КАЛІБРИ ДЛЯ КОНТРОЛЮ ГЛАДКИХ ЦИЛІНДРИЧНИХ ДЕТАЛЕЙ
Задано циліндричне з’єднання Æ80H8/h7. Розрахувати калібри.
Розв’язок.
1. Визначаємо за ДСТУ 2500 - 94 [1] граничні відхилення і розміри отвору (Æ80H8).
ES = 46 мкм; D = D + ES = 80,0 + 0,046 = 80,046 мм;
EI = 0 мкм; D = D + EI = 80,0 + 0 = 80,0 мм.
За ГОСТ 24853 – 81 [3], табл. 2 знаходимо дані для розрахунку розмірів калібрів: H = 5 мкм; Y = 5 мкм; Z = 7 мкм; a = 0.
Розрахунок виконавчих розмірів виконуємо за формулами, які приведені в [3], табл. 1.
Найбільший розмір прохідного нового калібру - пробки ПР:
ПР = D
+ Z + H/2 = 80,0 + 0,007 + 0,0025 = 80,0095 мм.
Найменший розмір спрацьованого калібру - пробки ПР :
ПР = D
- Y = 80,0 - 0,005 = 79,995 мм.
Найбільший розмір непрохідного калібру - пробки НЕ:
НЕ = D
+ H/2 = 80,046 + 0,0025 = 80,049 мм.
Отже, виконавчі розміри калібру - пробки Æ80 Н7:
ПР = 80,0095 мм;
ПР = 79,995 мм;
НЕ = 80,049 мм.
Побудуємо схему розміщення полів допусків калібру - пробки Æ80 Н7 у відповідності до [3], кресл. 1 (рис. 2.1, ст.11).
2. Визначаємо за [1] відхилення і розміри валу (Æ80 h7).
es = 0 мкм; d = d + es = 80,0 + 0 = 80,0 мм;
ei = -30 мкм; d = d + ei = 80,0 + (-0,030) = 79,970 мм.
За ГОСТ 24853 - 81 [3], табл. 2 знаходимо дані для розрахунку розмірів калібрів: H = 5 мкм; H
= 2 мкм; Y
= 3 мкм; Z
= 4 мкм.
Розрахунок виконавчих розмірів виконуємо за формулами, які приведені в [3], табл. 1.
Примітка. В даній таблиці у формулах розміри отворів і валів позначені однаково - літерою D з відповідними індексами .Для зручності, згідно означення в п. 1.1, будемо використовувати позначення розміру валу d.
|
|
Найменший розмір прохідного нового калібру - скоби ПР:
ПР = d
- Z
- H
/2 = 80,0 - 0,004 - 0,0025 = 79,994 мм.
Найбільший розмір спрацьованого калібру - скоби ПР :
ПР = d
+ Y
= 80,0 + 0,003 = 80,003 мм.
Найменший розмір непрохідного калібру - скоби НЕ:
НЕ = d
- H
/2 = 79,970 - 0,0025 = 79,968 мм.
Отже, виконавчі розміри калібру - скоби Æ80 h7:
ПР = 79,994 мм;
ПР = 80,003 мм;
НЕ = 79,967 мм;
Рис. 2.1 Схема розміщення полів допусків калібру - пробки Æ80 Н7.
3. Визначаємо розміри контрольних калібрів для калібру - скоби.
Найбільший розмір для контролю прохідного нового калібру - скоби:
К - ПР = d
- Z
+ H
/2 = 80,0 - 0,004 + 0,001 = 79,997 мм.
Найбільший розмір для контролю непрохідного нового калібру - скоби:
К-НЕ = d
+ H
/2 = 79,981 + 0,001 = 79,971 мм.
Найбільший розмір для контролю спрацьованого калібру скоби:
К-I = d
+ Y
+ H
/2 = 80,0 + 0,003 + 0,001 = 80,004 мм.
Отже, виконавчі розміри для контролю калібру - скоби Æ80 h6:
К – ПР = 79,997 мм;
К-НЕ = 79,971 мм;
К-I = 80,004 мм.
Побудуємо схему розміщення полів допусків калібру - скоби Æ80 h7 у відповідності до [3], кресл. 5 (рис. 2.2).
Рис.2.2Схема розміщення полів допусків калібр – скоби Æ80 h7.
Ескізи калібру – пробки і калібру – скоби показані на рис. 2.3.ст. 13.
Рис.2.3 Ескізи калібру – пробки і калібру – скоби.
РОЗМІРНІ ЛАНЦЮГИ
|
|
На рис. 3.2 показаний вузол кріплення диску ротора 1 на валу 5. Крутний момент диску ротора передається через пальці 4, призначення яких полягає в захисті машини і двигуна від перевантажень. За службовим призначенням пристрою необхідно, щоб зазор між диском ротору і ступицею 3 був витриманий в межах від 1,1 до 1,3 мм. Ступиця на валу кріпиться ковпаком – гайкою 2. Необхідно визначити допуски (відхилень) для всіх розмірів деталей, які впливають на величину вказаного зазору.
1. В даній задачі замикальною ланкою є зазор В∆. Приймаємо номінальний розмір цього зазору В∆ = 1 мм. Тоді, згідно завдання:
[В∆max] = 1,2 мм; [В∆min] = 0,2 мм;
[ES∆] = +0,2 мм; [EI∆] = -0,8 мм;
[∆c∆] = -0,3 мм; [T∆] = 1,0 мм.
а) б)
2. За рис. 3.1, а визначаємо ланцюг розмірів, які впливають на зміну замикаючої ланки і складаємо схему розмірного ланцюга (рис. 3.2. б). Зменшувальною є ланка В3, всі інші – збільшуючими.
3. Номінальні розміри складових ланок: В1 = 12 мм; В2 = 17 мм; В3 = 37 мм; В4 = 9 мм. Складаємо рівняння розмірного ланцюга (3.1):
В∆ = (В1 + В2 + В4 ) - В3 = (12 + 17 + 9) – 37 =1 (мм).
Отже, номінальні розміри складових ланок призначені правильно.
4. Розрахуємо допуски складових ланок за способом одного квалітету. За формулою (3.14) ст.23 і табл. 3.1 визначаємо середнє число одиниць допуску складових розмірів:
|
|
мкм;
По табл. 3.2 знаходимо, що таке число одиниць допуску відповідає наближено 12 – му квалітету в ЄСДП. Приймаємо, що така точність в даних умовах доцільна.
5. Таким чином, допуски складових розмірів з врахуванням степені складності виготовлення приймаємо згідно [1]: T1 =180 мкм; T2 = 180 мкм; T3 =250 мкм; T4 = 150 мкм.
Перевіряємо правельність призначення допусків складових ланок за рівнянням (3.4):
T∆ = 0,18*2 + 0,25 + 0,15 = 0,76 < [T∆] » 1,0 мм.
6. Призначаємо граничні відхилення на всі складові розміри виходячи з економічної доцільності виготовлення. Для ступеневих ланок В1 призначаємо відхилення js, тобто Dс1 =0. Для B3 призначаємо граничне відхилення js,тобто Dс3= 0. Для B4 призначаємо граничне відхилення c, тобто Dс4 = EI + 1/2T4 = = -0.155 мм ( EI = -0.230 мм). Тоді середнє відхилення поля допуску В2 = Вх (див. 3.18) [8], стор. 24:
Dс2 = Dcxзб = Dс3 – (Dс1 + Dс4) + [DсD]
Граничні відхилення В2 = Вх (3.19) [8], стор. 24:
ЕS2= ЕSx = Dcxзб + 1/2T2 = –145 + 90= –55мкм;
EI2 = EIx = Dcxзб – 1/2Т2 = –145 – 90 = –235 мкм.
Одержані значення близькі до 17d12 ; Dc2 = –140 мкм.
Прийняті розміри і відхилення заносимо в табл. 3.1:
Таблиця 3.1
Позначення ланок | Можлива кінцева технологічна операція | Розміри і відхилення, мм | Примітка |
BD | Складання | 1 ![]() | За умовою |
B1 | Токарна обробка | 12±0,090 | 12 js12 |
B2 | Токарна обробка | 17 ![]() | 17d12 |
B3 | Токарна обробка | 37±0,125 | 37 js12 |
B4 | Токарна обробка | 9 ![]() | 9c12 |
|
|
7. Правильність призначення граничних відхилень перевіряємо за формулами (3.8), (3.9), (3.10) [8], стор. 22:
ESD = (Dc2 +Dc1 + Dc4) - Dc3 + 1/2TD = (–140 + 0 – 155) – 0 + 380 = 0,085 ≤ [ESD] = = 0,2 мм;
EID = (Dc2 +Dc1 + Dc4) – Dc3 – 1/2TD = (–140 + 0 – 135) –0– 380 = –0,655 ≥ [EID] = = – 0,8 мм , тобто граничні відхилення складових ланок призначені правильно.
Дата добавления: 2019-09-02; просмотров: 353; Мы поможем в написании вашей работы! |
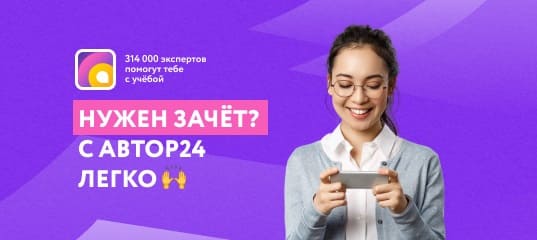
Мы поможем в написании ваших работ!