Глава ОБРАБОТКА МЕТАЛЛОВ
XIII СТРОГАНИЕМ
§ 1. ПРОЦЕСС СТРОГАНИЯ И РЕЖУЩИЙ
ИНСТРУМЕНТ
Процесс строгания, применяемый для обработки плоскостей и
фасонных поверхностей, осуществляется на строгальных станках
с прямолинейным главным (рабочим) движением. Строгальные станки
делятся на поперечно- и продольно-строгальные. У продольно-стро-
гальных станков главное движение имеет стол с закрепленной на
нем заготовкой, а движение подачи — инструмент (резец). У попе-
речно-строгальных станков (рис. 162), наоборот, главное движение
имеет резец, закрепленный в ползуне станка, а движение подачи —
стол, на котором крепится заготовка. Размерность подачи — м м/дв. ход.
У строгальных станков имеется рабочий ход, во время которого
происходит процесс резания, и холостой (обратный) ход, когда заго-
товка пли резец перемещаются в обратном направлении. При холо-
стом ходе резания не происходит, а в конце холостого хода начи-
нается движение подачи, т. е. относительное перемещение резца
и заготовки, необходимое для снятия следующего слоя металла при
рабочем ходе.
Для уменьшения времени на обработку скорость холостого хода
у строгальных станков больше скорости рабочего хода.
К строгальным станкам относятся и долбежные станки, у которых
возвратно-поступательное движение осуществляется не в горизон-
тальной, а в вертикальной плоскости (рис. 163). У этих станков ско-
рости рабочего и холостого ходов равны.
|
|
В качестве режущего инструмента при строгании применяют
строгальные резцы, а при долблении — долбежные.
На рис. 164 показан левый проходной строгальный резец с пла-
стинкой твердого сплава, предназначенный для обработки горизон-
тальных поверхностей, на рис. 165 — левый подрезной, предназна-
ченный для обработки вертикальных поверхностей, а на рис. 166 —
1 94
отрезной (прорезной) изогнутый резец, предназначенный для отрезки
или прорезки пазов. Форма передней поверхности строгальных резцов
та же, что и у токарных резцов.
В связи с тем, что строгальный резец вступает в работу каждый
раз с ударом, у строгальных резцов, изготовленных из быстрорежущей
стали, передний угол у делается на 5—10° меньше (по сравнению
с токарными резцами); угол на фаске yf = + 5°. У резцов, осна-
щенных пластинками твердых сплавов и изготовленных по форме I
Задний угол у проходных строгальных резцов из быстрорежу-
щей стали равен 6—8°; у проходных резцов с твердосплавными пла-
стинками — от 10 до 16°. У подрезных, отрезных и фасонных резцов
угол = 12 ¸ 14°. Главный угол в плане у проходных строгаль-
ных резцов равен 30—75°.
|
|
При обработке вертикальной плоскости у подрезного резца угол
j = 900 применяется в случае необходимости получения уступа,
составляющего с вертикальной плоскостью угол 90°. При обработке
же вертикальной плоскости на проход, чтобы не прострогать поверх-
ность стола, угол может быть и больше 90° (см. рис. 165). Однако
если есть возможность обработать вертикальную плоскость на про-
ход, не испортив стола станка1 то лучше использовать проходной
отогнутый резец с углом < 90°, так как чем меньше угол , тем
больше стойкость резца. У отрезных резцов = 80 ¸- 90°.
1 Для этого иногда применяют подкладки иод заготовку.
195
|
Вспомогательный угол в плане 1 у проходных и подрезных рез-
цов делается равным 10—30°, у отрезных и прорезных 2 или 3°.
Для сохранения вершины и уменьшения разрушающего дей-
ствия удара, а также для более плавного входа резца в заготовку
и выхода из нее угол наклона главной режущей кромки у проход-
ных и подрезных строгальных резцов делается обязательно положи-
тельным (до +20°). С той же целью у этих резцов радиус закругления
при вершине r < 1 мм не рекомендуется (1—2 мм). У отрезных (про-
резных) резцов r =0,5 ¸ 2,5 мм.
|
|
Угол врезания пластинки принят +12°.
Чтобы уменьшить заклинивание резца при резании, стержень
строгальных резцов рекомендуется делать изогнутым 1. При прямом
стержне (рис. 167, а) под влиянием сил, действующих на резец, изгиб
стержня вокруг точки О вызовет внедрение вершины резца в обрабо-
танную поверхность. При изогнутом стержне это внедрение будет
меньше и в случае, если вершина резца будет находиться в плоскости
опоры (рис. 167, б), его не будет совсем, так как радиус окружности R ,
по которой будет перемещаться вершина резца, будет равен вылету l .
При строгании на крупных строгальных станках успешно при-
меняют строгальные сборные резцы (рис. 168), способные выдер-
живать нагрузки при резании чугуна с глубиной резания до 30 мм
и подачей до 2—2,5 мм/дв.ход. Применение таких резцов понижает
затраты на их изготовление на 40—50% и повышает производитель-
ность на 20—30% (по отношению к обычным стержневым строгаль-
ным резцам) [84].
Для окончательной (чистовой) обработки применяют чистовые
резцы, имеющие большой радиус закругления или большую длину
1 Размеры изогнутых быстрорежущих строгальных резцов приведены в ГОСТе
10045—62, на твердосплавные резцы — в ГОСТе 9796 — 61.
|
|
196
197
(до 40 мм и более) режущей кромки с углом = 0 (так называемые
широкие чистовые или лопаточные резцы).
Чистовое строгание — высокопроизводительный процесс оконча-
тельной обработки плоскостей, заменяющий при обработке чугуна
такую трудоемкую операцию, как шабрение [89]. При этом тяжелый
ручной труд заменяется машинным и производительность повышается
до 10 раз. В отдельных случаях чистовое строгание заменяет и шлифо-
вание, так как при работе на станке широкими резцами можно полу-
чить высокую точность и чистоту обработанной поверхности (Ñ7 — при
подаче до 20.мм/дв. ход, глубине резания до 0,1 мм и соответствующей
смазывающе-охлаждающей жидкости).
На рис. 169 показан резец, оснащенный пластинкой твердого
сплава ВК.8, успешно применяемый при чистовом строгании чугуна.
Передняя и задняя поверхности тщательно доведены (Ñ 10); режущая
кромка острая и прямолинейная, что существенно влияет на повыше-
ние качества обработанной поверхности. Для обеспечения постепен-
ного входа и выхода резца по всей ширине среза, а также для умень-
шения разрушающего действия ударной нагрузки на вершину резец
имеет угол наклона режущей кромки = + 15°. На длине 10 мм
режущая кромка имеет угол = 1°, а на остальной части режущей
кромки угол = 0. Длина части режущей кромки с углом = 0
должна быть не менее 1,5 s; по ней резец устанавливается в резцедер-
жателе (но шлифованной плитке, положенной на предварительно
простроганную поверхность). Обработку таким резцом рекомендуется
вести не менее, чем с двух проходов: предварительного с глубиной
резания 0,5—0,8 мм, окончательного с глубиной резания не более
0,08 мм. При строгании чугунов для первого прохода рекомендуется
скорость резания 15—20, а для окончательного 4—12 м,/мин. Величина
подачи назначается в зависимости от длины режущей кромки я,,
имеющей угол = 0; s = (0,7 ¸ 0,3) а1. Для повышения качества
обработанной поверхности чугуна и охлаждения режущего инстру-
мента применяют керосин, подавая его небольшой струей на резец.
Хорошие результаты по чистоте обработанной поверхности дают
и широкие резцы, оснащенные пластинками твердых сплавов, с ре-
Ви д В
жущей кромкой, повернутой на угол 60° по отношению к направле-
нию рабочего движения.
При чистовой обработке плоскостей крупногабаритных деталей
применяют и строгальные вращающиеся (чашечные) резцы конструк-
ции ВНИИ (рис. 170).
Чашка 1 из быстрорежущей стали1 с цилиндрическим хвосто-
виком вращается в бронзовой втулке 7, которая запрессована в дер-
жавке 2. Во втулке 7 чашка 1 крепится с помощью шайбы 6, пру-
жины 5'и гайки 3; во избежание отвинчивания гайки в ней сделано
отверстие, в которое вставляется шплинт 4.
Для образования заднего угла ось отверстия в державке имеет
наклон под утлом 3°. Кроме этого наклона резец (державка) развора-
чивается в резцедержателе на угол 5" — 5°30' в плоскости, перпенди-
1 Применяют и твердосплавные чашки из сплава Г5К.Ю.
198
199
кулярнои к направлению главного движения; делается этот разворот
для обеспечения рационального стружкообразования и стружко-
отвода.
Чашечными вращающимися строгальными резцами работают с глу-
биной резания до 11 мм, с подачей до 5 мм/дв. ход, при скорости
резания до 8 м/мин. Стойкость резцов (при износе h 3 = 0,2 ¸ 0,3 мм)
очень высокая (22—24 ч), что дает возможность обрабатывать пло-
скости площадью до 30 м2 без переточки резца. Высокое качество
обработки (плоскостность в пределах 0,03—0,05 мм, чистота Ñ5),
получаемое при работе этими резцами, дает возможность снизить
трудоемкость отделочных работ и в отдельных случаях исключить
шабрение.
Как и при точении, в процессе стружкообразования при строга-
нии имеют место упругие и пластические деформации, трение, тепло-
выделение, упрочнение, наростообразование и износ режущего ин-
струмента. Типы стружек, получаемых при строгании, аналогичны
типам стружек, образующихся при точении. Однако процесс резания
при строгании имеет и некоторые особенности.
При непрерывном точении резец, врезавшись однажды в обраба-
тываемый металл, находится под воздействием стружки вдоль всей
длины обработки. При строгании же резец находится под воздей-
ствием стружки только во время рабочего хода. Во время холостого
хода процесс прерывается; при этом резец не режет, а охлаждается,
что положительно сказывается на его стойкости. Но строгальный
резец каждый раз входит в заготовку с ударом, разрушительная сила
которого возрастает с увеличением скорости резания, площади попе-
речного сечения среза и твердости обрабатываемого металла. Нали-
чие такой ударной нагрузки отрицательно сказывается на прочности
и стойкости резца, что вынуждает делать строгальные резцы более
массивными, жесткими и с более вязкими материалами режущей
части, а также работать на относительно низких скоростях резания.
Работу на высоких скоростях резания затрудняет и сама специ-
фика строгального станка, имеющего возвратно-поступательное дви-.
жение. Большие перемещающиеся массы и большие инерционные силы
вызывают тяжелые условия реверсирования (т. е. переключения с ра-
бочего хода на холостой и обратно), а потому на современных стро-
гальных станках скорости резания не превышают 80 м/мин.
В связи с тем, что подача осуществляется в конце холостого хода,
когда резец не имеет соприкосновения с заготовкой, она не влияет на
передний и задний углы в процессе резания. На эти углы не влияют
также размер заготовки и расстояние вершины резца от его опорной
плоскости.
Процесс резания при строгании производится обычно без охлаж-
дения (за исключением окончательного-—чистового строгания).
§ 2. СИЛЫ, ДЕЙСТВУЮЩИЕ НА РЕЗЕЦ,
СКОРОСТЬ РЕЗАНИЯ И МОЩНОСТЬ ПРИ
СТРОГАНИИ
На силы резания при строгании оказывают влияние те же фак-
торы, что и при точении:
Значения коэффициента СРя z , показателей степеней xz и yz и по-
правочных коэффициентов, входящих в общий коэффициент Кг,
приводятся в справочниках по режимам резания [90].
Скорость резания, допускаемая режущими свойствами
строгальных резцов, подсчитывается по формуле
Значения коэффициентов и показателей степеней см. [90]. Ре-
комендуемая стойкость для всех строгальных резцов 120 мин 167].
В ы с о к о п р о и з в о д и т е л ь н о е строгание резцами,
оснащенными пластинками твердых сплавов, как более произво-
дительный метод находит в металлообрабатывающей промышлен-
ности широкое применение. Однако, как уже было сказано выше,
скорость резания па современных строгальных станках не превы-
шает 80 м/мин, а на станках старых моделей 40—50 м/мин, несмотря
200
201
|
Необходимая (расчетная) мощность электродвигателя станка |
на то, что продольно-строгальные станки, как правило, имеют элек-
тродвигатели большой мощности. Для повышения производитель-
ности и полного использования мощности станка остается другой
фактор — увеличение подачи, т. е. строгание с большими
подачами.
Большие подачи (до 20 мм/дв. ход и более) успешно применяют
при чистовом строгании (с глубиной резания t£0,1 мм) широкими
резцами.
При получистовой обработке стали с подачами до 6 мм/дв. ход
применяют строгальные резцы, имеющие режущую кромку под углом
j1 =0° длиной (1,2 ¸ 1,8) s. Но при работе такими резцами часто
не используется полностью мощность станка, да к тому же при стро-
гании чугуна с относительно большими t и подачами более
1—1,5 мм/дв. ход может происходить скалывание заготовки по краям,
т. е. в местах входа и выхода резца. Учитывая все это, Средневолж-
ский станкостроительный завод предложил строгание, основанное на
применении многорезцовой державки, в которой закрепляются сразу
четыре резца (рис. 171). Конструкция державки позволяет смещать
вершины двух соседних резцов относительно друг друга на величину
подачи s, приходящейся на каждый резец. В результате этого сум-
марная величина подачи за один двойной ход будет 4s и машинное
время сократится соответственно в 4 раза.
Мощность, затрачиваемая на резание при строгании,
202
где т| — коэффициент полезного действия (к. п. д.).
§ 3. НАЗНАЧЕНИЕ ЭЛЕМЕНТОВ РЕЖИМА
РЕЗАНИЯ
Принципы и порядок назначения элементов режима резания при
строгании те же, что и при токарной обработке.
1. Определяют глубину резания в зависимости от припуска
на обработку (см. стр. 145).
2. Выбирают подачу, максимально допустимую по техноло-
гическим требованиям.
|
При черновом строгании чугуна обычными резцами с твердо-
сплавными пластинками (при = 45°) подача равна до 5,5 мм/дв. ход.
В зависимости от чистоты обрабо-
танной поверхности для обычного
резца подачу" можно назначать
такой же, как и при наруж-
ном продольном точении (вместо
мм/об — мм/дв. ход), с последую-
щей корректировкой по станку. При
работе широкими чистовыми рез-
цами подача s = 1 ¸ 20 мм/дв. ход.
При работе специальными сбор-
ными резцами с режущей кромкой
длиной до 150 мм при получисто-
вой обработке подача может быть
до 100 мм/дв. ход [92].
3. После выбора глубины резания и подачи подсчитывают ско-
рость резания, допускаемую режущими свойствами резца.
4. По найденной скорости резания определяют необходимое
число двойных ходов в минуту, которое корректи-
руют по станку, и затем подсчитывают действительную скорость
резания. Скорость резания по станку при строгании подсчитывается
по формуле
где k — число двойных ходов в минуту;
L — длина хода стола (ползуна) в мм;
т — отношение скорости рабочего хода к скорости холостого
хода (дается в паспорте на станок; тср =0,75).
5. Проверяют достаточность мощности электродвигателя станка,
для чего подсчитывают сначала Nрез; при недостаточности мощности
203
|
Раздел СВЕРЛЕНИЕ, ЗЕНКЕРОВАНИЕ, V РАЗВЕРТЫВАНИЕ |
электродвигателя статно, т. е. если Nм >■ Ncm , целесообразнее умень-
шить скорость резания (число двойных ходов), а не подачу. Для
поперечно-строгальных станков с качающейся кулисой проверку
необходимо вести по минимальной силе, развиваемой ползуном в се-
редине длины хода; необходимо, чтобы Р z £ Pmin (см. [331).
6, Подсчитывают м а ш и п и о е в р е м я: ■
где В1 — ширима обработанной поверхности (размер в направлении
подачи) в мм;
В1 — боковое врезание резца в мм (рис, 172); .B1 = /ctg;
В2 — боковой сход резца в мм (2—3 мм);
k — число двойных ходов в минуту;
. s — подача в мм/дв. ход.
7. При тяжелых условиях работы необходимо провести проверку
по прочности резца.
При решении задач по назначению элементов режима резания
при строгании см, [901.
Глава РЕЗАНИЕ МЕТАЛЛОВ СВЕРЛАМИ
XIV
Сверление является одним из самых распространенных методов
получения отверстия. Режущим инструментом здесь служит сверло
(рис. 173), которое дает возможность получать отверстия в сплошном
материале и увеличивать диаметр ранее просверленного отверстия
(рассверливание). Главное движение при сверлении — вращатель-
ное, движение подачи — поступательное. На обычных сверлильных
станках оба эти движения имеет сверло: оно вращается, будучи за-
крепленным в шпинделе станка, и одновременно перемещается в глу-
бину обрабатываемой заготовки, которая неподвижно закреплена на
столе станка.
Режущая часть сверла изготовляется из инструментальных сталей
(Р18, Р9, 9ХС, Р9К5) и из твердых сплавов.
Дата добавления: 2020-04-25; просмотров: 175; Мы поможем в написании вашей работы! |
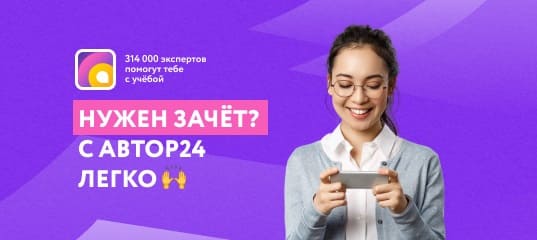
Мы поможем в написании ваших работ!