имеет общую кривизну не более 0,2% от общей длины трубы, а также отсутствуют на наружной поверхности трубы винтовой след, отпечатки, царапины, задиры и смятие переднего конца трубы.
Измерение кривизны труб производится на стеллажах приемных карманов при отключенном транспортном оборудовании. Если кривизна труб превышает допустимые значения, производится корректировка настройки правильной машины и повторный контроль кривизны труб. Трубы с кривизной, превышающей допустимые значения, передаются электромостовым краном на стеллаж перед правильной машиной для повторной правки.
В зависимости от назначения, трубы после правильной машины направляются по транспортному рольгангу на подрезку торцов и снятие наружной и внутренней фасок. Подрезка торцов и снятие наружной и внутренней фасок труб производится на двух параллельных линиях, каждая из которых оснащена транспортными средствами и двумя станками для обработки торцов труб.
Трубы, сваренные из одного штрипса, выкладываются на одну из линий торцеподрезных станков, трубы, сваренные из следующего штрипса выкладываются на другую линию и так далее с разделением труб каждого штрипса.
При остановке стана, отсутствии труб в отделке допускается задача труб с промежуточного склада электромостовым краном на линии торцовки.
По транспортному рольгангу трубы передаются к ультразвуковому дефектоскопу с вращающимися пробниками, где производится контроль качества труб по телу трубы и по сварному шву.
Забракованные трубы автоматически отмечаются краской. Отмеченные трубы выводятся из потока на браковочный стеллаж, формируются в пакеты и электромостовым краном передаются на склад.
Годные трубы, прошедшие ультразвуковой контроль, передаются по транспортному рольгангу на нарезку резьбы. Нарезка резьбы производится на двух параллельных линия, каждая из которых оснащена транспортными средствами и двумя трубонарезными станками с числовым программным управлением. Выбор линии нарезки осуществляется на главном транспортном пульте ротационного УЗК.
Резьбонарезной станок состоит из станины, шпиндельной бабки с инструментальной головкой, приводов, механизмов подачи, центрирования и зажима трубы. Инструментальная головка состоит из четырех резцовых блоков с кассетами, в которые вставляются резьбонарезные гребенки и пластины для обточки наружной поверхности трубы, суппортов и толкателя. Нарезка резьбы производится автоматически, согласно заданной программе. Для отвода стружки применяется стружколом.
После нарезания резьбы трубы проходят визуальный контроль состояния резьбовой поверхности и качества удаления внутреннего грата в объеме 100% контролерами ОТК. Затем трубы передаются на установку нанесения треугольного знака и маркировочной полосы. Нанесение треугольного знака и маркировочной полосы производится на годные трубы.
Контроль геометрических параметров резьбы производится специальными накладными приборами и резьбовыми калибрами. Контроль качества резьбы изделий включает:
- визуальный осмотр поверхности резьбы;
- контроль длины резьбы с полным профилем;
- контроль расстояния от торца трубы до треугольного знака;
- контроль геометрических параметров резьбы (высота профиля, шаг на длине 25,4 мм резьбы с полным профилем и шаг на суммарной длине с с полным профилем, конусность по внутреннему диаметру резьбы труб и ниппелей, конусность по наружному диаметру резьбы муфт и колец);
- контроль натяга резьбы;
- контроль соосности резьбы обоих концов муфт;
- контроль углов профиля резьбы труб и муфт;
- контроль сбега резьбы труб по стандарту API 5CT.
Контроль длины резьбы труб производится на каждой трубе с помощью шаблона, который подбирается в зависимости от условного диаметра труб.
Измерение расстояния до основания треугольного знака производится штангенциркулем ШЦ-1-125 ГОСТ 166 или шаблоном.
Контроль геометрических параметров и натяга резьбы производится специальными накладными приборами и резьбовыми калибрами.
Отклонение высоты профиля резьбы от эталонной определяет индикаторный высотомер (см. рис.2.4).
Контроль шага резьбы производится при помощи индикаторных шагомеров. Индикаторный шагомер показывает отклонение шага резьбы изделия от установленного расстояния между двумя наконечниками прибора.
Рисунок 2.4 - Индикаторный высотомер.
Измерение конусности резьбы производится по внутреннему диаметру резьбы индикаторным прибором (см. рис.2.5). Измерение конусности производится между первой, пятой и десятой нитками резьбы, при этом расстояние между измеряемыми сечениями составляет 25.4мм.
Рисунок 2.5 - Измерение конусности резьбы.
Контроль натяга резьбы труб производится рабочими резьбовыми определяют как расстояние между измерительной плоскостью калибра и торцом изделия и измеряют штангенглубиномером ШГ-80 ГОСТ 162.
Соосность муфт проверяется специальным индикаторным прибором (см. рис 2.6).
Рисунок 2.6- Индикаторный прибор для измерения соосности муфт.
Контроль точности профиля резьбы и углов наклона боковых сторон профиля резьбы труб и муфт производится трехиндикаторным прибором.
Контроль сбега резьбы труб производится накладным прибором
(см. рис.2.7).
![]() |
Рисунок 2.7 - Контроль сбега резьбы.
Годные трубы с нарезанной резьбой по транспортеру передаются на станок для предварительной навертки муфт, перед наверткой муфты на резьбу наносится резьбоуплотнительная смазка. Муфты для навертки поступают с участка их изготовления в специальных контейнерах.
Муфты для электросварных обсадных труб изготавливаются из бесшовных труб группы прочности J – 55 (Д), поставляемых по техническим условиям. Муфтовые трубы со склада цеха подготовки производства перевозятся автотранспортом в пакетах весом от 5 до 10 тонн. Трубы разгружаются электромостовым краном и хранятся на складе цеха в карманах по размерам, плавкам и заводам-поставщикам.
На отрезном станке производится разрезка муфтовых труб на мерные заготовки в ручном и автоматическом режиме. Подача контейнеров с заготовками к муфтонарезным станкам производится с помощью электропогрузчиков. Разгрузка заготовок из контейнера производится автоматическим манипулятором.
Торцовка, расточка и нарезка резьбы муфт производится на специальных станках. Муфты обрабатываются на станке по принципу «неподвижная заготовка – вращающийся инструмент» способом односторонней обработки. В качестве смазочно-охлаждающей жидкости используется водный раствор эмульсола. Заточка режущего инструмента производится на участке подготовки инструмента.
Годные муфты манипулятором загружаются в контейнер и электрокаром передаются на участок оцинковки муфт. Забракованные муфты укладываются оператором пульта управления вручную в контейнер с надписью «Брак». Контейнер с забракованными муфтами, по мере заполнения, передается электромостовым краном на площадку отгрузки металлоотходов.
Муфты, перед цинкованием в соответствии с требованиями договора подвергаются 100% ультразвуковому контролю. Муфты, не прошедшие ультразвуковой контроль, отсортировываются.
Специальные муфты в соответствии с требованием стандарта АНИ 5 СТ изготавливаются по требованию потребителя. Изготовление специальных муфт производится путем проточки наружного диаметра нормальных муфт. Проточка наружного диаметра производится на специальных станках с ЧПУ твердосплавным режущим инструментом по заданной программе.
Загрузка муфт в станок и разгрузка их после проточки в контейнеры производится оператором станка вручную.
Изготовление муфт с проточками под уплотнительные кольца из фторопласта производится на шестипозиционных агрегатных станках способом двухсторонней обработки. Установку уплотнительных колец в канавки муфт производит технологический рабочий на участке цинкования муфт, на отводящем рольганге, перед клеймовочной машиной или на отдельной площадке. Перед монтажом кольцу придают овальную форму, деформируя его по наружному диаметру, что обеспечивает свободное перемещение кольца в осевом направлении внутри муфты до месторасположения проточки.
После предварительной навертки на муфтонаверточном станке производится окончательная навертка муфт. Операция окончательной навертки муфт совмещена с шаблонированием труб по внутреннему диаметру.
После навертки муфт трубы поступают на кольценаверточный станок, где на свободный резьбовой конец трубы производится навертка защитного кольца.
Перед наверткой на резьбу наносится резьбоуплотнительная или антикоррозионная смазка, исключающая повреждение резьбы. Допускается ручная навертка предохранительных колец на трубы, которая производится на передающем транспортере к муфтозатяжному станку.
Трубы с навернутыми муфтами и кольцами по транспортеру поочередно поступают на промывку внутренней полости, затем проходят гидравлическое испытание внутренним давлением. Гидравлическое испытание труб внутренним давлением служит для выявления скрытых дефектов тела трубы, включая сварной шов, и обнаружения негерметичности резьбового соединения "труба-муфта".
Сначала осуществляют промывку струей воды, подаваемой во вращающуюся трубу со стороны муфтового конца. После промывки автоматически измеряют длину трубы, в соответствии с которой устанавливают заднюю уплотнительную головку пресса. Трубу перемещают на испытательную позицию пресса, осуществляя герметизацию концов трубы манжетами. Закрывают боковые защитные створки. Трубу заполняют испытательной жидкостью, которая вытесняет воздух через дренажный клапан, в качестве испытательной жидкости применяется водный раствор эмульсола. После удаления воздуха клапан закрывают и давление автоматически повышают до заданной величины, которая регистрируется на диаграмме манометра. При достижении испытательного давления жидкости в трубе автоматически производится обстукивание ее поверхности молотком. Прессовщик визуально контролирует сварной шов труб на наличие течи и выпотевания.
По истечении 10 секунд выдержки под давлением проводят сброс давления до нулевого уровня через редукционный клапан. Разгерметизируют полость трубы путем снижения давления жидкости в камерах манжет, при этом она восстанавливает сваю первоначальную форму, освобождая стеллаж.
Трубы, не выдержавшие гидравлическое испытание (наличие течи в резьбовом соединении «труба – муфта», разрывы труб по телу и сварному шву), маркируются краской краскоотметчиком нанесением браковочной метки.
Трубы, не выдержавшие гидроиспытание, с неудовлетворительным качеством навертки муфт (трещины, вмятины, на муфтах, не выполнение длины затяжки), выводятся из потока, направляются на приемный стеллаж. После осмотра, наладчиком агрегатных и специальных станков совместно с бригадиром или контрольным мастером ОТК трубы, не подлежащие ремонту (разрывы, трещины) маркируются краской нанесением отметки «Брак» наладчиком агрегатных и специальных станков и отгружаются в изолятор брака на складе.
Забракованные трубы по течи в резьбовом соединении при гидроиспытании и качеству навертки муфт направляются с помощью мостового крана на отрезной станок для обрезки муфты.
После гидроиспытания трубы поступают на станок для навертки ниппеля в свободный конец муфты. Ниппеля служат для защиты резьбы свободного конца муфты от механических повреждений и коррозии при транспортировке и хранении. Перед наверткой на резьбу муфты производится нанесение резьбоуплотнительной или антикоррозионной смазки. Допускается ручная навертка ниппелей в муфты, которая производится на транспортере к маркировочной машине. Ниппель навертывается на всю длину резьбы и должен свинчиваться вручную.
Годные трубы направляются на установку взвешивания и измерения длины. Взвешиванию и измерению длины поочередно подвергается каждая труба. В соответствии с требованиями заказа результаты измерения печатаются системной пишущей машинкой в британской (футы, фунты) или метрической системах. Измерение длины и взвешивание каждой трубы осуществляется в автоматическом режиме. Машина выполняет расчет длины и массы труб с исключением длины и массы кольца и ниппеля.
После взвешивания трубы проходят клеймение и маркировку на клеймовочной машине автоматически. Знаки клеймения наносятся на наружную поверхность вдоль трубы на расстоянии не более 305 мм от навинченной муфты и включают в себя: номер трубы, товарный знак, наименование стандарта, масса, марка стали, способ изготовления труб.
После проведения окончательной приемки контролером ОТК дается разрешение на нанесение на годных трубах маркировки. Она наносится вручную краскораспылителем белой краской по трафарету.
После нанесения маркировки на наружную поверхность труб и муфт наносится консервационное покрытие по требованию заказчика.
Трубы в объеме пакета передаются краном на загрузочный стеллаж установки пакетирования и обвязки. Установка пакетирования и обвязки предназначена для формирования труб в количестве от 7 до 19 штук в пакеты шестигранной формы и обвязки их проволокой диаметром 6 мм в 2 нитки в четырех-шести местах по длине пакета. С двух концов пакета крепятся металлические ярлыки, которые должны содержать необходимую информацию о продукции, внешнеэкономической организации, страну назначения, товарный знак.
Погрузка труб в вагоны производится в соответствии с приказами на отгрузку, выданными ПРБ цеха. Пакеты труб выдаются с помощью мостового крана из ячеек склада. После проверки соответствия труб, подлежащих отгрузке требованиям и технических условий производят погрузку их в вагон. Каждая поставляемая отгрузочная партия труб должна сопровождаться документом (сертификатом), удостоверяющим их соответствие требованиям технических условий.
Дата добавления: 2020-11-23; просмотров: 1178; Мы поможем в написании вашей работы! |
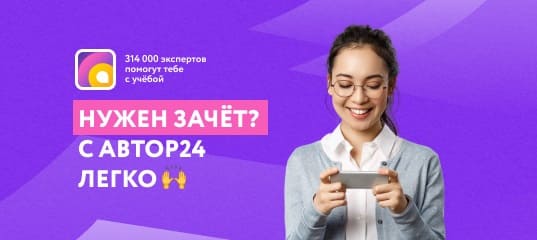
Мы поможем в написании ваших работ!