Диагностирование гидравлической системы трактора
Задание 5
Испытание и регулировка агрегатов системы охлаждения, системы смазки двигателей тракторов автомобилей и самоходных сельскохозяйственных машин.
Водяной насос двигателей внутреннего сгорания грузовых автомобилей и тракторов (типа СМД, А-01М, ЯМЗ, Д-50 и др.).
Дефекты, повреждения, отказы: трещины в корпусе, срыв резьбы в отверстиях, износ посадочных мест под подшипники и упорную втулку, износ посадочного места на валике под крыльчатку, износ боковой поверхности лопаток, износ поверхностей у валиков в сопряжении со втулками, сальниками и шкивами вентиляторов.
Трещины в чугунных корпусах заваривают газовой сваркой латунными прутками, припоями ЛОК и ЛОМНА и электродуговой сваркой порошковой проволокой ПАНЧ-11. Срыв резьбы исправляют постановкой резьбовых вставок и другими способами, характерными для восстановления резьб.
Изношенные посадочные места корпуса под подшипники и упорную втулку могут быть восстановлены путем отрезания части корпуса с последующими запрессовкой и приваркой вновь изготовленной части или запрессовкой колец с последующей механической обработкой посадочных мест до номинальных размеров. Торцевую поверхность опорной втулки и уплотнительную поверхность шайбы сальника притирают.
При износе крыльчатки старую ступицу отрезают, изготавливают и запрессовывают новую и стопорят двумя штифтами. Изношенные лопатки крыльчатки наплавляют газовой сваркой чугунными прутками и протачивают до требуемой высоты. Крыльчатки можно изготавливать литьем из алюминиевого сплава или капрона. При этом втулка ступицы должна быть стальной.
|
|
Изношенные поверхности у валиков восстанавливают наплавкой в среде углекислого газа с последующим хромированием и шлифованием.
После ремонта крыльчатку водяного насоса в сборе с валиком подвергают статической балансировке.
Водяные насосы обкатывают и испытывают на специальном стенде (например, насосы двигателей ЯМЗ-240Б на стенде ОР-8899). У насосов проверяют соответствие техническим требованиям величины зазора между корпусом и торцом крыльчатки, а также величины осевого разбега валика.
Обкатку насоса производят в течение 3 мин при температуре воды 85…90 0С, измеряют производительность насоса, сравнивают с нормативной.
Каждый отремонтированный насос проверяют на герметичность при давлении 0,07…0,12 МПа в течение 1 мин без вращения и с вращением валика. Подтекание воды не допускается.
Вентиляторы
Дефекты, повреждения, отказы: износ посадочных мест в шкивах под наружные кольца подшипников качения; износ ручьев в шкивах под ремень; ослабление заклепок на крестовине, изгиб крестовины и лопастей.
|
|
Изношенные посадочные места восстанавливают постановкой колец или железнением с последующей механической обработкой.
Изношенные ручьи в шкивах под ремень вентилятора (до 1 мм) протачивают.
Ослабленные заклепки на крестовине лопастей подтягивают. Овальные отверстия под заклепки рассверливают и лопасти приклепывают заклепками увеличенного диаметра. Кромки лопастей вентилятора должны лежать в одной плоскости, допускаемое отклонение от плоскостности 1 мм.
При необходимости крестовину и лопасти правят. Шаблоном проверяют форму лопастей вентилятора и угол их наклона относительно плоскости вращения (этот угол, например, для лопастей вентилятора двигателей типа СМД-14 у основания лопасти – 320, на конце – 240).
Собранный со шкивом вентилятор балансируют на настольном балансировочном стенде, при этом допускается сверлить углубления в торце чугунного шкива вентилятора или утяжелять лопасть с ее выпуклой стороны приваркой или приклеиванием пластинки.
Радиаторы
Основные дефекты, повреждения, отказы: отложение накипи на внутренних стенках резервуаров и трубок, механические повреждения их.
|
|
Радиатор промывают в ванне с 4%-м раствором соляной кислоты с добавкой ингибитора ПБ-5 до 3 г/л. Температура раствора 50…70 0С, время промывки 10…15 мин. Затем радиатор промывают в щелочном растворе СМС, в воде и испытывают в собранном виде. Отверстия в резервуарах радиатора закрывают резиновыми пробками. Радиатор заполняют водой, создают насосом избыточное давление: в течение 3…5 мин радиаторы не должны давать течи (радиаторы тракторов испытывают при давлении 0,05…0,10 МПа; трактора К-700 – 0,10…0,14 МПа). Можно радиаторы испытывать в ваннах с водой под соответствующим давлением воздуха. При ремонте радиатор разбирают. Трубки радиатора прочищают шомполом. Сердцевину испытывают отдельно на стенде КП-2002, создают давление не менее 0,10 МПа и определяют место течи.
При отсутствии стенда сердцевину помещают в ванну с водой, подавая воздух по шлангу от ручного насоса в каждую трубку, по пузырькам находят место повреждения.
Поврежденные трубки внешних рядов сердцевины запаивают припоем ПОС-30. Поврежденные трубки внутренних рядов заглушают (запаивают) с обоих концов. Допускается заглушить до 5% трубок, при большем проценте трубки заменяют, для этого трубки отпаивают от опорных и охлаждающих пластин с помощью горячего воздуха, нагреваемого до 500…600 0С паяльной лампой через укрепленный на ней змеевик. Трубку извлекают пассатижами с язычком, соответствующим сечению отверстия трубки.
|
|
Для отпайки трубок можно применять шомпол, нагретый до 700…800 0С в горне или электрическим током от сварочного трансформатора. Извлекают трубки по направлению усиков охлаждающих пластин, иногда необходимо отпаивать и снимать одну из опорных пластин.
Установленные трубки развальцовывают и припаивают к опорным пластинам специальным паяльником припоем ПОС-30, используя в качестве флюса хлористый цинк (цинк, травленный соляной кислотой).
Кроме замены поврежденных трубок существует способ ремонта их гильзованием. В расширенную трубку за счет протаскивания лебедкой уширенного на конце шомпола вставляют новую и припаивают по концам к опорным пластинам.
После ремонта сердцевину радиатора испытывают на герметичность, как и перед ремонтом.
Количество вновь установленных и гильзованных трубок у сердцевин не должно превышать 20…25%.
Трещины чугунных резервуаров радиаторов заваривают электродуговой сваркой биметаллическим электродом или проволокой ПАНЧ-11, газовой сваркой латунными прутками или пайкой.
У резервуаров из латуни трещины устраняют пайкой припоем ПОС-30, в том числе припайкой заплат.
Ремонт масляных радиаторов аналогичен ремонту водяных. Смолистые отложения удаляют промывкой препаратом АМ-15, испытывают под давлением 0,3 МПа, трубки припаивают к бакам твердым медно-цинковым припоем ПМЦ газовой сваркой.
Термостаты
Накипь удаляют растворами, применяемыми при промывке водяных радиаторов. Поврежденные места пружинной коробки запаивают припоем ПОС-40, применяя в качестве флюса канифоль. Пружинные коробки заполняют 15%-м раствором этилового спирта. Наполнителями могут быть порошок алюминия и церезин (парафин).
При испытании термостата в ванне с подогреваемой водой начало открытия клапана должно быть при 70 0С, а полное открытие при 85 0С. Величина полного подъема клапана 9,0…9,5 мм. При необходимости регулируют высоту подъема клапана, вращая его на резьбовом конце хвостовика пружинной коробки термостата.
Накипь в системе охлаждения образуется при жесткой воде. Жесткость измеряется в миллиграмм-эквивалентах на 1 л воды. Различают жесткость воды: временную, постоянную и общую. Временную образуют бикарбонаты кальция Ca(HCO3) и магния Mg(HCO3)2, которые распадаются при кипячении на карбонаты и газовые составляющие. Постоянную жесткость придают, например, наиболее чаще встречающиеся, карбонаты кальция (CaCO3) и магния (MgCO3), которые могут быть удалены растворами, в том числе на основе соляной кислоты (HCl). При этом различают мягкую воду, средней жесткости, жесткую воду и очень жесткую, содержащую в одном литре более 12 миллиграмм-эквива-лентов (1 мг-эквивалент соответствует 20,04 мг Ca или 12, 16 мг Mg). Мягкая вода содержит 4 мг-эквивалентов, жесткая – 8…12 мг-эквивалентов в каждом литре.
Масляный насос. Дефекты, повреждения, отказы: износ корпуса насоса в местах сопряжений с торцами шестерен, износ стенок корпуса около всасывающих отверстий и вершин зубьев шестерен; износ плоскостей крышек (проставок) и торцевой поверхности шестерен; износ поверхностей валиков, осей втулок; потеря герметичности клапанов; наличие трещин; срыв резьбы и износ шлицев у валиков.
Снижение производительности масляных насосов вызывается увеличением торцевого зазора между шестернями и крышками (проставками), который можно замерить по осевому перемещению ведущего валика с помощью приспособления, состоящего из стойки с индикатором часового типа. Для дизельных двигателей нормальный зазор в пределах 0,06…0,17 мм (для отдельных 0,07…0,22 мм), а допустимый без ремонта – 0,25 мм (для отдельных: типа А-01М, СМД-60 до 0,30 мм).
Если гнездо по высоте в корпусе изношено и больше высоты новых шестерен, то торцевую поверхность у корпуса можно подрезать, прошлифовать и профрезеровать, в том числе с использованием приспособления для токарной обработки корпуса масляного насоса.
С использованием этого же приспособления можно обработать цилиндрическую поверхность гнезд корпуса (например, до и после железнения или цинкования) или расточить отверстие под втулку.
Трещины и изломы корпуса можно устранить горячей газовой заваркой, а также электродуговой сваркой порошковой проволокой ПАНЧ-11 или постановкой фигурных вставок.
Изношенные бронзовые втулки восстанавливают термодиффузионным цинкованием. При замене их развертывают в корпусе и крышке совместно под нормальный или увеличенный размер валика.
Изношенные поверхности крышек и проставок, сопряженные с торцами шестерен, восстанавливают шлифованием или фрезерованием с последующим контролем на плите. Допускается неплоскостность до 0,03 мм на 100 мм длины. При необходимости крышки (проставки) пришабривают.
Потерю герметичности плунжерных клапанов устраняют исправлением формы гнезда с постановкой увеличенного клапана и последующей совместной притиркой. Шариковые клапаны в насосах и масляных фильтрах заменяют, а фаску гнезда исправляют сверлом или конической зенковкой. После этого клапан устанавливают в гнездо и обчеканивают через латунную наставку. Пружины при потере упругости заменяют.
Изношенные шестерни заменяют новыми. Изношенные посадочные места под втулки восстанавливают железнением или вибродуговой наплавкой пружинной проволокой с последующим шлифованием под нормальный или увеличенный размер.
Изношенные шлицы валиков заплавляют в среде углекислого газа или вибродуговой наплавкой без подачи охлаждающей жидкости, обтачивают на токарном станке и фрезеруют.
Изношенные шпоночные пазы зачищают или фрезеруют под увеличенную по ширине шпонку (при износе более 0,5 мм). Шпоночный паз можно фрезеровать в новом месте.
Изношенные оси ведомых шестерен заменяют новыми (нормального или увеличенного размера). Увеличенная ось может изготавливаться ступенчатой, когда необходимо развертывать отверстие только во втулке ведомой шестерни.
Поврежденный участок сетки маслозаборника запаивают легким припоем или устанавливают на него накладку из такой же сетки и припаивают вокруг. Площадь запаянных участков не должна превышать 10% всей площади сетки.
Масляные насосы испытывают на стенде КИ-5278. Необходимо отметить, что радиальный зазор между вершинами зубьев и корпусом обычно равен 0,12…0,20 мм, а допустимый без ремонта – 0,25…0,30 мм.
Нормальный зазор между валиком и втулками 0,03…0,07 мм, допустимый без ремонта – 0,12 мм.
Ведущий валик должен свободно проворачиваться от руки, а плунжер предохранительного клапана – перемещаться в гнезде под действием собственной массы.
При испытании насоса сначала его обкатывают в течение 6 мин, затем при номинальной частоте вращения коленчатого вала повышают давление до величины срабатывания предохранительного клапана, затем снижают давление до нормального и определяют количество жидкости, подаваемой в бак за 1 мин.
Масляные насосы автомобильных двигателей испытывают на развиваемое давление при прохождении рабочей жидкости через канал соответствующего диаметра и длины.
Масляные фильтры. Дефекты, повреждения, отказы: трещины, обломы корпуса, срывы резьбы, вмятины колпаков, загрязнение фильтрующих элементов.
Для очистки фильтрующих элементов грубой очистки масла их кипятят в течение 3 часов в 10%-м растворе каустической соды, промывают воде и помещают на 24 часа в моющую жидкость АМ-15, а затем промывают в струйных моющих машинах раствором СМС. Большой эффект дает промывка и прочистка фильтров в ультразвуковых ваннах.
После промывки фильтрующие элементы грубой очистки проверяют на пропускную способность (фильтрующие элементы тонкой очистки после загрязнения заменяют). При проверке закрывают пробкой центральное отверстие в наружной крышке фильтрующего элемента, погружают его в емкость с дизельным топливом так, чтобы кромки элемента были выше уровня топлива на 2…3 мм, и определяют время, в течение которого топливо заполняет внутреннюю полость элемента до уровня, отстоящего от верхней кромки на 30 мм. Время заполнения при температуре топлива 20 0С должно быть не более 15…20 с для новых фильтров и 40 с для фильтров, бывших в эксплуатации. Затем фильтр перевертывают крышкой вверх и снова погружают в дизельное топливо. В местах повреждений (вмятины, сдвиг витков, обрыв ленты) будут выходить крупные пузырьки воздуха. Поврежденные места запаивают (но не более 5 см2) оловянно-свинцовым припоем ПОС-30, применяя в качестве флюса канифоль.
В двигателе, где тонкая очистка масла выполняется реактивными масляными центрифугами, при ухудшении работы последних производят ремонт. При этом может быть загрязнение форсунок ротора, накопление отложений внутри самого ротора, износ втулок и оси ротора; трещины, срыв резьбы, негерметичность клапанов; повреждение сетки маслозаборника.
При уменьшении частоты вращения ротора последний разбирают, удаляют накопившиеся отложения, промывают. Отверстия в форсунках ротора прочищают медной проволокой и промывают.
При зазоре между втулками и осью ротора более 0,10…0,15 мм втулки заменяют. После запрессовки втулок их развертывают совместно в корпусе и крышке, обеспечивая зазор 0,016…0,090 мм в зависимости от марки двигателя.
Собранные фильтры испытывают и регулируют на стенде типа КИ-5278, или КИ-9156. При этом проверяется герметичность фильтров, проверяется и регулируется давление открытия клапанов, частота вращения центрифуги. Частота вращения центрифуги может быть проверена прибором КИ-1308В. Для определения частоты вращения ротора центрифуги применяют также стробоскопический тахометр.
Ориентировочно частоту вращения ротора определяют по времени его вращения после выключения стенда (по выбегу). Время выбега должно быть не менее 30…40 с. При соответствующем давлении масла фильтр проверяют на герметичность в течение 1 мин.
Задание 7
Дата добавления: 2020-01-07; просмотров: 553; Мы поможем в написании вашей работы! |
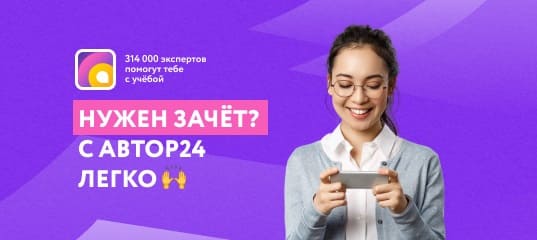
Мы поможем в написании ваших работ!