Характеристика отходов, стоков, вентиляционных выбросов. Методы их обезвреживания, утилизации, регенерации
Таблица 1.2 - Качественный и количественный состав сточных вод:
Вид сточ- ных вод |
рН | Показатели, мг/л | Количество стоков, м3/сут | ||||||
Cr+6 | Zn+2 | Feобщ | Cu+2 | SO42- | Cl- | CN- | |||
Промыв ные кис лощелоч ные | 4-8 | - | 25 | 25 | - | 300 | 200 | - | 400 |
Промыв ные хро мосодер жащие | 4,5- 4,7 | 50 | 0,5 | 10 | - | 150 | 100 | - | 50 |
Продолжение таблицы 1.2
Хромо содержа щий отрабо танный электро лит | 1-3 | 150000 | 25000 | 2500 | - | - | - | - | 0,2 |
Масло имульси онные | 7-9 | - | - | - | - | - | - | - | 12000 м3/год |
На МЗКТ очистные сооружения находятся в стадии проектирования. Очистные сооружения в термическом цехе должны обеспечивать необходимую степень очистки сточных вод гальванического производства и маслоэмульсионных стоков.
При проектировании очистных сооружений должны учитываться возможные изменения норм ПДК хрома. В проекте должны быть предусмотрены дополнительные финишные фильтры, которые обеспечат необходимую степень очистки, т.е. очистные сооружения должны быть рассчитаны на любые ПДК.
В ближайшие годы ПДК хрома и других веществ значительно не изменятся.
Состав сточных вод гальванического производства, поступающих в городскую канализационную сеть должны быть следующими:
-взвешенные вещества 300 мг/л
-сухой остаток 1000 мг/л
-хлориды 350 мг/л
-сульфаты 500 мг/л
|
|
-Fe+2 2 мг/л
-Cr+3 0,4мг/л
-Cr+6 0,1мг/л
-Cu+2 1 мг/л
-Zn+2 2 мг/л
-Ni+2 1 мг/л
-цианиды отсутствуют
-свинец 0,5 мг/л
-ртуть 0,5 мг/л
Очистка сточных вод от ионов тяжелых металлов осуществляется путем перевода ионов тяжелых металлов в малорастворимые соединения (гидроксиды) при нейтрализации сточных вод с помощью различных щелочных реагентов. Реагентная очистка сточных вод от шестивалентного хрома состоит из двух стадий:
1) восстановление шестивалентного хрома до трехвалентного; 2) осаждение трехвалентного хрома в виде гидроксида. В качестве реактивов - восстановителей наибольшее применение получили натриевые соли сернистой кислоты – сульфит, бисульфит, пиросульфит (Na2S2O5), а также дитионит натрия (Na2S2O4). Восстановление Cr6+ до Cr3+ происходит по реакциям:
Cr2O72- + 3SO34- + 8H+ = 2Cr3+ + 3SO42- + 4H2O;
Cr2O72- + 3HSO3¯ + 5H+ = 2Cr3+ + 3SO42- + 4H2O
После окончания реакции восстановления Cr6+ в кислой среде сточные воды подвергают нейтрализации с целью осаждения Cr3+ в виде гидроксида по реакции:
|
|
Cr3+ + 3ОН¯ → Cr(ОН)3↓.
Разработан одноступенчатый метод очистки хромсодержащих сточных вод с использованием в качестве реагента FeS, получаемого в обрабатываемом растворе путем введения в него двух(трех)-кратного избытка FeSO4, Na2S2O5 или NaHSO4 по отношению к концентрации Cr(VI). Удаление Cr(VI) происходит по реакции:
H2CrO4 + FeS + H2O → Cr(OH)3 + Fe(OH)3 + S + H2O.
Очистку электролитов хромирования от примесных металлов ионообменным методом проводят с помощью сильнокислых катионообменных смол в Н-форме для связывания металлов и выделения в раствор эквивалентного количества ионов водорода. Однако, этот метод применим только для регенерации разбавленных электролитов с концентрацией CrО3 до 100 г/л. При более высокой концентрации происходит деструкция смол с одновременным восстановлением Cr(VI) до Cr(III).
Поэтому рекомендуется проводить регенерацию раствора хромирования совместно с регенерацией хрома (VI) из промывочных вод от ванн улавливания или каскадных ванн промывки. В этом случае хромсодержащие растворы пропускают поочередно через катионообменные и анионообменные колонки. В катионитовой колонке из растворов удаляются катионы Cr3+, Zn2+, Fe3+, Cu2+ и др. В качестве катионита может использоваться сульфостирольная смола марки КУ-2-8 в Н-форме. Десорбция производится в 10%-ном растворе серной кислоты. В анионитовой колонке адсорбируются анионы хромовой кислоты. В качестве анионита используются иониты марки АВ-17-8, АВ-29,АВ-17-16. Десорбция анионитовых смол осуществляется раствором едкого натра. Образующийся элюат в виде хромата натрия направляется в катионообменную колонку для удаления ионов натрия.
|
|
Происходят следующие реакции:
– первая катионитовая колонка:
сорбция 3[R-SO3H] + Cr3+ → [R-SO3-]3Cr + 3H+
десорбция [R-SO3-]3Cr +3H+ → 3[R-SO3H] + Cr3+
– анионитовая колонка:
сорбция 2R′-OH + CrO3 → [R′]2CrO4 +H2O
десорбция [R′]2CrO4 + NaOH → 2R′-OH +Na2CrO4
– вторая катионитовая колонка:
сорбция Na2CrO4 + 2[R-SO3H] → 2[R-SO3Na] +CrO3 +H2O
десорбция [R-SO3Na] + H+ → [R-SO3H] +Na+
Регенерированная хромовая кислота с концентрацией CrO3 в пределах 50-60 г/л после частичного выпаривания направляется в ванны хромирования для корректировки электролита.
Для регенерации электролитов хромирования с концентрацией CrO3 150-300 г/л целесообразно применять электрохимические методы регенерации. В большинстве случаев анодными материалами служат свинец, сплавы его с сурьмой, серебром и оловом, графит, титан. Катоды изготавливаются из меди или нержавеющей стали. Используют керамические и фторопластовые диафрагмы, а также из винипора, винипласта, пористого стекла. Процесс протекает при t = 40-60°С, плотности анодного тока 3-4 А/дм2, катодного тока 17-20 А/дм2. Католитом служит раствор серной кислоты или смеси солей сульфатов и бисульфатов.
|
|
При использовании анионитовых мембран отработанные электролиты хромирования помещают в катодную камеру, а в анодную – 3-4% раствор серной кислоты. Электролиз в этом случае позволяет вернуть в производство 40-50% хромовой кислоты, остальное количество идет на осаждение гидроксида хрома. Раствор хромовой кислоты после окончания электролиза практически не содержит примесей Cr3+, Cu2+ и других металлов, которые осаждаются в катодной камере в виде гидроксидов.
При использовании катионитовых мембран отработанные электролиты помещают в анодную камеру, а в катодную заливают 5%-ный раствор серной кислоты. Примеси металлов осаждаются в катодном пространстве в виде гидроксидов или осаждаются в виде порошкообразного, легко отделяемого осадка. Процесс ведут при катодной плотности тока 2,7-10 А/дм2 и объемной плотности тока – 2,2-8 А/л. Расход электроэнергии на обработку 1л электролита хромирования составляет 0,4-1,7 кВт∙ч.
Для очистки сточных вод содержащих ионы хрома, никеля и цинка в основном используют метод электрокоагуляции.
В результате электролитического растворения стальных анодов при рН>2 образуются ионы Fe2+. Одновременно с этим ионы Fe2+, а также гидроксид железа (II), способствуют химическому восстановлению Cr6+ до Cr3+ по следующим реакциям:
при рН<5,5 Cr2O72- +6Fe2+ + 14H+ → 6Fe3+ +2Cr3+ +7H2O
при рН>5,5 Cr2O72- +3Fe(OH) + 4H2O → 3Fe(OH)3 + 2Cr(OH)3 + 2OH¯
Некоторое количество CrO42- и Cr2O72- ионов восстанавливается до ионов Cr3+ в результате катодных электрохимических процессов:
Cr2O72- + 14H+ + 6ē → 2Cr3+ +7H2O
Cr2O72- + 4H2O + 3ē → 2Cr(OH)3 + 5OH¯
При электрохимической обработке сточных вод происходит их подщелачивание, что способствует коагуляции гидроксидов железа (II) и (III) и хрома (III), а также гидроксидов других тяжелых металлов, ионы которых могут содержаться в сточных водах.
В основе принципа гальванокоагуляции лежат те же физико-химические процессы, которые составляют сущность электрокоагуляции. Отличие данного метода заключается в способе введения в обрабатываемый сток ионов железа, а также в отсутствии электростатической коагуляции, возникающей при наложении электрического поля. При данном методе очистки, очищаемую воду пропускают через железные стружки, смешанные с коксом в соотношении 4:1. За счет разности электрохимических потенциалов железо переходит в раствор:
Fe - 2ē → Fe2+
Процесс гальванокоагуляции проводят в проточных вращающихся аппаратах барабанного типа. При вращении стружечная загрузка попеременно то погружается в сток, то оказывается на воздухе, в результате протекает следующая реакция:
4Fe2+ + O2 + 10H2O → 4Fe(OH)3 +8H+
В свою очередь соединения железа(III) при контакте с железной стружкой восстанавливаются до железа(II). Соединения железа(II) способствуют восстановлению хрома(VI) до хрома(III).
Анализ причин брака
Таблица 1.3 – Виды брака
Вид дефекта | Причина возникновения | Способ устранения дефекта |
Отслаивание покрытия от основного металла | 1. Отсутствие анодной активации 2. Плохая химическая подготовка детали 3. Деталь недостаточно прогрелась в электро- лите 4. Перерыв тока во время хромирования 5. Наличие остатков покрытия от предыду- щего хромирования | 1. Проверить режим активации 2. Усилить контроль за выполнением этой опе- рации 3. Увеличить время прогрева детали 4. Устранить дефекты в контактах сети постоян- ного тока 5. Полностью уда- лить покрытие перед хромированием |
Отсутствие покрытия на отдельных участках хромируемой поверх- ности | 1. На углубленных уча- стках из-за недостаточ- ной для данного релье- фа кроющей способнос- ти 2. На краях отверстий из-за отвлечения тока на неизолированные внутрения поверхности отверстия 3. Мала плотность тока или чрезмерно высока температура | 1. Дать толчок тока пе- ред хромированием, применить дополнитель- ный анод 2. Закрыть отверстия свинцовыми или изо- лирующими пробками 3. Установить нормаль- ный режим |
Серое покрытие | 1. Высокое содержание в электролите трехва- лентного хрома 2. Значительное загряз- нение электролита желе- зом или медью 3. Низкая температура или на выступающих частях слишком высокая плотность тока | 1. Проработать электро- лит током при возможно большей поверхности анодов 2. Полностью или части- чно сменить электролит 3. Отрегулировать тем- пературу или на на выступающих частях установить экраны |
На поверхности детали имеется крупный пит- тинг | 1. Задержка пузырьков водорода на ниж- ней поверхности детали 2. Наличие в основном металле неметалличес- ких включений и порис- тости 3. Наличие в электроли- те взвешенных частиц | 1. Периодически пере- вворачивать деталь или хромировать в верти- кальном положении 2. Дефекты металла исключают возможность его хромирования 3. Очистить электролит |
Молочный хром по всей поверхности или на участках с понижен- ной плотностью тока | 1. Недостаточная плот- ность тока или завышен- ная температура | 1. Откорректировать ре- жим хромирования |
2 Характеристика основного и вспомогательного оборудования
Основное оборудование
Основным оборудованием для нанесения гальванопокрытий являются стационарные гальванические ванны, механизированные и автоматизированные линии.
Ванны предназначены для выполнения операций, предусмотренных технологическим процессом (по подготовке поверхности, нанесению покрытий, финишной обработке). Они представляют собой емкости прямоугольной формы, сваренные из листовой стали. Для большинства сред ванны футеруются. Ванны заполняются раствором или водой в соответствии с технологическим процессом [4].
В настоящее время известно очень много разработок по поводу конструкций ванн промывок и других операций, изложено большое количество способов обработки деталей. Ниже приведены некоторые из них.
Одно из изобретений относится к способу струйной промывки деталей, в частности на подвесках, и устройству для его осуществления в гальваническом и химическом производстве, в условиях повышенных требований к расходу моющей жидкости. Способ струйной промывки включает подачу пучков параллельных струй моющей жидкости, формируемых соответствующими элементами распределительных коллекторов, размещенных в верхней части ванны промывки, на поверхность перемещаемых относительно них в вертикальной плоскости подвесок с деталями. Элементы формирования пучка струй располагают над распределительными коллекторами и в шахматном порядке. Расстояние прямолинейного распространения параллельных струй в пучках определяется по определенной зависимости. Установка содержит ванну промывки со сливным трубопроводом и расположенные в верхней части распределительные коллекторы для подачи моющей жидкости от ее источника, с сопловыми насадками в виде модульных наборных панелей для формирования пучков параллельных струй жидкости, устройство для улавливания и локализации, незадействованных в процессе промывки струй жидкости.
Разработано устройство для укрытия технологических ванн. Укрывное устройство содержит приводной барабан, гибкое полотно, закрепленное неподвижно одним концом на барабане, подвижную балку, кинематически связанную с барабаном гибкой тяговой связью. Противоположный конец гибкого полотна снабжен тягой, прикрепленной к подвижной балке посредством упругих элементов. Использование устройства позволяет сократить энергозатраты на вентиляцию в 2,5 раза,
уменьшить потери электролита до 40% и энергозатраты на 10-20% с зеркала
электролизных ванн, улучшить тепловой баланс ванн, условия труда и экологическую обстановку в цехах и окружающей среде.
Предлагается изобретение, которое относится к оборудованию для нанесения гальванохимических покрытий на детали, размещаемые как на подвесках, так и в барабанах. Цель изобретения – повышение производительности линии. Устройство содержит ванны, оснащенные грузоопорами, устройствами загрузки и выгрузки, датчики загрузки, автооператор с грузозахватами и реверсивными приводами горизонтального и вертикального перемещения, рельсовый путь, датчики положения автооператора и его грузозахватов, сушильную камеру, командоаппарат, датчик загрузки. Выход датчика загрузки соединен с первым входом блока автоматического управления процессом перегрузки деталей из сушильной камеры на устройство выгрузки, первая группа выходов которого соединена с электромагнитными распределителями, управляющими работой силовых цилиндров для вертикального перемещения штанг с приспособлениями и деталями из сушильной камеры. Выход датчика положения автооператора из сушильной камеры соединен со вторым выходом блока деталей, вторая группа выходов которого соединена с электромагнитными распределителями, управляющими работой силовых цилиндров для углового перемещения штанг с приспособлениями с деталями из сушильной камеры на устройство выгрузки. Выход датчика загрузки соединен с третьим входом блока перегрузки, третья группа выходов которого соединена с электромагнитными распределителями, управляющими работой силовых цилиндров устройства выгрузки. Выход датчика положения автооператора соединен с четвертым входом блока перегрузки, четвертая группа выходов которого соединена с соответствующими входами командоаппарата. Повышение производительности линии достигается введением в данное устройство блока автоматического управления процессом перегрузки деталей из сушильной камеры на устройство выгрузки, оснащенное механизмом для перегрузки штанг с приспособлениями с деталями на устройство выгрузки, его выполнением, а так же выполнением устройства выгрузки, блока автоматического управления процессом перегрузки деталей из сушильной камеры на устройство выгрузки.
Для футеровки применяют пластмассовые и металлические материалы, резину или керамическую плитку. Наибольшее распространение нашли пластмассовые и металлические материалы. Часть ванны футеруется листовым свинцом марки С1 или С2 , винипластом марки ВН, пластикатом марки ПП-КЭ.
С целью снижения возможности разрушения футеровочного слоя и контакта агрессивной среды со стальной наружной оболочкой предложено составить ванну из двух ёмкостей, наружной из стали и внутренней из химически стойкого PVDF с тем, чтобы между ёмкостями был зазор. На бортах ванны между обеими ёмкостями располагается водяной затвор, который препятствует увеличению температуры и проникновению электролита в зазор между ёмкостями при монтаже ванны.
К вспомогательному оборудованию следует отнести то оборудование, которое непосредственно в технологическом процессе участия не принимает, но влияет на качество покрытия или работу основного оборудования. К нему относятся установки для фильтрации, перемешивания, перекачивания электролитов, сушильные шкафы и бортовые отсосы, площадка обслуживания.
Важной проблемой в гальванических цехах является обеспечение экологически безопасного микроклимата воздуха производственных помещений. Кроме общей вытяжки из верхней зоны помещения и общего притока свежего воздуха, большое значение для исключения опасных концентраций вредных веществ имеет местная вытяжная вентиляция. Для этого ванны с вредными выделениями оборудованы бортовыми отсосами, которые в зависимости от агрессивности паров выполнены из углеродистой или нержавеющей стали.
Бортовые отсосы устанавливаются по длинной стороне ванн и должны присоединятся к патрубкам сборного воздуховода вытяжной вентиляции [2].
Принцип работы бортового вентиляционного отсоса заключается в том, что воздух, всасываемый с большой скоростью через его узкую заборную щель, образует над зеркалом ванны сильную горизонтальную струю – «факел». Эта струя препятствует проникновению через нее выбрасываемых из раствора капель и заставляет часть их вернутся в ванну, а другая часть капель и газов увлекается этой струей в бортовой отсос. Для регулирования количества отсасываемого воздуха бортовые отсосы снабжены шиберными устройствами.
Для сушки деталей на линиях обычно применяют сушильные камеры. Сушка производится путем обдува изделий воздухом, нагретым в паровом калорифере или с помощью электронагревателей.
Сушильная камера представляет собой установку для удаления влаги с обработанных деталей. Камера состоит из корпуса, сваренного из листовой стали, парового калорифера, вентилятора, воздуховодов, шиберного устройства.
Стенки сушильной камеры теплоизолированы матами из стекловолокна. Для контроля температуры установлен термометр стеклянный. Сушильная камера работает с частичной рециркуляцией отработанного воздуха.
Воздух в сушильную камеру нагнетается вентилятором через калорифер, нагревается и через щели в стенках и дне корпуса подается на детали, находящиеся на сетчатом лотке. Часть воздуха вновь через воздуховод поступает к вентилятору, а часть отработанного воздуха удаляется в вытяжную вентиляцию.
Для сушки деталей в автоматических линиях применяют открытые сверху сушильные камеры, удобные для загрузки и выгрузки.
Таким образом, процесс реализовывается на автооператорной линии, работающей в автоматическом режиме. Она включает в себя: разводку трубопроводов, шкаф управления, пульт управления, электромонтаж, ванны электрохимической обработки (никелирования и хромирования), химической обработки (обезжиривания, активации, улавливания) и промывки (горячая и холодная), подвесной тележечный гибкотяговый манипулятор, захват, стойку подготовительную, подвесное приспособление, камеру сушильную, систему вентиляции, ВАКи и ВАКРМ.
3 Охрана окружающей среды
Важнейшим мероприятием по защите окружающей среды при производстве гальванопокрытий является очистка сточных вод от химически вредных взвешанных веществ. Очистка стоков обязательна и производится в соответствии с «Правилами охраны поверхностных вод от загрязнения сточными водами». Сточные воды гальванического производства различают по составу загрязнений, режиму сброса и концентрации. Стоки принято разделять на:
Ø концентрированные;
Ø низкоконцентрированные.
Содержание вредных веществ должно быть понижено до значения ПДК. Для возможного дальнейшего сброса сточных вод без ущерба для окружающей среды. Для шламов устанавливаются ограничения по степени влажности.
Стоки от гальванического производства принято разделять на три группы:
1) кислотно – щелочные (образуются в результате процессов цинкования, никелирования, обезжиривания и т.д.);
2) хромосодержащие сточные воды (образуются в результате процессов хроматирования, электрополирования, оксидирования алюминия, пассивирования цинка и т.д.);
3) цианосодержащие сточные воды (образуются в результате процессов обезжиривания изделий с одновременным их меднением, а также цанистые ванны нанесения покрытия).
По режиму сброса и концентрации сточные воды делятся на постоянно поступающие разбавленные воды после промывки деталей и периодически сбрасываемые из основных ванн отработанные концентрированные электролиты. Концентрация загрязняющих веществ в отработанных электролитах в 100-1000 раз больше, чем в разбавленных промывных водах, а объемы во много раз меньше.
Основными компонентами загрязнения сточных вод являются высокотоксичные соединения тяжелых металлов и цианиды. Около 40% стоков гальванического производства составляют хромсодержащие сточные воды.
Отработанные концентрированные электролиты сбрасываются в специальные емкости для обезвреживания. Растворы, содержащие кислоты и щелочи, используются как реагенты для нейтрализации. Хром- и циансодержащие, а также растворы ценных тяжелых металлов должны регенерироваться и вновь возвращаться в производство.
На МЗКТ очистные сооружения находятся в стадии проектирования. Очистные сооружения в термическом цехе должны обеспечивать необходимую степень очистки сточных вод гальванического производства и маслоэмульсионных стоков.
При проектировании очистных сооружений должны учитываться возможные изменения норм ПДК хрома. В проекте должны быть предусмотрены дополнительные финишные фильтры, которые обеспечат необходимую степень очистки, т.е. очистные сооружения должны быть рассчитаны на любые ПДК.
В ближайшие годы ПДК хрома и других веществ значительно не изменятся.
Состав сточных вод гальванического производства, поступающих в городскую канализационную сеть должны быть следующими:
-взвешенные вещества 300 мг/л
-сухой остаток 1000 мг/л
-хлориды 350 мг/л
-сульфаты 500 мг/л
-Fe+2 2 мг/л
-Cr+3 0,4мг/л
-Cr+6 0,1мг/л
-Cu+2 1 мг/л
-Zn+2 2 мг/л
-Ni+2 1 мг/л
-цианиды отсутствуют
-свинец 0,5 мг/л
-ртуть 0,5 мг/л
Дата добавления: 2019-09-13; просмотров: 127; Мы поможем в написании вашей работы! |
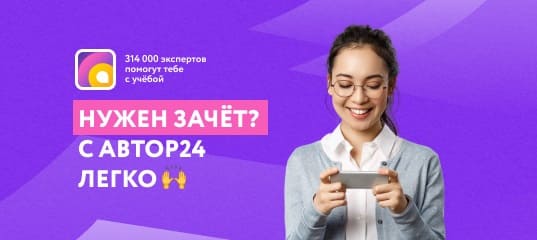
Мы поможем в написании ваших работ!