ЦЕЛЬ ИЗМЕЛЬЧЕНИЯ ТВЕРДЫХ МАТЕРИАЛОВ В ТЕХНОЛОГИЧЕСКИХ ПРОЦЕССАХ ХИМИЧЕСКОГО ПРОИЗВОДСТВА. КЛАССИФИКАЦИЯ ИЗМЕЛЬЧЕНИЯ ПО КРУПНОСТИ ЧАСТИЦ ПОЛУЧАЕМОГО МАТЕРИАЛА
Скорость химических и диффузионных процессов, протекающих с участием твердой фазы, повышается при увеличении ее поверхности. Увеличить поверхность обрабатываемого твердого материала можно, уменьшая размеры его кусков, т. е. путем измельчения. Измельчение твердых тел осуществляют с целью увеличения поверхности контакта материала с технологической средой, т. к. от величины этой поверхности зависит производительность многих процессов (химических, диффузионных, тепловых). Для этого при воздействии инструмента в измельчаемом материале создаются напряжения того или иного вида, приводящие к разрушению этого материала.
Результат воздействия характеризуется степенью измельчения Си, равной отношению среднего характерного размера кусков материала до измельчения D к соответствующему размеру d после измельчения. Работа внешних сил, затрачиваемая на измельчение, расходуется на объемную деформацию разрушаемых кусков и на образование новых поверхностей: А = Адеф + Ан.п.
Процессы измельчения условно подразделяют на дробление(крупное, среднее и мелкое) и измельчение(тонкое и сверхтонкое).Измельчение материалов осуществляют путем раздавливания, раскалывания, истирания и удара.
а .— раздавливание; б — раскалывание; в – истирание; г — удар.
Дробление твердых и хрупких материалов производят раздавливанием, раскалыванием и ударом, твердых и вязких — раздавливанием и истиранием.
|
|
Дробление материалов обычно осуществляется сухим способом (без применения воды), тонкое измельчение часто проводят мокрым способом (с использованием воды).
Результат измельчения характеризуется, степенью измельченияравной отношению среднего характерного размера D куска материала до измельчения к среднему характерному размеру d куска после измельчения: i = D/d.
Способы дробления крупнокусковых материалов и размеры дробильного оборудования зависят от размеров самых крупных кусков исходного и дробленого материала. Поэтому степень дробления часто определяется отношением характерного размера наиболее крупных кусков до измельчения к характерному размеру их после измельчения.
В промышленности в большинстве случаев требуются высокие степени измельчения. Часто размеры кусков исходного материала достигают 1500 мм, тогда как в технологических процессах иногда используется материал, размеры частиц которого составляют доли микрона. Такие степени измельчения достигаются при измельчении в несколько стадий.
В зависимости от размеров наиболее крупных кусков исходного и измельченного материала ориентировочно различают следующие виды измельчения:
|
|
Наименование вида дробления Размер, мм
до измельчения после измельчения
Крупное дробление 300–1500 100–300
Среднее дробление 100–300 10–50
Мелкое дробление 10–50 2–10
Тонкое измельчение 2–10 (2–75) • 10–3
Сверхтонкое измельчение(2–75) • 10–3 Менее 10–3
По своему назначению измельчающие машины условно делятся на дробилки крупного, среднего и мелкого дробления и мельницы тонкого и сверхтонкого измельчения.
По основному способу механического воздействия на материал измельчающие машины можно разделить на следующие основные группы: раскалывающего действия, раздавливающего действия, истирающе-раздавливающего действия, ударного действия, ударно-истирающего действия, коллоидные измельчители.
Дробление и особенно измельчение — весьма энергоемкие операции, поэтому необходимо стремиться к уменьшению массы перерабатываемого материала, руководствуясь принципом: не измельчать ничего лишнего. По этому принципу из материала, подлежащего измельчению, целесообразно перед измельчающей машиной выделить куски мельче того размера, до которого производится измельчение на данной стадии. Выделение «мелочи» осуществляется, например, ситовой классификацией — путем просеивания через одно или несколько сит. Классификация позволяет в значительной степени предотвратить попадание в измельчитель кусков материала, размеры которых меньше или равны заданному наибольшему размеру кусков продукта, получаемого в данной дробилке (мельнице). При этом уменьшается расход энергии на измельчение, становится возможным увеличение производительности измельчителя, конечный продукт получается более равномерным по размерам кусков.
|
|
Дробилки и мельницы работают в открытом и замкнутом циклах.
а — открытый цикл; б — открытый цикл с предварительной классификацией; в — замкнутый цикл; г — замкнутый цикл с совмещенными предварительной и поверочной классификацией: 1 - измельчитель; 2 — классификатор.
При измельчении в открытом цикле (рис.а) материал проходит через измельчающую машину один раз. В открытом цикле проводят крупное и среднее дробление, когда не требуется получать максимальные зерна конечного продукта определенного размера. При наличии «мелочи» в исходном материале его предварительно классифицируют (рис.б), при этом «мелочь» не подает в измельчитель, а сразу присоединяют к конечному продукту. При измельчении в замкнутом цикле (рис.в) материал неоднократно проходит через дробилку (мельницу). Измельченный продукт из измельчителя поступает вклассификатор, где из продукта выделяются куски (зерна) размерами больше допустимого предела, которые возвращаются в ту же дробилку (мельницу). Часто такую поверочную классификацию совмещают с предварительной классификацией исходного продукта (рис.г).
Дата добавления: 2019-11-25; просмотров: 648; Мы поможем в написании вашей работы! |
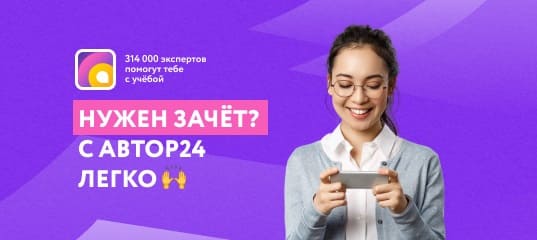
Мы поможем в написании ваших работ!