Дальнейшее совершенствование ДНУ было направлено на устранение выявленных недостатков, что привело к созданию целого ряда модифицированных конструкций.
Билет 8. Вопрос 3. Методы оптимизации работы системы пласт -УЭЦН.
Оптимизация работы системы пласт - УЭЦН предполагает в конечном счете создание условий в скважине, при которых отбор газожидкостной смеси равен притоку из пласта.
Особую категорию составляют обводненные скважины, образующие вязкие водонефтяные эмульсии, извлечение которых с помощью серийных УЭЦН также сопряжено с осложнениями.
Неблагоприятное влияние на работу УЭЦН оказывают механические примеси, неорганические соли, асфальтосмолистые соединения, а также образование парафиновых отложений, наличие в продукции скважин коррозионно-активных веществ. Перечисленные факторы требуют индивидуального подхода при решении вопросов, связанных с оптимизацией.
Одна из главных задач, которая решается при подборе УЭЦН к скважине, - это определение оптимального давления на приеме насоса.
Подбор УЭЦН к скважине следует начинать с установления оптимального значения дебита, рассчитываемого из условий геологического, технологического и технического порядка: прочность породы пласта, цементного камня, возможность разгазирования нефти, обводненность продукции, парафинообразование и т.д.
Принципиальное значение имеет параметр забойного давления, устанавливаемого в скважинах с точки зрения поддержания оптимальных условий разработки объекта. Этот параметр, как известно, обосновывается в проектах разработки месторождения.
|
|
При соблюдении линейного закона фильтрации Дарси и известном коэффициенте продуктивности пласта дебит скважины можно рассчитать по формуле
, (3.40)
где Q - дебит скважины, м3/сут; К - коэффициент продуктивности пласта, м3/(сут·МПа); Рп - пластовое давление, МПа; Рс - забойное давление в скважине, МПа.
Выразив забойное давление Рс через значение столба жидкости (газожидкостной смеси), можно определить динамический уровень жидкости Lд при работе скважины на стационарном режиме по формуле (3.3).
По расчетному значению динамического уровня жидкости в скважине можно записать формулу для определения глубины спуска погружного центробежного электронасоса в виде
, (3.41)
здесь hп - оптимальная глубина погружения насоса под динамический уровень жидкости, м. С этой величиной связан один из главных параметров, определяющих условия работы УЭЦН, - оптимальное давление на приеме Рпр. Именно этот параметр влияет на значение фактического объемного расходного газосодержания, а значит, и на оптимальную подачу УЭЦН.
Многие исследователи под оптимальным давлением на приеме понимают такое давление, при котором УЭЦН работает в области рекомендованного КПД, подачи, температуры в течение длительного времени.
|
|
Промысловыми исследованиями [85] установлено, что с увеличением газосодержания до определенного значения, особенно в скважинах, продуцирующих обводненную нефть, происходит некоторое увеличение КПД, затем он снижается.
В работе [30], выполненной институтом "ТатНИПИнефть", приводится оптимальное газосодержание в откачиваемой жидкости для некоторых типоразмеров УЭЦН (табл. 3.15). Для других типоразмеров газосодержание предлагается принять равным 0,106, что соответствует давлению на приеме 6,0 МПа для безводной нефти Ромашкинского месторождения.
Анализ рассмотренных материалов позволяет сделать следующие выводы:
· установлено существование в скважине, эксплуатируемой УЭЦН, оптимального газосодержания, часто отличающегося от рекомендаций в инструкциях по их применению;
· для конкретных месторождений определены значения оптимального давления на приеме насосов;
· построены графические зависимости давление - обводненность - газосодержание для ряда месторождений (рис. 3.9).
Рис. 3.9. График изменения объемного расходного газосодержания в жидкости в зависимости от давления на приеме насоса и обводненности продукции пласта, %:
|
|
1 - 0; 2 - 10; 3 - 20; 4 - 30; 5 - 40; 6 - 50; 7 - 60; 8 - 70; 9 - 80; 10 - 90
Газосодержание в безводной нефти для УЭЦН
Типоразмер УЭЦН | Газосодержание, м3/м3 | Давление на приеме УЭЦН, МПа |
УЭЦН5-80-1200 | 0,084 | 6,4 |
УЭЦН5-130-1200 | 0,152 | 5,2 |
УЭЦН6-160-1100 | 0,114 | 5,8 |
Билет 9. Вопрос 1 Промысловые исследования возможности эксплуатации двух скважин одним станком-качалкой
Кустовое расположение скважин и их наклонно направленный характер профиля ствола предъявляют специфические требования к технике эксплуатации скважин. Ввиду отсутствия промышленно освоенных образцов специальной техники возникает необходимость организации производства новых, менее материалоемких, с улучшенными энергетическими показателями станков-качалок. Этим требованиям отвечают групповые приводы. При этом желательно простое конструктивное решение, которое можно было бы реализовать силами НГДУ.
При использовании группового привода увеличивается долговечность устьевых сальников, так как применение шкивов на крайних опорах вместо головки балансира позволяет более точно центрировать точки подвеса штанг с осью скважины. Это преимущество имеет немаловажное значение при существующей экологической обстановке на промыслах.
|
|
Как показали исследования, экономия металла при замене индивидуального привода на групповой составляет до 3 т на одну скважину. Потребность в электрооборудовании и средствах управления на скважину уменьшается в 2 раза. Надежность работы станка-качалки возрастает за счет снижения максимальной нагрузки на головку балансира.
Однако групповым приводам присущи следующие характерные недостатки:
- остановка приводного устройства для спуско подъемных операций;
- установка строго фиксированного расстояния между устьями скважин при разбуривании скважин;
- невозможность эксплуатации одной скважины в период простоя другой;
- необходимость обеспечения одного и того же режима эксплуатации спаренных скважин;
- невозможность индивидуального регулирования режима работы спаренных скважин.
Установка работает следующим образом. Посредством канатных подвесок 6 и 18, направляющих шкивов 8, 13, 15, 17 и механизмов крепления 11 и 12 устьевые штоки 5 и 19 колонн штанг соединяют с головкой балансира 4 станка-качалки 3. При этом скважину, в которой нагрузка в точке подвеса штанг больше, подключают через канатную подвеску 18 и направляющие шкивы 13 и 17 к нижнему механизму крепления 12 головки балансира 4 станка-качалки 3. Скважина с меньшей нагрузкой в точке подвеса штанг подключается к верхнему механизму крепления 11. При этом уравновешивание станка-качалки 3 обеспечивает кривошипный уравновешивающий груз 2. При ходе переднего плеча балансира вниз устьевой шток 19 более нагруженной скважины совершает ход вниз, а устьевой шток 5 менее нагруженной скважины - вверх.
В случае изменения технологических параметров, когда более нагруженной окажется другая скважина, перемещением шкивов 15 и 13 относительно головки балансира 4 станка-качалки 3 изменяется порядок крепления устьевых подвесок 6 и 18. Таким образом, канатная подвеска 6 соединяется с нижним 12 механизмом крепления через шкив 13, а подвеска 18 - с верхним 11 механизмом крепления через шкив 15.
Надежная работа станка-качалки возможна при условии действия растягивающей нагрузки на головку балансира снизу. При эксплуатации скважин с близкими технологическими параметрами нагрузки, действующие на устьевые штоки 5 и 19, примерно одинаковые. Поэтому одинаковые нагрузки действуют на головку балансира 4 как со стороны верхнего 11, так и со стороны нижнего 12 механизма крепления канатных подвесок 6 и 18. При этом уравновешивание станка-качалки 3 грузом 2, установленным на кривошипе, не обеспечивается. Для достижения большей нагрузки на головку балансира 4 станка-качалки 3 со стороны нижнего 12 механизма крепления канатной подвески к устьевым штокам 5 и 19 посредством гибкой связи 9 крепятся дополнительные уравновешивающие контргрузы 10 и 20 соответствующего значения. При этом режим работы станка-качалки с точки зрения его уравновешивания становится соответствующим заданному. Изменением веса контргрузов 10 и 20 при любых условиях можно обеспечить превышение нагрузки в одной из скважин.
Привод допускает возможность эксплуатации одной скважины, присоединяя устьевой шток через канатную подвеску и направляющий шкив 13 к нижнему 12 механизму крепления головки балансира. Для проведения ремонтных работ шкивы 8 и 17 допускают возможность поворота относительно вертикальной оси.
Рис. 2.22. Схема опытно-промышленной установки для эксплуатации СШН в двух скважинах-
1- фундамент СК; 2 – уравновешивающий груз; 3 - станок-качалка; 4 - балансир; 5, 19 - устьевые штоки; 6, 18- канатные подвески, 7, 16 - стойки; 8, 13, 15, 17 - шкивы направляющие; 9 - гибкие связи контргрузов; 10, 20 - контргрузы; 11, 12 - механизмы крепления; 14 - основание дополнительной опоры
Для обеспечения работоспособности конструкции группового привода минимальная нагрузка в одной скважине должна превышать максимальную в другой. Поэтому схема предусматривает дополнительные устьевые контргрузы. При этом направляющие шкивы группового привода размещаются на одной стойке попарно. Первая пара шкивов связана с головкой балансира СК канатной подвеской, а шкивы выполнены двухручьевыми и допускают перемещение вдоль стойки относительно головки балансира. Это дает возможность закрепления канатной подвески при большой нагрузке в нижней точке балансира.
Другая пара четырехручьевых шкивов монтируется стационарно у устьев скважин, это позволяет соединить канатные подвески гибкой связью с уравновешивающими грузами.
Для эксплуатации скважин с расстоянием между устьями 5-13 м разработана конструкция установки с уменьшенным расстоянием между внутренними стойками вспомогательной рамы, предусматривающая крепление двухручьевых шкивов непосредственно на стойках. Регулировку расстояния между осями четырехручьевых шкивов производят изменением длины горизонтальной тяги.
Положительный эффект при применении описанных приводов достигается за счет снижения затрат на монтаж дополнительного индивидуального привода и его эксплуатацию.
Билет 9. Вопрос 2. Эксплуатация скважин винтовыми штанговыми насосами
Для решения проблемы откачки жидкости повышенной вязкости были предложены установки винтовых насосов, обладающие целым рядом преимуществ перед насосами других типов. По сравнению с УЭЦН при эксплуатации УВН имеет место весьма малое перемешивание перекачиваемой жидкости, что предотвращает образование стойких эмульсий из нефти и воды. Отсутствие клапанов и сложных проходов определяет простоту конструкции и снижает гидравлические потери. Насосы обладают повышенной надежностью (особенно при откачке жидкостей с механическими примесями) вследствие того, что имеют минимальное число движущихся деталей, просты в изготовлении и эксплуатации, более экономичны. При перекачке жидкости повышенной вязкости снижаются перетоки через уплотняющую контактную линию между винтом и обоймой, что улучшает характеристику насоса.
Благодаря нечувствительности к свободному газу винтовые насосы идеальны для перекачки высокогазированных нефтей. Они являются более износоустойчивыми при добыче нефти, содержащей механические примеси, так как твердые частицы, проходя через насос, вдавливаются в эластомер обоймы (статора), который деформируется, но не истирается.
Промышленность освоила погружные насосы типа УЭВНТ производительностью 16, 25, 100, 200 м3/сут с напором соответственно 1200, 1000, 1000, 900 м столба жидкости.
Однако конструктивные недостатки, присущие первым опытным экземплярам насосов, не были преодолены, что явилось причиной их ограниченного применения. В частности, очень часто выходила из строя обойма (статор), что приводило к заклиниванию винта и его слому, разрушались опорные подшипники и пята.
На зарубежном и российском рынках появились винтовые насосы, повторяющие основные технические решения отечественных конструкторов, но более надежные в применении. Это было достигнуто использованием более устойчивых к скважинным условиям конструкционных материалов, в частности эластомеров. Кроме того, в качестве привода был применен не погружной, а наземный электродвигатель, крутящий момент от которого передавался ротору насоса колонной штанг.
Винтовой штанговый насос включает в себя узлы, назначение и конструкция которых следующие.
Газовый сепаратор (рис. 4.1) обеспечивает частичную сепарацию газа из жидкости, поступающей в насос, за счет изменения направления ее движения в прием. Он состоит из системы труб, оборудованных приемными и выпускными каналами (рис. 4.2).
Якорь (в спецификации фирмы - торсионный анкер) обеспечивает надежную фиксацию насоса в обсадных трубах и тем самым предупреждает произвольное вращение насосно-компрессорных труб в процессе работы насоса.
Винтовой насос состоит из статора 3 и ротора (винта) 4 (см. рис. 4.1). Статор представляет собой металлическую трубу, в которую запрессован эластомер - материал, устойчивый к воздействию механических примесей, нефти и коррозионно-активной жидкости. Однако углекислоты и свободный диоксид углерода вызывают разрушение эластомера, поэтому вводится ограничение на содержание этих компонентов в добываемой жидкости, количество которых не должно превышать 1000 мг/л.
|

Рис. 4.3. Схема работы винтового насоса:
а - общий вид насоса: 1 - статор, 2 - ротор; б - статическое положение ротора в статоре: 1 - поверхность статора 2L, 2 - поверхность ротора при длине L; в - положение ротора в статоре в динамике: 1 - в начале вращения, 2 - после поворота на угол 90°, 3 - после поворота на угол 180°
Ротор представляет собой хромированный однозаходный винт, обработанный с соблюдением весьма малых допусков. Схема размещения ротора в статоре и его перемещения приведена на рис. 4.3.
Как и у отечественных винтовых насосов, ротор в статоре совершает планетарное движение, что обеспечивает создание между винтом и обоймой отсеченных друг от друга камер, заполненных жидкостью и перемещающихся при движении винта от приема к выкиду. Камеры достаточно герметичны и поэтому обеспечивается непрерывная подача жидкости, пропорциональная частоте вращения ротора.
Насосные штанги 5 (см. рис. 4.1) предназначены для передачи крутящего момента от наземного электропривода ротору насоса. Конструктивно они не отличаются от отечественных. Колонна штанг выбирается таким образом, чтобы она выдерживала нагрузки, возникающие при эксплуатации. Размеры и компоновка колонны рассчитываются по специальной методике.
Для центрирования вращающейся колонны штанг в насосно-компрессорных трубах и, таким образом, предотвращения истирания НКТ и штанг используют специальные устройства -протекторы. В наклонных скважинах рекомендуется применять невращающиеся протекторы. Количество протекторов выбирается в зависимости от кривизны скважины.
Устьевое оборудование (см. рис. 4.1) состоит из фланца 9, на котором монтируются превентор 10, второй сальник 11, полированный шток 12, взрывозащищенный электродвигатель 13 с приводной головкой 14.
Превентор (рис. 4.4) является противовыбросовым устройством, перекрывающим колонну НКТ при фонтанных проявлениях. Он приводится в действие вручную.
Монтаж УВН начинают со спуска колонны насосно-компрессорных труб: к самой нижней трубе крепят статор насоса, а трубы оборудуют центраторами в соответствии с данными (см. табл. 4.5). Затем на штангах спускают ротор. Длину труб и штанг перед спуском тщательно измеряют, а их свинчивание производят с максимально допускаемым силовым моментом на ключе.
Выбор эластомера для статора производится исходя из значения температуры, при которой предполагается его работа в скважине. При этом следует знать, что в насосах применяются эластомеры трех типов, работающие при различных температурах: тип 1 - при 90 °С; тип 2 - при 105 °С; тип 3 - при 135 °С.
При выборе ротора необходимо учитывать характеристику среды, в которой будет работать насос: при рН = 6 ÷ 8 применяют стандартный хромированный ротор, для других значений рН рекомендуют роторы из нержавеющей стали.
Билет 9. Вопрос 3. Эксплуатация скважин установками струйных насосов.
Установки струйных насосов обладают рядом существенных преимуществ по сравнению с другими способами эксплуатации:
- простота и компактность скважинного оборудования;
- отсутствие движущихся частей, кабеля и насосных штанг;
- высокая надежность скважинного оборудования, большой межремонтный период работы;
- простота регулирования отбора продукции скважины;
- замена насоса без подземного ремонта;
- подача в скважину необходимых реагентов и тепловой энергии с рабочей жидкостью;
- доступ на забой без подъема скважинного оборудования;
- создание требуемых депрессий на пласт;
- проведение гидродинамических исследований в скважине и оптимизация отбора жидкости;
- добыча нефти из малодебитных скважин - менее 10 м3/сут. (Сравнительные данные граничных условий применения различных способов эксплуатации и преимущества УСН приведены в табл. 4.12.);
- минимальные затраты на подъем жидкости при дебитах до 150 м3/сут;
- эксплуатация скважин в осложненных условиях (высокая температура, высокий газовый фактор, высокое давление насыщения нефти газом, большая вязкость откачиваемой продукции, большая глубина, соле- и парафиноотложения, высокое содержание песка, низкая проницаемость коллектора, нестабильный приток жидкости из пласта, большая кривизна скважины вплоть до горизонтали).
Есть и отрицательные стороны при применении струйных насосов: высокая цена оборудования (в 2,2 раза дороже, чем ШСНУ, и в 1,5, чем УЭЦН, при прочих равных условиях); необходимость привлечения для обслуживания персонала высокой квалификации.
Принцип работы всех УСН заключается в следующем. Рабочая жидкость под высоким давлением подается в сопло и истекает с высокой скоростью (до 300 м/с). При этом создается область разрежения и добываемая жидкость через горловину всасывается в диффузор. Диаметр диффузора в несколько раз (4-6) больше диаметра сопла, и поэтому скорость жидкости быстро падает. Происходит обратный процесс перехода кинетической энергии жидкости в потенциальную энергию ее подъема на поверхность.
Разработка конструкций струйных насосов идет по пути размещения силовых агрегатов в скважине (погружные агрегаты) и на поверхности. Применение погружных агрегатов ведет к уменьшению габаритов установки, снижению ее металлоемкости, повышению КПД. Однако помещение агрегата на устье создает лучшие условия для контроля и регулирования, а также для использования давления столба жидкости в скважине в качестве части рабочего давления. Этим и объясняется тот факт, что преимущественное распространение получили установки с наземными силовыми агрегатами.
На рис. 4.10 приведены конструкции подземной части оборудования струйных насосов. Все они имеют сходное устройство, включающее кожух струйного насоса 3, сопло 4, всасывающие окна 6, специальную муфту 7, колонну насосно-компрессорных труб 2. Различаются установки схемой подачи силовой жидкости: в схеме а она подается по колонне насосно-компрессорных труб и поднимается вместе с добываемой жидкостью по затрубному пространству; в схеме в силовая жидкость подается по эксплуатационной колонне и поднимается по колонне НКТ; в схеме б спущена вторая колонна НКТ, и силовая жидкость подается по кольцевому пространству, образованному двумя колоннами труб, а поднимается по центральной колонне.
Рис. 4.10. Установки струйных насосов с использованием поверхностного силового привода при компоновке:
а - пакерной с обратным расположением струйного насоса; б - беспакерной двухтрубной с прямым расположением струйного насоса; в - пакерной с прямым расположением струйного насоса; 1 - эксплуатационная колонна; 2 - колонна НКТ; 3 - кожух струйного насоса; 4 - сопло; 5 - пакер; 6 - всасывающие окна; 7 - специальная муфта; 8 - внешняя колонна НКТ
Все схемы имеют определенные достоинства и недостатки: подъем жидкости по эксплуатационной колонне может привести к ее запарафированию (при добыче высокопарафинистых нефтей), коррозионному и эрозионному ее разрушению; подача силовой жидкости по эксплуатационной колонне может вызвать разрушения последней вследствие создания критических давлений; схемы а и в предполагают применение пакера, монтаж и демонтаж которого часто бывает затруднен; применение дополнительной колонны НКТ (схема б) резко увеличивает металлоемкость установки и не всегда приемлемо из-за небольших диаметральных габаритов скважин.
Билет 10. Вопрос 1. Эксплуатация скважин установками электродиафрагменных насосов.
Отличительными конструктивными особенностями диафрагменного насоса являются изоляция его исполнительных органов от перекачиваемой среды эластичной диафрагмой и работа этих органов в герметичной полости, заполненной чистой жидкостью.
По принципу действия диафрагменный насос сравним с поршневым насосом - рабочий процесс осуществляется путем всасывания и нагнетания перекачиваемой жидкости.
Погружные диафрагменные насосы различных типов классифицируют по ряду признаков:
· по способу приведения диафрагмы в возвратно-поступательное движение: механический привод, гидравлический привод;
· по конструкции диафрагмы: плоская, цилиндрическая, сильфон;
· по виду энергии, подводимой к насосу с поверхности: электрическая, гидравлическая.
Первые экземпляры диафрагменных насосов для добычи нефти были испытаны в 60-х годах. Эксплуатационников привлекли следующие конструктивные достоинства УЭДН,выгодно отличающие их от применяемых повсеместно штанговых насосов:
· отсутствие крупногабаритного и металлоемкого наземного оборудования;
· небольшая установочная мощность электропривода;
· простота монтажа и эксплуатации;
· удовлетворительная эксплуатация скважин, дающих вязкие эмульсии, жидкости, содержащие механические примеси и свободный газ;
· возможность применения в скважинах с низкими дебитами;
· возможность эксплуатации месторождений с небольшими устьевыми площадками (море, болота и др.).
· эффективность использования в скважинах с кривыми или наклонно направленными стволами.
Погружной электродиафрагменный насос опускают в скважину на НКТ. Погружной электродиафрагменный насос (рис. 4.8) снабжается эластичной диафрагмой, совершающей колебательные движения и создающей за счет этого эффект всасывания и нагнетания. Отличительной конструктивной особенностью ЭДН является изоляция его исполнительных органов от перекачиваемой среды. Это должно обеспечить более длительную работу узлов и деталей насоса в скважине.
Диафрагма 19 взаимодействует с плунжером 5, перемещающимся возвратно-поступательно под действием эксцентрикового привода 4. Последний включает в себя эксцентрик, вращающийся в подшипниках, и редуктор 21, ведущая шестерня которого посажена на вал электродвигателя 2.
Рис. 4.8. Погружной электродиафрагменный насос типа ЭДН5:
1 – компенсатор электродвигателя; 2 - электродвигатель; 3 - стакан; 4 - эксцентриковый привод; 5 - плунжерный насос; 6 - пружина; 7 - корпус; 8 - резьба; 9 - головка; 10 - всасывающий клапан; 11 - нагнетательный клапан; 12 - сетка; 13 - газосепаратор; 14 - муфта; 15 - трубка; 16 - патрубок; 17 - крышка; 18 - токоввод; 19 - диафрагма; 20 - штекерный разъем; 21 - конический редуктор
Движение диафрагмы вниз вызывает срабатывание всасывающего клапана 10, через который скважинная жидкость поступает в диафрагменную полость. Движение вверх приводит к выталкиванию жидкости через нагнетательный клапан 11 в насосно-компрессорные трубы.
Трубка 15 служит для защиты нагнетательного клапана от осаждающихся из добываемой жидкости механических примесей при остановках насоса. Муфта 14 и патрубок 16 обеспечивают присоединение электронасоса к НКТ.
Наиболее нагруженными элементами агрегата являются редуктор, диафрагма и клапаны.
Билет 10. Вопрос 2. Методы борьбы с отложениями парафина в фонтанных скважинах
Сегодня, как и много десятилетий тому назад, в арсенале нефтяников преобладают следующие методы: тепловые, физические, химические, механические и применение покрытий.
На отдельных месторождениях в качестве экспериментальных проводятся работы по применению вибрационных и магнитных способов.
Тепловые методы основаны на свойствах парафина плавиться при температурах выше 50 °С и, стекая с нагретой поверхности, освобождать ее.
В настоящее время используются следующие технологии с применением:
· горячей нефти или воды в качестве теплоносителя;
· острого пара;
· электрических печей наземного и скважинного исполнения;
· агентов, взаимодействие которых ведет к химической реакции, сопровождающейся выделением некоторого количества тепла.
Технология применения теплоносителя предусматривает нагрев жидкости в специальных нагревателях - котельных установках передвижного типа и подачу ее в скважину способом прямой или обратной промывки.
Для этой цели промышленность выпускает специальные агрегаты - депарафинизационные передвижные установки, оснащенные котлами - подогревателями жидкости до температуры 150 °С и насосами, развивающими давление до 16 МПа. Нагретый агент может циркулировать в скважине определенное время, обеспечивая расплавление и удаление отложений.
Целесообразно применять ППУ для очистки манифольдов, арматуры и трубопроводов в зоне расположения скважины. Поднятые на поверхность НКТ лучше поместить в кассету и воздействовать на них паром от ППУ. При этом одновременно очищаются 10 - 20 труб. Для усиления эффекта в трубы можно вставить поршни.
Повышение эффективности очистки НКТ от отложений парафина может быть достигнуто ранее применявшейся, но к настоящему времени повсеместно утраченной технологией, приведенной на рис. 7.10. Улучшение процесса очистки происходит за счет совмещения операции промывки горячей жидкостью со спуском поршня. Последний обеспечивает направленное движение теплоносителя вдоль внутренней поверхности НКТ и более рациональное использование тепла.
Рис. 7.10. Схема оборудования скважины для депарафинизации горячей нефтью по центральной схеме с применением плунжера:
1 - направляющий ролик; 2 - лубрикатор; 3 - плунжер; 4 -парафин; 5 - лебедка с канатиком
Одной из разновидностей депарафинизации является применение устройств, располагаемых в области интенсивного парафинообразования.
Конструкция первых нагревателей (рис. 7.11) включала обмотку 2, сердечник 3, подвижной контакт 1, присоединительные клеммы 4 и 5, электроисточник 6.
Здесь сердечником служит колонна насосно-компрессорных труб. Подача напряжения осуществляется на индукционную катушку по обсадной колонне, а на сердечник по НКТ. Условием работы схемы является обеспечение надежной изоляции НКТ от обсадной колонны. Это достигается применением центраторов, выполненных из электроизоляционного материала.
В последние годы промышленность освоила выпуск установки для электропрогрева скважин типа УЭС-1500, которая обеспечивает спуск в скважину на кабель-канате на глубину до 1500 м электропечи мощностью до 50 кВт.
Установка создает температуру в интервале спуска до 100 °С и включает в себя лебедку, смонтированную на шасси автомобиля, автотрансформатор, кабель-канат и электропечь (рис. 7.12). Назначение автотрансформатора - компенсировать потери напряжения в кабеле, значение которых зависит от глубины спуска электропечи.
Дальнейшим развитием этого направления явился спуск нагревателей внутрь НКТ непосредственно в интервалы парафинообразования, для чего была разработана малогабаритная печь диаметром 29 мм и мощностью 9,45 кВт.
Применение электронагревателей для борьбы с отложениями парафина в устьевой арматуре и манифольдах было реализовано путем монтажа на устье скважины специальной батареи из трех сообщающихся между собой труб, на которые наматывалась электрическая обмотка. Трубы подключаются к арматуре и через них пропускается добываемая жидкость, а на обмотку подается напряжение (рис. 7.13).
Мощность нагревателя составляла 24 кВт, температура нагрева жидкости достигала 75 °С. Устройство позволяет осуществлять циркуляцию нагретой жидкости через арматуру и рабочий манифольд и обеспечивать удовлетворительную их очистку от парафина.
Рис. 7.13. Индукционный прямоточный подогреватель и схема его подключения:
1 - скважина; 2 - устьевая арматура; 3 - подогреватель
Методы, относящиеся к физическим, основываются на применении электрических, магнитных, электромагнитных полей, механических и ультразвуковых колебаний.
Устройства представляют собой цилиндры диаметрами 60 и 42 мм, длиной 450 и 350 мм, массой примерно 5 и 3 кг, выполненные из коррозионно-стойкой стали и снабженные элементами крепления внутри трубы и элементами, позволяющими подвешивать их в НКТ на проволоке, в том числе вместе с механическим скребком или утяжелителем. Подъема НКТ в большинстве случаев не требуется.
Форма корпуса МОЖ сконструирована так, что магнитный эффект усиливается гидравлическим. Защита от отложения осуществляется в результате формирования АСПО в объеме с последующим флотационным их выносом на устье скважины.
По результатам промысловых испытаний магнитных депарафинизаторов сделаны следующие выводы:
§ магнитными депарафинизаторами можно оборудовать скважины и выкидные линии;
§ в фонтанные скважины и скважины с ЭЦНУ депарафинизаторы следует спускать на скребковой проволоке;
§ в скважинах с большим газовым фактором депарафинизатор необходимо перед запуском поднимать до лубрикатора;
§ для месторождений с незаконченным обустройством магнитные депарафинизаторы являются оптимальным средством предотвращения АСПО;
§ срок окупаемости магнитных депарафинизаторов в скважинах с небольшим межочистным сроком (до нескольких суток) составляет не более одного месяца.
Вибрационные методы основаны на создании в области парафинообразования ультразвуковых колебаний, которые, воздействуя на кристаллы парафина, вызывают их микроперемещение, что препятствует осаждению на стенках труб. Устройство генерировало гидравлические колебания частотой до 1,8 Гц за счет колебания пластины, помещенной в центр потока струи движущейся жидкости.
В основе действия реагентов ингибиторов парафиноотложений лежат адсорбционные процессы, происходящие на границе раздела между жидкой фазой и твердой поверхностью. По этому признаку ингибиторы подразделяются на: смачивающие, модификаторы, депрессаторы и диспергаторы.
Механизм действия смачивающих агентов сводится к образованию на поверхности металла труб гидрофильной пленки, препятствующей адгезии кристаллов парафина к трубам и создающей условия для их выноса потоком жидкости. Условием эффективного применения агентов этой группы является отсутствие каких-либо отложений на трубах перед использованием ингибиторов.
Модификаторы взаимодействуют с молекулами парафина, ослабляя процесс укрупнения кристаллов. Это способствует поддержанию кристаллов во взвешенном состоянии в процессе их движения.
Механизм действия депрессаторов заключается в адсорбции их молекул на кристаллах парафина, что затрудняет их способность к агрегации и накоплению.
Диспергаторы - химреагенты, обеспечивающие повышение теплопроводности нефти и, следовательно, замедляющие процессы кристаллизации парафина. В результате время пребывания парафина во взвешенном состоянии в потоке и вероятность его подъема потоком жидкости увеличиваются.
Отдельную группу образуют химреагенты, назначение которых удалить уже образовавшиеся отложения или несколько уменьшить интенсивность их накопления. Они получили название удалителей и по химическому составу - это растворители, являющиеся отходами или промежуточными производными нефтехимических производств.
Механические методы предполагают удаление уже образовавшихся АСПО на насосно-компрессорных трубах. Для этой цели разработана целая гамма скребков различной конструкции.
Исследованиями ученых установлено, что шероховатость поверхности труб обсадных и подъемных колонн является одним из факторов, способствующих образованию отложений АСПО. По данным работы, отложения парафина возрастают с увеличением шероховатости поверхности. Установлено, что чем выше шероховатость поверхности, тем интенсивнее парафинообразование.
Дальнейшие исследования показали, что на гладкой поверхности, образованной из лаков, стекла, эмали, отложения незначительны.
Известно, что при эксплуатации в промысловых условиях НКТ подвергаются при перевозках, спускоподъемных операциях и в скважинах значительным ударным, растягивающим, сжимающим, изгибающим и другим нагрузкам. Испытания показали, что этим условиям наиболее соответствуют трубы с эпоксидными и эмалевыми покрытиями.
Стеклянное покрытие ввиду его хрупкости, значительной толщины и отсутствия сцепления с металлом трубы не надежно и разрушается в процессе спускоподъемных операций. Последнее ведет к образованию стеклянных пробок в колонне НКТ и заклиниванию насосов. Кроме того, технология образования стеклянных и эмалевых покрытий предполагает нагрев труб до 700 - 800 °С, что вызывает необратимые процессы в структуре металла и расплавление вершин резьб. Последнее приводит к уменьшению прочности резьбового соединения труб и провоцирует обрывы.
Применение футерованных лифтов в скважинах, эксплуатируемых УЭЦН, особенно эффективно, так как спуск скребка в скважину с большим дебитом затруднителен, а зачастую невозможен. Для спуска скребка насос необходимо остановить, но и это не исключает подбросов, запутывания проволоки и других осложнений, в ряде случаев заканчивающихся подземным ремонтом.
В НГДУ "Бузулукнефть" в 210 скважин были опущены трубы с эпоксидным покрытием, в четыре скважины - трубы, футерованные стеклоэмалью. Опыт их эксплуатации показал, что лучшими свойствами для применения в промысловых условиях обладают трубы с эпоксидным и стеклоэмалевым покрытиями.
Билет 10. Вопрос 3. Образование кристаллогидратов в нефтяных скважинах.
Термобарические условия в нефтяной скважине зависят от таких факторов, как температура и давление в продуктивном пласте, продуктивная характеристика, дебит нефти и обводненность продукции, геотермический градиент, количество растворенного газа и его состав, конструкция скважины и коэффициенты теплопроводности и теплопередачи труб, цементного камня и пород в разрезе скважины и т.д. Из всех перечисленных факторов многие являются характерными для месторождения и остаются постоянными на весь период разработки. Изменяются дебиты скважины, обводненность продукции, пластовые и забойные давления. За счет прогрева пород вокруг ствола скважины несколько меняется коэффициент теплопередачи.
На практике в процессе эксплуатации нефтяной залежи можно в известных пределах изменять только дебит скважины. При этом в конкретной системе пласт - скважина все остальные параметры устанавливаются автоматически, т.е. система имеет только одну степень свободы.
Анализ полученных материалов показывает:
§ при снижении забойного давления температура жидкости на устье уменьшается за счет выделения газа;
§ снижение забойного давления до значения меньшего, чем давление насыщения, приводит к некоторому увеличению температуры на устье за счет большего нагрева газа в призабойной зоне пласта;
§ увеличение обводненности ведет к росту устьевой температуры, что объясняется большей теплоемкостью воды, чем нефти;
§ понижение забойного давления повышает вероятность гидратообразования;
§ повышение обводненности снижает вероятность гидратообразования;
§ снижение забойного давления ниже давления насыщения ведет к сокращению зоны возможного гидратообразования.
Например, В.А. Истомин считает, что нефтяная скважина может длительное время работать в гидратном режиме вследствие того, что нефть снижает адгезию гидратов к трубам и способствует выносу образовавшихся гидратов газожидкостным потоком.
Однако при изменении режима работы скважины, особенно при ее остановке, вероятность образования гидратных пробок возрастает. Минерализация пластовых вод снижает равновесную температуру гидратообразования обычно на 5-12 °С.
Принято считать, что угроза гидратообразования в нефтяных скважинах наступает при переохлаждении, равном б °С.
ЭКЗАМЕНАЦИОННЫЙ БИЛЕТ № 11 1. Общая характеристика АСПО.
Под парафиновыми соединениями, выделяющимися из нефти в скважинах в процессе добычи нефти, понимают сложную углеводородную физико-химическую смесь.
В первую очередь это - собственно парафины, представляющие собой углеводороды метанового ряда от С16Н34 до C64H130, а также асфальтосмолистые соединения, силикагелевые смолы, масла, вода, механические примеси.
Технологическая классификация делит нефти по содержанию парафина на следующие виды:
· малопарафиновые менее 1,5 % (по массе);
· парафиновые от 1,5 до 6 % (по массе);
· высокопарафиновые более 6,0 % (по массе).
Парафины в нефти в пластовых условиях находятся в растворенном состоянии. Нефти одного и того же района содержат тем меньше парафина, чем больше в них смолистых веществ. Содержание парафина в нефтях одного и того же месторождения возрастает с глубиной залегания. Температура плавления твердых парафиновых углеводородов тем выше, чем больше их молекулярная масса. Плотность парафинов в твердом состоянии колеблется от 865 до 940 кг/м3, а в расплавленном - от 777 до 790 кг/м3. Растворимость парафина в органических жидкостях велика, падает с увеличением молярной массы и растет с повышением температуры.
В химическом отношении парафины различаются стойкостью по отношению к разным химическим реагентам. Серная кислота не действует на парафин не только при низких температурах, но и при высоких. Обычные азотная и соляная кислоты, а также щелочи инертны в отношении парафина. Парафин легко окисляется воздухом.
Высокомолекулярные парафины от С37Н74 до С53Н108 называемые церезинами, отличаются по своим свойствам от обычных парафинов - имеют более высокую температуру кипения, а также обладают большими молекулярными массами и плотностью.
В состав смолистых веществ входят азот, сера и кислород. Они обладают высокой молярной массой, нелетучи, имеют большую неоднородность. По классификации некоторых
ученых к группе смолистых соединений отнесены асфальтены.
В связи с испарением и окислением нефти увеличивается содержание смолистых веществ в ней. Содержание смол возрастает при контакте с краевыми водами. Нефти обводненных скважин оказываются более смолистыми даже в пределах одного и того же месторождения.
Билет 11 2. Особенности применения методов предупреждения образования АСПО при эксплуатации ШСНУ.
Парафинообразование в скважинах, оборудованных штанговыми насосами, имеет некоторые особенности. Они заключаются в следующем:
§ в области приема ШГН происходит снижение давления и начинается интенсивное газоотделение, которое сопровождается выпадением парафина;
§ парафин откладывается на фильтре насоса, уменьшая его полезное сечение, а значит, ухудшая поступление жидкости в насос и снижая его подачу;
§ парафин прилипает к седлам и клапанам, ухудшая герметичность этой пары, что приводит к утечкам части жидкости из цилиндра;
§ парафин откладывается в зазоре между цилиндром и плунжером, приводя к заклиниванию последнего;
§ парафин осаждается на штангах, увеличивая их массу и значение сил гидравлического сопротивления при их перемещении;
§ парафин откладывается на НКТ, уменьшая свободное сечение для движения добываемой жидкости и увеличивая нагрузку на головку балансира и штанги; последнее приводит к увеличению обрывности штанг.
Масса колонны штанг с отложившимся на ней парафином увеличивается в среднем на 600 кг, а количество отказов насоса, связанных с заклиниванием плунжера в цилиндре из-за парафина, достигает 72 % общего числа отказов насоса.
Среди тепловых методов, применяемых в скважинах, эксплуатируемых ШГН, в настоящее время преобладают: промывка скважин горячей нефтью; пропарка оборудования острым паром; использование электрических нагревателей.
Технология промывки горячей нефтью не отличается от описанной для фонтанной скважины. Разновидностью является использование промывки одновременно с работой штангового насоса. Это повышает эффективность отмыва отложений за счет интенсификации воздействия прокачиваемой жидкости на элементы оборудования и лучшего выноса АСПО из скважины.
С целью лучшей очистки труб и оборудования в теплоноситель добавляют химические реагенты.
Пропарка острым паром преимущественно используется для очистки приустьевой зоны скважины, а также арматуры и манифольдов.
Проведение этой операции имеет свои особенности. Во-первых, возможно образование парафиновых пробок вследствие накопления отделившегося парафина, устранение которых потребует дополнительной работы. Поэтому следует предусмотреть циркуляцию жидкости для выноса отложений. Во-вторых, пропарка поднятого из скважины оборудования - труб, штанг, насосов и т.д. - должна проводиться в закрытых кассетах. Это позволяет экономить тепло и утилизировать отложения. Последнее весьма важно с точки зрения охраны окружающей среды.
Электродепарафинизация в скважинах с УШГН в настоящее время приобрела несколько технических решений.
1. Использование серийной установки типа УЭС-1500, требующей подъема оборудования из скважины, спуска электронагревателя и его подъема с последующим спуском насосного оборудования. Это нерационально, так как вызывает длительный простой скважины.
2. Применение малогабаритного электронагревателя, спускаемого в затрубное пространство с помощью установки типа УЭС-1500. Диаметр нагревателя 29 мм, мощность 9,45 кВт, температура нагрева 125 °С, давление среды 15 МПа. Технология спуска не отличается от принятой для спуска глубинного манометра.
3. Применение над- и поднасосных нагревателей индукционного типа, монтируемых на приеме насоса или над ним и работающих одновременно с насосом.
Особенностью технологии является использование силового кабеля от погружных центробежных насосов для подачи напряжения к индукционному нагревателю. Спуск кабеля производится по технологии, принятой для УЭЦН.
Дозированная подача в затрубное пространство химреагентов может осуществляться как автономными дозировочными насосами, так и насосами с приводом от станка-качалки.
Инженерами объединения была разработана схема монтажа насоса-дозатора (рис. 7.22), которая включает тягу 3 и кривошип 10, связанные с балансиром СК и сообщающие поршню насоса возвратно-поступательное движение. Реагент из емкости 2 через линию 9 подается в затрубное пространство 8 скважины.
Рис. 7.22. Устьевой дозатор с приводом от СК:
1 - приемный трубопровод; 2 - емкость с ингибитором; 3 - крепление тяги к балансиру СК; 4 - катушка; 5,6,7- задвижки; 8 - линия перепуска жидкости в затрубное пространство; 9 - нагнетательная линия; 10 - кривошип; 11 – насос-дозатор
При использовании химреагентов, вязкость которых повышается при снижении температуры, предусматривается в емкости для реагентов монтировать змеевик, сообщающийся с рабочим манифольдом скважины. Это позволит поддерживать в емкости температуру добываемой жидкости.
Проведенный анализ показал, что многие из дозаторов известных типов не отвечают главным условиям их применения в скважинах - простоте, надежности и экономичности.
Так, основным недостатком дозаторов, работающих за счет деформации насосно-компрессорных труб, являются сложность конструкции, необходимость посадки корпуса дозатора с помощью якоря, что само по себе является трудоемкой операцией. При этом не исключаются повреждение обсадной колонны и заклинивание дозатора вместе с насосом.
Дозаторы гидростатического типа дозируют реагент независимо от работы насоса, т.е. непрерывно, что делает неэкономичным их применение, особенно в периодически работающих скважинах.
Дозаторы так называемого эжекторного типа труднорегулируемы.
На нефтяных месторождениях Башкортостана и Татарстана в последние годы внедряются скважинные дозаторы новой конструкции, совмещенные со штанговым насосом вставного и невставного типов.
Конструктивной особенностью описываемого дозатора, отличающей его от известных, является совмещение всасывающего клапана насоса с дозирующим узлом дозатора. Это обеспечивает его синхронную работу с насосом и дозировку реагента только при работе последнего. Для этой цели была изменена конструкция всасывающего клапана насоса: вместо шара была применена тарелка со штоком, который выполняет функцию плунжера дозирующего узла.
Использование дозирующего узла только в период работы насоса делает дозатор весьма экономичным и увеличивает межремонтный период его эксплуатации.
Механические методы в скважинах, эксплуатируемых ШСНУ, получили воплощение в виде скребков различной конструкции, укрепляемых на колонне штанг. Вначале это были фигурные скребки, изготовляемые из насосно-компрессорных труб или листовой стали длиной 240-250 мм. Скребки укреплялись на штангах хомутами с интервалом между центрами их расположения, равным длине хода. Скребки оказались ненадежными в эксплуатации: сминались при транспортировке, перемещались по колонне штанг, значительно утяжеляли колонну.
Применяются пластинчатые скребки со штанговращателями, представляющие собой пластину со скошенными концами, выполняемую из листовой стали толщиной 2,5-3,0 мм и длиной 450-500 мм, укрепляемую на штангах хомутами. Все скребки на штангах крепились в одной плоскости.
Очистка труб от парафина производилась торцевой поверхностью при повороте скребка на некоторый угол и одновременном перемещении колонны штанг вниз. Вращение колонны штанг со скребками осуществляется штанговращателем, представляющим собой диск с выполненными на его поверхности зубьями (рис. 7.28). Диск крепится на полированном штоке и получает крутящий момент от движителя, рычаг которого взаимодействует с упором, установленным на устье скважины.
|
|
За один ход полированного штока штанговращатель поворачивает колонну на определенный угол, значение которого пропорционально количеству зубьев. От обратного поворота колонну штанг предохраняет стопор.
Трубы с покрытиями в скважинах, эксплуатируемых ШСНУ, получили ограниченное применение. Это объясняется весьма напряженными условиями работы, которые выражаются в следующем:
§ вследствие механического контакта колонны штанг с трубами покрытие истирается;
§ при возвратно-поступательном движении штанг возникают знакопеременные нагрузки на НКТ, которые вызывают разрушение покрытия.
Билет 11 3. Методы защиты нефтепромыслового оборудования от коррозии в ОАО "Оренбургнефть" .
Стальные резервуары подвержены внешней и внутренней коррозии. Внешняя коррозия, в свою очередь, делится на почвенную и атмосферную.
Почвенной коррозии подвергается днище резервуара, находящееся в контакте с грунтом, а корпус и крыша резервуара – атмосферной коррозии, которая не бывает интенсивной, и ее предотвращают нанесением на наружную поверхность различных красок. Эти покрытия должны быть прочны и водонепроницаемы с тем, чтобы вода не проникала под слой краски и не вызывала электрохимического процесса разрушения. Коррозия днищ резервуаров зависит от химического состава грунтов и их влажности. Днища резервуаров защищают от коррозионного разрушения двумя методами: нанесением на внешнюю сторону днища битумной изоляции и созданием изолирующего слоя, а против агрессивного действия грунтовых вод применяют катодную и протекторную защиту.
Внутренняя коррозия резервуаров является более интенсивной, особенно в присутствии влажного воздуха и сернистых соединений, содержащихся в нефти. В этих условиях быстро выходит из строя крыша резервуара, которая постоянно контактирует с газовоздушной смесью.
Сероводород в присутствии кислорода воздуха образует серную кислоту и сульфиды железа, вызывающие иногда самовозгорание и воспламенение нефтепродуктов. Для устранения контакта газа и кислорода воздуха с металлом крыш и корпусом резервуара внутреннюю поверхность их покрывают различными металлическими и пластмассовыми покрытиями, стойкими к воздействию нефти и легких углеводородов.
Пластовая вода, осаждающаяся на дне резервуаров, содержит различные соли, являющиеся хорошими электролитами. Металл днища резервуаров, как правило, неоднороден по составу, и в присутствии электролита отдельные части листов, обладая различными потенциалами, образуют гальванопары, являющиеся источниками электрохимической коррозии днищ. Интенсивность
Коррозионному разрушению днищ в значительной степени способствует также подогрев нефти и пластовой воды, содержащихся в резервуарах.
Для защиты резервуаров от коррозии в ОАО "Оренбургнефть" широко используются следующие методы: периодическое добавление в подтоварную воду щелочей, нейтрализующих кислоты; нанесение покрытий из красок и лакокрасок; применение ингибиторов коррозии; протекторная защита. Однако ни один из перечисленных методов защиты, используемых в отдельности, не дает гарантий невыхода из строя резервуара по причине коррозии. Поэтому на практике применяется комплекс мер, включающий использование комбинаций из перечисленных методов.
В нефтепромысловой практике для снижения коррозионной агрессивности воды по отношению к металлу широко используют следующие методы:
§ исключение контакта пластовой сточной воды с кислородом воздуха;
§ введение в воду ингибиторов коррозии;
§ изоляцию поверхности труб и оборудования различными материалами;
§ обескислороживание воды;
§ применение материалов, стойких к коррозии в пластовых водах;
§ применение неметаллических труб и изделий отдельных узлов оборудования.
В основном осуществляется защита трубопроводов с применением ингибиторов коррозии. Ежегодно разрабатывается и внедряется специальная программа ингибиторной защиты нефтепромыслового оборудования и трубопроводов от коррозии. Программа включает в себя сбор промысловой информации, проведение лабораторных экспериментов и опытно-промысловых испытаний, выбор объектов для защиты оборудования от коррозии, выбор марки ингибитора, его удельного расхода и объема обрабатываемой воды. В процессе проведения опытно-промысловых испытаний отрабатывается режим закачки, уточняются оптимальные дозировки ингибитора и с учетом технологических особенностей реагентов определяется точка ввода ингибитора в поток воды.
Нефтяной газ не обладает коррозионной активностью, но его активность резко возрастает при наличии в нем сероводорода, диоксида углерода, кислорода, жидкого конденсата и, особенно, влаги. Появление жидкого конденсата в газопроводе сырого нефтяного газа объясняется двумя причинами: выносом жидкости из сепарационных узлов и конденсацией углеводородов газа и водяных паров. Конденсация происходит при снижении температуры при его перекачке по газопроводу, который имеет температуру грунта. Особенно повышается выделение конденсата зимой. Выделившийся конденсат создает в трубопроводе жидкостные пробки и пену. Возникают зоны периодического смачивания поверхности трубопровода высококоррозионной средой, которая содержит песок, механические примеси, сульфид железа, сероводород. Кроме общей коррозии возникают язвенная и ручейковая коррозии. При этом материал трубы подвергается сульфидному растрескиванию. Заметное влияние на степень коррозионной активности процессов оказывает характер трассы трубопровода.
При выборе способа защиты газопровода от коррозии руководствовались соображениями доступности и эффективности. Внутреннюю окраску трубопровода или ингибирование с помощью поршней нельзя осуществить из-за того, что весь газопровод был выполнен из спирально-шовных труб. Для данного случая эффективным оказался способ впрыскивания ингибитора в газопровод с помощью форсунок. Ингибитор в виде аэрозоли с потоком газа перемещается внутри газопровода и осаждается на его стенках. Установлено, что при этом толщина пленки ингибитора, образующегося на стенках трубопровода, снижается по мере удаления от точки ввода по экспоненциальному закону. Исходя из этого были рассчитаны количество и места ввода ингибитора.
При движении водогазонефтяных смесей по выкидным линиям и перекачке по нефтепроводам происходит скопление агрессивной воды на пониженных участках трубопроводов и создаются реальные возможности интенсивных коррозионных разрушений. Эта интенсивность также зависит от накопления механических примесей. Рыхлый осадок сульфида железа выделяется из среды и постепенно накапливается на поверхности металла и вместе с другими примесями (песок, глина) образует гальваническую пару. В результате происходит интенсивная локальная коррозия. Для удаления скопившейся внутри труб воды и осадков через них периодически пропускают скребки, что
значительно продлевает срок службы трубопроводов. Защита выкидных линий добывающих скважин при помощи ингибиторов коррозии затруднена, так как каждую скважину пришлось бы снабжать установками для закачки ингибитора. Поэтому основными направлениями борьбы с коррозией в выкидных линиях скважин стало использование коррозионно-стойких материалов.
Замена стальных труб на пластмассовые приводит к суммарному снижению затрат при строительстве трубопроводов до 20 % за счет увеличения скорости монтажа, использования легких землеройных машин. При применении пластмассовых труб увеличивается пропускная способность трубопровода на 30 – 40 %, возрастает срок эксплуатации в четыре-пять раз.
13.1
§ проникновением в ПЗП фильтрата бурового раствора или воды при первичном вскрытии пласта;
§ прорывом посторонних пластовых слабоминерализованных вод в продуктивный пласт.
Ухудшение проницаемости ПЗП происходит и по другим причинам, а именно:
ü при контакте пресной воды с некоторыми минералами может произойти обмен основных радикалов, разложение минералов, перераспределение зерен и перекрытие фильтрационных каналов;
ü при большом объеме проникшего в ПЗП фильтрата возможны растворение, перенос и переотложение солей, а также их отложение из высокоминерализованного фильтрата;
ü при разбуривании вышележащих пород в глинистый раствор могут попасть глинистые частицы минералов с высокой степенью разбухания.
В химически обработанном растворе они медленно разбухают. После вдавливания указанных частиц в поры или трещины призабойной зоны пласта происходят полное разбухание и значительное увеличение их размеров, в результате чего они не могут быть вымыты из пор. Таким образом, возникает закупоривание пор, нередко до полного перекрытия фильтрационных каналов. Ухудшение проницаемости ПЗП, степень которой колеблется от 5-10 до сотен процентов, как правило, происходит из-за одновременного действия нескольких причин.
проникновение в продуктивный пласт нижних высокотемпературных и сильноминерализованных вод и последующее охлаждение их, способствующее отложению солей и ухудшению проницаемости призабойной зоны.
При смешении воды из ЖГС с пластовой водой создаются условия для нарушения химического равновесия и выпадения твердых осадков в порах пород ПЗП, тем самым существенного увеличения фильтрационного сопротивления при движении флюидов. При этом возможна частичная закупорка перфорационных отверстий кристаллами солей. Вероятность выпадения солей в ПЗП достаточно велика из-за нарушения химического равновесия при смешении разных вод и изменении термодинамических условий.
Таким образом, использование для заводнения нефтяных залежей пресных вод с повышенным содержанием сульфат-ионов приводит также к образованию попутно добываемых вод, насыщенных сульфатом кальция.
13.2
13.3 Определение коэффициента продуктивности скважины, оборудованной ШСНУ, методом динамометрирования [132]
Определение коэффициента продуктивности малодебитной скважины, оборудованной ШСНУ, методом пробных откачек осложняется невозможностью спуска глубинных манометров для измерения забойного давления при заданных режимах работы скважины. С достаточной точностью для решения промысловых задач в таких случаях коэффициент продуктивности может быть определен по динамограммам, снятым на двух режимах работы скважины.
Известно, что в конце хода вверх сальникового штока на головку балансира станка-качалки действует максимальная статическая нагрузка
, (6.25)
где Gш - нагрузка от веса колонны штанг в жидкости; Gж -нагрузка от веса столба жидкости в НКТ; Gтр - силы трения; Gпогр - сила, действующая на плунжер насоса снизу и обусловленная погружением насоса под динамический уровень жидкости.
При этом допускается, что плотность откачиваемой жидкости в процессе динамометрирования не изменяется и силы трения постоянны.
При принятых условиях значение Gвmax в процессе исследования изменяется в зависимости от давления на приеме насоса Рпр, так как сумма трех первых слагаемых (6.25) в этом случае остается постоянной. Тогда
, (6.26)
или, выразив Gпогр через давление на приеме насоса, получим
, (6.27)
где fп - площадь плунжера ШГН.
Таким образом, если изменить режим откачки, то изменение забойного давления будет равно разности давлений на приеме насоса при работе на двух режимах. В связи с этим при справедливости линейного закона фильтрации жидкости в скважину коэффициент продуктивности с учетом принятых допущений можно определить по формуле
, (6.28)
где Gв max 2, Gв max 1 - статические нагрузки в точке подвеса штанг в конце хода вверх на разных режимах работы скважины, определенные при кратковременной остановке СК в крайнем верхнем положении головки балансира.
Процесс исследования скважины заключается в следующем:
§ устанавливают минимально возможный режим работы скважины;
§ при достижении установившегося режима работы снимают динамограмму, записывают нулевую линию, линию нагрузки от веса штанги и линию статической нагрузки в крайнем верхнем положении балансира при кратковременной остановке станка-качалки;
§ изменяют режим работы скважины в 1,5 - 2 раза и по достижении установившегося режима работы повторяют операции, предусмотренные п. 2.
При снятии динамограмм необходимо соблюдать следующие условия:
· линию нагрузки от веса штанг Gш записывать в положении, когда точка подвеса штанг не перешла нижнюю "мертвую" точку;
· линию максимальной статической нагрузки Gв max записывать в положении, когда точка подвеса штанг не перешла верхнюю "мертвую" точку.
14.1 Причины отложения карбоната кальция и магния
Карбонат кальция (кальцит) СаСО3 – осадок, часто встречаемый в нефтепромысловой практике. Растворимость его в дистиллированной воде очень невелика. При температуре 25 °С и контакте с атмосферным воздухом она составляет 0,053 г/л, что примерно в 40 раз меньше растворимости гипса. Растворимость кальцита с повышением температуры существенно уменьшается (рис. 9.6). Поэтому по мере повышения температуры возможность отложения СаСО3 увеличивается. Влиянием температурного фактора можно объяснить образование карбонатных осадков в некоторых глубоких нагнетательных скважинах с высокой пластовой температурой, куда закачивается вода, насыщенная карбонатом кальция в поверхностных условиях. Этим же обусловлено образование накипи на поверхности нагревателей водонефтяных эмульсий, в теплообменниках и т.д.
Таким образом, снижение давления в системе газ – вода, приводящее к соответствующему снижению парциального давления СО2, может быть одной из причин уменьшения растворимости кальцита и выпадения его в осадок. Именно этот процесс вызывает частое отложение кальцита на стенках НКТ в добывающих скважинах выше глубины начала разгазирования нефти или выше точки ввода газа в НКТ в газлифтных скважинах
Если из попутных вод выпадают и сульфатные, и карбонатные соли, то обычно наблюдается четкая локализация осадков: в НКТ, особенно в нижней половине скважины, преобладают сульфаты кальция и бария, а в наземных сооружениях отлагаются углекислые соли кальция и отчасти магния.
14.2 Тепловые методы основаны на повышении температуры в стволе скважины
(в месте начала гидратообразования) или сборном трубопроводе выше критической и поддержании ее в течение длительного времени.
Известны несколько способов решения этой проблемы. Например, для газовых скважин можно установлением количества отбора газа добиться такого режима, когда температура на устье станет несколько выше его температуры в области призабойной зоны. Увеличение дебита до определенного предела ведет к сокращению времени пребывания газа в стволе скважины и уменьшению его теплоотдачи. Однако таким условиям удовлетворяет определенный режим, так как дальнейшее увеличение дебита ведет к снижению температуры за счет дроссель-эффекта.
Можно создать необходимую температуру за счет экзотермической реакции путем смешивания пятихлористого фосфора РСl5 с водой:
2РС15 + 8Н2О -» 2Н3РО4 + 10НС1 + 514 Дж.
Однако поддерживать постоянно необходимую температуру по данной технологии сложно: здесь речь может идти о периодическом воздействии. Существуют также технологии, предусматривающие периодическую прокачку теплоносителя через скважину агрегатами депарафинизации.
На практике тепловые методы получили применение для борьбы с гидратообразованием в газопроводах путем подогрева газа устьевыми подогревателями и использования теплоизолированных труб.
14.3 Определение коэффициента продуктивности скважины методом прослеживания уровня жидкости
При совместной работе скважины и пласта на установившемся режиме в кольцевом пространстве между обсадной колонной и НКТ устанавливается практически постоянный динамический уровень жидкости. Если насосную установку остановить, то приток жидкости из пласта продолжается и происходит заполнение скважины. При этом поступление жидкости происходит на нестационарном режиме фильтрации, так как увеличение высоты столба жидкости в скважине приводит к возрастанию забойного давления.
Считая в каждый фиксированный момент времени режим установившимся и используя метод последовательной смены стационарных состояний, приток жидкости в скважину можно рассчитать по формуле Дюпюи, записанной в виде
, (6.29)
где Q(t) - изменяющийся во времени приток жидкости в скважину после ее остановки; Pк - давление на контуре питания пласта, для группового размещения добывающих скважин приравниваемое к динамическому пластовому давлению; Рc(t) -переменное во время заполнения скважины жидкостью забойное давление; Rк - радиус контура питания, принимаемый равным половине расстояния между соседними скважинами а, rс пр - приведенный радиус скважины, значение которого рассчитывается по паспортным данным скважины и графикам В.И. Шурова; остальные обозначения прежние.
Выражая пластовое и забойное давления через напоры столба жидкости, уравнение (6.29) запишем в виде
, (6.30)
где Нк - статический столб жидкости на контуре питания; Hc(t) - столб жидкости в скважине в заданный момент времени; ρ, g - соответственно плотность жидкости и ускорение свободного падения. Дебит скважины в любой момент времени после прекращения работы насоса
, (6.31)
F - площадь сечения обсадной колонны с внутренним диаметром D. Приравнивая левые части уравнений (6.30) и (6.31), получаем
. (6.32)
Разделив переменные в уравнении (6.32) и определив интервалы интегрирования по t и Нс, можно записать
. (6.33)
Интегрируя уравнение по t от нуля до t и по Нс от Нсо до H(t), получаем
, (6.34)
Здесь Нсо - динамический столб жидкости перед остановкой скважины.
Учитывая, что комплекс 2nkh/μln(a/rcпр) представляет собой коэффициент продуктивности скважины, можно записать
. (6.35)
Выражение (6.28) представляет собой уравнение прямой в координатах lnφ и t, где φ = [Нк - Hc(t)]/(Hк - Нс о).
Для обработки данных исследований скважины Нк определяют по результатам измерения статического уровня жидкости после полной ее стабилизации, т.е. полного восстановления забойного давления, приравниваемого к текущему динамическому пластовому давлению.
Итак, обработка данных исследования скважины сводится к следующему:
· по данным наблюдений за изменением динамического уровня жидкости в скважине строят график в координатах lnφ и t (рис. 6.9);
· на графике по произвольно выбранным двум точкам определяют lnφ1 и lnφ2 для заданных t1 и t2;
· рассчитывают значение тангенса угла α по формуле
; (6.36)
· по значению tgα рассчитывают коэффициент продуктивности скважины
. (6.37)
и значения коэффициента проницаемости k, подвижности нефти k/μ и гидропроводности kh/μ.
Некоторыми неудобствами рассматриваемого способа расчета является необходимость иметь для обработки данных исследования скважин значения статического уровня жидкости, соответствующие динамическому пластовому давлению. Для получения этого параметра необходимо дождаться полного восстановления давления после остановки скважины. В малодебитных скважинах восстановление пластового давления в условиях низкопродуктивных коллекторов, насыщенных
Рис. 6.9. К обработке кривых прослеживания уровня жидкости в скважине после ее остановки
вязкими нефтями, требует значительного времени простаивания скважины (месяц и более).
Для сокращения времени в БашНИПИнефти разработана методика обработки данных исследования методом прослеживания уровня жидкости, ускоряющая процесс изучения скважин в несколько раз. Приведем основные моменты этой методики.
15.1 Определение коэффициента продуктивности скважины по неполным кривым восстановления уровня жидкости в скважине (забойного давления)
Метод заключается в снятии неполных кривых восстановления уровня (давления) по исследуемой скважине после ее остановки. Неполные кривые снимаются на участке активного восстановления уровня (давления). Конечное значение пластового давления (статического уровня) определяется способом аппроксимации.
Исследования скважин при неустановившемся режиме фильтрации жидкости способом снятия неполной кривой восстановления пластового давления проводятся в следующем порядке.
1. Перед началом исследования в скважину спускается через затрубное пространство глубинный манометр, и после 1-2 ч работы скважина останавливается на восстановление пластового давления. В случае невозможности спуска в скважину манометра более тщательно отбивается динамический уровень жидкости в затрубном пространстве или путем спуска прибора в НКТ.
2. Периодически в течение 1- 8 сут ведется замер роста давления в скважине.
3. После 1- 8 сут наблюдения за восстановлением давления исследование прекращается и скважина вводится в дальнейшую эксплуатацию.
4. Во время исследования во избежание накопления газа затрубное пространство скважины должно быть открытым на факельную линию или организован принудительный отбор газа.
По полученным данным строится усредненная неполная кривая восстановления пластового давления (статического уровня). Выбор способа обработки данных замеров производится из следующих соображений. Считается, что положение Рк (статического уровня жидкости) неизвестно.
После преобразования уравнения (6.32) получим
. (6.38)
Графический анализ уравнения (6.38) показывает, что при значениях Нкi ≠ Нк ≠ const оно является уравнением некоторого семейства кривых, которые при Нкi → Нк → const стремятся преобразоваться в прямую линию (рис. 6.10).
Следовательно, перестраивая неполную кривую восстановления уровня (забойного давления) в координатах ln[Hкi - Hc(t], t при различных задаваемых значениях Hкi ≤ Нк, необходимо добиться такого значения Нкi, когда рассматриваемое семейство кривых трансформируется в прямую линию типа у = b - ах. При этом будет достигнуто равенство Hкi = Нк и будет определено значение динамического пластового давления в районе расположения исследуемой скважины.
Дальнейшая обработка замеров ведется по приведенному ранее методу прослеживания уровня жидкости в скважине.
Угловой коэффициент этой прямой согласно выражению (6.38)
, (6.39)
а отрезок, отсекаемый прямой на оси ординат,
. (6.40)
Из формулы (6.38) коэффициент продуктивности скважины
. (6.41)
Из графика (см. рис. 6.10) угловой коэффициент
. (6.42)
Рис. 6.10. К обработке данных исследования скважин по ускоренному методу
Значения φ1 и φ2 определяются по графику (см. рис. 6.10) при Ркi = Pк для двух произвольно взятых точек, соответствующих значениям t1 и t2.
По известному значению коэффициента продуктивности скважины можно рассчитать основные фильтрационные характеристики ПЗП: коэффициент проницаемости, подвижность нефти и гидропроводность пласта.
15.2Гидратообразование в системе сбора нефти
Выкидные линии скважин
Гидратные пробки могут образовываться также и в выкидных линиях скважин, условиями для этого являются:
· изменение давления от устья скважины до сепаратора первой ступени, связанное с обычными гидравлическими потерями, а также прохождением штуцеров;
· изменение температуры из-за теплоотдачи.
На Зайкинском месторождении в выкидных линиях поддерживается давление 5,5 - 6,0 МПа, а температура при ритмичной работе колеблется от 8 до 16 °С в зависимости от времени года.
Гидратообразование по фазовым диаграммам для нефти пластов Д-1П, Д-IV возможно при давлении 6,0 МПа и температуре 17,5 ºС, реальное образование пробок при переохлаждении продукции может произойти при температуре 11,5 ºС.
Для газоконденсатной смеси пласта Д-IV расчетный режим гидратообразования возможен при 18,5 ºС, реальное пробкообразование может возникнуть при температуре 14,5 ºС, т.е. практически в течение всего года.
При увеличении давления в сепараторе первой ступени до 10 МПа температура возможного гидратообразования для нефти повышается до 15 "С, а для газоконденсатной смеси - до 17 ºС, что соответствует значению среднегодовой температуры в выкидной линии. Это значит, что образования гидратных пробок следует ожидать в любое время года и необходимо разработать постояннодействующие мероприятия по борьбе с ними.
На Росташинском месторождении давление в сепараторах первой ступени равно 2,9 - 3,0 МПа, а в линиях - 3,5 - 4,0 МПа, что соответствует расчетной температуре гидратообразования 12,5 ºС, и на 6 °С меньше реальной температуры, т.е. 6,5 ºС. Эта температура несколько ниже минимальной для возможного гидратообразования, поэтому пробкообразование маловероятно.
Дата добавления: 2020-01-07; просмотров: 443; Мы поможем в написании вашей работы! |
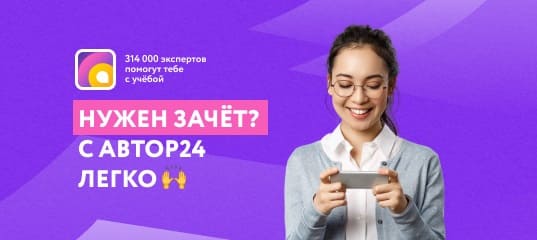
Мы поможем в написании ваших работ!