ЭЛЕМЕНТЫ РЕЖУЩЕЙ ЧАСТИ СВЕРЛА
Как и; резец, сверло имеет передний; и задний углы. Перед-
ний у г о л -угол между касательной к передней поверхности.
в рассматриваемой точке режущей кромки и нормалью в той же точке
к поверхности вращения режущей кромки вокруг оси сверла. Перед-
ний угол рассматривается в плоскости, перпендикулярной к режущей
кромке (плоскость ББ, рис. 174). В каждой точке режущей кромки
передний угол является величиной переменной. Он может быть опре-
делен (без учета ширины перемычки) по формуле
где r х — радиус окружности, на которой расположена рассматри-
ваемая точка;
R — радиус сверла;
- угол наклона винтовой канавки;
- половина угла при вершине сверла.
205
|
Наибольшее значение угол имеет на периферии сверла, где
в плоскости, параллельной оси сверла (плоскость АА), он равен
углу наклона винтовой канавки со. Наименьшее значение угол
имеет у вершины сверла. На поперечной кромке угол у имеет отри-
цательное значение, что создает угол резания больше 90°, а следо-
вательно, и тяжелые условия работы. Такое резкое изменение перед-
него угла вдоль всей длины режущей кромки является большим недо-
статком сверла, так как это вызывает более сложные условия образо-
вания стружки. На периферии сверла, где наибольшая скорость
резания и наибольшее тепловыделение, необходимо было бы иметь
и наибольшее тело зуба сверла. Большой же передний угол умень-
шает угол заострения, что приводит к более быстрому нагреву этой
части сверла, а следовательно, и к наибольшему износу.
|
|
Изменение переднего угла сверла вдоль всей длины режущей кромки можно
видеть из графического построения (рис. 175). Винтовая линия при развертывании
на плоскость представляет собой гипотенузу прямоугольного треугольника, одним
катетом которого является шаг винтовой канавки, а другим — длина окружности
того диаметра, на котором образована винтовая линия. Так как шаг винтовой
канавки одинаков в любом осевом сечении, то, рассматривая винтовую канавку
на цилиндре диаметром D1 < D , видим, что угол < , а так как в осевом
сечении передний угол равен углу наклона винтовой канавки, то и < ,
т. е. по мере приближения точки режущей кромки к оси сверла передний угол
уменьшается.
Задний угол — угол между касательной к задней по-
верхности в рассматриваемой точке режущей кромки и касательной
в той же точке к окружности ее вращения вокруг оси сверла. Этот
угол принято рассматривать в плоскости А А, направленной по каса-
тельной к цилиндрической поверхности (см. рис. 174), на которой
лежит рассматриваемая точка режущей кромки. Ось такой цилин-
дрической поверхности совпадает с осью сверла. Для точки, находя-
щейся на периферии сверла, задний угол в нормальной плоскости ББ
может быть определен по следующей формуле:
|
|
tgн,-< = tg sin .
Действительное значение заднего угла во время работы иное по
отношению к тому углу, который мы получили при заточке и изме-
рили в статическом состоянии. Это объясняется тем, что сверло во
время работы не только вращается, но и перемещается вдоль оси.
Траекторией движения точки будет не окружность (как это прини-
мают при измерении угла), а некоторая винтовая линия, шаг которой,
равен подаче сверла в миллиметрах за один его оборот. Таким обра-
зом, поверхность резания, образуемая всей режущей кромкой, пред-
ставляет собой винтовую поверхность (рис. 176), касательная к ко-
торой и будет действительной плоскостью резания. Действительный
задний угол в процессе резания р заключен между этой плоскостью
и плоскостью, касательной к задней поверхности сверла (рис. 177).
206
207
|
|
Он меньше угла, измеренного в статическом состоянии, на некоторую |
Чем меньше диаметр окружности, на которой находится рассматри-
ваемая точка режущей кромки, и чем больше подача s, тем больше
|
|
|
угол и. и меньше действительный задний
угол р .
Действительный же передний угол в
процессе резания р соответственно будет
больше угла у, измеренного после заточки
в статическом состоянии:
Чтобы обеспечить достаточную вели-
чину заднего угла в процессе резания у то-
чек режущей кромки, близко расположен-
ных к оси сверла, а также для получения
более или менее одинакового угла заостре-
ния зуба вдоль всей длины режущей
кромки задний угол заточки делается на периферии 8—14°, а у сердце-
вины 20—27°.
Кроме переднего и заднего углов, сверло характеризуется углом
наклона винтовой канавки оо, углом наклона поперечной кромки i|j
и углом при вершине 2 . Угол = 18 ¸ 30°, =55°; у сверл из
инструментальных сталей 2 = 116 ¸ 140°.
кромки (так как угол резания здесь больше 90°); в) отсутствие заднего
угла у ленточек сверла, что создает большое трение об обработанную
поверхность.
Таблица 12
Формы заточки сверл
Из рассмотрения геометрических элементов спирального сверла
видно, что оно имеет ряд особенностей, отрицательно влияющих на
протекание процесса стружкообразования при сверлении. К этим
особенностям относятся: а) уменьшение переднего угла в различных
точках режущих кромок но мере приближения рассматриваемой точки
к оси сверла; б) неблагоприятные условия резания у поперечной
|
|
С целью облегчения процесса стружкообразования и повышения
режущих свойств сверла производят двойную заточку сверла и под-
точку перемычки и ленточки. В табл. 12 приведены различные формы
заточки спиральных сверл из инструментальных сталей. Элементы
заточки и подточки спиральных сверл даны на рис. 178.
208
209
При двойной заточке сверла вторая заточка производится
под углом 2 0 = 70°, на ширине В = 2,5 ¸ 15 мм (рис. 178). Такая
заточка повышает стойкость сверла, а при одной и той же стойкости
позволяет увеличить и скорость резания.
Подточка перемычки (сердцевины) производится на
длине l =3¸ 15 мм. От такой подточки уменьшаются длина попе-
речной кромки (размер А = 1,5 ¸7,5 мм, см. рис. 178) и величина
угла резания в точках режущих кромок, расположенных вблизи пере-
мычки сверла.
Для уменьшения трения ленточек об обработанную поверхность
(о стенки отверстия) производится подточка ленточек под
углом =6¸ 8° на длине l 1 = 1,5 ¸ 4 мм (форма ДПЛ), что при-
водит к повышению стойкости сверла.
У сверл, заточенных по методу В. И. Жирова (см. форму ДП-2,
табл. 12, рис. 179), наряду с двойной заточкой и подточкой попереч-
ной кромки (под углом =25¸30°) производится прорезка пере-
210
мычки (ширина а = 1 ¸ 6 мм; угол = 50¸56°; передний угол
у дополнительной режущей кромки = 3¸5°). Такая комбиниро-
ванная заточка облегчает врезание сверла (осевая сила уменьшается
по отношению к обычному сверлу в 3—4 раза), что дает возможность
, повысить подачу в 2—3 раза и соответственно уменьшить машинное
время.
При сверлении на большую глубину сверлом большого диаметра
образуется широкая, трудно отводимая по канавкам стружка, что
|
увеличивает трение и затрудняет
подвод охлажденной жидкости
к месту резания. Во избежание
этого у сверл делают специальные
стружкоразделительные канавки,
которые могут быть на передней
|
ВидА
поверхности сверла (рис. 180, а) и на задней (рис. 180, б). Глубина
канавки примерно равна 0,05 D , ширина примерно 0,07 D . Такие
канавки разделяют широкую стружку на несколько узких, облегчают
условия работы сверлом, снижая.силы, действующие при резании, и
тепловыделение.
Во избежание разбивки отверстия и увода сверла в сторону (от
оси отверстия) оно должно иметь после заточки режущие кромки оди-
наковой длины и симметрично расположенные.
Сверла, оснащенные пластинками тверды х сплавов (см.
рис. 193), обладают высокой стойкостью, обеспечивают более высо-
кую производительность, повышают качество обработанной поверх-
ности и в результате снижают стоимость обработки. Особенно эффек-
тивно применение сверл с пластинками твердых сплавов при сверлении
211
чугунов и рассверливании чутунов и сталей. Твердосплавные сверла
имеют передний угол = О ¸ 7°, задний угол — 8 ¸16°, угол
2 =118ч- 150е', yf — 0" на фаске f — 0,5 ¸ 1,5 мм. При обра-
ботке сталей рекомендуется применять твердый сплав марки Т15К6,
при обработке чугунов — ВК8.
У сверл с пластинками твердых сплавов, как и у сверл, изготов-
ленных из быстрорежущей стали, производится подточка перемычки
(рис. 181) и двойная заточка под углом 2, = 70°, В = 0,2 D .
Большое значение для успешной работы сверла с пластинкой твер-
дого сплава имеет симметричность заточки обеих режущих кромок.
Биение по режущим кромкам желательно иметь не более 0,02 мм,
а по ленточкам не более 0,03 мм.
§ 2. ЭЛЕМЕНТЫ РЕЖИМА РЕЗАНИЯ И СРЕЗА
ПРИ СВЕРЛЕНИИ
Скорость резания для различных точек режущей кромки
сверла различна: на периферии сверла скорость резания наибольшая,
а по мере приближения к оси сверла она уменьшается и в центре равна
нулю. В расчет принимается наибольшая скорость резания на пери-
ферии:
где D — диаметр сверла в мм\
п - число оборотов сверла в минуту.
Подача (s мм/об.) — величина перемещения сверла вдоль оси
за один его оборот (или за один оборот заготовки, если она вращается,
а сверло только перемещается). У сверла две главные режущие кромки;
подача, приходящаяся на каждую из них,
Как и при токарной обработке, подачу можно измерять и в мил-
лиметрах за 1 мин (минутная подача):
Толщина среза а (рис. 182, а) измеряется в направлении,
перпендикулярном к режущей кромке:
III и р и н а среза b измеряется вдоль режущей кромки и равна
ее длине:
212
П л о щ а д ь п о п е р е ч н о г о с е ч е н и я с р е з а, приходя-
щаяся на одну режущую кромку,
О б in а я п л о щ а д ь поперечного сечения среза, приходя-
щаяся на обе режущие кромки.
Под г л у б и н о й резания при сверлении (которая обычно
в расчетах не фигурирует) подразумевается расстояние от обработан-
ной поверхности до оси сверла, т. е.
При рассверливании (рис, 182, б) глубина резания
где D •-- диаметр сверла в мм;
D0 — диаметр ранее просверленного отверстия в мм.
Рис. 182. Элементы резания:
а — при сверлении: б --■ при рассверливании
|
Ill и р и н асре з а при рассверливании |
Т о л щ и н а среза при рассверливании опреде-
ляется так же, как и при сверлении в сплошном материале:
213
Площадь поперечного сечения среза при рас-
сверливании, приходящаяся на одну режущую кромку,
2 sin ф
Общая площадь поперечного сечения среза при рассвер-
ливании
■D0)s
При рассверливании скорость резания пере-
менна вдоль всей длини активной части режущей кромки и изме-
няется от
|
Машинное время при сверлении и рассверливании |
|
Во всех расчетах принимается наибольшее значение скорости реза-
ния, соответствующее наружному диаметру сверла D .
где L — полный путь, проходимый сверлом в направлении подачи,
в мм;
I — глубина сверления в мм (глубина отверстия, рис. 183);
— величина перебега (1—2 мм);
п — число оборотов сверла в минуту;
s — подача в мм/об;
у — величина врезания в мм; у— ctgcp (из треугольника
OMN ; рис. 183, а); для обычных сверл одинарной заточки
при угле 2 = 116 ¸118° у » 0,3 D ; для сверл с двойной
заточкой у » 0,4 D ; при рассверливании у = t ctg (из тре
угольника O MN ; рис. 183, в).
214
§ 3. ПРОЦЕСС ОБРАЗОВАНИЯ СТРУЖКИ
ПРИ СВЕРЛЕНИИ
Сверло — более сложный инструмент, чем резец. В более слож-
ных условиях протекает и процесс резания сверлом: затруднен отвод
стружки и подвод охлаждающей жидкости; наблюдается значительное
трение стружки о поверхность канавок сверла и самого сверла об
обработанную поверхность; вдоль режущей кромки возникает резкий
перепад скорости резания (от vmaх до нуля), так что в отдельных точках
режущей кромки срезаемый слой деформируется и срезается с разной
скоростью; различная деформация получается и в связи с переменным
углом у вдоль всей режущей кромки спирального сверла, а потому
по мере приближения точки режущей кромки к периферии сверла
деформация (усадка) уменьшается (вследствие увеличения v и у).
Все это вызывает более тяжелые, по сравнению с точением, условия
процесса стружкообразования при сверлении, большие деформации
срезаемого слоя, увеличенное тепловыделение и повышенный нагрев
сверла. Если рассматривать процесс стружкообразования на неболь-
шом участке режущей кромки, то он подчиняется тем же закономер-
ностям и сопровождается теми же явлениями, что и при точении;
упругие и пластические деформации, тепловыделение, нарсстообразе-
вание, упрочнение, износ инструмента здесь возникают по тем же
причинам.
Как и при точении, на температуру резания при сверлении ско-
рость резания оказывает большее влияние, чем подача; температура
резания возрастает с увеличением глубины (длины) сверления, но
уменьшается с увеличением диаметра сверла (из-за усиления тепло-
отвода вследствие большей массы сверла и большей поверхности со-
прикосновения с заготовкой, а также вследствие облегчения подвода
охлаждающей жидкости и отвода стружки по канавкам большего
сечения).
При сверлении сталей образуется в основном сливная стружка,
а при обработке чугунов — стружка надлома.
§ 4. СИЛЫ, ДЕЙСТВУЮЩИЕ НА СВЕРЛО
На все элементы еверла при резании действуют некоторые силы.
Разложим равнодействующие сил сопротивления в каждой точке
режущей кромки на силы в трех взаимно перпендикулярных направ-
лениях: Р z , Рв и Рг (рис. 184). Горизонтальные силы Рс, действующие
на обеих режущих кромках, можно считать * взаимно уравновешен-
ными. Силы Р«, направленные вверх, препятствуют проникновению
сверла в глубину заготовки. В этом же направлении действует и
сила Рх на поперечной кромке. Кроме того, продвижению сверла
* Принимая вследствие малого значения толщины перемычки сверла действие
сил вдоль одной прямой.
215
препятствуют силы трения на ленточках сверла (в результате трения
об обработанную поверхность отверстия) и силы трения от сходящей
стружки Рт.
Для проникновения сверла в обрабатываемую заготовку к сверлу
от станка должна быть приложена такая сила Р', которая могла бы
|
преодолеть сумму сил сопротивления, действующих
вдоль оси сверла:
Р'> (2Рв+Р1+Рт).
Суммарная сила от указанных сил сопротивле-
ния в осевом направлении сверла называется
осевой силой Р (или усилением подачи).
Измерения показывают, что силы сопротивле-
ния проникновению сверла Р„, возникающие на
режущих кромках, составляют около 40% общего
сопротивления (или силы Р); силы сопротивления,
возникающие на поперечной кромке (P1), состав-
ляют 57% и силы от трения Рт — около 3%.
Силы, препятствующие продвижению сверла в
материал, преодолеваются механизмом подачи свер-
лильного станка, который и рассчитывается по
максимальной осевой силе Р.
При эксплуатации станка с заданными усло-
виями сверления необходимо, чтобы сумма сил
сопротивления, действующих вдоль оси сверла,
или осевая сила Р, была меньше или, в крайнем
случае, равна наибольшему усилию Рmах, допу-
скаемому механизмом подачи станка (во избежание
поломки слабого звена механизма подачи), т. е.
Наибольшее усилие Рmах рассчитывается при конструиро-
Суммарный момент от сил сопротивления реза-
н и ю складывается из момента от сил Р2, момента от сил скобления
и трения на поперечной кромке Мпк, момента от сил трения на лен-
точках Мл и момента от сил трения стружки о сверло и обработанную
поверхность Мс, т. е.
М=Мср+Мп.к+Мл + Мс
Измерения показывают, что 80% общего момента сопротивления
резанию приходится на долю режущих кромок, 8% — на поперечную
кромку и 12% — на трение стружки о сверло и стенки отверстия и
сверла своими ленточками об обработанную поверхность (Мл + Мс).
Для того чтобы на данном станке могло быть осуществлено реза-
ние, кроме указанного выше условия проникновения сверла необ-
216
ходимо, чтобы суммарный момент сопротивления резанию был пре-
одолен вращающим (крутящим) моментом станка, т.е. МвріМ.
Вращающий момент станка подсчитывается по формуле
где N ш n — мощность на шпинделе в квт;
п — число оборотов шпинделя (сверла) в минуту.
В свою очередь,
где Ncm — мощность электродвигателя станка;
— к. п. д. станка.
Суммарный момент сопротивления резанию М должен быть меньше
или, в крайнем случае, раиен не только вращающему моменту Мвр,
развиваемому электродвигателем станка на данной ступени числа
оборотов шпинделя, но и меньше, или, в крайнем случае, равен макси-
мальному крутящему моменту М'вр, допускаемому слабым звеном
механизма главного движения станка (во избежание поломки его),
т. е. М £ М'вр.
Если момент Мвр легко подсчитывается по приведенной выше
формуле, то момент М'вр рассчитывается при конструировании станка
и приводится обычно в его паспорте.
По силе Р и моменту М можно рассчитать необходимую (потреб-
ную) мощность электродвигателя сверлильного станка.
Мощность, затрачиваемая на резание, будет
складываться из мощности, затрачиваемой на вращение, и мощности,
затрачиваемой на движение подачи, т. е.
Мощность, затрачиваемая на вращение,
где М — момент от сил сопротивления резанию в кГмм\
п — число оборотов сверла в минуту.
Мощность, затрачиваемая на подачу сверла,
где Р — осевая сила в кГ *.
Расчеты показывают, что, как и при токарной обработке, мощ-
ность, затрачиваемая на движение подачи, мала (0,5—1,5% мощ-
* По системе СИ 1 кГ--=9,81 н.
217
ности, затрачиваемой на вращение сверла) и ею можно пренебречь.
Поэтому
или
Зная мощность, затрачиваемую на резание, легко подсчитать и
необходимую (потребную) мощность электродвигателя
станка, которая обеспечит проведение процесса резания при сверле-
нии при определенных условиях работы:
Сравнивая NM с действительной мощностью электродвигателя
станка Ncm , легко проверить возможность осуществления процесса
сверления на заданном станке при заданных условиях сверления
(резания), для чего должно быть соблюдено условие NM £S Nст *.
Однако, как и при проверке возможности осуществления процесса
сверления на заданном станке по моменту, необходимо учитывать
не только мощность электродвигателя станка, но и мощность на
шпинделе по слабому звену механизма главного движения станка N 'ш n .
Во избежание поломки этого слабого звена должно быть соблюдено
условие Nрез £ N 'ш n .
В практике наиболее слабое звено механизма главного движения
станка проверяют1 по моменту или по мощности в зависимости от
того, какие данные приводятся в паспорте станка.
Знание осевой силы и момента сопротивления резанию, возни-
кающих при сверлении, необходимо как для расчета и конструиро-
вания станков, сверл и приспособлений, так и для правильного исполь-
зования их в производстве.
ВЛИЯНИЕ РАЗЛИЧНЫХ ФАКТОРОВ
Дата добавления: 2020-04-25; просмотров: 187; Мы поможем в написании вашей работы! |
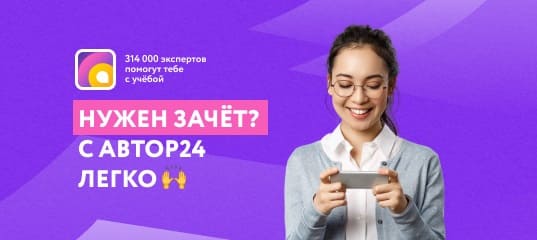
Мы поможем в написании ваших работ!