Д) Окускование железорудного сырья
Окускование - это процесс превращения мелких железорудных материалов (руд, концентратов, колошниковой пыли) в кусковые необходимых размеров, применение которых значительно улучшает показатели работы металлургических агрегатов. Для подготовки сырья к доменной плавке широко применяются два способа окускования: агломерация и окомкование.
Агломерация.Это процесс окускования мелких руд, концентратов и колошниковой пыли спеканием в результате сжигания топлива в слое спекаемого материала. Наиболее распространены ленточные агломерационные машины со спеканием слоя шихты на движущейся колосниковой решетке при просасывании воздуха через шихту.
Продукт спекания (агломерации) - агломерат представляет собой кусковой пористый продукт черного цвета; упрощенно можно характеризовать его как спеченную руду или спеченный рудный концентрат.
Основные составляющие агломерационной шихты - железосодержащие материалы (рудный концентрат, руда, колошниковая пыль); возврат (отсеянная мелочь ранее произведенного агломерата); топливо (коксовая мелочь); влага, вводимая для окомкования шихты; известняк, вводимый для получения офлюсованного агломерата.
Кроме того, в шихту зачастую вводят известь (до 25-80 кг/т агломерата), что улучшает комкуемость шихты, повышая ее газопроницаемость и прочность агломерата; марганцевую руду (до 45кг/т агломерата) для повышения содержания марганца в чугуне и отходы (прокатную окалину, шламы и другие материалы, вносящие оксиды железа).
|
|
Подготовку шихты, как и спекание, ведут на агломерационных фабриках. Подготовка шихты должна обеспечить усреднение, необходимую крупность, дозирование компонентов шихты, смешивание и окомкование ее.
Производство агломерата ведут на агломерационных фабриках, в состав которых входят комплекс оборудования для подготовки шихты, ленточные (конвейерные) агломерационные машины и комплекс оборудования для дробления и охлаждения полученного агломерата и отсева его мелочи.
Рис. 10. Схема агломерационной машины
Производство окатышей. Расширение использования бедных руд и особенно стремление к более глубокому обогащению их привели к получению тонкоизмельченных железорудных концентратов (менее 0,07 мм), для которых появилась необходимость найти новые пути окускования. В связи с этим начал развиваться так называемый процесс окатывания или окомкования
1 - шихтовые бункеры; 2 - сборный конвейер; 3 - смесительный барабан; 4 - бункер для бентонита; 5 - тарельчатый гранулятор; 6 - обжиговая машина; 7 - вентиляторы; 8 - грохот
Рис. 11. Схема производства окатышей
|
|
Процесс производства окатышей состоит из двух стадий: а) получения сырых (мокрых) окатышей; б) упрочнения окатышей (подсушка при 300-600 и обжиг при 1200-1350 °С).
Металлизованные окатыши. В последнее время в доменном производстве опробованы металлизованные окатыши, в которых часть оксидов железа восстановлена до железа. Повышение степени металлизации окатышей на каждые 10% обеспечивают снижение расхода кокса на 4,5-6% и увеличение производительности доменной печи на 5-7%. На металлизацию расходуется топлива больше, чем кокса на восстановление железа в доменной печи, но это более дешевое и менее дефицитное топливо, чем кокс (уголь, природный газ).
Топливо
Основным топливом доменной плавки является кокс - кусковой пористый материал из спекшейся углеродистой (83-88%С) массы, получающейся при прокаливании каменного угля без доступа воздуха. Вследствие своей прочности, термостойкости (способности не растрескиваться) и способности не спекаться кокс сохраняет форму кусков на всем пути движения шихты от колошника до горна. Благодаря этому кокс разрыхляет столб шихты в печи, обеспечивая необходимую ее газопроницаемость. В нижней части печи (в заплечиках и горне) только кокс остается в твердом состоянии, образуя как бы подвижную дренажную решетку (коксовую насадку), через которую в горн стекают жидкие продукты плавки, а вверх проходят газы.
|
|
Рис.12.Кокс каменноугольный
Как топливо кокс, сгорая у фурм, обеспечивает доменную печь теплом, необходимым для нагрева и расплавления шихтыи протекания процессов восстановления железа из оксидов. Кроме того, углерод кокса является восстановителем и служит для науглероживания железа, а продукт сгорания кокса — газ СО также является восстановителем.
Производство кокса. Кокс получают сухой перегонкой (нагревом до 1100 °С без доступа воздуха) коксующихся каменных углей в коксовых печах, представляющих собой камеры из динасового кирпича высотой 5-7, длиной 15-17 и шириной 0,4-0,45 м; их объем составляет 30-42 м3. В камеру объемом 30 м3 загружают 22 т шихты.
1 - приемный бункер для сырого каменного угля; 2 — конвейер; 3 — рампа выгрузки охлажденного кокса; 4 - тушильный вагон; 5 - кокс; 6 - регенераторы; 7 — камера коксования; 8 — штанга коксовыталкивателя; 9 — коксовыталкиватель; 10 — отвод коксового газа; 11 — загрузочный вагон; 12 — распределительная башня; 13 — тушильная башня; 14 — отделение для дробления и смешивания угля
|
|
Рис. 13. Общий вид коксовой батареи
Свойства кокса. Кокс содержит 83-88 % углерода; 8-13 % золы; 0,7-1,5% летучих; 0,5-5% влаги; 0,4-1,8% серы; 0,02-0,05 % фосфора. Кокс хорошего качества светло-серого цвета и при ударе куска о кусок издает легкий звон. Удельное количество тепла при сгорании кокса 28000-31500 кДж/кг. Наряду с высокой теплотой сгорания кокс как доменное топливо должен обладать определенным комплексом свойств, эти основные свойства следующие:
- высокая прочность, чтобы кокс не был раздавлен столбом вышележащей шихты в печи и не истирался при движении от колошника до фурм, а также высокая термостойкость, чтобы он не растрескивался при нагреве. В случае измельчения в печи кокса сильно снижается газопроницаемость шихты. Прочность кокса определяют в барабане диаметром 1м и длиной 1 м, на внутренней поверхности которого по всей длине приварены четыре угловых профиля. Для истирания берут 50 кг кокса. Барабан вращается с частотой 25 об/мин в течение 4 мин. Затем кокс рассеивают на сите. Показателями прочности кокса служат величины выхода класса более 40 мм (показатель М40) и менее 10 мм (показатель М10), выраженные в процентах. Величина М40 должна составлять 72-82, а М10 8,5-10%;
- малое содержание золы, основными составляющими которой являются Si02 и А12Оэ. Для их ошлакования необходимо увеличивать расход флюса, что увеличивает количество шлака. Увеличение зольности кокса на 1 % вызывает снижение производительности печи на 1,3% и увеличение расхода кокса на 1,3 %. Зола также снижает прочность кокса;
- неспекаемость в условиях доменного процесса;
- определенный размер кусков— от 25 до 60мм; загружать в печь более мелкий кокс недопустимо, так как при этом ухудшается газопроницаемость шихты;
-малое содержание вредных примесей серы и фосфора.
-малое и, что особенно важно, постоянное содержание влаги. Неучитываемые колебания количества влаги во взвешиваемом коксе при его дозировании приводят к тому, что действительное количество поступающего в печь кокса будет отличаться от расчетного, а это нарушает заданный тепловой режим работы печи. При сухом тушении влажность кокса составляет 0,4-1 %, при тушении водой 2-5 %;
- высокая пористость, благодаря чему достигается высокая скорость сгорания кокса. Обычно пористость кокса находится в пределах 37-53 %.
Другие виды топлива. Кокс является дорогостоящим и дефицитным материалом, поскольку запасы коксующихся углей во многих странах невелики. В связи с этим в последние годы при доменной плавке часть кокса заменяют природным газом, пылевидным топливом.
Природный газ содержит 90-98% углеводородов (главным образом, СН4и С2Н6) и небольшое количество азота (около 1%, а в газе Ишимбайского месторождения до 10%).
В качестве пылевидного топлива обычно используют молотый каменный уголь. В настоящее время общей тенденцией в доменном производстве является неуклонное сокращение доли металлургического кокса в энергетическом и материальном балансе доменной плавки по причине его высокой стоимости. Сокращение достигается путем замены части металлургического кокса другими видами технологического топлива, такими как: природный газ, мазут, каменноугольная смола или пылеугольное топливо (ПУТ). Последнее по разным источникам может заменить до 30-50% массы кокса, расходуемого на выплавку чугуна.Выбор исходных компонентов для ПУТ определяется свойствами, которыми должно обладать пылеугольное топливо, а именно:
- теплотворная способность ПУТ должна быть приближена к теплотворной способности кокса;
- ПУТ должен быстро сгорать (около 7-9 мкс), т.к. он должен сгорать в фурменной зоне, чтобы не образовывать замусоренность столба шихтовых материалов, ухудшающую газопроницаемость и фильтрацию жидких продуктов;
- зола, образующаяся при сгорании ПУТ должна быть легкоплавкой;
- также необходимо, чтобы ПУТ обладал, низкой абразивностью, слипаемостью, коксуемостью.
В настоящее время в большинстве доменных печей для достижения оптимального результата используют ПУТ со следующими характеристиками:
- влажность: не более 12,0%;
- зольность: не более 13,0%
- углерод в целом: 85,0%;
- содержание летучих веществ: 10,0-40,0%;
- содержание серы: не более 1,0%;
- содержание хлоридов: не более 0,2%;
- теплотворная способность: 33,4 МДж/кг.
Для производства ПУТ чаще всего используют малозольные угли (как правило, смесь из 2-3 типов углей).
Использование угля в качестве ПУТ для доменного производства не обеспечивает достаточного удешевления процесса плавки чугуна, поскольку из-за роста спроса стоимость угля постоянно возрастает. В связи с такой тенденцией появляется необходимость в замене угля альтернативными, менее дорогими веществами и продуктами.
Конструкция доменной печи
Доменная печь является мощным и высокопроизводительным агрегатом, в котором расходуется огромное количество шихты и дутья. Современная, наибольшая по размерам, доменная печь ежесуточно расходует около 23000 т шихты, 18000 т дутья, 1700 т природного газа и выдает 12000 т чугуна, 4000 т шлака и 27000 т колошникового газа. Таким образом, в большой доменной печи ежеминутно выплавляется около 9 т чугуна. Для обеспечения непрерывной подачи и выпуска столь большого количества материалов необходимо, чтобы конструкции печи были просты и очень надежны.
Общее описание доменной печи
Доменная печь- печь шахтного типа . Сверху в печь порциями непрерывно загружают шихтовые материалы - агломерат (окатыши) и кокс, которые медленно опускаются вниз; длительность их пребывания в печи составляет 4-6 ч. В нижнюю часть печи (верх горна) через фурмы подают дутье - нагретый воздух; у фурм за счет кислорода дутья сгорает кокс с выделением тепла, а горячие продукты сгорания движутся через столб шихты вверх, нагревая ее; время пребывания газов в печи составляет 3-12 с. При опускании нагревающейся шихты в ней из оксидов восстанавливается железо, которое науглероживается, расплавляется и каплями стекает в горн, формируя чугун, а не восстановившиеся оксиды в нижней части печи (низ шахты, распар) расплавляются, образуя шлак, который также стекает в горн. Накапливающиеся в горне чугун и шлак, имеющие температуру 1450-1500 °С,периодически выпускают через чугунные и шлаковые летки.
Общий вид доменной печи, оборудованной двух конусным засыпным аппаратом, показан нарис.14.Печьопирается нафундамент1,большая часть которого заглубленав землю. Снаружи печь заключена всплошнойстальной кожух 9. Внутри кожуха находится футеровка 8, охлаждаемая холодильниками, которые крепятся к внутренней поверхности кожуха. В нижней части печи (горне) расположены летки 3 для выпуска чугуна и летки 21 для выпуска шлака. Вокруг печи проложен кольцевой футерованный воздухопровод 6, в который из воздухонагревателейподаетсягорячеедутье(воздух); кольцевой воздухопроводслужит для подвода дутья к многочисленным расположенным по окружности печи фурменным устройствам 5, через которые дутье поступает в верхнюю часть горна. Выше колошника10печирасположеноколошниковое устройство. Оновключаетгазоотводы 15,19служащиедляотводаизпечи доменного газа;засыпной (загрузочный) аппарат и ряд других механизмов, связанных загрузкой шихты и отводом газа. Показаны элементы засыпного
1— фундамент; 2 — колонна; 3— летка для выпуска чугуна;
4— чугунные желоба; 5 — фурменные устройства; б — кольцевой воздухопровод; 7 — мараторное кольцо кожуха; 8 — футеровка; 9 — стальной кожух; 10 — колошник; 11 — большой конус; 12 — малый конус; 13 — вращающий механизмзасыпного устройства; 14 —приемная воронка; 15, 19 —газоотводы; 16 — скип; 17—воронка; 18 — наклонный мост;20 — воронка (чаша); 21—летка для выпуска шлака; 22 —площадка
Рис. 14. Общий вид доменной печи с двух конусным засыпным аппаратом
аппарата:большой конус 11, закрывающий воронку (чашу) 20; малый конус 12, закрывающий воронку 17, и механизм 13, обеспечивающий их вращение; приемная воронка 14, в которую шихтовые материалы высыпают из скипа 16 путем его опрокидывания, причем скип доставляют на колошник по рельсам наклонного моста 18.
Тяжесть кожуха и футеровки верхней части печи передается на фундамент через мараторное кольцо 7 кожуха и колонны 2. Выпускаемый из печи через летки 3 жидкий чугун поступает в располагаемые на рабочей площадке 22 чугунные желоба 4 и по ним в чугуновозные ковши; выпускаемый через летки 21 шлак по расположенным на площадке 22 шлаковым желобам стекает в шлаковозные ковши либо на установки припечной грануляции жидкого шлака.
Дата добавления: 2019-09-13; просмотров: 499; Мы поможем в написании вашей работы! |
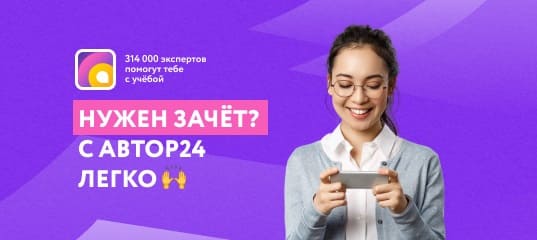
Мы поможем в написании ваших работ!