Профилировании лопаток турбин
Этап профилирования лопаток турбин наступает после проведения газодинамического расчета ступени. Конструирование обводов профиля лопатки возможно двумя основными способами: первый способ – применение ранее разработанных профилей, обычно представляемых в атласах профилей, второй способ – собственная разработка геометрических параметров профиля. Известно, что обводы профиля лопатки могут быть описаны различными кривыми: параболами, совокупностью сопряженных окружностей, лемнискатами, эллиптическими кривыми и т.д. Этому вопросу посвящено достаточно много литературы. Однако если рассматривать основу расчетной схемы построения профиля лопатки, то схема основана на одних и тех же положениях и исходных параметрах, несмотря на различие в кривых, описывающих спинку и корытце профиля. На рис. 1 показана наиболее типичная расчетная схема [1] построения профиля лопатки с параболической спинкой и корытцем в виде дуги одной окружности. Основные сложности при проектировании новых профилей возникают при соблюдении одного из требований методики – дуга спинки lpf должна проходить через точку p. Опыт проектирования показал, что указанное требование практически на начальной стадии проектирования не выполняется. Необходимы дополнительные построения, чтобы добиться прохождения кривой спинки через точку p. Рисунок 1 - Расчетная схема построения профиля лопатки турбины [1] В работе [1] рекомендуется для этого увеличивать угол заострения выходной кромки γвых. Однако как показали дальнейшие исследования, этот путь не является однозначным. Секция 2 «ПОРШНЕВЫЕ И ГАЗОТУРБИННЫЕ ДВИГАТЕЛИ». Материалы международной научно-технической конференции ААИ «Автомобиле- и тракторостроение в России: приоритеты развития и подготовка кадров», посвященной 145-летию МГТУ «МАМИ». 74 Для решения этой проблемы был проведен численный эксперимент с использованием программы построения расчетной схемы профиля лопатки турбины и подпрограммы расчета параметров сопряжения входной и выходной кромок профиля и окружности корытца. В таблице 1 представлена подпрограмма расчета параметров сопряжения кромок и окружности корытца профиля.
|
|
Билет
Классификация пусков и основной принцип их проведения
Технология пуска турбины в большой степени зависит от температурного
состояния оборудования перед ним. В соответствии с этим различают пуски
из холодного, неостывшего и горячего состояний.
446
Эта классификация (для энергоблоков) производится по температуре турбины
и главных паропроводов перед пуском.
Если котел и паропроводы блока ТЭС полностью остыли, а температура
турбины не превышает 150 °С, то считают, что пуск происходит из холодного
состояния. Для мощных энергоблоков для остывания до такой температуры
требуется не менее 90 ч. Пускам из горячего состояния соответствует
температура турбины 420—450 °С и выше. Такая температура достигается за
6—10 ч. Промежуточным значениям температуры турбины перед пуском
соответствуют пуски из неостывшего состояния.
На практике обычно пусками из горячего состояния называют пуск после
ночного простоя, из неостывшего состояния — после простоя в субботу и
воскресенье, из холодного состояния — после простоев большей
длительности. Пуск турбины из любого температурного состояния должен
проводиться с учетом явлений, возникающих при нестационарных тепловых
режимах, рассмотренных выше.
Всякое удлинение пуска приводит к дополнительным затратам топлива.
Поэтому пуск должен производиться быстро, однако не в ущерб надежности.
Таким образом, основной принцип проведения пуска состоит в том, что он
должен проводиться со скоростью, максимально возможной по условиям
надежной работы.
|
|
Обозначения на схеме ТЭС:
1. Топливное хозяйство;
2. подготовка топлива;
3. котел;
|
|
4. промежуточный пароперегреватель;
5. часть высокого давления паровой турбины (ЧВД или ЦВД);
6. часть низкого давления паровой турбины (ЧНД или ЦНД);
7. электрический генератор;
8. трансформатор собственных нужд;
9. трансформатор связи;
10. главное распределительное устройство;
11. конденсатор;
12. конденсатный насос;
13. циркуляционный насос;
14. источник водоснабжения (например, река);
15. подогреватель низкого давления (ПНД);
16. водоподготовительная установка (ВПУ);
17. потребитель тепловой энергии;
18. насос обратного конденсата;
19. деаэратор;
20. питательный насос;
21. подогреватель высокого давления (ПВД);
22. шлакозолоудаление;
23. золоотвал;
24. дымосос (ДС);
25. дымовая труба;
26. дутьевой вентилятов (ДВ);
27. золоуловитель.
Описание технологической схемы ТЭС:
Обобщая все вышеописанное, получаем состав тепловой электростанции:
§ топливное хозяйство и система подготовки топлива;
§ котельная установка: совокупность самого котла и вспомогательного оборудования;
§ турбинная установка: паровая турбина и ее вспомогательное оборудование;
§ установка водоподготовки и конденсатоочистки;
§ система технического водоснабжения;
§ система золошлокоудаления (для ТЭС, работающих, на твердом топливе);
|
|
§ электротехническое оборудование и система управления электрооборудованием.
Билет
1) Параметры пара существенно влияют на КПД цикла паротурбинной установки. Так, термический КПД цикла при изменении начальных давления (от 10 МПа до 23,5 МПа) и температуры (от 500 до 565°С), а также давления в конденсаторе (от 4 до 6 кПа) может изменяться от 0,43 до 0,48. Рассмотрим, как влияют начальные параметры (температура t0 и давление p0) пара, наличие промежуточного перегрева пара и его температуры tпп, а также давление конденсаторе рк на термический КПД [3].
Начальное давление пара. Повышение начального давления пара р0 связано с увеличением температуры его насыщения, т. е. уровня, при котором происходит передача теплоты в котле. Как известно, наиболее совершенным термодинамическим циклом является цикл Карно, КПД которого
ηк = 1- Тк/Т0, где Т0 и Тк - температуры подвода и отвода теплоты. Для любого цикла, например цикла Ренкина, можно определить эквивалентную температуру подвода теплоты Тэ=(Т0)к, которая обеспечила бы соответствующий термический КПД ηt
(1.20)
На рис. 1.1,б была показана эта эквивалентная температура Тэ.
Для сравнения на рис. 1.5(а), изображены в T,s-диаграмме два идеальных цикла ПТУ при начальных давлениях пара р0 и р01.
Рис.1.5. Сравнение T,s-диаграмм циклов ПТУ с разными начальными темпера турами (а), давлениями (б), с промежуточным перегревом (в) и разными давлениями в конденсаторе (г).
В цикле 1—2—3'—4'—5'—1 с повышенным начальным давлением p01>p0 подвод теплоты происходит на более высоком температурном уровне, т. е. Tэ1>Tэ. Следовательно, этот цикл более экономичен, чем цикл 1—2—3—4—5—1.
Необходимо отметить, что увеличение начального давления пара при той же температуре приводит к росту влажности в кон це процесса расширения, что при прочих равных условиях отри цательно влияет на надежность турбины (увеличивается эрозия металла) и снижает ее относительный внутренний КПД.
Однако по мере увеличения начального давления пара экви валентная температура Tэ сначала возрастает, а затем начинает постепенно уменьшаться. Таким образом, существует оптималь ное по эквивалентной температуре Tэ начальное давление пара. Причем, чем выше эта температура, тем выше давление, при ко тором получают максимальный термический КПД.
Начальная температура пара. Повышение начальной темпе ратуры tо пара существенно увеличивает экономичность ПТУ. Если сравнить два цикла, различающиеся только начальными температурами пара (рис. 1.5,б), то КПД первого цикла 1—2—3— 4'—5'—1 с более высокой температурой Т01 будет выше КПД вто рого цикла 1—2—3—4—5—1 с меньшей температурой То. При прочих равных условиях начальная температура Tэ1 подвода теплоты в первом цикле выше начальной температуры Тэ подво да теплоты во втором цикле.
Трудности, которые возникают при повышении температуры, связаны с тем, что стали, применяемые в современном энергомашиностроении, теряют прочность при высоких температурах, так как резко падают пределы их текучести и прочности, а также снижается предел длительной прочности. Последнее обстоятельство приводит к необходимости ограничивать срок службы деталей или применять дорогие жаростойкие высоколегированные стали.
Кроме того, увеличение температуры tо в реальных турбинах уменьшает влажность в конце процесса расширения пара. Это повышает надежность и срок службы турбины вследствие менее интенсивной эрозии металла, а также несколько увеличивает ее относительный внутренний КПД.
Промежуточный перегрев пара. В цикле с промежуточным перегревом пар после расширения в ЧВД турбины (см. рис. 1.1,а) от давления р0 до давления р1 направляется в промежуточный перегреватель, где к нему дополнительно подводится теплота и повышается его перегрев. Затем пар вновь возвращается в турбину и расширяется до давления рк в конденсаторе.
Как видно из T,s-диаграммы, показанной на рис. 1.5,в, промежуточный перегрев может вызвать повышение экономичности цикла. В самом деле, начальная температура TЭ1 эквивалентного цикла Карно в схеме с промежуточным перегревом выше соответствующей температуры Тэ в цикле без
промежуточного перегрева. Повышение КПД цикла произойдет только в том случае, если промежуточный перегрев осуществляется до такой температуры, при которой эквивалентная температура (TЭ)ПП присоеди ненного цикла 4—5—6—7—4 окажется выше, чем основного, изображенного на рис.1.5,в площадью 1—2—3—4—1.
При введении промежуточного перегрева влажность пара в конце процесса расширения уменьшается, что повышает относительный внутренний КПД турбины. При этом интенсивность эрозии уменьшается, что положительно сказывается на надежности работы турбины.
Для дальнейшего повышения термического КПД можно при менять двукратный промежуточный перегрев, который из-за усложнения ПТУ мало распространен.
Давление в конденсаторе. При уменьшении давления рк в конденсаторе понижается температура Тк, при которой произво дится отвод теплоты от пара охлаждающей водой. В результа те увеличивается средняя разность температур в цикле, а следовательно, и его термический КПД. Для сравнения на рис. 1.5,г изображены в T,s-диаграмме два идеальных цикла, отличаю щиеся только давлением пара рк в конденсаторе. Располагаемая работа цикла с пониженным давлением рк 1'—2—3—4—5—1' превышает располагаемую работу цикла 1—2—3—4—5—1 с бо лее высоким давлением на значение, эквивалентное площади 1—5—5'—1'—1. Но в этом случае увеличивается влажность па ра в конце процесса расширения и потеря энергии с выходной скоростью, что отрицательно сказывается на надежности турбины и снижает ее относительный внутренний КПД.
2 ) Вибрация турбо агрегата и ее последствия. Нормы допустимой вибрации Когда говорят о вибрации турбоагрегата то обычно имеют в виду колебания системы состоящей из собственно турбоагрегата и его фундамента установленного на свайне основание или на грунт. Непосредственным источником колебаний являются валопровод турбоагрегата котрой вращаясь на маслянной пленке подшипников предеает через нее усилия на вкладыши подшипников и их корпуса. В свою очередь вирирующие корпуса подшипников и связанные с ними корпуса целиндров возбуждают вибрацию верхней фундаментной плиты а та вибрацию колонн и нижней фундаментной плиты. Вибрация турбо агрегата должна измерятся и регистрироватся с помощью стационарной аппаратуры не прерывного контроля вибрации подшипников опор, которая должна соотв-вать гос стандарт. В часности эта аппаратура должна включать в себя систему защиты с сигнализацией и последующей остановкой турбоагрегата в случае возникнавения недопустимой вибрации или ее внезапного изменения. Вибрация турбо агрегата может происходить во всех трех направлениях. Поэтому ее измеряют на всех подшипниковых опорах в трех взаимно перпендикулярно направлениях. Вертикальном, горизонтально -поперечным, и горезонтально осевом по отношении к оси вала турбоагрегата. Нормы допустимой вибрации. Работающий турбоагрегат всегда какой то степени вибрирует. по этому ПТЭ предусматривает жесткие нормы на допустимый уровень вибрации. Вибрационное состояние турбоагрегата оценивает по наибольшему значению виброскорости, действующем вертикальном горизонтально - поперечном и горизонтально осевом направлениях. Длительная эксплуатация турбоагрегатов мощностью 200 МВт и более допускается при вибрации подшипников опор, не превышающей 2,8 мм/с. На первый взгляд может показатся что нормы вибрации турбоагрегатов чрезмерно жесткие. Однако следует имет введу что вибрация измеряется на корпусе подшипника, а для турбоагрегата важна вибрация вала,которую и вызывают вибрацию корпуса подшипника. Подшипник установленный на фундамента или встроенный в выходной потрубок обладает как и всякая система своими вибрационными характеристиками и его вибрация зависят от близасти частоты возмущающей силы.
Билет
§ 1)Подавляющее большинство АЭС с водным теплоносителем имеет турбины на насыщенном паре. Основные конструктивные особенности таких установок связаны с их относительно низкой экономичностью (большие расходы пара) и нарастающей влажностью по ступеням (организация сепарации между цилиндрами).
§ В любых паровых турбинах приходится иметь дело с работой на влажном паре. Если для турбин на перегретом паре это относится только к последним ступеням, то для машин на насыщенном паре большая часть ступеней, (а в отсутствие промежуточного перегрева — все ступени турбины) работают на влажном паре. Влияние влажности пара сказывается на тепловой экономичности установки, так как внутренний относительный к.п.д. турбины уменьшается при работе на влажном паре. Если для группы ступеней на перегретом паре в зависимости от объемного расхода и отношения давлений на входе и выходе к.п.д. = 89—90%, то при использовании влажного пара он тем меньше, чем больше влажность. Приближенно можно считать, что увеличение средней влажности пара на 1 % приводит к уменьшению внутреннего относительного к.п.д. турбины также примерно на 1%.
§ Влажность пара отрицательно влияет на работу турбины, вызывая эрозию ее лопаток. Существуют разные методы предотвращения этого. Один из методов — отвод влаги из проточной части турбины при помощи различных сепарационных устройств. К этим устройствам относятся прежде всего внешние турбинные сепараторы, устанавливаемые между корпусами турбины.
§ Конструкции внутри турбинных сепарационных устройств различны. Значительная часть влаги отбрасывается к корпусу по поверхности лопаток рабочего колеса, поэтому такие сепарационные устройства целесообразней располагать непосредственно за рабочим колесом, тогда отведенный конденсат уже не будет оказывать вредного влияния на работу последующих ступеней турбины. Если в потоке пара, поступающем из предыдущей ступени, содержится значительное количество конденсата, то можно отводить влагу и при помощи влагоулавливающего устройства, расположенного за сопловым аппаратом. Для удаления влаги из влагоулавливающей камеры отсасывается пар, который направляется затем в регенеративную систему. Эффективность влагоудаления возрастает с увеличением отсоса, но при влажностях менее 5% она невелика. Поэтому, хотя теоретически было бы целесообразно отводить влагу после каждой ступени, влагоулавливающие устройства располагают не за всеми ступенями. В ряде установок, несмотря на наличие таких устройств, их не используют и предпочитают ограничиваться только внешней сепарацией между корпусами турбин. Так как эрозионные разрушения лопаток паровых турбин начинаются с их поверхности, то применяют различные способы борьбы с эрозией путем упрочнения поверхности лопаток — хромирование, местную закалку их кромок, нагартование, упрочнение поверхностного слоя электроискровым способом и др. На отечественных заводах наиболее распространен последний способ. В качестве упрочняющего сплава хорошо зарекомендовал себя стеллит.
§ В современных турбинах на насыщенном паре упрочнение поверхностного слоя обязательно, особенно для последних ступеней, у которых эрозионный износ больше в связи со значительными окружными скоростями. Эффективность защитных мероприятий в решающей мере зависит от качества их выполнения, причем при плохой защите эрозия идет в еще большей мере, чем в отсутствие защиты. В последние годы стали изготовлять лопатки для влажного пара из коррозионно-стойких материалов.
§ На рисунке 5 представлена проточная часть цилиндра высокого давления (ЦВД) турбины К-500-65/3000 спо ступенчатой сепарацией, представляющей собой систему ловушек для влаги, срывающейся с рабочих и направляющих лопаток. На рабочих лопатках с малыми углами входа (менее 90°) входные кромки лопаток открыты за счет среза части бандажа для улучшения сепарации влаги. Напротив этого среза в статоре турбины расположена входная щель ловушки. Размер выбран таким, чтобы отсос пара невелик, а влага из отсасываемого потока не выпадает. За щелью расположена промежуточная буферная полость, соединенная с последующей камерой регенеративного отбора.
§ Поскольку реакторная установка РБМК - 1000, являться одноконтурной то пар поступающий на турбину является радиоактивным, что в свою очередь приводит к некоторым особенностям при работе.
§ В системе одноконтурной АЭС досушивание пара досуха перед его перегревом приводит к твердым радиоактивным отложениям в области пароперегревателя, что затрудняет доступность оборудования для ремонта. Протекание через турбинную установку радиоактивного пара способствует различной радиоактивности отдельных ее элементов. Это должно учитываться при размещении оборудования и организации его эксплуатации. В машинном зале наибольшая радиоактивность связана с острым паром; она учитывается при компоновке машинного зала. Радиоактивность связана с газовой активностью, быстро спадающей при останове оборудования.
§ Турбина в эксплуатации не требует постоянного обслуживания, поэтому для турбин одноконтурных атомных электростанций не нужна специальная биологическая защита. Относительно большой уровень радиоактивности фильтров конденсатоочистки характерен для конечного периода их эксплуатации и связан с накоплением в них радиоактивных продуктов коррозии. В начальный период эксплуатации фильтров их радиоактивность находится на уровне активности в водяной емкости конденсаторов. Водяные емкости конденсаторов и конденсатоочистку снабжают биологической защитой.
§ Радиоактивность подогревателей регенеративной системы турбины различна. Если для первого по ходу воды подогревателя уровень радиоактивности низок, то в последнем по ходу воды он относительно высок. Греющий пар для последнего подогревателя отводится из головной части машины, и конденсация его в корпусе подогревателя приводит к относительно высокой радиоактивности водяной емкости. Радиоактивность конденсата греющего пара выше, чем радиоактивность самого пара, так как весовое количество среды в водяном объеме подогревателя больше, чем в ступени турбины.
§ Радиоактивность водяной емкости корпуса подогревателя, обогреваемого паром из головной части турбины, больше, чем водяного объема конденсатора, так как за время прохождения пара от входа в турбину до конденсатора газовая радиоактивность в значительной мере спадает. Поэтому водяная емкость подогревателей регенеративной системы турбин одноконтурной станции тоже требует биологической защиты. Безусловно необходима биологическая защита и той части объема сепаратора, в которой скапливается сепарат. Все это находит свое отражение в компоновочных решениях машинного зала одноконтурной АЭС. В частности на Смоленской АЭС конденсаторы подогреватели низкого давления и сепаратор подогреватель расположены под полом машинного зала, ниже оси турбины.
§ На концевые уплотнения турбины нельзя подавать радиоактивный пар, чтобы не повысить радиоактивный фон машинного зала. В связи с этим в системе одноконтурной АЭС обязательно должен быть испаритель, производящий чистый нерадиоактивный пар. Так как весь конденсат пара, поступающего на турбину, проходит через конденсатоочистку, то радиоактивность его ничтожна. Поэтому испаритель, производящий пар для уплотнений, питается конденсатом (питательной водой) после деаэратора.
§ Пар, подаваемый на уплотнения вала турбины, отсасывается специальным эжектором уплотнений. Эжекторы уплотнений турбины работают постоянно, как и основной эжектор, но расход парогазовой смеси и давление всасывания у эжекторов уплотнений больше, чем у основных. Промежуточный пароперегреватель предназначен для осушки (сепарации) и перегрева пара после ЦВД турбины.
§ СПП-500-2 выполнен в виде однокорпусного вертикального аппарата и состоит из сепаратора, расположенного в верхней части, и пароперегревателя, расположенного в нижней части аппарата. Схема СПП-500-2 показана на рисунке 2.
§ Сепаратор представляет собой цилиндрический сварной сосуд высотой 4367 мм с наружным диаметром 4170 мм.
§ Основными узлами сепаратора являются:
§ Корпус (5), состоящий из обечайки и приваренного к ней крышки, в крышку вварены два патрубка Ду – 700, один для отбора пара (четвертый обор турбины), другой для присоединения предохранительных клапанов.
§ На обечайке корпуса расположены два патрубка Ду – 200 для слива сепарата и один патрубок для подвода влажного пара.
§ Обечайка и крышка изготовлены из стали 12Х18Н9Т;
§ В верхней части корпуса СПП расположены:
§ а) центральная труба Ду-1200, переходящая в верхней части в переходной выходной патрубок, по которому осуществляется отвод перегретого пара из СПП;
§ б) сепарационное устройство;
§ г) цилиндрическаяпроставка с линзовым компенсатором. Проставка помещается между сепарационным устройством и центральной трубой.
§ Сепарационное устройство (6) состоит из 20 унифицированных блоков (смотри рисунок 3), расположенных радиально в кольцевом пространстве между обечайкой корпуса и центральной трубой. В сепарационном устройстве отделение влаги осуществляется на поверхности сепарирующих элементов. Сепарирующие элементы – жалюзи, представляют собой волнообразно изогнутые листы, расположенные вертикально и набранные в пакеты. Пакеты жалюзи прикрепляются к вертикальным стойкам каркаса. Каждый пакет в нижней части имеет корыто, по которому сливающийся в него сепарат отводится к центру аппарата.
§ Каждый унифицированный блок состоит из трех вертикально расположенных пакетов, Для равномерного распределения потока пара по каждому пакету перед ним установлены направляющие лопатки, а запакетам установлены дырчатые щиты.
§ Соседние блоки отделены друг от друга радиально расположенным изогнутым листом, образующим вместе с передним блоком клиновидный, сужающийся к низу канал для распределения пара по пакетам, а с задним такой же канал, но расширяющийся к низу для выхода осушенного пара.
§ Все детали сепарационного устройства изготовлены из стали 12Х18Н9Т;
§ Пароперегреватель содержит следующие основные узлы:
§ а) корпус;
§ б) теплообменная установка 1 и 2 ступеней перегрева;
§ в) четыре камеры подвода греющего пара;
§ г) четыре камеры отвода конденсата греющего пара;
§ Корпус пароперегревателя состоит из обечайки и приваренной к ней нижней опорной юбки. Нижняя часть опорной юбки представляет собой плиту толщиной 135 мм. В опорную юбку вварено днище пароперегревателя с патрубком Ду-50 для опорожнения СПП. На обечайке корпуса находятся 8 патрубков в которых расположены камеры подвода греющего пара и отвода его кондесата.
§ Обечайка и опорная юбка изготовлены из стали 12Х18Н9Т.
§ Теплообменная установка 1 и 2 ступеней перегрева состоит из отдельных однотипных кожухотрубных теплообменников, так называемых модулей, представляющих собой трубы в которые вварены трубные доски. В трубных досках развальцованы и обварены трубки Ø25x2 к центру верхней трубной доски каждого модуля. К центру нижней трубной доски каждого модуля приварены так же трубки для отвода из модулей конденсата греющего пара. Для предотвращения проскоков нагреваемого пара мимо трубок модуля, проходы между модулями, как сверху, так и снизу закрываются листами, имеющими форму зазора между модулями.
§ Камеры подвода греющего пара к модулям 1 и 2 ступени перегрева расположены в верхней части корпуса пароперегревателя. Каждая камера представляет собой патрубок Ду-300, в верхней части которого имеется штуцер Ду-120 для подвода греющего пара. В патрубок вварена трубная доска, в которой развальцованы и обварены трубки Ø25x2, подающие пар к модулям. Для удобства обнаружения протечек и глушения трубок подвода греющего пара, патрубки в торцевой части имеют фланцевые заглушки.
§ Камеры отвода конденсата греющего пара 1 и 2 ступеней перегрева расположены в нижней части корпуса пароперегревателя. Каждая камера представляет собой патрубок, имеющей в торцевой части фланцевую заглушку. В верхнюю часть патрубка вварен штуцер Ду-20 для отвода неконденсирующихся газов, в нижнюю часть – штуцер Ду-120 для отвода конденсата греющего пара. В патрубок вварена трубная доска, в которой развальцованы и обварены трубки Ø25x2 для отвода конденсата греющего пара и неконденсирующихся газов из модулей пароперегрвателя.
§ Ориентирование и крепление СПП производится с помощью промежуточного опорного кольца поставляемого вместе с аппаратом. Днище пароперегревателя устанавливается на опорное кольцо и крепится к нему болтами. Затем после окончательной установки и выверки аппарата опорное кольцо приваривается к закладному кольцу фундамента.
§ 2) Пар от начального состояния пара /?0, г0 (или д:0) до давления в конденсаторе рк или на выходе из турбины с противодавлением р2 проходит не только проточную часть, т. е. последовательно расположенные турбинные ступени, но и ряд других элементов, а именно клапаны, входные и выходные патрубки, перепускные ресиверы.
§ Очевидно, что экономичность турбины зависит не только от эффективности проточной части, но и от аэродинамического совершенства этих элементов парового тракта. Определение размеров клапанов и патрубков, рациональное их проектирование— необходимый этап конструирования всего агрегата; не зная потерь энергии в клапанах, патрубках и т. п., нельзя достаточно точно определить экономичность всей установки и правильно определить расход пара через турбину при заданной ее мощности.
§ Основными клапанами турбины являются:
§ стопорный и регулирующие -на входе;
§ отсечной и регулирующий — на линии после промежуточного перегрева;
§ отсечные — перед ЦНД турбин насыщенного и слабоперегретого пара, т. е. после внешней сепарации и промперегрева.
§ Каждому регулируемому отбору пара в турбинах для комбинированной выработки теплоты и электроэнергии соответствует регулирующий орган — клапан или поворотная диафрагма (см. гл. 10).
§ Регулирующие клапаны, так же как регулирующие (поворотные) диафрагмы, во время работы могут быть открыты полностью или частично. Стопорные и отсечные клапаны обычно находятся только в двух положениях —они или закрыты, или полностью открыты.
§ К клапанам предъявляются общие требования:
§ обеспечение необходимой плотности в закрытом положении;
§ по возможности меньшее сопротивление и тем самым меньшие потери энергии при прохождении пара через полностью открытый клапан;
§ приемлемая величина усилия, требуемого для перемещения клапана;
§ стабильный характер течения при всех режимах.
§ Конструкции клапанов разнообразны, и здесь рассматриваются только наиболее типичные из них.
§ В подавляющем большинстве случаев клапаны выполняются односедельными.
§ Наиболее простым является тарельчатый клапан, представленный на рис. 5.19, а. Однако такой клапан имеет серьезные недостатки. Для обеспечения плотного прилегания клапана к седлу необходимы большая удельная сила и, следовательно, значительное усилие. Необтекаемая форма проходного сечения при полностью открытом клапане создает значительное аэродинамическое сопротивление. В таком клапане обычно допускаются небольшие скорости пара — до 50—70 м/с, что, естественно, требует увеличения его размеров, а это в свою очередь приводит к повышенным усилиям для его открытия. Это усилие равно
§
§ Если клапан в месте посадки будет иметь коническую или сферическую форму, то касание клапана с седлом будет происходить по окружности; за счет упругого вдавливания обеспечивается лучшая плотность. Более сложная форма клапана в сочетании с коническим диффузором на выходе (рис. 5.19, б), с одной стороны, создает аэродинамически совершенную форму канала для протекания пара, с другой, позволяет в последующем диффузоре частично использовать кинетическую энергию потока для повышения давления. При этом скорость пара можно увеличить до 100—150 м/с, тем самым примерно вдвое по сравнению с клапаном на рис. 5.19, а сокращается усилие
§ Поскольку для уменьшения усилия Я необходимо дальнейшее сокращение диаметра клапана <1 и тем самым при заданном объемном пропуске пара увеличение скорости с^ и связанный с этим рост потерь, во многих конструкциях применяются различные способы разгрузки усилий. Примеры таких разгруженных клапанов приведены на рис. 5.19, в — д.
§ Клапан малого диаметра ^0 открывается первым, в результате чего давление за всем клапаном повышается и тем самым для подъема основного клапана диаметром йх требуется
§
§ меньшее усилие. Более сложная конструкция разгруженного клапана показана на рис. 5.19, г.
§ Подъем внутреннего клапана малого диаметра с! вызывает понижение давления над главным клапаном и сокращает усилие, необходимое для отрыва его от седла. В отличие от предыдущей конструкции здесь достигается не повышение давления за основным клапаном, а, наоборот, понижение давления над ним, благодаря чему происходит эффективная разгрузка усилия. В практике турбостроения встречаются и иные способы разгрузки. Относительно малое сопротивление имеет клапан колокольного типа (рис. 5.19, д).
§ Особое место занимают двухседельные клапаны, в которых посадка клапана осуществляется одновременно по двум плоскостям. Один из возможных типов такого клапана показан на рис. 5.19, е. Хотя такой клапан почти полностью разгружен и поэтому может быть выполнен очень большого размера, однако имеются трудности обеспечения плотности одновременного прилегания на два седла. Двухседельные клапаны применяются, главным образом, в турбинах невысоких начальных параметров, в которых объемные пропуски пара и, следовательно, размеры клапанов велики.
§ Для того чтобы не суммировать потери давления в двух последовательно расположенных клапанах — стопорном и регулирующем или отсечном и регулирующем, используются объединенные клапаны. Одним из примеров такого клапана
§
§ является конструкция ХТЗ, показанная на рис. 5.20. Два независимых привода (системы регулирования и защиты) управляют одним клапаном, выполняющим функции стопорного и регулирующего клапанов.
§ В турбинах насыщенного пара, где из-за малого тешюперепада турбины #о потери давления в клапанах особенно ощутимы, объединенная конструкция стопорного и регулирующего кЛапапов нашла широкое распространение.
§ В этих же турбинах в качестве стопорных (перед турбиной) и отсечных устройств (после сепарато-ра-промперегревателя перед ЦНД) используются и поворотные заслонки, в которых при полностью открытом положении (рис. 5.21, а) давление пара перед и за ними практически одинаково.
§ Примерами использования таких заслонок являются конструкция блока стопорного и регулирующего клапанов турбины насыщенного пара К-1000-5,9 ЛМЗ (рис. 5.21 б) и заслонка, применяемая перед ЦНД турбин К-220-4,4 ХТЗ (рис. 5.21, а). Часто используется чашечная конструкция регулирующих клапанов (рис. 4.22, а).
§ МЭИ разработана конструкция клапана с перфорированной поверхностью (рис. 5.22, б). За счет перфорации, т. е. большого числа отверстий на поверхности клапана, течение в клапанной системе стабилизируется, потери давления сокращаются, надежность клапана и его штока повышается.
§ При лроектировании турбины в лабораториях проводятся испытания клапанов, в результате которых отрабатывается оптимальная их конструкция, проверяется возможность стабильной (без пульсаций потока) работы и определяются потери, которые учитываются при расчете турбины.
§ Процесс протекания пара в системе клапан — диффузор в //, ^-диаграмме условно можно изобразить следующим образом (рис. 5.23): пусть на входе (точка О) параметры пара
§
§
§
§ Ро и /0(или лг0), а давление рх устанавливается в минимальном сечении, где средняя теоретическая скорость равна
§
§ Пренебрегая потерями от входа в клапан до этого сечения, .можно принять, что точка 1 находится на изоэнтропе. В диффузоре происходит восстановление давления до р0, которое сопровождается потерями энергии, в связи с чем состояние пара на выходе из диффузора определяется не точкой 2, а точкой 2. Если восстановление давления
§
§ , то потери энергии
§ На выходе из
§ состояние пара на входе в сопловую
§ решетку первой ступени отвечает точке О и параметрам р0 =р2 и И0.
§ Полные потери энергии при протекании пара в клапанной системе характеризуются величиной
§
§
§ Однако, принимая во внимание, что относительная скорость
§ невелика и обычно меньше 0,2—0,3, аЕ1алогично (2.14) можно записать
§
§ определяются главным образом конструкцией клапанной системы и составляют обычно ^кл = 0,4-г-0,8.
§ Для предварительных расчетов турбин потери давления в клапанах и перепускных ресиверах принимаются согласно рекомендациям § 6.4.
§ = 20-г-45 кДж/кг и могут в некоторых тур-
§ . Поэтому как частичное
§ восстановление давления в патрубке, так и дополнительные потери давления в нем могут существенно сказаться на экономичности турбины. С другой стороны, ограниченные размеры патрубка при очень больших объемных пропусках пара Скрк, сложность рационального конструирования его требуют особого подхода к проектированию патрубка и оценки его эффективности.
§ При проектировании выходного патрубка исходными являются характеристики последней ступени ЦН Д—скорость потока с2, веерностьступени 1/0 и абсолютная величина высоты лопатки /, а также предельные габариты патрубка и расположение конденсатора.
§ Проектируемый выходной патрубок должен отвечать следующим требованиям:
§ обеспечивать отвод пара в заданном направлении с минимальными потерями энергии;
§ обладать требуемой жесткостью, так как при больших размерах на патрубок действует перепад давления, примерно равный Ар = 0,1 МПа;
§ обеспечивать по возможности равномерное по окружности давление пара за рабочими лопатками последней ступени, поскольку неравномерность этого давления создает дополнительный импульс, действующий на лопатки и увеличивающий в них динамические напряжения;
§ обеспечивать по возможности равномерное поле скоростей на входе в конденсатор;
§ при всех режимах работы, т. е. при различных значениях расхода пара Ск и давления рк, должен сохраняться устойчивый характер течения.
§ В практике энергетического турбостроения применяются несколько вариантов расположения конденсатора относительно турбины и тем самым возможны различные направления потока в патрубке. Наиболее распространенной является конструкция турбины с подвальным конденсатором, представленная схематично на рис. 5.24, а и изображенная на большинстве чертежей в гл. 10. Здесь пар, покидая последнюю ступень, расходится в радиальном и осевом направлениях и затем, поворачивая под прямым углом, направляется в конденсатор, расположенный под турбиной.
§ Кольцевые конденсаторы (рис. 5.24, б) встречаются редко. Осевой патрубок, когда конденсатор располагается по оси турбины (рис. 5.24, г), может использоваться в однопоточных ЦНД, например в турбинах для ПГУ.
§ Боковые конденсаторы, расположенные по бокам турбины, когда поток пара, выходящий из последней ступени, делится пополам и направляется не вниз, а вбок (рис. 5.24, в), нашли распространение в некоторых зарубежных и отечественных турбинах. Пример такой конструкции приведен на рис. 10.29. Боковые конденсаторы использованы в турбинах К-1000-5,9/25-1 ХТЗ. Испытания, проведенные на Южно-Украинской АЭС, показали высокую эффективность бокового выходного патрубка.
§ В патрубках турбин с подвальным и боковым расположением конденсатора происходит не только поворот потока, но и переход от кольцевого входа к прямоугольному или овальному выходу.
§ Следует отметить, что, как правило, патрубки ограничены в своих осевых размерах, так как увеличение осевого габарита патрубка не только увеличивает длину турбины, удорожая всю установку и увеличивая осевые перемещения, но зачастую технически просто нереализуемо из-за технологической
§
§ невозможности выполнить ротор столь большого размера, а также из-за уменьшения жесткости ротора. Определенные трудности в проектировании патрубка связаны с расположением опор для подшипников турбины. Эти опоры должны быть весьма жесткими и поэтому часто устанавливаются на специальных фундаментах. Для облегчения ремонта также должен быть обеспечен доступ к подшипникам.
§ Меридиональное (продольное) сечение типичного патрубка показано па рис. 5.25, а. Корпус патрубка выполнен сварным с горизонтальным разъемом. Нижняя часть патрубка представляет собой прямоугольную коробку, а верхняя имеет наклонную торцевую стенку А В с местным вырезом СДВ, обеспечивающим доступ к подшипнику, который в данной конструкции устанавливается на нижней части патрубка. На выходе из последней ступени с внутренней стороны патрубок ограничен конической втулкой (на рис. 5.25, а показана втулка, образованная двумя коническими поверхностями с углами конусности у1 и у2). Эти ограничивающие поверхности переходят в торцевые стенки патрубка.
§ В данной конструкции патрубка, который является бездиф-фузорным, даже аэродинамическая отработка его стенок не позволяет обеспечить восстановление давления, т. е. давление на выходе из последней ступени р2т будет выше давления на выходе из патрубка рк.
§ . Эффективность такого
§ патрубка обеспечивается главным образом диффузором, расположенным за последней ступенью (рис. 5.25, б). Большое значение имеет увеличение осевого расстояния от последней ступени до торцевых стенок Ь{ и Ь2 и отношение площади выхода из патрубка (входа в конденсатор) к кольцевой площади последней ступени Гвых/С1г. Желательно, чтобы эти размеры были по возможности большими, а именно:
§
§ Для равномерного распределения потока пара в выходном патрубке необходимы промежуточные вставки, которые должны, направляя поток пара, выходящего из последней ступени, поворачивая его в направлении конденсатора, расположенного под турбиной, по возможности равномерно делить его. Кроме того, по бокам турбины для этого потока должно быть достаточно места, чтобы из-за уменьшения проходного сечения не было местного увеличения скорости пара.
§ На рис. 5.25, в показан патрубок, использованный ЛМЗ в турбине К-1000-5,9/50 (см. рис. 10.32). В этом патрубке сразу же за последней ступенью происходи! внезапное увеличение проходной площади и вызванное этим уменьшение скорости
§
§ пара на входе в патрубок. Такая конструкция позволяет избежать существенного снижения эффективности патрубка при больших околозвуковых скоростях на выходе из последней ступени. Дело в том, что эффективность патрубка зависит не только от его геометрических характеристик, но и от условий на входе в патрубок -выходе из последней ступени. Закрутка потока, распределение по радиусу скоростей пара на выходе из ступени и число М, подсчитанное по скорости с2, существенно влияют на протекание пара в выходном патрубке. Если скорость с2а, подсчитанная как средняя по выходной площади, г. е.
§
§ при проектировании последней ступени (см. ниже, § 6.2). В плохо спроектированных патрубках с большой неравномерностью скоростей на выходе из последней ступени и в самом патрубке, даже при относительно умеренных скоростях, сопротивление патрубка настолько велико, что понижение давления в конденсаторе (при том же расходе пара) не приводит к увеличению теплоперепада последней ступени и не может быть полезно использовано в турбине (см. также § 8.10).
§ Характеристикой эффективности патрубка является величина относительных потерь (или восстановления) давления
§
§ При положительной величине ^вос в патрубке происходит восстановление давления, при отрицательной возникают дополнительные потери.
§ Процесс протекания пара в патрубке в Л, ^--диаграмме представлен на рис. 5.26. Все потери отнесены к величине с2/2, т. е. к потерям с выходной скоростью последней ступени Д^в.с- Эта величина является суммой трех слагаемых—: восстановления давления (которое, как в примере на рис. 5.26, а, может быть отрицательным:.рк<р22), потерь в самом патрубке
§
§
§
§ В случае малых скоростей с2 (несжимаемая жидкость)
§
§ вместо выражения (5.11) можно воспользоваться формулой
§
§ —удельный объем и скорость пара на входе в патрубок.
§ . Очевидно, что относительная величина полных потерь
§
§ является достаточно универсальной характеристикой патрубка.
§ , то в патрубке происходит восстановление
§ , то
§ . Из-за сложности процессов, происходящих в патрубке, особенно с учетом эффекта вращения ступени, характеристики патрубка получаются чисто эмпирически в результате лабораторных исследований и опытов на натурных турбинах.
§ *104м2/с2 и меняется очень мало, после преобразований, аналогичных сделанным при выводе формулы (5.9), получаем выражение
§
§ На рис. 5.27 представлены характеристики различных типов патрубков.
§
§
Дата добавления: 2020-04-25; просмотров: 430; Мы поможем в написании вашей работы! |
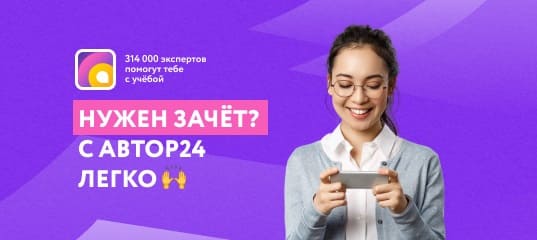
Мы поможем в написании ваших работ!