Общие сведения и классификация зубчатых передач
3.1. Механизм, в котором два подвижных звена являются зубчатыми ко лесами, образующими с неподвижным звеном вращательную или поступатель ную пару, называют зубчатой передачей (рис. 3.1).
Рис. 3.1. Виды зубчатых передач: а, б, в — цилиндрические зубчатые передачи с внешним зацеплением; г — передача винт-гайка; д — цилиндрическая передача с внутренним зацеплением; е — зубчатая винтовая передача; ж, з, и — конические зубчатые передачи; к — гипоидная передача
В большинстве случаев зубчатая передача служит для передачи вращательного движения. В некоторых механизмах эту передачу применяют для преобразования вращательного движения в поступательное (или наоборот, см. рис. 3.1, г).
Зубчатые передачи — наиболее распространенный тип передач в современном машиностроении и приборостроении; их применяют в широких диапазонах скоростей (до 100 м/с), мощностей (до десятков тысяч киловатт).
3.2. Основные достоинства зубчатых передач по сравнению с другими передачами:
• технологичность, постоянство передаточного числа;
• высокая нагрузочная способность;
• высокий КПД (до 0,97—0,99 для одной пары колес);
• малые габаритные размеры по сравнению с другими видами передач при равных условиях;
• большая надежность в работе, простота обслуживания;
• сравнительно малые нагрузки на валы и опоры.
Перечислите достоинства зубчатой передачи по сравнению с ранее изученной фрикционной передачей.
|
|
3.3. К недостаткам зубчатых передач следует отнести:
• невозможность бесступенчатого изменения передаточного числа;
• высокие требования к точности изготовления и монтажа;
• шум при больших скоростях; плохие амортизирующие свойства;
• громоздкость при больших расстояниях между осями ведущего и ведомого валов;
• потребность в специальном оборудовании и инструменте для нарезания зубьев;
• зубчатая передача не предохраняет машину от возможных опасных перегрузок.
Сравните зубчатые и рассмотренные в гл. 2 фрикционные передачи. Дайте оценку в целом по применению в машиностроении зубчатых передач.
Лекция 3.6 Самостоятельно
Классификация зубчатых колес.
3.4. Зубчатые передачи и колеса классифицируют по следующим призна кам (см. рис. 3.1):
• по взаимному расположению осей колес — с параллельными осями (цилиндрические, см. рис. 3.1, а—д), с пересекающимися осями (конические, см. рис. 3.1, ж—и), со скрещивающимися осями (винтовые, см. рис. 3.1, е, к);
• по расположению зубьев относительно образующих колес — прямозубые, косозубые, шевронные и с криволинейным зубом;
• по конструктивному оформлению — открытые и закрытые;
|
|
• по окружной скорости — тихоходные (до 3 м/с), для средних скоростей (3—15 м/с), быстроходные (св. 15 м/с);
• по числу ступеней — одно- и многоступенчатые;
• по расположению зубьев в передаче и колесах — внешнее, внутреннее (см. рис. 3.1, д) и реечное зацепление (см. рис. 3.1, г);
• по форме профиля зуба — с эвольвентными, круговыми;
• по точности зацепления. Стандартом предусмотрено 12 степеней точности. Практически передачи общего машиностроения изготовляют от шестой до десятой степени точности. Передачи, изготовленные по шестой степени точности, используют для наиболее ответственных случаев.
3.5. Из перечисленных выше зубчатых передач наибольшее распространение получили цилиндрические прямозубые и косозубые передачи, как наиболее простые в изготовлении и эксплуатации. Конические передачи применяют только в тех случаях, когда это необходимо по условиям компоновки машины; винтовые — лишь в специальных случаях.
Чем отличается закрытая передача от открытой?
Лекция 3.7
Краткие сведения о методах изготовления зубчатых колес , их конструкциях , материалах
3.6. Существуют следующие способы изготовления зубчатых колес (обработки зубьев):
|
|
• литье (без последующей механической обработки зубьев), для современных машин этот способ применяют редко;
• накатка зубьев на заготовке (также без последующей их обработки);
• нарезание зубьев (т. е. зубья получаются в процессе механической обработки заготовки).
Способ изготовления зубчатых колес выбирают в зависимости от их назначения и по технологическим соображениям.
Для отдельных конструкций машин в массовом производстве применяют способ накатки зубьев. Возможны также штамповка, протягивание и. т. д. В этом случае форма инструмента повторяет очертания впадины ;:ли зубьев). В большинстве же случаев зубчатые колеса изготовляют нарезанием.
3.7. Зубья нарезают, как правило, методами копирования и обкатки. Копирование заключается в прорезании впадин между зубьями с помощью тисковой (рис. 3.2) или пальцевой (рис. 3.3) фрезы.
Рис 3.2. Нарезание зубьев методом копирования дисковой фрезой
Рис. 3.3. Нарезание зубьев пальцевой фрезой
Обработка зубьев по методу обкатки производится инструментами . очертаниями, отличными от очертаний нарезаемых зубьев, — долб—" (рис. 3.4 — зуб наружного зацепления, рис. 3.5 — зуб внутреннего заие~ ния), червячной фрезой (рис. 3.6) или инструментальной рейкой (рис. :
|
|
Достоинством метода обкатки (огибания) является то, что он позволь одним и тем же инструментом изготовлять колеса с зубьями различное формы. Изменяя относительное расположение инструмента и заготовки ш
|
|
Рис. 3.4. Нарезание зубьев наружного зацепления
Рис. 3.5. Нарезание зубьев внутреннего зацепления
Рис. 3.6. Нарезание зубьев червячной фрезой
Рис. 3.7. Нарезание зубьев инструментальной рейкой
станке, можно получать зубья различной формы и толщины (передачи со смещением).
Обкатка по сравнению со способом копирования обеспечивает большую точность и производительность.
На рис. 3.8 показана схема нарезания зубьев конического колеса на зубо- строгальном станке. Как называется этот способ обработки зубьев?
Рис. 3.8. Нарезание зубьев конического колеса
3.8. Для достижения высокой точности и малой шероховатости поверх
ности зубьев после нарезания производится их отделка.
Способы отделки зубьев:
• шлифование — производится методом копирования или обкатки
шлифовальным кругом;
• шевингование — выполняется специальным инструментом ше-
вер-шестерней или шевер-рейкой (обкатывая обрабатываемое коле
со, шевер отделывает зубья до требуемых точности и шероховатости
поверхности);
• притирка — производится с помощью специального чугунного колеса
(притира), находящегося в зацеплении с обрабатываемым колесом.
3.9. В зависимости от способа получения заготовки зубчатые колеса
подразделяют на литые (рис. 3.9), кованые или штампованные, изготовлен ные механической обработкой (рис. 3.10), сварные (рис. 3.11).
|
|
|
Рис. 3.9. Литое зубчатое колесо Рис. 3.10. Кованое или штампованное Рис. 3.11. Сварное зубчатое колесо
колесо, механически обработанное
Зубчатые колеса, у которых диаметр впадин незначительно превышает диаметр вала в месте посадки зубчатого колеса, изготовляют за одно целое с валом. Такую конструкцию (рис. 3.12) называют валом-шестерней. В остальных случаях зубчатое колесо выполняется отдельно, после чего насаживается на вал.
Рис. 3.12. Вал-шестерня
Колеса диаметром меньше 400 мм имеют форму диска с выточками (см. рис. 3.9) или без выточек. Чаще всего эти колеса изготовляют из поковок. Колеса диаметром более 400—500 мм изготовляют со спицами (рис. 3.13) различного сечения.
Рис. 3.13. Зубчатое колесо со спицами
При конструировании колеса наиболее важным требованием является его жесткость. Основные соотношения элементов зубчатых колес в зависимости от их конструкции приведены в специальных справочниках.
Для экономии высокопрочных дорогостоящих материалов изготовляют сборные конструкции — бандажированные колеса (рис. 3.14). В этом случае зубчатый венец колеса изготовляют из качественной стали, а центральную часть делают из менее дорогого материала (например, чугуна).
|
Венец |
Окно Ступица
Рис. 3.14. Зубчатый венец бандажированного колеса
Дата добавления: 2019-09-13; просмотров: 552; Мы поможем в написании вашей работы! |
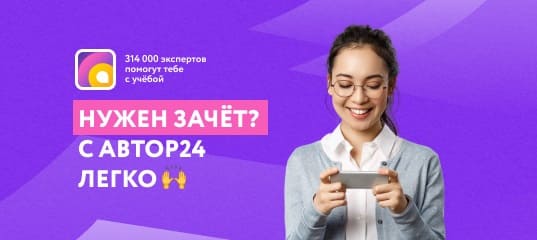
Мы поможем в написании ваших работ!