Измерение координат с помощью трекера.
Трекеры собирают информацию о 3D-координатах, которая может быть с помощью программного обеспечения сопоставлена с геометрическими объектами, такими как точки, сферы или цилиндры. Обычно данные выдаются в местной координатной системе, привязанной к характерным деталям измеряемого объекта. Плоская поверхность объекта, к примеру, может представлять плоскость OXY. В другом варианте местная координатная система может быть привязана к элементам, которым можно поставить в соответствие точки или линии. Роль точек могут исполнять, например, отверстия в измеряемом объекте.
Иногда необходимо переместить трекер в другое место для измерения всех интересующих параметров объекта. Удобный способ сделать это - поместить три или более гнезда для ретрорефлектора на измеряемый объект или рядом с ним. Трекер измеряет координаты ретрорефлекторов в каждом гнезде до и после изменения своего положения. Собранные данные автоматически трансформируются программным обеспечением трекера в положение местной координатной системы.
Ряд аксессуаров расширяют функциональность трекера. Пульт дистанционного управления позволяет оператору производить измерения без перемещения от компьютера к объекту и обратно. Приспособления для измерения деталей определенной формы увеличивают скорость проведения сложных измерений. Температурные сенсоры позволяют компенсировать флуктуации температуры окружающей среды и вызванное ими изменение размеров измеряемых объектов. Инклинометр (уровень) измеряет ориентацию трекера по отношению к гравитационному полю.
|
|
Рисунок 5 – Анализ собираемости БЗ в помещении судна:
1 - зональный блок; 2 - лазерный трекер.
Погрузка
Рисунок 6 – Схема заводки БЗ в помещение заказа:
1 – роликовая дорожка; 2 – помещение заказа; 3 – рама БЗ; 4 – стапельная тележка.
Так как зональный блок находится на роликовой дорожке, то для его заведения в помещение заказа необходимо преодолеть трение качение, возникающее между стальными роликами и стальными рельсами, по которым будет производиться закатка.
Сила трения качения рассчитывается по формуле: , где
- коэффициент трения качения в мм.,
- радиус катящегося тела, в данном случае радиус ролика,
– прижимающая сила.
Прижимающую силу найдем по формуле: N=(mБЗ+mосн)∙g, где mБЗ-масса зонального блока, mосн-масса такелажной оснастки, g - ускорение свободного падения.
N=(63000+140,7)∙9,81=623198,71 (Н).
Значение коэффициента трения качения в паре материалов сталь-сталь равняется 0,05 мм. Радиус ролика принимаем равным 0,1 м.
Основная формула для расчета стропа: , где -количество стропов,
- коэффициент неравномерности распределения массы груза на ветви стропа, зависит от количества ветвей для n≤4, к=1; n≥4, к=0.75,
-угол отклонения стропа от вертикали.
|
|
=77899,86 (Н)
Разрывное усилие в ветви стропа, находим по формуле (Н), где kзап - коэффициент запаса прочности стропа, определяемый в зависимости от группы классификации механизма, находим его из таблицы 1.
Таблица 1 - Зависимость коэффициента запаса прочности стропа от группы классификации механизма.
Группа классификации механизма по ИСО 4301/1 | Подвижные канаты | Неподвижные канаты |
Значение коэффициента kзап | ||
Ml | 3,15 | 2,50 |
М2 | 3,35 | 2,50 |
М3 | 3,55 | 3,00 |
М4 | 4,00 | 3,50 |
М5 | 4,50 | 4,00 |
М6 | 5,60 | 4,50 |
М7 | 7,10 | 5,00 |
М8 | 9,00 | 5,00 |
Принимает запас прочности равный 9, т.к. ЗБ относится к весьма тяжелым механизмам, которые имеют интенсивное использование по классификации ИСО 4301/1.
Разрывное усилие равно
По найденному разрывному усилию R1 подбираем временное сопротивление разрыву, которое должно быть близко по значению к разрывному усилию, но больше его по значению. Данные берем из таблицы 2.
Таблица 2 - Характеристики стальных канатов.
Диаметр каната в мм.
| Маркировочная группа, Н/мм2 (МПа) | |||||||
1470 (150) | 1570 (160) | 1670 (170) | 1770 (180) | 1860(190) | 1960 (200) | |||
разрывное усилие каната в целом, Н, не менее | ||||||||
6,5 | - | - | - | 22950 | 24000 | 24900 | ||
8,5 | - | 35950 | 38200 | 39450 | 41150 | 42800 | ||
11,5 | - | 62600 | 66500 | 68750 | 71700 | 74550 | ||
13,5 | - | 88650 | 94200 | 97100 | 100500 | 105500 | ||
15,5 | - | 113500 | 121000 | 124000 | 130000 | 136000 | ||
17,0 | - | 142000 | 151000 | 155500 | 162500 | 170000 | ||
19,5 | 169000 | 180000 | 191500 | 197000 | 206500 | 215500 | ||
21,5 | 208500 | 222500 | 237000 | 244500 | 255500 | 266500 | ||
23,0 | 241500 | 258000 | 274000 | 283000 | 295000 | 307000 | ||
25,0 | 281000 | 300000 | 318500 | 328500 | 343000 | 358500 | ||
27,0 | 332000 | 354500 | 376500 | 388500 | 406000 | 423500 | ||
29,0 | 378000 | 403500 | 428500 | 441500 | 462000 | 482000 | ||
30,5 | 427000 | 455500 | 484000 | 499000 | 522000 | 544500 | ||
33,0 | 489500 | 522000 | 555000 | 571500 | 597500 | 624000 | ||
35,0 | 556000 | 590000 | 630500 | 650000 | 679500 | 709000 | ||
39,0 | 677000 | 722000 | 767000 | 791000 | 827500 | 863000 |
709000>701098,77
По результатам расчета определили:
1. Натяжение в одной ветви стропа 77899,86 (Н)
2. Разрывное усилие стропа R1 =701098,77 (Н)
3. Подобран канат с временным сопротивлением разрыву = 709000 (Н), диаметром = 35,0мм, маркировочной группы 1960 (200), что соответствует достаточному временному сопротивлению каната равному 1960 Н/мм2 или 200 МПа.
Базирование
Все механизмы строго связаны с конструкцией судна устанавливают в определенное положение путем его базирования.
|
|
Базирование – совмещение базовой системы механизма с общей технологической монтажной базой.
При выполнении центровки механизмов основным методом ее выполнения является центровка по методу «проб и ошибок». Длительность и трудоемкость центровки определяется необходимостью выполнения многократных перемещений механизмов отжимными приспособлениями и совместного проворачивания валов механизмов для контроля параметров центровки и зависит от опыта и квалификации производителя работ.
Недостатки процессов центровки по методу «проб и ошибок» стимулировали развитие процессов центровки по методу «разовой сборки».
Сущность метода заключается в том, что после измерения текущих значений параметров центровки рассчитывают значения перемещений механизма в заданных опорных точках и затем за один обход отжимных приспособлений производят перемещение механизма и его установку в заданное положение. Разработка электронных систем центровки явилось важным этапом решения задачи снижения трудоемкости и длительности операций центровки. Однако, несмотря на бесспорные преимущества электронных систем центровки применение их в российском судостроении сдерживается их высокой стоимостью. Рынок систем центровки, несмотря на их простоту, представлен практически только зарубежными образцами.
Вывешивание зонального блока.
Рисунок 7 – Принципиальное устройство гидродомкрата.
Предмонтажная подготовка амортизаторов.
Для амортизации зонального блока его закрепляют с корпусом судна при помощи пневматических амортизаторов, в которых звукоизолирующие и противоударные функции выполняет сжатый воздух и страхующий резиновый массив.
В данном случае выбраны амортизаторы АПРКу-1500.
Амортизаторы состоят из:
- резинокордной оболочки (РКО) тороидального типа, заполненной воздухом под давлением и служат упругим элементом амортизатора;
- оси, на которой установлена РКО;
- двух полуобойм, охватывающих РКО и служащих для крепления амортизаторов к механизмам или фундаментам;
- двух кронштейнов, служащих для крепления амортизаторов к механизмам или фундаментам;
- невозвратно-запорного устройства для запитки амортизаторов.
Объем воздуха, необходимый для восстановления номинального положения амортизатора после просадки на 3 мм, составляет 0, 005 м³. Минимально допустимое давление в оболочке амортизатора должно быть не менее 0,3МПа.
Номинальное положение амортизатора – когда зазор между осью и ограничителем составляет 10±1мм. Для амортизаторов, у которых рабочее давление меньше указанного в паспорте на величину более 0, 05 МПа, допускается установка зазора 10±2 мм.
Разность зазоров между кронштейнами и ограничителями в амортизаторе не должна превышать 4 мм.
Для демонтажно-монтажных работ и контроля герметичности к невозвратно-запорному устройству должен быть обеспечен доступ.
Рисунок 8 – Схема амортизатора АПРКу-1500:
1 – БЗ; 2 – амортизатор; 3 – металлическая подкладка; 4 – фундамент.
Установка амортизаторов.
Рисунок 9 – Схема установки амортизаторов
Рисунок 10 – Крепление амортизаторов АПРКу-1500:
1 – болт; 2 – лапа БЗ; 3 – подкладка; 4 – платик фундамента; 5 – опорная поверхность фундамента.
Выбор компенсирующих звеньев
Для жесткого и плотного прилегания механизма к фундаменту применяют подкладки.
Размеры и материал подкладок выбирается исходя из удельного давления, веса механизма на подкладку.
Удельное давление, которое обеспечивают подкладки:
• из стали: [g] £ 40 МПа;
• из чугуна, силумина и др. [g] £ 20 МПа.
Технические требования к подкладкам:
- обеспечивать надежное крепление при минимальной высоте;
- обеспечивать неизменность механических характеристик в процессе эксплуатации;
- сохранять геометрически размеры при обжатии крепежа (неизменность формы);
- обеспечивать плотное прилегание как к фундаменту, так и лапам (раме механизма).
Типы подкладок: металлические подкладки; пластмассовые; деревянные.
Наиболее технологичными из перечисленных являются металлические прямоугольные подкладки.
Обработка прокладок и замер их по толщине должны производиться по размерам, снятым с места. Измерение толщин каждой выравнивающей подкладки производить в четырех точках, с точностью не ниже 0,05 мм. При замерах толщин выравнивающих подкладок механизм выставляется без перекосов на отжимных приспособлениях и не касается фундамента.
Материал подкладок Ст20. Прокладки прямоугольной формы клиновые пригоняемые.
Для снятия замеров монтажного зазора использовать штихмассы, нутрометры или другие средства измерения, имеющие цену деления не более 0,01 мм и погрешностью измерения не более ±0,05 мм.
Подкладки изготавливать в соответствии с требованиями детальных чертежей. Максимальная толщина подкладок не должна превышать 63,0 мм, минимальная величина 6 мм. Шероховатость опорных поверхностей подкладок должна быть не более Rz 20 мкм. Острые кромки подкладок должны быть запилены.
Обработку подкладок в размеры по толщине производить по результатам измерения монтажного зазора между опорными поверхностями механизма и фундамента.
Предельные отклонения размеров длины и ширины подкладок принимать ±1,5 мм. Отклонения размеров подкладок по толщине после механообработки от их значений, определенных по результатам измерения монтажного зазора допускается не более ±0,05 мм.
При установке подкладок выдерживать установленные монтажным чертежом зазоры в соединениях подкладок с сопрягаемыми поверхностями механизма и фундамента. При этом пластина щупа с толщиной 0,05 мм не должна проходить в зазор на 0,66 периметра соединения. На остальной части допускается местное прохождение пластины щупа толщиной 0,10 мм.
При установке подкладок на соединяемы опорные поверхности рекомендуется наносить смазку К-17 по ГОСТ 10877-76.
Возможное свисание подкладки с опорной поверхности фундамента не должно превышать 3 мм.
Крепление зонального блока
При выполнении работ соблюдать требования инструкций:
- в части обеспечения мероприятий по сохранению чистоты внутренних полостей механизмов;
- в части обеспечения мероприятий по защите кабелей и электрооборудования;
- в части сохранения установленных на заказе спецпокрытий;
- в части обеспечения мероприятий по сохранению материальной части.
Крепление механизма на фундаменте выполняется в соответствии с требованиями рабочих чертежей.
Устанавливаются шпильки крепления амортизаторов и рамы БЗ. При установке шпилек, пружинных шайб должно выполняться условие собираемости крепежных деталей. Шпильки должны свободно проходить через отверстия амортизатора и рамы БЗ. Гайки шпилек закрутить вручную до упора.
Окончательное обжатие гаек шпилек крепления рамы БЗ к амортизаторам производится с помощью: ключей гаечных по ГОСТ 2838-80, ГОСТ 2839-80, щупа по ГОСТ 882-75. Сначала следует произвести обжатие «крест-накрест» одной половины шпилек, затем второй половины. Затяжка гаек должна быть выполнена динамометрическим ключом. Крутящий момент при затяжке гаек 237 Н∙м. Щуп 0,05 мм не должен проходить под установленную под гайку пружинную шайбу.
Перед установкой в соединения резьбу крепежных деталей необходимо смазывать. Резьбовые соединения из стали собирать на смазке АМС-3 по ГОСТ 1227-75. Резьбовые соединения из сплава собирать с применением графитной смазки.
В результате работы оборудования, установленного на зональный блок, накапливается статическое электричество. С целью предотвращения возгорания в результате электрического разряда и с целью обезопасить обслуживающий персонал, рама зонального блока должна быть заземлена. В качестве перемычки используется медный провод, зажатый с двух сторон в бонках. Бонки привариваются к корпусу установки, к фундаменту и к основанию согласно схеме заземления.
Рисунок 11 - Схема заземления. Рисунок 12 - Узел заземления.
Если ребра или подкрепления фундамента препятствуют установке крепежных болтов, допускается производить подрубку фундамента или подрезку головки болта с одной стороны, но не более чем до стержня болта. Места среза (подрубки) защищать грунтом.
Для обеспечения прилегания головки болта допускается подрезать полку фундамента на глубину не более 10 % от ее толщины. Шероховатость подрезанной поверхности обеспечить не грубее Rz = 40 мкм.
По окончании монтажа крепежные изделия загрунтовать и окрасить. Покрытие крепёжных изделий - химическое фосфатирование с грунтовкой ВЛ-02,1 в один слой.
Окраска амортизаторов не допускается.
Подключение электрооборудования производить в соответствии со схемой внешних соединений. Заземление механизма производить в соответствии с инструкцией. Перемычки заземления не должны ограничивать свободы перемещения механизма на амортизирующих элементах во всех направлениях не менее 50 мм. После установки перемычки заземления необходимо нанести антикоррозионные покрытия на поверхности бонок заземления.
Контроль качества
1. Размеры БЗ и фундаментов, отклонения формы и расположения присоединительных поверхностей БЗ и фундаментов под них контролировать с применением лазерных средств 3D – измерений с последующей проверкой условий собираемости по 3D – моделям в соответствии с требованиями п. 1.5.
2. Проверка отклонений от горизонтальной плоскости транспортировочных путей контролируют с помощью поверочной линейки ШД-3000 по ГОСТ 8026, квадранта оптического КО-10, трубы визирной измерительной ППС-11, или набором щупов в соответствии с требованиями п. 2.4.
3. Собираемость БЗ в помещениях заказа контролируют с помощью лазерного трекера и электронного тахеометра в соответствии с требованиями п.1.7.
4. Контроль защиты опорной поверхности платиков БЗ и фундаментов от действия атмосферной влаги выполняют согласно ГОСТ 9.014
5. Контроль давления рабочей среды при базировании в выделенных группах гидродомкратов выполняют манометрами МА100ВУ63.
6. Снятие нагрузки с жестких опор контролируют визуально по появлению подвижности жесткой опоры.
7. Входной контроль амортизирующих элементов производят внешним осмотром на соответствие требованиям документации (технические условия, стандарты и т. п.) на изготовление и поставку.
8. Контроль установки амортизаторов на штатное место и закрепления крепежными деталями производят в соответствии с монтажным чертежом.
Используемые средства измерений должны быть поверены (откалиброваны) и иметь не просроченные свидетельства (клейма).
ПЛАН ТЕХНОЛОГИЧЕСКОГО ПРОЦЕССА
Дата добавления: 2020-01-07; просмотров: 179; Мы поможем в написании вашей работы! |
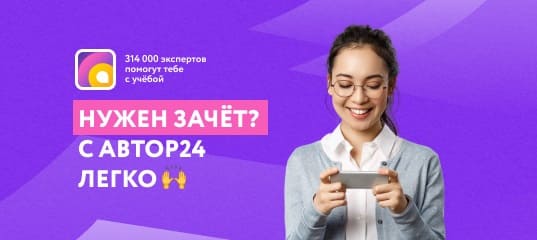
Мы поможем в написании ваших работ!