Стандартизация и контроль качества продукции
![]() |
Существует взаимосвязанная единая система стандартов, которая устанавливает общие для всех видов материалов и изделий требования, правила, нормы и методы по обеспечению защиты их от коррозии, старения и биоповреждений на стадиях разработки, производства и эксплуатации (хранения). Очень важно придерживаться этой системы, она помогает выбрать покрытие для данного металла или сплава с заданными свойствами, выбрать рациональные условия получения этого покрытия, способов хранения и методов контроля полученного покрытия.
Стандартизация, контроль и управление качеством покрытий осуществляется в соответствие с ЕСЗКС – единой системой защиты от коррозии и старения.
ЕСЗКС – комплекс взаимосвязанных государственных стандартов, устанавливающий общие для всех видов материалов и изделий требования, правила, нормы и методы по обеспечению защиты от коррозии, старения и биоповреждений на стадиях разработки, производства и эксплуатации.
ЕСЗКС предназначена для обеспечения и сохранения заданного уровня качества изделий и материалов средствами и методами защиты от коррозии, старения и биоповреждений с учётом требований конкурентоспособности изделий на мировом рынке.
Эффективное функционирование ЕСКЗС, в соответствии с её назначением, обеспечивается применением стандартов.
В Республике Беларусь существуют стандарты, основанные на ГОСТ – государственных общесоюзных стандартах.
|
|
ГОСТ 9.303 – 84.
Настоящий стандарт устанавливает общие требования к выбору металлических и неметаллических неорганических покрытий деталей и сборочных единиц, наносимых химическими и электрохимическими способами.
При выборе покрытий следует учитывать: назначение покрытий; условия эксплуатации; материал детали; назначение стали; свойства покрытия; экономичность металла покрытия; экономическую целесообразность.
ГОСТ 9.101-78 представляет собой единую систему защиты изделий от коррозии и старения. Настоящий стандарт устанавливает определения, назначения, структуру и состав единой системы защиты изделий и материалов от коррозии, старения и повреждений, правила наименования и обозначения стандартов системы. Устанавливает общие для всех видов материалов и изделий требования, правила и методы по обеспечению
защиты от коррозии, старения на стадиях разработки, производства и хранения.
ГОСТ 9.301 – 86.
Настоящий стандарт распространяется на металлические и неметаллические неорганические покрытия, полученные электрохимическими и химическими способами, и устанавливает общие требования к поверхности основного металла и покрытиям в процессе их производства и контролю качества основного металла и покрытий.
|
|
ГОСТ 9.305 – 84.
Настоящий стандарт устанавливает параметры операций, входящих в технологические процессы получения покрытий, кроме операций подготовки
поверхности основного металла и обработки покрытий, производимых механическими способами.
Стандарт распространяется на металлические и неметаллические неорганические покрытия, наносимых химическими и электрохимическими способами на детали и сборочные единицы, за исключением деталей из высокопрочных сталей и магнитных сплавов.
При разработке технологического процесса получения покрытия варианты операций и конкретные величины режимов обработки выбирают в соответствии с указаниями, приведенными в картах, исходя из конструктивно-технологических характеристик, подлежащих обработке деталей и применяемого метода обработки (на подвесках или насыпью, погружением, струёй или в потоке электролита).
ГОСТ 9.309-86. Единая система защиты от коррозии и старения. Покрытия гальванические. Стандарт распространяется на гальванические покрытия и устанавливает методику определения рассеивающей способности (РС) электролита для получения этих покрытий при средних плотностях тока
|
|
ГОСТ 9.314-90.Настоящий стандарт устанавливает общие требования воды для гальванического производства и схемы промывок.
Контроль качества гальванических покрытий предусматривает определение следующих характеристик: внешний вид покрытия, прочность сцепления слоя покрытия с основным металлом, твердость покрытия, толщина и равномерность покрытия, пористость покрытия.
Контроль внешнего вида покрытия на деталях, покрываемых на подвесках, проводят на выборке 2% деталей от каждой партии. На поверхности деталей, если нет специальных указаний в конструкторской документации, не являются браковочными следующие признаки:
1. следы механической обработки и другие отклонения, допускаемые нормативной документацией на основной металл;
2. незначительная волнистость поверхности покрытия после вытяжки, выявляющаяся после травления;
3. темные или светлые полосы или пятна в труднодоступных для зачистки отверстиях и пазах, на внутренних поверхностях и вогнутых участках деталей сложной конфигурации, местах сопряжения неразъемных сборочных единиц, в сварных, паяных швах, околошовной зоне и местах снятия плакировочного слоя;
|
|
4. неравномерность блеска и неоднородность цвета;
5. следы от потеков воды;
6. блестящие точки и штрихи, образовавшиеся от соприкосновения с измерительным инструментом, приспособлениями;
7. отсутствие покрытия.
Контроль деталей проводят осмотром деталей невооруженным глазом на расстоянии 25 см от контролируемой поверхности при естественном или искусственном освещении. При оценке внешнего вида покрытия необходимо учитывать состояние поверхности детали перед нанесением покрытия. Цвет блестящего никелевого покрытия светло-серый или серебристо-серый.
Для контроля толщины покрытия используют различные методы, приведенные в ГОСТ 9.302-79.Для этого от каждой партии отбирают от 0,1 до 1% деталей, но не менее трех деталей. Контроль толщины покрытия проводят на наружной поверхности детали, на доступных участках, не имеющих накатки, резьбы, на расстоянии 2-5 мм от ребер, углов, отверстий, мест контакта с приспособлениями.
Толщину покрытий контролируют неразрушающими магнитными методами с помощью толщиномеров типа МТ-41НЦ.
Прочность сцепления электролитических осадков с основой оценивается качественно по результатам испытаний: нагреванием до 150—250°С с последующим быстрым охлаждением.
Критерием достаточной прочности сцепления при этих испытаниях является отсутствие отслаивания покрытия или отсутствие вздутий—при натирании и нагревании.
Твердость электролитических осадков измеряется путем вдавливания алмазной пирамиды под действием нагрузки в течение определенного времени с последующим измерением глубины отпечатка. Число твердости определяется как отношение нагрузки к поверхности отпечатка в Па.
Оптимальным является приборный контроль, дающий более точные и объективные результаты. При обнаружении дефектов покрытий необходим анализ причин их появления, для чего могут быть использованы все перечисленные выше методы определения характеристик покрытий с привлечение дополнительной информации, например, о структуре и текстуре покрытий.
Дата добавления: 2019-09-13; просмотров: 90; Мы поможем в написании вашей работы! |
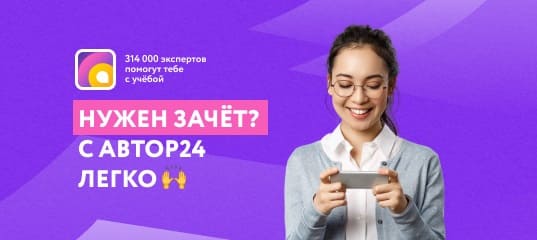
Мы поможем в написании ваших работ!