МЕДИЦИНСКОЕ СТЕКЛО. ОПРЕДЕЛЕНИЕ ОСНОВНЫХ ПОКАЗАТЕЛЕЙ КАЧЕСТВА
Медицинское стекло - твердый раствор, полученный в результате охлаждения расплавленной смеси силикатов, оксидов металлов и солей. Наибольшую термическую и химическую устойчивость имеет кварцевое стекло, получаемое из кварцевого песка, который состоит из 95-98% кремния диоксида. Из такого стекла изготовить и запаять ампулу очень трудно, так как оно имеет высокую температуру плавления (1550-1800°С). Поэтому в его состав для понижения температуры плавления добавляют различные модификаторы: натрия и калия оксиды. Их введение резко уменьшает химическую устойчивость и может привести к получению растворимого или жидкого стекла - натрия или калия силикатов Na2Si03, К2SiO3. Бытовое стекло получают сплавлением кварцевого песка, известняка, натрия карбоната или сульфата, при этом его сложный состав можно представить в виде Na2OCaO · 6SiO2. Применение этого стекла из-за низкой термической и химической стойкости ограничено изготовлением оконных стекол, бутылок и т. д. Повышения химической устойчивости добиваются введением алюминия и бора оксидов. В этом случае образуется качественно новый состав - алюмоборо-силикатное стекло с образованием сложных труднодиссоциируемых комплексов,- Добавление в состав магния оксидов в значительной мере увеличивает термическую устойчивость. Регулирование содержания бора, алюминия и магния оксидов повышает ударную прочность и снижает хрупкость стекла.
|
|
Основным сырьем для получения стекла являются: кварцевый песок (кремния диоксид) – SiO2, нефелин- KNa3 [AlSiO4]4, магнезит (магния карбонат) - MgCO3, доломит (кальция и магния карбонат) - Ca↔Mg(CO3)2. натрия тетраборат - (Na2В4O7), кислота борная - Н3ВО3, известняк (кальция карбонат) – СаСО3, поташ (калия карбонат) - К2СО3, сода кальцинированная (натрия карбонат) - Nа2СО3, натрия сульфат - Na2SO4.
Изменяя состав компонентов и их концентрацию, можно получить стекло с заданными свойствами.
К стеклу для ампул предъявляются следующие требования: прозрачность - для визуального н оптического контроля на отсутствие механических включений; бесцветность - позволяет обнаруживать, кроме механических включений, изменение цвета раствора; легкоплавкость - необходима для запайки ампул (наполненных раствором) при сравнительно невысокой температуре во избежание его нагревания; термическая устойчивость - способность стекла не разрушаться при резких колебаниях температуры, например, выдерживать тепловую стерилизацию; химическая устойчивость, гарантирующая сохранность лекарственного вещества и других компонентов препарата; механическая прочность - для выдерживания нагрузок при обработке ампул в процессе производства, транспортировке и хранении. Последнее требование должно сочетаться с необходимой хрупкостью для легкого вскрытия капилляра ампул.
|
|
В таблице 13.2 приводится состав марок медицинского стекла разного назначения. НС-3 - нейтральное стекло для изготовления ампул и флаконов для растворов веществ, подвергающихся гидролизу, окислению и т.д. (например, растворы солей алкалоидов). НС-1 - нейтральное стекло для ампулирования менее чувствительных к щелочам лекарственных веществ (растворы натрия хлорида, магнезии сульфата, кальция хлорида и др.). СНС-1 - светозащитное нейтральное стекло для изготовления ампул с растворами светочувствительных веществ. АБ-1-щелочное (ампульное безборное) стекло для ампул и флаконов, содержащих устойчивые в масляных растворах вещества, так как в этом случае выщелачивание практически не происходит. ХТ-1 - химически и термически стойкое стекло для изготовления шприцев, бутылок для хранения крови, трансфузионных и инфузионных препаратов. iHTO - медицинское тарное обесцвеченное стекло для изготовления флаконов, банок и предметов ухода за больными. ОС, ОС-1 -оранжевое тарное - для изготовления флаконов и банок. НС-2, НС-2А - нейтральное - для изготовления флаконов для крови, трансфузионных и инфузионных препаратов и аэрозольных баллонов.
|
|
Таблица 13.2. Марки и состав медицинского сиекла
Марки стекла | Состав стекла. % от массы | ||||||||
SiO2 ±0,50 | Al2O3 ±0,20 | B2O3 ±0,25 | СаО± +MgO ±0,30 | Na2O ±0,25 | K2О ±0,20 | Fe2O3 ±0,30 | MnO2, ±0,50 | BaO ±0,20 | |
НС-3 НС-1 СНС-1 НС-2,НС-2A АБ-1 XT XT-1 МТО ОС ОС-1 | 72,80 73,00 67,00 73,00 73,00 74,00 72,00 73,00 73,50 73,00 | 4,50 4,50 4,10 3,5 3,0 5,0 6,0 1,50 1,50 1,30 | 6,00 4,00 5,20 2,50 - 8,00 10,50 - - - | 6,90 8,00 6,30 8,00 9,50 1,20 0,80 10,00 9,50 10,00 | 8,10 8,50 7,50 11,00 13,50 5,00 6,70 15,50 15,50 15,70 | 1,70 2,00 2,00 2,00 1.00 2,80 1,80 - - - | - - 2,90 - - - - - - - | - - 5,0 - - - - - - - | - - - - - 4,00 2,20 - - - |
На поверхности стекла при контакте с растворами в ампулах и флаконах во время хранения и особенно при тепловой стерилизации в зависимости от его марки и значения рН раствора может происходить выщелачивание или растворение. При растворении в раствор переходят компоненты стекла в тех же соотношениях, что и в стекле. Выщелачивание - это преимущественно выход из стекла оксидов щелочных и щелочноземельных металлов, в результате чего на поверхности стекла образуется защитная кремнеземная пленка, которая препятствует продолжению процесса.
|
|
В нейтральных и кислотных растворах при взаимодействии с водой и кислотами щелочные ионы натрия и калия переходят в раствор, вызывая некоторые изменения в величине рН, а на поверхности стекла образуется защитная пленка кислоты кремниевой. По мере взаимодействия толщина пленки увеличивается за счет малой степени диссоциации и слабой реакционной способности этой кислоты, диффузия затрудняется и процесс резко замедляется.
В растворах, имеющих значение рН 3,0, реакция среды почти не изменяется, так как щелочность нейтрализуется дополнительной диссоциацией кислоты.
Растворы, имеющие значение рН 5,0, дают наибольший его сдвиг в ампулах из стекла НС-1: после стерилизации оно увеличивается на 1,2, а при хранении в течение 1 года на 1,65. Это связано с высокой степенью диссоциации кислот при величине рН 5,0.
В щелочных растворах происходит растворение щелочных и кислотных компонентов стекла. Разрывается связь Si - О - Si с образованием натрия и калия силикатов, при этом растворяется поверхностный слой на большую глубину. На поверхности образуется слой плохо растворимых магния и кальция силикатов, но концентрация этих соединений недостаточна для формирования сплошной и прочной пленки. Поэтому она при хранении в ампулах из стекла с недостаточной химической устойчивостью отслаивается, образуя механические включения, что недопустимо в инъекционных растворах. В ампулах из стекла НС-1 растворы, имеющие значение рН 9,0, после стерилизации изменяют его на +1,75, а после годичного хранения - на +0,5 от исходной величины.
Таблица 13.3. Удельная поверхность контакта стекла в зависимости от вместимости ампул
Номинальная вместимость ампулы, мл | Общая внутренняя поверхность в ампуле, см2 | Удельная поверхность контакта, см2/мл | |
1 | 10,6 | 10,6 | |
15 | 48,0 | 3,20 | |
50 | 80,5 | 1,60 |
Важно учитывать удельную поверхность контакта раствора со стеклом.
В таблице 13.3 приведены данные об удельной поверхности контакта стекла в зависимости от вместимости ампул.
Как видно из данных, представленных в табл. 13.3, удельная поверхность контакта раствора со стеклом в мелкоемких ампулах значительно больше. Поэтому их химическая стойкость должна быть более высокой.
Таким образом, сохранность ампулированных растворов зависит от марки стекла, исходного значения рН раствора, времени его контакта со стеклом, температуры, при которой производится стерилизация и хранение, и от вместимости ампул, т. е. удельной поверхности контакта раствора со стеклом.
Определение основных показателей качества. Щелочестойкость. Метод основан на воздействии на образцы стекла площадью 0,10-0,15 дм2 смеси равных объемов 0,5 М раствора натрия карбоната и 0,1 М раствора натрия гидроксида при кипении в течение 3 ч. Перед испытанием и после воздействия щелочных соединений образцы тщательно моют, высушивают при температуре 140°С до постоянной массы и взвешивают.
Щелочность стекла X (мг/дм2) рассчитывают по формуле:
X = (m – m1) / S,
где m - масса образца до обработки, мг; m1 - масса образца после воздействия щелочей, мг; S - площадь поверхности образца, дм2.
Проводят три испытания и по среднеарифметическому значению определяют класс щелочности.
Класс щелочности | Среднеарифметическое значение щелочности, мг/дм2 | |
1 | До 75 | |
2 | Свыше 75 до 175 | |
3 | Свыше 175 |
Водостойкость. Подготавливают 3 пробы из 300 г измельченного до 0,315 мм стекла с массой по 11,0 г, обезжиривают этанолом и ацетоном, сушат при температуре 140°С. Три точные навески по 10,0 г помещают в конические колбы вместимостью 250 мл с 50 мл свежепрокипяченной воды дистиллированной с доведенным рН до исходного (5,5). В две контрольные колбы наливают только свежепрокипяченную воду дистиллированную. Колбы закрывают и автоклавируют 30 мин при температуре 121°С (0,10-0,11 мПа). Затем их охлаждают, добавляют по 2 капли метилового красного и титруют 0,02 моль/дм3 раствором кислоты хлороводородной до перехода окраски раствора от желтого цвета до оранжевого.
Водостойкость стекла X (мл/г) при температуре 121°С вычисляют по формуле:
X = (V1 – V2) / m,
где V1 - объем раствора кислоты хлороводородной, израсходованный на титрование испытуемого раствора, мл; V2 - средний объем раствора кислоты хлороводородной, израсходованной на титрование каждого из двух контрольных опытов, мл; m - масса стекла, г.
Проводят три испытания и по среднеарифметическому определяют класс водостойкости.
Класс водостойкости | Расход 0.02 ч раствора кислйты хлороводородной при титровании, мл/г | |
1 | До 0,10 | |
2 | От 0,10 до 0,85 | |
3 | От 0,85 до 1,50 |
Примечание. 1 мл 0,02 М раствора кислоты хлороводородной эквивалентен 0,62 мг натрия оксида.
Термическая устойчивость. Ампулы в количестве 50 шт. выдерживают при температуре 18°С 30 мин, помещают в кассеты в сушильный шкаф не менее чем на 15 мин при температуре, указанной в ГОСТ. Кассеты выгружают из шкафа быстро за 5 с, погружают в воду с температурой 20 ± 1°С ниже уровня ее поверхности и выдерживают не менее 1 мин. Термостойкими должны быть не менее 98% ампул от взятых на проверку. Ампулы из стекла НС-3 должны оставаться целыми и выдерживать перепад температур, равный 160°С, НС-1 - 130°С, СНС-1 - 150°С и АБ-1 - 110°С. Если результаты не удовлетворительны, то испытание проводят на удвоенном количестве ампул той же партии (т. е. берут 100 штук) и повторный результат считается окончательным.
Химическая стойкость ампул. Для испытания берут разное количество ампул в зависимости от их вместимости: 0,3 мл -150, от 1 до 5 мл - 50, от 5 до 20 мл - 20 и свыше 20 мл - 10 штук. У отобранных ампул проверяют качество отжига, вскрывают капилляры, промывают 2 раза водой дистиллированной, нагретой до температуры 65 ± 5°С, дважды ополаскивают и заполняют водой дистиллированной, имеющей значение рН 6,0 ± 0,2, до номинальной вместимости. Значение рН воды при необходимости доводят до нормы 0,01 н. раствором кислоты хлороводородной или 0,01 н. раствором натрия гидроксида, ампулы запаивают и стерилизуют паром под давлением в строго регламентированном режиме нагрева при 0,10- 0,11 мПа (121 ± 1°С) в течение 30 мин. За 10 мин снижают давление до атмосферного, охлаждают ампулы до температуры 20 ± 5°С не более чем за 60 мин. Проверяют герметичность. Вскрывают капилляры и берут для одного определения на рН-метре 15 мл. Параллельно проводят не менее 3 определений для ампул до 6 мл и 5 измерений для ампул вместимостью от 10 до 50 мл.
До стерилизации паром под давлением измеряют 5-6 раз значения рН исходной воды. Установлены нормы изменения значения рН для ампул: из стекла НС-3 на 0,9; СНС-1 - 1,2; НС-1 - 1,3; АБ-1 на 4,5.
Остаточные напряжения. Они образуются при изготовлении ампул за счет неравномерного нагрева разных участков дрота. Капилляр и донышко ампул нагреваются до расплавления стекла, корпус - незначительно. В местах резкого контраста температур образуются напряжения. Кроме этого, наружная поверхность сильно нагреваемых участков стенки ампулы значительно быстрее охлаждается за счет контакта с окружающим воздухом и быстро затвердевает, а внутренние слои стекла охлаждаются медленнее и дольше находятся в расплавленном состоянии, что также вызывает образование внутренних напряжений. Остаточные напряжения определяют с помощью поля-ризационно-оптического метода по разности хода лучей в образце, связанной с наличием остаточных напряжений, на полярископе-поляриметре ПКС-125, ПКС-250 и на полярископе ПКС-500.
Разность хода лучей Δ (нм) вычисляют по формуле:
Δ = (λ · φ) / 180 = 3φ
где λ - при зеленом светофильтре (540 нм); φ - угол поворота лимба анализатора, град.
Разность хода, отнесенную к 1 см пути луча в стекле, Δ1 млн-1, вычисляют по формуле:
Δ1 = Δ / l
где l - длина пути луча в напряженном стекле, см.
Не допускается остаточное напряжение, содержащее удельную разность хода Δ1 более 8 млн-1.
Светозащитные свойства. Эти свойства испытывают с помощью метода светопропускания в области спектра от 290 до 450 нм с интервалом 20 нм. Из цилиндрической части ампулы вырезают образец, ПрОтирают его и помещают параллельно щели спектрофотометра СФД-2. Максимальный процент светопро-пускания должен составлять 35 при толщине стенки от 0,4 до 0,5 мм; 30% - от 0,5 до 0,6 мм; 27% - от 0,6 до 0,7 мм; 25% - от 0,7 до 0,8 мм и 20% - от 0,8 до 0,9 мм. Допустимые пределы показывают, что для полной светозащиты ампулы необходимо укладывать в картонные упаковки, лучше черного или красного цвета.
ИЗГОТОВЛЕНИЕ АМПУЛ
В нашей стране выпускаются ампулы шприцевого и вакуумного наполнения разных типов с различными обозначениями. Ампулы вакуумного наполнения: В - без пережима, ВП - с пережимом. Ампулы шприцевого наполнения: ШП - с пережимом, ШПР - с пережимом и раструбом, ШВ - с воронкой, ШПВ - с пережимом и воронкой. Ампулы для глицерина обозначаются - Г, для хлорэтила - ХЭ.
Наряду с буквенным обозначением указывается вместимость ампул, марка стекла и номер стандарта. Например, ампула из стекла НС-3 вакуумного наполнения с пережимом вместимостью I мл, изготовленная по ОСТ 64-2-485-85, должна обозначаться следуюпшм образом (ВП-1 НС-3 ОСТ 64-2-485-85).
Для удобства заполнения соответствующим способом ампулы имеют разную форму и диаметр капилляра. Пережим на капилляре препятствует попаданию раствора в верхнюю его часть при запайке и улучшает условия вскрытия ампул перед инъекцией.
Производство ампул осуществляется из стеклянных трубок (дрот медицинский) и включает следующие основные стадии: изготовление дрота, калибровка, мойка и сушка дрота, выделка ампул.
Дрот выпускается на стекольных заводах (ТУ 64-2-5-76 с изменениями) из медицинского стекла двух групп: А и А-1 - для флаконов, пробирок и других изделий. Качество дрота жестко регламентируется по следующим показателям: конусность, разностенность, прямолинейность, овальность, изогнутость, отмываемость загрязнений. Должны отсутствовать механические включения, пузырьки и другие дефекты стекла. Допуски в толщине стенок устанавливаются в зависимости от наружного диаметра. Так, трубки группы А с наружным диаметром от 8,00 до 13,50 мм должны иметь толщину стенок 0,4-0,6 мм, от 13,50 до 16,50 (0,5-0,7 мм), от 16,50 до 21,00 (0,6-0,8 мм), от 21,00 до 23,00 (0,7-0,9 мм) и от 25,00 до 27,00 мм (0,8-1,00 мм).
Изготовление дрота. Дрот производится из жидкой стеклянной массы на специальных линиях АТГ 8-50 путем вытягивания в горизонтальном положении (рис. !3.1), освоено также производство вертикально-горизонтальным способом. Длина трубок должна составлять 1500+50 мм, их отрезка производится механико-термическим методом.
Рис. 13.1. Устройство машины для горизонтального вытягивания дрота.
1 - питатель стекловаренной печи; 2 - корпус; 3 - колеса для перемещения машины по рельсам; 4, 5, 6 - регуляторы;
7-шпиндель машины; 8 - электродвигатель для сращения шпинделя; 9 - гибкий шланг для подачи воздуха внутрь вытягиваемой трубки, Ш - труба из жароупорной стали; 11 - вращающийся керамический мундштук; 12, 13 - струя стекломассы, льющаяся из питателя печи па керамический мундштук; 14 - роликовый конвейер.
Калибровка дрота. Трубки выпускаются разного наружного диаметра от 8,00 до 27,00 мм (через 0,25 мм). Это очень важно для получения из соответствующих трубок ампул, однородных по размерам, заданной вместимости и одинаковых для всей серии. Поэтому их калибруют по наружному диаметру в двух сечениях на расстоянии 350 мм от середины трубки на машине Н.А.Филипина (рис. 13.2). На вертикальной раме машины укреплено пять калибров по 2 каждого размера на расстоянии между ними в 700 мм, щели которых увеличиваются снизу вверх на 0,25 мм. С помощью захватов трубки ступенчато подаются снизу к первым калибрам, если размеры позволяют, трубка проходит их и скатывается в накопитель. Если диаметр трубки больше щели, трубка поднимается выше на следующие калибры с большим зазором. Поизводительность - 130 кг трубок в час.
Сортировка трубок по нескольким показателям осуществляется на более сложных машинах, в которых последовательно происходит отбраковка по длине, наружному диаметру, кривизне и конусности. Весовое устройство набирает в 6 накопителей отсортированные трубки в пучки заданной массы.
Важным показателем качества трубок является толщина стенок, которую определяют косвенно по массе. Для этого трубки предварительно калибруют по наружному диаметру. Затем на специальной машине их сортируют по длине и с помощью взвешивающего устройства распределяют в приемные лотки на 8 групп, каждая из которых имеет соответственно одинаковый наружный диаметр и толщину стенок.
Мойка и сушка дрота. После изготовления и сортировки дрот подвергается мойке. К основным загрязнениям относится стеклянная пыль. Она образуется при резке трубок термическим ударом на стадии их изготовления и во время транспортировки. Для уменьшения загрязнений дрота стеклянной пылью предлагаются другие способы резки, оплавление концов трубок и упаковка их пучков в картон вместо бумаги. При мойке дрота легче освободиться от основной массы загрязнений, чем при ее удалении через узкие капилляры готовых ампул.
Рис. 13.2. Устройство установки для калибровки дрота по наружному диаметру.
1 - направляющие; 2 - накопитель; 3 - калибр; 4 - общая планка; 5 - захваты; 6 - упор; 7 - привод;
8-10 - стеклянные трубки; 11 -этажерка ял я калибровки дрота.
Известно несколько способов мойки. Самым распространенным является камерный. Мариупольский завод технологического оборудования серийно выпускает установку для мойки и сушки трубок камерного типа 129 (рис. 13.3). Работа установки осуществляется следующим образом. 250-350 кг трубок загружается в контейнер в вертикальном положении и он закатывается внутрь камеры с помощью пневмопривода. Двери камеры герметизируются и включается система автоматического управления режимом мойки. Камера с трубками заполняется водой или раствором моющего средства. Жидкость нагревается до кипения. После замачивания проводится подача пара или сжатого воздуха через барботер. Барботаж повышает эффективность мойки за счет создания турбулентных потоков и кавитационных эффектов. Затем жидкость из камеры сливается, в душирующее устройство подается обессоленная вода под давлением. С помощью пневмоцилиндра форсунки душирующего устройства перемещаются в горизонтальной плоскости, обеспечивая интенсивное и равномерное по всему сечению камеры споласкивание трубок. Для сушки внутрь камеры подается горячий фильтрованный воздух.
В зависимости от диаметра трубок и степени их загрязненности режим работы выбирается эмпирически. Так, например, трубки для мелкоемких ампул моются следующим образом: замачивание горячей водопроводной водой при температуре 60°С в течение 1 ч, барботаж - 40 мин, душирование обессоленной водой под давлением в течение 30-60 мин, сушка горячим профильтрованным воздухом с температурой 60°С-15-20 мин. Мойка дрота для крупноемких ампул: душировка водопроводной водой с температурой 40°С в течение 15 мин, замачивание водой, обессоленной и барботаж с помощью острого пара -20 мин, душированне под давлением 392 266 Н/м2 обессоленной водой с температурой 40°С- 15 мин, сушка горячим фильтрованным воздухом при 60°С - 15 мин.
Поточная линия Ленинградского, производственного объединения «Октябрь» обеспечивает автоматическую многостадийную мойку (рис. 13.4). Пучки трубок подаются на загрузочный столик в горизонтальном положении с помощью штангового транспортера с крючковыми захватами передаются последовательно с одной позиции на другую. В начале мойки пучки замачиваются в ванне с кипящей водой. Затем подаются в ванну для турбулентной промывки, которая создается гребными винтами, расположенными с двух торцовых сторон трубок. Следующая ванна предназначена для струйной промывки. Специальное устройство вызывает спиралеобразное движение сопла от центра к периферии. Струя воды с температурой 60 - 70°С под давлением 6 кг/см2 поочередно осуществляет равномерную мойку с двух торцовых поверхностей пучка трубок. Вымытые трубки сушатся в туннеле фильтрованным, нагретым до 75-80°С воздухом.
Недостатками камерного способа мойки является большой расход воды, недостаточная скорость ее потока - порядка 10 см/с (для преодоле-ния сил адгезии необходимо около 100 см/с). Повышение эффективности мойки этим способом добиваются за счет барботажа, создания турбулентных потоков и струйной подачи воды.
Рис. 13.3. Установка для мойки и сушки трубок,
1 - вентилятор; 2 - пневмоцилиндр перемещения душирующего устройства; 3 - пневмоцилиндр перемещения тележки;
4- дозировочный бак; 5 - бак для воды с моющим раствором; 6 - сборник воды после мойки тру бок;
7 - сборник регенерированной обессоленной воды (схема)
Более эффективным и перспективным является способ мойки с помощью ультразвука, который используется в нескольких вариантах. Так, на Харьковском производственном химико-фармацевтическом объединении «Здоровье» установка такой мойки трубок работает следующим образом. Трубки в горизонтальном положении с загрузочного лотка подаются на транспортные диски, подходят к газовым горелкам для оплавления с одной стороны и погружаются в барабан ванны, заполненной водой дистиллированной, нагретой до температуры 50°С. На дне ванны расположен ряд магнитно-стрикционных генераторов ультразвука с частотой 22 кГц и интенсивностью облучения 1,5 Вт/см2. Время озвучивания - около 2 мин. Воздействие ультразвука сочетается со струйной мойкой. В этой же ванне в отверстия трубок из сопел подается струя воды со скоростью 0,18 м/с. Загрязнения удаляются в два отстойника. Вымытые трубки сушатся воздухом при температуре 270°С в течение 5 мин.
Рис. 13.4. Устройство поточной линии для обработки трубок.
1 - лоток загрузки; 2 - ванна для кипячения трубок; 3 - ванна промывки пучков трубок турбулентным потоком;
4 - привод гребных винтов; 5 - ванна для струйной промывки пучков трубок; 6 - устройство для перемещения сопла струйной промывки; 7 - туннель для сушки трубок; 8 - лоток выгрузки; 9 - транспортная система шагающего движения для перемещения пучков трубок в линии; 10 - захваты для пучков трубок; 11 - пневмоцилнндры вертикального перемещения транспортной системы; 12 - пневмоцилиндры продольного перемещения транспортной системы;
13 - привод конвейера туннеля для сушки трубки.
Контактно-ультразвуковой способ значительно улучшает эффективность мойки, так как к специфическим факторам- воздействия ультразвука: кавитация, давление и ветер добавляется механическая вибрация трубок с высокой частотой. В установке, работающей по этому принципу, трубки по одной подаются на транспортирующую цепь и плотно подводятся к вибрирующей поверхности магнитно-стрикционных излучателей, расположенных в нижней части ванны с водой.
При этом колебания поверхности излучателей передаются непосредственно моющимся трубкам. Озвучивание ведется в течение 7 с при 20 кГц и интенсивности 1,2 Вт/см2. В верхней части ванны трубки обрабатываются струей профильтрованной воды под давлением 5-6 кГс/см2. Затем трубки собирают в пучки, подвергают сушке в отдельных воздушных сушилках, обертываются с торцовых сторон плотной бумагой и оставляются в специальных камерах для передачи на стеклодувный участок.
Рис. 13.5. Принцип работы полуавтомата для выделки ампул.
1 - верхний патрон; 2 - горелка; 3 - ограничительный упор; 4 - нижний патрон; 5 - ролик; 6 - копир;
7 - горелка с острым пламенем; 8 -- стеклянная трубка; 9 - готовая ампула.
Качество мойки проверяется визуально путем осмотра внутренней поверхности при освещении пучка трубок с противоположной стороны. При этом поверхность должна быть ровная без заметных механических включений.
Выделка ампул. В зависимости от назначения, способа наполнения и свойств ампулируемых препаратов (растворы, вязкие жидкости, порошки) ампулы выпускают вместимостью от 0,3 до 50 мл. Они имеют разную форму и диаметр капилляра.
Все типы ампул изготавливаются на роторных стеклоформующих автоматах. На отечественных заводах широко применяют автоматы ИО-8 «Тунгсрам» (Венгерская республика). На рис. 13.5 представлена схема получения ампул на автоматах этого типа. На роторе вращается 16 пар верхних и нижних патронов. Трубки загружаются в накопительные барабаны, предназначенные для каждой пары патронов, и проходят 6 позиций:
1) трубки подаются из накопительного барабана внутрь патрона. С помощью ограничительного упора устанавливается их длина. Верхний патрон сжимает трубку, оставляя ее на постоянной высоте на всех позициях;
2) к вращающейся трубке подходят горелки с широким пламенем и нагревают их до размягчения стекла. В это же время нижний патрон, двигаясь по копиру, поднимается вверх и зажимает нижнюю часть трубки;
3) нижний патрон, продолжая движение по копиру, опускается вниз и размягченное стекло трубки вытягивается в капилляр;
4) к верхней части капилляра подходит горелка с острым пламенем. На этой позиции происходит отрезка капилляра;
5) одновременно с отрезкой капилляра происходит запайка донышка следующей ампулы;
6) нижний патрон освобождает зажимы и полученная ампула опускается на наклонный лоток. Трубка с запаянным донышком подходит к ограничительному упору 1-й позиции и цикл работы автомата повторяется.
Недостатком такого способа изготовления ампул является образование внутренних напряжений. Опасность использования таких ампул связана с тем, что при тепловой стерилизации в местах наибольших внутренних напряжений могут образоваться микротрещины, обнаружить которые обычно применяемыми методами контроля невозможно. Поэтому после изготовления происходит снятие напряжений с помощью отжига ампул в специальных печах.
Нежелательным свойством ампул, полученных этим способом, является также то, что при изготовлении они герметически запаиваются в момент, когда внутри амп\'лы находится нагретый воздух. После охлаждения ампул до комнатной температуры внутри них образуется вакуум. При вскрытии капилляра в месте излома образующаяся стеклянная пыль засасывается вакуумом внутрь ампулы, удаление которой является сложным и трудоемким процессом.
Для уменьшения этого явления на Московском химико-фармацевтическом заводе № 1 предложена приставка к автомату, которая располагается в непосредственной близости от лотка в позиции 6. Ампула, еще находящаяся в нагретом состоянии после падения в лоток, тотчас подается» на приставку к автомату и вскрывается. Для этого на капилляре ампулы делается круговая насечка с помощью алмазного диска, на месте которой он отламывается под действием двух пружин. Это снижает температуру воздуха в ампуле и вакуум при запаивании не образуется. Количество стеклянной пыли внутри ампулы резко уменьшается.
В последнее время используется несколько вариантов работы роторных стеклоформующих автоматов, которые при сохранении общей принципиальной схемы позволяют получать безвакуумные ампулы.
Так, в одном варианте на позиции 6 (см. рис. 13.5) в момент отрезки капилляра корпус ампулы нагревается специальной дополнительной горелкой. При этом воздух внутри ее, нагреваясь, расширяется, возникает его избыточное давление и в месте отпайки, где стекло находится в расплавленном состоянии, из ампулы прорывается воздух, оставляя в этом месте небольшое отверстие. Наличие отверстия приводит к тому, что при дальнейшем охлаждении вакуум внутри ампулы не образуется.
Другой вариант основан на том, что в позиции 6 при отпайке (см рис. 13.5) нижний патрон освобождает зажимы и под действие-.- силы тяжести ампулы в месте отпайки вытягивается очень тонкий капилляр, который при одновременном падении и вращении ампулы отламывается. Герметичность внутри ампулы за счет этого капилляра нарушается и они получаются безвакуумными.
На химико-фармацевтических заводах применяются роторные стеклоформующие автоматы, позволяющие за один оборот ротора получить две безвакуумных ампулы. Общий принцип работы авюмата, описанный выше, сохраняется. Различие состоит в том, что участок обогрева оттяжными горелками с широким пламенем значительно больше, чем у автоматов, выпускающих за цикл одну ампулу, кроме того, с помощью специального устройства капилляр в средней его части отрезается в нагретом состоянии, поэтому получаются безвакуумные ампулы.
Ампулы с пережимом производят на таких же автоматах, оснащенных специальным устройством с роликами.
В зависимости от марки стекла, диаметра и толщины стенок трубки выбирается режим работы горелок, скорость вращения ротора и др. Оптимальная температура лежит в пределах 1250-1350°С, что достигается подачей в горелки смеси природного газа, воздуха и кислорода в определенном соотношении. Нагрев до более высоких температур и увеличение его времени понижают химическую устойчивость и повышают остаточные напряжения в ампулах.
Дата добавления: 2020-04-25; просмотров: 232; Мы поможем в написании вашей работы! |
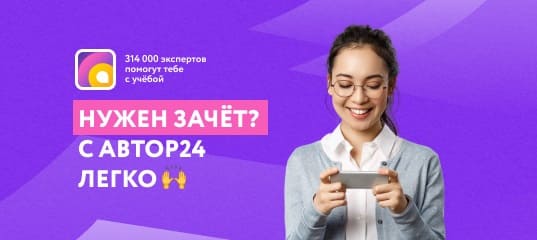
Мы поможем в написании ваших работ!