Механизированная сварка плавящимся электродом
в защитных газах (СО2)
Общие сведения
Механизированная сварка в СО2 является одним из основных способов дуговой сварки, применяемом для изготовления сварных конструкций в основном, в цеховых условиях. Она обеспечивает, в сравнении с ручной дуговой сваркой штучными электродами, высокую производительность сварки, значительную глубину проплавления, связанную с высокими плотностями тока в электроде, уменьшение зоны термического влияния и снижение деформаций. Сварка протяженных швов может производиться без перерывов, что уменьшает, например, количество кратеров и начальных участков отдельных швов, что приводит к повышению качества сварки.
К недостаткам сварки в СО2 можно отнести меньшую маневренность, меньшую доступность к стесненным местам, необходимость газовой защиты, более сложное оборудование, значительные потери электродного металла (10-12%).
Однако эти недостатки при сварке в цеховых условиях для конкретных конструкций могут быть несущественными или могут быть устранены.
Оборудование для механизированной сварки
Механизированной называется сварка с механизированной подачей проволоки или других сварочных материалов в зону плавления и ручным перемещением дуги вдоль линии сварного соединения. Аппараты для механизированной сварки называются полуавтоматами.
Полуавтоматы классифицируют по следующими признакам:
1. По способу защиты зоны сварки: для сварки в защитных газах, под флюсом, без внешней защиты, универсальные.
|
|
2. По типу применяемой электродной или присадочной проволоки: для сварки сплошной стальной (жесткой) проволокой, проволокой из алюминиевых сплавов (мягкой), порошковой проволокой, универсальной.
3. По способу регулирования скорости подачи проволоки: с плавным, со ступенчатым, со смешанным (комбинированным) регулированием.
4. По компоновке: однокорпусные (с механизмом подачи, встроенным в корпус источника питания), с вынесенным подающим механизмом.
5. По транспортабельности: стационарные, с транспортируемым во время работы подающим механизмом.
6. По способу транспортировки подающих механизмов: передвижные, переносные (чемоданного типа), ранцевые, ручные ( с подающим механизмом и катушкой или шпулей проволоки, встроенными в держатель горелки).
7. По способу подачи проволоки: толкающего, тянущего, тянуще-толкающего типа.
8.По способу охлаждения горелки: с естественным (воздушным), с искусственным (водяным или газовым).
Основные элементы сварочных полуавтоматов
В состав сварочного полуавтомата обычно входят: горелка или комплект горелок со шлангами, механизм подачи электродной проволоки, кассета (катушка, шпуля) с электродной или присадочной проволокой, шкаф или блок управления (конструктивно может быть объединен с источником питания), аппаратура для регулирования и измерения параметров системы подачи газов, подогреватель газа, источник питания, шланги, провода сварочной цепи и цепей управления.
|
|
Горелки. В качестве основного параметра горелок принят номинальный сварочный ток, который для механизированной сварки выбирают из стандартного ряда: 125, 160, 220, 315, 400, 500, 630 А.
Горелки могут быть с естественным (воздушным) и искусственным (водяным или газовым) охлаждением. Обычно водяное охлаждение применяют в горелках, рассчитанных на токи выше 400 А.
По характеру взаимного расположения основного корпуса и рукоятки различают горелки молоткового и пистолетного типов. Горелки пистолетного типа удобны для сварки швов на вертикальных поверхностях, а также при сварке проволокой большого диаметра.
Горелки обычно снабжены шлангами (гибкими направляющими каналами) длиной до 3 мм. Для сварки тонкой электродной проволокой (d =0,6-1 мм) и для сварки проволокой из мягких алюминиевых сплавов горелки комплектуются шлангами длиной 1,5-2 м.
Гибкие направляющие каналы полуавтоматов могут быть раздельного и совмещенного (канал в полом сварочном кабеле) типов.
|
|
Направляющие каналы могут быть в виде спирали из стальной проволоки или ленты, а также в виде пластмассовых трубок из тефлона, полиэтилена, нейлона и т.д., которые обычно применяют для подачи проволоки из алюминиевых и коррозионно-стойких сталей.
Механизмы подачи электродной (присадочной) проволоки. Механизмы подачи бывают со ступенчатым механическим, с плавным и со смешенным регулированием скорости подачи.
В механизмах со ступенчатым механическим регулированием в качестве приводного обычно применяют асинхронный трехфазный электродвигатель. Механизмы подачи такого типа просты и надежны в эксплуатации, обеспечивают точное соблюдение режима работы. Изменение скорости подачи электродной проволоки осуществляется сменными шестернями или коробкой скоростей.
Подающие механизмы с плавным регулированием скорости подачи имеют электродвигатели постоянного тока типа СЛ, КПА, КПК, Д-90 с частотами вращения соответственно- 3600, 5500, 8000 мин-1.
Подача электродной проволоки осуществляется в основном роликами. Применяют схему с одним приводным роликом (тонкая стальная проволока), с двумя приводными роликами (стальная проволока диаметром 1,6-2,5 мм) и четырьмя приводными роликами (алюминиевая проволока, порошковая проволока).
|
|
Системы управления. Различают системы управления сварочными полуавтоматами:
а) с асинхронным электродвигателем;
б) с электродвигателем постоянного тока с плавным регулированием скорости подачи проволоки;
в) с электродвигателем постоянного тока с питанием электрической схемы от источника питания дуги.
В настоящей работе рассматривается система управления типа «б».
Система подачи газа. Для подачи защитного газа от баллона или цеховой сети до электромагнитного клапана полуавтомата используются газовые редуктора и расходомеры, которые могут быть объединены в одном приборе редукторе-расходомере. При сварке в СО2 в газовый комплект входит также подогреватель газа, например, редуктор-расходомер со встроенным подогревателем УЗО.
3 Общие вопросы технологии сварки в СО2.
СО2 является наиболее распространенным защитным газом, применяемым при сварке плавящимся электродом. В зоне сварки при высокой температуре СО2 диссоциирует:
Выделяющийся при диссоциации СО2 кислород окисляет жидкий металл с образованием закиси железа FeO , растворимой в жидком металле и ряда нерастворимых оксидов элементов, входящих в состав металла- SiO 2 , MnO , AI 2 O 3 и др.
При взаимодействии FeO с углеродом образуется нерастворимая в металле окись углерода СО, вызывающая образование пористости при сварке.
Окислительная способность углекислого газа растет с повышением температуры. Однако реакцию окисления углерода можно затормозить за счет введения в сварочную ванну элементов-раскислителей (Si , Mn , Т i , А I и др.).
В связи с этим при сварке сталей применяют сварочные проволоки, легированные элементами - раскислителями. Некоторые марки сварочных проволок, применяемых для сварки конструкционных сталей приведены в таблице 1.
Достаточно широкое распространение при производстве сварных конструкций получила механизированная сварка в смеси газов. Смесь 80% СО2+20%О2 обеспечивает более лучшее формирование шва, уменьшает несколько разбрызгивание и повышает плотность металла шва. Обычно такие смеси применяют для сварки низкоуглеродистых и низколегированных сталей. Для сварки низкоуглеродистых и легированных сталей находит применение смесь 75%Аr + 25%CO2, что повышает стабильность горения дуги, снижает пористость металла шва и улучшает формирование швов.
Таблица1- Марки сварочных проволок для сварки в СО2
Свариваемый металл | Марка сварочной проволоки (ГОСТ 2246-70) |
1. Низкоуглеродистые стали Ст1, Ст2, Ст3 | СВ-08ГС, СВ-08Г2С |
2. Легированные стали средней прочности ( ![]() | СВ-18ХГСА, СВ-10ГСМ |
3. Низколегированные стали 10ХСНД, 15ХСНД, 14ХСНД, 09Г2, 14Г2 | СВ-08Г2С (при одно- или двухслойной сварке) СВ-08ХГ2С |
4. Теплоустойчивые стали 20ХМЛ, 15Х1Мф | СВ-08ХГСМФ |
5. Высокохромистые стали 12Х13, 20Х13 | СВ-08Х14ГНТ |
6.Аустенитные стали 12Х18Н10Т, 12Х18Н12Т | СВ-08Х25Н13БТЮ |
Техника сварки. Металл толщиной 1-2 мм сваривают при равномерном поступательном перемещении электрода без поперечных перемещений электрода, за исключением мест, имеющих зазоры. При сварке в нижнем положении стыковых соединений с V-образной или Х –образной разделками кромок (ГОСТ 14771-76) первый слой (корень) шва выполняют равномерным поступательным или возвратно-поступательным перемещением электрода с шагом «а», равным 3-10 мм (рисунок 1а). Средние слои многослойного шва выполняют при перемещении электрода по вытянутой спирали с шагом «а!» равным 4-20 мм при амплитуде поперечных колебаний в=4…15 мм. Верхние слои выполняют змейкой, при этом шаг продольных перемещений «а!!» равен примерно 3-6 мм, а амплитуда поперечных колебаний в=10…30 мм. Шаг перемещений и амплитуда поперечных колебаний зависят от ширины разделки, которая связана с углом разделки, толщиной свариваемого металла и номером слоя шва.
Нахлесточные соединения из металла толщиной до 1,5 мм сваривают вертикальным электродом, перемещая дугу по кромке верхнего листа. При толщине свариваемого металла 2 мм и более наклон электрода и смещение дуги должно быть таким же, как и при сварке тавровых соединений. Сварку угловых швов тавровых соединений производят с наклоном горелки от вертикальной стенки на 30-450 и наклоном горелки к оси шва «углом назад» на 5-150 (рисунок 1б).
Механизированной сваркой в СО2 соединения различного типа можно сваривать во всех пространственных положениях. Обычно применяется электродная проволока диаметром 0,5-1,2 мм. Сварка в положениях, отличных от нижнего, производится, как правило, на пониженном напряжении (17-19 В).
Сварка металла толщиной до 6 мм стыковых соединений, а также угловых швов с катетом до 5-6 мм в вертикальном положении выполняется сверху вниз. В начале процесса сварки электрод располагают перпендикулярно к свариваемым кромкам с целью обеспечения хорошего провара начала шва. После образования сварочной ванны электрод располагается под углом 10-150 к горизонтали (сваркой «углом назад»). При этом давление дуги способствует удержанию металла сварочной ванны от стекания. При сварке металла толщиной до 3 мм поперечные колебания не производят, при большей толщине сварку ведут с поперечными колебаниями электрода. Сталь толщиной более 6 мм производят с поперечными колебаниями электрода.
Сварка в горизонтальном положении производится проволоками диаметром 0,8-1,4 мм. Металл толщиной до 3 мм сваривается без скоса кромок. Электрод наклоняется вниз, сварка производится «углом назад» без поперечных колебаний. Металл большей толщины сваривается при скошенной кромке верхнего листа, электрод в этом случае наклоняется вверх.
Швы в потолочном положении свариваются на пониженных сварочных токах и напряжении, при увеличенном расходе углекислого газа. Применяются электроды диаметром 0,5-1,4 мм. Для лучшего удержания жидкого металла от стекания электрод располагается с небольшим наклоном «углом назад».
|
Рисунок 1– Перемещение и положение электрода при сварке стыковых соединений с разделкой кромок (а) и угловых швов тавровых соединений (б)
Параметры режима сварки. К основным параметрам режима сварки относятся: скорость подачи проволоки, диаметр электрода, величина сварочного тока, напряжение на дуге, скорость сварки, вылет электрода, расход защитного газа, полярность постоянного тока. На рисунке 2 представлены ориентировочные параметры режима сварки в среде СО2. Параметры сварочного тока, скорость подачи проволоки и коэффициент наплавки на номограмме считаются стандартными, при сварке в стандартных условиях.
|
Рисунок 2 - Параметры режима сварки в среде СО2
Дата добавления: 2020-01-07; просмотров: 166; Мы поможем в написании вашей работы! |
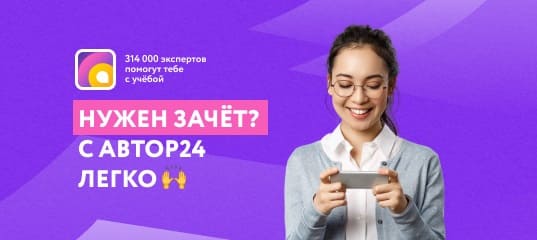
Мы поможем в написании ваших работ!